第三章磨损及磨损理论
机械设备修理工艺——失效理论概述

20 11:17:54
第三章 失效理论概述
§3.6 老化
老化:机械设备和零部件制造后,在长 期的使用或保管、闲置过程出现精度下降、 性能变坏、价值贬低的现象。 一、老化的分类
1、有形老化:因摩擦磨损、变形、断裂、 腐蚀等作用产生的实物形态变化。
2、无形老化:因技术进步产生的使用价值 降低的现象。
术依据、提供改进措施等。 二、失效分析的基本内容
1、调查检测 2、分析诊断 3、处置与预测
27 11:17:54
第三章 失效理论概述
§3.8 失效分析技术简介
三、失效形式的特征及其判断(表3-3) 弹性变形失效、屈服失效、疲劳断裂失
效、腐蚀失效、磨损失效、蠕变失效等。
28 11:17:54
第三章 失效理论概述
30 11:17:54
31 11:17:54
第三章 失效理论概述
§3.8 失效分析技术简介
五、失效分析举例 1、带式运输机的托辊轴承; 2、柴油机缸套外圆受到气蚀破坏; 3、转子液压泵的转子与轴套咬死; 4、挖掘机斗齿的磨损失效分析。
32 11:17:54
简答题及参考答案
1、故障和失效有何不同? 答:机器失去正常工作能力称故障。机器零件失去正常工
主要原因:应力超过材料的屈服强度。 1、外载荷——永久变形; 2、温度——屈服强度下降、蠕变(缓慢塑性变 形)、内应力和热应力; 3、内应力——弹性变形,对策:时效处理; 4、结晶缺陷(位错,空位)——金属滑移变形。
8 11:17:54
第三章 失效理论概述
§3.2 变形 四、减少变形的措施
1、设计:重视强度、刚度、制造、装配、 使用、拆卸、修理等问题,正确选材。
第三章磨损及磨损理论ppt课件
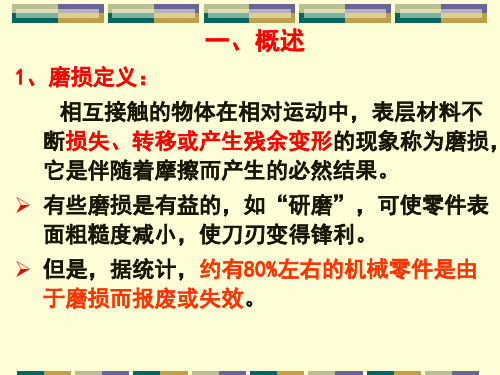
➢ 剪切破坏发生在离粘着结合面不远的较软金属浅层内, 软金属涂抹(粘附)在硬金属表面上;
➢ 摩擦系数与轻微磨损差不多,但磨损程度加剧。
c.擦伤
➢ 粘着强度比摩擦副的两基体金属的剪切强度都高; ➢ 剪切主要发生在软金属的亚表层内,有时也发生在硬
“雪亮工程"是以区(县)、乡(镇) 、村( 社区) 三级综 治中心 为指挥 平台、 以综治 信息化 为支撑 、以网 格化管 理为基 础、以 公共安 全视频 监控联 网应用 为重点 的“群 众性治 安防控 工程” 。
Ⅲ 剧烈磨损阶段:当材料磨损量达到一定数值时, 摩擦条件发生较大的变化,磨损速度急剧增加。 这时机械效率下降,精度降低,出现异常的噪音 及振动,最后导致零件完全失效。 ** 从磨损过程的变化来看,为了提高机器零件的 使用寿命,应尽量延长“稳定磨损阶段”。
单位滑动距离的磨损量,横坐标 代表平均接触压力。
压力值小于H/3(σs ),磨损率小而且保持不变(即K保
持常数-磨损量与压力成正比);
压力值为H/3,各个微凸体上的塑性变形区开始发生相
互影响;
压力值超过H/3,磨损量急剧增大(K值急剧增大),高
的载荷作用下,整个表面变成塑性流动区,发生大面 积的粘着焊连,出现剧烈的粘着磨损。
a.轻微磨损
