304不锈钢焊接热裂的原因及解决方法
各种焊接裂纹成因特点及防止措施这条必须收藏了

各种焊接裂纹成因特点及防止措施这条必须收藏了焊接是一种常见的连接工艺,但焊接过程中容易产生焊接裂纹。
为了提高焊接质量,减少焊接裂纹的产生,需要了解不同焊接裂纹的成因特点,并采取相应的防止措施。
焊接裂纹可分为热裂纹、冷裂纹和固化裂纹等不同类型。
下面将就各种焊接裂纹的成因特点及防止措施进行介绍:1.热裂纹:热裂纹是由于焊接过程中材料受热引起的裂纹。
其特点是呈现出明显的沿晶裂纹特征,并且易于在焊接接头中形成交叉网络裂纹。
常见的热裂纹包括低温热裂纹和高温热裂纹。
低温热裂纹通常发生在焊接高碳钢、不锈钢、铝合金等材料时,主要原因是在焊接过程中产生的低熔点物质(如非金属夹杂物、硫化物)会导致裂纹的形成。
因此,防止低温热裂纹的关键在于降低焊接接头中的夹杂物含量,控制焊接温度和速度,使用合适的焊接电流和电压等。
高温热裂纹主要发生在焊接高强度钢、铝合金等材料时,其主要原因是焊接接头中的合金元素偏析或金属在焊接中的高温下形成致密的化合物,导致焊接接头发生脆性断裂。
预热和后热处理是防止高温热裂纹的常用方法,通过控制焊接温度梯度和应力,避免裂纹的生成。
2.冷裂纹:冷裂纹是焊接接头在冷却过程中产生的裂纹,主要由于焊接接头的收缩应力超过了材料的塑性变形能力而引起。
冷裂纹通常呈现出沿晶和剥离两种形态。
冷裂纹的形成与焊接材料的化学成分、焊接参数(如预热温度、焊接电流和速度等)、接头几何形状和约束条件等因素密切相关。
为防止冷裂纹的产生,可以采取增加预热温度和焊接层间温度、降低残余应力、使用低氢焊条或填充剂等措施。
3.固化裂纹:固化裂纹是焊接过程中焊缝和熔敷金属中的液态组织在冷却过程中发生凝固收缩而产生的裂纹。
固化裂纹主要由于焊接接头中的组织偏析、组织转变和凝固缩短等因素导致。
防止固化裂纹的关键是通过合理的焊接参数、选择合适的填充材料和焊接序列等措施控制焊接缩短率,减少焊接接头中的温度梯度和残余应力。
总之,了解不同焊接裂纹的成因特点并采取相应的防止措施对于提高焊接质量具有重要意义。
不锈钢封头开裂分析及对策
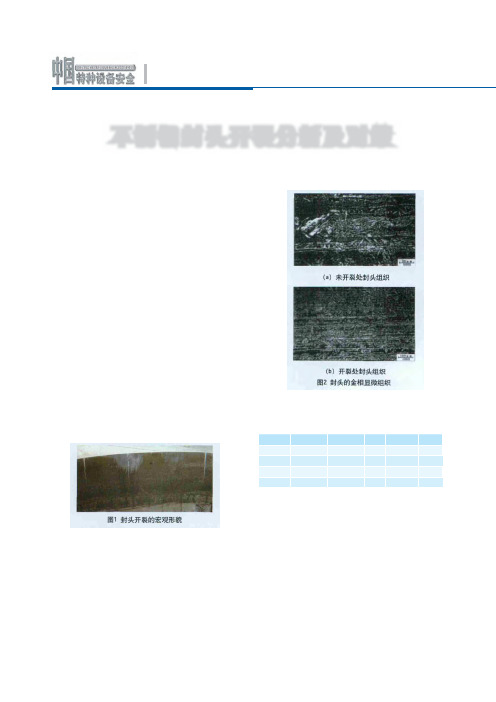
不锈钢封头开裂分析及对策支泽林 王富岐 陕西省锅炉压力容器检验所某封头厂受压力容器制造厂委托,压制了8张材料牌号为304奥氏体不锈钢椭圆型封头。
经检查,钢板规格为6000×1500×10mm和6400×1800×10mm,坯料直径、外观质量,均满足成型要求。
封头厂采用两次冷拉伸成型工艺,在2010年2月7日前压制完毕并进行了切边,同时对成型后的封头进行了外观、形状、几何尺寸等检查,未见异常,遂被制造厂运走。
在2010年2月12日后,发现封头在直边和圆弧部位沿垂直于封头端面方向上均出现了开裂,长度约30~200mm,裂缝都为穿透性开裂,其中有一个封头出现了20多处。
