车铣复合高效加工薄壁零件
车铣复合加工工艺介绍
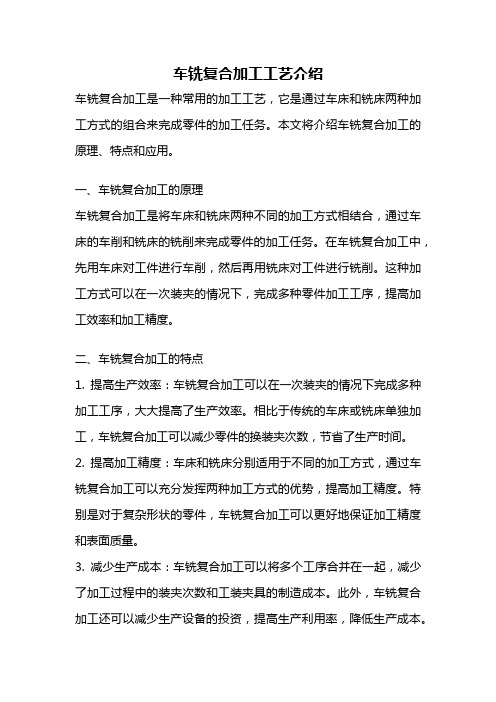
车铣复合加工工艺介绍车铣复合加工是一种常用的加工工艺,它是通过车床和铣床两种加工方式的组合来完成零件的加工任务。
本文将介绍车铣复合加工的原理、特点和应用。
一、车铣复合加工的原理车铣复合加工是将车床和铣床两种不同的加工方式相结合,通过车床的车削和铣床的铣削来完成零件的加工任务。
在车铣复合加工中,先用车床对工件进行车削,然后再用铣床对工件进行铣削。
这种加工方式可以在一次装夹的情况下,完成多种零件加工工序,提高加工效率和加工精度。
二、车铣复合加工的特点1. 提高生产效率:车铣复合加工可以在一次装夹的情况下完成多种加工工序,大大提高了生产效率。
相比于传统的车床或铣床单独加工,车铣复合加工可以减少零件的换装夹次数,节省了生产时间。
2. 提高加工精度:车床和铣床分别适用于不同的加工方式,通过车铣复合加工可以充分发挥两种加工方式的优势,提高加工精度。
特别是对于复杂形状的零件,车铣复合加工可以更好地保证加工精度和表面质量。
3. 减少生产成本:车铣复合加工可以将多个工序合并在一起,减少了加工过程中的装夹次数和工装夹具的制造成本。
此外,车铣复合加工还可以减少生产设备的投资,提高生产利用率,降低生产成本。
4. 适用范围广:车铣复合加工可以适用于各种材料的加工,包括金属材料和非金属材料。
无论是批量生产还是单件加工,车铣复合加工都能够满足不同的需求。
三、车铣复合加工的应用车铣复合加工在各个领域都有广泛的应用。
特别是对于复杂形状的零件加工,车铣复合加工可以更好地满足生产需求。
以下是一些常见的应用领域:1. 汽车制造:汽车零部件通常具有复杂的形状和高精度要求,车铣复合加工可以满足汽车制造的需求,提高生产效率和产品质量。
2. 机械制造:机械零件通常需要进行多个加工工序,车铣复合加工可以减少加工过程中的换装夹次数,提高生产效率。
3. 航空航天:航空航天零件通常具有高精度要求和复杂的形状,车铣复合加工可以满足航空航天领域对零件精度和质量的要求。
薄壁零件加工工艺方法分析

薄壁零件加工工艺方法分析什么是薄壁零件?薄壁零件是指壁厚相对较薄,外形也相对复杂,常见于汽车、电子、机械等领域的零件,如汽车车门、电子设备外壳等。
薄壁零件加工的难点薄壁零件加工的难点主要在于以下两个方面:1.零件壁厚薄:由于零件壁厚相对较薄,所以容易产生振动和翘曲等变形现象,而且易热变形,导致加工难度增加。
2.外形复杂:薄壁零件外形通常比较复杂,加工难度也大。
薄壁零件加工的常用方法单点加工法单点加工法是指通过刀具对薄壁零件进行加工的方法。
该方法适用于对平面零件和简单形状的薄壁零件进行加工。
常见的单点加工法包括:1.铣削:用铣刀对薄壁零件进行加工,可实现高速、高效、高精度的加工。
2.钻孔:用钻头对薄壁零件进行加工,也可加工一定程度的凸凹面。
3.车削:用刀具对薄壁零件进行加工,通常适用于对旋转体进行加工。
轧制加工法轧制加工法是指通过轧制的方式对薄壁零件进行加工。
该方法适用于对较大尺寸的薄壁零件进行加工,如汽车车身等。
常见的轧制加工法包括:1.深冲模:利用模具对薄壁零件进行加工,可加工多曲面、异形和复杂形状的零件。
