PCB制程能力要求
PCB制程能力要求
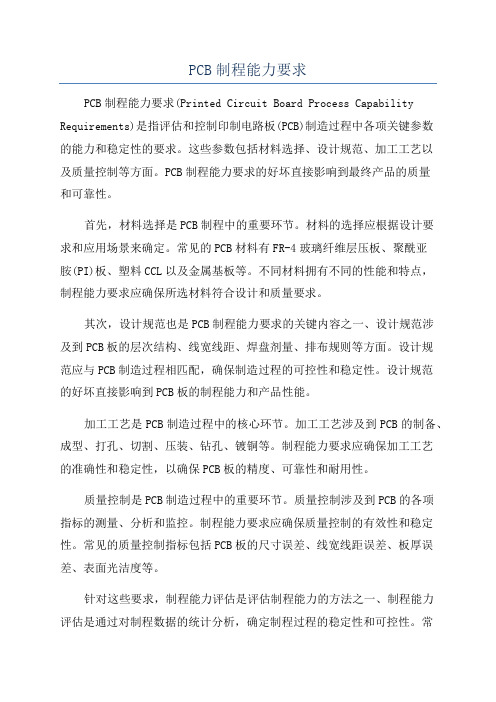
PCB制程能力要求PCB制程能力要求(Printed Circuit Board Process Capability Requirements)是指评估和控制印制电路板(PCB)制造过程中各项关键参数的能力和稳定性的要求。
这些参数包括材料选择、设计规范、加工工艺以及质量控制等方面。
PCB制程能力要求的好坏直接影响到最终产品的质量和可靠性。
首先,材料选择是PCB制程中的重要环节。
材料的选择应根据设计要求和应用场景来确定。
常见的PCB材料有FR-4玻璃纤维层压板、聚酰亚胺(PI)板、塑料CCL以及金属基板等。
不同材料拥有不同的性能和特点,制程能力要求应确保所选材料符合设计和质量要求。
其次,设计规范也是PCB制程能力要求的关键内容之一、设计规范涉及到PCB板的层次结构、线宽线距、焊盘剂量、排布规则等方面。
设计规范应与PCB制造过程相匹配,确保制造过程的可控性和稳定性。
设计规范的好坏直接影响到PCB板的制程能力和产品性能。
加工工艺是PCB制造过程中的核心环节。
加工工艺涉及到PCB的制备、成型、打孔、切割、压装、钻孔、镀铜等。
制程能力要求应确保加工工艺的准确性和稳定性,以确保PCB板的精度、可靠性和耐用性。
质量控制是PCB制造过程中的重要环节。
质量控制涉及到PCB的各项指标的测量、分析和监控。
制程能力要求应确保质量控制的有效性和稳定性。
常见的质量控制指标包括PCB板的尺寸误差、线宽线距误差、板厚误差、表面光洁度等。
针对这些要求,制程能力评估是评估制程能力的方法之一、制程能力评估是通过对制程数据的统计分析,确定制程过程的稳定性和可控性。
常见的制程能力评估方法有过程能力指数(Cpk)、过程性能指数(Ppk)、过程交叉性能指数(Pp/Ppk)等。
针对不同的应用场景和要求,PCB制程能力要求也有所不同。
例如,在高频应用中,对PCB板的信号损耗和传输特性要求较高;在高可靠性应用中,对PCB板的可靠性和耐用性要求较高。
国产PCB制程能力

0间隙拼
是拼版出货,中间板与板的间隙为0
拼版:有间隙拼版间隙
1.6mm
有间隙拼版的间隙不要小于1.6mm,否则锣边时比较困难
抗剥强度
≥2.0N/cm
阻燃性
94V-0
阻抗控atch方式铺铜
厂家是采用还原铺铜,此项用pads设计的客户请务必注意
Pads软件中画槽
最小字符高
≥1mm
字符最小的高度,如果小于1mm,实物板可能会因设计原因造成字符不清晰
字符宽高比
1:05
最合适的宽高比例,更利于生产
表面处理
喷铅锡、喷纯锡、化学沉金、大批量可做防氧化
板厚范围
0.4--3.0mm
华强PCB目前生产常规板厚:0.4/0.6/0.8/1.0/1.2/1.6/2.0 mm,大批量最厚板厚可加工到3.0
最小孔径(机器钻)
0.25mm
机械钻孔最小孔径0.25mm,条件允许推荐设计到0.3mm或以上
孔径公差(机器钻)
±0.07mm
机械钻孔的公差为±0.07mm
孔径公差(激光钻)
±0.01mm
激光钻孔的公差为±0.01mm
过孔单边焊环
3mil
Via最小3mil,器件孔最小5mil,加大过孔焊环对过电流有帮助