304奥氏体不锈钢压制封头较普遍,但开裂情况较罕见。
为此,本文针对304奥氏体不锈钢封头失效情况进行分析,找出开裂产生的原因和失效机理,提出解决对策。
1 检查与试验取封头直边和圆弧部位沿开裂处,进行光谱分析、力学性能、弯曲性能和金相分析。
1.1 封头开裂的宏观形貌封头的材料为304,规格为φ1500×8m m 和φ1400×8mm,封头开裂的宏观形貌如图1所示。
图1 封头开裂的宏观形貌1.2 封头材料化学成分对封头开裂和未开裂部位进行光谱分析,其化学成分满足GB24511-95的标准要求。
1.3 金相分析封头开裂部位和未开裂部位金相组织如图2所示,可以看出,两个部位的金相组织均为奥氏体和形变马氏体,晶粒度6~7级,清晰可见。
压制前金相组织应该是奥氏体(含孪晶)+碳化物+少量铁素体。
(a)未开裂处封头组织(b)开裂处封头组织图2 封头的金相显微组织1.4 力学性能分析力学性能试验结果见表1。
表1 力学性能根据GB/T4237-2007,R m ≥520、R p0.2≥206、A ≥40%、力学性能符合标准。
2 结果讨论2.1 材料分析经原厂家提供的《产品质量证明书》表明交货状态为:固溶、酸洗、热轧。
不锈钢开裂补焊方法
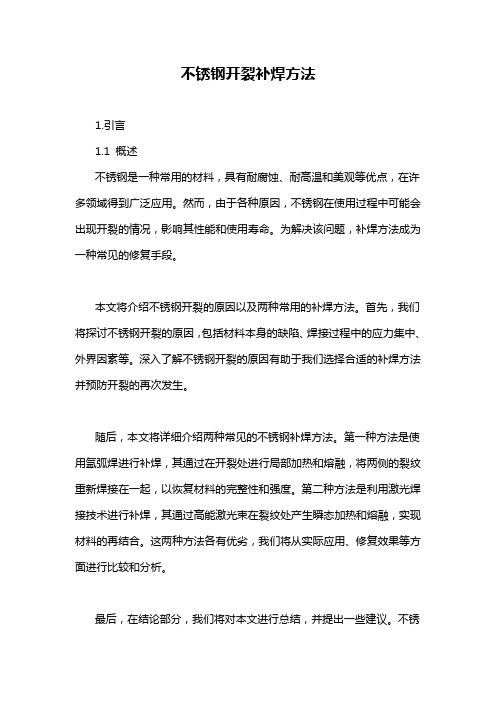
不锈钢开裂补焊方法1.引言1.1 概述不锈钢是一种常用的材料,具有耐腐蚀、耐高温和美观等优点,在许多领域得到广泛应用。
然而,由于各种原因,不锈钢在使用过程中可能会出现开裂的情况,影响其性能和使用寿命。
为解决该问题,补焊方法成为一种常见的修复手段。
本文将介绍不锈钢开裂的原因以及两种常用的补焊方法。
首先,我们将探讨不锈钢开裂的原因,包括材料本身的缺陷、焊接过程中的应力集中、外界因素等。
深入了解不锈钢开裂的原因有助于我们选择合适的补焊方法并预防开裂的再次发生。
随后,本文将详细介绍两种常见的不锈钢补焊方法。
第一种方法是使用氩弧焊进行补焊,其通过在开裂处进行局部加热和熔融,将两侧的裂纹重新焊接在一起,以恢复材料的完整性和强度。
第二种方法是利用激光焊接技术进行补焊,其通过高能激光束在裂纹处产生瞬态加热和熔融,实现材料的再结合。
这两种方法各有优劣,我们将从实际应用、修复效果等方面进行比较和分析。
最后,在结论部分,我们将对本文进行总结,并提出一些建议。
不锈钢开裂问题对许多行业都具有一定的影响,因此,我们需要加强对材料质量的控制和焊接工艺的改进,以减少不锈钢开裂的发生。
同时,在补焊过程中,应根据具体情况选择合适的补焊方法,并结合预防措施,提高不锈钢的使用寿命和性能。
通过本文的阐述,相信读者能够更好地了解不锈钢开裂补焊方法,并在实际应用中做到理论与实践相结合,为相关行业的发展和生产提供有益的参考。
1.2 文章结构文章结构的设计是为了使读者能够清晰地了解整篇文章的框架和内容安排。
