反应再生器安全技术
SH 3504-2000催化裂化装置反应再生系统设备施工及验收规范

2 壳体直径允许偏差为 mm,同一断面上最大直径与最小直径之差不得大于设计 0
直径的 0.5%。筒体直段的长度允许偏差为±3mm; 3 锥体表面用 300mm 钢板尺沿母线检查,其局部凸凹值不得大于 lmm。锥体下端插
入灰斗内的长度允许偏差+50 mm; 4 螺旋顶板表面应平整,螺旋线应圆滑过渡; 5 焊缝按设计要求检验完毕,内部焊缝加强高度均应打磨平滑,其局部凸凹值不
UDC
中 华 人 民 共 和 国 行业 标 准
P
SH 3504-2000
催化裂化装置反应再生系统设备
施工及验收规范
Specification for construction and acceptance of Reactor-regenerator system equipment of catalytic crakdng unit
4
b 一、二级旋风分离器接口处断面中心线应与筒体直段轴线平行,其平行度偏差不 应大子 2mm。
9 旋风分离器总长允许偏差为 ± 8 mm,同一装置中同一级任意两个旋风分离器总长 之差不得超过 6mm;
10 已衬里后供货的旋风分离器尚应检查衬里的质量,衬里质量应符合《隔热耐磨 混凝土衬里技术规范》SH3531 的有关要求。 3.2.2 翼阀制造质量应符合设计图样要求,若设计无要求,则应符合下列规定:
主编单位: 中国石化集团第四建设公司 主编部门: 中 国 石 油 化 工 集 团 公 司 批准部门: 国 家 石 油 和 化 学 工 业 局
2000—10—26 发布
2001—03—01 实施
国家石油和化学工业局 发 布
关于批准《石油化工厂区绿化设计规范》
等 27 项石油化工行业标准的通知
什么是化工本质安全?本质安全详解
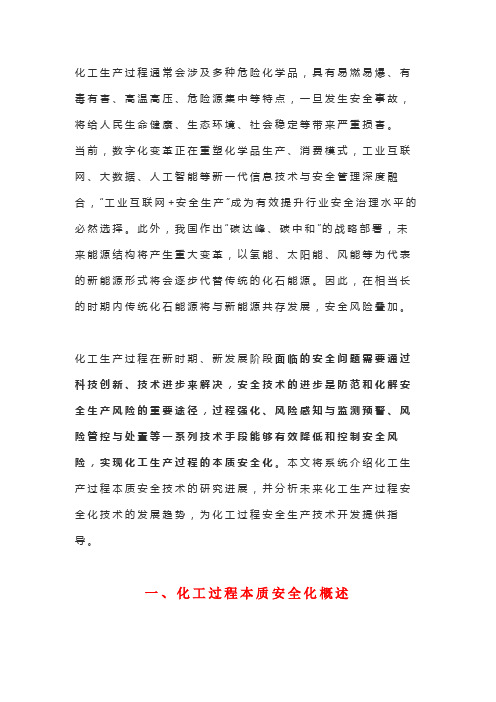
化工生产过程通常会涉及多种危险化学品,具有易燃易爆、有毒有害、高温高压、危险源集中等特点,一旦发生安全事故,将给人民生命健康、生态环境、社会稳定等带来严重损害。
当前,数字化变革正在重塑化学品生产、消费模式,工业互联网、大数据、人工智能等新一代信息技术与安全管理深度融合,“工业互联网+安全生产”成为有效提升行业安全治理水平的必然选择。
此外,我国作出“碳达峰、碳中和”的战略部署,未来能源结构将产生重大变革,以氢能、太阳能、风能等为代表的新能源形式将会逐步代替传统的化石能源。
因此,在相当长的时期内传统化石能源将与新能源共存发展,安全风险叠加。
化工生产过程在新时期、新发展阶段面临的安全问题需要通过科技创新、技术进步来解决,安全技术的进步是防范和化解安全生产风险的重要途径,过程强化、风险感知与监测预警、风险管控与处置等一系列技术手段能够有效降低和控制安全风险,实现化工生产过程的本质安全化。