国产pcb制程能力项目最高层数加工能力16华强pcb批量加工能力112样品加工能力116华强pcb暂时只允许接受500x500mm以内特殊情况请联系客最大尺寸550x560mmoz55mil成品铜厚15oz66mil成最小线宽线距44miloz条件允许推荐加大线宽线距最小孔径机器025mm孔径公差机器007mm机械钻孔的公差为007mm孔径公差激光001mm激光钻孔的公差为001mmvia最小3mil器件孔最小5mil加大过孔焊环对过电流有帮过孔单边焊环3mil有效线路桥成品外层铜厚成品内层铜厚阻焊类型6mil指的是线路中两块铜皮的连接线宽机械钻孔最小孔径025mm条件允许推荐设计到03mm或以3570um指成品电路板外层线路铜箔的厚度1735um指的是线路中两块铜皮的连接线宽感光油墨白色黑色蓝色绿色黄色红色等字符最小的宽度如果小于015mm实物板可能会因设计原最小字符宽015mm因而造成字符不清晰字符最小的高度如果小于1mm实物板可能会因设计原因造最小字符高1mm成字符不清晰字符宽高比表面处理1
PCB制程规范

1.制定设计规范:(1)限定DIP零件与所有其它零件之安全距离建议数值为2.5mm 最小安全距离为24mil 约0.6mm(为有效解决波峰焊炉后连锡问题,要求所有零件与DIP零件间距>=0.6mm,指pad与pad间的距离)(2)所有DIP零件孔以Thermal relief方式衔接,及十字型导通方式,非全面导通, (为有效提升空焊及锡洞等问题,当PTH接大铜箔时,均需以Thermal relief方式衔接,降低波峰焊时,因热流失过大形成的空焊及吃锡不良问题)(3)拖锡点的导入,为解决DIP零件波峰焊尾数脚短路问题,在制程流向确定后,由制程单位提供拖锡点位置,RD & layout协助放置.(拖锡点直径建议为PAD直径1.225倍距离16~20mil 效果最佳)(4)为增加焊点强度及吃锡性,NPTH孔改为PTH孔.(限制导通除外,单面板需进行成本评估)(5)为降低SMT零件空焊问题,针对0402及0603零件修正其layout尺寸database info:RES_SM_R0402 package, pad-stack (20mil X 24mil ---0.51mm X 0.61mm), pitch 40mil (1.02mm);RES_SM_R0603 package, pad-stack (40mil X 50mil ---1.02mm X1.27mm), pitch 72mil (1.83mm);suggestion:Package 0402: 0.5mm X 0.6mm, Pitch 0.9mm;Package 0603: 0.9mm X 0.9mm, Pitch 1.5mm;(6)多连板的摆放方式,协助提供编排.(7)色环电阻的Ring环尺寸以线径+0.2mm为孔径大小,Ring环单边>=0.2mm (例如线径0.8mm 钻孔就设计1.0mm Ring环单边最少0.2mm)(8)V-cut与边缘chip零件距离要求:※零件方向与V-cut方向平行≧60mil (1.5mm)※零件方向与V-cut方向垂直≧160mil (4mm)(9)BGA边缘禁止置件距离≧50mil (1.25mm),BGA背面零件禁放IC,BGA,connector等大型零件.(10)所有具极性零件,需于PCB板上标示明显清楚的方向.(11)layout设计上需尽可能避免红胶制程,所有零件能放置在与DIP(component Side)同一面为佳,另一面(solder side)如需放置零件,请与DIP零件保持2.5mm以上之距离,方便载具之设计.(12)机种如合适PIP制程之导入,RD零件选用上请注意零件需能承受250度高温5 sec (过SMT reflow后,外观不可改变)。
