基于MCGS的天然气燃烧装置控制系统的设计
DCS系统在天然气处理装置中的优化设计

DCS系统在天然气处理装置中的优化设计随着社会经济的快速发展和能源需求的不断增长,天然气已成为世界上最重要的清洁能源之一。
而在天然气处理过程中,为了提高生产效率和产品质量,DCS(分布式控制系统)的优化设计显得尤为重要。
DCS系统是一种先进的工业自动化控制系统,它可以对生产过程进行全面的监控,并实现智能化的自动控制。
本文将对DCS系统在天然气处理装置中的优化设计进行探讨,并且从硬件、软件和网络三个方面来详细分析。
一、硬件优化设计在天然气处理装置中,DCS系统的硬件设计需要考虑到系统的稳定性、可靠性和安全性。
针对天然气处理装置的特殊工作环境,需要选择高温、高压和腐蚀等特性的硬件设备,以保证系统长时间稳定运行。
需要采用双重备份的硬件设计,即使某一部件出现故障,也能够自动切换到备用设备,避免系统中断带来的损失。
为了保证系统的安全性,还需要加强硬件设备的防火防爆设计,确保系统不受外界环境的影响。
硬件的优化设计是DCS系统在天然气处理装置中的重要一环,能够有效提高系统的稳定性和安全性。
在软件方面,天然气处理装置的DCS系统需要实现智能化的控制和优化的算法。
软件应该具备高效的数据处理能力,能够及时准确地处理大量的生产数据,并对数据进行分析、统计和存储。
软件需要具备智能化的控制算法,能够根据实时生产数据进行自动调节,并实现过程的智能化运行。
软件还需要具备故障诊断和预测能力,能够及时发现系统故障并进行预警,避免故障对生产过程造成影响。
软件的优化设计是DCS系统在天然气处理装置中的关键技术,能够提高系统的智能化程度和生产效率。
在天然气处理装置中,DCS系统的网络优化设计是保证系统稳定运行的关键环节。
网络需要具备高速稳定的数据传输能力,确保生产数据能够实时传输到控制中心,并且能够保障数据的准确性和完整性。
网络需要具备良好的安全保护能力,能够有效防范网络攻击和数据泄露,确保系统的安全稳定运行。
还需要进行网络带宽的合理分配和优化配置,以满足系统对数据传输的实时性和高效性的要求。
DCS系统在天然气处理装置中的优化设计
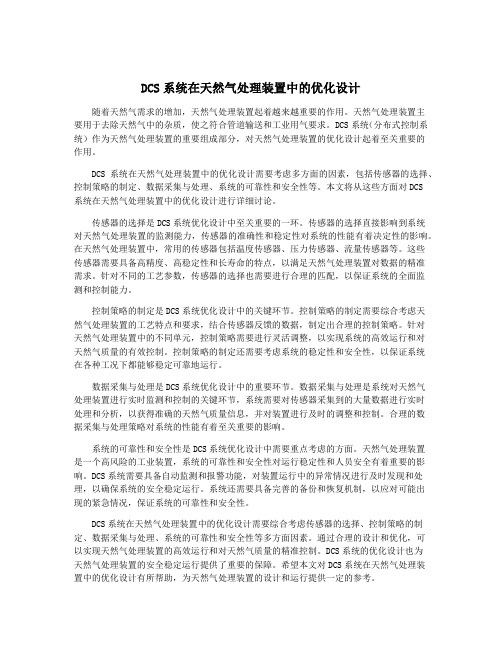
DCS系统在天然气处理装置中的优化设计随着天然气需求的增加,天然气处理装置起着越来越重要的作用。
天然气处理装置主要用于去除天然气中的杂质,使之符合管道输送和工业用气要求。
DCS系统(分布式控制系统)作为天然气处理装置的重要组成部分,对天然气处理装置的优化设计起着至关重要的作用。
DCS系统在天然气处理装置中的优化设计需要考虑多方面的因素,包括传感器的选择、控制策略的制定、数据采集与处理、系统的可靠性和安全性等。
本文将从这些方面对DCS系统在天然气处理装置中的优化设计进行详细讨论。
传感器的选择是DCS系统优化设计中至关重要的一环。
传感器的选择直接影响到系统对天然气处理装置的监测能力,传感器的准确性和稳定性对系统的性能有着决定性的影响。
在天然气处理装置中,常用的传感器包括温度传感器、压力传感器、流量传感器等。
这些传感器需要具备高精度、高稳定性和长寿命的特点,以满足天然气处理装置对数据的精准需求。
针对不同的工艺参数,传感器的选择也需要进行合理的匹配,以保证系统的全面监测和控制能力。
