金属全冠制作常见问题铸道安插不当
铸造铸件常见缺陷原因与解决方法分析

铸造铸件常见缺陷原因与解决方法分析前言铸造工艺过程复杂,影响铸件质量的因素很多,往往由于原材料控制不严,工艺方案不合理,生产操作不当,管理制度不完善等原因,会使铸件产生各种铸造缺陷。
常见的铸件缺陷名称、特征和产生的原因,详见下表。
★ 常见铸件缺陷及产生原因★缺陷名称特征产生的主要原因气孔在铸件内部或表面有大小不等的光滑孔洞①炉料不干或含氧化物、杂质多;②浇注工具或炉前添加剂未烘干;③型砂含水过多或起模和修型时刷水过多;④型芯烘干不充分或型芯通气孔被堵塞;⑤春砂过紧,型砂透气性差;⑥浇注温度过低或浇注速度太快等缩孔与缩松缩孔多分布在铸件厚断面处,形状不规则,孔内粗糙①铸件结构设计不合理,如壁厚相差过大,厚壁处未放冒口或冷铁;②浇注系统和冒口的位置不对;③浇注温度太高;④合金化学成分不合格,收缩率过大,冒口太小或太少砂眼在铸件内部或表面有型砂充塞的孔眼①型砂强度太低或砂型和型芯的紧实度不够,故型砂被金属液冲入型腔;②合箱时砂型局部损坏;③浇注系统不合理,内浇口方向不对,金属液冲坏了砂型;④合箱时型腔或浇口内散砂未清理干净粘砂铸件表面粗糙,粘有一层砂粒①原砂耐火度低或颗粒度太大;②型砂含泥量过高,耐火度下降;③浇注温度太高;④湿型铸造时型砂中煤粉含量太少;⑤干型铸造时铸型未刷涂斜或涂料太薄夹砂铸件表面产生的金属片状突起物,在金属片状突起物与铸件之间夹有一层型砂①型砂热湿拉强度低,型腔表面受热烘烤而膨胀开裂;②砂型局部紧实度过高,水分过多,水分烘干后型腔表面开裂;③浇注位置选择不当,型腔表面长时间受高温铁水烘烤而膨胀开裂;④浇注温度过高,浇注速度太慢铸件沿分型面有相对位置错移①模样的上半模和下半模未对准;②合箱时,上下砂箱错位;③上下砂箱错型未夹紧或上箱未加足够压铁,浇注时产生错箱冷隔铸件上有未完全融合的缝隙或洼坑,其交接处是圆滑的①浇注温度太低,合金流动性差;②浇注速度太慢或浇注中有断流;③浇注系统位置开设不当或内浇道横截面积太小;④铸件壁太薄;⑤直浇道(含浇口杯)高度不够;⑥浇注时金属量不够,型腔未充满浇不足铸件未被浇满裂纹铸件开裂,开裂处金属表面有氧化膜①铸件结构设计不合理,壁厚相差太大,冷却不均匀;②砂型和型芯的退让性差,或春砂过紧;③落砂过早;④浇口位置不当,致使铸件各部分收缩不均匀★ 常见铸件缺陷及预防措施★序缺陷名称缺陷特征预防措施1 气孔在铸件内部、表面或近于表面处,有大小不等的光滑孔眼,形状有圆的、长的及不规则的,有单个的,也有聚集成片的。
铸造缺陷原因及其解决方法

铸造缺陷原因及其解决方法
铸造缺陷是铸造行业经常出现的一类问题,对铸件的功能和使用寿命有负面影响。
在近年来,随着材料科学领域的进步,铸铁、钢、金属等的性能越来越高,越来越多的新型铸造形式和新型工艺方法被开发出来,但是铸造缺陷依然存在,需要及时解决。
