虚拟制造技术及其应用外文文献翻译、中英文翻译、外文翻译
虚拟制造技术的发展及其应用
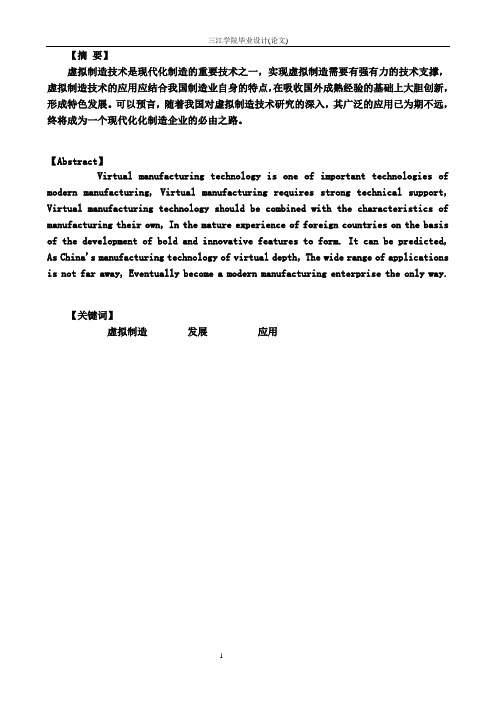
【摘要】虚拟制造技术是现代化制造的重要技术之一,实现虚拟制造需要有强有力的技术支撑,虚拟制造技术的应用应结合我国制造业自身的特点,在吸收国外成熟经验的基础上大胆创新,形成特色发展。
可以预言,随着我国对虚拟制造技术研究的深入,其广泛的应用已为期不远,终将成为一个现代化化制造企业的必由之路。
【Abstract】Virtual manufacturing technology is one of important technologies of modern manufacturing, Virtual manufacturing requires strong technical support, Virtual manufacturing technology should be combined with the characteristics of manufacturing their own, In the mature experience of foreign countries on the basis of the development of bold and innovative features to form. It can be predicted, As China's manufacturing technology of virtual depth, The wide range of applications is not far away, Eventually become a modern manufacturing enterprise the only way.【关键词】虚拟制造发展应用目录第一章虚拟制造技术的基本概念——————————————————————03第二章虚拟制造技术的发展————————————————————————04§2.1虚拟制造技术的发展及其国内外发展趋势———————————————04 §2.2国内机械装备数字化虚拟制造的发展————————————————05 §2.3我国虚拟制造技术的发展策略————————————————————07 第三章虚拟制造技术的应用————————————————————————10 §3.1虚拟制造技术应用发面所面对的难题—————————————————10 §3.2实施虚拟制造应采取的措施—————————————————————10 §3.3虚拟制造技术在未来装备研制中的应用————————————————11 §3.4虚拟制造技术在制造业中的应用———————————————————12 第四章结束语——————————————————————————————14谢辞—————————————————————————————————15 附件—————————————————————————————————16第一章虚拟制造技术的基本概念为了在竞争激烈的全球市场求得生存与发展,必须能够更好地满足市场所提出的T、Q、C、S要求,即要以最短的产品开发周期(Time),最优质的产品质量(Quality),最低廉的制造成本(Cost)和最好的技术支持与售后服务(Service)来赢得市场与用户.面对不可预测、持续发展、快速多变的市场需求,企业的生产活动必须具有高度的柔性。
制造专业毕业设计外文翻译--仿真技术在制造业中的应用与发展
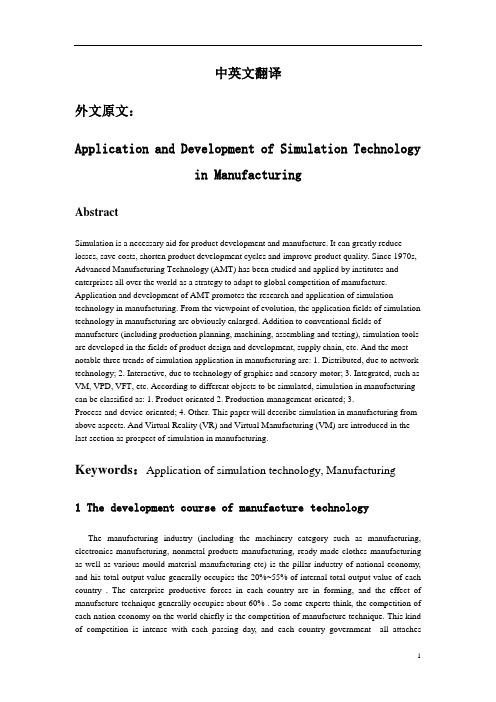
中英文翻译外文原文:Application and Development of Simulation Technologyin ManufacturingAbstractSimulation is a necessary aid for product development and manufacture. It can greatly reduce losses, save costs, shorten product development cycles and improve product quality. Since 1970s, Advanced Manufacturing Technology (AMT) has been studied and applied by institutes and enterprises all over the world as a strategy to adapt to global competition of manufacture. Application and development of AMT promotes the research and application of simulation technology in manufacturing. From the viewpoint of evolution, the application fields of simulation technology in manufacturing are obviously enlarged. Addition to conventional fields of manufacture (including production planning, machining, assembling and testing), simulation tools are developed in the fields of product design and development, supply chain, etc. And the most notable three trends of simulation application in manufacturing are: 1. Distributed, due to network technology; 2. Interactive, due to technology of graphics and sensory-motor; 3. Integrated, such as VM, VPD, VFT, etc. According to different objects to be simulated, simulation in manufacturing can be classified as: 1. Product-oriented 2. Production-management-oriented; 3.Process-and-device-oriented; 4. Other. This paper will describe simulation in manufacturing from above aspects. And Virtual Reality (VR) and Virtual Manufacturing (VM) are introduced in the last section as prospect of simulation in manufacturing.Keywords:Application of simulation technology, Manufacturing1 The development course of manufacture technologyThe manufacturing industry (including the machinery category such as manufacturing, electronics manufacturing, nonmetal products manufacturing, ready-made clothes manufacturing as well as various mould material manufacturing etc) is the pillar industry of national economy, and his total output value generally occupies the 20%~55% of internal total output value of each country . The enterprise productive forces in each country are in forming, and the effect of manufacture technique generally occupies about 60% . So some experts think, the competition of each nation economy on the world chiefly is the competition of manufacture technique. This kind of competition is intense with each passing day, and each country government all attachesimportance to research to the manufacturing industry very much to the constantly change of development as well as requirement of customer's at a high speed along with the economy technology and market environment . The advanced manufacture technique ( AMT: the manufacturing integration technology that in order to improve with T's ( developing period ) , Q's ( product quality ) , C's ( development cost ) , S's ( after-sale service ) and E ( pollution of the environment level ) give first place to to weigh the product of quota and product development course , the United States has put forward including system overall technology , management technology in the 80's ends and design , manufacture technology and equipment technology and big technology crowd of support technology five Advanced Manufacturing Technology ) the generally thought .As a result of the development of ten remaining years, now the content of five big technology crowds is arrived richly greatly, his concrete meaning as follows [ 12 ] :System overall technology crowd: Study the overall technology such as design, planning and integration etc like flexible manufacturing, computer integrated manufacturing, quick manufacturing and intellect manufacturing etc advanced manufacture techniquesTechnology crowd is managed: Study and makes the various technology of the production management of enterprise and organization and administration correlation, if computer-aided production control and thing material requirement plan /'s manufacturing resources plans / enterprise resources plans and the supply chain is managed and the completely quality management and the technology such as manufacturing, excellent production and enterprise management course reconfiguration etc punctually . Integration technology crowd is made in the design : Studies and product design , manufacturing and waiting entirely the various technology of course correlation until tests , if the parallel engineering and computer-aided design /'s computer-aided engineering /'s computer-aided and makes and draws up solid manufacturing , reliability design , intelligent optimization design and the quality merit can be disposed and the technology such as preservation and transportation , automatic control , checkout supervision as well as quality assurance etc are expected by digital control technology and thing . Manufacture technology and equipment technology crowd, The research reaches the various technology that the equipment is mutually related with the manufacture technology , process technology that the nothing cutting process technology reaching equipment ( casting , forging , welding and heat treatment etc ) if material production technology reaches equipment ( smelts and steel rolling etc ) and convention process technology and lacks reaches that the equipment and ultrahigh speed process technology at a high speed reaches the equipment and precisely super precise and the nanometer and equipment and special process technology and equips ( laser and electron beams etc )Technology crowd puts up : This technology crowd is the correlation technique that the advance was not gained in above technology crowd Lai Yi existence absolutely , if the standardization technology , computer technology , software engineering , data base technology , multi-medium technology , internet work communication technology , artificial intelligence and virtual reality technology , materials science and personnel educate and train and human engineering and environmental science etcCan conclude in the stage that the development course of above major manufacture technique that involves and his were applied in product life period to the picture 1 .The picture is in 1 , indulges spool represents age , the cross axle represents the life period ofproduct , from the requirement in market forms begins , passes generally reads design ( appearance , characteristic , material , price and batch ) and initial ( overall ) design and detail ( the parts ) design , technological design , production planning formulation ( material is purchased ) and produces ( process’s , assembles and tests ) , arrives continuously the sale and safeguards , involves each department of enterpriseThe quality and production efficiency of product have been raised greatly by way of research and application to the advanced manufacture technique2 computers simulation develops and applying in the manufacturing industryThe general situationThe computer technique of simulation is as a new and developing high technology , and his methodology is built above the foundation of computer ability .Along with the development of computer technology, the technique of simulation also gets the rapid development, and his application domain and his effect is also more and more bigger . Particularly