控制策略的制定是DCS系统优化设计中的关键环节。
控制策略的制定需要综合考虑天然气处理装置的工艺特点和要求,结合传感器反馈的数据,制定出合理的控制策略。
针对天然气处理装置中的不同单元,控制策略需要进行灵活调整,以实现系统的高效运行和对天然气质量的有效控制。
控制策略的制定还需要考虑系统的稳定性和安全性,以保证系统在各种工况下都能够稳定可靠地运行。
数据采集与处理是DCS系统优化设计中的重要环节。
数据采集与处理是系统对天然气处理装置进行实时监测和控制的关键环节,系统需要对传感器采集到的大量数据进行实时处理和分析,以获得准确的天然气质量信息,并对装置进行及时的调整和控制。
合理的数据采集与处理策略对系统的性能有着至关重要的影响。
系统的可靠性和安全性是DCS系统优化设计中需要重点考虑的方面。
天然气处理装置是一个高风险的工业装置,系统的可靠性和安全性对运行稳定性和人员安全有着重要的影响。
DCS系统在天然气处理装置中的优化设计

DCS系统在天然气处理装置中的优化设计天然气是一种主要的能源,其在国民经济中占有重要地位。
随着国内天然气需求的不断增加,天然气处理厂已成为天然气工业中不可或缺的一部分。
DCS系统在天然气处理装置中的优化设计,具有重要的意义。
天然气处理装置是将原始天然气处理成工业天然气、液化天然气(LNG)以及一些其他的工业气体和产品的设备。
这个过程包括天然气中的硫化氢、二氧化碳、水、甲烷、乙烷、丙烷、丁烷等成分的分离和去除。
这些成分的分离需要复杂的工艺流程和精细的控制。
而DCS系统则为这些工艺流程和控制提供了一种先进的解决方案。
DCS系统是指分布式控制系统,它由一系列的控制节点组成,这些节点可以相互通信以实现协调控制。
DCS系统可以通过网络连接到中央控制站,与PLC系统、SCADA系统以及云计算等技术相结合,实现全面的过程控制、监控和管理。
在天然气处理装置中,DCS系统可以实现对各个系统的实时监测和优化控制,从而保证整个过程的高效、稳定和安全。
具体体现在以下几个方面:1. 化学品投加控制天然气处理装置中,为了去除其中的硫化氢和二氧化碳等物质,需要对化学品进行投加,这个过程需要精确的控制。
DCS系统可以实时监测化学品的流量、压力和浓度等参数,精确地控制其投加量,并配合其他设备对其进行混合和反应,以确保处理效果。
2. 压缩机控制压缩机是天然气处理装置中的重要设备,它可以将气体压缩到更高的压力,以方便运输和储存。
DCS系统可以实时监测和控制压缩机的转速、出入口压力等参数,调整压缩机的负载,提高其效率,降低能耗。
3. 蒸汽和热能控制天然气处理过程中需要大量的蒸汽和热能,DCS系统可以对各个热交换器、锅炉等进行实时监测和温度控制,确保热能的有效利用。
4. 环保监测天然气处理过程中,还需要对废气进行处理,以保护环境。
DCS系统可以实时监测废气的排放量和质量,调整处理设备的操作参数,确保废气排放达到环保标准。
综上所述,DCS系统在天然气处理装置中的优化设计,可以极大地提高整个生产过程的效率和安全性。
基于MCGS软件的天然气输配站远程监控系统
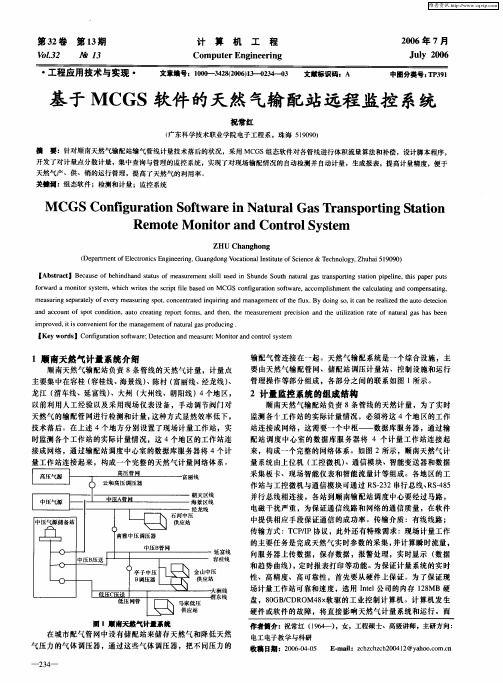
——
。
基于 MC GS软 件 的 天 然 气输 配站 远程 监 控 系统
祝常 红
( 广东科学技术职业学院 电子工程系 ,珠海 5 0 0 9) l 9
摘