铸造缺陷的原因很复杂,主要有以下几类:一是铸件的铸造工艺参数不当,包括铸件尺寸参数不合理,成型材料未能满足要求,流体特性、温度、压力等参数不足;二是模具设计过程中出现问题,包括模具结构设计不当、表面材质不满足要求等;三是原料误差,原料中病害比例高,导致铸件组织结构不稳定,抗拉强度低。
解决铸造缺陷的方法:一是针对工艺参数不当,应采取有效的治理措施,进行工艺参数的优化及控制,在模具设计中加强细部处理或使用更高性能的材料;二是对原材料误差,应采取措施分离优良料和劣料,保证原料质量,增加试验对原料力学和化学性质检测,改善铸件质量;三是在成型前,应做出正确的实验,要求较高,确保模具尺寸精度,应用胶粉注射成型增加工艺性能。
通过科学的铸造工艺参数设计,优质的原材料配置,模具精细设计,合理的实验控制,减少不合格品,增加铸件质量,都可以有效地解决铸造缺陷的问题。
只有把解决这些铸造缺陷的解决方案扎实,从技术、过程、品质等角度进行多方面开展,才能保证铸件的功能以及使用寿命,有助于企业提升铸件的整体质量水平,建立良好的企业形象。
第十一章 固定义齿制作中出现的问题及处理
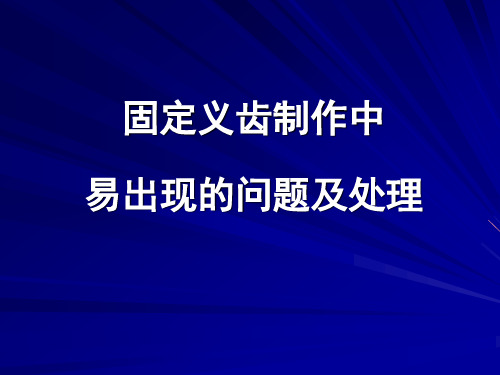
印模颈部边缘狭小 采用震荡或真空灌注
(二)蜡模制作不当
原因 蜡型材料选择不当 蜡型材料不纯 熔化蜡的温度不恰当 蜡模厚薄不均 蜡模反复修改
预防
选择流动变形率和热膨胀率 都较低的铸造蜡制作蜡模。
铸造蜡中不能混合有其他蜡 铸造蜡的熔点范围一般在70 度左右。 蜡模厚薄均匀
避免反复修改
二、冠桥熔模翘动
分钟 6.控制铸型的焙烧温度和熔金温度,烘烤的时间要达到要求 7.选择粗糙度和耐火度适当的包埋材料 8. 研磨是不同的部位选用不同的磨具,采取适当的研磨速度和压
力 9. 在合金块熔化崩塌达到熔铸时机要求的一瞬间进行铸造,使熔
金的温度尽可能低
六.金属瘤
由于包埋料调拌食混入空气或包埋方法不当,在熔模的凹 陷处附着气泡,包埋料结固后,气泡形成圆形的空穴,熔 铸时液体合金流入空穴中,在铸件表面形成金属瘤 预防措施: –仔细对熔模进行脱脂 –调拌包埋料一定要注意排除气泡,包埋料最好采用真
原因
预防
(一)分离剂涂布过多
分离剂涂布合适
(二)蜡熔化温度过低
铸造蜡的熔点范围一般在70 度左右。
(三) 蜡型材料选择不当 选择形变率较小的铸造蜡
熔模变
形
外界温度影响 熔模制作好后,应立即包埋
(四)桥体过长
分段制作,焊接起来
(五)修改不当
禁止离开模型对熔模进行加 蜡修改
三、冠轴面突度不适
原因 唇颊舌轴面突度不适
固定义齿制作中 易出现的问题及处理
冠、桥熔模制作中常见的问题及处理
一、边缘不密合
(一)石膏模型颈部边缘不准确
原因
预防
印模材料调拌过稀或 过稠 不正确
的印模 印模性能
制取和
金属全冠试题及答案
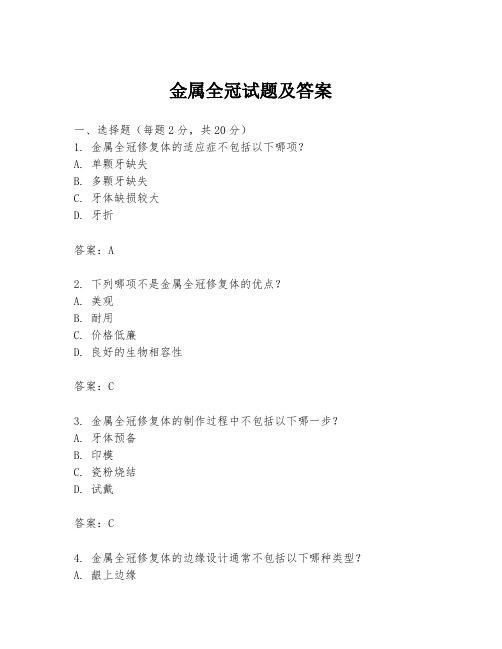
