不锈钢焊接工艺
不锈钢无缝焊接工艺

不锈钢无缝焊接工艺不锈钢无缝焊接是一种高要求的焊接工艺,其目的是在不锈钢材料上实现无缝隙的连接。
在焊接过程中,需要注意表面处理、定位、打底焊、填充焊、表面焊、焊接完成、热处理和无损检测等环节。
1.表面处理在进行不锈钢无缝焊接前,首先需要对焊接区域进行表面处理。
表面处理主要包括清洗、打磨和干燥三个步骤。
清洗是为了去除表面的油污、锈迹等杂质,以保证焊接质量;打磨则是为了去除不锈钢表面的氧化膜,以提高焊接的牢固度;干燥则是为了确保焊接区域的干燥,以避免气孔、裂纹等缺陷的产生。
2.定位在表面处理完成后,需要进行定位操作。
定位的目的是为了确定焊接位置,以确保焊接过程的位置精度。
首先需要在焊接位置绘制草图,明确各部分的相对位置;然后用记号笔或标签纸对需要焊接的位置进行标记,以便在焊接过程中进行识别。
3.打底焊打底焊是整个焊接过程中关键的一步。
在焊接过程中,需要选择合适的电流、电压和焊接速度,以保证打底焊的质量。
同时,还需要注意焊条的角度和运条方法,以避免气孔、夹渣等缺陷的产生。
打底焊的质量直接影响到整个焊接过程的牢固度和精度,因此需要严格控制。
4.填充焊填充焊是在打底焊完成后进行的焊接工艺。
在填充焊过程中,需要控制好电流、电压和焊接速度,同时注意焊条的角度和运条方法。
填充焊的主要目的是为了填充打底焊留下的空隙,使整个焊接部位更加牢固。
5.表面焊表面焊是在填充焊完成后进行的焊接工艺。
在表面焊过程中,需要控制好电流、电压和焊接速度,同时注意焊条的角度和运条方法。
表面焊的主要目的是为了修整焊接表面的形状和尺寸,使整个焊接部位更加平滑、美观。
6.焊接完成当表面焊完成后,整个焊接过程就结束了。
此时,需要对焊接部位进行外观检查,以确保没有气孔、夹渣、裂纹等缺陷的产生。
同时,还需要进行无损检测,以确保焊接部位的内部质量和精度。
常用的无损检测方法有超声波检测、射线检测和磁粉检测等。
7.热处理在焊接完成后,通常需要对焊接部位进行热处理,以消除焊接应力和提高材料的韧性。
不锈钢板材焊接工艺

不锈钢板材的焊接工艺可以根据具体应用需求和材料类型选择不同的方法。
以下是几种常见的不锈钢板材焊接工艺:
1. 电弧焊接:电弧焊是最常用的焊接方法之一。
常见的电弧焊方法包括手工电弧焊和氩弧焊。
手工电弧焊适用于简单的焊接任务,而氩弧焊通常用于高质量要求的焊接,其中使用惰性气体(如氩气)来保护熔化金属,防止与大气中的氧气和其他杂质发生反应。
2. 激光焊接:激光焊接是一种高效、精确的焊接方法,适用于较薄的不锈钢板材。
激光焊接使用激光束来加热和融化焊接接头,形成坚固的焊缝。
3. TIG焊接:TIG(Tungsten Inert Gas)焊接也是一种常用的焊接方法,适用于各种不锈钢板材的焊接。
TIG焊接使用非消耗性钨电极和惰性气体(如氩气)提供保护,产生高质量的焊接接头。
4. MIG/MAG焊接:MIG(Metal Inert Gas)和MAG(Metal Active Gas)焊接是在常规气体(MIG)或复合气体(MAG)保护下进行的焊接方法。
这种焊接方法速度快,适合大批量生产和自动化焊接任务。