2.拉伸模:利用模具对薄壁零件进行加工,适合加工尺寸大、平面面积较小的零件。
其他加工法除了上述两种方法外,还有一些其他的薄壁零件加工方法,如:1.冷却加工法:通过冷却液对薄壁零件进行加工,可减少热变形和振动。
2.激光加工法:通过激光对薄壁零件进行加工,可实现高精度、高效率的加工。
结论薄壁零件的加工难度比较大,但是通过一些常用的加工方法,如单点加工法和轧制加工法,以及一些其他的加工方法,如冷却加工法和激光加工法,就可以有效地解决加工难题,对薄壁零件进行高精度、高效率的加工。
盘轴一体结构零件高效车铣复合加工技术研究

零件 的装 夹需 要讲究 技 巧。安装 夹 具时 , 先将 夹具 基准端 面和 花盘 端面修 整平 滑 ; 安装 联接 螺栓 时先进 行预 拧紧 ,拧 紧力适 中 ,当夹 具找 正后 ,进行 两两对 点渐 进压 紧 ,同时 观察外 圆 的跳动 ,避免 由于 一点 用力 过大 导致 已找正 的平 面 出现 异常 。零 件安 装时 ,同样 采用 渐进 压紧方 式 ,避免 产生压 痕和 零件压 紧变 形 。
工业技术
C — h i n — a N e — ws a n d P r o d u c t s 口匪翟盈圈 — ■ ‘ 硼 瞄 I 啦 l
盘轴一体结构零件高效车铣 复合加工技术研究
林 大 力
( 沈 阳黎 明航 空发动机 ( 集 团) 有 限责任公 司,辽 宁 沈阳 1 1 0 0 4 3 )
盘 轴 一 体 结 构 零 件 由于 其 特 殊 的 深 腔 结构 ,且从 超声 波探 伤到成 品有 较 大的 加工 余量 ,半 封闭 深腔加 工 中走刀 困难 , 加工 过程 中刀 具与 零件容 易产 生碰 撞 ,因 此 刀具结 构设 计成 为关键 ,同时零 件加 工 采用 了卧 式车铣 复合 加工 中心 ,在进 行 刀 具结 构设 计时 要充分 考虑 机床 接 口和刀具 的可 达性 , 考 虑到设 备 的特点 和 内部 功能 , 高压 内冷结 构 刀具属 于首 选方 案 。根 据 以 往加 工经 验 ,最 终确 定的 刀具方 案 。 2 . 3 专 用T装 的结 构设计
关 键词 :盘 轴 结 构零 件 高效 车铣复 合 加 工技 术 中图分 类号 : T K 1 6 2 1 研究 目标 文 献标识 码 :A
典型薄壁零件数控铣削加工工艺

典型薄壁零件数控铣削加工工艺随着制造业的发展,数控加工技术逐渐成为最常用的加工方法之一。
而在数控加工领域中,数控铣削技术是常见的加工方法之一。
本文将介绍典型薄壁零件数控铣削加工工艺,包括工艺准备、加工流程、刀具选择和切削参数等方面的内容。
一、工艺准备1.1 材料选择因为薄壁零件通常是轻型结构件,所以材料一般选择铝合金、镁合金、不锈钢等轻质、高强度的材料。
1.2 工件夹紧在加工薄壁零件时,一定要保证工件夹紧牢固。
否则,易造成加工过程中工件的振动或位移,导致加工精度降低。
1.3 加工精度要求由于薄壁零件的厚度较小,所以在加工过程中要保证加工精度高,以防加工出错或造成损失。
二、加工流程2.1 预处理将所选材料进行预处理,包括去表面氧化层、去毛刺等。
2.2 下刀编制好数控加工程序后,进行下刀和切割。
2.3 清洗清洗零件,以便检查和测试。
2.4 检测检测零件的精度、结构、特性等。