金属全冠试题及答案一、选择题(每题2分,共20分)1. 金属全冠修复体的适应症不包括以下哪项?A. 单颗牙缺失B. 多颗牙缺失C. 牙体缺损较大D. 牙折答案:A2. 下列哪项不是金属全冠修复体的优点?A. 美观B. 耐用C. 价格低廉D. 良好的生物相容性答案:C3. 金属全冠修复体的制作过程中不包括以下哪一步?A. 牙体预备B. 印模C. 瓷粉烧结D. 试戴答案:C4. 金属全冠修复体的边缘设计通常不包括以下哪种类型?A. 龈上边缘B. 平齐边缘C. 龈下边缘D. 无边缘答案:D5. 金属全冠修复体的固位力主要来源于以下哪部分?A. 牙体预备的深度B. 牙体预备的形状C. 牙体预备的表面处理D. 以上都是答案:D6. 金属全冠修复体的咬合设计中,以下哪项是错误的?A. 避免咬合过紧B. 避免咬合过松C. 避免咬合不均D. 咬合面应设计成尖锐的边缘答案:D7. 金属全冠修复体的金属材质通常不包括以下哪种?A. 金合金B. 钴铬合金C. 钛合金D. 不锈钢答案:D8. 金属全冠修复体的制作过程中,以下哪项是不必要的?A. 牙体预备B. 印模C. 瓷粉烧结D. 试戴答案:C9. 金属全冠修复体的修复效果评估中,以下哪项不是评估标准?A. 边缘密合度B. 咬合关系C. 颜色匹配D. 患者的年龄答案:D10. 金属全冠修复体的维护中,以下哪项是不正确的?A. 定期复查B. 避免硬食C. 定期清洁D. 可以随意咬硬物答案:D二、填空题(每题2分,共20分)1. 金属全冠修复体的边缘设计通常包括________、________和________三种类型。
答案:龈上边缘、平齐边缘、龈下边缘2. 金属全冠修复体的制作过程中,牙体预备后需要进行________,然后进行________。
答案:印模、试戴3. 金属全冠修复体的固位力主要来源于牙体预备的________和________。
答案:深度、形状4. 金属全冠修复体的咬合设计中,应避免________和________。
常见铸造缺陷产生的原因及防止方法

常见铸造缺陷产生的原因及防止方法铸件缺陷种类繁多,产生缺陷的原因也十分复杂.它不仅与铸型工艺有关,而且还与铸造合金的性制、合金的熔炼、造型材料的性能等一系列因素有关.因此,分析铸件缺陷产生的原因时,要从具体情况出发,根据缺陷的特征、位置、采用的工艺和所用型砂等因素,进行综合分析,然后采取相应的技术措施,防止和消除缺陷.一、浇不到1、特征铸件局部有残缺、常出现在薄壁部位、离浇道最远部位或铸件上部.残缺的边角圆滑光亮不粘砂.2、产生原因1 浇注温度低、浇注速度太慢或断续浇注;2 横浇道、内浇道截面积小;3 铁水成分中碳、硅含量过低;4 型砂中水分、煤粉含量过多,发气量大,或含泥量太高,透气性不良;5 上砂型高度不够,铁水压力不足.3、防止方法1 提高浇注温度、加快浇注速度,防止断续浇注;2 加大横浇道和内浇道的截面积;3 调整炉后配料,适当提高碳、硅含量;4 铸型中加强排气,减少型砂中的煤粉,有机物加入量;5 增加上砂箱高度.二、未浇满1、特征铸件上部残缺,直浇道中铁水的水平面与铸件的铁水水平面相平,边部略呈圆形.2、产生原因1 浇包中铁水量不够;2 浇道狭小,浇注速度又过快,当铁水从浇口杯外溢时,操作者误认为铸型已经充满,停浇过早.3、防止方法1 正确估计浇包中的铁水量;2 对浇道狭小的铸型,适当放慢浇注速度,保证铸型充满.