➢ 粘着强度比摩擦副两金属基体剪切强度低; ➢ 剪切发生在粘着结合面上,表面转移的材料较轻
微;
➢ 摩擦系数增大,但磨损量很小; ➢ 金属表面具有氧化膜、硫化膜或其他涂层时发生
轻微粘着摩损。
b.涂抹 “雪亮工程"是以区(县)、乡(镇)、村(社区)三级综治中心为指挥平台、以综治信息化为支撑、以网格化管理为基础、以公共安全视频监控联网应用为重点的“群众性治安防控工程”。
摩擦与磨损

表面摩擦与磨损一、摩擦与磨损的定义摩擦的定义是:两个相互接触的物体在外力的作用下发生相对运动或者相对运动趋势时,在切相面见间产生切向的运动阻力,这一阻力又称为摩擦力。
磨损的定义是:任一工作表面的物质,由于表面相对运动而不断损失的现象。
据估计消耗在摩擦过程中的能量约占世界工业能耗的30%。
在机器工作过程中,磨损会造成零件的表面形状和尺寸缓慢而连续损坏,使得机器的工作性能与可靠性逐渐降低,甚至可能导致零件的突然破坏。
人类很早就开始对摩擦现象进行研究,取得了大量的成果,特别是近几十年来已在一些机器或零件的设计中考虑了磨损寿命问题。
在零件的结构设计、材料选用、加工制造、表面强化处理、润滑剂的选用、操作与维修等方面采取措施,可以有效地解决零件的摩擦磨损问题,提高机器的工作效率,减少能量损失,降低材料消耗,保证机器工作的可靠性。
二、摩擦的分类及评价方法在机器工作时,零件之间不但相互接触,而且接触的表面之间还存在着相对运动。
从摩擦学的角度看,这种存在相互运动的接触面可以看作为摩擦副。
有四种摩擦分类方式:按照摩擦副的运动状态分类、按照摩擦副的运动形式分类、按照摩擦副表面的润滑状态分类、按照摩擦副所处的工况条件分类。
这里主要以根据摩擦副之间的状态不同分类,摩擦可以分为:干摩擦、边界摩擦、流体摩擦和混合摩擦,如图2-1所示。
图2-1 摩擦状态1、干摩擦当摩擦副表面间不加任何润滑剂时,将出现固体表面直接接触的摩擦(见图2-1a),工程上称为干摩擦。
此时,两摩擦表面间的相对运动将消耗大量的能量并造成严重的表面磨损。
这种摩擦状态是失效,在机器工作时是不允许出现的。
由于任何零件的表面都会因为氧化而形成氧化膜或被润滑油所湿润,所以在工程实际中,并不存在真正的干摩擦。
2 、边界摩擦当摩擦副表面间有润滑油存在时,由于润滑油与金属表面间的物理吸附作用和化学吸附作用,润滑油会在金属表面上形成极薄的边界膜。
边界膜的厚度非常小,通常只有几个分子到十几个分子厚,不足以将微观不平的两金属表面分隔开,所以相互运动时,金属表面的微凸出部分将发生接触,这种状态称为边界摩擦(见图2-1b)。
刀具磨损课程设计

刀具磨损课程设计一、课程目标知识目标:1. 学生能理解刀具磨损的基本概念,掌握影响刀具磨损的主要因素;2. 学生能够描述不同类型刀具磨损的特征及产生原因;3. 学生能够运用所学知识,分析并估算刀具的使用寿命。
技能目标:1. 学生通过观察、分析和实验,能够培养观察问题、解决问题的能力;2. 学生能够运用刀具磨损的相关知识,进行简单的工艺优化和成本控制;3. 学生能够利用图表、数据和文字,清晰、准确地表达自己的观点。