如果不合格,要重新加工。
进行表面处理,包括抛光、喷漆、防锈等。
三、刀具选择在加工薄壁零件时,需要选用比较特殊的刀具。
常用的刀具主要包括切割刀具、削铣刀具、倒角刀具、钻头等。
3.1 切割刀具为了保证零件表面的质量和精度,需要选用切割刀具。
切割刀具的作用是将零件中的材料割离,形成所需的几何形状。
在进行倒角时,需要选用倒角刀具。
倒角刀具能够将薄壁零件边缘处的角进行倒角处理,使其具有更好的平滑度和美观度。
3.4 钻头在加工薄壁零件时,常常需要进行孔加工。
钻头是一种常用的刀具,在加工孔时经常被使用。
四、切削参数在加工薄壁零件时,需要注意切削参数的选择。
切削参数对加工质量起着重要的影响。
4.1 切削速度切削速度是指刀具在切割过程中移动的速度。
切削速度过快,容易导致刀具磨损、表面质量差等问题。
切削速度过慢,加工效率低下。
切削深度是指刀具在一次切削过程中切入材料的深度。
切削深度过大,会导致切屑对切削影响的加重,影响加工质量和效率。
总之,在加工薄壁零件时需要注意工艺准备、加工流程、刀具选择和切削参数等方面的内容。
未来机床发展的重要方向之一复合加工——车铣复合加工技术的发展及应用

制 、工装靠模多以及管理难的技术难题 ,而且 引进 在线测量加工、随动加工等新型的加工工艺。
1车铣 的在 线测量加工工艺 .
( )装夹中测量定位 凸轮轴毛坯上有 已锻打 1
成 形 凸轮 ,如要 对 凸轮进 行 首 次车 铣 加 工 ,则必 须 知 道 在每 次 装 夹过 程 中各 凸轮 所处 的位 置 。解 决 这 个 问 题 常规 的 工 艺是 制 作 专 用装 备 对 凸轮 轴进 行 定 位 ,先加 工定位 销孔再加 工 凸轮 型面 ,此加工 工艺对
高速 旋 转 ,工 件低 速 旋 转 ,因此 其 切 削 力 比传 统切
集成 了现代先进控制技术 、精密测量技术和
)A / M应用技术的先进机械加 工技术。 C
削加工要小许多 ,非常适合薄壁件的加 工,也不会 因工件高速旋 转而形成的离心力造成薄 壁件和细长
} } 复合加工的发展及特点
薄壁套等零部件的加工 ,具有广阔的发展和应用前 景 ,是机械制造领域 的重要发展方向。
加工主要可分为轴向车铣和正交车铣 。车铣运
复合运动 ,是利用铣 刀旋转和工件旋转的合成
来实现对工件的切 削加工。车铣不是简单 的将 和铣削两种加工方法合并在一起 ,而是利 用车 成运 动来完成 各类表 面的加 工 。在进 行车铣
重要 方向
技术、信息技术、可靠性技术的发展,向构件简 约化、结构紧凑化、配置模块化和部件商品化方
向发展 。复合加工机床的性能也会根据用户的加
工要求向多样化发展,有适合于多品种、单件和
小批量生产条件 的全功能性复合加工机床 , 也有
适合于提高生产效率、较大批量生产条件的专用
的功能适宜的复合加工机床 。同时,复合加工技
薄壁件的三种加工方法
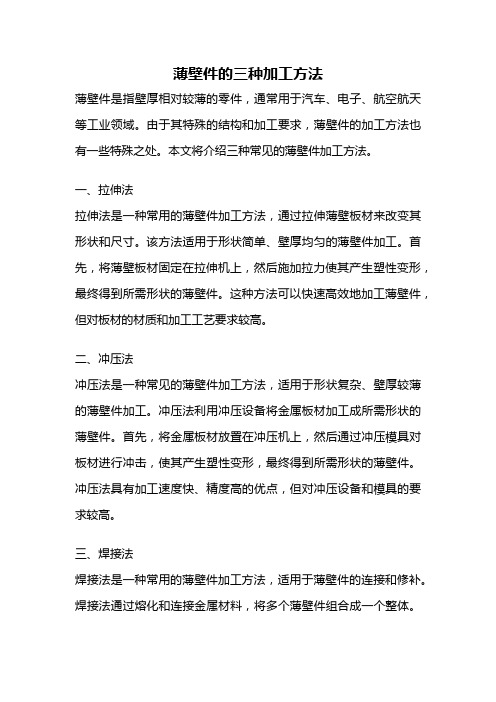
薄壁件的三种加工方法
薄壁件是指壁厚相对较薄的零件,通常用于汽车、电子、航空航天等工业领域。
由于其特殊的结构和加工要求,薄壁件的加工方法也有一些特殊之处。
本文将介绍三种常见的薄壁件加工方法。
一、拉伸法