in aviation, aerospace and in national defense and the research and development course of other large-scale complex systems, computer simulation is continuously the tool that cannot lack , and has given play to hugely to act on aspect it is reducing losses , practices thrift the funds and shortens development period and raise the product quality etcDesigning to making so that in testing whole life period safeguarded from the product , the computer technique of simulation runs through from beginning to end ( the shadow part in the picture 1 represents the application of technique of simulation , and concludes further to the table 1 ) .See that is expanding to product design development and sale domain in the manufacturing domain ( production planning is laid down , processes , assembles and is tested ) from the tradition of the domain of technique of simulation application from the course developed .In a word, the application for computer simulation has provided the new stage to the development of advanced manufacture technique , and has also put forward the higher requirement , and the application of technique of simulation at present possesses following characteristic and trend : The application in whole product life period of 1 computer in table simulation1)The unprecedented enlargement of the application scope of technique of simulation.By studying the dynamics property the to make the object (product), kinematics property, process and assembly course of research product, enlarging to studying design and the operating making the system , the advance side by side one-step enlarges to the rear service supply , inventory control , organization of product development course and product test etc at the aspect of the object and the purpose of simulation , involves making each aspect of enterprise2)Combine distribution of simulation that brings with the network technology.Distribution of simulation is by the distribution decision of manufacturing.The generally thought itself such as quick manufacturing and invented enterprise etc has the person who cooperates a meaning in network implementation place far away from home basseted on3)Each other combine with diagram and the sensor technology, and makes the interactivity of simulation strengthen greatly .Having formed draws up the solid manufacturing (VM: from this Virtual Manufacturing ) and the invented product development ( VPD: Virtual Product Development ) and the invented test ( VT: Virtual Test ) wait the new generally thought4)The Integra ionization of technique of simulation application.Namely the synthetically application technique of simulation, product development and the manufacturing environment that the formation can moveThe object of technique of simulation application is seen, and can be divided into 4 kinds with simulation applied in the manufacturing industry: Towards the simulation of productTowards the simulation with equipment of manufacture technologyTowards the simulation of production controlTowards the simulation of other link of enterprise.Will follow above four aspects in third part of this text, and introduce the concrete application in the manufacturing industry of computer simulation.What the virtual reality solidly with draws up was made generally reads except this , sum aggregate one-tenthizations trend that the concentration has embodied the distribution of technique of simulation application and each other , so simply introducing , as the forecast of the application of computer simulation in the manufacturing industry .3 The concrete application in the manufacturing industry of computer simulation3.1 towards the simulation of productSimulation towards the product chiefly includes the following aspect:1)The analysis of the static state of product and dynamic capability.The quieting of product chiefly indicates the mechanics property such as stress and intensity etc The dynamic characteristic of product is when chiefly indicating the product sports , the connection and colliding between the organization2)The manufacturability analysis (DFM) of product.The DFM includes that the technology is analyzed and is analyzed with economy.The technology is analyzed the production environment to ask reaching reality according to the product technology and is carried on the analysis to the manufacturability completelyThe economy is analyzed carrying on the cost analysis, and according to the feedback factors such as time and cost etc , the economy to part process is appraised .3)Assembly nature analysis ( DFA ) of product.Analysis of DFA's is loaded and is dismantled the possibility, collides that the interference tests , and draws up out the reasonable assembly process route , and interference after visual display assembly course and assembly are reached the designated position and colliding problem .The reference [ 16 ] has been described the assembly process planning construction of simulation model system and has been realized3.2 Towards the simulation with equipment of manufacture technologyChiefly indicate to the simulation and the simulation of robot processing the center process course towards the manufacture technology with simulation equipped.Process course simulation (MPS): By NC's code drive, is chiefly used to test NC's code , and the colliding interference that the factors such as clamp etc cause is loaded in the inspection .His concrete merit can include:1)The simulation is processed equipment and is processed the sports and the state in the process course of object2)Every one-step of process course simulation is equal to NC's code drive3)The part process courses possess three to be tied up the real time to move the drawing merit ability, and can issue the warning when the discovery is collidedThe reference [15] has been introduced the structure and key technology and the major algorithm of MPS's system in the parallel engineering of applicationThe simulation of robot Along with the rapid development of robot technology, the robot has also got the extensive application in making the system.But the complicated dynamic system of machine, electricity and liquid owing to the robot being one kind of synthesis’s only makes by way of computer simulation to come the dynamic characteristic of simulation system, ability the control algorithm of the reasonable sports scheme of organization and effective is announced, thus the problem in robot design , manufacturing as well as operating course of settlement .3.3 How many kind [13] of robot technique of simulation below roughly can being divided into:1)Apply open-minded research be dead against the robot in making the system, and makes in the system simulation problem of robot if the flexible is made the system or the computer is integrated 2)Operate the simulation study that the property of hand itself is in progress be dead against the robot , like kinematics simulation , dynamics simulation , orbit planning and colliding inspection etc the problem3)The robot off-line is compiled the research of range system , if using the sports scheme automatic switchover one-tenth robot control procedure of simulation formation satisfaction to go the drive controller action3.3 Towards the simulation of production controlThe basic function of production control is plan, dispatch and controls .As far as the application in the production control of technique of simulation , roughly there are following three aspects :1)Define the production control strategy2) Design and the dispatch of workshop layer are used3)Used the inventory controlThe application of above three aspects introductions technique of simulations will be followed to the next3.3.1 The application in the production control strategy of computer simulationThat the simulation of the production control strategy being used includes defines the concerned parameter as well as is used the comparison between the different control strategy’s.The fairly more common control strategy has1) MRP: This is one kind of control strategy of the type " pushing “, and by way of the demand forecasting, the synthesis is thought over that the production plant capacity , available capacity of raw material and the stock measures and lays down the production planning2) KANBAN's (seeing the board) : This is one kind of control strategy of " pulling " type , lays down the production planning according to the order , and namely punctual production spoken usually3) LOC: Towards the control strategy of load ability.Control the production process according to the stock standard4)DBR: Towards the control strategy of bottleneck.Control whole distance traveled by a stream of water according to the bottle neck link in the production processThe quota weighing that compares generally includes outcome