高强度紧固件制造技术
高强度紧固件材料的技术特性
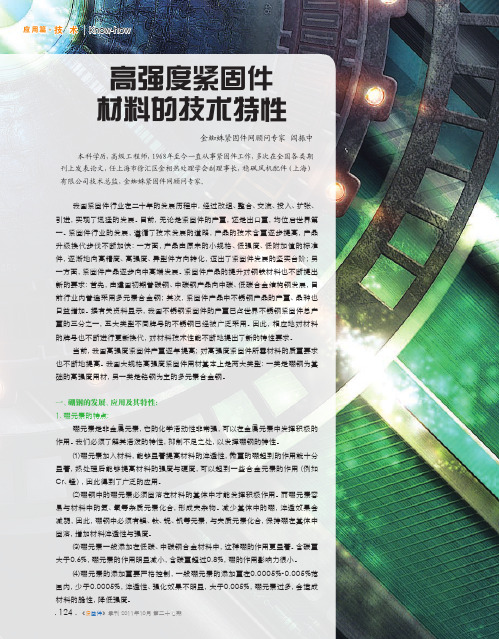
我国紧固件行业在二十年的发展历程中,经过改组、整合、交流、投入、扩张、引进,实现了迅猛的发展。
目前,无论是紧固件的产量,还是出口量,均位居世界第一。
紧固件行业的发展,遵循了技术发展的道路,产品的技术含量逐步提高,产品升级换代步伐不断加快:一方面,产品由原来的小规格、低强度、低附加值的标准件,逐渐地向高精度、高强度、异型件方向转化,迈出了紧固件发展的坚实台阶;另一方面,紧固件产品逐步向中高端发展。
紧固件产品的提升对钢铁材料也不断提出新的要求:首先,由建国初期普碳钢、中碳钢产品向中碳、低碳合金结构钢发展,目前行业内普遍采用多元素合金钢;其次,紧固件产品中不锈钢产品的产量、品种也日益增加。
据有关资料显示,我国不锈钢紧固件的产量已占世界不锈钢紧固件总产量的三分之一,五大类型不同牌号的不锈钢已经被广泛采用。
因此,相应地对材料的牌号也不断进行更新换代,对材料技术性能不断地提出了新的特性要求。
当前,我国高强度紧固件产量逐年提高;对高强度紧固件所需材料的质量要求也不断地提高。
我国大规格高强度紧固件用材基本上是两大类型:一类是硼钢为基础的高强度用材,另一类是铬钢为主的多元素合金钢。
一、硼钢的发展、应用及其特性:1. 硼元素的特点:硼元素是非金属元素,它的化学活动性非常强,可以在金属元素中发挥积极的作用。
我们必须了解其活泼的特性,抑制不足之处,以发挥硼钢的特性。
⑴硼元素加入材料,能够显著提高材料的淬透性,微量的硼起到的作用就十分显著,热处理后能够提高材料的强度与硬度,可以起到一些合金元素的作用(例如Cr、锰),因此得到了广泛的应用。
⑵硼钢中的硼元素必须固溶在材料的基体中才能发挥积极作用。
而硼元素容易与材料中的氮、氧等杂质元素化合,形成夹杂物。
减少基体中的硼,淬透效果会减弱,因此,硼钢中必须有铝、钛、铌、钒等元素,与夹质元素化合,保持硼在基体中固溶,增加材料淬透性与强度。
⑶硼元素一般添加在低碳、中碳钢合金材料中,这样硼的作用更显著。
高强螺栓生产工艺
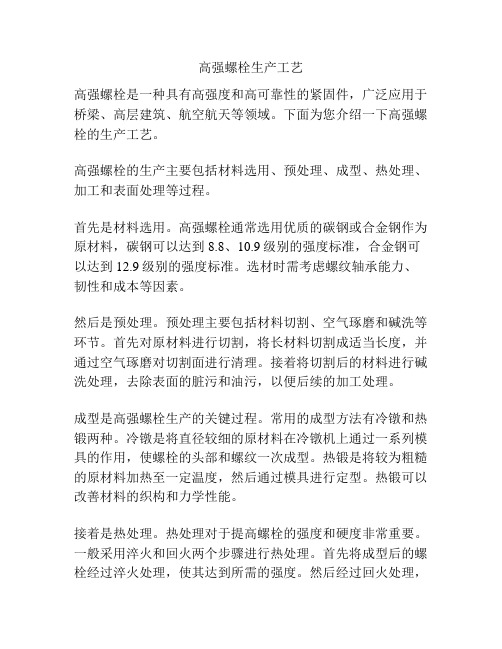
高强螺栓生产工艺高强螺栓是一种具有高强度和高可靠性的紧固件,广泛应用于桥梁、高层建筑、航空航天等领域。
下面为您介绍一下高强螺栓的生产工艺。
高强螺栓的生产主要包括材料选用、预处理、成型、热处理、加工和表面处理等过程。
首先是材料选用。
高强螺栓通常选用优质的碳钢或合金钢作为原材料,碳钢可以达到8.8、10.9级别的强度标准,合金钢可以达到12.9级别的强度标准。
选材时需考虑螺纹轴承能力、韧性和成本等因素。
然后是预处理。
预处理主要包括材料切割、空气琢磨和碱洗等环节。
首先对原材料进行切割,将长材料切割成适当长度,并通过空气琢磨对切割面进行清理。
接着将切割后的材料进行碱洗处理,去除表面的脏污和油污,以便后续的加工处理。
成型是高强螺栓生产的关键过程。
常用的成型方法有冷镦和热锻两种。
冷镦是将直径较细的原材料在冷镦机上通过一系列模具的作用,使螺栓的头部和螺纹一次成型。
热锻是将较为粗糙的原材料加热至一定温度,然后通过模具进行定型。
热锻可以改善材料的织构和力学性能。
接着是热处理。
热处理对于提高螺栓的强度和硬度非常重要。
一般采用淬火和回火两个步骤进行热处理。
首先将成型后的螺栓经过淬火处理,使其达到所需的强度。
然后经过回火处理,降低螺栓的脆性,提高其韧性和硬度。
加工是对螺栓进行精细加工的过程。
加工包括车削、铣削、钻孔和磨削等工艺。
通过这些工艺可以对螺栓进行尺寸精密加工,保证其质量和使用性能。
最后是表面处理。
高强螺栓通常需要进行防腐处理。
常用的表面处理方法有镀锌、镀镍和磷化等。
这些方法可以提高螺栓的抗腐蚀性能,延长其使用寿命。
以上就是高强螺栓的生产工艺,通过合理的材料选用和工艺流程,可以生产出高质量的高强螺栓,满足各种建筑和工程领域的需求。