情感态度价值观目标:1. 学生培养对机械加工行业的兴趣,增强对工程技术的尊重和热爱;2. 学生通过学习刀具磨损,认识到安全生产、节约资源的重要性,培养良好的职业素养;3. 学生通过小组合作,培养团队协作精神,增强沟通与交流的能力。
课程性质:本课程为机械加工专业课程,旨在帮助学生掌握刀具磨损的基本知识,提高实际操作能力。
学生特点:学生为中职二年级学生,具备一定的机械基础知识,动手能力较强,对实际操作有浓厚兴趣。
教学要求:结合学生特点,注重理论知识与实际操作相结合,采用案例教学、实验演示等教学方法,提高学生的学习兴趣和参与度。
通过本课程的学习,使学生能够达到课程目标,为今后的职业生涯奠定基础。
二、教学内容1. 刀具磨损基本概念:介绍刀具磨损的定义、分类及磨损过程;2. 影响刀具磨损的因素:分析切削速度、进给量、切削深度等对刀具磨损的影响;3. 刀具磨损特征及原因:学习不同类型刀具磨损的特征、产生原因及防治措施;4. 刀具使用寿命估算:教授刀具使用寿命的估算方法及在实际生产中的应用;5. 刀具磨损的检测与监控:介绍刀具磨损的检测方法、监控技术及维护保养;6. 刀具磨损案例分析:分析实际生产中的刀具磨损案例,提出解决方案。
教学内容安排与进度:第1课时:刀具磨损基本概念、分类及磨损过程;第2课时:影响刀具磨损的因素及分析;第3课时:刀具磨损特征、原因及防治措施;第4课时:刀具使用寿命估算方法及应用;第5课时:刀具磨损的检测与监控技术;第6课时:刀具磨损案例分析及讨论。
磨损及磨损理论

第一节 概 述
任何机器运转时,相互接触的零件之间都将因相对运动而产 生摩擦,而磨损正是由于摩擦产生的结果。由于磨损,将造成 表层材料的损耗,零件尺寸发生变化,直接影响了零件的使用 寿命。从材料学科特别是从材料的工程应用来看,人们更重视 研究材料的磨损。据不完全统计,世界能源的1/3~1/2消耗 于摩擦,而机械零件80%失效原因是磨损。
表表面面存存在在明明显显粘粘着着痕痕迹迹和和材材料料转转移移,,有有较较大大粘粘着着坑坑块,块在,高在速高重速 载重下载,下大,量大摩量擦摩热擦使热表使面表焊面合焊,合撕,脱撕后脱留后下留片下片片粘片着粘坑着。坑。
黏黏着着坑坑密密集集,,材材料料转转移移严严重重,,摩摩擦擦副副大大量量焊焊合合,,磨磨损急损剧急增剧加增,加, 摩摩擦擦副副相相对对运运动动受受到到阻阻碍碍或或停停止止。。 材材料料以以极极细细粒粒状状脱脱落落,,出出现现许许多多““豆豆斑斑””状状凹凹坑坑。。
所以磨损是机器最常见、最大量的一种失效方式。据调查轮,胎压联痕(SEM 邦德国在1974年钢铁工业中约有30亿马克花费在维修上,其5中000X) 直接由于磨损造成的损失占47%,停机修理所造成的损失与磨损 直接造成的损失相当,如果再加上后续工序的影响,其经济损失 还需加上10%一20%。
摩擦痕迹 (350X)
此时虽然摩擦系数增大,但是磨损却很小,材料迁移也不显著。通常 在金属表面具有氧化膜、硫化膜或其他涂层时发生轻微粘着摩损。
(2)涂抹:
粘着结合强度大于较软金属抗剪切强度,小于较硬金属抗剪切强度。 剪切破坏发生在离粘着结合面不远的较软金属浅层内,软金属涂抹在硬 金属表面。这种模式的摩擦系数与轻微磨损差不多,但磨损程度加剧。