and productivity etcNeeds definite parameter pack to draw together in per kind of control strategy: The batch is big or small and sees board quantity and stock standard etcProvide a simulation course who compares in the reference [ 8 ] as for the different control strategies3.3.2 The application in making the design in workshop of computer simulationGenerally can be divided into the design process of workshop two major stages, Preliminary design stage and detail design stage .The assignment of preliminary design stage is the requirement to study user, then defines the preliminary design scheme from this .The major assignment of detail design stage is on the foundation of preliminary design, and puts forward the detailed and complete description to each component cell of workshop , and making the design result can achieve to carry on the experiment and goes into operation the level making policy , processing system and workshop layout etc are expected to the concrete definite equipment , tool , clamping apparatus , tray and thing approaching .And but the technique of simulation is chiefly used evaluation and the selection of scheme.In preliminary design stage, can contain the economic performance parsing algorithm in the emulators , and move the simulation model built according to the preliminary design scheme , and give following evaluation information :Product type sum whether satisfied user of capacity who produces in the new workshop can ask :Whether or not the quality and precision of product can satisfy the requirementReasonably whether or not the efficiency and investment rate of recovery of new workshopIn detail design stage , the use technique of simulation can to candidate the following aspect of scheme makes the evaluation :Can the major equipment processed get the full utilization in the workshop when making themajor part?Whether or not the load is fairly more balancedWhether or not the thing material processing system can and the flexible level of workshop be adaptable each otherCan the requirement of production scheduling be satisfied in the entire layout of new workshop?But whether or not possess the fixed reconfiguration abilityWhether or not the product system in workshop can be kept the production capacity of fixed level when breaking downThe available design in the supplementary workshop product system of the software that some ripen has all been developed out in the home and abroad at present, like AUTOMOD/AUTOGRAM and IMMS that the Singh University develops etc [ 2 ] that the SIMAN/CINEMA and Auto Simulation corporation that the GCMS and System Modeling corporation that the PURDUE university develops .3.3.3 The application in making the operating in workshop of computer simulationThe scheduling problem among the FMS can the definition be the production resources that distribution and coordination can gain, if processing the machine and leads voluntarily transportation tool (AGV), robot as well as time worked overtime etc, in order to satisfy the objective appointed .These objectives can be satisfied delivery date and outcome achieve fully, and the utilization ratio of machine achieves highly , or the combination of mentioned above objective .The scheduling process among the FMS includes:Select the work piece of FMSProcess and select process route for the work pieceSelect the work processed gone at the machine gone forwardThe rule is sent in the selection for AGVMajor above aspect degree of the exchanging problem of emulation mode is analyzed and is appraisedThere are some the person who ripens available settlement scheduling problems of software at present, if Autosched, JobTimePlus, FACTOR, FACTOR/AIM, SIMNETDs etc. That our country has also developed is used the workshop to dispatch the simulation software of layer , if : Environment FASE, as well as the intelligent rule dispatching system developed on this foundation etc [ 3 ] is dispatched in the factory simulation of the Singh University and the Ministry of Aerospace Industry 204 unit waiting development to Job Shop’s dispatch simulation software of NanKai University development .3.3.4 The application in the inventory control of computer simulationStock the sub system taking to stress the effect wanted in the whole product system.Divide according to stocking the effect of material in the production line, and can be divided into online storehouse and center storehouse.According to stocking the material quality branch, can be divided into that raw material andoutside purchases the warehouse and in products warehouse, stock and maintenance spare parts and tool warehouseThe purpose of inventory control depends on, and makes the stock invest lastly, and just will satisfy the requirement producing and selling .Simulation as for the inventory control includes:1) Defining orders goods the tactics2)Order and order batch are defined3) Define the distribution of storehouse4) Define the safety stock standardThe reference [ 9 ] has been described the model building and the simulation of the pass the steps , distribution and inventory control system of trends译文:仿真技术在制造业中的应用与发展摘要在制造企业产品设计和制造的过程中,计算机仿真一直是不可缺少的工具,它在减少损失、节约经费、缩短开发周期、提高产品质量等方面发挥了巨大作用。
【精品】柔性制造中英文翻译外文文献翻译

【关键字】精品Flexible ManufacturingAs an introduction to the subsequent discussions of production systems and advanced manufacturing technologies it is useful to present a definition of the term manufacturing system. A manufacturing system can be defined as a series of value-adding manufacturing processes converting the raw materials into more useful forms and eventually finished products.In the modern manufacturing setting, flexibility is an important characteristic. It means that a manufacturing system is versatile and adaptable, while also capable of handling relatively high production runs. A flexible manufacturing system is versatile in that it can produce a variety of parts. It is adaptable because it can be quickly modified to produce a completely different line of parts.A flexible manufacturing system is an individual machine or group of machines served by an automated materials handling system that is computer controlled and has a tool handling capability. Because of its tool handling capability and computer control, such a system can be continually reconfigured to manufacture a wide variety of parts. This is why it is called a flexible manufacturing system.A FMS typically encompasses:* Process equipment e.g. , machine tools, assembly stations, and robots* Material handling equipment e.g. , robots, conveyors, and AGVs (automated guided vehicles) * A communication system* A computer control systemFlexible manufacturing represents a major step toward the goal of fully integrated manufacturing. It involves integration of automated production processes. In flexible manufacturin , the automated manufacturing machine and the automated materials handling system share instantaneous communication via a computer network. This is integration on a small scale.Flexible manufacturing takes a major step toward the goal of fully integrated manufacturing by integrating several automated manufacturing concepts:* Computer numerical control (CNC) of individual machine tools* Distributed numerical control (DNC) of manufacturing systems* Automated materials handling systems* Group technology (families of parts)When these automated processes, machines, and concepts are brought together in one integrated system, an FMS is the result. Humans and computers play major roles in an FMS. The amount of human labor is much less than with a manually operated manufacturing system, of course. However, humans still play a vital role in the operation of an FMS. Human tasks include the following:* Equipment troubleshooting, maintenance, and repair* Tool changing and setup* Loading and unloading the system* Data input* Changing of parts programs* Development of programsFlexible manufacturing system equipment, like all manufacturing equipment, must be monitored for bugs, malfunctions, and breakdowns. When a problem is discovered, a human troubleshooter must identify its source and prescribe corrective measures. Humans also undertake the prescribed measures to repair the malfunctioning equipment. Even when all systems are properly functioning, periodic maintenance is necessary.Human operators also set up machines, change tools, and reconfigure systems as necessary. The tool handling capability of an FMS decreases, but does not eliminate involvement in tool changing and setup. The same is true of loading and unloading the FMS. Once raw material has been loaded onto the automated materials handling system, it is moved through the system in the prescribed manner. However, the original loading onto the materials handling system is still usually