在选择焊接方法时,需要考虑不锈钢板材的厚度、合金成分、应用环境和质量要求等因素。
此外,操作人员需要具备相关焊接技能和经验,以确保焊接过程的质量和安全。
建议在进行不锈钢板材焊接前,咨询专业的焊接工程师或相关专业机构,以获取更详细和准确的建议。
不锈钢焊接工艺要点和注意事项

不锈钢焊接工艺要点和注意事项一、不锈钢焊接工艺要点:1.选择合适的焊接方法:不锈钢焊接常用的方法包括手工电弧焊、氩弧焊、TIG焊、MIG/MAG焊等,选择适合的焊接方法可以根据具体需求进行判断。
2.选择合适的焊接材料:不锈钢的焊接材料要和母材具有一致的化学成分、冶金性能和耐蚀性能,以保证焊接接头的质量。
3.确保焊接面干净:在焊接之前,要保证焊接面的干净度,通过刮除氧化层、油脂和其他杂质,可以使用酸性或碱性清洗剂进行清洗。
4.控制焊接参数:控制焊接电流、电压、焊接速度等参数,以保证焊接过程中的熔融状态和热输入量,避免产生过多的热应力。
5.合理选择焊接顺序:大型不锈钢构件的焊接顺序要循序渐进,避免热应力的集中和变形的发生。
6.控制焊接热输入:避免产生过多的热应力,可以采取预热、焊接层间温度控制、控制冷却速度等措施。
7.合理选用填充材料:对于一些不锈钢材料,需要选用添加元素的填充材料,以提高焊接接头的强度和耐蚀性。
8.保持密封性:焊接过程中要保持密封性,避免空气进入焊接接头,以避免氧化和腐蚀。
二、不锈钢焊接的注意事项:1.防止氧化:不锈钢焊接过程中需要避免氧化,可以使用保护性气体如氩气进行保护,避免氧气进入焊接接头。
2.注意预热和后热处理:尤其是对于厚板材料和高合金不锈钢,预热和后热处理非常重要,可以减少热应力和残余应力,提高焊接接头的强度和耐蚀性。
3.控制焊接变形:不锈钢焊接容易发生变形,可以通过控制焊接顺序和方法,以及使用临时支架等方法来减少变形。
4.注意焊接序列和方向:焊接接头的序列和方向应当遵循一定的原则,避免产生过多的焊缝和热应力集中。
5.合理选择气体保护:不锈钢焊接过程中,选择合适的气体保护有助于减少氧化和减少焊缝材料中的杂质。
6.细节处理:对于不锈钢焊接接头的边缘和焊缝部分,需要进行细致的处理,保证其质量和耐蚀性。
7.严格控制焊接质量:不锈钢焊接的质量直接影响其耐蚀性能,需要严格控制焊接质量,特别是焊接接头的表面质量和焊缝的性能。
不锈钢扩散焊接工艺

不锈钢扩散焊接工艺不锈钢扩散焊接工艺是一种高效的不锈钢连接方法,其利用高温条件下不锈钢表面的氧化反应进行焊接。
该工艺具有低成本、高接头质量、环保等优点,被广泛应用于不锈钢制造行业。
下面将详细介绍不锈钢扩散焊接工艺的原理、工艺流程和实施要点。
1. 原理不锈钢扩散焊接是一种利用高温条件下对不锈钢表面进行反应的焊接方法。
不锈钢扩散焊接的原理是利用氮、氧、碳等元素在高温条件下与不锈钢表面反应,形成一种含氮、含氧、含碳等元素的薄层,使不锈钢材料表面具有良好的焊接性能。
在扩散焊接工艺过程中,可使用特殊的焊接设备,将工件加热到适当的温度,使其表面氧化,然后进行压合,使氧化物被压实形成焊缝。
2. 工艺流程不锈钢扩散焊接的工艺流程主要包括选择材料、准备工件、预热、焊接、热处理、修磨等环节。