要 :针对顺南天然气输配站输气管线计量技术落后的状 况,采 用 MC S G 组态软件对各管线进行体积流量算法和补偿 ,设计脚本程序 ,
f r r n t r s se o wa d a mo io y t m,wh c it s t e s rp l a e n M CGS c n i r t n s fwa e a c i h wr e h c t e b s d o i f i o f gu a i o t r o c ompl h n e c l u a i g a d c mp n ai g i me tt ac l t n o e s tn , s h n
维普资讯
第3 卷 第 l 期 2 3
V 3 oL 2 № l 3
计
算 机
工
程
20 06年 7 月
J l 0 6 uy 2 0
Co p t rEn i e rn m u e gn e i g
・ 工程应用技术 与实现 ・
文 编号 l 3 8 0 ) _ 2 _ 3 文 标 掘 章 :o 一4 (0l _3 _ o 2 2 6, o 4 0 献 识 A
开发 了对计量点分散计量 ,集中查询与 管理 的监控 系统 ,实现 了对现场输配情况的 自动检测并 自动计量 ,生成报表 ,提高计量精度 ,便于 天然气产、供、销的运行管理 ,提高了天然气的利用率。
关健 诃 :组态软件 ;检测和计量 ;监控系统
M CG S Co fg r to o t r t r l a a s o tn t to n u a in S fwa ei Na u a s i n G Tr n p ri gS a i n Re o eM o i ra d Co to y tm m t n t n n r l se o S
DCS系统在天然气处理装置中的优化设计

DCS系统在天然气处理装置中的优化设计摘要:随着天然气的开采和利用逐渐增加,天然气处理装置的规模和复杂性也在不断提高。
为了更好地实现天然气处理装置的自动化控制,提高生产效率和产品质量,DCS系统逐渐被应用于天然气处理装置中。
本文将介绍DCS系统在天然气处理装置中的优化设计,并分析其应用的效果和优势。
一、引言1. 控制系统硬件设计DCS系统的硬件设计是DCS系统在天然气处理装置中应用的重要组成部分。
智能化、模块化的硬件设计,能够满足天然气处理装置的运行需求,提高控制系统的稳定性和可靠性。
合理的硬件设计可以降低系统故障率,减少维修和运行成本。
2. 控制策略和算法设计天然气处理装置涉及到多个工艺单元的协调运行,需要设计相应的控制策略和算法。
DCS系统可以根据不同的工艺要求,实时调整控制参数,实现多变量控制和优化运行。
基于模型预测控制、自适应控制等算法的设计和优化,能够提高天然气处理装置的运行效率和稳定性。
3. 现场设备的监测和管理天然气处理装置中涉及大量的传感器和执行机构,需要进行实时监测和管理。
DCS系统可以实时采集和处理现场数据,监测设备状态,实现故障预警和快速故障处理,提高设备运行的可靠性和安全性。
1. 提高生产效率DCS系统可以实时监控天然气处理装置的各个工艺单元的运行状态,通过调整控制策略和算法,优化系统运行,提高生产效率。
DCS系统能够快速响应设备故障,并进行故障处理,减少停机时间,提高生产效率。
2. 提高产品质量DCS系统能够对天然气处理装置的关键参数进行实时监测和控制,在保证产品质量的前提下,最大限度地提高产量和质量。
