成品出货(OQC)作业流程
OQC出货检验控制程序

文件制修订记录1、总则1.1目的本公司为加强产品品质管制,确保出货品质稳定,特制定本程序。
1.2.适用范围凡本公司生产完成之后的产品,在出货前的品质管制,悉依本程序执行1.3.权责单位1.3.1品管部负责本规定制定、修改、废止之起草工作。
1.3.2总经理负责本规定制定、修改、废止之核准。
2、出货检验规定2.1.成品入库检验成品入库前,依《最终检验规定》采取逐批检验入库方,每一订单的成品可以以一批或数批的方式交验入库。
2.2.成品出货检验同一订单(生产指令单)的成品入库完成后,在出货之前,应进行成品出货检验。
检验方式如下:2.2.1由客户派员或客户指定验货机构人员对产品进行出货检验;2.2.2客户授权由本公司品管部派员作出货检验;2.2.3上述两种情况以外的产品,本公司视同(2)款的情形,由品管部派员作出货检验。
2.3.客户验货配合2.3.1业务部提前联络客户验货人员到本公司验货;2.3.2品管部协助客户做抽样及检验工作;2.3.3由客户出示检验报告,品管部存档并汇总。
2.4.合格出货客户或本公司品管部出货检验判定合格的产品,可以办理出货手续。
2.5.拒收返工2.5.1客户或品管部出货检验判定不合格(拒收)的产品,由品管部填写《不合格通知单》通知相关部门;2.5.2品管部、生产部联合制定返工的对策,其中:2.5.2.1品管部主导返工的对策和返工的作业流程;2.5.2.2生产部负责返工作业必要时,因返工时间较长,由生产部做计划调度按排2.5.3返工后,生产车间视同其他成品,依交验逐批经FQC最终检验入库。
2.5.4待整个订单批(生产指令批)返工并检验合格入库,再由客户验货人呀或品管部人员进行复检。
2.5.5品管部负追踪后续生产的预防改善对策。
2.6.特采出货2.6.1特采申请下列情形,业务部,生产部可提特采申请:2.6.1.1产品缺陷轻微,不致影响使用特性和销售;2.6.1.2出货时间紧迫;2.6.1.3其他特殊状况。
PCB成品检验OQC作业指导书

OQC作业指导书1.目的:为确保公司所有产品在出货时都能达到一定的品质标准且符合客户的要求。
2. 适用范围:公司所有的成品检验(客户提供检验标准除外)均适用之。
3. 定义:3.1 FQC:Final Quality Control(最终检验)3.2 FQA:Final Quality Assure(最终稽核)3.3 产品分级3.3.1. 产品分级(Classification)介绍:本公司按其功能可靠度(FunctionalReliability)与性能(Performances Requirement)两方面,分为如下:3.3.1.1 第一级(Class 1)Gerneral Electronic Productions:一般电子产品,此级包括:消费品,性产电脑与电脑周边产品,其主要品质要求在于电路板或其组装板是否能够发挥功能3.3.1.2 第二级(Class 2):Dedicated Service Electronics Products专用性电子产品。
此级包括:通信设备,复杂商务机器,仪器等,此级在品质上已讲究高性能及寿命长,同时希望能不间断地工作,但不是关键性的,因而某些外观缺陷是允许的。
3.4 弯曲度:四角在同一平面上,整板成圆柱形或球面弯曲的状况3.5 板翘曲:四角不在同一平面上4. 相关权责:4.1.FQC: 负责对成品进行全检,并将品质信息及时反馈给前制程及公司管理层.。
4.2.OQC: 负责对成品板进行抽检,及时反馈QC检板品质状况,并对相关品质问题跟踪处理和报告。
5.设备、工具及物料:检验台、手套、指套、刮刀、划线笔、90倍放大镜、万用表6.作业流程:无7. 检验标准(附表)8. 