本文将系统介绍化工生产过程本质安全技术的研究进展,并分析未来化工生产过程安全化技术的发展趋势,为化工过程安全生产技术开发提供指导。
一、化工过程本质安全化概述本质安全(i n h e r en t sa f e t y)概念最早由英国的T re vo r K l e tz 于1976年提出,其理念是从工艺源头上永久地消除风险,而不是单独靠控制系统、报警系统、联锁系统的使用来减小事故发生概率和减轻事故后果的严重性。
本质安全是绝对安全的理想状态,生产运行上很难达到,实际中需要通过本质安全化(i n h e r e n t l y s af e r)的一系列技术措施降低过程风险,使化工过程本质上更安全。
化工过程全生命周期的本质安全如图1所示,最小化、替代、缓和、简化这4个本质安全化策略适用于研发、设计、建设、操作、变更和维护等化工过程的整个生命周期。
工艺过程的本质安全化与被动型、主动型和程序型安全防护措施一起构成了化工过程的保护层,其中本质安全化工艺技术在所有保护层中处于最核心的部分,对安全风险控制起到决定性作用。
反应器、再生器检修施工方案
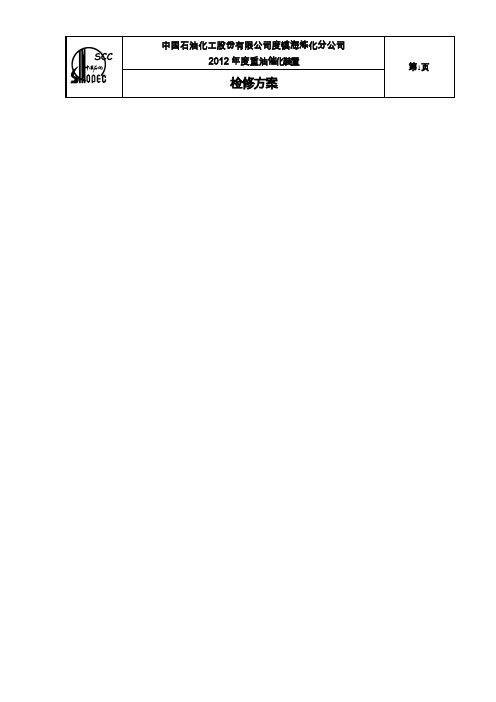
检修方案检修方案1.0工程概况1.1工程简介中国石化镇海炼化分公司炼油四部催化车间反应区的沉降器(T-201)、第二再生器(T-203)、外取热器(T-204)及其附属的项目检修是镇海炼化2012年度催化车间检修的关键项目。
本方案将重点阐述检修过程中的生产组织、施工程序、计划安排、质量控制、现场管理、安全措施以及施工机具和手段用料等内容。
1.2 工程特点本次检修施工时间紧,安装、吊装难度大,沉降器器、再生器、外取热器同时检修,由于施工作业空间狭小,给安装、吊装制造了极大的难度,施工时,大型吊车交叉作业多,各工种、工序、空间交叉施工较多,施工难度非常大。
为确保施工工期,前期预制工作要求在装置停气前进入施工现场并提前预制完毕。
1.3具体检修内容(根据镇海炼化炼油四部提供的资料)1.3.1沉降器(T-201)检修具体工作量1.3.2第二再生器(T-203)检修具体工作量序号名称材质规格(毫米)重量(吨)标高(米)备注序号名称材质规格(毫米)重量(吨)标高(米)备注1 开、封人孔和装卸孔2 ∮1100大油气线盲板装2次,拆1次3 ∮1100大油气线盲板法兰加碟璜.4 反再系统各人孔软梯安放固定5 DN1200提升管封头拆开6 提升管沉降器人孔、装卸孔档圈修理7 沉降器翼阀检查、更换8 汽提档板通气孔疏通9 提升管原料油进料喷嘴更换10 油桨进料喷嘴检查11 提升管中心环管,喷嘴加工更换12 DN1200提升管封头及法兰恢复13 底封头法兰拆开4对。
14 底部短节拆装(DN150)检修方案1 开、封人孔2 炉前瓦斯过滤短节拆装1只,DN803 F202火盆1只拆开,DN700,PN2.04 火盆连接软管拆除,DN80,DN40,DN15各1只5 配合火盆调试,油枪疏通,阀门拆装6 二再主风分布板检查,修补7 烧焦罐筒体钢板部分更换。