紧固件制造流程
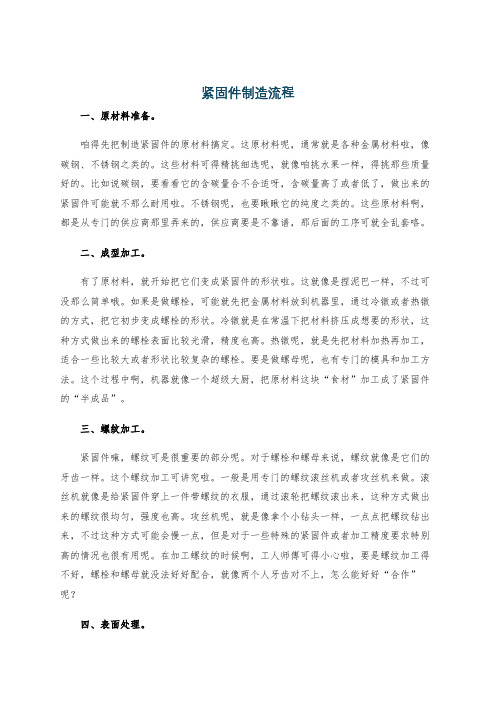
紧固件制造流程一、原材料准备。
咱得先把制造紧固件的原材料搞定。
这原材料呢,通常就是各种金属材料啦,像碳钢、不锈钢之类的。
这些材料可得精挑细选呢,就像咱挑水果一样,得挑那些质量好的。
比如说碳钢,要看看它的含碳量合不合适呀,含碳量高了或者低了,做出来的紧固件可能就不那么耐用啦。
不锈钢呢,也要瞅瞅它的纯度之类的。
这些原材料啊,都是从专门的供应商那里弄来的,供应商要是不靠谱,那后面的工序可就全乱套咯。
二、成型加工。
有了原材料,就开始把它们变成紧固件的形状啦。
这就像是捏泥巴一样,不过可没那么简单哦。
如果是做螺栓,可能就先把金属材料放到机器里,通过冷镦或者热镦的方式,把它初步变成螺栓的形状。
冷镦就是在常温下把材料挤压成想要的形状,这种方式做出来的螺栓表面比较光滑,精度也高。
热镦呢,就是先把材料加热再加工,适合一些比较大或者形状比较复杂的螺栓。
要是做螺母呢,也有专门的模具和加工方法。
这个过程中啊,机器就像一个超级大厨,把原材料这块“食材”加工成了紧固件的“半成品”。
三、螺纹加工。
紧固件嘛,螺纹可是很重要的部分呢。
对于螺栓和螺母来说,螺纹就像是它们的牙齿一样。
这个螺纹加工可讲究啦。
一般是用专门的螺纹滚丝机或者攻丝机来做。
滚丝机就像是给紧固件穿上一件带螺纹的衣服,通过滚轮把螺纹滚出来,这种方式做出来的螺纹很均匀,强度也高。
攻丝机呢,就是像拿个小钻头一样,一点点把螺纹钻出来,不过这种方式可能会慢一点,但是对于一些特殊的紧固件或者加工精度要求特别高的情况也很有用呢。
在加工螺纹的时候啊,工人师傅可得小心啦,要是螺纹加工得不好,螺栓和螺母就没法好好配合,就像两个人牙齿对不上,怎么能好好“合作”呢?四、表面处理。
紧固件做好了形状和螺纹,还不能就这么结束呢。
表面处理也是很关键的一步。
为啥要做表面处理呢?就像咱化妆一样,是为了让紧固件更好看,更耐用。
比如说镀锌,这是很常见的一种表面处理方式。
把紧固件放到锌液里泡一泡,或者用电镀的方式给它镀上一层锌。
高强度铝或铝合金紧固件及其制造方法与设计方案
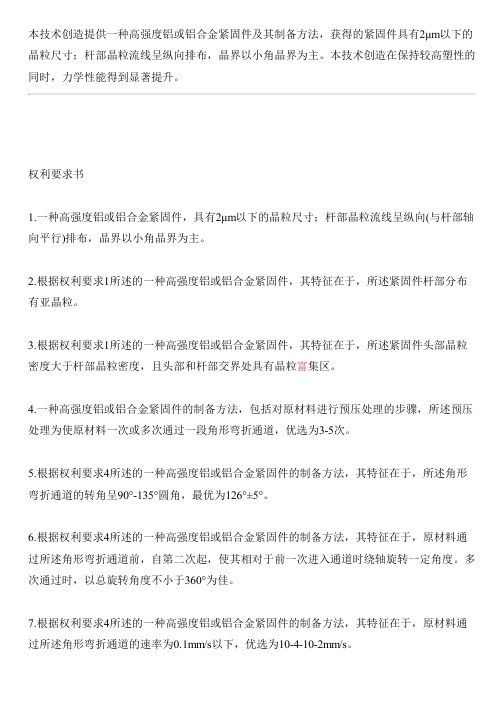
本技术创造提供一种高强度铝或铝合金紧固件及其制备方法,获得的紧固件具有2μm以下的晶粒尺寸;杆部晶粒流线呈纵向排布,晶界以小角晶界为主。
本技术创造在保持较高塑性的同时,力学性能得到显著提升。
权利要求书1.一种高强度铝或铝合金紧固件,具有2μm以下的晶粒尺寸;杆部晶粒流线呈纵向(与杆部轴向平行)排布,晶界以小角晶界为主。
2.根据权利要求1所述的一种高强度铝或铝合金紧固件,其特征在于,所述紧固件杆部分布有亚晶粒。
3.根据权利要求1所述的一种高强度铝或铝合金紧固件,其特征在于,所述紧固件头部晶粒密度大于杆部晶粒密度,且头部和杆部交界处具有晶粒富集区。
4.一种高强度铝或铝合金紧固件的制备方法,包括对原材料进行预压处理的步骤,所述预压处理为使原材料一次或多次通过一段角形弯折通道,优选为3-5次。
5.根据权利要求4所述的一种高强度铝或铝合金紧固件的制备方法,其特征在于,所述角形弯折通道的转角呈90°-135°圆角,最优为126°±5°。
6.根据权利要求4所述的一种高强度铝或铝合金紧固件的制备方法,其特征在于,原材料通过所述角形弯折通道前,自第二次起,使其相对于前一次进入通道时绕轴旋转一定角度。
多次通过时,以总旋转角度不小于360°为佳。
7.根据权利要求4所述的一种高强度铝或铝合金紧固件的制备方法,其特征在于,原材料通过所述角形弯折通道的速率为0.1mm/s以下,优选为10-4-10-2mm/s。
8.根据权利要求4所述的一种高强度铝或铝合金紧固件的制备方法,其特征在于,所述角形弯折通道的直径比紧固件目标产品的杆部标准直径略大,以大1±0.5mm为佳。