作业内容8.1 FQA人员将FQC置于待抽验之成品板依《产品检验与试验控制程序》对应取样,允收标准为XX公司抽样标准AQL:0.65,并依据附表<二>成品检验标准中所有检验类别及标准进行外观检验8.2 FQA人员在外观抽检过程中,如发现有不符合标准现象,则用红色三角标签标示,然后依XX公司零缺点抽样标准和检验标准(见附表)判定此批“允收”或“拒收”8.3 抽检合格后,FQA抽检人员将该批板转入合格区8.4 将检验结果记入《QA检查记录》中,其记录如下:8.4.1 日报表上须注明班别、日期;8.4.2 每批板须注明该批板生产型号(注明版本)、批量、抽检数;8.4.3 记录时,依照相应检验项目填写不良数及不良率并在判定栏中打“√”标明“拒收”或“允收”;8.4.4 如有批退板经FQC重检或重工后,转入重新检验时,FQA报表需能识别为重工板;8.4.5 对于库存品1个月以上,3个月以内由FQA做信赖度试验,合格则出货,不合格依《产品检验与试验控制程序》处理;8.4.6 对于库存品3个月以上直接退FQC返检,并做相关信赖度试验8.4.7 对库存品每周FQA按20箱抽取1箱开箱检验,判定是否可出货;8.4.8 新单、返单更改出货前依MI做全尺寸测量,具体依《产品检验与试验控制程序》。
工厂出货检验流程图及工作细则

流程责任部门工作内容
相关文件/表单商务部
商务部、仓库仓库OQC 检验员OQC 检验员
OQC 检验员仓库保安
1、商务部根据出货计划安排,在OA 上
公布具体出货明细。
2、商务制定《发货单》,并督促销售和财务审核,由仓库打印、仓管员签名确认。
仓管员确认单据明细无误后,由仓库账务员做销售出库单,将帐调出仓库,打印《销售出库单》并由仓管员和OQC 共同签名确认。
3、仓库依据发货通知单上的产品型号、规格、数量进行备货。
4、OQC 根据《发货单》,按《组件出货检查表》进行检验检查。
5、OQC 检验完毕,填写《组件出货检查表》进行检验检查。
6、OQC 检验合格,在发货单上签名(须签全名,不允许只签姓名或者一个字、或字迹潦草—详见范本一);如发现不符合项,处理流程参见《不合格品控制
程序》。
7、仓管员在得到OQC 检验员确认货物
合格之后,尽快装箱发货,不得以各种
理由推迟发货。
8、该批产品在厂门检查,保安人员须
确认《发货单》上具备可识别的OQC 人员的签名,否则不得放行出货。
《发货单》《销售出库单》《组件出货检查表》、《唛头打印规范》、《组件成品检验标准》《不合格品控制程序》、《HOLD
单》、
《重工作业程序》、《重工单》各种表单需经相关部门领导审批后方可生效。
结束
保安确认
仓库出货
仓库备货
OQC 检验
检验结果
出货通知
开始
填写检验表
订单审核。
OQC检验作业指导书

1.目的为了标准OQC 抽检作业流程,满足产品品质标准,特制定此流程.2.适用范围适用本公司XXX 周密科技生产的全部产品。
3.定义3.1OQC(Outgoing Quality Control):产品出货前的品质检验/品质稽核及管制3.2作业依据3.2.1《OQC 首件标准检验指导书》 3.2.2 《OQC 检验特别处理作业指导书》3.2.3 《OQC 检验不良停复线作业指导书》3.2.4 成品出货检验标准3.2.5 检验指导书〔SIP〕 3.2.6 研发/工程变更文件3.2.7 生产任务单 3.2.8 软件释放单3.2.9 CMF 文件 3.2.10 内部行文3.2.11 安规认证文件 3.2.12 包装BOM 与实物核对3.2.13 check list4.工作职责4.1制造中心4.1.1负责供给测试良品机器并依据批次送检2023.10.12 版第一次制订A/0编制修订履审核历批准4.1.2负责送检机器的物料标识卡及产品追踪表内容填写4.1.3负责对OQC 检验批退的不良机器安排重工并二次送检4.2工程部负责不良品分析缘由,并制定订正改善方法及预防措施4.3品质中心4.3.1对制造送检的机器进展检验〔外观、功能〕并记录报表中4.3.2负责对产品进展质量监控,对检验工程的完整性,负责报告的最终判定。
5.工作内容5.1检验抽样打算5.1.1抽样打算:公司执行国家标准GB/T2828:2023 单次正常检验抽样打算,抽样检验依据一般检验水平Ⅱ级抽样方法抽样,AQL 值取Cri=0;Maj:0.65;Min:1.5。
5.1.2抽检比例:正常抽检数量依据生产送检每个批次的10%进展检验。
5.1.3抽检规章:正常状况下,依据GB/T2828.1-2023,承受一般检验水平Ⅱ级抽取样品;非正常状况下,转换规章如下:正常-->加严:在正常检验〔10%〕状态下,假设连续5 批中有2 批被拒绝,则由正常〔10%〕转为加严检验〔15%〕。
OQC岗位职责

OQC岗位职责说明书
一、岗位流程
二、岗位职责
1、根据作业指导书、检验规范、样板进行成品及出货检验负对成品
进仓品质及出货产品品质负责.
