超深井举升工艺存在问题分析及技术进展
深井超深井钻井技术现状和发展趋势
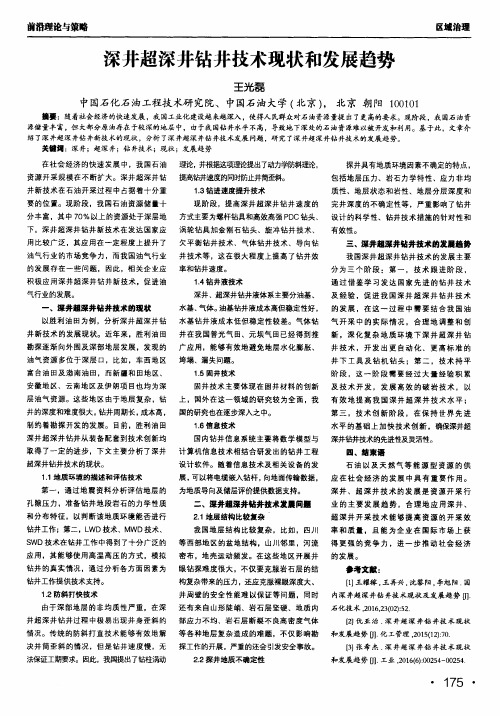
在社会经济的快速发展中,我国石油 资源开采规模在不断扩大。深井超深井钻 井新技术在石油开采过程中占据着十分重 要的位置。现阶段,我国石油资源储量十 分丰富,其中70%以上的资源处于深层地 下,深茹超深井钻井新技术在发达国家应 用比较广泛,其应用在一定程度上提升了 油气行业的市场竞争力。而我国油气行业 的发展存在一些问题,因此,相关企业应 积极应用深井超深井钻井新技术。促进油 气行业的发展。
· 175 ·
理论.并根据这项理论提出了动力学防斜理论. 提高钻井速度的同时防止井筒歪斜。
1.3钻进速度提升技术 现阶段,提高深井超深井钻井速度的 方式主要为螺杆钻具和高效高强PDC钻头、 涡轮钻具加金刚石钻头、旋冲钻井技术、 欠平衡钻井技术、气体钻井技术、导向钻 井技术等,这在很大程度上提高了钻井效 率和钻井速度。 1.4钻并液技术 深井、超深井钻井液体系主要分油基、 水基、气体。油基钻井液成本高但稳定性好, 水基钻井液成本低但稳定性较差。气体钻 井在我国普光气田、元坝气田已经得到推 广应用.能够有效地避免地层水化膨胀、 垮塌、漏失问题。 1。5固井技术 固井技术主要体现在固井材料的创新 上,国外在这一领域的研究较为全面,我 国的研究也在逐步深入之中。 1.6信息技术 国内钻井信息系统主要将数学模型与 计算机信息技术相结合研发出的钻井工程 设计软件。随着信息技术及相关设备的发 展,可以将电缆嵌入钻杆,向地面传输数据。 为地质导向及储层评价提供数据支持。 二、深并超深并钻井技术发晨问囊 2.1地层结构比较复杂 我国地层结构比较复杂,比如,四JIl 等西部地区的盆地结构,山川邻里,河流 密布,地壳运动频发。在这些地区开展井 眼钻探难度很大,不仅要克服岩石层的结 构复杂带来的压力。还应克服裸眼深度大、 井周壁的安全性能难以保证等问题。同时 还有来自山形陡峭、岩石层坚硬、地质内 部应力不均、岩石层断裂不良高密度气体 等各种地层复杂造成的难题,不仅影响勘 探工作的开展,严重的还会引发安全事故。 2.2探井地质不确定性
长寿命高效举升技术及下步攻关方向
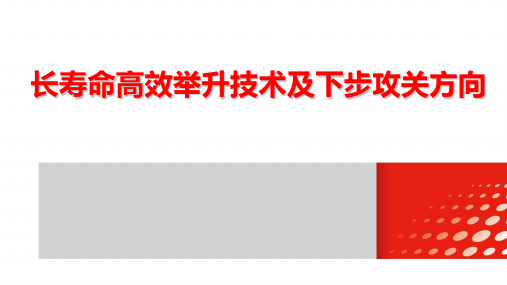
“木桶定律” 内衬管
抽油泵
油 井 “ 五 大 木 板”
木桶效应告诉我们,木桶盛 水量的多少取决于短板。
木板一:油管 木板二:抽油泵 木板三:抽油杆 木板四:工况
木板五:井下工具
无短板长寿命特征定义表
长板设置 抽油杆 油管 抽油泵 工况 脱接器
井下 工具
泄油器
油管悬挂 器
筛管
变径接头 泵拉杆
长寿命特征定义 已实施抽油杆分年限管理、全井为新杆、大修杆或修复Ⅰ
室内评价表明:内衬管磨损量小,起到了双向保护的作用。 ✓ 内衬管磨损量(0.39mm)要小于N80油管磨损量
(0.62mm) 37%。 ✓ 内衬管对接箍磨损量基本为0。
钢制圆形连续杆
内
抽油杆选型
衬
小直径抗磨接箍
油 管
配套工具完善
脱接器研制
举
泄油器研制
升
系
95配套泵
统
配
70配套泵
套
特种泵配套
63配套泵
50配套泵
胜胜利利采采油油厂厂
一、长寿命举升技术的研究及成效
2、长寿命举升技术研究所做工作
2)、长寿命耐磨蚀抽油泵的研究改进