pcb项目指标

PCB项目指标主要包括以下几个方面:1. 生产能力:PCB制造工厂必须具备一定的生产能力,包括单、双面、多层板,HDI板,高频板,厚板,高密度板(≥2.0mm)以及一些金属基板(铝基、铜基)等不同产品的生产能力。
此外,还需考虑设备到位、产能提升、设备升级及不良品的处理能力等。
2. 质量标准:PCB的质量标准包括外观、阻抗、厚度、线宽/间距、平整度、孔径/孔位精度、阻焊膜/铜膜厚度公差等常规项目,以及预处理(CP)、电镀(PP)、化学镍金(NI)、电镀硬金(硬金PP)等后制程项目。
所有产品在出厂前均需经过严格的质量检测,以确保合格率。
3. 交货周期:PCB项目通常需要一定的生产周期才能完成,具体时间取决于多种因素,如产品类型、数量、生产难度等。
一般来说,客户会根据项目的具体情况给出相应的交期要求,工厂则需要根据自身生产能力及生产周期进行评估和回复。
4. 价格水平:PCB项目的价格通常由工厂成本、利润空间和市场竞争状况等因素综合决定。
工厂需要在保证利润的前提下,综合考虑市场因素和客户需求,为客户提供合理的报价。
5. 客户满意度:客户满意度是衡量PCB项目成功与否的重要指标。
工厂需要不断提高自身服务水平,加强与客户沟通,确保客户对项目的满意度。
6. 环保标准:PCB制造行业是一个环保要求较高的行业,工厂需要遵守各种环保法规,确保生产过程中的环保达标,为客户提供安全、环保的生产环境。
7. 创新与研发:PCB行业是一个技术密集型行业,工厂需要不断投入研发力量,提高产品技术含量,增强市场竞争力。
同时,也需要关注行业发展趋势,不断引进先进设备和技术,提高生产效率和产品质量。
总之,PCB项目的成功与否取决于多个因素的综合作用。
工厂需要不断提高自身生产能力和管理水平,加强与客户沟通,为客户提供安全、环保、优质的产品和服务。
PCB基础培训
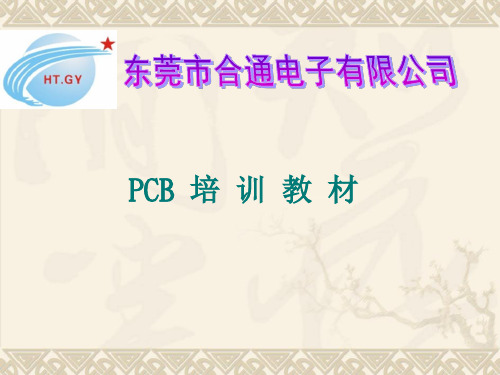
(NG)
(根本解决方 案)
(OK) 曝光线路工艺,线到贴片焊盘的最小安全间隙为0.1mm,若是间 距不足容易造成干膜附着力不够而产生漂浮,导致开路现象。遇到 此类问题时,一般选择填实线路的间隙。
4.双面板线路焊环(Ring)设计标准
(VIA孔) 双面多层板正片线路焊环设计:
(PTH孔)
VIA孔(导通孔)焊环最小为0.15mm,PTH孔焊环最小为0.2mm。
另外线路大铜面如要设计网格方式,网格的线宽线距最佳做 0.25/0.25mm或更大一点,这样的设计有助与线路显影后的干膜碎减少 且大,为提升线路制程的良率而起到关键作用。
線徑/線距(H/H 、1/1、 2/2) Line width/spacing (H/H、 1/1、 2/2)
最小孔徑(钻孔) Min. Hole Size (Before Plating)
各層通孔對準度 Registration Between Layers
防焊誤差值 Solder Mask Tolerance
10mil 0.25mm +/-4mil +/-0.1mm +/-3mil +/-0.076mm
