脱模力计算
强制脱模的计算方法

域——顶杆端面。另外,使用推板结构(图 8),可使顶出面积增大,塑件可以安全地脱出,
这也是笔者力荐的首选结构。
中心顶杆
图 6 障碍内侧的单个中心顶杆——塑件的高度最大变形在脱出障碍时产生
6
顶
顶
杆
杆
图 7 障碍内侧的多顶杆脱模——顶杆作用端面为应力最高区域
推板
图 8 推板顶出 (2)二次顶出 在强脱过程中,有一点是非常重要的,那就是带有障碍的弹臂,内则的障碍与外侧是要 顺序脱出才可完整而不被拉坏。一般情况下,是首先脱开障碍外则,让内侧的障碍得到足够 的弹出空间,如图 2。一般的障碍外侧弹出空间 g 的取值可按下式:
第10讲 脱模机构设计
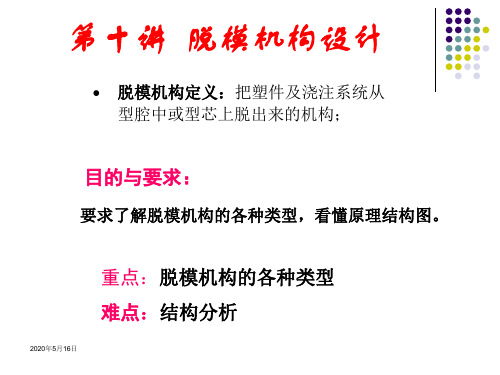
二级推出机构产生的原因
由于特殊形状或自动化生产的需要, 在一次脱模动作完成后,仍难于从 型腔中取出或不能自动脱落。
有时为避免一次脱模塑件受力过大,也采用二次脱模推出, 以保证塑件质量。
2013年7月14日
1.弹簧式二级推出机构
这种方法结构简单,装 配后所占面积小,缺点 是动作不可靠,弹簧容 易失效,需要及时更换。
2013年7月14日
2.斜楔滑块式二次推出机构
8-14斜楔滑块式二次推出机构 1- 动模座板 2-推板 3-弹簧 4-滑块 5-销钉 6-斜楔; 7-推件板 8-推杆 9-型芯 10-中心推杆 11-复位杆
2013年7月14日
3.三角滑块式二级推出机构
图8-15 三角滑块式二次推出机构 1- 一次推板 2- 三角滑块 3- 二次推板 4-推杆固定板 5-斜楔杆 6-推杆 7-动模型腔板 8-型芯 9-推杆
2013年7月14日
1.推杆推出机构
(1)推出机构组成: 推杆、拉料杆、复位杆、推杆固定板、推杆垫板、
推杆导柱、推杆导套、限位钉。
2013年7月14日
(2)推杆的设计
• • 适用范围:脱模阻力小的简单塑件 特点:简单、灵活,但与塑件接触面积小,易将 塑件顶变形或损坏。
推杆的形状及尺寸 推杆的固定及装配 推杆推出位置的选择
(四)螺纹塑件推出机构
手动脱螺纹机构
模内手动脱螺纹机构 齿轮齿条脱螺纹机构 直角式注射机脱螺纹机构 推杆轴承旋转式脱出机构
2013年7月14日
1.手动脱螺纹机构
2013年7月14日
手动脱螺纹机构
2013年7月14日
手动脱螺ቤተ መጻሕፍቲ ባይዱ机构
2013年7月14日
2.模内手动脱螺纹机构
第四章 推出机构的设计6

•
压缩空气配合推板脱模
• 设置引气装置以后:
4. 推块推出机构 平板状带凸缘的塑件,如 用推板件推出会黏附模具 时,则应使用推块推出机 构推出,如图所示。推块 是型腔的组成部分,因此 应有较高的硬度和较低的 表面粗糙度值,推块与型 腔及型芯应有良好的间隙 配合,既要求滑动灵活, 又不允许溢料。推块所使 用的推杆与模板不必要求 精度很高的配合。
难,同时因增加推件板而使模具质量增加。12
为减少脱模过程中推件板与 型芯之间的摩擦,两者之间 留有0.2~ 0.25mm的间隙, 并采用锥面配合,以防止推 件板 偏斜溢料,锥面的斜 度约取3~5˚左右,
4