在对抽油泵持续跟踪调查的基础上,进行了四次改进,形成改Ⅳ系列抽油泵;目前改Ⅳ泵在我厂推广应用1566口井, 并作为特种泵在全油田推广,引领了全局抽油泵技术的发展。
抽油泵三类8项改进
杆、在井抽油杆杆断次数不大于三次 偏磨井全井内衬油管、或不偏磨井应用普通油管 改Ⅳ系列抽油泵,或实施对应改进的特种抽油泵(斜井泵、
防腐泵、长柱塞防砂卡泵) 处于工况合理区,且冲程≥4.8米,冲次≤3.5次
83以下抽油泵不配套脱接器,83、95泵配套旋转脱接器
我国超深立井凿井提升面临的问题及建议

Байду номын сангаас
煤 炭 工 程
COAL ENGINEERING
Vo1 .
50.
No.6
doi: 10.1 1799/ce201806018
我 国超 深 立 井 凿 井 提 升 面 临 的 问题及 建 议
范 文博
(中煤第五建设有 限公 司 ,江苏 徐州 221000)
摘 要 :论述 了我 国国 内超 深 立 井提 升 装备 和 项 目现 状 .并与 国外 超 深 立 井提 升 系统 参数 配 置情 况进行 了对 比 。在 现 有 国产 装备 及 安 全规 程 条 件 下 ,分析 了超 深 立 井 凿 井 在 提 升 高度 、 提 升 效 率、提 升机 滚 筒宽度 等 方 面 面 临 的 困境 ,并探 讨 在 提 升 钢 丝 绳安 全 系数 、最 大提 升速 度 和缠 绕层数 方 面存在 的 问题 。进 一步提 出 了超 深立 井 凿井提 升发展及 研 究方 向 的建议 。
关键词 :超 深 立 井 ;凿井提 升 系统 ;钢 丝 绳安 全 系数 :提 升速度 中图分 类 号 :TD262.1 文献 标识 码 :A 文章 编号 :1671—0959(2018)06—0062—05
Problem s and suggestions on hoisting system of super deep vert ical shaft sinking in China
1 国 内深 立 井凿 井提升 装备 现状
近十年 ,我国一些 矿 山建 设企 业 、装备 制造 企 业及 大
专 院校 ,积极开展 了超 深立 井研究 ,在 深立 井凿 井及装 备 方 面 取 得 了长 足 进 步 。 15t、21t、25t新 型 钩 头 已 研 制 成 功 , vI型凿井井架 已定 型 ,6m 、7m 大体 积 吊桶 已投 入应用 , 凿井提升机最大直径也 已达 5.5m。作 为凿井关 键设备之 一 的国产凿井提升机性能参数见表 1。
《深井超深井钻井技术现状和发展研究》

《深井超深井钻井技术现状和发展研究》《深井超深井钻井技术现状和发展研究》薛飞(大庆钻探工程公司钻井四公司吉林松原138000)摘要:随着经济的发展,我国石油资源的开采力度越来越大,我国石油储量丰富,但大部分都处在深层地下。
面对资源能源危机日益加剧的局面,传统的浅井钻探已经不能满足我国资源消耗的需求,发展深井、超深井钻井技术是紧迫而必要的。
本文就深井、超深井钻井技术发展的现状及未来发展的趋势进行了分析讨论。
关键词:深井;超深井;钻井技术;现状;发展趋势深井、超深井钻井技术在石油开采中的应用具有重要意义,我国未探明的石油储量约为t,在庞大的石油储量中73%的部分处在深层地下,发达国家深井超深井钻井技术的迅速发展,使其本国油气行业的竞争力不断上升,我国油气行业发展面临窘境。
在我国大力发展深井、超深井钻井技术具有重要意义[1]。