8 脱气罐锥体,再生立管部分更换。
9 大孔分布检查,耐磨喷嘴更换。
10 二再旋分检查3只,翼阀更换2只。
UOP连续重整第三代再生技术的应用
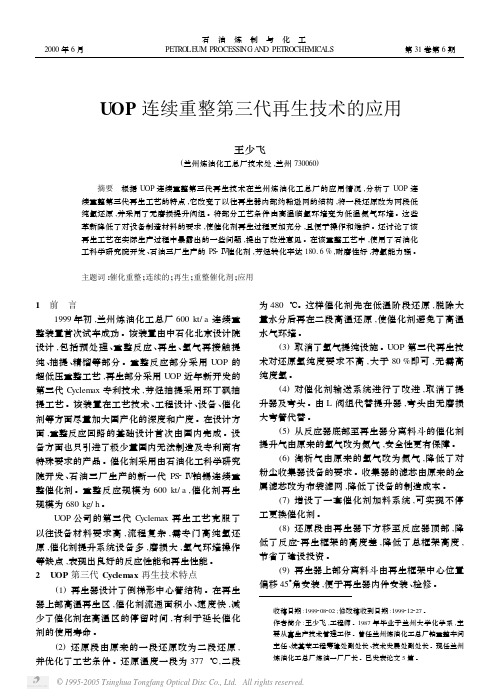
UOP连续重整第三代再生技术的应用王少飞(兰州炼油化工总厂技术处,兰州730060) 摘要 根据UOP连续重整第三代再生技术在兰州炼油化工总厂的应用情况,分析了UOP连续重整第三代再生工艺的特点,它改变了以往再生器内部约翰逊网的结构,将一段还原改为两段低纯氢还原,并采用了无磨损提升阀组。
将部分工艺条件由高温临氢环境变为低温氮气环境。
这些革新降低了对设备制造材料的要求,使催化剂再生过程更加充分,且便于操作和维护。
还讨论了该再生工艺在实际生产过程中暴露出的一些问题,提出了改进意见。
在该重整工艺中,使用了石油化工科学研究院开发、石油三厂生产的PS2Ⅳ催化剂,芳烃转化率达180.6%,耐磨性好,持氯能力强。
主题词:催化重整;连续的;再生;重整催化剂;应用1 前 言1999年初,兰州炼油化工总厂600kt/a连续重整装置首次试车成功。
该装置由中石化北京设计院设计,包括预处理、重整反应、再生、氢气再接触提纯、抽提、精馏等部分。
重整反应部分采用UOP的超低压重整工艺,再生部分采用UOP近年新开发的第三代Cyclemax专利技术,芳烃抽提采用环丁砜抽提工艺。
该装置在工艺技术、工程设计、设备、催化剂等方面尽量加大国产化的深度和广度。
在设计方面,重整反应回路的基础设计首次由国内完成。
设备方面也只引进了极少量国内无法制造及专利商有特殊要求的产品。
催化剂采用由石油化工科学研究院开发、石油三厂生产的新一代PS2Ⅳ铂锡连续重整催化剂。
重整反应规模为600kt/a,催化剂再生规模为680kg/h。
UOP公司的第三代Cyclemax再生工艺克服了以往设备材料要求高,流程复杂,需专门高纯氢还原,催化剂提升系统设备多,磨损大,氢气环境操作等缺点,表现出良好的反应性能和再生性能。
2 U OP第三代Cyclem ax再生技术特点(1)再生器设计了倒梯形中心管结构。
在再生器上部高温再生区,催化剂流通面积小、速度快,减少了催化剂在高温区的停留时间,有利于延长催化剂的使用寿命。
大型催化裂化装置再生器旋风分离器更换施工技术

大型催化裂化装置再生器旋风分离器更换施工技术周旭东;梁卓;彭振亚【摘要】在炼油装置中催化裂化装置占有重要地位,其反应/再生系统中旋风分离器的分离效果直接影响到反应/再生系统的正常运转,对于性能不满足要求的旋风分离器要及时进行更换.文章以中国石油大连石化公司350万t/a催化裂化装置检修为例,介绍了大直径再生器旋风分离器的更换作业,详细阐述了旋风分离器高精度安装的施工难点及施工工艺.施工实践验证了再生器顶部大直径开孔、旋风分离器成组更换施工方法的可行性,有效地缩短了施工工期.