9.根据权利要求4所述的一种高强度铝或铝合金紧固件的制备方法,其特征在于,所述预压处理过程中,可以施加润滑和/或进行冷却。
10.根据权利要求4所述的一种高强度铝或铝合金紧固件的制备方法,其特征在于,所述制备方法还包括在预压处理后,对原材料进行终压成型的步骤。
高强度紧固件的制造工艺

高强度紧固件的制造工艺高强度紧固件是一种用于连接和固定机械设备的特殊零件,它们承受着很大的力和振动负荷。
高强度紧固件的制造工艺是确保其性能和质量的关键。
高强度紧固件的制造一般包括以下几个步骤:1. 材料选择:高强度紧固件的制造通常采用高强度合金钢材料,如40Cr、35CrMo等。
这些材料具有较高的强度和韧性,能够满足紧固件在使用过程中的要求。
同时,材料的选择也需要考虑到紧固件的使用环境和温度等因素。
2. 热处理:热处理是高强度紧固件制造的一个重要步骤,它能够提高紧固件的强度和硬度。
常用的热处理方法包括淬火、回火和正火等。
通过热处理,可以改变材料的组织结构,得到均匀的组织和理想的硬度分布,提高紧固件的强度和韧性。
3. 切削加工:紧固件的制造过程中需要进行各种形状的切削加工,如车削、铣削、钻削等。
这些切削工艺可以用于制造紧固件的外形和孔径等部分,确保紧固件的尺寸和形状精度。
4. 成形加工:成形加工是指通过冷镦、热锻和冷锻等方法,将材料加工成为紧固件的形状。
成形加工可以提高紧固件的强度和硬度,并改变其内部组织结构和性能。
5. 表面处理:高强度紧固件通常需要进行表面处理,以提高其抗腐蚀性能和耐磨性。
常用的表面处理方法包括镀锌、镀镍、磷化和氮化等。
这些表面处理方法可以形成一层保护膜,保护紧固件不受外界环境的侵蚀。
6. 检测和质量控制:紧固件的制造过程中需要进行各种检测和质量控制措施,以确保产品的质量。
常用的检测方法包括尺寸检测、力学性能测试、金相分析和超声波检测等。
通过这些检测方法,可以检验紧固件的尺寸精度、强度和韧性等指标,确保其满足设计和使用要求。
在整个高强度紧固件的制造过程中,各个工艺步骤需要严格控制,以确保紧固件的性能和质量。
通过科学合理的制造工艺,可以提高紧固件的强度、硬度和使用寿命,确保其在各种严苛工况下的安全可靠性。
不仅如此,制造工艺的不断创新和优化,也可以提高制造效率和降低成本,满足市场的需求。
高强度紧固件生产工艺流程
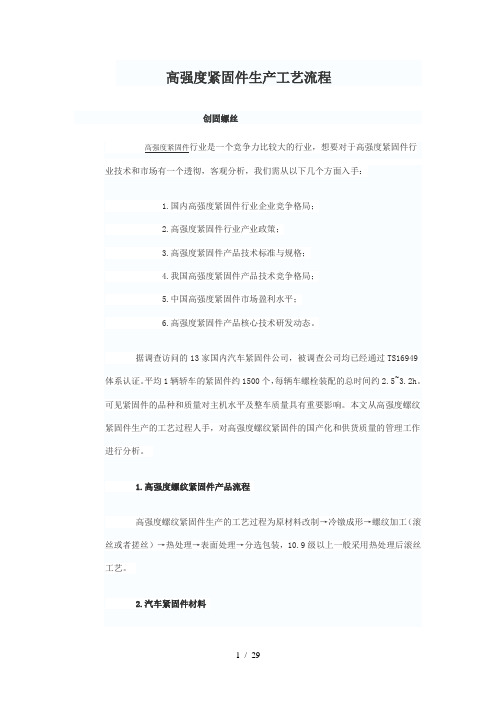
高强度紧固件生产工艺流程创固螺丝高强度紧固件行业是一个竞争力比较大的行业,想要对于高强度紧固件行业技术和市场有一个透彻,客观分析,我们需从以下几个方面入手:1.国内高强度紧固件行业企业竞争格局;2.高强度紧固件行业产业政策;3.高强度紧固件产品技术标准与规格;4.我国高强度紧固件产品技术竞争格局;5.中国高强度紧固件市场盈利水平;6.高强度紧固件产品核心技术研发动态。
据调查访问的13家国内汽车紧固件公司,被调查公司均已经通过TS16949体系认证。
平均1辆轿车的紧固件约1500个,每辆车螺栓装配的总时间约2.5~3.2h。
可见紧固件的品种和质量对主机水平及整车质量具有重要影响。
本文从高强度螺纹紧固件生产的工艺过程人手,对高强度螺纹紧固件的国产化和供货质量的管理工作进行分析。
1.高强度螺纹紧固件产品流程高强度螺纹紧固件生产的工艺过程为原材料改制→冷镦成形→螺纹加工(滚丝或者搓丝)→热处理→表面处理→分选包装,10.9级以上一般采用热处理后滚丝工艺。
2.汽车紧固件材料高强度螺栓常用的钢材牌号为:“8.8级”螺栓用35钢、45钢、ML35钢“10.9级”螺栓用35CrMo;40Cr“12.9级”螺栓用35CrMo,42CrMo、SCM435汽车标准件用国内材料主要以宝钢公司生产的材料为主,其在国内轿车轮胎、商用车发动机等特种高强度紧固件的用钢市场占有率较高。
目前,宝钢公司已成为一汽、东风、上汽等公司特殊标准件用钢的指定厂家。