2、负责将检验结果如实记录,并做好日、周、月报表记录。
3、产品成品进仓后,需监督仓储条件,化学反应及有效库存期限的
控制,提前做好预防工作,对库存品的品质鉴定负责。
4、有权对制程中的不良现象进行稽核,要求相关部门提出有效的纠
正预防措施。
5、对客诉品、客退品进行确认,并督促相关部门提出有效的改善对
策,并跟踪效果,直至得到客户认可。
6、监督维护OQC检验现场的6S情况。
7、承办上级领导交办的工作任务。
编制: 审核: 核准:
日期:日期:日期:。
OQC出货检验程序(含表格)

OQC出货检验程序(ISO9001-2015)1.0目的:为确保生产线所生产的成品品质符合客户品质要求,对整个出货检验过程进行有效的管理,特制定本程序.2.0范围:适用于汕头市万晖实业有限公司所有产品出货品质检验作业.3.0职责:3.1OQC:出货品质检验、品质判定、状态标识、异常反馈与跟踪、检验结果记录。
3.2QE:制定或修订出货品质检验标准、异常原因分析、异常跟踪及作业指导。
3.3生产部:出货待检通知、不合格批的重工作业、不合格品处理.3.4仓库:成品入库管理、库存超保质期成品再检通知。
3.5业务部:成品特采申请、重工作业安排.4.0定义无5.0作业内容5.1入库成品待检通知生产部入库待检的成品必须是经FQC全检并判定合格(需贴合格标识)的产品,入库前需核对入库数量与检验数量是否相符,最后将待检之成品移入成品仓库指定的出货待检区域。
然后开立《出货待检通知单》通知OQC进行出货检验。
5.3出货品质检验作业5.3.1检验依据OQC检验时依据《成品检验规范》、《产品检验标准书》、工程样办等对产品进行品质检验和判定,抽样作业时按照MIL-STD-105E普通Ⅱ级抽样,合格质量允收水准(AQL):致命缺陷(CRI):0、主要缺陷(MAJ):0.65、次要缺陷(MIN):1.5,若客户有特别要求按照客户要求的允收水准进行抽样作业,具体参照《抽样检验计划》执行.5.3.2检验项目检验项目包括:外观/尺寸/结构/特性/包装/标识等项目,具体检验项目参照《成品检验规范》中规定检验项目进行检验.5.3.3OQC出货检验作业时应按照抽样计划规定的抽检数量从待检批中的不同部位、不同箱号的箱子中抽取指定数量进行检验,尽量减少不量流入客户端.检验完成后需在《出货待检通知单》上进行品质判定,然后将《出货待检通知单》归还生产部.5.3.4正常情况出货检验需在6个工作小时内完成,急出货情形需在2个工作小时内完成检验.检验结果是否合格都需真实且详细的记录于《OQC成品检查报告》上,以便追溯和统计分析.5.3.5经OQC检验合格批次,由生产部门填写《成品入仓单》办理入库.5.4检验状态标识检验合格在标签上盖PASS印章,不合格贴红色REJECT标签,特采使用贴黄色特采使用标签.挑选或加工使用则贴挑选/加工使用标签.具体参考《产品标识与追溯性控制程序》.5.5品质异常反馈及处理经抽检判不合格批次,需在产品外箱上贴上红色的不合格(REJECT)标签,并将判定结果记录于《成品待检通知单》上并归还仓库,同时OQC开立《出货检验异常报告》给OQC组长确认/主管审核/经理核准,然后由业务/PMC/生产/品质/工程等相关单位会签评审.