【期刊名称】《石油工程建设》【年(卷),期】2014(040)001【总页数】5页(P34-37,41)【关键词】催化裂化装置;大直径再生器;旋风分离器;更换;高精度安装;施工工艺【作者】周旭东;梁卓;彭振亚【作者单位】中国石油天然气第一建设公司,河南洛阳471000;中国石油天然气第一建设公司,河南洛阳471000;中国石油天然气第一建设公司,河南洛阳471000【正文语种】中文在炼油装置中催化裂化装置占有重要地位,其反应/再生系统中旋风分离器的分离效果不但直接影响到反应/再生系统的正常运转和催化剂的跑损,而且对分馏塔底油浆固体含量亦有很大影响。
因此保证旋风分离器的分离效果对企业节能减排、环境保护具有重要意义,对于性能不满足要求的旋风分离器要定期进行更换。
中国石油大连石化分公司 350 万 t / a 催化裂化装置,是我国迄今为止最早、最大的高低并列式催化裂化装置,其核心设备之一再生器的规格为D15600/9 300 × 43 550×36/34(单位为 mm),焊接后采用内燃法进行整体热处理。
这是 2003 年该催化裂化装置建成后运行至今的首次大修。
更换旋风分离器因其施工周期长、难度大,成为催化裂化装置检修工作的重点。
常规的再生器旋风分离器更换多采用侧壁开孔、单体更换的施工工艺。
本次旋风分离器更换作业对实际情况进行了充分分析,首次采用了旋风分离器工厂化深度预制,壳体顶部开孔,脚手架分段循环拆搭的施工方法,确保了整个工程的如期完工。
化工企业工艺管理制度
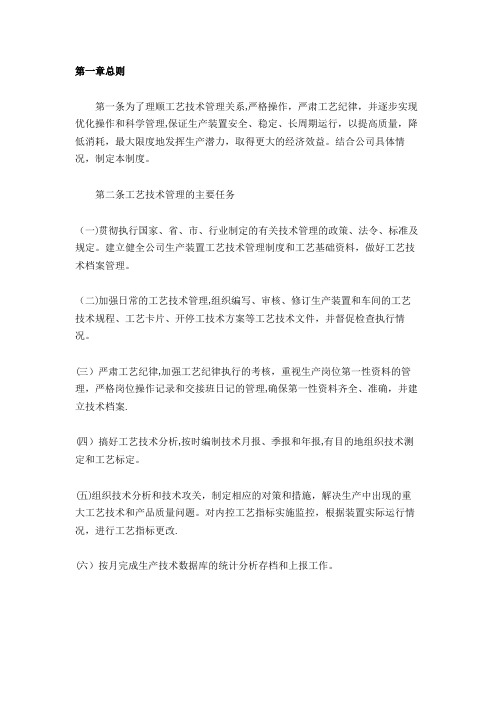
第一章总则第一条为了理顺工艺技术管理关系,严格操作,严肃工艺纪律,并逐步实现优化操作和科学管理,保证生产装置安全、稳定、长周期运行,以提高质量,降低消耗,最大限度地发挥生产潜力,取得更大的经济效益。
结合公司具体情况,制定本制度。
第二条工艺技术管理的主要任务(一)贯彻执行国家、省、市、行业制定的有关技术管理的政策、法令、标准及规定。
建立健全公司生产装置工艺技术管理制度和工艺基础资料,做好工艺技术档案管理。
(二)加强日常的工艺技术管理,组织编写、审核、修订生产装置和车间的工艺技术规程、工艺卡片、开停工技术方案等工艺技术文件,并督促检查执行情况。
(三)严肃工艺纪律,加强工艺纪律执行的考核,重视生产岗位第一性资料的管理,严格岗位操作记录和交接班日记的管理,确保第一性资料齐全、准确,并建立技术档案.(四)搞好工艺技术分析,按时编制技术月报、季报和年报,有目的地组织技术测定和工艺标定。
(五)组织技术分析和技术攻关,制定相应的对策和措施,解决生产中出现的重大工艺技术和产品质量问题。
对内控工艺指标实施监控,根据装置实际运行情况,进行工艺指标更改.(六)按月完成生产技术数据库的统计分析存档和上报工作。