一、深井、超深井的发展美国在1938年钻成世界上第一口深井,井深4573m,又分别于1949年、1972,钻成世界上第一口超深井和特深井,井深分别为6254.8m、9159m。
在1984年,前苏联钻成世界上第一口井深超万米的特深井(井深1226Om),1991年该井第二次侧钻至井深12869m,到今天为止它仍保持着世界最深钻井的纪录[2]。
美国、苏联、德国等深井、超深井钻井技术的发展起步都较早,技术发展速度较为迅速。
我国深井、超深井钻井技术起步较晚,20世界90年代以来,我国针对西部塔里木盆地以及川东地区进行资源开发,相继完成了多口深井、超深井的钻井工作[3]。
我国深井、超深井钻井技术正处在迅速发展的过程中。
二、深井、超深井技术的发展现状1.地质环境描述与评估技术(1)充分利用地震资料对地层孔隙压力和以及待钻井段岩石力学参数纵向剖面和区域分布进行评估分析。
通过总体的分析评估来判断地质环境是否适合钻井作业。
(2)MWD、LWD、SWD技术在钻井工程中被广泛应用,这些技术能够通过有效的高温、高压模拟手段来模拟钻井中的真实状况,并综合各种因素的进行全面的分析,为钻井工程的进行提供强有力的技术支持[4]。
油井举升方式优化调整探索与实践

一、油田举升设备存在问题1.产能足与设备举升能力不匹配通过现场生产数据统计,部分井其设备无法满足生产。
(1)螺杆泵井方面。
调查2016年底数据,有145口大泵型(1200以上泵型)且高产的螺杆泵井存有上产空间,平均日产液130t,动液面356m,平均转速95.9r/min。
其中有6口井,平均日产液大于190t,螺杆泵举升设备已无法满足生产需求,可更换电泵设备。
2)抽油机井方面。
有64口井机型、泵型、参数已经匹配到极限,但该井具有产能足、液面浅等特点,有一定的上产空间。
2.举升设备使用效率低(1)电泵井效率低,目前采用掺液的方式维持生产。
经统计,有8口低产能电泵井,平均单井日产液81t,日耗电858kWh,是同产量抽油机井、螺杆泵井耗电量的4倍多。
2)抽油机井使用效率低,一般情况下14型抽油机应匹配83mm 或95mm的抽油泵,但统计了200口14型抽油机井,其中有127口井由于产液低,匹配了57mm和70mm的抽油泵,由此造成设备使用的资源浪费。
二、举升方式设计原则及技术解决方案1.抽油机机型设计目前抽油机井泵效一般最大按60%设计。
结合产液情况,选择57、70、83、95m m抽油泵。
根据实际情况,产液Q≤60t/d的井采用57mm泵,60t/ d<Q≤90t/d的井采用70mm泵,90t/d <Q≤115t/d的井采用83mm泵,产液Q>115t/d的井采用95mm泵。
根据产液量、泵型,参照抽油机的承载标准(载荷利用率小于或等于95%或扭矩利用率小于或等于90%)设计机型。
2.螺杆泵设计根据螺杆泵排量进行设计。
由于目前大泵型螺杆泵存在反转的安全隐患,故现场一般使用800以下的泵型。
3.电泵设计根据电泵排量进行设计。
4.方案设计在以往的举升方式“双转”的过程中,更换下来的地面设备、井下杆管会被暂时存放,以备他用,一定程度上造成不必要的浪费;为此,方案设计要结合检泵时机与地质预产。
以“泵效最高,设备吨液单耗最低”为匹配原则,利用原井管柱及机组,同步开展举升方式互换调整以及检泵作业,最大限度地降低成本投入,盘活资产。
超深钻井技术现状与发展趋势