拉伸法是一种常用的薄壁件加工方法,通过拉伸薄壁板材来改变其形状和尺寸。
该方法适用于形状简单、壁厚均匀的薄壁件加工。
首先,将薄壁板材固定在拉伸机上,然后施加拉力使其产生塑性变形,最终得到所需形状的薄壁件。
这种方法可以快速高效地加工薄壁件,但对板材的材质和加工工艺要求较高。
二、冲压法
冲压法是一种常见的薄壁件加工方法,适用于形状复杂、壁厚较薄的薄壁件加工。
冲压法利用冲压设备将金属板材加工成所需形状的薄壁件。
首先,将金属板材放置在冲压机上,然后通过冲压模具对板材进行冲击,使其产生塑性变形,最终得到所需形状的薄壁件。
冲压法具有加工速度快、精度高的优点,但对冲压设备和模具的要求较高。
三、焊接法
焊接法是一种常用的薄壁件加工方法,适用于薄壁件的连接和修补。
焊接法通过熔化和连接金属材料,将多个薄壁件组合成一个整体。
焊接法可以用于不同材质、不同厚度的薄壁件的连接,具有连接牢固、结构简单的优点。
常见的焊接方法包括电弧焊、气体保护焊、激光焊等。
焊接法的缺点是加工过程中会产生热变形和应力集中等问题,需要通过控制焊接参数和采取适当的焊接工艺来解决。
薄壁件的加工方法包括拉伸法、冲压法和焊接法。
不同的加工方法适用于不同形状、不同壁厚的薄壁件加工。
在实际应用中,需要根据具体的要求和条件选择合适的加工方法,以确保薄壁件的质量和性能。
薄壁类零件的车削工艺分析

薄壁类零件的车削工艺分析段立波一.引言薄壁类零件指的是零件壁厚与它的径向、轴向尺寸相比较, 相差悬殊, 一般为几十倍甚至上百倍的金属材料的零件,具有节省材料、结构简单等特点。
薄壁类零件已广泛地应用于各类石油机械部件。
但是薄壁类零件的车削加工是比较棘手的,具体的原因是因为薄壁类零件自身刚性差、强度弱,在车削加工中极容易变形,很难保证零件的加工质量。
如何提高薄壁类零件的加工精度是机械加工行业关心的话题。
二.薄壁类零件车削过程中常出现的问题、原因及解决办法我们在车削加工过程中,经常会碰到一些薄壁零件的加工。
如轴套薄壁件(图1),环类薄壁件(图2),盘类薄壁件(图3)。
本文详细分析了薄壁类零件的加工特点、防止变形的装夹方法、车刀材料、切削参数的选择及车刀几何角度。
进行了大量的实验,为以后更好地加工薄壁类零件,保证加工质量,提供了理论依据。
图1轴套薄壁件图2环类薄壁件图3盘类薄壁件1.薄壁类零件的加工特点1.1因零件壁薄,在使用通用夹具装夹时,在夹压力的作用下极易产生变形,而夹紧力不够零件又容易松动,从而影响零件的尺寸精度和形状精度。
如图4所示,当采用三爪卡盘夹紧零件时,在夹紧力的作用下,零件会微微变成三角形,车削后得到的是一个圆柱体。
但松开卡爪,取下零件后,由于零件弹性,又恢复成弧形三角形。
这时若用千分尺测量时,各个方向直径相同,但零件已变形不是圆柱体了,这种变形现象我们称之为等直径变形。
图4三爪卡盘装夹1.2因零件较薄,加工时的切削发热会引起零件变形,从而使零件尺寸难以控制。
对于膨胀系数较大的金属薄壁零件,如在一次安装中连续完成半精车和精车,由切削热引起零件的热变形,会对其尺寸精度产生极大影响,有时甚至会使零件卡死在芯轴类的夹具上。
1.3薄壁类零件加工内孔中,一般采用单刃镗刀加工,此时,当零件较长时,如果刀具参数及切削用量处理不当,将造成排屑困难,影响加工质量,损伤刀具。