通过优化控制策略和算法,降低产品的成分波动和偏差,提高产品的稳定性和一致性。
3. 降低能耗和成本DCS系统可以对能源的使用进行监测和控制,通过优化控制策略和算法,降低能耗和成本。
DCS系统能够实现对设备的智能调度和管理,降低设备维修和运行成本。
四、结论。
燃烧控制系统的设计(DOC)11页

燃烧控制系统的设计(DOC)11页摘要:燃烧控制系统是一种具有广泛应用的系统。
本文从系统设计的角度,对燃烧控制系统进行分析,并结合实际案例进行设计。
关键词:燃烧控制系统;系统设计;案例分析;1.引言燃烧控制系统是一种将燃料和空气控制在一定比例下进行燃烧的系统。
燃烧控制系统具有广泛的应用,包括工业生产、家用电器等。
通过控制燃气的流量、温度和压力等参数,可以实现对燃烧过程的控制。
因此,燃烧控制系统的设计十分重要。
2.燃烧控制系统燃烧控制系统的设计包括三个方面:系统硬件设计、软件设计和参数控制设计。
2.1 系统硬件设计燃烧控制系统的硬件设计包括传感器、执行器和控制器等部分。
其中,传感器主要负责收集燃烧过程中的相关参数,如温度、压力、流量等。
执行器则根据控制信号控制燃气的流量和压力等参数。
控制器则在接收传感器和执行器的输入信号后,对燃气进行控制和调节。
具体的硬件设计要根据不同的燃烧设备和系统的实际情况进行设计。
燃烧控制系统的软件设计主要包括控制算法和程序设计。
控制算法主要用于计算燃烧过程中燃气回路和空气回路的气流量和热能等参数,并根据设计要求实现燃气的自动调节。
程序设计则是将控制算法实现成计算机程序,以便通过人机界面进行人工控制或实现自动化控制。
2.3 参数控制设计燃烧控制系统的参数控制涉及到多个参数,包括燃烧温度、空气比、燃气流量和燃气压力等。
在进行燃烧控制系统的参数设计时,需要考虑燃料的种类、规格和燃烧要求,以及系统的工作环境等因素。
同时,还需要将参数设置在合理的范围内,以保证燃气的安全和稳定性。
3.案例分析某公司需要制造一种热水锅炉,需要设计一套燃烧控制系统,以保证燃气的安全和稳定性。
具体设计要求如下:(1)燃料种类:天然气(2)热量输出:10000千瓦(3)燃气流量:1000立方米/小时(4)燃气压力:50kpa(5)烟气排放:不超过30ppm如此,燃烧控制系统的设计方案如下:(1)硬件设计:利用压力传感器、温度传感器和流量计等传感器收集燃气的压力、温度和流量等参数;利用调压阀、进气门和排气门等执行器对燃气进行控制;利用控制器对传感器和执行器输出的信号进行处理和控制。
DCS系统在天然气处理装置中的优化设计
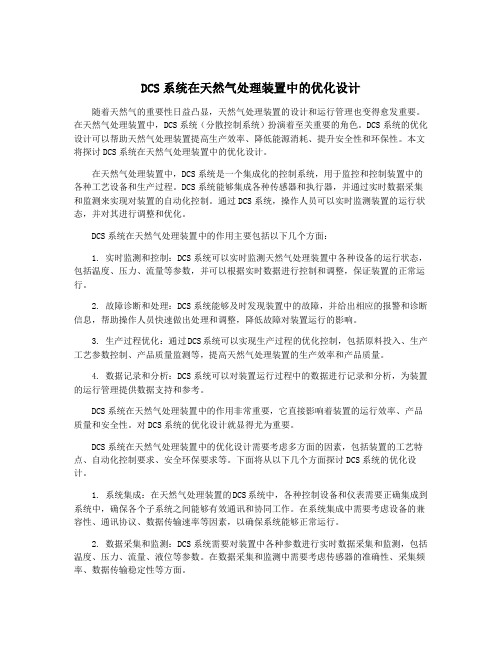
DCS系统在天然气处理装置中的优化设计随着天然气的重要性日益凸显,天然气处理装置的设计和运行管理也变得愈发重要。
在天然气处理装置中,DCS系统(分散控制系统)扮演着至关重要的角色。
DCS系统的优化设计可以帮助天然气处理装置提高生产效率、降低能源消耗、提升安全性和环保性。
本文将探讨DCS系统在天然气处理装置中的优化设计。
在天然气处理装置中,DCS系统是一个集成化的控制系统,用于监控和控制装置中的各种工艺设备和生产过程。
DCS系统能够集成各种传感器和执行器,并通过实时数据采集和监测来实现对装置的自动化控制。