231我国未探明的石油储量达到8500万吨,其中约七成以上是埋藏在深层,有关油气资源的勘探,对于社会发展和秩序稳定以及国家燃料安全都具有非常重大的意义,同时在未来的竞争中,企业之间的竞争方式主要是通过提高油气勘探的成果和效率来进行角逐的。
随着目前我国浅层油气资源开发已经过了峰值水平,未来该行业的发展,更多的是面向深层石油勘探和开发。
超深井钻井技术是一项复杂的工程,工程内包含各项复杂的科学技术和装备,由于其专业性较高,其操作人员也必须是具有高素质的人才才能进行运作,为了提高团队运作的效率,还需要一支能具有科学管理水平的管理团队进行监督和指导。
1 超深井发展概况美国是全世界第一个进行该方面工作,研究和实验的国家,也是目前所有国家中,探深历史最长,技术水平最高的国家。
经过半个多世纪的发展,美国的深井钻井技术已经达到了全球领先水平,在深井钻井的过程中,能够从容的,在成本和效益之间选择平衡点,同时钻井速度很快,工作中出现安全事故的几率较少,其对于单井成本的控制为世界之最,仅仅是世界平均水平的40%~50%。
2005年3月,中国大陆科学钻探工程科钻一井顺利完钻,井深达5158米,在该工程中运用了大量最新的技术成果,标志着目前我国钻井技术的最高水平。
2 深井超深井钻井工作的主要难点2.1 地质条件复杂目前我国陆上深井的分布位置主要位于新疆,四川等地,上述地区地形复杂,自然气候多变,地质情况较为复杂。
进行深井超深井钻井时,会出现地层压力过大,井壁稳定性条件复杂,局部地区还会出现高温高压等情况影响工程的进行。
在地壳深处深层地层岩石的可钻性较差,也是影响深井超深井钻井工程顺利进行的原因。
为了达成深井超深井钻井工作的顺利完成,工作人员需要同时面对地应力集中,地层压力异常,地层破碎,高矿化,高硫化氢浓度等。
2.2 深井地质不稳定性钻井尤其是新区第一口钻井具有地质环境因素不确定的特点。
在进行第一口钻井的过程前,工作人员需要综合调查分析当地的地质条件,尤其是对于当地的地层压力,地质成形年代,地质分层深度,完井深度,地层状态,主要地质材料进行准确的调查,并通过岩石力学的专业知识进行综合考量,充分了解当地的地质条件你作为选择状态方案的重要参考。
国内超深井钻机技术现状与发展建议

国内超深井钻机技术现状与发展建议随着陆地油气开采高难度井的增加和海洋深水勘探的需要,超深井钻机的需求量将会有所增加,尤其是海洋资源领域的开发,将会有一定的需求。
超深井钻机的开发目前在国内还~JfJN起步,为防止国外大的跨国公司对中国实行关键技术垄断,同时也为保证国家战略能源安全,应加速超深井钻机技术的研发。
超深井由于其建井、钻井和完井时间都比较长,而且普遍存在地层结构复杂的问题,因此对钻井设备的要求是:可靠性高;过载能力大,能够及时处理井下事故;同时超深井钻井还有一个特殊性,就是起下钻所用的时间在整个钻井过程中所占的比重非常大,因此钻井效率也是考核钻机的一个非常重要的指标。
由于这些因素的存在,也就使得超深井钻机在技术发展上不同于常规钻机。
一、国内技术现状超深井钻机技术在国内近几年才开始研究,2004年由兰石国民油井公司和美国国民油井公司共同研制的9000m直流电驱动钻机在科威特成套,尽管关键件的总体设计和生产制造由美国国民油井公司掌握,但这也是我国在超深井钻机研制方面迈出的第1步。
国内由宝石机械公司2005年自主研发的首台9000m交流变频电驱动钻机目前正在油田进行工业性试验。