(3)磨损比
《机械设计》第三节-摩擦-磨损-润滑
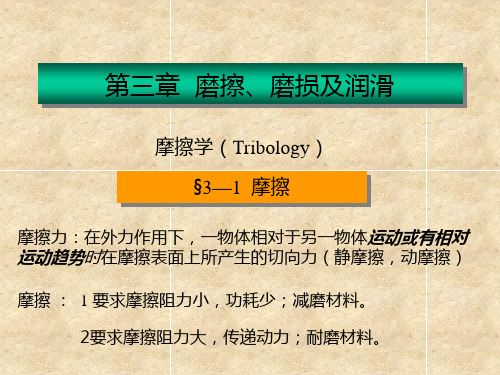
t
度不会继续改变,所占时
间比率较小
O
时间t
2、稳定磨损阶段
经磨合的摩擦表面加工硬化,形成了稳定的表面粗糙度,摩擦
条件保持相对稳定,磨损较缓,该段时间长短反映零件的寿命
3、急剧磨损阶段 经稳定磨损后,零件表面破坏,运动副间隙增大→动载振动
→润滑状态改变→温升↑→磨损速度急剧上升→直至零件失效
二、磨损的类型
弹性变形
流体摩擦(润滑)
塑性变形
边界膜
边界摩擦(润滑)—最低要求
边界膜 液体
液
混合摩擦(润滑)
边界膜
液体
一、干摩擦
摩擦理论: 库仑公式 Ff f () Fn
新理论:分子—机械理论、能量理论、粘着理论
简单粘着理论:
Ff
Ar B
Fn
sy
B
a
n
Ar Ari i 1
f () Ff B Fn sy
(3)条件粘度(相对粘度)—恩氏粘度
3、影响润滑油粘度的主要因素
(1)温度 润滑油的粘度随着温度的升高而降低
粘度指数VI ,35,85,110
(2)压力
p 0 ep
P>10MP时,随P↑→ηP↑
4、配油计算
K v vB vA vB
配油比
1、根据摩擦面间存在润滑剂的状况,滑动摩擦分
为哪几种? 2、获得流体动力润滑的基本条件是什么?
3、典型的磨损分哪三个阶段?磨损按机理分哪几 种类型?
4、什么是流体的粘性定律?
5、粘度的常用单位有哪些?影响粘度的主要因素是 什么?如何影响?
6、评价润滑脂和润滑油性能的指标各有哪几个?
润滑油压分布
v1
v2
磨损及磨损理论
粘着结合强度比两基体金属的抗剪强度都高,切应力高于粘着结合强度。 剪切破坏发生在摩擦副金属较深处,表面呈现宽而深的划痕。
此时表面将沿着滑动方向呈现明显的撕脱,出现严重磨损。如果滑动继 续进行,粘着范围将很快增大,摩擦产生的热量使表面温度剧增,极易出现 局部熔焊,使摩擦副之间咬死而不能相对滑动。 这种破坏性很强的磨损形式,应力求避免。
所以磨损是机器最常见、最大量的一种失效方式。据调查, 轮胎压痕(SEM 5000X) 联邦德国在1974年钢铁工业中约有30亿马克花费在维修上,其中 直接由于磨损造成的损失占47%,停机修理所造成的损失与磨损 直接造成的损失相当,如果再加上后续工序的影响,其经济损失 还需加上10%一20%。
摩擦痕迹 (350X)
1.6
磨损过程的一般规律:
1、磨损过程分为三个阶段:
表面被磨平, 实际接触面 积不断增大, 表面应变硬 化,形成氧 化膜,磨损 速率减小。
随磨损的增长,磨耗 增加,表面间隙增大, 表面质量恶 化,机件快速失效。
斜率就是磨损速率,唯一稳定值; 大多数机件在稳定磨损阶段(AB 段)服役; 磨损性能是根据机件在此阶段 的表现来评价。
(3)磨损比
冲蚀磨损过程中常用磨损比(也有称磨损率)来度 量磨损。
Hale Waihona Puke 材料的冲蚀磨损量(g或μ m 3) 磨损比= 造成该磨损量所用的磨料量(g)