推件板推出机构形式-4zzzzz 对于大型深腔的容器,尤其是采用软质塑料时, 如果用推件板脱模,应考虑附设引气装置,以防止在 脱模过程中内腔形成真空,造成脱模困难,甚至使塑 件变形损坏(见下图)。
(4)推管外径应比塑件外壁尺寸小0.5mm左右;推管内 径比塑件内径每边大0.2 ~0.5mm。 (5)推管与型芯的配合长度比推出行程S长3~5 mm,推 管与模板的配合长度一般为(1.5~2)D;其余部分扩 孔,推管扩孔d+l,模板扩孔D十1。推管的厚度一般取 1.5 ~5mm,以保证刚性。
• 3. 推件板推出机 构 • 深腔薄壁的容器、 壳体形塑件以及 不允许有推杆痕 迹的塑件都可采 用推件板推出机 构。推件板推出 机构的结构形式 与原理如图所示。
2、影响塑件脱模力的因素: 1) 脱模力的大小主要与塑件包络型芯侧面积的大小有关 2)脱模力大小与型芯的脱模斜度有关 脱模斜度越大,脱模力越小。 3) 脱模力的大小与型芯的表面粗糙度有关 表面粗糙度值越低,型芯表面越光洁,所需的脱 模力 就越小。 4) 脱模力的大小与塑件的结构有关 塑件厚度越大、形状越复杂,冷却凝固时所引起的包 紧力和收缩应力越大,则所需的脱模力越大。 5)脱模力的大小还与塑件底部是否有孔有关。
粉末冶金原理及模具计算要求
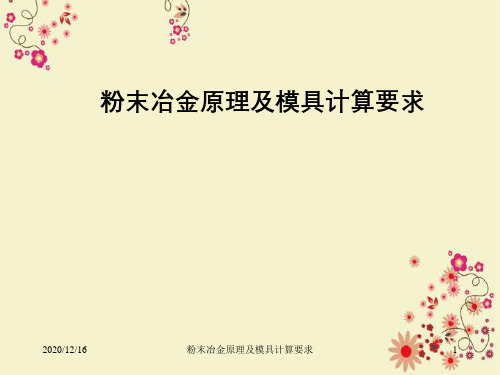
3.4 组合模具的设计原理
形状完整,具有一定强度
3.5 压制过程的图示
2020/12/16
粉末冶金原理及模具计算要求
2
•压制压力的计算
模压过程的总压制力等于净压力与外摩擦力 之和
单位压制压力与压坯密度定量关系的研究, 是近60年来粉末成形理论研究的主要内容
•脱模力的计算
压制压力去掉后,侧压力因为高度方向的弹 性后效,侧压力会下降35~77%
单向压制
S侧max/S=[1-(ρ下/ρ上)m]/μξ=K
当柱状压坯S侧/S<K或者圆柱体压坯高径比
H/D<K/4时,采用单向压制可以满足压坯密度
分布均匀性的要求
2020/12/16
粉末冶金原理及模
粉末冶金原理及模具计算要求
17
双向压制
S侧max/S=[1-(ρ中/ρ上)m]/μξ=2K
压力相等时双向压制与非同时双向压制的效 果相同
非同时双向压制中第二次压制的模冲移动距 离:
x=(d2-d1)h/d1
或者 y=x/l=100(d2-d1)/d1(k-1)
其中:d2为要求的压坯平均密度;d1为单向压 制的平均密度;h为压坯高度;k为压缩比;l 为装粉高度与压坯高度之差。
2020/12/16
•压制时粉体产生柱式流动,几乎不产生明显
的横向流动 2020/12/16
粉末冶金原理及模具计算要求
8
压坯中中立层的位置可以表示压坯密度分布
的均匀程度。通过压制方式和压模结构合理
选择使中立层2边受相同压缩,提高密度分布
均匀性 2020/12/16
粉末冶金原理及模具计算要求
9
2020/12/16
d粉—粉末松装密度; d1—第一次压制后压坯平均密度; 第一次压制后:d粉H粉=d1h1 x=h1-h d粉H粉=d1(h+x) ∴x=(d粉H粉-d1h)/d1 第二次压制后:d粉H粉=dh d粉=d ·h/H粉 x=(d-d1)h/d1; k=H粉/h=(l+h)/h 粉末冶金原理及∴模x具=计(算d要-d求1)l/d1(k-1); y=x/l ·11000%