10.9级和12.9级发动机用紧固件进口材料主要来自日本神户、日本新日铁、韩国浦项等公司。
进口材料淬透性好、纯净度高,装配稳定。
成本约高于国内材料的15%-20%。
目前,国内高强度螺栓生产质量最好的上海特强公司从原材料(进口)、冷镦工艺、热处理、表面处理全部按照日本合资方的流程生产,其质量稳定,但成本较高。
国内规模最大的汽车标准件公司?东风汽标对乘用车用紧固件的材料选用也是以进口材料为主,商用车选用宝钢公司材料。
风电塔架高强紧固件技术规范 10 02 09
3.4.2 无损检测设备
无损检测设备按照相关的标准由权威部门进行校验和标定。 4 生产准备 4.1 本公司要求供应商在生产前提供下列文件 1)质量计划 2)生产计划 3)运输计划 4)工艺规程 5)热处理规范 6)表面处理规范 7)主要原材料名称规格及供应商名称 8)主要操作工名单及资质证明 9)无损检验人员名单及资质证明 10)无损检验规范 11)材料转换 (如果有) 12)项目负责人及项目组织机构图
要求供应商制订生产和检验计划,其目的是给出生产和检验工艺 的详细说明。使每个操作者充分了解并贯彻执行。生产和检验计划至 少应该包括如下内容:适用范围、引用的文件、产品特性分析、工艺 特性分析、材料要求(化学成分)、机械性能(拉伸强度、冲击性能、 试样的位置)、制造工艺规范或车间工作指导书、标记打印和装运、 交工文件(证书和报告)。
螺栓的性能等级为 8.8 级,其机械性能应符合 GB/T3098.1-2000 中 8.8 级的要求。对于螺纹公称直径≥20mm 的螺栓(螺钉或螺柱),
9
风电机组塔架高强度紧固件技术质量规范 按 GB/T229-2007 中关于标准夏比 V 型缺口冲击试件的规定制成试件, 螺栓低温(-40℃)冲击吸收功平均值大于或等于 37J,一组试件允 许有一件冲击功的最小值小于 27J,但不小于平均值的 70%。 5.3.2 螺母
螺栓实物的机械性能试验项目为楔负载、保证载荷和硬度,试验 结果应符合 GB/T3098.1-2000 中 10.9 级的要求。螺栓机加工试件的 机械性能测试项目为抗拉强度、规定非比例伸长应力、断后伸长率、 断面收缩率,试验结果应符合 GB/T3098.1-2000 中 10.9 级的要求。 螺栓规格直径小于或等于 M39 为中心取样,大于 M39 为偏心取样。
高强度螺栓生产加工工艺流程
高强度螺栓生产加工工艺流程高强度螺栓生产主要分为热轧盘条-(冷拨)-球化(软化)退火-机械除鳞-酸洗-冷拨-冷锻成形-螺纹加工-热处理-检验几步!一,钢材设计在紧固件制造中,正确选用紧固件材料是重要一环,因为紧固件的性能和其材料有着密切的关系。
如材料选择不当或不正确,可能造成性能达不到要求,使用寿命缩短,甚至发生意外或加工困难,制造成本高等,因此紧固件材料的选用是非常重要的环节。
冷镦钢是采用冷镦成型工艺生产的互换性较高的紧固件用钢。
由于它是常温下利用金属塑性加工成型,每个零件的变形量很大,承受的变形速度也高,因此,对冷镦钢原料的性能要求十分严格。
在长期生产实践和用户使用调研的基础上,结合GB/T6478-2001《冷镦和冷挤压用钢技术条件》GB/T699-1999《优质碳素结构钢》及目标JISG3507-1991《冷镦钢用碳素钢盘条》的特点,以8.8级,9.8级螺栓螺钉的材料要求为例,各种化学元素的确定。
C含量过高,冷成形性能将降低;太低则无法满足零件机械性能的要求,因此定为0.25%-0.55%。
Mn能提高钢的渗透性,但添加过多则会强化基体组织而影响冷成形性能;在零件调质时有促进奥氏体晶粒长大的倾向,故在国际的基础上适当提高,定为0.45%-0.80%。
Si能强化铁素体,促使冷成形性能降低,材料延伸率下降定为Si小于等于0.30%。
S.P.为杂质元素,它们的存在会沿晶界产生偏析,导致晶界脆化,损害钢材的机械性能,应尽可能降低,定为P小于等于0.030%,S小于等于0.035%。