它必须在稳态磨损过程中测量,在其它磨损阶段 中所测量的磨损比将有较大的差别。 不论是磨损量、耐磨性和磨损比,它们都是在一 定实验条件或工况下的相对指标,不同实验条件或 工况下的数据是不可比较的。
当材料产生塑性变形时,法向载荷W与较软材料的屈服极限σy之间的关系:
(1)
当摩擦副产生相对滑动,且滑动时每个微凸体上产生的磨屑为半球形。 其体积为(2/3)πa3,则单位滑动距离的总磨损量为:
磨损及磨损理论
,
汇报人:
目录
01 添 加 目 录 项 标 题
02 磨 损 的 基 本 概 念
03 磨 损 理 论
04 磨 损 的 预 防 与 控 制
05 磨 损 的 检 测 与 评 定
Prt One
单击添加章节标题
Prt Two
磨损的基本概念
磨损的定义
磨损:物体表面在相对运动过程中产生的损耗和破坏 磨损类型:包括磨粒磨损、粘着磨损、腐蚀磨损、疲劳磨损等 磨损过程:包括初始阶段、稳定阶段、加速阶段和结束阶段 磨损影响因素:包括载荷、速度、温度、润滑、材料等
润滑:润滑不良会导致磨 损加剧
材料:材料的硬度、韧性 和耐磨性对磨损有直接影 响
环境:温度、湿度、腐蚀 性气体等环境因素也会影 响磨损
Prt Three
磨损理论
粘着磨损理论
粘着磨损是指两个接触表面 在相对滑动过程中由于粘着 作用而产生的磨损
粘着磨损理论是研究粘着磨 损现象的理论
粘着磨损理论主要包括粘着 磨损机理、粘着磨损模型和
磨损量的应用:在机械设计、材料察
磨损类型:磨粒磨损、粘着磨损、腐蚀磨损等 磨损程度:轻微磨损、中度磨损、严重磨损等 磨损部位:表面磨损、内部磨损、边缘磨损等 磨损特征:颜色变化、表面粗糙度、尺寸变化等
磨损性能的评定
磨损检测方法:光学显微镜、电子显微镜、X射线衍射等 磨损评定标准:磨损量、磨损率、磨损寿命等 磨损性能指标:耐磨性、抗磨性、耐蚀性等 磨损机理研究:摩擦学、材料科学、表面工程等
磨粒磨损理论
磨粒磨损:由硬质 颗粒引起的磨损
磨粒来源:自然界 中的砂石、金属颗 粒等
磨损过程:磨粒与 材料表面接触、摩 擦、剥落
磨损后果:材料表 面磨损、疲劳、断 裂等
摩擦磨损基本原理
4.犁沟效应
犁沟效应是硬金属的粗糙峰嵌入软金属后,在滑 动中推挤软金属,产生塑性流动并划出一条沟槽。 犁沟效应的阻力是摩擦力的组成部分,在磨粒磨损 和檫伤磨损中,为主要分量。
硬金属表面的粗糙峰由许多半角为θ 的圆锥体组成,在法向载荷作用下,硬 峰嵌入软金属的深度为h,滑动摩擦时, 只有圆锥体的前沿面与软金属接触。 接触表面在水平面上的投影面积A =πd2/8; 在垂直面上的投影面积S=dh/2。 如果软金属的塑性屈服性能各向同性,屈服极限为σs,于是 法向载荷W和犁沟力Pe 分别为
定律三:摩擦系数与滑动速度无关。虽然对于金属材料基 本符合,而对粘弹性显著的弹性材料,摩擦系数则明显与滑 动速度有关。
特别注意:在古典摩擦定律中,摩擦系数µ是一个常数。 大量的试验指出,很难确定某种摩擦副固定的摩擦系数, 仅在一定的环境(湿度温度等)和工况(速度和载荷等)下,对 于一定的材质的摩擦副来说,µ才有可能是一个常数。如在 正常的大气环境下,硬质钢摩擦副表面的µ为0.6,但在真 空下,其µ可达到2.0。 因此,通过摩擦试验测得试样的摩擦系数时,必须注明 试验条件,否则所得的试验数据没有意义。