塑料模具设计第七周 第一讲(第四章)
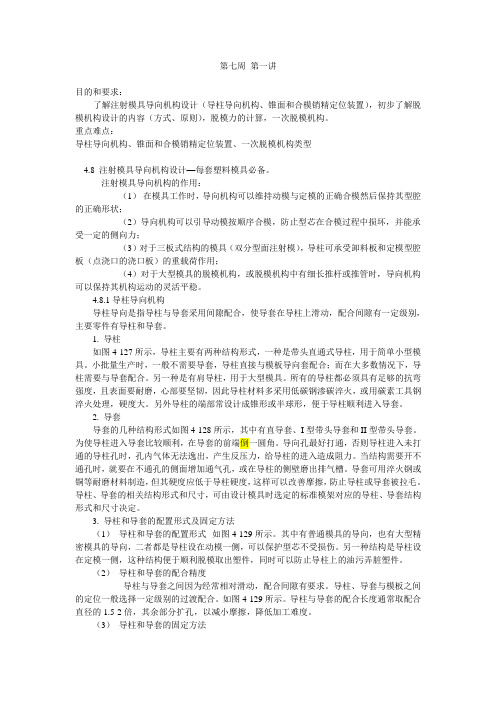
第七周第一讲目的和要求:了解注射模具导向机构设计(导柱导向机构、锥面和合模销精定位装置),初步了解脱模机构设计的内容(方式、原则),脱模力的计算,一次脱模机构。
重点难点:导柱导向机构、锥面和合模销精定位装置、一次脱模机构类型4.8 注射模具导向机构设计—每套塑料模具必备。
注射模具导向机构的作用:(1)在模具工作时,导向机构可以维持动模与定模的正确合模然后保持其型腔的正确形状;(2)导向机构可以引导动模按顺序合模,防止型芯在合模过程中损坏,并能承受一定的侧向力;(3)对于三板式结构的模具(双分型面注射模),导柱可承受卸料板和定模型腔板(点浇口的浇口板)的重载荷作用;(4)对于大型模具的脱模机构,或脱模机构中有细长推杆或推管时,导向机构可以保持其机构运动的灵活平稳。
4.8.1导柱导向机构导柱导向是指导柱与导套采用间隙配合,使导套在导柱上滑动,配合间隙有一定级别,主要零件有导柱和导套。
1. 导柱如图4-127所示,导柱主要有两种结构形式,一种是带头直通式导柱,用于简单小型模具。
小批量生产时,一般不需要导套,导柱直接与模板导向套配合;而在大多数情况下,导柱需要与导套配合。
另一种是有肩导柱,用于大型模具。
所有的导柱都必须具有足够的抗弯强度,且表面要耐磨,心部要坚韧,因此导柱材料多采用低碳钢渗碳淬火,或用碳素工具钢淬火处理,硬度大。
另外导柱的端部常设计成锥形或半球形,便于导柱顺利进入导套。
2. 导套导套的几种结构形式如图4-128所示,其中有直导套、I型带头导套和II型带头导套。
为使导柱进入导套比较顺利,在导套的前端倒一圆角。
导向孔最好打通,否则导柱进入未打通的导柱孔时,孔内气体无法逸出,产生反压力,给导柱的进入造成阻力。
当结构需要开不通孔时,就要在不通孔的侧面增加通气孔,或在导柱的侧壁磨出排气槽。
导套可用淬火钢或铜等耐磨材料制造,但其硬度应低于导柱硬度,这样可以改善摩擦,防止导柱或导套被拉毛。
导柱、导套的相关结构形式和尺寸,可由设计模具时选定的标准模架对应的导柱、导套结构形式和尺寸决定。
注塑模具设计说明书

数码相机盖模具设计说明书班级:10材料专业:材料成型及控制工程姓名:刘树飞学号:100118019指导老师:引言 (2)一.产品工艺性分析 (3)1.1设计产品概述 (3)1.2产品工艺性分析 (3)二、注塑机的选择 (3)1、塑件的质量、体积计算 (4)2、浇注系统凝料体积的初步估算 (4)3、注射容量与锁模力校核 (4)(1)注射容量校核 (4)(2)锁模力的校核 (4)4.利用UG软件,设置工件尺寸。
(4)三、分型设计 (5)四、标准模架的选用 (6)(1)先定系列。
(6)(2)看型芯固定方式是否需要加支撑板。
(6)(3)确定模板尺寸。