B.含硼量最大值均为0.005%,因为硼元素虽然具有显著提高钢材渗透性等作用,但同时会导致钢材脆性增加。
含硼量过高,对螺栓,螺钉和螺柱这类需要良好综合机械性能的工件是十分不利的。
二,球化(软化)退火沉头螺钉,内六角圆柱头螺栓采用冷镦工艺生产时,钢材的原始组织会直接影响着冷镦加工时的成形能力。
冷镦过程中局部区域的塑性变形可达60%-80%,为此要求钢材必须具有良好的塑性。
高强螺栓生产工艺流程
高强螺栓生产工艺流程下载温馨提示:该文档是我店铺精心编制而成,希望大家下载以后,能够帮助大家解决实际的问题。
文档下载后可定制随意修改,请根据实际需要进行相应的调整和使用,谢谢!并且,本店铺为大家提供各种各样类型的实用资料,如教育随笔、日记赏析、句子摘抄、古诗大全、经典美文、话题作文、工作总结、词语解析、文案摘录、其他资料等等,如想了解不同资料格式和写法,敬请关注!Download tips: This document is carefully compiled by theeditor. I hope that after you download them,they can help yousolve practical problems. The document can be customized andmodified after downloading,please adjust and use it according toactual needs, thank you!In addition, our shop provides you with various types ofpractical materials,such as educational essays, diaryappreciation,sentence excerpts,ancient poems,classic articles,topic composition,work summary,word parsing,copy excerpts,other materials and so on,want to know different data formats andwriting methods,please pay attention!高强螺栓生产工艺流程解析高强螺栓是一种常用于钢结构连接的紧固件,其生产工艺流程主要包括原材料采购、加工制造、成品检验等多个环节。
高强度螺栓加工工艺
高强度螺栓加工工艺螺栓类零件是一种重要标准件,用做连接紧固件,在各领域的应用相当广泛,根据其机械和物理性能的不同,分成10种类别,其中机械性能等级大于等于8.8级的螺栓,我们通常称其为高强度螺栓。
一、高强度螺栓主要结构及作用高强度螺栓种类较多,形状也不尽相同,外部尺寸更是千变万化,但整体上其主要结构和整体外部形状具有一定的相似性。
根据这些相似性,我们将其分成三个主要部分:头部、杆部和螺纹部分。
如下简图所示:下面我们简要介绍一下各部分的作用极其重点要素:1. 头部头部主要作用是在螺母与螺栓配合时施加一个反向力矩,保证螺母有足够拧紧力矩。
形式种类较多,主要有方头、半圆头、六角头等形式。
另外,一些非标准件高强度螺栓头部形式由设计者根据装配需要特别设计。
2. 杆部杆部主要起导向作用,特别是导径螺栓,装配后承受一定的径向剪切力,要求与孔小间隙配合,对杆部外圆精度和粗糙度要求严格。
一些装配后只承受轴向拉伸力的螺栓对杆部要求不是很严格,外圆尺寸公差较大。
对高强度螺栓来说,杆部与头部接触部位要求一定圆角,避免承受较大拉力时该部位断裂,同时避免热处理冷却时产生裂纹,是加工重点注意要素。
3. 螺纹部分螺纹部分是螺栓最主要部分,主要起连接紧固作用。
可以分成有效螺纹部分,收尾部分(退刀部分)和螺纹末端三部分;螺纹三个主要要素:螺距、牙形半角和螺距,直接影响螺纹配合精度,也是加工重点注意要素。
二、高强度螺栓工艺分析高强度螺栓机械加工一般不需要精度极高的专用机床,在普通设备上即可完成加工。