a.金属的整体机械性质:如剪切强度、屈服极限、硬度、弹 性模量等,都直接影响摩擦力的粘着项和犁沟项。 b. 晶态材料的晶格排列:在不同晶体结构单晶的不同晶面 上,由于原子密度不同,其粘着强度也不同。如面心立方晶 系的Cu的(111)面,密排六方晶系的Co的(001)面,原子密度 高,表面能低,不易粘着。
对金属间的摩擦而言,主要是粘着作用,其次是“犁沟”作用。 而材料的弹性变形引起的能量消耗很小,因而对总摩擦阻力的 影响很小,故可忽略不计,因此摩擦阻力可用下式表达:
F = F 剪 + F犁
(试卷真题)第3章_摩擦
第3章摩擦、磨损及润滑一、选择题1.干摩擦时,摩擦力与所受载荷及表观接触面积的关系为:____A.与表观面积无关而与载荷成正比B. 与表观面积有关而与载荷无关C. 与表观面积有关而与载荷成正比选A第3章摩擦、磨损及润滑第1节摩擦力与接触面积的关系来源:机械设计学习要点与习题解析P162.摩擦副表面为液体动压润滑状态,当外载荷不变时,摩擦面间的最小油膜厚度随相对滑动速度的增加而____。
A.变薄B.增厚C.不变选B第3章摩擦、磨损及润滑第1节摩擦的性质来源:机械设计学习要点与习题解析P163.两相对滑动的接触表面,依靠吸附油膜进行润滑的摩擦状态称为____。
A.干摩擦B.边界摩擦C.混合摩擦D.液体摩擦选B第3章摩擦、磨损及润滑第1节摩擦的判别来源:机械设计学习要点与习题解析P164.减少磨损的一般方法有很多中,其中____是错误的。
A.选择合适的材料组合B.生成表面膜C.改滑动摩擦为滚动摩擦D.增加表面粗糙度选D第3章摩擦、磨损及润滑第2节减少磨损的方法来源:机械设计学习要点与习题解析P165.表面疲劳磨损(点蚀)的发生与____有关。
A.酸碱盐介质B.瞬时速度C.硬质磨粒D.材料浅层缺陷选D第3章摩擦、磨损及润滑第2节磨损的性质来源:机械设计学习要点与习题解析P176.各种油杯中,____可用于脂润滑。
A.针阀油杯B.油绳式油杯C.旋盖式油杯选C第3章摩擦、磨损及润滑第3节润滑的分类来源:机械设计学习要点与习题解析P177.零件表面在混合润滑状态时的摩擦系数比液体润滑状态时的摩擦系数____。
A.大B.小C.可能大可能小D.相等选A第3章摩擦、磨损及润滑第1节摩擦的性质来源:机械设计学习要点与习题解析P178.为了减轻摩擦副的表面疲劳磨损,下面措施中,____是不合理的。
A.降低表面粗糙度B.增大润滑油粘度C.提高表面硬度D.提高相对滑动速度选D第3章摩擦、磨损及润滑第2节磨损的判别来源:机械设计学习要点与习题解析P179.采用含有油性和极压添加剂的润滑剂,主要是为了减少____。
- 1、下载文档前请自行甄别文档内容的完整性,平台不提供额外的编辑、内容补充、找答案等附加服务。
- 2、"仅部分预览"的文档,不可在线预览部分如存在完整性等问题,可反馈申请退款(可完整预览的文档不适用该条件!)。