最终由(副)总经理批准,不合格批的处理方式按(副)总经理批准意见执行,会签完后将此单给责任单位进行原因分析和制定改善对策,至于检验发现之不合格品的处理方式参照《不合格品的控制程序》执行.5.6特采放行作业5.6.1经OQC检验不合格批产品,经公司(副)总经理批准决定特采使用的,由业务开立《特采申请单》并附上《出货检验异常报告》给品质部/工程部/生产部/PMC等相关单位会签评审,由公司(副)总经理批准执行,最后由OQC将不合格标签撕下,在标签上盖PASS印章,若是经客户同意特采使用需在外箱贴特采使用标识.5.7不合格批重工再检判重工的不合格批,OQC需对重工过程进行跟踪(包括重工项目是否与反馈之项目相符,重工之数量是否与判退的数量相符等内容),重工后生产部必须重新报验此批,并在《出货待检通知单》上注明”已重工”字样.重工再检OQC必须再次填写《OQC成品检查报告》,报告上需详细注明为”重工再检”字样,并详细记录《出货检验异常报告》编号和其他相关信息,以便于追溯.5.8库存成品再检所有库存成品超过保存期限,仓库必须重新提报给OQC重检和判定.重检后原标识需更换,若重检判不合格,需开立《出货检验异常报告》给相关单位会签评审,不合格批的处理参照5.5/5.6/5.7执行,不合格品参照《不合格品控制程序》执行.5.9控制计划的传递和执行5.9.1在新产品投产之前,由品质经理针对此项产品的特殊特性内容,对检查员进行培训,要求品管员严格按特殊特性的内容执行检查。
OQC检验流程

OQC检验流程1 产品:入库成品。
2 送检:一般情况OQC按“成品入库单”顺序抽检,特殊情况需要时(如急需出货等),由PMC部另行通知检验。
3 检验:OQC收到《成品入库单》,首先核对制单、机型、数量、商标等内容须与《业务/生产指示单》相符。
测试及试验方法按《QA作业指导书》进行;检验依据《抽样检验规定》和《***检验标准》进行抽样、检验和判定。
4 处理:经OQC检验合格的成品机,按《仓库管理规定》存放、标识。
入库品经OQC检验不合格时,OQC填写《OQC检验报告》,连同不良品一起交PE分析处理,分析原因由PE填写在《OQC检验报告》的“原因分析”栏上。
不合格批的《OQC检验报告》,PE在《OQC检验报告》的“备注”栏上填写返工内容、交质控部长批准、送总办批示。
返工按《返工管理办法》运行。
5 说明:在保证质量的前提下,为了仓库现场的规范管理,作业时间的统一性,绩效考核的有效性,OQC的行政方面属PMC部管理;技术方面属质控部管理。
1) OQC人员(包括OQC管理员)的招聘,由PMC部申请,经质控部技能方面的考核合格后方可上岗;2) OQC人员(包括OQC管理员)的解雇或辞职,由PMC部管理;3) OQC人员(包括OQC管理员)绩效考核以及纪律,由PMC部管理;4) OQC人员(包括OQC管理员)的技能培训由OQC拉长申请,质控部负责培训或通知有关培训;5) OQC的所有质量记录,归档质控部;6) OQC拉长每天要到质控部看传阅文件,了解有关信息;7) OQC的《作业指导书》和“检验标准”同QA。
6记录:每单产品的质量状况由OQC记录在《OQC检验报告》上,不合格项由PE填写分析原因,审核后交质控部部长批准,由质控部文员发放、归档质控部。
7统计:每周的检验记录统计在《OQC周质量统计报表》上,每月的检验记录统计在《OQC月份质量统计报表》上。
报表统计由OQC拉长负责,送质控部文员编制,由PE分析、审核后交部长批准。
成品出货检验流程
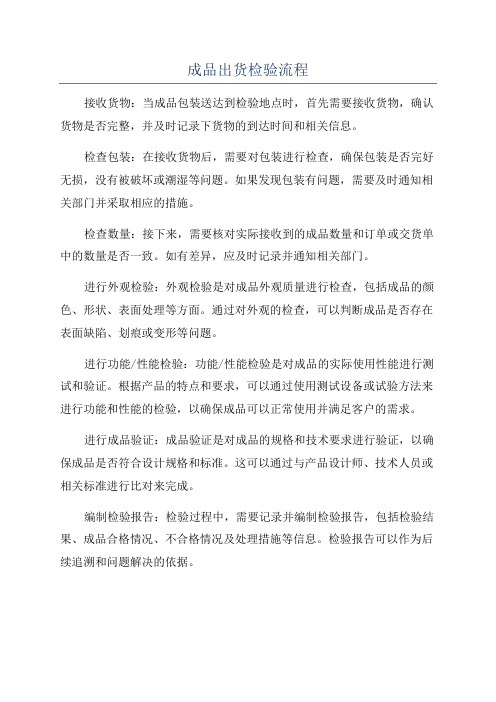
成品出货检验流程
接收货物:当成品包装送达到检验地点时,首先需要接收货物,确认货物是否完整,并及时记录下货物的到达时间和相关信息。
检查包装:在接收货物后,需要对包装进行检查,确保包装是否完好无损,没有被破坏或潮湿等问题。