尽管该项目早在2001年就在国家经贸委立项,但由于受大功率变频控制技术的成熟度和大功率齿轮传动绞车可靠性等因素的影响,长期没有明确的用户,为此宝石机械公司进行了7000m交流变频电驱动、齿轮传动绞车钻机的研制,2003年7月完成工业性试验,为大功率交流变频技术应用以及自动送钻技术的应用积累了一定的经验。
随后,各个油田也看到了交流变频技术的优势,5000m、7000 m交流变频电驱动钻机在国内市场的销量大幅增长。
随着国际市场油价的升高,国内高难度井开采量的加大,超深井钻机的需求也突现。
2004年年底中石油集团公司组织行业专家对方案进行了评审,同时将9000m交流变频电驱动钻机列为集团公司2005年重点科研项目,至此,9000m交流变频电驱动钻机的研发正式进入实施阶段。
油井高效举升配套工艺与合理匹配探究

油井高效举升配套工艺与合理匹配探究油井采油是一个基础性行业,其高效举升配套工艺和合理匹配,对于实现油井的高效、稳定和安全运行具有重要作用。
本文结合目前油井举升工艺的现状和问题,探究油井高效举升配套工艺与合理匹配的关系及其优势。
一、油井举升工艺现状及问题油井举升是在采油过程中,将地下的原油通过注水或气提等方式排到地面的一种方法。
现有的油井举升工艺主要包括液力提升、电力提升和气体提升等方式。
液力提升是一种机械驱动油泵通过液压作用将地下的原油往上提升的方式。
需要一个专门的液压站来提供液压动力,并通过液压油管将液压动力传递到油泵上。
这种方式有稳定、耐磨等优点,但也存在能耗大、噪音污染等问题。
电力提升是通过电动机驱动油泵进行提油,相比于液力提升,不需要专门液压站,能耗更小。
但是需要一个专门的电源来提供电动机电力资讯,一旦电源中断稳定性就会受到影响。
气体提升是通过注入一定压力的气体到井底进行提油的方式。
这种方式需要注入压缩空气或氮气等气体,具有能耗低、环保等优点,但也存在注气量难以控制、需要更多安全防护等问题。
由此可见,现有的油井举升工艺各有优缺点,需要根据实际情况选择适合的方式。
但同时也存在以下问题:1. 工艺耗能较大,在提高油井开发效率的同时,也增加了企业的生产成本。
2. 工艺噪声污染较大,如液力提升和电力提升工艺在运行时会产生噪声影响周围环境。
3. 注气量难以控制和安全防护措施不足等问题,如气体提升工艺需要对注气量进行控制,否则会影响工艺稳定性和安全性。
为了解决现有油井举升工艺存在的问题,提高油井的开发效率、降低生产成本,需要采取一些高效的举升配套工艺,对其进行优化和改善。
具体工艺措施如下:1. 液力提升与电力提升相结合液力提升和电力提升两种工艺各有优点,可以相互补充。
如液力提升用于底井,采用电力提升进行中、浅井;或是在同一底井内用不同的工艺设置不同的油泵,分工协作,从而达到降低成本且提高效率的效果。
- 1、下载文档前请自行甄别文档内容的完整性,平台不提供额外的编辑、内容补充、找答案等附加服务。
- 2、"仅部分预览"的文档,不可在线预览部分如存在完整性等问题,可反馈申请退款(可完整预览的文档不适用该条件!)。
- 3、如文档侵犯您的权益,请联系客服反馈,我们会尽快为您处理(人工客服工作时间:9:00-18:30)。
超深井举升工艺存在问题分析及技术进展徐建礼张雷刘丙生(胜利油田分公司采油工艺研究院)摘要:塔河油田奥陶系碳酸盐岩油藏具有超深、缝洞发育等特点,由于注水困难,后期开采方式将以追踪液面深抽为主。
本文综合分析了深抽的技术难点,提出了防气、锚定、减小偏磨等具体解决措施。