通过DCS系统,操作人员可以实时监测装置的运行状态,并对其进行调整和优化。
DCS系统在天然气处理装置中的作用主要包括以下几个方面:1. 实时监测和控制:DCS系统可以实时监测天然气处理装置中各种设备的运行状态,包括温度、压力、流量等参数,并可以根据实时数据进行控制和调整,保证装置的正常运行。
2. 故障诊断和处理:DCS系统能够及时发现装置中的故障,并给出相应的报警和诊断信息,帮助操作人员快速做出处理和调整,降低故障对装置运行的影响。
3. 生产过程优化:通过DCS系统可以实现生产过程的优化控制,包括原料投入、生产工艺参数控制、产品质量监测等,提高天然气处理装置的生产效率和产品质量。
4. 数据记录和分析:DCS系统可以对装置运行过程中的数据进行记录和分析,为装置的运行管理提供数据支持和参考。
DCS系统在天然气处理装置中的作用非常重要,它直接影响着装置的运行效率、产品质量和安全性。
对DCS系统的优化设计就显得尤为重要。
DCS系统在天然气处理装置中的优化设计需要考虑多方面的因素,包括装置的工艺特点、自动化控制要求、安全环保要求等。
下面将从以下几个方面探讨DCS系统的优化设计。
1. 系统集成:在天然气处理装置的DCS系统中,各种控制设备和仪表需要正确集成到系统中,确保各个子系统之间能够有效通讯和协同工作。
在系统集成中需要考虑设备的兼容性、通讯协议、数据传输速率等因素,以确保系统能够正常运行。
推荐-基于MCGS的6MW循环流化床锅炉燃烧过程自动控制系
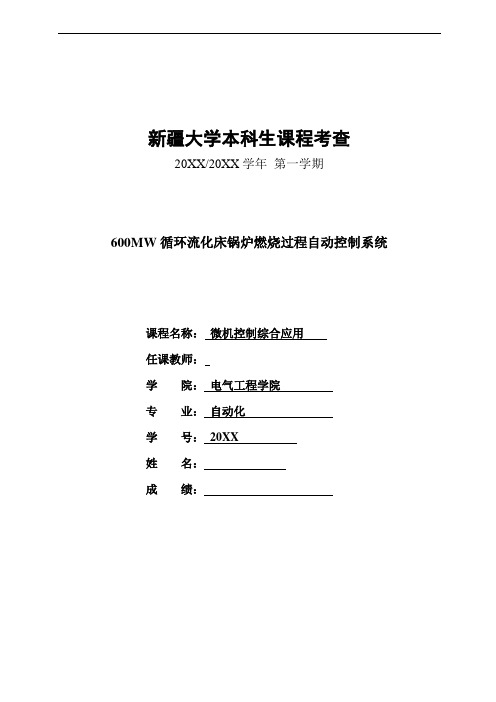
新疆大学本科生课程考查20XX/20XX学年第一学期600MW循环流化床锅炉燃烧过程自动控制系统课程名称:微机控制综合应用任课教师:学院:电气工程学院专业:自动化学号:20XX姓名:成绩:调研1、问题的提出:随着电力工业的发展,高参数大容量的火力发电机组在电网中所占的比例越来越大,电网因用电结构变化,负荷峰谷逐差逐步加大,因此要求大型机组具有带变动负荷运行的能力,以便迅速满足负荷变化的需要及参加电网调频。
另外,机组容量不断地增加,锅炉的蓄热量相对减少,采用机炉分别控制方式已不适应外界负荷的要求和保持机炉之间的平衡,因此通常采用锅炉汽轮发电机组的单元制运行方式。
2、解决问题总体方案:我们采用循环流化床锅炉燃烧控制。
1)燃烧控制系统主要由锅炉的燃烧室(炉膛)、送风装置、送煤装置、灰渣排放装置、引凤装置等组成。
主要功能是完成燃料的燃烧过程,将燃料所含能量以热能形式释放出来,用于加热锅炉里的水。
主要流程有烟气流程、通风流程、排灰出渣流程、给煤控制流程等。
燃烧过程控制的根本任务是使燃料所提供的热量适应锅炉蒸汽负荷的要求,保证锅炉安全运行。
燃烧过程的具体任务及其控制策略因燃料种类、制粉系统、燃烧设备及锅炉的运行方式的不同而有所不同。
具体而言,燃烧控制的基本任务可归纳为以下几点:(1)维持蒸汽压力稳定,(2)保证燃烧过程的经济性,(3)维持炉膛压力稳定。
锅炉燃烧过程的上述三项控制任务是不可分开的,它的三个被控参数蒸汽压力、过剩空气系数或最佳含氧量、炉膛压力与三个调节量燃料量、送风量、引风量间存在着关联。
因此燃烧控制系统内各子系统应协调运作,共同完成其控制任务。
2)燃烧过程的有关参数及其影响:(1)给煤。
给煤量影响送进床料的热量。
(2)循环流化床风速和风量。