4mil 0.1mm +/-4mil +/-0.1mm
20″×30″
6:1
8mil 0.2mm
PCB钻孔制程
1.单面板孔径制作: 1)钻孔及模冲成型一般孔径公差都是+/-0.lmm 2)针对孔径要求高的公差可以达到+/-0.05mm,但此模具必须开
PCB板材分类
7、铝基板材:是一种三明治结构,由基材为铝+导热绝缘 材料+铜箔的特殊散热板材。(采用铝基板主要是注重此板 材的高散热性能,一般导热率为1--2W/M-K)
PCB制程能力尺寸公差设计规范_相互

PCB制程能力尺寸公差设计规范_相互PCB制程能力尺寸公差设计规范是指在PCB(Printed Circuit Board,印刷电路板)的制作过程中,确定各个元件的尺寸精度范围,以保证PCB的质量和可靠性。
下面将介绍一些常用的PCB制程能力尺寸公差设计规范。
1.组件尺寸公差:在设计PCB时,需要确定每个元件的尺寸公差。
尺寸公差是指元件在制造过程中,其实际尺寸与设计尺寸之间可以接受的最大偏差。
常用的尺寸公差包括线宽、线间距、焊盘尺寸、焊盘间距等。
2.PCB板厚公差:PCB板厚是指PCB板在垂直方向上的厚度,其厚度公差是指板厚的实际测量值与设计值之间允许的最大差异。
一般来说,PCB板的厚度公差为±10%。
3. 孔径公差:孔径公差是指PCB板上的孔的尺寸偏差。
常见的孔有贯穿孔和盲孔,其公差会直接影响到后续的插件焊接和组装工艺。
一般来说,孔径公差应控制在±0.05mm以内。
4. 焊盘公差:焊盘公差是指焊盘的尺寸偏差,焊盘是PCB上焊接元器件的位置,其尺寸的公差可以影响到元器件的插拔和焊接质量。
一般来说,焊盘公差应控制在±0.05mm以内。
5. 线宽和线间距公差:线宽和线间距是PCB上导线的尺寸,其公差可以影响到导线的导电性能和阻抗匹配。
一般来说,线宽和线间距的公差应控制在±0.05mm以内。
综上所述,PCB制程能力尺寸公差设计规范是确保PCB制造过程中各个元件的尺寸精度范围,以保证PCB的质量和可靠性。
通过对组件尺寸公差、PCB板厚公差、孔径公差、焊盘公差以及线宽和线间距公差等要素的控制,可以有效避免制造过程中的尺寸偏差,提高PCB的可靠性和稳定性。
pcb板制作工艺及制程能力简介

最小孔径
纵横比 最厚板厚 最薄板厚
0.2mm
≦ 6:1 3.0mm (最小孔径原则为≦ 6:1) 0.1mm
沉铜速率
15+/-5u”
备注:对于PTFE材质的生产板在沉铜工序采用了PI调整剂进行调整,提高孔化良率。同时沉铜工序采用的是 自动化程序,其产品可控性强,部分生产板还可以采用两次沉铜工艺进行生产提升沉铜品质
金手指电金
化学沉银 化学沉金
防氧化
较好的焊接性,良好的平整性,低廉成本,但是上件环境有比较严的要求,
目前应用量仅次于沉金
佰生技术部
bestprint
B&P
昆山市佰生电子元件厂
制程能力:
表面处理类型 喷锡 电镍金 金手指 化学沉银 化学沉金 防氧化 锡厚 镍层 金厚 金厚 银厚 镍厚 金厚 膜厚 喷锡;电镍金;金手指电金;化银;化金;防氧化等 3-38um 2.5-8.0um 1-2u” 3-40u” 6-18u” 2.5-8.0um 1-3u” 0.2-0.6um
佰生技术部
bestprint
B&P
昆山市佰生电子元件厂
7:图形电镀
目的:
在显影后的铜层上进行电镀,将面上以及孔内电镀到符合客户要求铜厚。
图形电镀又称二次铜和电铜锡,因此此工序不仅仅是加厚铜层,同时还需要在铜层上加电上一 层锡。
同时对图形电镀的理解为电镀客户所需要的各类连接线涵盖接电线以及焊接pad…
孔径公差
孔位公差 槽宽公差 NPTH孔径公差
≦ 0.0254mm
≦ 0.075mm +/-0.1mm +/-0.05mm
备注:可以加工各类异型孔,如锥形沉头孔,直角沉头孔,深度孔等等
PCB板制程能力及设计通用规范参考

PCB板制程能力及设计通用规范参考1、开料最大开料尺寸:530×630mm 最大厚度:≤3.2mm 最小厚度:≥0.15mm2、钻孔最小孔径:≥0.2mm(钻孔刀具0.25mm)最小槽孔:≥0.65mm(刀具0.8MM) 最大孔径:≤6.4mm(>6.5的孔扩孔或改锣)孔径公差:PTH:≥0.075mm,NPTH:0.05mm 孔位公差:0.075-0.1 mm同网络的孔边到孔边间距最小0.3MM,否则钻孔容易断刀不同网络的孔边到孔边间距最小0.5MM,否则容易孔壁微短PCB板制程能力3、沉铜(PTH)最薄板:≥0.2mm 板厚:孔径≥5:14、线路最小线径/线距:金板:4/4mil,锡或沉金:5/5mil 过孔焊环单边:0.12-0.15mm最小插件孔环宽:金板:单边≥0.2mm 锡板: 单边≥0.25mm椭圆焊盘:窄边做0.15mm以上焊环设计建议:线路到贴片及贴片到地线铜皮安全间距≥0.25mm ,若设计0.15以下很容易短路内层独立孔距铜皮:≥0.35mm 内层孔到线0.3 MM 过孔焊盘到地线≥0.2mm5、阻焊最大铜厚:30z,焊盘开窗:单边0.1(BGA≥ 0.05)mm,厚度:10-15um绿油桥最小宽度:0.12mm,绿油到线安全距:≥0.15mm,丝印最小网格:0.35×0.35mm 6、字符字符宽:≥0.15mm 字符距PAD:≥0.17mm,字符距外形:≥0.2mm字高:≥0.9 mm 字符不要设计在开窗焊盘上丝印位号及字符框到焊盘≥0.2mm7、啤板最大板面:200×300mm 外型公差:+/-0.1mm (精密模+/-0.05)最大板厚:2.0mm 孔边到外形安全距离:>0.3mm,板越厚距离越大线到外形安全距离:大于0.4mm8、锣板最小槽孔:0.8mm 最小线或PAD到边距离:0.3mm 最大锣板尺寸:550X650mm(小机550×410)孔到边距离:最小0.3mm 外形公差:+/-0.13定位销钉:最小1.5mm(若无工艺边拼版时一定要在板内设计大于1.5的定位孔)9、V-cut角度:30°、20° 板厚:0.4-2.0mm (0.4板厚只能单面V-CUT)V割安全间距:即安全间距内不能布线和放置贴片板厚:①0.2-0.6mm ≥0.3mm ②0.8-1.0mm ≥0.4mm③1.2-1.6mm ≥0.5mm ④2.0mm ≥0.7mm最小横尺寸:40~380mm 纵尺寸:≥80mm(客户自已拼版时一定要注意此尺寸,即V-CUT 方向的尺寸必须大于80MM) 横向最大不可超过:380mm若横众向都要V-CUT则拼版都需≥80mm10、板厚公差:±10﹪(工艺增厚约:0.08-0.1mm,H/H OZ计)0.4±0.08mm 0.6±0.08mm 0.8±0.1mm 1.0±0.1mm1.2±0.12mm 1.6±0.16 mm2.0±0.2mm3.0±0.25 mm11、飞测:最大面积:520×400mm;治具测:最大板长:580MM12.