- 3、如文档侵犯您的权益,请联系客服反馈,我们会尽快为您处理(人工客服工作时间:9:00-18:30)。
磨损的快慢程度)为:
第三章磨损及磨损理论
(2)
由(1)和(2)式,可得:
(3)
式(3)是假设了各个微凸体在接触时均产生一个磨粒而导出。
如果考虑到微凸体相互产生磨粒的概率数K和滑动距离L,
则接触表面的粘着磨损量表达式为:
(4)
由于对于弹性材料σs≈H/3,H为布氏硬度值,则式(4)可
变为:
式中K为粘着磨损系数
第三章 磨损及磨损理论
第三章磨损及磨损理论
一、概述
1、磨损定义: 相互接触的物体在相对运动中,表层材料不
断损失、转移或产生残余变形的现象称为磨损, 它是伴随着摩擦而产生的必然结果。 ➢ 有些磨损是有益的,如“研磨”,可使零件表 面粗糙度减小,使刀刃变得锋利。 ➢ 但是,据统计,约有80%左右的机械零件是由 于磨损而报废或失效。
第三章磨损及磨损理论
3、磨损过程 零件的正常磨损过程大致可分为三个阶段: Ⅰ:跑合(磨合)阶段;Ⅱ:稳定磨损阶段;
Ⅲ:剧烈磨损阶段
第三章磨损及磨损理论
Ⅰ:跑合(磨合)阶段
出现在摩擦副的初始运动阶段,由于表面存在 粗糙度,微凸体接触面积小,接触应力大,磨 损速度快。 在一定载荷作用下,摩擦表面逐渐 磨平,实际接触面积逐渐增大,磨损速度逐渐 减慢,如图所示。 第三章磨损及磨损理论
持常数-磨损量与压力成正比);
压力值为H/3,各个微凸体上的塑性变形区开始发生相
互影响;
压力值超过H/3,磨损量急剧增大(K值急剧增大),高
的载荷作用下,整个表面变成塑性流动区,发生大面 积的粘着焊连,出现第剧三章烈磨损的及磨粘损理着论 磨损。
式中的K代表微凸
体中产生磨粒的 概率,即粘着磨 损系数。
** 从磨损过程的变化来看,为了提高机器零件的 使用寿命,应尽量延第长三章“磨损稳及磨损定理论磨损阶段”。
二、 磨 损 的 分 类
第三章磨损及磨损理论
1、粘着磨损
(1)定义 当摩擦副相对滑动时, 由于粘着效应 所形成的结点发生剪切断裂,接触表 面的材料从一个表面转移到另一个表 面的现象称为粘着磨损; 法向力和切向力共同作用的结果。
第三章磨损及磨损理论
2、磨损研究的主要内容:
(1) 主要磨损类型的发生条件、特征和变化 规律; (2) 磨损的影响因素, 包括摩擦副材料、表 面形态、润滑状况、环境条件, 以及滑动速 度、载荷、工作温度等工况参数; (3) 磨损的模型与磨损计算; (4) 提高材料耐磨性的措施; (5) 磨损研究的测试技术与实验分析方法。
环不断进行,构成粘着磨损过
程。
第三章磨损及磨损理论
(3) 粘着磨损的分类
根据粘着点的强度和破坏位置不同,粘着磨损 有几种不同的形式,共同的特征是:出现材料迁 移,以及沿滑动方向形成程度不同的划痕。
a.轻微磨损
➢ 粘着强度比摩擦副两金属基体剪切强度低; ➢ 剪切发生在粘着结合面上,表面转移的材料较轻
由(4)式可得粘着磨损的三个定律:
①材料磨损量与滑动距离成正比:源自用于多种条件②材料磨损量与法向载荷成正比:适用于有限载荷范围
③材料磨损量与较软材料的屈服极限σs(或硬度H)成反比
第三章磨损及磨损理论
纵坐标为K/H,代表单位载荷、