done by human operators, as is the unloading of finished products.Humans are also needed for interaction with the computer. Humans develop part programs that control the FMS via computers. They also change the programs as necessary when reconfiguring the FMS to produce another type of part or parts. Humans play less labor-intensive roles in an FMS, but the roles are still critical.Control at all levels in an FMS is provided by computers. Individual machine tools within an FMS are controlled by CNC. The overall system is controlled by DNC. The automated materials handling system is computer controlled, as are other functions including data collection, system monitoring, tool control, and traffic control. Human/computer interaction is the key to the flexibility of an FMS.1 Historical Development of Flexible ManufacturingFlexible manufacturing was born in the mid-1960s when the British firm Molins, Ltd. Developed its System24. System 24 was a real FMS. However, it was doomed from the outset because automation, integration, and computer control technology had not yet been developed to the point where they could properly support the system. The first FMS was a development that was ahead of its time. As such, it was eventually discarded as unworkable.Flexible manufacturing remained an academic concept through the remainder of the 1960s and 1970s. However, with the emergence of sophisticated computer control technology in the late 1970s and early 1980s, flexible manufacturing became a viable concept. The first major users of flexible manufacturing in the United States were manufacturers of automobiles, trucks, and tractors.2 Rationale for Flexible ManufacturingIn manufacturing there have always been tradeoffs between production rates and flexibility. At one end of the spectrum are transfer lines capable of high production rates, but low flexibility. At the other end of the spectrum are independent CNC machines that offer maximum flexibility, but are capable only of low production rates. Flexible manufacturing falls in the middle of continuum. There has always been a need in manufacturing for a system that could produce higher volume and production runs than could independent machines, while still maintaining flexibility.Transfer lines are capable of producing large volumes of parts at high production rates. The line takes a great deal of setup, but can turn out identical in a part can cause the entire line to be shut down and reconfigured. This is a critical weakness because it means that transfer lines cannot produce different parts, even parts from within the same family, without costly and time-consuming shutdown and reconfiguration.Traditionally, CNC machines have been used to produce small volumes of parts that differ slightly in design. Such machines are ideal for this purpose because they can be quickly reprogrammed to accommodate minor or even major design changes. However, as independent machines they cannot produce parts in large volumes or at high production rates.An FMS can handle higher volumes and production rates than independent CNC machines. They cannot quite match such machines for flexibility, but they come close. What is particularly significant about the middle ground capabilities of flexible manufacturing is that most manufacturing situations require medium production rates to produce medium volumes with enough flexibility to quickly reconfigure to produce another part or product. Flexible manufacturing fills this long-standing void in manufacturing.Flexible manufacturing, with its ground capabilities, offers a number of advantages for manufacturers:* Flexibility within a family of parts* Random feeding of parts* Simultaneous production of different parts* Decreased setup time and lead time* More efficient machine usage* Decreased direct and indirect labor costs* Ability to handle different materials* Ability to continue some production if one machine breaks down3 Flexible Manufacturing System ComponentsAn FMS has four major components:* Machine tools* Control system* Materials handling system*Human operators(1) Machine ToolsA flexible manufacturing system uses the same types of machine tools as any other manufacturing system, be it automated or manually operated. These include lathes, mills, drills, saws, and so on. The type of machine tools actually included in an FMS depends on the setting in which the machine will be used. Some FMS are designed to meet a specific, well-defined need. In these cases the machine tools included in the system will be only those necessary for the planned operations. Such a system would be known as a dedicated system.In a job-shop setting, or any other setting in which the actual application is not known ahead of time or must necessarily include a wide range of possibilities, machines capable of performing at least the standard manufacturing operations would be include. Such systems are known as general purpose systems.(2) Control SystemThe control system for an FMS serves a number of different control functions for system:* Storage and distribution of parts programs* Work flow control and monitoring* Production control*System/tool control/monitoringThe control area with the computer running the FMS control system is the center from which all activities in the FMS are controlled and monitored. The FMS control software is rather complicated and sophisticated since it has to carry out many different tasks simultaneously. Despite the considerable research that has been carried out in this area, there is no general answer to designing the functions and architecture of FMS software.The scheduler function involves planning how to produce the current volume of orders in the FMS, considering the current status of machine tools, work-in-process, tooling, and so on. The scheduling can be done automatically or can be assisted by an operator. Most FMS control systems combine automatic and manual scheduling; the system generates an initial schedule that can be changed manually by the operator. The dispatcher function involves carrying out the schedule and coordinating the activities on the shop floor, that is, deciding when and where to transport a pallet, when to start a process on a machining center, and so on.The monitor function is concerned with monitoring work progress, machine status, alarm messages, and so on , and providing input to the scheduler and dispatcher as well asgenerating various production reports and alarm messages. A transport control module manages the transportation of parts and palettes within the system. Having an AGV system with multiple vehicles, the routing control logic can become rather sophisticated and become a critical part of the FMS control software. A load/unload module with a terminal at the loading area shows the operators which parts to introduce to the system and enables him or her to update the status of the control system when parts are ready for collection at the loading area. A storage control module keeps an account of which parts are stored in the AS/RS as well as their exact location. The tool management module keeps an account of all relevant tool data and the actual location of tools in the FMS. Tool management can be rather comprehensive since the number of tools normally exceeds the number of parts in the system, and furthermore, the module must control the preparation and flow of tools. The DNC function provides interfaces between the FMS control program and machine tools and devices on the shop floor. The DNC capabilities of the shop floor equipment are essential to a FMS; a “full” DNC communication protocol enabling remote control of the machines is required.The fact that most vendors of machine tools have developed proprietary communication protocols is complicating, the development and integration of FMSs including multi-vendor equipment. Furthermore, the physical integration of multi-vendor equipment is difficult; for example, the differences in pallet load /unload mechanics complicate the use of machine tools from different vendors. Therefore, the only advisable approach for implementing a FMS is to purchase a turn-key system from one of the main machine tool manufacturers.(3)Human OperatorsThe final component in an FMS is the human component. Although flexible manufacturing as a concept decreases the amount of human involvement in manufacturing, it does not eliminate it completely. Further, the roles humans play in flexible manufacturing are critical. These include programming, operating, monitoring, controlling, and maintaining the system.柔性制造正如对制造系统和先进的制造技术后来的讨论,介绍制造业系统术语的定义是十分有用的。
快速成型与虚拟成型在产品设计和制造中的应用毕业课程设计外文文献翻译
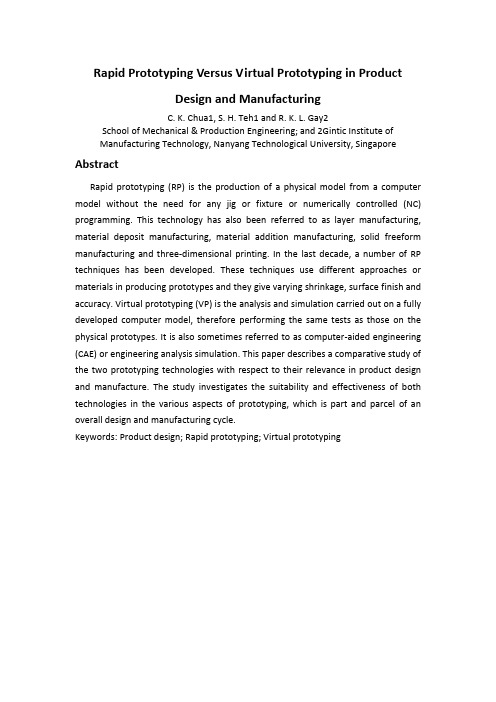