具体的工艺流程如下:(1)选择材料:要选择与所要焊接材料相似的、高品质的、具有良好机械性能的初始材料。
初始材料的质量直接关系到焊接后的接头质量和使用寿命。
(2)准备工件:将工件表面清洗干净,排除杂质和粉尘,以免影响焊接效果。
然后将工件按要求放在热交换板上。
(3)预热:将工件放在预热炉里,热处理时间根据不同的材料和焊接要求而定,一般在800-1000℃左右预热。
预热使得工件表面的氧化层软化,并加速氧化反应。
(4)焊接:将加热后的工件取出,然后将待焊接部位压紧,形成合适的接触面积。
然后再找到合适的热交换板,用力按压,使工件表面形成一层薄质的氮氧化物层。
接下来,进行焊接,并在符合要求的时间范围内完成。
(5)热处理:在完成焊接后,需要进行一定时间的热处理,以降低内部应力,并使接头连结更加牢固。
(6)修磨:在热处理结束后,删除焊接部位的氧化层、镀层、氧化产物等,并对接头进行磨削、抛光,使接头表面达到平整、光滑的要求。
3. 实施要点(1)选择合适的材料是扩散焊接的前提,必须对所采用的材料有深入的理解与熟悉。
(2)预热温度要根据材料和复杂工件结构来调整,热处理时间及温度应符合材料的要求,以保证焊接质量。
完整版)史上最全的不锈钢焊接工艺
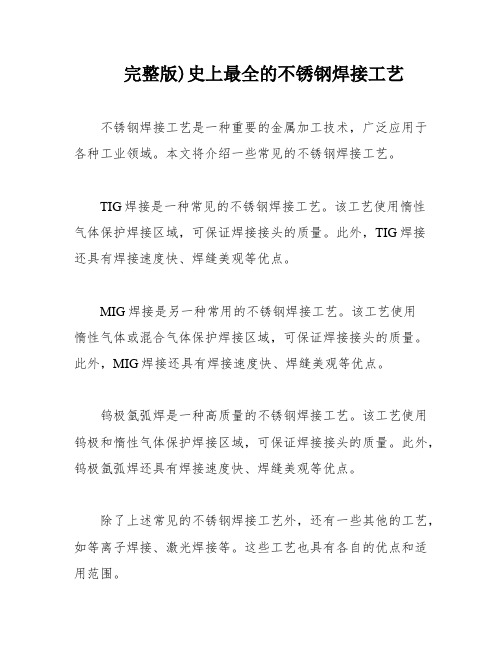
完整版)史上最全的不锈钢焊接工艺不锈钢焊接工艺是一种重要的金属加工技术,广泛应用于各种工业领域。
本文将介绍一些常见的不锈钢焊接工艺。
TIG焊接是一种常见的不锈钢焊接工艺。
该工艺使用惰性气体保护焊接区域,可保证焊接接头的质量。
此外,TIG焊接还具有焊接速度快、焊缝美观等优点。
MIG焊接是另一种常用的不锈钢焊接工艺。
该工艺使用惰性气体或混合气体保护焊接区域,可保证焊接接头的质量。
此外,MIG焊接还具有焊接速度快、焊缝美观等优点。
钨极氩弧焊是一种高质量的不锈钢焊接工艺。
该工艺使用钨极和惰性气体保护焊接区域,可保证焊接接头的质量。
此外,钨极氩弧焊还具有焊接速度快、焊缝美观等优点。
除了上述常见的不锈钢焊接工艺外,还有一些其他的工艺,如等离子焊接、激光焊接等。
这些工艺也具有各自的优点和适用范围。
总之,不锈钢焊接工艺是一项重要的金属加工技术,应用广泛。
选择合适的焊接工艺可以保证焊接接头的质量,提高生产效率。
不锈钢焊管是通过焊管成型机将不锈钢板经过若干道模具碾压成型并经过焊接而成。
由于不锈钢的强度较高,且其结构为面心立方晶格,易形成加工硬化,使焊管成型时,模具容易磨损,不锈钢板料易与模具表面形成粘结(咬合),使焊管及模具表面形成拉伤。
因此,好的不锈钢成型模具必须具备极高的耐磨和抗粘结(咬合)性能。
进口焊管模具的表面处理采用超硬金属碳化物或氮化物覆层处理。
激光焊接、高频焊接和传统的熔化焊接相比具有焊接速度快、能量密度高、热输入小的特点。
因此,热影响区窄,晶粒长大程度小,焊接变形小,冷加工成形性能好,容易实现自动化焊接、厚板单道一次焊透,其中最重要的特点是Ⅰ形坡口对接焊不需要填充材料。
金属焊接方法有40种以上,主要分为熔焊、压焊和钎焊三大类。
熔焊是在焊接过程中将工件接口加热至熔化状态,不加压力完成焊接的方法。