本文将按照下述结构进行分析和论述:2.正文:2.1 不锈钢开裂的原因2.2 补焊方法一2.3 补焊方法二2.1 不锈钢开裂的原因在这一部分,我们将详细探讨导致不锈钢开裂的可能原因。
不锈钢是一种耐腐蚀材料,但在特定条件下仍可能发生开裂现象。
我们将介绍热裂纹和冷裂纹两种常见的开裂形式,并深入分析它们的成因。
同时,我们会探讨一些特殊情况下引起开裂的特殊因素。
焊接产生裂纹的原因

焊接产生裂纹的原因焊接是一种常见的金属连接方法,它通常用于制造和维修工业部件。
然而,焊接过程中经常会出现裂纹,对焊接接头的强度和可靠性产生负面影响。
本文将探讨焊接产生裂纹的原因,并提供一些预防措施和解决方法。
1. 温度梯度引起的热应力焊接过程中,焊接区域会受到局部加热和快速冷却的影响,导致温度梯度的存在。
这种温度梯度会引起金属的热应力,使焊接接头产生裂纹。
解决方法:•控制焊接过程中的局部预热和退火,使温度梯度减小。
•使用预热设备在焊接区域加热,使温度分布更均匀。
•合理选择焊接电流和速度,避免出现过大的温度梯度。
2. 结构应力引起的裂纹焊接接头通常会承受结构应力,如拉伸、挤压或弯曲力。
由于焊接引起的组织和性能变化,焊接接头在受到结构应力时容易产生裂纹。
解决方法:•选择合适的焊接方法和焊接接头结构,减少结构应力对焊接接头的影响。
•优化焊接参数,使焊接接头的强度与结构应力相匹配。
•进行后焊热处理,提高焊接接头的强度和韧性。
3. 金属材料的选择和准备焊接材料的选择和准备对焊接接头的质量有重要影响。
不同材料的熔点、热膨胀系数和焊接性能不同,可能导致焊接接头产生裂纹。
解决方法:•选择合适的焊接材料,使其熔点和热膨胀系数与基材相匹配。
•对焊接材料进行预处理,去除氧化物和杂质,提高焊接接头的强度和韧性。
•使用合适的焊接方法和技术,确保焊接材料在焊接过程中融合良好。
4. 不适当的焊接参数和工艺焊接参数和工艺的选择对焊接接头的质量和裂纹的形成有重要影响。
过高或过低的焊接电流、电压、焊接速度和功率都可能导致焊接接头产生裂纹。
解决方法:•根据焊接材料的特性和焊接要求,选择合适的焊接参数。
•进行焊接试验和质量控制,确保焊接接头达到预期的质量要求。
•遵循正确的焊接工艺和操作规程,保证焊接接头的质量和强度。
5. 应力集中和裂纹敏感区域焊接接头通常存在着应力集中和裂纹敏感区域,这些区域容易产生裂纹。
焊接过程中的热收缩和组织变化可能导致焊接接头的应力集中和裂纹敏感性增加。
焊接热裂纹的产生原因及防止方法
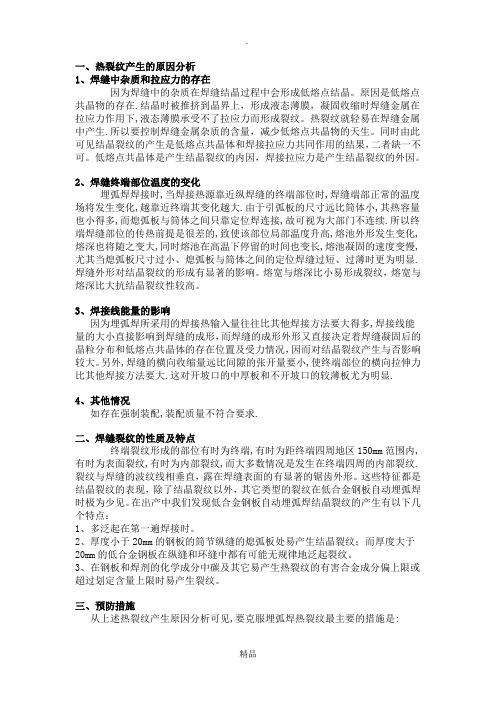
一、热裂纹产生的原因分析1、焊缝中杂质和拉应力的存在因为焊缝中的杂质在焊缝结晶过程中会形成低熔点结晶。
原因是低熔点共晶物的存在.结晶时被推挤到晶界上,形成液态薄膜,凝固收缩时焊缝金属在拉应力作用下,液态薄膜承受不了拉应力而形成裂纹。
热裂纹就轻易在焊缝金属中产生.所以要控制焊缝金属杂质的含量,减少低熔点共晶物的天生。