对于超深液面油井,建议采用有杆泵-电泵复合举升工艺。
关键词:深抽油气分离气油管锚定长冲程复合举升随着开发的不断深入,油层能量逐渐降低,低液面油井不断增多。
特别是以塔河油田奥陶系碳酸岩储层为代表的西部油藏具有超深、高气油比、缝洞型地层等特征,油井深度5000米以上。
随着油藏的开发,地层能量逐渐降低,由于塔河油田特殊的地层条件和西达里亚等外围油田特定的社会环境,目前还没进行正规的注水开发。
由于地层能量没能及时得到补充,地层压力不断下降,将有越来越多的油井表现为深泵挂、低液面、低产能。
进行深抽是塔河油田后期提液的主要手段。
一、超深井举升技术现状及存在的问题深抽的目的是为了放大生产压差,强化开采,进一步挖掘油藏的生产潜力,以保证油田的持续稳定生产。
从国内外的综合分析来看,其主要手段以有杆泵、电潜泵为主。
特别是塔河油田全部采用了H级超高强度抽油杆,抽油机基本上是14型大抽油机,这些都为深抽创造了有利条件。
目前最大下泵深度已超过3000m,居国内领先地位。
近年来,由于潜油电泵制造质量的提高,电缆的耐温等级、电泵机组整体技术可靠性都有了较大改善,大功率电机的推出,使机组有效扬程可高达3000米以上,平均无故障连续运转时间长达1年半以上。
高扬程潜油电泵越来越多地应用于深抽井中。
深井举升存在的难点问题主要有以下几方面。
1、深井举升面临的首要问题是液面低造成原油脱气,将严重影响举升泵的效率。
当井筒压力低于气体溶于液体的饱和压力时,溶解于井液中的气体将分离出来,对举升设备将产生很大的影响。
对于抽油泵来说,通常以两种方式影响泵的排量。
首先在下死点开始上冲程时,由于泵筒内有气体,抽汲时泵筒压力下降缓慢,固定阀不能及时打开,减少了泵的有效冲程。
同时造成在吸入过程中气体伴随液体进入泵内,降低了每一冲程的产液量。
其次,由于泵腔内含气,下冲程时泵腔内压力上升缓慢,游动阀不能及时打开,降低了排油时间。
当气体影响极端严重时,会造成泵腔内气体往复膨胀、压缩。
上行程泵腔压力始终大于泵吸入口压力,下行程泵腔压力始终小于液柱压力,固定阀和游动阀均无法开启,形成气锁。
气体对离心泵的影响更大。
根据离心泵的工作特点,在工作介质为气液两相的情况下,泵的排量、压头和效率都会明显下降。
离心泵叶轮在工作时,当气体分离后,在叶轮和导壳中产生涡流。
这些气泡一方面占据了流道体积,使液体排量减少。
另一方面,气体使混合液密度降低,离心力减小,从而降低了泵的扬程。
严重时会造成气锁排不出液体,并产生气蚀现象,损坏叶轮和导轮。
2、深抽大负荷引起杆管失稳偏磨失稳弯曲是造成管杆偏磨的主要原因。
在上冲程过程中,杆柱每一点的合力都是向上的,杆柱被拉直,不会发生偏磨现象。
中合点(即合力为零的点)以下油管受力如下:上部油管在井液中的重力形成的向下的压力,下部油管在液体中的重力以及管内介质对油管和活塞泵筒向上的摩擦力。
在上述力的作用下,下部油管发生摆动与抽油杆接箍产生偏磨。
在下冲程过程中,油管每一点的合力都是向下的,油管被拉直,不会发生偏磨现象。
杆柱下冲程时各点受力比较复杂,而且处于变化中,下冲程运动开始时,还受到杆柱向上的惯性力的作用。
下部杆柱在压力作用下完成下冲程,容易弯曲变形,发生偏磨现象。
由于杆柱的塑性较强,上部的重力不会很快对下部形成压力,而下部杆柱在上冲程的惯性力作用下还在向上运动,大大增加了中下部杆柱的弯曲程度,杆柱发生弯曲的这种现象,称为失稳。
杆柱失稳是偏磨的主要原因。