1.4由于切削力和夹紧力的影响,零件会产生变形或振动,尺寸精度和表面粗糙度不易控制。
薄壁零件的车削技巧

薄壁零件的车削技巧薄壁零件是指壁厚相对较薄的零件,在车削加工中,由于其壁厚薄,容易产生变形和振动,所以需要特殊的车削技巧来保证加工质量。
本文将介绍薄壁零件的车削技巧。
首先,保持机床的稳定性。
薄壁零件在车削时容易产生振动,而振动会影响加工精度和表面质量。
为了保持机床的稳定性,首先要确保机床具备足够的刚性和抗震性,同时要确保机床的紧固件处于良好的状态,以免因紧固件松动而导致振动。
此外,还可以通过合理的刀具和夹具选择来减少振动,例如选择合适的刀具长度和刚度,使用刀柄的支撑力等。
其次,选择合适的切削参数。
在车削薄壁零件时,要选择合适的切削参数,以保证刀具的切削力不会过大。
一般来说,应尽可能采用小的进给量和切削深度,降低切削力。
另外,应注意保持刀具的尖角和刃磨状况良好,以减小刀具的切削力。
第三,选择合适的刀具和夹具。
在车削薄壁零件时,要选择合适的刀具和夹具,以提高加工的稳定性和精度。
刀具要选择具有较高刚度和切削性能的硬质合金刀具,以减小切削力和振动。
夹具要选择刚性好的夹具,以确保零件的稳定夹持,同时要避免夹持过紧而导致变形。
第四,采用适当的刀具路径。
在车削薄壁零件时,为了避免产生振动和变形,应采用适当的刀具路径。
一般来说,应优先选择切削路径中的外切削和镗削,避免内切削和过切削,这样可以减小刀具对零件的负荷,减少振动和变形。
第五,采用适当的刀具进给方式。
在车削薄壁零件时,应采用适当的刀具进给方式,以减小切削力和振动。
一般来说,可以采用铣削进给,即刀具的进给方向与工件的旋转方向相同,这样可以减小刀具对零件的冲击力和振动。
最后,进行切削加工时要进行监控和调整。
在车削薄壁零件时,要进行监控和调整,以确保加工质量。
可以通过加工中的监测手段,例如振动传感器、力传感器等,对加工过程中的切削力、振动等进行监测,及时调整切削参数和刀具路径,以减小振动和变形,保证加工质量。
总之,薄壁零件的车削技巧包括保持机床稳定性、选择合适的切削参数、刀具和夹具、采用适当的刀具路径和进给方式,以及进行监控和调整等。
- 1、下载文档前请自行甄别文档内容的完整性,平台不提供额外的编辑、内容补充、找答案等附加服务。
- 2、"仅部分预览"的文档,不可在线预览部分如存在完整性等问题,可反馈申请退款(可完整预览的文档不适用该条件!)。
- 3、如文档侵犯您的权益,请联系客服反馈,我们会尽快为您处理(人工客服工作时间:9:00-18:30)。
车铣复合高效加工薄壁零件
“工欲善其事、必先利其器”,随着装备制造技术的日益发展,数控机床在机械制造行业得到了广泛应用。
相比传统的单刀架数控机床,车铣复合中心凭借双刀架、双主轴的结构优势,通过双刀架同时切削加工,能够提高加工效率、保证产品质量。
下文将以加工零件A 为例,阐述如何使用车铣复合中心高效加工薄壁零件。
零件A的加工特性:
◆易变形:零件A为环形零件,单边只有18mm,该零件的毛坯为板材弯曲后焊接成形,从结构和毛坯工艺上分析,该零件在加工过程中易产生变形;
◆难加工:该零件的材料为10#钢,因材料很软,在加工过程中不易断屑;
◆精度高:该零件的技术要求主要有:内孔相对于外圆的跳动为0.08mm,外圆公差为