Rapid Prototyping Versus Virtual Prototyping in ProductDesign and ManufacturingC. K. Chua1, S. H. Teh1 and R. K. L. Gay2School of Mechanical & Production Engineering; and 2Gintic Institute ofManufacturing Technology, Nanyang Technological University, Singapore AbstractRapid prototyping (RP) is the production of a physical model from a computer model without the need for any jig or fixture or numerically controlled (NC) programming. This technology has also been referred to as layer manufacturing, material deposit manufacturing, material addition manufacturing, solid freeform manufacturing and three-dimensional printing. In the last decade, a number of RP techniques has been developed. These techniques use different approaches or materials in producing prototypes and they give varying shrinkage, surface finish and accuracy. Virtual prototyping (VP) is the analysis and simulation carried out on a fully developed computer model, therefore performing the same tests as those on the physical prototypes. It is also sometimes referred to as computer-aided engineering (CAE) or engineering analysis simulation. This paper describes a comparative study of the two prototyping technologies with respect to their relevance in product design and manufacture. The study investigates the suitability and effectiveness of both technologies in the various aspects of prototyping, which is part and parcel of an overall design and manufacturing cycle.Keywords: Product design; Rapid prototyping; Virtual prototyping1. IntroductionRapid prototyping (RP) is emerging as a key prototyping technology with its ability to produce even complicated parts virtually overnight. It enables product designers to shorten the product design and development process. The coming-of-age of this technology is clearly reflected in the inclusion of a stereolithography (STL) file generator in most, if not all, CAD. systems today. The STL file is the de facto standard used by RP systems in the representation of the solid 3D CAD models.While RP is a relatively young technology, virtual prototyping (VP) has been in steady development since the 1970s in many guises. Virtual prototyping is taken to mean the testing and analysis of 3D solid models on computing platforms. Today, VP is often tightly integrated with CAD/CAM software and sometimes referred to as CAE packages. It provides the ability to test part behaviour in a simulated context without the need to manufacture the part first [1].2. Definitions of RP and VPRapid prototyping (RP) is a widely used term in engineering, particularly in the computer software industry where it was first coined to describe rapid software development.This term has also been adopted by the manufacturing industry to characterise the construction of physical prototypes from a solid, powder, or liquid in a short period of time when compared to “traditional” subtractive machining methods. This technology has also been variously referred to as layer manufacturing, material deposit manufacturing, material addition manufacturing, solid freeform manufacturing and threedimensional printing [2].Virtual prototyping (VP) refers to the creation of a model in the computer, often referred to as CAD/CAM/CAE. Virtual or computational prototyping is generally understood to be the construction models of products for the purpose of realistic graphical simulation [1]. In this paper, VP will refer to thesimulation, virtual reality and manufacturing process design domains [3].Nevertheless, there are many areas where the distinction between RP and VP is blurred. As RP systems rely on CAD systems to generate the files needed to produce the prototype, it would seem that RP is a downstream process from VP in the product or part development cycle. Indeed, Pratt’s definition of VP reveals the factthat VP is a term which is loosely used in the prototyping community. As such, it would be appropriate to clearly define both RP and VP.Rapid prototyping will be taken to mean, as above, the production of a physical model from a computer model without the need of any jig or fixture or NC programming. This also includes other related processes and applications which use RP-produced objects, such as rapid tooling.Similarly, VP is defined as the subsequent manipulation of a solid CAD model as a substitute for a physical prototype for the purposes of simulation and analysis, and is not inclusive of the construction of the solid 3D model. VP includes the following functions:1. Finite element analysis.2. Mechanical form, fit and interference checking.3. Mechanical simulation.4. Virtual reality applications.5. Cosmetic modelling.6. Assemblability.The relationships between RP and VP are shown in Fig. 1.Fig. 1. Classification of RP and VP3. Prototyping in SingaporeTwo selected multi-national companies (one American and one French) based in Singapore with significant product development activities showed differing approaches to both RP and VP. Both use RP in their prototyping activities.The first company, B, placed more emphasis on virtual prototyping. It manufactures telecommunications equipment such as pagers and handphones. It is moving all prototyping applications upstream, which is to move prototyping from RP to VP. At present, their RP models are used only for proof of concept and marketing purposes. Other prototyping activities are being carried out with VP.The second company, C, manufactures consumer electronics products such as television sets, video cassette recorders and telephones. It uses VP only as a tool to create a solid 3D model. From the solid 3D model, C generates the STL file needed to produce the RP prototype. Company C then uses the RP part as a master for silicone rubber moulds to produce a limited number of physical ABS (polyacrylonitrite butadienestyrene) prototypes for the various prototyping tests and simulation.Company B intends to move more prototyping to VP, rather than using physical models. Virtual prototyping allows for improvements in reliability and quality as well as reducing costs. Manipulation of virtual prototypes makes it easier for B to implement design improvements compared to an iterative cycle using physical prototypes.Company B drafts the CAD models in Pro/ENGINEER, then uses Patran to pre-process the models. Static finite-element analysis (FEA) is carried out with ABAQUS Standard whereas dynamic scenarios are analysed with ABAQUS Explicit. ALIAS/Wavefront is used for cosmetic modelling when presenting different conceptual and actual designs.The bulk of the VP carried out by B uses FEA, which typically takes 4–6 weeks for a pager design. Of all the FEA carried out, the majority are concentrated on structural strength (static) analysis and drop test (dynamic) analysis. Vibration tests are occasionally carried out. Some cosmetic modelling is carried out, but usually only for presentation purposes.Finite-element analysis is used to investigate the following problems:Relative comparison of different design options; to see how one design compares to another. Possible failure modes are:1. To evaluate a design change or design correction.2. To assess the possibility of failure, based on past experience.3. To make some educated-guess correlation with physical testing.4. To try to identify what initiated a failure.According to B, the drawback of VP is that it cannot simulate process problemsefficiently and effectively. The accuracy of FEA is also limited because of the inconsistent behaviour ofmaterial. The amount of computing power also determines the accuracy of FEA.The application of RP is rather limited in B. The in-house laminated object manufacturing (LOM) RP system is used to produce design prototypes for proof of concept only, and notgeometrical prototypes.Company C uses RP heavily, but has very little VP. The parts produced using RP range from audio products to 29-in. television casings. Typically, it takes 1 year from the conception of the product to the sale of the product. Company C aims to prototype all (mostly plastic) parts by RP. A comparison between numerically controlled (NC) machining of prototypes from ABS against RP is shown in Table 1. Company C projected 50% savings using an in-house RP system versus an NC machining system.CAD models are created using I-DEAS. The .STL format is then created for production of the RP part. The main purpose of the RP parts is to verify the design. Rapid prototyping parts are used for the following functions:1. Form fitting.2. Ergonomics check.3. Proof of concept (to confirm design with industrialdesigners).4. Manufacturability (design for tooling, design for assemblability).5. Reliability check (whether part dislodges or breaks when force applied, especially snap-on covers).6. Kinematic check.Company C offers some insight into the limitations of VP, in that VP is unable to