单位滑动距离的磨损量,横坐标 代表平均接触压力。
压力值小于H/3(σs ),磨损率小而且保持不变(即K保
K值必须按不同的
滑动材料组合和 不同的摩擦条件 求得。右表给出 了不同工况和摩 擦副配对时的磨
损系数K值。
第三章磨损及磨损理论
(5) 粘着磨损的影响因素
①摩擦副材料性质的影响 a.脆性材料比塑性材料的抗粘着能力高。 塑性材料粘着点的破坏以塑性流动为主,发生在表 层深处,磨损颗粒大。脆性材料粘着点的破坏主要 是剥落,发生在表层浅处,磨损颗粒小,呈磨屑状, 磨屑容易脱落, 不堆积在表面上。
c.擦伤
➢ 粘着强度比摩擦副的两基体金属的剪切强度都高; ➢ 剪切主要发生在软金属的亚表层内,有时也发生在硬
金属的亚表层内,转移到硬金属上的粘着物又刮削软 金属表面,使软金属表面出现划痕,所以擦伤主要发 生在软金属表层,硬第三金章磨属损及表磨损面理论也偶有划伤。
d.咬合(胶合)
➢ 粘着强度比两金属基体的剪切强度高得多; ➢ 粘着点面积较大时,剪切破坏发生在一个或两
Ⅱ稳定磨损阶段:
出现在摩擦副的正常运行阶段。经过跑合,摩擦 表面加工硬化,微观几何形状改变,实际接触面 积增大,压强降低,从而建立了弹性接触的条件, 这时磨损已经稳定下来,如图所示,磨损量随时 间增大缓慢增大。第三章磨损及磨损理论
Ⅲ 剧烈磨损阶段:当材料磨损量达到一定数值时, 摩擦条件发生较大的变化,磨损速度急剧增加。这 时机械效率下降,精度降低,出现异常的噪音及振 动,最后导致零件完全失效。
微; ➢ 摩擦系数增大,但磨损量很小; ➢ 金属表面具有氧化膜、硫化膜或其他涂层时发生
轻微粘着摩损。 第三章磨损及磨损理论
b.涂抹
➢ 粘着强度大于摩擦副中较软金属的剪切强度,小于较 硬金属的剪切强度;
➢ 剪切破坏发生在离粘着结合面不远的较软金属浅层内, 软金属涂抹(粘附)在硬金属表面上;
➢ 摩擦系数与轻微磨损差不多,但磨损程度加剧。
上图为粘着磨损模型,假设摩擦副的一方为较硬的
材料,摩擦副另一方为较软的材料;法向载荷W由n
个半径为a的相同微凸体承受。
第三章磨损及磨损理论
则当材料产生塑性变形时,法向载荷W与较软材料
的屈服极限σs之间的关系:
(1)
当摩擦副产生相对滑动,且滑动时每个微凸体上产
生的磨屑为半球形,其体积为(2/3)πa3,则单位滑动 距离的总磨损量(即体积磨损率,通常用于判断材料
第三章磨损及磨损理论
(2) 粘着磨损机理
在一定的法向载荷作用下,微凸体接触,发生 塑性变形,产生粘着;
在相对滑动过程中,剪切粘着点,材料就会从 一个表面转移到另外一表面,形成磨损;
一部分转移的材料分离, 从而形成游离磨粒; 再形成新的粘着点。
** 接触-塑性变形-粘着-剪断
粘着点-材料转移-再粘着,循
个金属表层深的地方,发生严重磨损,剪切应 力高于粘着结合力; ➢ 剪切应力低于粘着结合力,摩擦副之间咬死不 能滑动。 ➢ 高速重载下,微凸体塑性变形大,温度高,粘 着点的强度和面积大,通常产生胶合磨损。 *** 这种破坏性很强第的三章磨磨损及损磨损形理论式,应力求避免。
(4)简单粘着磨损计算(Archard模型)