(6)(4)模架厚度 (6)五、模具滑块设计 (6)(1)抽芯距离和抽芯力的计算 (6)(2)斜导柱设计 (7)①斜导柱倾斜角的确定 (7)②斜导柱的直径计算 (7)③斜导柱长度的计算 (7)④滑块其他零部件设计 (7)六、导向与顶出机构设计 (8)(1)顶出机构设计 (8)①脱模力计算 (8)②推出零件尺寸计算 (8)③创建顶管 (8)④创建拉料杆 (8)(2)导向机构的设计 (8)①导柱的选取 (8)②复位杆的选取 (9)七、浇注系统设计 (9)1.浇注系统整体方案确定 (9)2.主流道设计 (9)3、分流道、浇口和冷料穴设计 (9)八、冷却系统设计 (10)1、冷却水道的尺寸计算 (11)(1)计算单位重量的塑料熔体在凝固时所放出的热量Q1(kJ/kg) (11)(2)求冷却水的体积流量qv(m³/min) (11)(3)查表使冷却水处于紊流状态,取d (11)九、画模具装配图 (12)引言虽然受到全球金融危机影响,但是我国模具整体实力还是得到进一步加强。
近两年来中国的模具制造技术水平又有了新的提高。
从模具产品进出口的地域来看,华东地区的江苏、浙江、上海、山东均位列中国进口和出口模具的十大省市之中。
长江三角地区在模具制造整体水平的数量和质量上均已在国内处于行业重要位置。
脱模力计算

Thank You~ Thank You~
頂出力(脫模力)說明
(一)定義
在注射動作結束後,塑件在模內冷卻定型,由於體積收縮,對公模型腔產生包 緊力,當其從模具中推出時,就必須克服因包緊力而產生的摩擦力,對於底部 無孔的筒、殼類塑料製件,脫模推出時還要克服大氣壓力。 開始脫模時所需的脫模力最大,其後推出力的作用僅僅是為了克服推出機構移 動的摩擦力,所以計算脫模力的時候,總是計算剛開始脫模時的初始脫模力。 將塑件從型腔上頂出時所需克服的阻力,包括: 成形收縮的包緊力; 不帶通孔的殼體類塑件的大氣壓力; 機構運動的摩擦力; 塑件對模具的黏附力;
(二)影響脫模力的因素
公模型腔成形部份的表面積及其形狀; 收縮率及摩擦係數; 脫模斜度; 塑件壁厚和包緊公模型腔的數量; 公模型腔表面粗糙度; 成形條件(工藝):如成形壓力、冷卻時間
塑件脫模力的分析
力力)的大小隨著塑件包覆型腔的面積增加而增大, 隨著脫模斜度增大而減小,大氣壓力及推出機構本身在推出運動時的摩擦阻力之間的 摩擦係數有關,事實上,影響脫模力的因素很多,因此在計算公式中不可能一一反映, 所以只能做大概的分析和估算。 其影響脫模力因素整理如下: 主要與塑件包覆型腔側面積的大小有關。脫模斜度越大,所需的脫模力越小。 與型腔的脫模斜度有關。脫模斜度越大,所需的脫模力越小。 與型腔的表面粗糙度有關。表面粗糙度值越低,型腔表面越光潔,所需的脫模力越 小。 與塑件的結構有關。塑件厚度越大,形狀越複雜,冷卻凝固時所引起的包緊力和收 縮應力越大,則所需的脫模力越大。 與射出成形條件有關。 成形壓力越大,則包緊型腔的力越大,所需脫模力越大; 脫模時模具溫度越高,所需的脫模力越小; 塑件在模內停留時間越長,所需的脫模力越大。 與成形塑件的塑料種類有關。 不同的塑料種類,由於分子結構不一樣,因而它們的脫模力也不一樣。
衬套注塑模具设计说明书