根据其三个主要部分,我们将其加工工艺分成三部分:头部的加工、杆部加工和螺纹加工。
每一部分的加工工艺又因其尺寸形状及技术要求的不同分成若干种类,采用不同的加工方法;虽然我们将其分成了三部分,但三部分的加工是相辅相成的,相互关联的,可能共存于同一工序,也可能共存于同一工步。
1. 头部的加工⑴毛坯毛坯形式:螺栓头部形状直接决定产品毛坯形式。
一般来说,方头螺栓毛坯可选用冷拉方钢,六角头螺栓毛坯可选用冷拉六角钢,半圆头螺栓毛坯应选用锻件毛坯;头部形状特别设计的螺栓应根据具体形状具体分析选用毛坯,为避免增加头部加工工序,在技术要求允许的情况下建议选用锻件毛坯;头部最大被包容尺寸和杆部外圆尺寸相差较大或者整体长度尺寸较大的,为减少材料浪费和减少加工工时,建议选用锻件毛坯。
- 1、下载文档前请自行甄别文档内容的完整性,平台不提供额外的编辑、内容补充、找答案等附加服务。
- 2、"仅部分预览"的文档,不可在线预览部分如存在完整性等问题,可反馈申请退款(可完整预览的文档不适用该条件!)。
- 3、如文档侵犯您的权益,请联系客服反馈,我们会尽快为您处理(人工客服工作时间:9:00-18:30)。
终端用户和供应商如何明确地选用紧固件标准对于紧固件的质量至关重要紧固件行业教育集团(FIEG)供稿国家紧固件经销商协会(NFDA)工业紧固件协会(IFI)合著NFDA 工业紧固件协会 (IFI)紧固件行业教育集团 – 紧固件标准明确地选用2007年11月1日第1页共20页前言国家紧固件经销商协会(NFDA)以及工业紧固件协会(IFI) 的人员联合组成了一个工作小组共同撰写了本文。
本文全面介绍了采用正确的步骤来保证进入商业流通的紧固件都是合格产品的重要性。
为了达到上述目的,在本文中,明确规范各方在供应链中的职责。
上述工作小组的名称为紧固件行业教育集团(FIEG),以下为该工作小组的工作任务:由国家紧固件经销商协会-工业紧固件协会的人员成立的紧固件行业教育集团(FIEG)的工作任务为教育所有紧固件终端用户和和供应商(制造商,进口商,经销商)关于认识和有效应用行业和政府紧固件标准的重要性,以及如何判断产品是否符合这些标准。
1. 介绍:正确和详细规范紧固件的重要性。
标准是紧固件行业的基础。
如果能够理解并且遵循一致性的紧固件标准,将能更有效地生产、配销与使用,以降低经营成本。
如果终端用户要求特殊设计的紧固件,他们也必须尽量引用各种适用其紧固件特性的现有标准。
一旦紧固件用户理解尽量使用现有的紧固件的标准,以可减少质量问题,进而降低成本。
如果紧固件供应商能够理解这些标准并且始终遵循应用于其销售的产品的这些标准,对于客户有较有实际效益。
供应商本身也能够减少错误,从而降低经济损失也节省理解这些问题所要花费的时间。
理解并遵循紧固件标准将降低经营成本,从而给用户和供应商均带来更高的效率和收益。
如果所有的紧固件都能够一直遵循各自的适用标准,将大大的降低消费型和工业型产品以及设备的失效数,以保障大众安全。
紧固件行业教育集团 – 紧固件标准明确地选用2007年11月1日第2页共20页2. 什么是紧固件标准?a. 紧固件标准指的是由标准机构制定的文件用来保证紧固件(合适的尺寸)能够正确地满足它们的设计用途,安装到位以后,这些紧固件将可以提供需要的设计功能(强度,寿命,防腐蚀性等)。
紧固件终端用户和供应商(制造商以及代销商)负责理解并且正确彻底的应用紧固件标准从而保证达到终端产品的设计质量,并且避免在采购过程中发生错误和误解。
紧固件标准中包含了对于不同类型的紧固件的尺寸,材料,机械特性要求。
终端用户参考这些标准来决定适用于某种用途的合适的紧固件。
紧固件制造商利用这些标准来指导制造紧固件。
所有的用户和供应商遵循这些标准的试验和检验要求从而来保证产品的合格性。
b.最常见的紧固件标准机构有哪些?i. 美国机械工程师学会 (ASME)主要涵盖了紧固件的尺寸要求。