其它建议:1)POWER 或PADS 文件请不要将槽孔,定位孔,外形和焊盘或大铜面的开窗等需要在板上作出来的东西设置在非正常层,正常为:TOP——BOT层;21,28阻焊层;26,29丝印层,24分孔层(有些客户习惯将槽孔不放在24层而开窗图却又放在22,27层的锡膏层或贴片层,这样容易漏掉)2)不用板厂作出来的东西不要设置在正常层,更不要在每一层都放置,如二维线等,特别是线路层3)PADS设计的文件板厂通常是用Hatch(Hatch All)铺铜,而不用Flood(Flood All)铺铜。
- 1、下载文档前请自行甄别文档内容的完整性,平台不提供额外的编辑、内容补充、找答案等附加服务。
- 2、"仅部分预览"的文档,不可在线预览部分如存在完整性等问题,可反馈申请退款(可完整预览的文档不适用该条件!)。
- 3、如文档侵犯您的权益,请联系客服反馈,我们会尽快为您处理(人工客服工作时间:9:00-18:30)。
1.目的
根据现有PCB供应商的设备条件、工艺基础、管理水平,以及研发部PCB设计的工艺需求,规定公司对PCB供应商现在及未来批量生产的制程水准的要求。
用于指导PCB的设计、指引PCB供应商制程能力的开发、指导新PCB供应商的开发和认证,同时作为PCB 供应商与我司的一个基本约定,指导合同评审和问题仲裁。
2.引用/参考标准或资料
IEC-60194 印制板设计、制造与组装术语与定义
IPC-6011 印制板通用性能规范
IPC-6012A 刚性印制板鉴定及性能规范
IPC-A-600F 印制板的验收条件
3.名词解释
3.1 一般名词
双面印制板(Double-side printed board):两面均有导电图形的印制板。
本文特指只有两层的PCB板,通常简称“双面板”。
多层印制板(Multilayer printed board):三层或更多层印制板线路和/或印制电路层由刚性或挠性绝缘材料交替粘合到一起并作电气互连的印制板的通称。
简称“多层板”。
金属芯印制板(Metal core printed board):采用金属芯基材的印制板。
通常用铝、铜、铁作为金属芯。
刚性印刷板(Rigid printed board):仅使用刚性基材的印制板。
挠性印刷板(Flexible printed board):应用挠性基材的单面、双面或多层印制电路或印刷线路组成的印制板。
铜厚(Copper thickness):PCB制作要求中所标注的铜厚度为最终铜厚,即:铜箔厚度+镀层铜厚。
厚铜箔印制板(Thick-copper printed board):任意一层铜厚的设计标称值超过(不包括)2oz/70um的印制板,通称为厚铜箔印制板。
简称“厚铜板”。
成品厚度(Production board thickness或Thickness of finished board):最终成品板的厚度,包括阻焊厚度,不包括蓝胶或其他暂时性的包装物、保护性粘接纸等。
简称“板厚”。
3.2 等级定义
进行等级定义的目的:
1、评价和区分PCB供应商的能力,明确对供应商的技术要求,牵引其改善;
2、评价PCB的可生产性,以牵引PCB的设计,降低制造难度,扩大制程的工艺窗口。
工序的技术能力等级有别于最终成品的验收等级,即运用不同能力生产的产品,最终检验标准可能一样。