由于偏磨,使抽油杆强度变低,加之交变载荷的影响,抽油杆容易疲劳。
因此,底部抽油杆出现断脱的情况较多。
3、深抽冲程损失明显加大有杆泵在抽油过程中,油管承受交变载荷,上冲程油管因卸载而缩短,下冲程油管因受载而伸长,这不仅会增加光杆冲程损失,而且将造成油管弯曲、偏磨,从而影响了管柱寿命。
对于直井,如果不进行锚定,则冲程损失为式中,λ为冲程损失,m;ρ1 为液体密度,kg/ m3 ;f p 、f t为活塞、油管金属截面积,m2 ;L 为抽油杆柱总长度,m;E 为钢的弹性模数,2. 06 ×1011 Pa ;η 为影响泵效, %;S 为光杆冲程,m 。
在以下参数情况下生产: 1600m 泵挂、44mm 泵、冲程为5m 、冲次为3次、73mm 油管、井液密度为0. 9g/ cm 3,因管柱伸缩可造成的冲程损失在0. 14m ,泵效降低2. 8 个百分点,而且泵挂越深,影响越大。
表1 不同泵深的冲程损失由此可见,油管锚定是深抽配套技术的一项重要内容。
4、抽油泵的漏失加大,应用缝隙流的流量方程计算漏失量。
()122U Pulq ⎡⎤=-⎣⎦323δΔ2πD 1+εδ式中,q —— 漏失量,m 3/s ;D —— 柱塞直径,m ; ε—— 相对偏心距ε=e/δ; g —— 9.8m/s 2δ——单面间隙,m ; ΔP ——柱塞上下压差,Pa ; U ——柱塞最大运动速度,m/s ; μ——动力粘度Pa.s由于漏失量与柱塞压差成正比,随着举升高度的增加,泵的漏失显著增加。
5、单项举升工艺无法满足进一步深抽的要求 表2 举升工艺适应性对比从上表可以看出,单项举升采油工艺应用于3000米之内是可行的,但对于更深液面的举升,必须采用新的采油技术。
总之,深抽井对系统设计,油井设备及配套工具和生产管理提出了更高的要求。
深井采油要取得好的效果,必须要有完善的配套技术做保正。
二、深抽配套技术进展1、有杆泵油气分离器有杆泵油气分离器结构如图所示。
油气分离装置的基本原理是利用油气的密度差, 通过滑脱和离心作用将油气分开。
分气过程可分为五 个步骤。
第一步:气泡在套管内随液流上升时,由于油气密 度差,使油气产生滑脱,气泡上行速度v g 等于液体上升 速度v f 加上气泡在静止液体中上升速度vd 。
因此,气泡 上升速度较液体上升速度快一个v d , 气泡首次分离。
根据斯托克公式()2d o g o1.8d gv ρρμ=- 式中 v d ——气泡在静止液体中的上浮速度,cm/s ; d ——气泡直径,cm ,一般取0.1~0.2cm ;ρo ——原油密度,g/cm 3; ρg ——气密度,g/cm 3; μo ——油的动力粘度,P a ·s ; g ——重力加速度,cm/s 2;因此,气泡上浮速度与气泡直径平方成正比,与液体粘度成反比。
降低泵吸入口压力使气泡直径变大会大大提高分气能力,而高粘度原油中气泡不易分离。
第二步:气泡在进液孔附近进行二次分离。
当气泡到进液孔附近时,液流要流向进液孔,流动方向发生改变,气泡上升速度及方向也将改变,气泡垂直分速为v d +v fv ,水平分速为液流水平分速v fh ,如图2所示。
由图2可见,液体比气泡更容易进入分离器,而且液体中气泡能否进入分离器将取决于垂直分速度与水平分速度的比值。
垂直分速度愈大,水平分速度愈小,则气泡越不容易进入。
因此,越靠近吸入口的气泡,水平分速度愈大,越容易被液流带入。
气泡直径愈小,垂直分速度愈小,越容易被液流带人气锚。