三、损伤1、特征铸件损伤断缺.2、产生原因1 铸件落砂过于剧烈,或在搬运过程中铸件受到冲撞而损坏;2 滚筒清理时,铸件装料不当,铸件的薄弱部分在翻滚时被碰断;3 冒口、冒口颈截面尺寸过大;冒口颈没有做出敲断面凹槽.或敲除浇冒口的方法不正确,使铸件本体损伤缺肉.3、防止方法1 铸件在落砂清理和搬运时,注意避免各种形式的过度冲撞、振击,避免不合理的丢放;2 滚筒清理时严格按工艺规程和要求进行操作;3 修改冒口和冒口颈尺寸,做出冒口颈敲断面,正确掌握打浇冒口的方向.四、粘砂和表面粗糙1、特征粘砂是一种铸件表面缺陷,表现为铸件表面粘附着难以清除的砂粒;如铸件经清除砂粒后出现凹凸不平的不光滑表面,称表面粗糙.2、产生原因1 砂粒太粗、砂型紧实度不够;2 型砂中水分太高,使型砂不易紧实;3 浇注速度太快、压力过大、温度过高;4 型砂中煤粉太少;5 模板烘温过高,导致表面型砂干枯;或模板烘温过低,型砂粘附在模板上.3、防止方法1 在透气性足够的情况下,使用较细原砂,并适当提高型砂紧实度;2 保证型砂中稳定的有效煤粉含量;3 严格控制砂水分;4 改进浇注系统,改进浇注操作、降低浇注温度;5 控制模板烘烤温度,一般与型砂温度相等或略高.五、砂眼1、特征在铸件内部或表面充塞有型砂的孔眼.2、产生原因1 型砂表面强度不够;2 模样上无圆角或拔模斜度小导致钩砂、铸型损坏后没修理或没修理好就合箱;3 砂型在浇注前放置时间过长,风干后表面强度降低;4 铸型在合箱时或搬运过程中损坏;5 合箱时型内浮砂未清除干净,合箱后浇口杯没盖好,碎砂掉进铸型.3、防止方法1 提高型砂中粘士含量、及时补加新砂,提高型砂表面强度;2 模样光洁度要高,并合理做出拔模斜度和铸造圆角.损坏的铸型要修好后再合箱;3 缩短浇注前砂型的放置时间;4 合箱或搬运铸型时要小心,避免损坏或掉入砂型腔砂粒;5 合箱前清除型内浮砂,并盖好浇口.六、披缝和胀砂1、特征披缝常出现在铸件分型面处,是垂直于铸件表面,且厚薄不均匀的薄片状金属突起物. 胀砂是铸件内、外表面局部胀大,形成不规则的瘤状金属突起物.2、产生原因1 紧实度不够或不匀;2 面砂强度不够、或型砂水分过高;3 液态金属压头过大、浇注速度太快.3、防止方法1 提高铸型紧实度、避免局部过松;2 调整混砂工艺、控制水分,提高型砂强度;3 降低液态金属的压头、降低浇注速度.七、抬箱1、特征铸件在分型面处有大面积的披缝,使铸型外形尺寸发生变化.抬箱过大,造成跑火——铁水自分型面外溢,严重时造成浇不足缺陷.2、产生原因1 砂箱未紧固、压铁质量不够或去除压铁过早;2 浇注过快,冲击力过大;3 模板翅曲.3、防止方法1 增加压铁重量,特铁水凝固后再去除压铁;2 降低浇包位置,降低浇注速度;3 修正模板.八、掉砂1、特征铸件表面上出现的块状金属突起物,其外形与掉落的砂块很相似.