model:1. Tactile feeling (for buttons) not quantified; may be able to VP if able to quantify “pressing” force.2. Assemblability (e.g. PCBs inserted at an angle, difficult to visualise).4. Case Study 1: Prototyping of a Telephone HandsetThis case study investigates the design verification, assembly, interference check and form fitting aspects of both the RP and VP model. The production ABS, RP and VP parts or models were evaluated in the above aspects. The RP system usedhere is the stereolithography apparatus (SLA). Both the ABS and RP parts are shown in Fig. 2. Inspection of the RP parts reveal that:1. The surface finish was much poorer than in the ABS part.2. Warpage was clearly evident (see Fig. 3).4.1 Design VerificationAs a true dimensional physical part, the RP model is able to give the designer a sense of size estimation. The judgement of a VP part can be erroneous because parts are often automatically sized to fit the viewing window. Another advantage of a physical part is that it allows for ergonomic checks, ranging from the fit of a telecommunications device in a user’s palm to the inspection of potentially dangerous corners and edges. Also, it offers tactile inspection which is crucial in products for which ergonomics is important, such as touch buttons on audio or video products, which is not possible on VP systems.Rounded edges which appear innocuous on a VP model may prove to be unsafe upon scrutiny of the RP part. Above all, most RP parts are produced for aesthetic evaluation purposes. Aesthetic evaluation is also possible on VP models. All CAD software allows the model to be viewed in any spatial orientation, along with at least rudimentary rendering capabilities. It is then possible to view the part under the desired simulated lighting conditions with millions of shading and colour combinations. RP parts cannot be coloured, thus surface preparation and painting introduce additional finishing processes. Any visibly apparent design discrepancies could be immediately rectified without having to invest in a physical part. It also allows designers to evaluate the aesthetics of the design and make corrections, if necessary. In the case of most multi-national companies, the design and manufacturing facilities are often a considerable distance apart and in different countries and continents. The ease with which CAD files can be sent and received via electronic means greatly helps the design process, be it iterative or concurrent. With identical or compatible CAD software, the prototyping process can be swift and cheap. Any design change of the virtual prototype can bemade almost instantly available to all parties involved in the design process.4.2 AssemblyAssembly of RP parts must be carried out quickly, as warpage and shrinkage increases with time. Warpage is a function of both part geometry design andshrinkage. All but the bestdesigned parts suffer from varying degrees of warpage and shrinkage. Some RP material such as the SLA inherently shrinks and the part is actually built slightly larger to allow it to shrink to its proper dimensions. With such arrangements, assembly is possible but is often hampered by warpage and/or shrinkage. Some parts can be mated only with the application of some force. Assembly of RP parts allows the user not only to attempt different assembly sequences, but also if a part cannot be positioned in a linear movement, to insert the part, say, at an angle before being set into its proper location. The drawback in assembling RP parts is that for some RP parts such as SLA, the material is weak and brittle, and fails when attached using fasteners or under low to moderate loading (see Figs 4 and 5). CAD software allows for the assembly of parts and subassemblies in the form of 3D solid or surface models. Assembly in the virtual realm is very often used to check for interference and form fitting which will be discussed later. The ability ofCAD software to assemble parts and/or subassemblies allows a product designer to quickly check to see if he or she has designed the part or parts correctly, i.e. whether a boss is tall enough to accept a screw inserted through another part or if two slots are aligned to form a larger slot. The advantage of assembling in a virtual environment is that no physical parts need be produced and thus this reduces cost. The absence of physical parts also means that tooling time is eliminated. The assembly in a virtual environment can be done in a matter of minutes or up to a few days, but is much faster than producing the physical parts and then assembling them. The user can also build or change a part, or modify its attributes when all instances of the part will be changed accordingly. Assembly relationships can be written in engineering parameters, part dimensions and orientation dimensions. The equations are solved variationally to allow for flexibility while working with the assembly. Evaluation of the tolerance specifications of the design to optimise the engineering performance at the lowest possible cost can be carried out. This allows the user to measure the sensitivity of a critical dimension in an assembly to changes in individual constraints. Manufacturing cost can then be reduced by tightening the tolerances which contribute most to the overall variation of a critical dimension, and loosening tolerances that have little impact.4.3 Interference Check and Form FittingAgain, interference checking and form fitting is hampered by warpage andshrinkage of the RP part. Therefore, the problem of parts which interfere or fit poorly may be due to one or more of: warpage; shrinkage; or design error. Even when RP parts fit well, there is no assurance that the parts are dimensionally correct, as shrinkage of two or more parts in the same direction or directions could still produce a good fit. When such situations arise, CAD models are often used to determine whether the interference or poor fit is due to design flaws.The ability to check for interference as well as form fitting is very widely used in CAD systems. It gives the user the ability to fit two parts together and check for interference without having to produce a part or parts which are potentially dimensionally incorrect, thereby increasing cost.The interactive nature of the process in a CAD system also frees the user or designer from the need to manually interpret engineering drawings to detect interference. This process also allows the user to establish tolerances which are crucial in the manufacturing process. The advantage of interference checking on a CAD system is not evident when an assembly consists of a small number of parts. For complex assemblies with alarge number of parts, there are often many features on a particular part that must be mated or aligned with features on one or more other parts. CAD systems allow not only the detection of any misalignment or interference but also immediate rectification of the problem. Interference checking is performed by the CAD system on an assembly when required by the user, and is relatively faster and more accurate and precise than other methods. The CAD system would also identify and list the features which interfere. The user can then view the entities to rectify the situation.5. Case Study 2: Prototyping of a Knee Prosthesis5.1 BackgroundRapid prototyping has applications in the field of medicine. However, in this application the STL file is no longer obtainable from a CAD model. There is a need to generate the necessary STL files from data acquired by medical equipment. Swaelens and Kruth [4] proposed three approaches to producing an RP part from computer assisted tomography (CT) scanner data (see Fig. 6). In most cases, STL-interfacing was used. In STL-interfacing, a CT scanner maps the contour of a 3D surface. This data is then converted into triangular file format which is then converted into the STL format required by RP machines. There is a direct conversion of data from the CTscanner to the RP machines. In effect, the scanned surface is faithfully reproduced by the RP machine.When used in this fashion, VP plays an almost negligible role, in RP-assisted surgery prototyping, as a viewer to verify the contour of the surface. Jacob et al. [5] constructed 3D models from CT scanner data using CTrans from Proform. They reported that the decisive advantage lies in the clearness and manual “getting in touch” as the s urgery proper is elaborate manual craftsmanship. The model can be viewed and palpated from any angle and could even be operated upon. In that way, surgeons could literally grasp the problem. This study shows VP as a viewer for a 3D model. While the study did not state whether the 3D model was a solid model, it opened the possibility of integrating CAD