南京农业大学工学院课程设计课题名称:塑料模塑成型技术题目名称:衬套注塑模具设计专业班级:材料成型及控制工程04班学号:学生姓名:指导教师:聂信天夏荣霞史立新徐秀英2013年10 月28 日目录一.塑件成型工艺性分析 (3)1.1 塑件的分析 (3)1.2 PP的性能分析 (3)1 .3 PP的注射成型过程及工艺参数 (3)二.拟定模具的结构形式 (4)2.1 分型面位置的确定 42.2 确定型腔数量和排列方式 42.3 注塑机型号的确定4三.浇注系统的确定 63.1 主流道设计 63.2 浇口的设计7 四.成型零件的结构设计和计算94.1 成型零件的机构设计94.2 成型零件的钢材选用94.3 成型零件工作尺寸的计算94.4 模架的确定和标准件的选用11五.脱模推出机构设计11六.模架的确定13 七.排气槽的设计14 八.冷却系统的设计 (14)九.导向和定位结构的设计.........................................................错误!未定义书签。
十.总装图错误!未定义书签。
总结 (18)参考文献 (18)一.塑件成型工艺性分析1.1.塑件的分析(1)外形尺寸:壁厚6mm,结构对称,适合注射成型。
(2)精度等级:MT5,查表确定每个尺寸的公差。
(3)脱模斜度:PP 为无定型塑料,流动性好,选择该塑件上型芯和凹模的统一脱模斜度为45分。
(4)圆角过渡:半径1.5mm.1.2.PP 的性能分析(1)使用性能:密度小,强度高耐热性均优于聚乙烯,可在100°C 左右使用,具有优良的耐腐蚀性高频绝缘性,不受湿度影响,(2)但低温时变脆,不耐磨,易老化。
(3)成型性能:1.结晶料,吸湿性小,易发生熔体破裂,长期与热金属接触易分解。
2.流动性好,但收缩范围和收缩大,易发生缩孔,凹痕,变形。
3.冷却速度快,浇注系统和冷却系统应缓慢散热。
4.塑料壁厚需均匀,避免缺口,尖角。
- 1、下载文档前请自行甄别文档内容的完整性,平台不提供额外的编辑、内容补充、找答案等附加服务。
- 2、"仅部分预览"的文档,不可在线预览部分如存在完整性等问题,可反馈申请退款(可完整预览的文档不适用该条件!)。
- 3、如文档侵犯您的权益,请联系客服反馈,我们会尽快为您处理(人工客服工作时间:9:00-18:30)。
带斜销抽芯机构的压铸模是一种常见的压铸成型模具,该类模具利用开闭模动力抽芯复位,结构简单。
但其结构参数的设计对模具的工作状况和工作质量影响很大,如何在对该类模具进行可靠力学分析的基础
上,优化其结构参数的设计,具有十分重要的应用价值。
1 带斜销抽芯机构压铸模工作原理
图一为带斜销抽芯机构压铸模结构简图。
合模状态时斜销2与分型面成一定角度固定在定模座板
3内并穿过定模套板4进入滑块6,滑块由楔紧块5锁紧。
开模时滑块由斜销带动在导滑槽内运动,抽出型芯。
抽芯结束后
滑块由限位块7挡住,不离开导滑槽。
闭模后斜销滑块复位。
图一带斜销抽芯机构压铸模结构简图
1-定模镶块2-斜销3-定模座板4-定模套板5-楔紧块
6-滑块7-限位块8-动模套板9-动模座板
2 带斜销抽芯机构压铸模力学分析
2.1 滑块力学分析
模具中斜销抽芯机构滑块能否正常工作与其受力情况有关,而滑块受力情况与其设计参数直接关联,所以分析滑块
受力情况和自锁条件是合理设计斜销抽芯机构的基础。
图二为滑块受力情况。
a、b、c、h、s为滑块结构尺寸,F为抽芯力,N1为斜销对滑块的正压力,f1为斜销对滑块的