同时由此可见结晶裂纹的产生是低熔点共晶体和焊接拉应力共同作用的结果,二者缺一不可。
低熔点共晶体是产生结晶裂纹的内因,焊接拉应力是产生结晶裂纹的外因。
2、焊缝终端部位温度的变化埋弧焊焊接时,当焊接热源靠近纵焊缝的终端部位时,焊缝端部正常的温度场将发生变化,越靠近终端其变化越大.由于引弧板的尺寸远比筒体小,其热容量也小得多,而熄弧板与筒体之间只靠定位焊连接,故可视为大部门不连续.所以终端焊缝部位的传热前提是很差的,致使该部位局部温度升高,熔池外形发生变化,熔深也将随之变大,同时熔池在高温下停留的时间也变长,熔池凝固的速度变慢,尤其当熄弧板尺寸过小、熄弧板与筒体之间的定位焊缝过短、过薄时更为明显. 焊缝外形对结晶裂纹的形成有显著的影响。
熔宽与熔深比小易形成裂纹,熔宽与熔深比大抗结晶裂纹性较高。
3、焊接线能量的影响因为埋弧焊所采用的焊接热输入量往往比其他焊接方法要大得多,焊接线能量的大小直接影响到焊缝的成形,而焊缝的成形外形又直接决定着焊缝凝固后的晶粒分布和低熔点共晶体的存在位置及受力情况,因而对结晶裂纹产生与否影响较大。
另外,焊缝的横向收缩量远比间隙的张开量要小,使终端部位的横向拉伸力比其他焊接方法要大.这对开坡口的中厚板和不开坡口的较薄板尤为明显.4、其他情况如存在强制装配,装配质量不符合要求.二、焊缝裂纹的性质及特点终端裂纹形成的部位有时为终端,有时为距终端四周地区150mm范围内,有时为表面裂纹,有时为内部裂纹,而大多数情况是发生在终端四周的内部裂纹.裂纹与焊缝的波纹线相垂直,露在焊缝表面的有显著的锯齿外形。
不锈钢焊缝裂纹产生的原因的重新陈述

不锈钢焊缝裂纹产生的原因的重新陈述不锈钢焊缝裂纹产生的原因的重新陈述在不锈钢焊接过程中,焊缝裂纹的产生是一个常见的问题。
虽然在之前的文章中已经探讨过这个主题,但现在我将重新陈述关于不锈钢焊缝裂纹产生原因的深入讨论。
我将从多个方面分析这个问题,以便我们更全面地理解不锈钢焊缝裂纹产生的原因。
1. 焊接材料选择不当:不锈钢焊缝裂纹的产生可以归因于焊接材料的选择不当。
不同等级的不锈钢具有不同的化学成分和热处理特性,因此选择合适的焊接材料对于避免焊缝裂纹至关重要。
当焊接材料的化学成分与母材不匹配时,焊缝裂纹的风险就会增加。
2. 母材的应力集中:母材中的应力集中也是导致不锈钢焊缝裂纹产生的原因之一。
当焊接过程中施加的热应力与存在的局部应力相结合时,焊缝周围的母材就会受到更大的应力,从而增加了焊缝裂纹的形成风险。
3. 焊接过程的热控制不当:热控制是焊接过程中至关重要的方面。
不当的热输入或冷却速度可能导致焊缝区域的热循环不均匀,从而引发焊缝裂纹。
热输入过高可能导致焊缝区域过热,而热输入过低则可能导致冷凝速度过快,这两种情况都会增加焊缝裂纹的风险。
4. 焊接残余应力:焊接过程中产生的残余应力也是不锈钢焊缝裂纹产生的原因之一。
焊接会改变材料的晶体结构并引入残余应力,当这些应力超过材料的强度极限时,焊缝裂纹可能会出现。