在铸件其它部位,则往往出现砂眼或残缺.2、产生原因1 模样上有深而小的凹槽,同于结构特征或拔模斜度小,起模时将砂型带坏或震裂;2 紧实度不匀,铸型局部强度不足;3 合箱、搬运铸型时,不小心使铸型局部砂块掉落.3、防止方法1 模样拔模斜度要合适、表面光洁;2 铸型紧实度高且均匀;3 合箱、搬运过程中,操作小心.九、错型错箱1、特征铸件的一部分与另一部分在分型面的接缝处错开,发生相对位移,使铸件外形与图纸不相符合.2、产生原因1 模样制作不良,上下模没有对准或模样变形;2 砂箱或模板定位不准确,或定位销松动;3 挤压造型机上零件磨损,例如正压板下衬板、反压板轴承的磨损等;4 浇注时用的套箱变形,搬运、围箱时不注意,使上下铸型发生位移.3、防止方法1 加强模板的检查和修理;定2 经常检查砂箱、模板的定位销及销孔、并合理地安装;3 检查挤压造型机的有关零件,及时调整,磨损大的要更换;4 定期对套箱整形.脱箱后的铸型在搬运时要小心.在面浇注的砂型,应该做一排砂型围一排.十、灰口和麻点1、特征铸件断口呈灰黑色或出现黑色小点,中心部位较多,边部较少,金相观察可见到片状石墨.2、产生原因1 铁水化学成分不合要求,碳、硅含量过高;2 炉前孕育的铋加入浇包内过早或过迟,或是铋量不足.3、防止方法1 正确选择化学成分,合理配料,使铁水中碳、硅量在规定范围内;2 增加铋的加入量并严格炉前孕育工艺.十一、裂纹热裂、冷裂1、特征铸件外部或内部有穿透或不穿透的裂纹.热裂时带有暗色或黑色的氧化表面断口外形曲折.冷裂是较干净的脆性裂纹,断口较平,具有金属光泽或轻微的氧化色泽.2、产生原因1 铁水中碳、硅含苞欲放量过低,含硫量过高;2 浇注温度过高;3 冒口颈过大、过短,造成局部过热严重,或重口太小,补缩不好;4 铸件在清理、运输过程中,受冲击过大.3、防止方法1 控制铁水化学成分在规定的范围内;2 降低浇注温度;3 合理设计冒口系统;4 铸件在清理、运输过程中避免过度冲击.十二、气孔1、特征气孔的孔壁光滑明亮,形状有圆形、梨形和针状,孔的尺寸有大有小,产生在铸件表面或内部.铸件内部的气孔在敲碎后或机械加工时才能被发现.2、产生原因1 小炉料潮湿、锈蚀严重或带有油污,使铁水含气量太多、氧化严重;2 出铁孔、出铁槽、炉衬、浇包衬未洪干;3 浇注温度较低,使气体来不及上浮和逸出;4 炉料中含铝量较高,易造成氢气孔;5 砂型透气性不好、型砂水分高、含煤粉或有机物较多,使浇注时产生大量气体且不易排出.3、防止方法1 炉料要妥善管理,表面要清洁;2 炉缸、前炉、出铁口、出铁槽、浇包必须烘干;3 提高浇注温度;4 不使用铝量过高的废钢;5 适当降低型砂的水分、控制煤粉加入量,扎通气孔等.十三、缩松、疏松1、特征分散、细小的缩孔,带有树枝关结晶的称缩松,比缩松更细小的称疏松.常出现在热世部位.2、产生原因1 铁水中碳、硅含量过低,收缩大;2 浇注速度太快、浇注温度过高,使得液态收缩大;3 浇注系统、冒口设计不当,无法实现顺序凝固;4 冒口太小,补缩不充分.3、防止方法1 控制铁水的化学成分在规定范围内;2 降低浇注速度和浇注温度;3 改进浇冒口系统,利用顺序凝固;4 加大冒口体积,保证充分补缩.