风速影响床料流动性、气泡直径及床内燃烧率等,进而影响液化质量和燃烧效率。
(3)床料高度。
其高度的变化影响床温。
(4)过剩空气系数。
在一定范围内,提高过剩空气系数可改善燃烧效率,但其很高时,将导致床温下降,CO浓度升高,总的燃烧效率下降。
- 1、下载文档前请自行甄别文档内容的完整性,平台不提供额外的编辑、内容补充、找答案等附加服务。
- 2、"仅部分预览"的文档,不可在线预览部分如存在完整性等问题,可反馈申请退款(可完整预览的文档不适用该条件!)。
- 3、如文档侵犯您的权益,请联系客服反馈,我们会尽快为您处理(人工客服工作时间:9:00-18:30)。
基于MCGS的天然气燃烧装置控制系统的设计
摘要:采用MCGS组态软件设计燃烧控制系统,通过昆仑通态(MCGS)TPC7062KS 触摸屏作为人机界面,不仅可以实时监控工业炉内燃烧状况及控制系统的运行情况,而且可以进行数据分析,分析故障原因,对燃烧系统进行全面的监控。
控制系统采用PID温度控制器,可使控制过程在短时间内达到预定的设定值,同时尽可能抑制升温过程中的超调现象或外部负载干扰,达到精准可靠控制。
关键词:PID控制;MCGS组态;PLC控制
DOI:10.16640/ki.37-1222/t.2016.12.061
0 引言
燃烧装置在冶金行业、石油化工、铸造行业等广泛应用。
燃烧装置的燃料主要有油和气两种,本设计以天然气燃烧控制系统为例进行设计。
燃烧控制系统主要以精准的、稳定的闭环系统来控制燃烧室的温度,达到控制工艺要求的目的。
电控系统采用PLC控制,温控系统采用智能PID温控器,实现空气燃气量的自动调节。
利用MCGS组态软件实现上位机与PLC、温控器之间的通信,并对现场设备运行状态实时监控。
1 燃烧控制系统的组成及原理
(1)燃烧装置的组成。
燃烧装置主要由燃烧器、燃气
主管路、点火管路、风管路组成。
(2)控制系统的组成。
控制系统主要有火焰检测控制
系统、燃气压力检测控制系统、自动点火控制系统、空气燃气自动控制系统和上位机监控通信系统组成[1]。
(3)工作原理。
为了实现炉膛工件的加热温度保持恒定,炉膛温度和给定温度通过PID控制器,手/自动整定PID 参数,来控制加热装置,使加热炉温度为恒定,并能实时显示当前温度值。
燃气量和空气量构成比例控制,输出的理论分量和实际分量构成PID控制,输出到调节器进行调风。
(4)工作原理框图。
工作原理框图见图1。
2 燃烧控制系统的控制功能
2.1 火焰检测控制系统
在燃烧室内安装火焰检测器,通过火检信号来控制燃气管道上截止阀的通断,同时,具有熄火报警保护功能。
2.2 压力检测控制系统
在燃气管道上安装压力表和压力传感器,通过检测超压、低压信号来控制燃气截止阀的通断,同时,具有超高压和超低压报警功能。
2.3 自动点火控制系统
在燃烧室内安装可自动伸缩的点火枪,点火枪点火成功后,自动退出燃烧室,来延长点火枪的使用寿命。
2.4 空气燃气自动控制系统
利用PID控制器来实现空气燃气自动调节,通过空气量燃气量适当的配比,可使燃料充分燃烧并快速达到预期工艺要求。
2.5 控制柜
控制柜除了正常的配电功能外,主要以S7-200为控制核心,通过控制程序来实现逻辑控制工艺要求。
采用232/485通信协议与上位机进行通信。
控制柜安装温控仪表和流量监测仪表,可以实时采集现场数据信息,以供显示和计算偏差。