熔焊时,热源将待焊两工件接口处迅速加热熔化,形成熔池。
在熔焊过程中,如果大气与高温的熔池直接接触,大气中的氧就会氧化金属和各种合金元素,大气中的氮、水蒸汽等进入熔池,还会在随后冷却过程中在焊缝中形成气孔、夹渣、裂纹等缺陷,恶化焊缝的质量和性能。
不锈钢焊接工艺流程
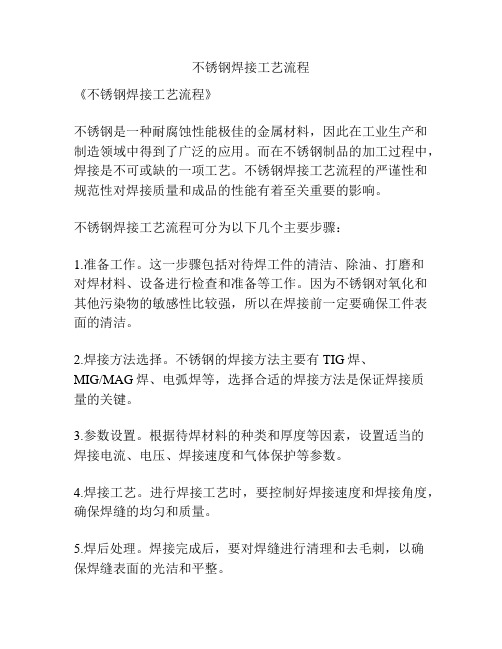
不锈钢焊接工艺流程
《不锈钢焊接工艺流程》
不锈钢是一种耐腐蚀性能极佳的金属材料,因此在工业生产和制造领域中得到了广泛的应用。
而在不锈钢制品的加工过程中,焊接是不可或缺的一项工艺。
不锈钢焊接工艺流程的严谨性和规范性对焊接质量和成品的性能有着至关重要的影响。
不锈钢焊接工艺流程可分为以下几个主要步骤:
1.准备工作。
这一步骤包括对待焊工件的清洁、除油、打磨和
对焊材料、设备进行检查和准备等工作。
因为不锈钢对氧化和其他污染物的敏感性比较强,所以在焊接前一定要确保工件表面的清洁。
2.焊接方法选择。
不锈钢的焊接方法主要有TIG焊、
MIG/MAG焊、电弧焊等,选择合适的焊接方法是保证焊接质
量的关键。
3.参数设置。
根据待焊材料的种类和厚度等因素,设置适当的
焊接电流、电压、焊接速度和气体保护等参数。
4.焊接工艺。
进行焊接工艺时,要控制好焊接速度和焊接角度,确保焊缝的均匀和质量。
5.焊后处理。
焊接完成后,要对焊缝进行清理和去毛刺,以确
保焊缝表面的光洁和平整。
以上就是不锈钢焊接工艺流程的基本步骤,虽然焊接工艺看似简单,但实际操作中需要经验和技巧的积累,而且要严格按照规范和标准进行操作,以确保焊接质量,避免后续的质量问题和安全隐患。
(完整版)史上最全的不锈钢焊接工艺
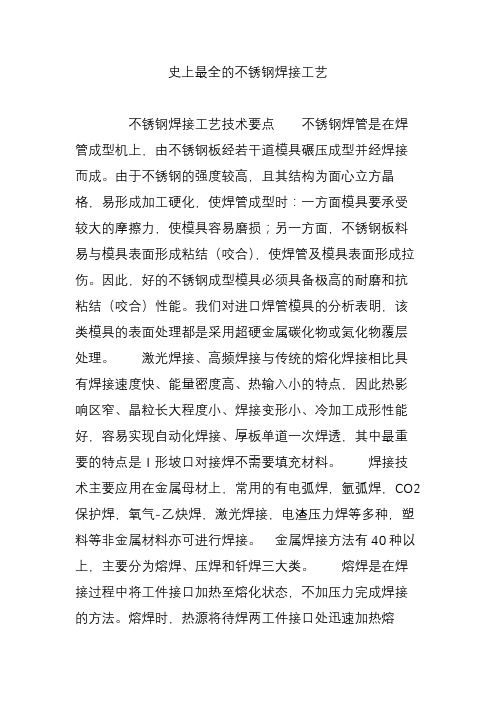
史上最全的不锈钢焊接工艺不锈钢焊接工艺技术要点不锈钢焊管是在焊管成型机上,由不锈钢板经若干道模具碾压成型并经焊接而成。
由于不锈钢的强度较高,且其结构为面心立方晶格,易形成加工硬化,使焊管成型时:一方面模具要承受较大的摩擦力,使模具容易磨损;另一方面,不锈钢板料易与模具表面形成粘结(咬合),使焊管及模具表面形成拉伤。
因此,好的不锈钢成型模具必须具备极高的耐磨和抗粘结(咬合)性能。
我们对进口焊管模具的分析表明,该类模具的表面处理都是采用超硬金属碳化物或氮化物覆层处理。
激光焊接、高频焊接与传统的熔化焊接相比具有焊接速度快、能量密度高、热输入小的特点,因此热影响区窄、晶粒长大程度小、焊接变形小、冷加工成形性能好,容易实现自动化焊接、厚板单道一次焊透,其中最重要的特点是Ⅰ形坡口对接焊不需要填充材料。
焊接技术主要应用在金属母材上,常用的有电弧焊,氩弧焊,CO2保护焊,氧气-乙炔焊,激光焊接,电渣压力焊等多种,塑料等非金属材料亦可进行焊接。
金属焊接方法有40种以上,主要分为熔焊、压焊和钎焊三大类。
熔焊是在焊接过程中将工件接口加热至熔化状态,不加压力完成焊接的方法。
熔焊时,热源将待焊两工件接口处迅速加热熔化,形成熔池。
熔池随热源向前移动,冷却后形成连续焊缝而将两工件连接成为一体。
在熔焊过程中,如果大气与高温的熔池直接接触,大气中的氧就会氧化金属和各种合金元素。