(七)开展合理化建议活动和“三剂”(催化剂、添加剂、助剂等)的日常管理工作,制定生产装置化工“三剂”消耗定额,审查化工“三剂”年度和月度消耗计划,组织新型“三剂”应用技术方案审查、实施和效果验收工作。
(八)参加技措项目的方案讨论,参加设计审查,组织并参加技术考核和标定总结。
(九)收集和对比国内外技术发展的情报资料,开展公司内外的技术交流工作,结合公司实际,推广应用先进的工艺技术和新型“三剂"。
(十)认真学习和研究国内外先进的工艺技术管理经验,逐步应用现代化管理手段和方法,充分发挥信息资源共享的作用,提高工艺技术管理水平。
第三条工艺技术管理体制(一)工艺技术管理实行统一领导,分级管理.即公司、车间二级管理。
以公司一级为主,基点放在车间。
典型化工单元操作过程的安全技术—加热操作的安全技术
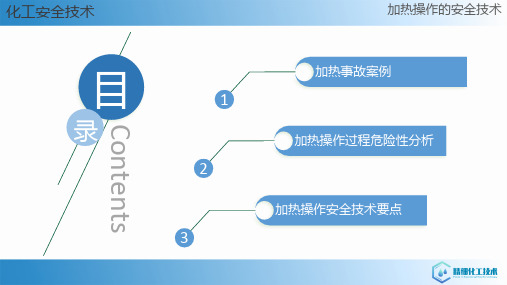
化工安全技术
加热操作安全技术
事故原因:在再生器系统清洗、置换不彻底的情况下,用蒸汽对再生器下部的加 热器进行试漏(等于用加热器加热),使残留和附着在器壁等部件上的铜氨液(或沉积 物)解析或分解,析出的一氧化碳、氨气等可燃气与再生器内空气形成混合物达到爆 炸极限范围,遇再生器内试漏作业产生的机械火花(不排除内衣摩擦静电火花)引起 爆炸。
15:40,用空气试漏,合成车间主任熊某等二人戴面具再次从再生器人孔进入检 查。17:20,在未对再生器内采样分析的情况下,车间主任李某决定用0.12MPa蒸 汽第三次试漏,并四人一起进入,李某用哨声对外联系关停蒸汽,工艺主任王某在 人孔处进行监护。17:40再生器内混合气发生爆炸。除一人负重伤从器内爬出外, 其余三人均死在器内,人孔处王某被爆炸气浪冲击到氨洗塔平台死亡。生产副厂长 赵某、安全员蔡某和机械员魏某均被烧伤。
化工安全技术
加热操作安全技术
二、加热操作过程危险性分析
➢生产中常用的加热方式:直接火加热(包括烟道气加热)、蒸汽或热水加热、有机载体 (或无机载体)加热以及电加热等。
热水: 100℃以下 水蒸气:100-140℃ 加热炉或热载体: 140℃以上 电加热: 250℃以上 ➢提供热源的设备主要为:蒸汽锅炉、导热油炉、热风炉等,均属于特种设备。
化工安全技术
加热操作的安全技术
目
录
Contents
1 2 3
加热事故案例 加热操作过程危险性分析 加热操作安全技术要点
化工安全技术
加热操作安全技术
一、加热事故案例
1995年1月,陕西省某化肥厂铜洗工段回流塔在检修过程中发生再生器爆炸事故, 造成4人死亡,多人受伤。
该化肥厂铜氨液再生由回流塔、再生器和还原器组成。1月13日早7时,再生系统 清洗置换后打开再生器人孔和顶部排气孔。14:00采样分析,14:30用蒸汽对再生器下 部的加热器试漏,技术员徐某和陶某戴面具进入再生器检查。因温度高,所以用消防 车向再生器充水降温。
催化裂化装置操作安全技术(2篇)