比如不同的线宽、间距能力,最终都不能有短路、断路等缺陷。
技术的发展、新标准的推行、客户要求的提升也在推动PCB的进步,因此规范中的制程能力等级会发生变化,比如新设备的应用、新技术的开发、工艺管制水平提高等,等级会
从高级别降为低级别。
本文中结合各供应商相同制程的各自实际水平、业界标准、将制程能力等级分成4级。
由于产品开发的超前性、标准的滞后性,因此以供应商实践作为主要依据,其他作为补充说明或参考。
(见下表)
注:
1、本文按照单面、双面及多层板分别说明,已经体现了一定的等级差异(比如制程复
杂程度),因此部分相同的工序,其级别在不同类型的印制板中实际上有了不同涵
义。
为了尽量减少差异,有些工序直接从2、3级开始;
2、综合评价某个印制板时,应该取其所有工序中的最高等级为该印制板的等级;
3、同一类别的印制板,其级别只向下兼容,即具备高级别的制程,自然具备同样制程
低级别能力,比如同样条件下,最小线宽间距6mil(Class 3),自然兼容最小线宽间
距10mil(Class 2)。
4.内容
4.1 通用要求
4.1.1 文件处理
光绘文件最大尺寸:508mmX660mm(20”X26”),光绘精度:±0.01mm
4.1.2 板材类型
可供选择的板材类型有(包括基材和半固化片):
4.1.3 板厚公差
4.1.4 钻孔
孔的种类按功能分:元件孔、导通孔、埋孔、盲孔、安装孔、定位孔等;按加工工艺分:金属化孔(PTH )和非金属化孔(NPTH )。
一般情况下,元件孔、导通孔、埋孔、盲孔采用金属化孔,安装孔、定位孔采用非金属化孔。
非金属化孔(NPTH )
孔的中心必须在以孔的设计中心为圆心,偏差值为半径的圆内。
4.1.5 图形
若无特殊说明,内层图形、外层图形要求相同。
各距离定义如下图所示:
图注:A :线路宽度;B
:线路间距;C :PTH 孔壁至线路距离;D :PTH 孔壁至PTH
孔壁距离;E :SMD 焊盘至线路距离;F :SMD 焊盘至SMD 焊盘距离;G :SMD 焊盘至PTH 孔壁距离。
4.1.6 外形加工
4.1.7 表面处理
4.1.8 阻焊
4.1.9 字符
这里的字符指油漆印刷字符,非蚀刻的阻焊负字符、铜箔负字符。
4.1.10 标准材料
所列标准材料为推荐要求,并非强制,但需要变更时,必须提前互相知会,以便留有足够的时间进行试验、评估、沟通和确认。
无论采用何种材料,不仅该材料要符合其国际标准,而且用其加工成的成品最终品质指标要满足相应的标准。
4.1.10.1 半固化片
4.1.10.2 板材
4.1.10.3 铜箔
4.1.1 UL
所有成品必须获得UL机构的认证,并标明UL档案号
4.2 单面、双面及多层印制板
本节所述内容适用于铜厚≤2oz(70um)、20um≤孔铜厚≤35um的单面、双面及多层印制板,如无特殊说明,基材类型都是刚性基材FR4和半固化片FR4。
关于单面、双面及多层板的其他内容,直接引用4.1 通用要求。
4.2.1 层数
4.2.2 拼板尺寸
注:最大拼板尺寸也是单个印制板的最大尺寸;最小拼板尺寸也是单个印制板的最小尺寸。
4.2.3 铜厚公差
4.2.4 层压厚度
板厚的标称值(设计值)。
必须兼顾铜厚公差、最终板厚公差、工艺调制能力给定。
4.2.5 翘曲
注:同时存在SMT和THT时,按SMT的要求。