5. 焊接操作技术不当:不正确的焊接操作技术也会导致焊缝裂纹的形成。
这包括焊接速度、焊接电流和焊接电压的控制不当,以及不适当的焊接角度和焊接位置等因素。
这些技术问题可能会导致焊接过程中的应力不均匀,从而引发焊缝裂纹。
不锈钢焊缝裂纹的产生是由多种因素共同作用导致的。
正确选择焊接材料、控制焊接过程中的热量和应力、遵循正确的焊接操作技术等都是避免焊缝裂纹的关键。
只有全面理解这些原因,我们才能更好地避免不锈钢焊缝裂纹的产生,并确保焊接质量的稳定性和可靠性。
我对这个问题的理解是,不锈钢焊缝裂纹产生的原因是一个复杂且多方面的问题。
电焊开裂整改方案
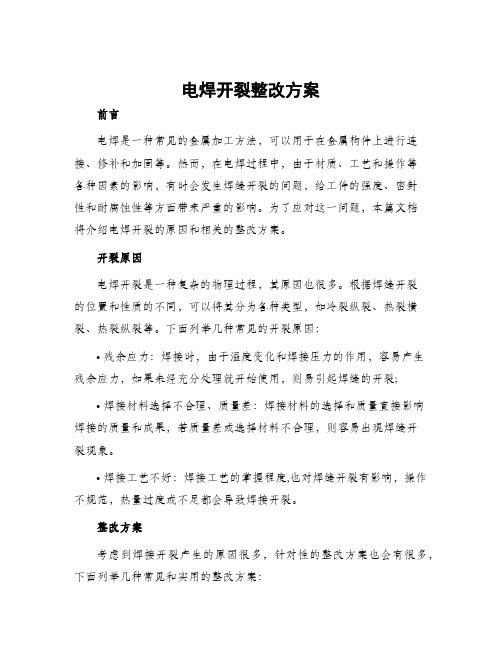
电焊开裂整改方案前言电焊是一种常见的金属加工方法,可以用于在金属构件上进行连接、修补和加固等。
然而,在电焊过程中,由于材质、工艺和操作等各种因素的影响,有时会发生焊缝开裂的问题,给工件的强度、密封性和耐腐蚀性等方面带来严重的影响。
为了应对这一问题,本篇文档将介绍电焊开裂的原因和相关的整改方案。
开裂原因电焊开裂是一种复杂的物理过程,其原因也很多。
根据焊缝开裂的位置和性质的不同,可以将其分为各种类型,如冷裂纵裂、热裂横裂、热裂纵裂等。
下面列举几种常见的开裂原因:•残余应力:焊接时,由于温度变化和焊接压力的作用,容易产生残余应力,如果未经充分处理就开始使用,则易引起焊缝的开裂;•焊接材料选择不合理、质量差:焊接材料的选择和质量直接影响焊接的质量和成果,若质量差或选择材料不合理,则容易出现焊缝开裂现象。
•焊接工艺不好:焊接工艺的掌握程度,也对焊缝开裂有影响,操作不规范,热量过度或不足都会导致焊接开裂。
整改方案考虑到焊接开裂产生的原因很多,针对性的整改方案也会有很多,下面列举几种常见和实用的整改方案:1. 严格控制操作规程焊接工作一定要按照操作规程进行,实现“三看,四验,五控制”(看材料看工具看操作位置,验质量和尺寸,控制温度和热量等),确保焊接质量的稳定和控制。
2. 质量管理与控制加强钢材的入库检验,对于质量不好的焊接材料,立即停用。
每一批焊接材料均要有入库单、出库单进行信息监控,对于不合格产品及时进行淘汰。
同时,对焊缝进行全面、严格的检验,并建立检测档案,做到每炉焊接成果都有质量记录。
3. 合适的焊接材料的使用使用合适质量又合适规格的物料,一方面保证了施工的安全稳定,另一方面,使得进行焊接时浪费的材料减少,避免需要不合理的加工处理。
采用可靠的品牌物料,这种材料具有更好的性能和更佳的合金配方,由于使用可靠性更强,按钮更长。
4. 严格控制焊接工艺确保焊接温度合适,势充分,保证其熔化,可将材料焊在一起,减少了孔洞,坚决停止还手一些不合理的焊接工艺,例如“拼接熔化”,坚决避免出现加热过程不均相关问题。
304不锈钢焊接热裂的原因及解决方法