ASME标准涵盖建筑以及普通工业装配的紧固件。
ii. 美国材料与试验协会(ASTM)主要涵盖了材料化学成份和机械试验要求。
ASTM标准涵盖建筑和通用工业产业中的紧固件。
iii. 美国汽车工程师学会 (SAE) 主要涵盖了材料化学成份和汽车,航空航天,以及其它通用工业装配用的紧固件的机械性质。
iv. 工业紧固件协会(IFI)创造许多标准包含广泛各类紧固件的尺寸,材料以及机械性质。
这些标准都旨在通过某些程度的行业认可以后,最终成为ASME, ASTM 或者SAE标准。
v. 国际标准化组织(ISO) 涵盖了关于公制紧固件的尺寸,材料和机械性质的规范标准。
ISO是用于生产在国际市场销售的产品的最通用的一种标准。
vi. 德国标准协会(DIN)涵盖了关于公制紧固件的尺寸,材料和机械性质的规范标准,但是大多数用于紧固件的DIN标准已经被取消,而由ISO标准取代了。
只有很少一部分的DIN标准现在还在使用当中。
紧固件行业教育集团 – 紧固件标准明确地选用2007年11月1日第3页共20页vii. 日本工业标准 (JIS) 中包含了关于公制紧固件的尺寸,材料和机械性质的规范标准。
许多用于紧固件的JIS标准已经被取消,而由ISO标准取代了,但是仍然还有很少一部分的JIS标准现在还在使用当中。
在日本汽车制造行业中,JIS标准仍然占据着主导地位。
viii. 美国航天工业协会 (AIA) 的国家航空航天标准委员会(NASC)编制了并且维护着国家航空航天标准(NAS英寸制和NA公制),适用于用于航空航天和国防工业的紧固件。
此外,过去的军用标准(MS)和军队/海军标准(AN)合并构成了现在的国家航空航天军用标准(NASM),NASM标准也已经转变成为了NASC的一部分以便得到维护和更新。
ix. 欧洲航天工业—标准化协会 (AECMA) 编制并公布了欧洲标准(EN)适用于航空航天和国防工业。
x. 英国航空航天公司协会(SBAC) 编制并公布了航天标准(AS)用于航空航天和国防工业。
c. 紧固件标准是由谁创建并且维护的呢?紧固件标准是由一些具有技术背景的人士志愿编写维护的。
这些志愿者们包括紧固件终端用户,制造商,代销商以及通过各种产品和服务来支持紧固件工业的人士。
他们的背景和日常工作各不相同,但是他们共同的兴趣在紧固件。
参与这些标准机构的条件非常简单。
最主要的要求是你必须对紧固件有着浓厚的兴趣。
标准机构的主要工作是编辑,促进和发布这些标准,但很少干涉标准的内容。
3.紧固件标准中的哪些内容可以帮助保证供应的紧固件的质量?a. 这些标注如何引导购买者订购到正确的产品?大部分的标准中都包含了订购信息以及描述订购信息的一些范例。
值得一提的是,ASTM标准中列出很完善的订购信息。
如果在其他的标准里您找不到相关的订购参考,您可以参考大部分ASTM紧固件标准中的信息和范例来进行订购。
紧固件行业教育集团 – 紧固件标准明确地选用2007年11月1日第4页共20页一个完整的紧固件说明应该包含以下各项:i. 螺纹尺寸 (英制通称直径和每英寸螺纹数,公制通称直径和螺距)ii. 长度iii. 紧固件的类型 (螺钉,螺栓,铆钉,螺母等)iv. 拧紧方式,如果适用v. 使用的紧固件标准vi. 等级或者性质级别vii. 表面处理1. 类型2. 厚度或者等级3. 使用的标准b. 一个紧固件需要经过哪些测试?紧固件标准中明确要求对以下一个或多个方面进行测试:尺寸,化学,和/或物理特性。
为了保证满足所有应用需求,一个紧固件都要经过完整的测试;以上三个方面必须经过在制造过程中或者制造完成后的验证。
(见附件中ASME B18.18.2紧固件尺寸清单和ASTM F1470紧固件物理特性测试清单)c. 谁能够进行紧固件的测试?供应链上的任何一方(制造商,承销商或者最终用户)都能对紧固件进行合规性测试,但在生产工厂处要求对紧固件至少进行一次完全测试或验证。
测试可以由供应链上的任何内部人员进行;也可外包给合格的实验室。