十四、反白口1、特征铸件断口内部出现白口组织,边缘部分出现灰口.2、产生原因1 碳、硅含量较高的铁水,含氢量过高;2 炉料中带入的铬等白口形成元素过多;3 元素偏析严重;3、防止方法1 控制化学成分、碳、硅含量不宜过高;2 炉衬、包衬要烘干;型砂水分不宜过高;3 加强炉料管理,减少带入白口化元素.。
金属烤瓷全冠修复后常见问题的分析及应对措施
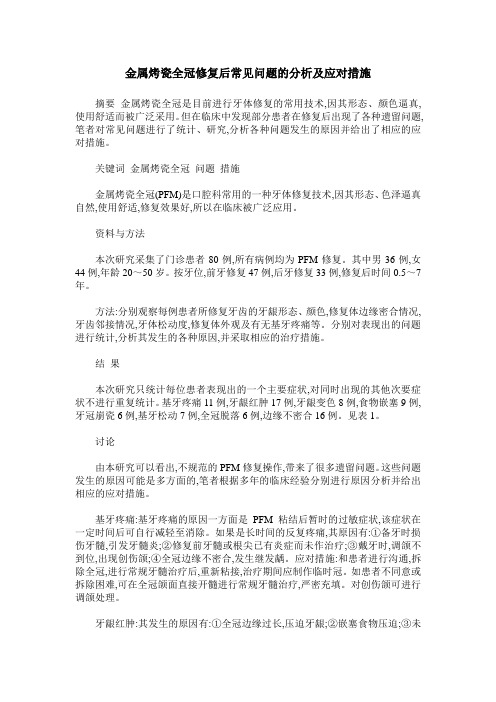
金属烤瓷全冠修复后常见问题的分析及应对措施摘要金属烤瓷全冠是目前进行牙体修复的常用技术,因其形态、颜色逼真,使用舒适而被广泛采用。
但在临床中发现部分患者在修复后出现了各种遗留问题,笔者对常见问题进行了统计、研究,分析各种问题发生的原因并给出了相应的应对措施。
关键词金属烤瓷全冠问题措施金属烤瓷全冠(PFM)是口腔科常用的一种牙体修复技术,因其形态、色泽逼真自然,使用舒适,修复效果好,所以在临床被广泛应用。
资料与方法本次研究采集了门诊患者80例,所有病例均为PFM修复。
其中男36例,女44例,年龄20~50岁。
按牙位,前牙修复47例,后牙修复33例,修复后时间0.5~7年。
方法:分别观察每例患者所修复牙齿的牙龈形态、颜色,修复体边缘密合情况,牙齿邻接情况,牙体松动度,修复体外观及有无基牙疼痛等。
分别对表现出的问题进行统计,分析其发生的各种原因,并采取相应的治疗措施。
结果本次研究只统计每位患者表现出的一个主要症状,对同时出现的其他次要症状不进行重复统计。
基牙疼痛11例,牙龈红肿17例,牙龈变色8例,食物嵌塞9例,牙冠崩瓷6例,基牙松动7例,全冠脱落6例,边缘不密合16例。
见表1。
讨论由本研究可以看出,不规范的PFM修复操作,带来了很多遗留问题。
这些问题发生的原因可能是多方面的,笔者根据多年的临床经验分别进行原因分析并给出相应的应对措施。
基牙疼痛:基牙疼痛的原因一方面是PFM粘结后暂时的过敏症状,该症状在一定时间后可自行减轻至消除。
如果是长时间的反复疼痛,其原因有:①备牙时损伤牙髓,引发牙髓炎;②修复前牙髓或根尖已有炎症而未作治疗;③戴牙时,调颌不到位,出现创伤颌;④全冠边缘不密合,发生继发龋。
应对措施:和患者进行沟通,拆除全冠,进行常规牙髓治疗后,重新粘接,治疗期间应制作临时冠。
如患者不同意或拆除困难,可在全冠颌面直接开髓进行常规牙髓治疗,严密充填。
对创伤颌可进行调颌处理。
牙龈红肿:其发生的原因有:①全冠边缘过长,压迫牙龈;②嵌塞食物压迫;③未彻底清除的多余粘结剂刺激牙龈;④金属过敏。
专业知识伸、侧方及开闭

于金属 115.全口义齿下颌基托后缘应在磨牙后垫的中1/2 116.上颌第一磨牙近中舌尖与平面的关系是在平面上 117.全口义齿印模托盘要求:宽于无牙颌2~3mm 118.铸造支架邻面板的作用叙述是引导义齿取戴,增强