大气中的氮、水蒸汽等进入熔池,还会在随后冷却过程中在焊缝中形成气孔、夹渣、裂纹等缺陷,恶化焊缝的质量和性能。
压焊是在加压条件下,使两工件在固态下实现原子间结合,又称固态焊接。
常用的压焊工艺是电阻对焊,当电流通过两工件的连接端时,该处因电阻很大而温度上升,当加热至塑性状态时,在轴向压力作用下连接成为一体。
各种压焊方法的共同特点是在焊接过程中施加压力而不加填充材料。
多数压焊方法如扩散焊、高频焊、冷压焊等都没有熔化过程,因而没有象熔焊那样的有益合金元素烧损,和有害元素侵入焊缝的问题,从而简化了焊接过程,也改善了焊接安全卫生条件。
不锈钢410 焊接工艺

不锈钢410 焊接工艺
不锈钢410的焊接工艺主要包括以下步骤:
1. 预热:在150°C至260°C的温度范围内进行预热,以防止在焊接过程中出现裂纹和变形等问题。
2. 坡口准备:在焊接前,需要将焊接区域两侧各50mm范围内的油污和锈蚀清理干净,并刨成合适的坡口。
3. 装配:以复层SUS410S钢板为基准进行装配,错边量应小于0.5mm。
定位焊应在基层上进行,所用焊接材料应与正式施焊用的焊接材料相同。
4. 焊接:先进行基层的焊接,然后进行盖面焊。
基层焊接完成后,应进行X射线探伤,合格后才能进行过渡层和复层的焊接。
在过渡层和复层的焊接前,应修磨基层焊缝表面,使其与平台基本平齐。
5. 焊接顺序:先进行复层侧的基层焊缝焊接,再进行盖面焊。
基层焊接时,应使用直径3.2mm的J507(E5515型)焊条进行封底焊,然后用直径4mm的焊条进行盖面焊。
盖面焊的表面应略高于坡口平台。
6. 埋弧焊和气体保护焊:在进行过渡层和复层焊接时,应使用直径1.2mm的FCWE309T 药芯焊丝气体保护焊进行施焊。
7. 焊接后处理:焊接完成后,应进行热处理以消除应力,并保证材料具有良好的力学性能和耐腐蚀性能。
需要注意的是,不锈钢410的焊接工艺需要根据具体的工况条件和材料要求进行调整。
同时,为了确保焊接质量和安全性,操作人员应具备相应的技能和经验,并严格遵守工艺要求和安全操作规程。
- 1、下载文档前请自行甄别文档内容的完整性,平台不提供额外的编辑、内容补充、找答案等附加服务。
- 2、"仅部分预览"的文档,不可在线预览部分如存在完整性等问题,可反馈申请退款(可完整预览的文档不适用该条件!)。
- 3、如文档侵犯您的权益,请联系客服反馈,我们会尽快为您处理(人工客服工作时间:9:00-18:30)。
二、1、焊前:坡口及其附近必须清理干净,对于有油污不可以用钢丝刷和砂轮清理,用丙酮和或酒精进行清理。
2、坡口加工或下料采用机械加工或炭弧气刨。
3、在搬用、坡口的制备、装配个过程,应避免损伤钢材的表面。
三、焊接工艺:1、应采用快速焊、多道焊;焊接电流不易过大,焊接时尽量采用平焊位置,焊条最好不做摆动或稍做摆动;且焊接过程中,应严格控制层间温度,待上一层焊道冷到60度以下在焊下一道焊道。
2、焊条角度应正确,运条要稳,电弧不宜太长,与腐蚀介质接触的焊道应最后施焊。
3、在条件允许的时候,应采用强制冷却的方式冷却焊道。
四、焊后:焊缝必须进行酸化和钝化处理。