测试人必须熟悉所有的标准要求且具备测试需要的必要仪器与设备。
d. 什么是正确的取样数量的意义以及为何要随机取样?大部分,如果不是全部,紧固件标准都说明了为进行相应标准测试所需采用的取样计划。
使用正确的样本量使我们更加自信判断所验该批次的紧固件是否符合标准要求。
样本计划一般与最终检验相关。
如果制造商使用一个以文件化的统计数据为基础的制程检验系统(统计制程质检),那么其过程检验的测试结果一般可以被接受而取代最终检验。
紧固件行业教育集团 – 紧固件标准明确地选用2007年11月1日第5页共20页在来料检验和最终检验中,很关键的一点是从发货批次中随机抽取样本。
随机抽取的样本能够使测试和检验结果确实反映同一批次中在不同时间生产的零件的情况。
e. 紧固件的测试记录中应包含哪些内容?谁应该负责保存记录?每个批次的紧固件的测试记录应该存放在供应链中的一个或者多个地方。
至少,紧固件制造商应该保存这些记录。
当标准或者买卖双方协议中有要求时,这些记录的副本应该转交给相关方。
当紧固件的质量需要得到更严格的确认或者买卖双方协议中有要求,供应链上的任何一方都能够对紧固件的任何批次进行审核测试。
所有的测试记录都应该至少包含以下内容:i. 紧固件的完整描述ii. 制造批次标示iii. 发货批次标示(如果与制造批次号不同)iv. 适用的紧固件标准中要求的测试项目的清单v. 测试结果与标准所要求的比照vi. 测试日期vii. 紧固件供应商(制造商和/或承销商)viii. 买方,如果测试时已经明确了买方。
f. 测试结果的保存期是多长?测试记录应该自测试之日起至少保留一年,除非标准中、制造商的质量保证手册中或者买卖双方的协议中另有要求。
g. 如何处理质量投诉,以确保真实的“根本原因”能尽快被发现?当买方对紧固件的质量提出了一个问题,采取系统化的因应方式是很重要的。
首先确定紧固件不合规是否存在,或第二步若紧固件是合规的,就是要确认客户疑虑的根本原因是什么?紧固件行业教育集团 – 紧固件标准明确地选用2007年11月1日第6页共20页建议至少执行以下步骤:i. 清晰说明问题中的紧固件,使用:1.完整的描述2.出货批号和/或制造批号ii. 确定记录中供货者的名称是正确的。
iii. 从投诉人处获得关于问题或者感觉不合格处的清晰和全面的描述。
iv. 确定这个问题零件是用在旧的使用方式或新的使用方式。
v. 确定类似的问题之前是否发生过,如果有发生,当时的结论是什么。
vi. 从买方手中获得任何书面的或者其他的文件资料。
vii. 可能的话,获取破损和/或怀疑有问题的零部件的样品,以及同一批次中未经使用的零部件样品。
viii. 可能的话,获取其配套件。
ix. 当问题的出现是由于组装失败原因时,获取失败现场的照片和/或亲自观察产品使用情形。
x. 确定问题出现时的装配因素-例如:装配规定的扭矩是多少?实际装配时的扭矩是多少?用于检测扭矩的量具是否已经经过校准?是否有一些异常点与紧固件产生干涉,例如进入配套件的前端末倒角?xi. 检阅供应链中存在的任何测试记录,确定是否有支持投诉的证据存在。
xii. 测试同一批次中未经使用的零件,确定报告的不合格项是否可以在内部或者外部实验室再次发生。
xiii. 如果记录和新的测试能够证明不合格项的存在,与买方共同商定改进措施并解决问题。
xiv. 如果记录和/或新的测试都不能证明不合格项的存在,买卖双方要评审其配套件和/或与该产品相关的装配明细,以确定在紧固件没有问题的情况下,造成使用上失败的真正根本原因。
xv. 在失败的根本原因是应用因素(配套件,装配工艺或工具等),而非紧固件供应商所能控制时,从买方获得谅解,这问题与紧固件无关,而且供应商不需实行任何改进措施。
紧固件行业教育集团 – 紧固件标准明确地选用2007年11月1日第7页共20页h. 谁应该负责去理解和明确地使用紧固件标准?i. 最终用户的职责:1. 最终用户应该负责设计界定其产品,因此产品将达到预期性能要求。