0.097mm,内孔公差为0.063mm。
零件A的加工工艺和加工结果
◆设备简介:
EMCO公司的HT690是一台典型的车铣复合中心,该设备具有两套完全独立的主轴系统,上下刀架可分别对主副轴进行加工、上下刀架通过配置动力刀座可用于铣加工、两套主轴之间可以实现工件的自动对接。
图1:设备结构
◆工艺过程和结果:
在工艺试验中尝试了主副轴均采用卡爪装夹的方法,试验结果内孔变形量0.1~0.2mm,尺寸全部超差。
最终实施的工艺方案是:主轴端采用标准六爪内撑、副轴端采用法兰盘夹具装夹。
从加工结果看,10个零件的内孔变形全部合格,由此可以得出下述结论:副轴端用法兰盘装夹零件的工艺方法是可行的。
◆工艺总结:
⑴主轴端采用标准六爪内撑,车削后的外圆变形在0.08~0.1mm之间,该类型的卡爪可沿圆弧方向作微量摆动,这样就与毛坯有了足够长的接触面积,在毛坯变形大的情况下也可以保证主轴端零件的变形量;
⑵零件变形主要由三种因素引起:夹变形、前道加工变形、焊疤影响;副轴端采用卡爪装夹的方法只能完全反映零件的变形,无法减小前道工序带来的变形;
⑶副轴端采用法兰盘式车夹具,即通过端面螺孔对零件进行夹紧。
该方法使零件仅轴向受力,可消除夹变形影响、减小前道变形和焊疤变形对零件最终变形的影响;
⑷对于零件A这样的软质零件,内孔与端面在夹紧过程中相互影响非常明显:手工装夹时,如果前道加工的端面平面度不好或者零件端面与夹具端面贴合不好,都会使端面不平度间接反映到工件的变形上;
⑸该设备通过主副轴之间的自动对接,可减少一次装夹时间;自动对接时,副轴带动夹具向主轴移动,直至夹具端面与磁轭端面完全贴合、副轴才会停止移动。
该项功能可保证端面平面度及与夹具端面的贴合度,彻底排除了人为因素的影响,保证了产品的质量。
图2:主副轴对接
平衡节拍、高效加工
车铣复合中心的高效在于两套系统的同时加工,但在实际情况中,因加工内容的差异、刀具与机床、夹具、工件之间的干涉,两套系统的节拍往往不能平衡,从而损失了效率。
因此,要根据零件的加工精度和加工要求,在各加工要素互不干涉的前提下,合理安排上下刀塔的加工内容和加工顺序,力求加工时间最短。
从表1中分别统计主副轴加工时间,因副轴端负责精车,加工内容多,因此副轴端所需的加工时间比主轴端多3分钟。
并且由表2可知,老方案的上刀塔加工时间比下刀塔加工时间多3分钟,上刀塔不仅完成主轴端的加工内容,而且承担了一部分副轴端的加工内容,上下刀塔的加工时间并不平衡,因此可以通过增加下刀塔的加工内容来平衡加工节拍。
表1:改善前的加工工序和加工时间(单位:分钟)
表2:改善后的加工工序和加工时间(单位:分钟)
由表1可知,通过增加下刀塔的加工内容、使上下刀塔同时加工,从而达到最佳的加工节拍。
该方案经过改善后,单件加工时间从30分钟/件减少到26分钟/件,加工效率提高13%。
双主轴车铣复合中心的出现为高效加工类似的盘类零件提供了有效契机。
为了满足先进生产力的需要,我们要制定更完善的工艺方案、平衡两通道的加工节拍,在保证零件质量的前提下尽可能提高零件的加工效率,保质保量的完成生产任务。
随着劳动力成本在生产成本中的比例日益增加,多任务机床的推广和使用已成为机加工设备未来发展的趋势。
在转载时请注明出处:东莞市清溪金可迪五金制品有限公司。