焊接材料:不锈钢A002焊条,焊丝,焊条直径:3.2和4.0焊接电流(A) 80-110A,110-150A 焊接电压(V)焊接速度3.5焊缝返修3.5.1焊缝返修应由持证焊工或有相应合格焊工担任3.5.2返修前应根据片位分析缺陷性质,缺陷长度,宽度,确认缺陷位置3.5.3消除缺陷方法采用砂轮机机磨削,根部返修部位进行坡口修理.3.5.4返修的焊接工艺与正式焊接相同.3.5.5焊缝返修的管理程度执行《压力管道质量保证书手册》中的规定.3.6颜色检查:根部焊接完毕,浅色到淡蓝色表明焊缝充氩保护不好,以被氧化,银白色表示保护良好.4,结论:超低碳不锈钢槽体及管道焊接施工中,必须严格执行工艺要求,认真施焊,确保焊口一次合格率98.6%以上,肉眼观察无缩孔。
引用:一、奥氏体不锈钢的焊接特点:1、容易出现热裂纹。
防止措施:(1)尽量使焊缝金属呈双相组织,铁素体的含量控制在3-5%以下。
因为铁素体能大量溶解有害的S、P杂质。
(2)尽量选用碱性药皮的优质焊条,以限制焊缝金属中S、P、C等的含量。
2、晶间腐蚀:根据贫铬理论,焊缝和热影响区在加热到450-850℃敏化温度区时在晶界上析出碳化铬,造成贫铬的晶界,不足以抵抗腐蚀的程度。
防止措施:(1)采用低碳或超低碳的焊材,如A002等;采用含钛、铌等稳定化元素的焊条,如A137、A132等。
(2)由焊丝或焊条向焊缝熔入一定量的铁素体形成元素,使焊缝金属成为奥氏体+铁素体的双相组织,(铁素体一般控制在4-12%)。
(3)减少焊接熔池过热,选用较小的焊接电流和较快的焊接速度,加快冷却速度。
(4)对耐晶间腐蚀性能要求很高的焊件进行焊后稳定化退火处理3、应力腐蚀开裂:应力腐蚀开裂是焊接接头在特定腐蚀环境下受拉伸应力作用时所产生的延迟开裂现象。
奥氏体不锈钢焊接接头的应力腐蚀开裂是焊接接头比较严重的失效形式,表现为无塑性变形的脆性破坏。
应力腐蚀开裂防止措施:(1)合理制定成形加工和组装工艺,尽可能减小冷作变形度,避免强制组装,防止组装过程中造成各种伤痕(各种组装伤痕及电弧灼痕都会成为SCC的裂源,易造成腐蚀坑)。
(2)合理选择焊材:焊缝与母材应有良好的匹配,不产生任何不良组织,如晶粒粗化及硬脆马氏体等;(3)采取合适的焊接工艺:保证焊缝成形良好,不产生任何应力集中或点蚀的缺陷,如咬边等;采取合理的焊接顺序,降低焊接残余应力水平;(4)消除应力处理:焊后热处理,如焊后完全退火或退火;在难以实施热处理时采用焊后锤击或喷丸等。
(5)生产管理措施:介质中杂质的控制,如液氨介质中的O2、N2、H2O等;液化石油气中的H2S;氯化物溶液中的O2、Fe3+、Cr6+等;防蚀处理:如涂层、衬里或阴极保护等;添加缓蚀剂。
4、焊缝金属的低温脆化:对于奥氏体不锈钢焊接接头,在低温使用时,焊缝金属的塑韧性是关键问题。
此时,焊缝组织中的铁素体的存在总是恶化低温韧性。
防止措施:通过选用纯奥氏体焊材和调整焊接工艺获得单一的奥氏体焊缝。
5、焊接接头的σ相脆化:焊件在经受一定时间的高温加热后会在焊缝中析出一种脆性的σ相,导致整个接头脆化,塑性和韧性显著下降。
σ相的析出温度范围650-850℃。
在高温加热过程中,σ相主要由铁素体转变而成。
加热时间越长,σ相析出越多。