催化裂化装置操作安全技术催化裂化是蜡油和渣油在高温和催化剂作用下,在提升管式反应器中进行快速反应,把较大分子的烃类裂化为较小分子烃类,再经分馏、吸收等工序生产汽油、柴油、液态烃干汽等产品的炼油生产装置。
催化裂化反应类型主要有裂化反应、异构化反应、氢转移反应和芳构化反应四种。
反应再生和分馏是催化裂化装置的核心。
装置除具有易燃、易爆、易中毒特点外,油浆易结焦堵塞设备管线,也是比较突出的安全问题。
(一)反应再生单元安全特性在反应再生过程中,原料油与再生后的高温催化剂在反应器提升管的下部进入并呈沸腾流化状态(催化剂为固体)接触反应,反应后的催化剂和油气经上部的反应沉降器进行气固分离,反应油气去分馏。
催化剂由斜管回到烧焦罐烧焦。
在烧焦罐中,反应后催化剂自待生斜管进入烧焦罐底部,在压缩空气推动下呈沸腾流化状态进行烧焦,并由主风带入上部再生器进一步烧焦。
再生后的高温催化剂由再生斜管进入提升管式反应器底部流化反应。
在这个反应再生过程中,同时存在着易燃物(反应油气)、助燃物(压缩空气)和烧焦明火三个要素。
所以在实际操作中必须严格控制汽提段流量和二段流量。
另外,如果沉降器顶压过高,不仅会迫使系统停车,甚至可能会使催化剂倒流引发重大事故。
(二)反应再生过程操作异常现象(1)提升管温度大幅度波动,会烧坏设备。
引起温度大幅度波动的原因主要有:流量波动大或原料带水;烧焦罐温度大幅度波动;原料预热温度大幅度波动;两器差压波动;催化剂量波动;再生滑阀控制失灵。
对温度波动要查明原因,有针对性地采取措施。
如对原料进行脱水,稳定进料量和原料预热温度,稳定烧焦温度,调节两器差压。
如仪表失灵改用手动等。
(2)沉降器压力大幅波动。
如果沉降器出现压力大幅度波动,首先要准确判断异常原因,采取对应的处理措施。
如果是原料带水,要立即进行脱水。
进料量波动大时要稳定进料量。
其它原因如汽提蒸汽量及压力波动大,催化剂循环波动量大,以及分馏塔釜液位过高等,都要及时采取对应的调节控制措施。
- 1、下载文档前请自行甄别文档内容的完整性,平台不提供额外的编辑、内容补充、找答案等附加服务。
- 2、"仅部分预览"的文档,不可在线预览部分如存在完整性等问题,可反馈申请退款(可完整预览的文档不适用该条件!)。
- 3、如文档侵犯您的权益,请联系客服反馈,我们会尽快为您处理(人工客服工作时间:9:00-18:30)。
反应再生器安全技术
设备名称故障故障原因及后果预防措施反应器(沉降器)提升管温度
过高( 1)进料量减少( 2)再生剂循环量过大,易造成分馏系统大幅
度波动,只产气体,下部液体少,冲塔等事故(1)提高进料量( 2)检查再生器滑阀是否出现问题提升管温度过低(1)原料油带水严重(2)再生器循环量减少或中断,造成沉降压力上升,气体段藏量急降,待
生催化剂带油,再生器超温,严重时烟囱带黄烟( 1
④ 减少待生催化剂,去再生器的量⑤温度太低 (重催低于 485℃)启动原料自动保护联锁装置切断
进料( 2