304不锈钢焊接热裂的原因及解决方法本页仅作为文档封面,使用时可以删除This document is for reference only-rar21year.March一、304不锈钢是奥氏体不锈钢,相当于1Cr19Ni9.SUS304不锈钢是0Gr18Ni9的材质,产生热裂纹的可能性比较大,奥氏体不锈钢有一个特点:他在900多度以上时是奥氏体,900多度以下至600多度时是马氏体,温度继续下降,就又转变为奥氏体。
焊接时接口开裂就是在马氏体阶段开裂的。
解决的方法:减小一下焊接时的热输入量,加大焊后水冷却的工艺,使其在马氏体阶段的时间缩短,避免焊件在敏感的温度区间停留,接口就不会裂了。
二、不锈钢的焊接1、奥氏体不锈钢的焊接不锈钢是不锈钢和耐酸钢的总称,钢中所加合金元素在10%(质量分数)以上,属于高合金钢。
它包括奥氏体型、马氏体型、铁素体型、奥氏体-马氏体型和沉淀硬化型五类。
焊接奥氏体不锈钢(0Cr18Ni9、00Cr18Ni9、0Cr18Ni12Mo2、00Cr18 Ni12Mo2、0Cr18Ni9Ti、1Cr18Ni9Ti、1Cr18Ni12Mo3Ti等)主要问题是热裂纹――焊接过程中,焊缝和热影响区金属冷却到固相线附近的高温区所产生的焊接热裂纹、脆化、晶间腐蚀――沿金属晶粒边界发生的腐蚀破坏现象。
和应力腐蚀开裂――金属材料(包括焊接接头)在一定温度下受腐蚀介质和拉应力的共同作用而产生的裂纹。
此外,因导热性差,线膨胀系数大,焊接变形也大。
1)热裂纹与结构钢相比,它的热裂纹倾向较大,在焊缝及热影响区均可能出现热裂纹。
最常见的是焊缝结晶裂纹--在焊缝凝固过程的后期所形成的焊接裂纹,时在热影响区和多层焊层间还会出现液化裂纹。
含镍量越高,产生热烈倾向越大,而且越不容易控制。
;防止措施:a.严格限制硫、磷等杂质的含量。
b.调整焊缝金属组织,以奥氏体为主的γ+δ双相组织具有良好抗裂性。
c.调整焊缝金属合金成分,在单相稳定奥氏钢中适当增加锰、碳、氮的含量。
- 1、下载文档前请自行甄别文档内容的完整性,平台不提供额外的编辑、内容补充、找答案等附加服务。
- 2、"仅部分预览"的文档,不可在线预览部分如存在完整性等问题,可反馈申请退款(可完整预览的文档不适用该条件!)。
- 3、如文档侵犯您的权益,请联系客服反馈,我们会尽快为您处理(人工客服工作时间:9:00-18:30)。
一、304不锈钢就是奥氏体不锈钢,相当于1Cr19Ni9、
SUS304不锈钢就是0Gr18Ni9的材质,产生热裂纹的可能性比较大,奥氏体不锈钢有一个特点:她在900多度以上时就是奥氏体,900多度以下至600多度时就是马氏体,温度继续下降,就又转变为奥氏体。
焊接时接口开裂就就是在马氏体阶段开裂的。
解决的方法:减小一下焊接时的热输入量,加大焊后水冷却的工艺,使其在马氏体阶段的时间缩短,避免焊件在敏感的温度区间停留,接口就不会裂了。
二、不锈钢的焊接
1、奥氏体不锈钢的焊接
不锈钢就是不锈钢与耐酸钢的总称,钢中所加合金元素在10%(质量分数)以上,属于高合金钢。