防止措施:(1)限制焊缝金属中的铁素体含量(小于15%);采用超合金化焊接材料,即高镍焊材。
(2)采用小规范,以减小焊缝金属在高温下的停留时间;(3)对已析出的σ相在条件允许时进行固溶处理,使σ相溶入奥氏体。
二、奥氏体不锈钢的焊条选用要点:不锈钢主要用于耐腐蚀,但也用作耐热钢和低温钢。
因此,在焊接不锈钢时,焊条的性能必须与不锈钢的用途相符。
不锈钢焊条必须根据母材和工作条件(包括工作温度和接触介质等)来选用。
1、一般来说,焊条的选用可参照母材的材质,选用与母材成分相同或相近的焊条。
如:A102对应0Cr19Ni9;A137对应1Cr18Ni9Ti。
2、由于碳含量对不锈钢的抗腐蚀性能有很大的影响,因此,一般选用熔敷金属含碳量不高于母材的不锈钢焊条。
如316L必须选用A022焊条。
3、奥氏体不锈钢的焊缝金属应保证力学性能。
可通过焊接工艺评定进行验证。
4、对于在高温工作的耐热不锈钢(奥氏体耐热钢),所选用的焊条主要应能满足焊缝金属的抗热裂性能和焊接接头的高温性能。
(1)对Cr/Ni≥1的奥氏体耐热钢,如1Cr18Ni9Ti等,一般均采用奥氏体-铁素体不锈钢焊条,以焊缝金属中含2-5%铁素体为宜。
铁素体含量过低时,焊缝金属抗裂性差;若过高,则在高温长期使用或热处理时易形成σ相脆化,造成裂纹。
如A002、A102、A137。
在某些特殊的应用场合,可能要求采用全奥氏体的焊缝金属时,可采用比如A402、A407焊条等。
(2)对Cr/Ni<1的稳定型奥氏体耐热钢,如Cr16Ni25Mo6等,一般应在保证焊缝金属具有与母材化学成分大致相近的同时,增加焊缝金属中Mo、W、Mn等元素的含量,使得在保证焊缝金属热强性的同时,提高焊缝的抗裂性。
如采用A502、A507。
5、对于在各种腐蚀介质中工作的耐蚀不锈钢,则应按介质和工作温度来选择焊条,并保证其耐腐蚀性能(做焊接接头的腐蚀性能试验)。
(1)对于工作温度在300℃以上、有较强腐蚀性的介质,须采用含有Ti或Nb稳定化元素或低碳不锈钢焊条。
如A137或A002等。
(2)对于含有稀硫酸或盐酸的介质,常选用含Mo或含Mo和Cu的不锈钢焊条如:A032、A052 等。
(3)工作,腐蚀性弱或仅为避免锈蚀污染的设备,方可采用不含Ti或Nb的不锈钢焊条。
为保证焊缝金属的耐应力腐蚀能力,采用超合金化的焊材,即焊缝金属中的耐蚀合金元素(Cr、Mo、Ni等)含量高于母材。
如采用00Cr18Ni12Mo2类型的焊接材料(如A022)焊接00Cr19Ni10焊件。
6、对于在低温条件下工作的奥氏体不锈钢,应保证焊接接头在使用温度的低温冲击韧性,故采用纯奥氏体焊条。
如A402、A407。
7、也可选用镍基合金焊条。
如采用Mo达9%的镍基焊材焊接Mo6型超级奥氏体不锈钢。
8、焊条药皮类型的选择:(1)由于双相奥氏体钢焊缝金属本身含有一定量的铁素体,具有良好的塑性和韧性,从焊缝金属抗裂性角度进行比较,碱性药皮与钛钙型药皮焊条的差别不像碳钢焊条那样显著。
因此在实际应用中,从焊接工艺性能方面着眼较多,大都采用药皮类型代号为17或16的焊条(如A102A、A102、A132等)。