阀无问题要考虑是否是再生管被堵塞,尤其是滑阀无问题,催化剂中
断,应停工处理压力波动大( 1)原料带水( 2)反应温度波动( 3)分
馏塔液面高( 4)分馏冷回流启动大或冷空出现问题( 5)气压机故障停车,易造成反应 --再生器压力波动大,沉降器油气压力波动大,再生器超温,烧坏设备。
沉降器旋风分离器工作不稳定造成油浆中固体含
量增加,若处理不好,造成油浆系统堵塞不畅等(1)原料带水见上(2)降低分馏塔底页面多甩油浆,提高分馏塔下部温度少产油浆(3)检查好塔顶空冷冷却温度等( 4)必要时启动原料自动保护联锁装置
再生器超温( 1)待生催化剂带油( 2)重油催化、原料轻重不均( 3)再生取热系统故障造成再生器以及烟气后部系统内构件损坏,损坏烟
道,催化剂跑损等(1)检查汽提蒸汽除油气效果(2)调整好重油催
化的重油与蜡油的比例( 3)分析再生取热系统故障原因后要加大取热量以降低再生温度,自动联锁启用,保护装置安全反应 ----再生系统衬
里脱落,尤其是斜管、提升管衬里脱落(1)施工质量不好(2)两器开工升温不按升温曲线,升温波动大(3)两器超温频繁,反应—再生出现热点(壁温在500℃以上)强度降低,增加磨损,产生催化剂泄露,处理不当,停工斜管、提升管衬里脱落,造成再生滑阀堵塞,斜管堵
塞,催化剂循环量减少或中止,装置大幅度降量或停工( 1)严把施工质量关,选用好的绝缘耐磨衬里( 2)两器尤其在装置第一次开工,严格按升温要求烘干衬里( 3)严格操作,做到原料、操作条件平衡,保证水、电、气、风平衡,防止两器频繁超温( 4)加强两器日常检查,使用红外温度计和夜间闭烟检查,及早发现过热点,及早维护超压或
压力过低(1)沉降室压力大,造成再生压力波动(自动位量)(2)再生主风控制波动(3)再生压力控制或烟机突然故障停车(4)再生器取热管爆管再生器超压易引起主风机、增压机飞动,从而引起无主风,引起催化剂倒入,主风机恶性事故或再生压力太高,再生剂压空,空
气要进入沉降室的重大恶性事故(催化剂倒流)(1)再生压力控制手动,控制好再生压力( 2)再生器主风进量改手动,控制入再生器风量稳定( 3)三机组时烟机停车则主风机要减少一半(二台主风机并联操作),反应—再生降压操作,若烟机与主风机分体,只发电,则控制好烟气放空( 4)取热器坏,停用取热器,同时要调解好原料,降低生焦油量以保证热平衡( 5)造成倒流迹象启动主风、原料自动保护联锁装
置沉降室结焦( 1)沉降室提升管出口的快速分离器型式落后(2)沉降室中油气停留时间长(3)大气管线保温不好,结焦焦块堵塞,能分
离造成催化剂进分馏系统,加速油浆系统磨损和堵塞,进入待生斜管
或在待生催化剂出口结焦、造成待生催化剂进不了再生器而停工(1)选用新型提升管出口的快速分离器,减少油气在沉降室中停留时间(2)大油气线改用冷壁管,降低油气管的温差,减少结焦(3)采用新型汽提段,采用滤油设施,防止焦块进入待生斜管(4)采用高效喷嘴,提高原料雾化粒度。