摩擦力,N2、N3、N4分别指楔紧块、定模套板、动模套板对滑块的正压力,f2、f3、f4分别表示N2、N3、N4所对应
的摩擦力。
图二滑块受力分析
考虑到滑块不受弯矩作用,则开模瞬间滑块的静力平衡方程表示为:
F f3 f4 f2·sinβ f1·sinα=N1·cosα N2·cosβ (1)
N3 N1·sinα f1·cosα=N2·sinβ N4 (2)
(N1·cosα-f1·sinα)b (N1·sinα f1·cosα)·(s btgα) f2(S-h)·sinβ N4(a/2-s)=Fc f3·
b N2sinβ(s-h/2) N2cosβ(b-sinβh/2) N3(a/2-s) (3)
因此,开模时滑块的受力情况既与抽芯力有关,同时与滑块及斜销的结构尺寸相关。
考虑到楔紧块
和定模套板只在合模状态及开模瞬间起作用。
同时f1=μN1,f2=μN2,f3=μN3,f4=μN4,则抽芯
过程中滑块静力平衡方程简化为:
N1·cosα=F f3=F μN3 (4)
N1·sinα=N3 (5)
联立(4)、(5)式解得
N1=F/(cosα-μsinα)
若cosα-μsinα为零,则N1为无穷大,此时滑块自锁,即滑块自锁条件为μ=tanα。
为可靠保证滑块工作时不自锁,α取值不宜过大,但α值减少时将导致滑块和斜销度必须相应增加才能
保证抽芯距,所以α取值一般以15°"25°为宜。
2.2 斜销力学分析
从滑块受力分析,斜销受力情况如图三所示。
图三斜销受力分析
把斜销看成支点为A的悬壁梁,设斜销固定伸出端点,B为抽芯力作用点,则弯矩为:
M=N1·h1
=[F/(cosα-μsinα)]·h/cosα
=Fh/[cosα(cosα-μsinα)]
而抽芯力的计算由图四可知:
图四抽芯力计算参考
F=F阻·cosθ-F包·sinθ
F=clp(μcosθ-sinθ)
式中c表示型芯断面周长,l表示被铸件包紧的型芯长度,p表示单位包紧力,θ表示型芯脱模斜度,μ摩擦系数。
2.3 锁模力计算
锁模力必须大于胀型力在合模方向上的合力。
由图五知,胀型力在合模方向上的合力包括铸件熔融合金冲满型腔后对动、定模产生的沿锁模方向的压力
F1、型芯成型部分沿抽芯方向垂直方向压力作用在楔紧块上的分力F2之和。
图五锁模力计算
F1=PA
F2=F法=F反·tanβ=PA 1·tanβ
即:F锁≥K(PA PA1·tanβ)
式中K表示安全系数,P表示压射比压、A表示铸件在合模方向垂直面上的投影面积,A1表示型芯在抽芯方
向垂直方向投影面积、β表示楔紧块斜面与合模方向的夹角。
3 模具参数设计
3.1 斜销长度计算
如图六知,斜销总度既与模具结构有关,也同抽芯距有关,即:
L=L1 L2 L3 L4 L5
L=D/2·tanα H/cosα d/2·tanα s/sinα
式中s表示抽芯距,H表示斜销固定部分套板厚度,d表示斜销直径,D表示斜销固定台阶直径。
考虑抽芯可靠,实际斜
销长度比计算值大5~10mm。
图六斜销长度计算图
3.2 斜销直径设计
由斜销受力分析知其所受弯矩为Fh/[cosα(cosα-μsin
α)],若材料许用抗弯强度为[σ]ω,则Fh/[cosα(cosα-μsin α)0.1d3]≤[σ]ω,由此可得:。