它包括奥氏体型、马氏体型、铁素体型、奥氏体-马氏体型与沉淀硬化型五类。
焊接奥氏体不锈钢(0Cr18Ni9、00Cr18Ni9、0Cr18Ni12Mo2、0 0Cr18Ni12Mo2、0Cr18Ni9Ti、1Cr18Ni9Ti、1Cr18Ni12Mo3Ti 等)主要问题就是热裂纹――焊接过程中,焊缝与热影响区金属冷却到固相线附近的高温区所产生的焊接热裂纹、脆化、晶间腐蚀――沿金属晶粒边界发生的腐蚀破坏现象。
与应力腐蚀开裂――金属材料(包括焊接接头)在一定温度下受腐蚀介质与拉应力的共同作用而产生的裂纹。
此外,因导热性差,线膨胀系数大,焊接变形也大。
1)热裂纹与结构钢相比,它的热裂纹倾向较大,在焊缝及热影响区均可能出现热裂纹。
最常见的就是焊缝结晶裂纹--在焊缝凝固过程的后期所形成的焊接裂纹,时在热影响区与多层焊层间还会出现液化裂纹。
含镍量越高,产生热烈倾向越大,而且越不容易控制。
;防止措施:a、严格限制硫、磷等杂质的含量。
b、调整焊缝金属组织,以奥氏体为主的γ+δ双相组织具有良好抗裂性。
c、调整焊缝金属合金成分,在单相稳定奥氏钢中适当增加锰、碳、氮的含量。
d、采用小线能量及小截面焊道
2)接头脆化奥氏体钢焊接接头的低温脆化与高温脆化就是值得注意的问题
防止措施:a、严格控制焊缝中铁素体含量(体积分数)2~7%,因为4 75℃脆化与δ相脆化易出现在铁素体中。
b、多层焊时采用较小线能量,以减少熔池体积,提高冷却速度,缩短高温滞留时间。
3)晶间腐蚀有三种形式:焊缝的晶间腐蚀;热影响区的“敏化区腐蚀”--敏化区腐蚀――在焊接热循环作用下,奥氏体不锈钢焊接热影响区中,被加热到易引起晶间腐蚀的敏化温度(理论上为450-850℃)的部位,称为敏化区。
在敏化区发生的晶间腐蚀现象; 刀蚀――发生在焊接接头近缝区一个狭带(小于1mm)上的晶间腐蚀。
这种腐蚀的破坏形式像刀的切口,故称为刀蚀。
;防止措施:a、尽量降低母材及焊缝中含碳量;b、采用热量集中的焊接方法,小的焊接线能量,多道焊、焊缝背面加铜衬垫等措施使接头快速冷却,使焊缝与热影响区在450~850℃的停留时间尽量缩短;c、在钢中添加稳定化元素Ti、Nb等;d、在钢及焊缝金属中加铁素体形成元素,从而获得奥氏体加少量铁素体的双相组织;e、焊后进行固溶处理(加热至1050~1150℃,保温后淬火)或稳定化处理(加热至85 0℃保温2h后空冷)。
;4)应力腐蚀开裂随材料腐蚀介质及拉应力大小的不同,开裂的断口可能就是沿晶的,也可能就是穿晶的,还可能就是两种皆有的混合形式。
焊接残余应力就是引起应力腐蚀开裂的主要原因。
接头过热区对这种开裂最敏感。
;减缓或防止措施:a、焊后消除或减少焊接残余应力;b、选用奥氏体-铁素体双相组织的母材或焊接材料;c、采用高Ni(达40%)的铬镍不锈钢焊条。
焊接奥氏体不锈钢常采用焊接方法有手工电弧焊、钨极氩弧焊与熔化极富氩混合气体保护焊。