义齿的固位力;减少义齿对基牙的损害;防止食物 嵌塞;降低余留牙龋病的发生率 119.焊料焊接的基本条件包括润湿性;焊件和焊料;焊 媒;温度 120.用于转移颌位关系的保持器为牙合架 121.若采用体瓷、透明瓷自身上釉,烧结温度是高于体 瓷烧结温度 10℃ 122.双曲舌簧加力后其游离段抵住牙的舌侧颈部应与牙 长轴垂直 123.弯制卡环时不得损伤或者磨损模型 124.卡环体部及间隙卡环的越牙合部分应在非倒凹区, 且不妨碍咬合 125.卡臂尖和卡臂的二分之一长度应在基牙的倒凹区, 不得压迫牙龈 126.决定可摘局部义齿基托蜡型的伸展范围的因素有缺 牙的部位、义齿的支持形式、牙槽骨的吸收程度、 基牙的健康状况 127.是下颌骨缺损的特点下颌骨缺损患者多数存在咬合 错乱;下颌骨缺损患者张口受限;下颌骨缺损修复 时印模和修复体摘戴都较困难;下颌骨缺损植骨后 颊沟平浅 128.矫治深覆牙合可选用的功能性矫治器是上颌平面导 板矫治器 129.在全口义齿基托折裂修复时,磨去断端两侧基托斜 面宽度是 3~5mm 130.焊料焊接过程中,不能抗氧化的措施是不能及早在 焊接区加焊媒 131.适用于活动矫治器中邻间钩弯制的工具是尖头钳 132.做烤瓷修复体时,首先应在可卸代型上涂布间隙涂 料 133.清创术中冲洗创口最常用的冲洗液是1.5%~3%的过 氧化氢和生理盐水 134.用于冠周冲洗的过氧化氢溶液浓度是3% 135.面弓是由叉和弓体两部分组成 136.托是由基托和堤两部分组成 137.作为全口义齿的人工牙,是塑料牙的优点外形好; 与基托的结合性好;韧性好;质地轻 138.咀嚼效率降低;吞咽功能障碍;语言模糊不清;吸 吮功能丧失是颌面部缺损造成的影响 139.为避免损伤牙龈组织,活动义齿上颌前牙区腭侧基 托边缘应远离龈缘 4~6mm 140.牙列缺失患者,同一颌弓内常见牙槽骨呈不对称吸 收,其原因是与失牙原因和时间有关 141.除气、氧化的目的是形成较光的表面,防止瓷层烧 结时产生气泡 142.间隙卡的弯制合面弯:向对侧,中间部分可以先下 再上,不要直线越过合面,要求合面贴合 143.义齿基托加厚的常见部位如牙槽嵴吸收较多处;牙 槽嵴缺损处;颊侧基托;唇侧基托 联合卡环的固位体适用于牙冠短,相邻两牙有自然 间隙的游离端缺失修复
口腔铸造支架和金属内冠失败原因分析

口腔铸造支 架和金属 内冠失败原 因分析
姚. 勤
( 泰州职业技术学院 , 江苏 泰州 2 5 0 ) 2 30
摘
要: 目的 探讨 口腔铸件常见失败原 因。 方法 对 20 牙体或牙列缺损患者进行熔模铸 9例 造 , 作 30件金 属 内冠和 支 架。结 果 30件铸 件 中失败 4 制 8 8 0件 , 中铸 造不 全 1 件 , 其 8
铸件 变形 1 6件 , 缩孔 2件 , 眼 1 , 砂 件 裂缝 2件 , 属 瘤 1 。结论 金 件
变形是 临床 铸件 失败 的 主要 原 因。
铸 造 不全和铸 件