(2)只有在结构刚性很大或焊缝金属抗裂性较差(如某些马氏体铬不锈钢、纯奥氏体组织的铬镍不锈钢等)时,才考虑选用药皮代号为15的碱性药皮不锈钢焊条(如A107、A407等)。
综上所述,奥氏体不锈钢的焊接是有其独特特点的,奥氏体不锈钢的焊接时焊条选用尤其值得注意,只有这样才能达到针对不同材料实施不同的焊接方法和不同材料的焊条,不锈钢焊条必须根据母材和工作条件(包括工作温度和接触介质等)来选用。
这样才有可能能达到所预期的焊接质量。
304L不锈钢板304L不锈钢是一种通用性的不锈钢材料。
304L不锈钢牌号:00Cr19Ni10(0Cr18Ni10),分析304L不锈钢化学化学成分%C:≤0.07,Si:≤1.0,Mn:≤2.0,Cr:17.0~19.0,Ni:8.0~11.0,S:≤0.03,P:≤0.035。
304L不锈钢的力学性能屈服强度(N/mm2)≥205抗拉强度≥520延伸率(%)≥40硬度HB≤187HRB≤90HV≤200 密度7.93g·cm-3比热c(20℃)0.502J·(g·C)-1热导率λ/W(m·℃)-1(在下列温/℃)2010050012.116.321.4线胀系数α/(10-6/℃)(在下列温度间/℃)20~10020~20020~30020~40016.016.817.518.1电阻率0.73Ω·mm2·m-1熔点1398~1420℃304是一种通用性的不锈钢,它广泛地用于制作要求良好综合性能(耐腐蚀和成型性)的设备和机件。
301不锈钢在形变时呈现出明显的加工硬化现象,被用于要求较高强度的各种场合。
302不锈钢实质上就是含碳量更高的304不锈钢的变种,通过冷轧可使其获得较高的强度。
302B是一种含硅量较高的不锈钢,它具有较高的抗高温氧化性能。
303和303Se是分别含有硫和硒的易切削不锈钢,用于主要要求易切削和表而光浩度高的场合。
303Se不锈钢也用于制作需要热镦的机件,因为在这类条件下,这种不锈钢具有良好的可热加工性。
304L是碳含量较低的304不锈钢的变种,用于需要焊接的场合。
较低的碳含量使得在靠近焊缝的热影响区中所析出的碳化物减至最少,而碳化物的析出可能导致不锈钢在某些环境中产生晶间腐蚀(焊接侵蚀)。
304N是一种含氮的不锈钢,加氮是为了提高钢的强度。
305和384不锈钢含有较高的镍,其加工硬化率低,适用于对冷成型性要求高的各种场合。
308不锈钢用于制作焊条。
309、310、314及330不锈钢的镍、铬含量都比较高,为的是提高钢在高温下的抗氧化性能和蠕变强度。
而30S5和310S乃是309和310不锈钢的变种,所不同者只是碳含量较低,为的是使焊缝附近所析出的碳化物减至最少。
330不锈钢有着特别高的抗渗碳能力和抗热震性.316和317型不锈钢含有铝,因而在海洋和化学工业环境中的抗点腐蚀能力大大地优于304不锈钢。
其中,316型不锈钢由变种包括低碳不锈钢316L、含氮的高强度不锈钢。
316N以及合硫量较高的易切削不锈钢316F。
321、347及348是分别以钛,铌加钽、铌稳化的不锈钢,适宜作高温下使用的焊接构件。
348是一种适用于核动力工业的不锈钢,对钽和钻的合量有着一定的限制。
回转窑拖轮调整。