第三步:进入吸入口的气泡,在吸入口附近进行三次分离。
当油气刚进入吸入口时,液体流向是近似水平的,而气泡有向上的上浮速度,这时有部分气泡上浮,从吸入口排出。
第四步:气泡在沉降分离总成环形空间进行四次分离。
这时气泡速度是液流下行速度减去气泡上浮速度,环形空间有一部分能分离的最小气泡滞留在环形空间。
第五步:初步脱气后的流体向上进入螺旋分离总成,含气油流在螺旋分离总成环形空间内旋转流动,由于不同密度的流体,离心力不同,使聚集的大气泡沿螺旋内侧流动,带有未被分离的小气泡的液体则沿外侧流动。
被聚集的大气泡不断聚集,沿内侧上升至螺旋顶部聚集成气帽,经过排气孔排到油套环形空间。
液体则下行通过螺旋分离总成的中心通道进入泵内。
在下冲程时(泵的排出阶段),泵的固定阀以下液体流速为零,所进行的以上步骤的气泡都在静止条件下上浮。
2、电泵防气装置防气装置也是利用滑脱效应、离心效应等原理。
在举升泵之上部分油管换成特殊设计的双层管,双层管中间环空及双层管与套管之间的环空构成井液流动和油气分离的通道。
高气油比井内液体首先从双层管外部上升到举升泵上方位置,上升过程中靠减压分离降低压力使v fhvfvv d图2 二步骤气泡矢量图溶解气析出,成为气泡或气体段塞从井口套管放出。
脱气液体由上而下从双层管环空进入举升泵,双层管环空采用重力分离螺旋降压分离,进一步使溶解气析出,从而大大降低进泵液体中含气量,消除了气体对泵的影响。
本分离装置的双层防气管柱长度可以任意延长,通过流动时的压力降低使溶解气充分析出,并且气泡合并膨胀足以排至井口。
从根本上消除了气体对采油泵的影响。
3、有杆泵防偏磨配套技术是以治理杆管失稳弯曲及避免井斜部位杆管直接接触为出发点,针对杆管失稳弯曲造成的杆管偏磨问题,应用抽油杆底部集中加重技术,克服杆柱下行阻力造成的杆柱失稳弯曲;杆管缓冲补偿防失稳技术,消除振动载荷造成的杆管失稳弯曲。
针对井斜部位杆管直接接触造成的偏磨,研究杆管抗磨副抗磨蚀技术,避免杆管直接接触,消除井斜造成的杆管偏磨。
通过优化设计防偏磨技术,优化生产参数及防偏磨工具的位置和用量,提高系统效率,降低能耗。
(1)抽油杆集中加重防失稳技术 在有杆泵抽油过程中,抽油泵活塞下行过程中由于阻力的影响,导致下部抽油杆失稳弯曲,造成杆管偏磨,摩擦阻力增加。
由中心杆、外管组成的加重抽油杆位于杆柱的最下端,抽油时,中心杆承受载荷,外管起到加重的作用,中心杆受拉扶正外管,提高了杆柱的稳定性。
同时外管的重力通过上管压下管的方式向下传递,集中加到抽油泵活塞上,使抽油杆柱的中和点下移到抽油泵活塞上,克服抽油泵活塞下行阻力造成的下部抽油杆柱失稳弯曲、杆管偏磨。
图3为防偏磨加重抽油杆集中加重示意图。
(2)抽油杆缓冲补偿防失稳技术 抽油杆本身是一弹性体,在抽油杆往复运动过程中,由于杆柱作变速运动以及液柱载荷周期性的作用于抽油杆柱,从而引起抽油杆的弹性振动,造成的下部抽油杆柱的失稳弯曲偏磨。
中心杆、外筒组成的抽油杆防失稳补偿器连接在抽油杆柱的失稳部位,当抽油杆失稳弯曲之前,外筒与中心杆之间相对滑动,使抽油杆柱的弹性势能通过抽油杆补偿器转化为抽油杆柱图3 防偏磨集中加重示意图中心杆 加重外管滑套 接箍的重力势能,造成抽油杆失稳弯曲的力得到释放,抽油杆柱的稳定性提高,同时液体阻尼的作用,使作用在抽油杆柱上的振动载荷快速衰减,抽油杆柱不会失稳,抽油杆与油管之间不会产生接触压力,从而可以防止抽油杆与油管之间的偏磨。