software into the process, data exchange problems notwithstanding.This contrasts with the CAD system route shown above. Researchers in the University of Leuven, Belgium identified contours from CT scanner data and introduced them into CAD software to generate surface models. The physical model of a hip was produced with much effort, and the whole procedure took several working weeks.The procedure of converting CT scanner data to a solid 3D model is tedious and prone to error. Given the triangulation points from the CT scanner, they must be joined to the appropriate adjacent points to form curves. Confusion sometimes occurs when a surface folds back; while a po int “below”is the nearest point, it may not be an adjacent point.These curves must then be individually and manually selected to define surfaces. Again, care must be taken to ensure that the appropriate surfaces which approximate the original surfaces are formed. After the surfaces are formed, they are connected to form patches or quilts. These quilts are then combined to form a surface model. If the surface model is fully enclosed, the CAD system may then convert it into a shell or solid 3D model.The complexity and shape of the human body also presents problems. Most of the extracted outlines are represented as complicated Bezier curves. A mapping algorithm sometimes fails to combine these Bezier outlines to form 3D data. So, it is necessary that this process be supported by hand [6]. Human supervision is also required where software is unable to recognise features such as joints where bone structures abut. The data must be separated into individual components(disarticulation) in order to evaluate a function (e.g. a jaw joint).Direct interfacing has two major problems. The data from the CT scanner are in the form of shaded images and are automatically segmented. While it is possible to calculate triangles from the images, they do not contain enough surface information. Therefore, it is difficult for the RP system which requires supports to construct the appropriate support structures. Secondly, the interpolation from successive contours obtainedfrom the segmentation is not evident.The CT scanner has a threshold filter to isolate regions within the desired density range. When tissue density ranges across this threshold setting, there are problems in identifying the tissue. For example, for cortical bone (high density) with a structure larger than the voxel dimension, surfaces are well defined and the transitions are easy to recognise. When lowerdensity structures are scanned (cancerous bone) or the structure is so thin that it only partially fills the voxel, the density measured at the surfaces may not surpass the threshold. Consequently, a fixed threshold filter will result in shrinking the structure dimension or creating a void [7], so most research is focused on the STL interface.Virtual prototyping has more applications in biomechanics. CAD systems are used to design prostheses and the simulation and analysis modules are used to help refine the design of the part. Finite-element analysis is a useful tool in the design of load-bearing prostheses such as knees and hips. Kinematics simulation and analysis is applied where the range of movement of the limbs linked by the prostheses is specified. Thermal simulation is not usually carried out as the service condition for the prostheses is an even 37 C.Rapid prototyping parts produced for the prostheses are for the proof of the concept as well as for size estimation. Formfitting or assembly can be done in some cases but is not possible for others such as a ball-socket joint found in a hip prosthesis. For prostheses with moving parts, a rough kinematics check can be performed.5.2 Finite-Element Modelling InvestigationThis case study explores the basic finite-element modeling (FEM) capabilities of VP packages and how corresponding RP parts compare to them. The basis for this study is a knee prosthesis designed by Chow [8]. The prosthesis was designed on Mechanica. The files were exported into IGES format. When retrieved usingPro/ENGINEER Release 15, the surface model was discontinuous and in certain cases, incomplete. (See Figs 7 and 8.) The analysis software used is Ansys version 5.4 by Ansys Inc. The parts were constructed in Pro/ENGINEER Release 15 by Parametric Technology Corporation. Pro/ENGINEER does not have a finite-element modelling module. The RP parts for this study were built on an SLA system. However, Pro/ENGINEER has a FEM post-processor that allows the user to:1. Add or modify finite-element analysis loads or boundary conditions on the model.2. Specify maximum and minimum element sizes for both local and global elements.3. Specify the number of points for the mesh on an edge.4. Set material properties for the model.Pro/ENGINEER can pre-process the part by creating the mesh. The part created in Pro/ENGINEER was then exported to ANSYS using the IGES standard. As the tibial assembly is symmetrical, only half was built and meshed, as shown in Fig. 9.The ability to use a finite-element modelling module or package is highly dependent on the user’s skill and knowledge.The user must be familiar with the concepts and terms used in finite-element modelling.Not all CAD software has an integrated finite-element solver. In these cases, the finite-element package may or may not be able to accept that particular software’s CAD file format.Then, a data exchange format is required such as IGES, DXFor VDA.Data exchange is not the only barrier to the transfer of part data to a finite-element software. Each CAD software system represents the solid models differently. In the construction of the tibia, two geometrically identical parts were produced using different feature-creation techniques. One part could be meshed by Pro/ENGINEER but not by ANSYS; the other could be meshed by both. Again, the user’s judgement is required to avoid such problems.A user’s judgement is also crucial in deciding what features of a part can be safely suppressed to facilitate analysis, but at the same time retain the integrity of the analysis results. Certain geometries and features, especially the intersection of a few edges, can create degeneracies. The solver is unable to createelements or nodes at these degeneracies. Therefore, these degeneracies must be removed. Some finite-element packages allow the editing of the part but some allow only limited editing. The changes then would have to be made in the CAD softwareand then re-exported to the finite-element software. It would take an experienced user to foresee these problems or to identify the problems correctly, and then correct them.The RP model is more useful as a visualising tool. An actual part always gives a better perception of size and shape than an image on a screen. In the case of the knee prosthesis, a rough assembly could be made to see how the femur and the tibial assembly fitted together. In fact, an RP assembly helps in determining the placement of parts in a VP assembly. A rough kinematics check could also be done and the designer is able to assess the part intuitively when simulating the femur sliding against the tibial assembly. The designer can get a “feeling” of whether rocking motion along the axis perpendicular to the sliding motion is possible. While moments can be obtained from a virtual prototype, it does not always show visual clues such as whether a design is ungainly and cumbersome which only a physical prototype can properly exhibit.6. ConclusionRapid prototyping is preferred to VP for kinematic simulation, assembly, fit and interference checking. As a physical part, RP allows the user to gauge the size of the prototype. It is also used for ergonomic and tactile evaluations. Rapid prototyping parts are also used for manufacturing input, usually for a cross-functional team where representatives from all disciplines evaluate the prototype from their own specialist requirements. Most RP parts suffer from mechanical property drawbacks. SLA components are brittle and prone to warpage. The need to build supports in some RP systems also creates problems. In addition, very thin parts cannot be built by some RP systems.Virtual prototyping provides a quick iterative design process, where problems can be rectified immediately whenever indicated from analysis. Solving the problems in the VP domain helps reduce physical prototyping costs and time. Virtual prototyping has high initial investment costs in hardware andsoftware and demands skilled and experienced operators to extract the full benefit from the software. Transfer of data between differing VP systems is poor and vendors often recommend total reconstruction of parts.快速成型与虚拟成型在产品设计和制造中的应用C.K.Chua1, S. H.Tech1,and R.K.Gay1School of Mechanical & Production Engineering; and Gintic Intitute of Manufacturing Techniology,Nanyang Technological University,Singapore引言快速成型是一种从不需任何加工或数控加工程序就得到实体形状的加工过程。