2.6 工控机
工控机采用安装有MCGS组态软件和SETP7软件的工业PC机,通过MCGS组态软件生成的HMI界面,具有画面模拟与监控、故障报警显示与分析、数据报表显示与输出等功能。
例如:模拟燃烧控制元件的状态、燃烧室内的燃烧状态,数据报表,实时温度曲线等。
通过SETP7软件可在线修改、调试用户程序,并查看用户程序的执行状态。
3 燃烧控制系统的组态设计
3.1 MCGS组态软件
MCGS是为工业过程控制和实时监测领域服务的通用计算机系统软件,具有功能完善、操作简便、可视性好、可维护性强的突出特点。
MCGS组态软件所建立的工程由主控窗口、设备窗口、用户窗口、实时数据库和运行策略五部分构
成,每一部分分别进行组态操作,完成不同的工作,具有不同的特性[2]。
本设计采用昆仑通态(MCGS)TPC7062KS 触摸屏作为人机界面。
TPC7062KS是一款以嵌入式低功耗CPU 为核心的高性能嵌入式一体化工控机。
该产品预装了微软嵌入式实时多任务操作系统和MCGS 嵌入式组态软件。
3.2 组态窗口(HMI)设计
用户窗口设计。
用户窗口设计主要是监控画面的制作,主要包括主页面设计、监控页面设计、报表页面设计、报警页面设计等。
①主页面设计。
主页面主要包括燃烧监控系统、温度监控系统、温度报警系统和控制柜几部分。
可以实现各个界面之间的相互切换。
并将此窗口设置为启动窗口。
②监控页面设计。
燃烧监控系统主要模拟实际工况,显示管路内介质的动态流动效果、各种电气设备的通断情况、燃烧室内的燃烧状况及自动点火的过程。
能做到与现场设备同步运行。
燃烧监控系统图见图2。
③报表及报警页面设计。
本控制系统需要保持炉膛温度恒定,对温度要求严格,所以对温度数据进行监测和存储。
温度不仅需要实时数据监测,还要有历史数据记录,同时还设置有超温报警功能。
3.3 设备窗口的设计
为了能够使HMI与PLC、温控仪表成功通讯,必须把定义好的数据对象与PLC内部变量和温控仪表的变量进行设置。
首先选择通用串口父设备,设置属性,选择串口端口号、波特率等然后检查确定,其次选择要连接的设备,西门子
S7200PPI,进行设备编辑,新增设备通道,建立与PLC的变
量连接。
PID温控仪表,进行设备编辑,新增设备通道,建
立与仪表的数据连接。
设备连接设置图见图3。
3.4 动画制作
设置动画链接,将监控画面中的电气元件与数据库中的变量依次建立链接。
分别设置动画连接的基本属性和操作属性,编写动作脚本。
3.5 调试
系统配置完成,对系统进行调试。
首先进行通讯测试,当检测到通讯测试正常,进行工程下载,完成下载。
其次启动运行,系统直接跳转到启动页面,这时就可以进行各个页面之间的切换,实现实时监控的作用。
4 结语
燃烧控制系统采用MCGS组态软件进行设计,不仅使控制原理及实时工况一目了然,而且提高了控制系统的先进性。
系统采用组态控制后,运行可靠,投资低,能够实现燃烧控制系统的工艺要求,达到预期的目标,为企业创造一定的经济效益。
参考文献:
[1]王英.回转窑天然气燃烧装置控制系统的设计[J].科技与企业,2015(05).
[2]刘小春.基于MCGS和PLC的电机运行参数监控系统设计[J].自动化技术及应用,2010(09).
作者简介:王英(1982-),女,满族,学士学位,工程师,研究方向:工业控制自动化。