关键 词 : 牙科铸 造技 术 ; 牙修 复 体 ; 义齿 ; 熔模 中图分类 号 : 7 R8 文献标 识码 : A 文章 编号 :6 104 (070 — 0 30 17 — 12 20 )4 06 — 2
维普资讯
第 7卷 第 4期 20 0 7年 8月
泰 州职 业技 术 学 院 学 报
Jun l f azo oyeh ia n tue o ra ih uP ltc nc l s tt oT I i
Vo. N . 1 7 o4
Au .0 7 g2 0
件关键嘲 2琼脂是复制模型的常用材料 , ;) 其质量是获得高精度铸件的前提和基础 , 琼脂复制后脱水也可
ቤተ መጻሕፍቲ ባይዱ
引起铸造变形 ;) 3熔模在铸型内的位置影响着铸件的适合性 , 铸型在凝固膨胀和加热膨胀时铸型不同位
置的膨胀率不同 , 包埋时将熔模置于铸型中心远端 2 的位置 , / 5 可避免铸件变形r4 蜡型制作完毕后未 z ) l ; 及时包埋 , 导致蜡型变形 , 固定桥单位过多 , 桥体过长导致金属收缩 。 预防措施为蜡型制作完毕后及时包 埋, 在基牙条件允许的情况下尽量缩短 固定桥的长度 , 原则上较大范 围的固定桥不要做成一个整体 , 最 好做成分段 固定桥 , 待铸造完成后再将各部分焊接成一个整体 。 () 3缩孔 缩孔是不常见的铸造缺陷 , 产生的原因有 : 合金收缩未得到充分的补偿 , 铸道的直径 、 长 度, 与铸件 的大小 、 厚薄不相适宜 , 安插位置不正确 , 熔模未避开铸件 的热 中心区 , 铸型的透气性差 以及
- 1、下载文档前请自行甄别文档内容的完整性,平台不提供额外的编辑、内容补充、找答案等附加服务。
- 2、"仅部分预览"的文档,不可在线预览部分如存在完整性等问题,可反馈申请退款(可完整预览的文档不适用该条件!)。
- 3、如文档侵犯您的权益,请联系客服反馈,我们会尽快为您处理(人工客服工作时间:9:00-18:30)。
4. 铸道的长度:铸 道的长度一般根据 蜡型在铸圈内的位 置确定,原则上使 蜡型位于铸圈的上 2/5 ,避开热中心。 同时不宜过长,保 证在铸造时液态金 属能以最快的速度 流入铸模腔内,一 般在 5 ~ 10mm 。
2. 铸道的形态、直径: 铸道的截面形态应为圆 形,因为圆形截面的铸 道表面积小,保温性能 好,有利于液态金属顺 畅流入铸模腔;铸道的 直径与蜡型的大小、体 积有关,小铸件铸道可 细些,大铸件铸道应粗 大些。铸道的直径应大 于蜡型最厚处的厚度。
3. 铸道的安插角度:铸 道与蜡型连接应呈一圆 钝的角度,以形成平滑 的流入口,便于液态金 属流入铸模腔的各个方 向。切忌铸道与蜡型轴 面形成小角度,使金属 液体产生回流,造成铸 模腔被金属液冲压破坏 ,或因离心力不足导致 铸造失败。
金
常见问题
1. 铸道的位置、方向错误 2. 铸道的形态、直径错误 3. 铸道的安插角度错误 4. 铸道的长度错误
解决方法
1. 铸道的位置、方向:铸道原则上应 放置在蜡型最厚、最大的光滑部位, 不破坏咬合、邻接关系,不使蜡型的 组织面形成死角,有利于金属的流入 及补偿收缩。