虚拟制造技术内容简介
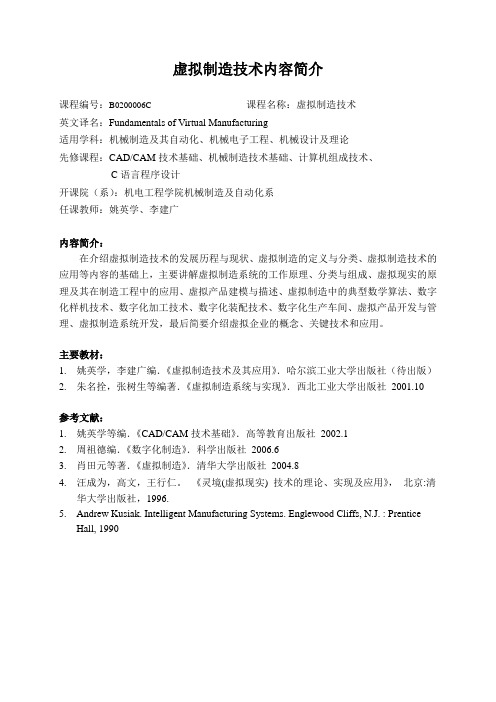
虚拟制造技术内容简介课程编号:B0200006C课程名称:虚拟制造技术英文译名:Fundamentals of Virtual Manufacturing适用学科:机械制造及其自动化、机械电子工程、机械设计及理论先修课程:CAD/CAM技术基础、机械制造技术基础、计算机组成技术、C语言程序设计开课院(系):机电工程学院机械制造及自动化系任课教师:姚英学、李建广内容简介:在介绍虚拟制造技术的发展历程与现状、虚拟制造的定义与分类、虚拟制造技术的应用等内容的基础上,主要讲解虚拟制造系统的工作原理、分类与组成、虚拟现实的原理及其在制造工程中的应用、虚拟产品建模与描述、虚拟制造中的典型数学算法、数字化样机技术、数字化加工技术、数字化装配技术、数字化生产车间、虚拟产品开发与管理、虚拟制造系统开发,最后简要介绍虚拟企业的概念、关键技术和应用。
主要教材:1.姚英学,李建广编.《虚拟制造技术及其应用》.哈尔滨工业大学出版社(待出版)2.朱名拴,张树生等编著.《虚拟制造系统与实现》.西北工业大学出版社2001.10参考文献:1.姚英学等编.《CAD/CAM技术基础》.高等教育出版社2002.12.周祖德编.《数字化制造》.科学出版社2006.63.肖田元等著.《虚拟制造》.清华大学出版社2004.84.汪成为,高文,王行仁。
《灵境(虚拟现实) 技术的理论、实现及应用》,北京:清华大学出版社,1996.5.Andrew Kusiak. Intelligent Manufacturing Systems. Englewood Cliffs, N.J. : PrenticeHall, 1990虚拟制造技术教学大纲课程编号:B0200006C课程名称:虚拟制造技术开课院系:机电工程学院机械制造及自动化系任课教师:姚英学、李建广先修课程:CAD/CAM技术基础、机械制造技术基础、计算机组成技术、C语言程序设计适用学科范围:机械制造及其自动化、机械电子工程、机械设计及理论学时:26 学分:1.5开课学期:春季开课形式:授课+讨论课程目的和基本要求:近年来,信息技术在制造中的应用越来越广泛,本课程是在学生完成计算机基础技术、CAD/CAM技术基础、机械设计制造等相关课程学习的基础上,培养学生综合应用现代信息技术手段解决制造工程领域技术问题能力的重要环节,为学生开展制造业信息化的研究与应用奠定基础。
虚拟制造技术及应用

对虚拟制造技术 的研究正处于不 断的深入 、 细化之中, 因此对 t u a l Wo r k s ; 虚拟制造在汽车生产设备 、 工装和模具, 甚至 校 车
当前 一般 的 定义 是 :虚 拟 制 造 是 实 际 制造 过 程 在 计 算 机 电动 机 车 部 ( Ge n e r a l Mo t o r s E l e c t r o Mo t i v e Di v i s i o n ,E MD ) 上 的映 射 , J 采 用 计算: 机仿真与虚拟现实技术, 在 高 性 能 计 机 及 高 速 网络 的支 持 下 , 在 汁算 机 上 群 组 协 同工 作 , 实现 产 品 机 模 型 , 并 围绕 这 个 数 字 模 型 并 行 地进 行 产 品设 计 、 分析、 制 设 计、 工 艺规 划 、 加工制造、 性能分析、 质 量检 验 , 以及企 业 各 造 、夹模 具 工装 设 计和 可 维 修 性 设 计 。欧 洲 空 中客 车 采 用 虚 级 过程 的管 理 与 控制 等产 品制 造 的本 质 过 程 ,以增 强制 造 过 拟制造及仿真技术 , 把空中客车试制周期从 4 年缩短为 2 . 5 年, 程 各 级 的 决策 与 控 制 能 力 。
汁算机网络和虚拟现实等先进技术 的出现 , 虚拟制造技术应运 而 生, 它的诞生是现代科学技术和生产技术发展的必然结果,
是各 种 现 代制 造 技 术 与 系统 发 展 的 必 然趋 势 。 1 虚 拟 制 造技 术 定 义
3 . 2硬 件 的 有 关技 术 ( 1 ) 输 入 输 出设 备 : 如 头 盔 式 立 体 显 示 器( H MD ) , 适 用 的 汁算 机 屏 幕 、可视 化 眼 镜 , 数 据 手套 、 三 维 鼠标 、 数据 衣 、 游 戏 棒 等 。( 2 ) 与 输 入 和输 出有 关 的存 储 信 息 设 备 。 ( 3 ) 能 支 持 各
特殊应用英文作文高中作文

特殊应用英文作文高中作文1. Virtual Reality。
Virtual reality is a technology that allows users to enter a simulated environment through a headset or other device. It has a wide range of applications, from gaming and entertainment to education and training. With virtual reality, users can interact with a virtual world in a way that feels real, making it a powerful tool for immersive experiences.2. Augmented Reality。
Augmented reality is a technology that overlays digital information onto the real world. It can be used for a variety of purposes, such as enhancing a museum exhibit or providing real-time information about a product. Augmented reality has the potential to revolutionize the way we interact with the world around us, making it more engaging and informative.3. 3D Printing。
3D printing is a technology that allows users to create physical objects from digital designs. It has a wide range of applications, from manufacturing and prototyping to art and design. With 3D printing, users can quickly and easily create custom objects with a high degree of precision, making it a valuable tool for innovation and creativity.4. Artificial Intelligence。
虚拟仪器技术中英文对照外文翻译文献
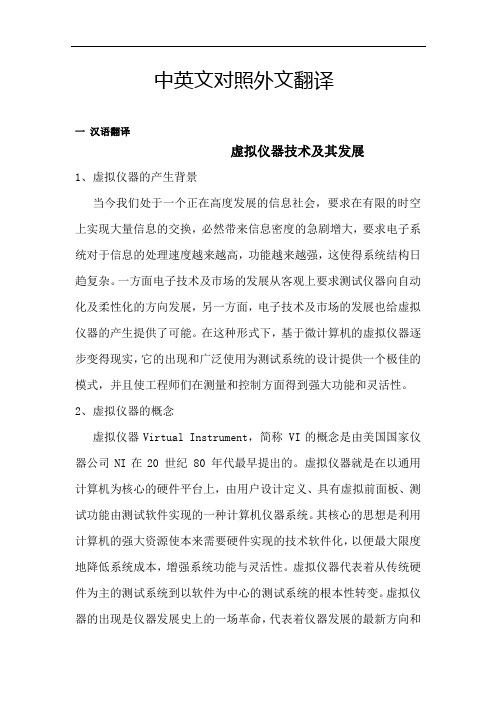
中英文对照外文翻译一汉语翻译虚拟仪器技术及其发展1、虚拟仪器的产生背景当今我们处于一个正在高度发展的信息社会,要求在有限的时空上实现大量信息的交换,必然带来信息密度的急剧增大,要求电子系统对于信息的处理速度越来越高,功能越来越强,这使得系统结构日趋复杂。
一方面电子技术及市场的发展从客观上要求测试仪器向自动化及柔性化的方向发展,另一方面,电子技术及市场的发展也给虚拟仪器的产生提供了可能。
在这种形式下,基于微计算机的虚拟仪器逐步变得现实,它的出现和广泛使用为测试系统的设计提供一个极佳的模式,并且使工程师们在测量和控制方面得到强大功能和灵活性。
2、虚拟仪器的概念虚拟仪器Virtual Instrument,简称 VI的概念是由美国国家仪器公司NI在20 世纪 80 年代最早提出的。
虚拟仪器就是在以通用计算机为核心的硬件平台上,由用户设计定义、具有虚拟前面板、测试功能由测试软件实现的一种计算机仪器系统。
其核心的思想是利用计算机的强大资源使本来需要硬件实现的技术软件化,以便最大限度地降低系统成本,增强系统功能与灵活性。
虚拟仪器代表着从传统硬件为主的测试系统到以软件为中心的测试系统的根本性转变。
虚拟仪器的出现是仪器发展史上的一场革命,代表着仪器发展的最新方向和潮流,对科学技术的发展和工业生产的进步将产生不可估量的影响。
虚拟仪器具有性能高、扩展性强、开发时间短、无缝集成等优势。
3.图形化虚拟仪器开发平台—LABVIEW 简介及其优势LABVIEW 是Laboratory Virtual Instrument Engineering Workbench 实验室虚拟仪器集成开发环境的简称,是由美国国家仪器公司National instruments IN创立的一个功能强大而又灵活的仪器和分析应用开发工具。
Labview 一种图形化的编程语言,主要用来开发数据采集,仪器控制及数据处理分析等软件,功能强大。
目前,该开发软件在国际测试、测控行业比较流行,在国内的测控领域也得到广泛应用。
- 1、下载文档前请自行甄别文档内容的完整性,平台不提供额外的编辑、内容补充、找答案等附加服务。
- 2、"仅部分预览"的文档,不可在线预览部分如存在完整性等问题,可反馈申请退款(可完整预览的文档不适用该条件!)。
- 3、如文档侵犯您的权益,请联系客服反馈,我们会尽快为您处理(人工客服工作时间:9:00-18:30)。
附录1 外文译文虚拟制造技术及其应用摘要:阐述了虚拟制造的基本概念,虚拟制造的核心技术,以及虚拟制造技术应用。
关键词:制造业虚拟制造虚拟现实0 引言当今的制造业基本技术日臻成熟,其市场处于以消费者为导向的市场环境下,产品品种、上市时间和用户满意度成为企业取得竞争优势的主要因素。
制造业这种全球化的激烈竞争不断催生了各种先进制造技术和新的制造哲理,虚拟制造技术将会在本世纪涌向潮头,其朴素的思想和高新的技术手段都为研究领域和业界所推崇。
虚拟制造就是根据企业市场竞争的需求,在强调柔性和快速的前提下,美国80年代提出的,随着计算机技术和信息网络技术的发展,在90年代得到人们的重视,并获得迅速的发展。
1 虚拟制造虚拟制造的基本思想是在产品制造过程的上游——设计阶段就进行对产品制造全过程的虚拟集成,将全阶段可能出现的问题解决在这一阶段,通过设计的最优化达到产品的一次性制造成功。
虚拟现实技术是使用感官组织仿真设备的真实或虚幻环境的动态模型生成或创造出人能够感知的环境或现实,使人能够凭借直觉作用于计算机产生的三维仿真模型的虚拟环境。
基于虚拟现实技术的虚拟制造技术在一个统一模型之下对设计和制造等过程集成,它将与产品制造相关的各种过程与技术集成在三维的、动态的仿真真实过程的实体数字模型之上。
其目的是在产品设计阶段,借助建模与仿真技术及时地、并行地、模拟出产品未来制造过程乃至产品全生命周期的各种活动对产品设计的影响,预测、检测、评价产品性能和产品的可制造性等等。
从而更加有效的、经济的、柔性的组织生产,增强决策与控制水平,有力地降低由于前期设计给后期制造带来的回溯更改,达到产品的开发周期和成本最小化、产品设计质量的最优化、生产效率的最大化。
虚拟制造系统是各制造功能的虚拟集成,它的可视化集成范围包括与设计相关的各项子系统的功能,如用户支持、工程分析、材料选用、工艺计划、工装分析、快速原型,甚至包括制造企业全部功能(如计划、操作、控制)的集成。
虚拟制造系统拥有产品和相关制造过程的全部信息,包括虚拟设计、制造和控制产生的数据、知识和模型信息。
虚拟控制制造系统按照功能归集为三种不同类型的子环境,共同构成中心三元耦合的系统模式:(1)虚拟制造设计中心:给设计者提供各种工具以便虚拟设计、虚拟制造,设计出符合设计准则(如DFX)的产品模型;(2)虚拟制造加工中心:研究开发产品制造过程模型和环境模型及其分析各种可行的生产计划和工艺规划;(3)虚拟制造控制中心:评价产品设计、产品原型、生产计划、制造模拟和控制策略等等。
2 虚拟制造技术支持虚拟制造技术是多学科综合的系统技术,需要研究开发相应的硬件集成系统与软件,就软件技术而言,相关的研究支持如下:可视化:真实、直观地再现主观产品与客观制造过程;基本环境:增强可视化和其它虚拟制造功能的集成系统平台;信息描述:表达各种信息,包括数据、知识和模型的统一的方法、语义、语法;中介模型:构造、定义、开发对过程易于中断介入的模型;基层集成组织结构:硬件与软件的基层组织结构;仿真模型:在计算机系统中设计的真实系统模型;应用方法:产品多样性与过程动态性的共同特征的抽象提取;制造特征:各种材料在虚拟制造环境中的变化过程;虚拟制造系统评价:可制造性、工艺性、可靠性、经济性、质量、工期等等。
2.1建模技术虚拟制造系统是现实制造系统在虚拟环境下的映射,是RMS的模型化、形式化和计算机化的抽象描述和表示。
VMS的建模应包括:生产模型、产品模型和工艺模型的信息体系结构。
(1)生产模型归纳为静态描述和动态描述两个方面。
静态描述是指系统生产能力和生产特性的描述。
动态描述是指在已知系统状态和需求特性的基础上预测产品生产的全过程。
(2)产品模型是制造过程中,各类实体对象模型的集合。
对VMS来说,要使产品实施过程中的全部活动集成,就必须具有完备的产品模型,所以虚拟制造下的产品模型不再是单一的静态特征模型,它能通过映射、抽象等方法提取产品实施中各活动所需的模型。
(3)工艺模型将工艺参数与影响制造功能的产品设计属性联系起来,反应生产模型与产品模型之间的交互作用。
工艺模型必须具备以下功能:计算机工艺仿真、制造数据表、制造规划、统计模型以及物理和数学模型。
2.2仿真技术仿真就是应用计算机对复杂的现实系统经过抽象和简化形成系统模型,然后在分析的基础上运行此模型,从而得到系统一系列的统计性能。
仿真的基本步骤为:研究系统——收集数据——建立系统模型——确定仿真算法——建立仿真模型——运行仿真模型——输出结果并分析。
产品制造过程仿真,可归纳为制造系统仿真和加工过程仿真。
虚拟制造系统中的产品开发涉及到产品建模仿真、设计过程规划仿真、设计思维过程和设计交互行为仿真等,以便对设计结果进行评价,实现设计过程早期反馈,减少或避免产品设计错误。
加工过程仿真,包括切削过程仿真、装配过程仿真,检验过程仿真以及焊接、压力加工、铸造仿真等。
目前上述两类仿真过程是独立发展起来的,尚不能集成,而VM中应建立面向制造全过程的统一仿真。
2.3虚拟现实技术虚拟现实技术是在为改善人与计算机的交互方式,提高计算机可操作性中产生的,它是综合利用计算机图形系统、各种显示和控制等接口设备,在计算机上生成可交互的三维环境(称为虚拟环境)中提供沉浸感觉的技术。
由图形系统及各种接口设备组成,用来产生虚拟环境并提供沉浸感觉,以及交互操作的计算机系统称为虚拟现实系统。
虚拟现实系统包括操作者、机器和人机接口3个基本要素。
利用VRS可以对真实世界进行动态模似,通过用户的交互输入,并及时按输出修改虚拟环境,使人产生身临其境的沉浸感觉。
虚拟现实技术是VM的关键技术之一。
3 VM在制造业中应用虽然在产品开发过程中应用建模和仿真可以大大缩短开发周期,改进产品的性能和可靠性,但在工业界的设计过程中实际应用并不多。
目前的仿真系统还不能适应工业界在设计过程中进行分析和验证等的要求。
高级工程仿真系统应具有下列特点:三维的复杂零件”零件接口;本质上不同响应特性的多元材料;材料重要的非线性性质,诸如:非牛顿行为、塑料变形、断裂;多相现象;带有化学反应的多相能量转移;移动或自由边界;非线性动力学。
在以模型为基础的设计中,实现高级工程仿真的关键技术可归纳如下:用户接口;分析式立体造型;对壳体和实体的先进网格生成算法(有限元分析用);解的误差分析和改进;材料模型;优化目标函数的设计;面向对象的软件工程;海量并行计算;可视化。
把这些技术集成起来,可以帮助设计者进行设计,了解设计出来的产品的性能。
应用上述先进的网格生成算法、误差分析及计算,可组成自适应算法,使仅懂得机构、不懂得分析的设计者也能设计产品及设计这一产品的制造过程。
自适应能力可以保证分析的精度。
由于重要的几何性质可以参数化,因此可以进行形状的优化等。
虚拟制造技术首先在飞机、汽车等领域获得成功的应用。
目前VMT应用在以下几个方面:3.1虚拟企业虚拟企业建立,其中有一条最重要的原因是因为各企业本身无法单独满足市场需求,迎接市场挑战。
因此,为了快速响应市场的需求,围绕新产品开发,利用不同地域的现有资源、不同的企业或不同地点的工厂,重新组织一个新公司。
该公司在运行之前,必须分析组合是否最优,能否协调运行,并对投产后的风险、利益分配等进行评估。
这种联作公司称为虚拟公司,或者叫作动态联盟,是一种虚拟企业,它具有集成性和实效性两大特点的经济实体。
3.2虚拟产品设计例如飞机、汽车的外形设计,其形状是否符合空气动力学原理,运动过程中的阻力,其内部结构布局的合理性等。
在复杂管道系统设计中,采用虚拟技术,设计者可以”进入其中0进行管道布置,并可检查能否发生干涉。
在计算机上的虚拟产品设计,不但能提高设计效率,而且能尽早发现设计中的问题,从而优化产品的设计。
例如美国波音公司投资40亿美元研制波音777喷气式客机,从1990年10月开始到1994年6月仅用了3年零8个月时间就完成了研制,一次试飞成功,投入运营。
波音公司分散在世界各地的技术人员可以从777客机数以万计的零部件中调出任何一种在计算机上观察、研究、讨论,所有零部件均是三维实体模型。
可见虚拟产品设计给企业带来的效益。
3.3虚拟产品制造应用计算机仿真技术,对零件的加工方法、工序顺序、工装的选用、工艺参数的选用,加工工艺性、装配工艺性、配合件之间的配合性、连接件之间的连接性、运动构件的运动性等均可建模仿真,可以提前发现加工缺陷,提前发现装配时出现的问题,从而能够优化制造过程,提高加工效率。
3.4虚拟生产过程产品生产过程的合理制定、人力资源、制造资源、物料库存、生产调度、生产系统的规划设计等,均可通过计算机仿真进行优化,同时还可对生产系统进行可靠性分析,对生产过程的资金进行分析预测,对产品市场进行分析预测等,从而对人力资源、制造资源的合理配置,对缩短产品生产周期,降低成本意义重大。
4 虚拟制造系统体系结构CIM集成是通过物理的、逻辑的联系以便在制造设备之间传递信号,以庞大的信息流为“网线”粘连起企业活动的全部活动“节点”,共同浇结成一整块“企业机器”,实际上从各个方面降低了企业的柔性。
而虚拟制造则完全是数字模型的集成,提供了有别于CIMS“物理集成”的虚拟集成方案,将相互孤立的制造技术如CAD、CAM、CAPP等等集成在一个虚拟产品制造环境下,以现实对制造过程的一一对应的模型化映射关系,它相对于物理世界有功能一致性、结构相似性的特点,是对实体制造企业的产品、作业、环境及其评价行为等等四个特征的虚拟实现。
虚拟现实技术应用于现在的制造系统如CAD、CAPP、CAM,能够大大增强各个子系统之间的协调与并行。
面向模型集成各个子系统功能是虚拟制造技术的关键之一,由于产品的多样性与制造过程的动态性,虚拟制造环境是一个动态多变的集成环境,其过程会产生大量的各种数据,虚拟过程的数据管理变得非常复杂。
面向产品与过程的虚拟制造系统需要对产品、作业、环境和评价的数据、知识、模型进行共同特征抽取与异型制造过程创建。
拟实制造的基础是对制造过程(即把各种材料变成产品的过程)的理论和方法进行深入的了解。
有了这些了解,才有可能在计算机上进行拟实制造,从而揭示一个产品制造全过程的种种复杂问题。
随着拟实制造的发展,它将为工程师们提供一个从产品的概念形成、设计、制造到实现的全过程三维可视及交互的环境;它将促使实现制造驱动设计,要求设计者在设计阶段把一个产品的构思、设计、制造统统考虑好。
目前,电子类产品,特别是大规模集成电路,相对地比机械类产品简单,制造过程具有通用性,发展得较成熟;机械类产品相对较复杂,进展得较慢。
另外,拟实制造的实现是建筑在一个企业内外实行计算机集成基础上的,只有在大范围采用计算机集成后,才能有效地实行拟实制造,并在这基础上过渡到敏捷制造时代。