如果发现包装有问题,需要及时通知相关部门并采取相应的措施。
检查数量:接下来,需要核对实际接收到的成品数量和订单或交货单中的数量是否一致。
如有差异,应及时记录并通知相关部门。
进行外观检验:外观检验是对成品外观质量进行检查,包括成品的颜色、形状、表面处理等方面。
通过对外观的检查,可以判断成品是否存在表面缺陷、划痕或变形等问题。
进行功能/性能检验:功能/性能检验是对成品的实际使用性能进行测试和验证。
根据产品的特点和要求,可以通过使用测试设备或试验方法来进行功能和性能的检验,以确保成品可以正常使用并满足客户的需求。
进行成品验证:成品验证是对成品的规格和技术要求进行验证,以确保成品是否符合设计规格和标准。
这可以通过与产品设计师、技术人员或相关标准进行比对来完成。
编制检验报告:检验过程中,需要记录并编制检验报告,包括检验结果、成品合格情况、不合格情况及处理措施等信息。
检验报告可以作为后续追溯和问题解决的依据。
装运包装:在检验合格后,可以将成品进行装运包装,包括重新包装、封箱、标记等工作。
确保成品在运输过程中不受损坏,并能够正常到达目
的地。
以上是成品出货检验流程的一般步骤,不同行业和企业可能会有所差异。
对于特殊行业和高风险产品,可能需要进行更加详细和专业的检验流程。
- 1、下载文档前请自行甄别文档内容的完整性,平台不提供额外的编辑、内容补充、找答案等附加服务。
- 2、"仅部分预览"的文档,不可在线预览部分如存在完整性等问题,可反馈申请退款(可完整预览的文档不适用该条件!)。
- 3、如文档侵犯您的权益,请联系客服反馈,我们会尽快为您处理(人工客服工作时间:9:00-18:30)。
权责参考文件作业依据其它
《生产管理控制程序
《生产计划》
《产品检验控制程序
》《送检单》
《产品检验控制程序
》《客户合同、订单》
NG
品质
业务生产《OQC成品检验报告
研发
《产品检验控制程序》
生产《不合格品管理程序》《OQC成品检验报告
品质
NG
《OQC成品检验报告
《送检单》
计划《出货计划》
仓库《出库单》
仓库核对入库数量符合订单数量业务部安排出货
成品送检单送检
OQC核对成品送检单OQC抽检检验
OQC填写成品异常单
OQC在送检单上签字承认合格或让步放行仓库根据OQC合格或让步放行签名安排入库
《物控计划控制程序
》《OQC成品检验报告
》
《OQC成品检验报告
》
《送检单》
一,
OQC接到客户订单后,根据合同、
订单,先了解什么客户、具体有什么品质要求。
生产时到车间跟
踪订单完成情况及品质状况。
二, OQC等产品送检后进行抽检。
抽检时注意拍好照片和留样,以便日后追溯。
拍照内容从外包装到内产品细节。
包括封箱方式、外箱正
侧唛、内盒正侧
唛、包装方式、
印字、附件等内容。
三,
出货产品留样1PCS,性能测试报告保存完好,以便日后追溯(根据公司实际情况再定)。
四,
出货时发货部门重点注意和收货单位或者托运人在出库单上签字,做好数量、件数的书面交接工作。
OQC
OQC
仓库
《产品检验控制程序》《MRB异常处理控制程序》
《产品检验控制程序
》
《产品检验控制程序》《产品检验控制程序》《品质管理制度》
《产品检验控制程序》《物料管理控制程序》
生产OQC
OQC
OQC OQC xxxxxxxx成品和出货流程图
让步放行贴让步放行标签
生产返
工QQC复检
OK
贴合格标签
OK 返 工品质返
工贴合格标签
OK
合 格
贴合格标签
MRB评审。