磨损及磨损机理
耐磨材料的磨损机理研究

耐磨材料的磨损机理研究耐磨材料是一类能在磨损条件下保持较高耐磨性能的材料,它们广泛应用于工业生产中的磨损环境中。
然而,耐磨材料仍然存在一定程度的磨损。
因此,研究耐磨材料的磨损机理对于改进其性能和延长使用寿命具有重要意义。
一、磨损机理的基本概念磨损是指材料表面在摩擦或其他机械作用下逐渐失去物质的过程。
磨损机理是指导致磨损过程发生的各种因素和机制。
磨损主要分为三种类型:磨削磨损、疲劳磨损和腐蚀磨损。
磨削磨损是由于颗粒在材料表面与其它材料之间的相对运动中引起的磨损。
疲劳磨损是由于材料的重复应力加载引起的破裂和磨损。
腐蚀磨损是由于材料与介质之间的化学或电化学反应引起的磨损。
二、磨损机理的研究方法磨损机理的研究通常采用实验方法和理论模型相结合的方式进行。
实验方法主要包括摩擦磨损试验和磨损机理分析。
摩擦磨损试验可以模拟实际工作条件下材料的磨损过程,通过测量磨损量和观察磨损形貌等参数来评估材料的耐磨性能。
磨损机理分析则通过对磨损表面的观察、扫描电镜分析等手段来揭示磨损的机理和过程。
理论模型则是通过建立材料磨损的数学模型,从而定量地描述磨损过程和磨损机理。
三、磨损机理的影响因素耐磨材料的磨损机理受到多种因素的影响。
首先是材料的力学性能,包括硬度、强度和韧性等。
硬度是表征材料耐磨性能的重要指标,硬度较高的材料通常具有较好的耐磨性能。
其次是摩擦条件,包括摩擦力、摩擦速度和工作温度等。
摩擦力和摩擦速度的增加都会导致材料的磨损加剧。
此外,介质以及杂质的存在也会对耐磨材料的磨损机理产生一定的影响。
四、耐磨材料的改进策略为了改进耐磨材料的耐磨性能,可以采取多种策略。
一方面,可以通过优化材料的组织结构和成分,例如通过合金化、热处理或表面改性等方式来增加材料的硬度、强度和韧性等力学性能。
另一方面,可以通过涂层或复合材料等方式增加材料的摩擦和磨损性能,例如通过在材料表面涂覆一层硬度较高的薄膜来提高耐磨材料的耐磨性能。
此外,加工工艺的改进也有助于提高耐磨材料的性能,例如通过冷加工、表面处理等方式来优化材料的结构和性能。
机械零件的磨损机理与疲劳分析

机械零件的磨损机理与疲劳分析引言:机械零件是构成各种机械设备的核心组成部分,其质量和可靠性直接影响着整个设备的性能和寿命。
在机械运动过程中,零件之间的接触和磨擦不可避免地会导致磨损和疲劳,从而降低机械零件的工作效率和寿命。
因此,研究机械零件的磨损机理与疲劳分析成为提高机械设备的性能和寿命的重要课题。
一、磨损机理磨损是机械零件在相对运动过程中表面材料的损失,主要包括磨粒磨损、疲劳磨损和润滑磨损等。
1. 磨粒磨损磨粒磨损是由于杂质等颗粒物进入零件表面的接触区域,与零件表面发生相对滑动而引起的既摩擦又磨损现象。
磨粒磨损会导致零件表面粗糙度增加,磨粒在摩擦接触区域形成凹槽和划痕,进一步加剧磨损。
2. 疲劳磨损疲劳磨损是由周期性应力作用引起的损伤,主要发生在机械零件承受往复或交变载荷的部位。
机械零件在往复运动过程中,由于应力的交变作用,材料表面会出现微裂纹,随着应力的不断作用,微裂纹会逐渐扩展并最终导致零件的疲劳破坏。
3. 润滑磨损润滑磨损是由于润滑油膜的破坏而引起的磨损现象。
当机械零件表面的润滑油膜无法保持稳定时,摩擦接触表面之间的直接接触会增加,摩擦热和摩擦力会增大,从而导致零件表面的磨损加剧。
二、疲劳分析疲劳分析是研究机械零件在循环加载下的疲劳性能和寿命的工程方法。
通过对零件材料的应力应变状态和疲劳强度的分析,可以判断零件在正常工况下的抗疲劳性能,并提出相应的改进措施。
1. 应力分析应力是导致机械零件疲劳破坏的主要因素。
在进行疲劳分析时,需要对零件所受的静态和动态载荷进行分析,计算出零件的应力分布情况,并结合材料的疲劳强度曲线,判断零件是否会发生疲劳破坏。
2. 循环载荷循环载荷是指在零件使用过程中的周期性变化的载荷。
循环载荷下,机械零件会发生应力集中和应力交变,进而引起疲劳裂纹和疲劳破坏。
因此,在疲劳分析中,需要对循环载荷进行精确的统计和计算,以准确评估零件在实际工作条件下的疲劳性能。
3. 疲劳强度分析疲劳强度是指材料在循环加载作用下能够承受的最大载荷水平。
磨损及磨损理论

第一节 概 述
任何机器运转时,相互接触的零件之间都将因相对运动而产 生摩擦,而磨损正是由于摩擦产生的结果。由于磨损,将造成 表层材料的损耗,零件尺寸发生变化,直接影响了零件的使用 寿命。从材料学科特别是从材料的工程应用来看,人们更重视 研究材料的磨损。据不完全统计,世界能源的1/3~1/2消耗 于摩擦,而机械零件80%失效原因是磨损。
表表面面存存在在明明显显粘粘着着痕痕迹迹和和材材料料转转移移,,有有较较大大粘粘着着坑坑块,块在,高在速高重速 载重下载,下大,量大摩量擦摩热擦使热表使面表焊面合焊,合撕,脱撕后脱留后下留片下片片粘片着粘坑着。坑。
黏黏着着坑坑密密集集,,材材料料转转移移严严重重,,摩摩擦擦副副大大量量焊焊合合,,磨磨损急损剧急增剧加增,加, 摩摩擦擦副副相相对对运运动动受受到到阻阻碍碍或或停停止止。。 材材料料以以极极细细粒粒状状脱脱落落,,出出现现许许多多““豆豆斑斑””状状凹凹坑坑。。
所以磨损是机器最常见、最大量的一种失效方式。据调查轮,胎压联痕(SEM 邦德国在1974年钢铁工业中约有30亿马克花费在维修上,其5中000X) 直接由于磨损造成的损失占47%,停机修理所造成的损失与磨损 直接造成的损失相当,如果再加上后续工序的影响,其经济损失 还需加上10%一20%。
摩擦痕迹 (350X)
此时虽然摩擦系数增大,但是磨损却很小,材料迁移也不显著。通常 在金属表面具有氧化膜、硫化膜或其他涂层时发生轻微粘着摩损。
(2)涂抹:
粘着结合强度大于较软金属抗剪切强度,小于较硬金属抗剪切强度。 剪切破坏发生在离粘着结合面不远的较软金属浅层内,软金属涂抹在硬 金属表面。这种模式的摩擦系数与轻微磨损差不多,但磨损程度加剧。
(3)磨损比
机械系统中的摩擦与磨损机理分析
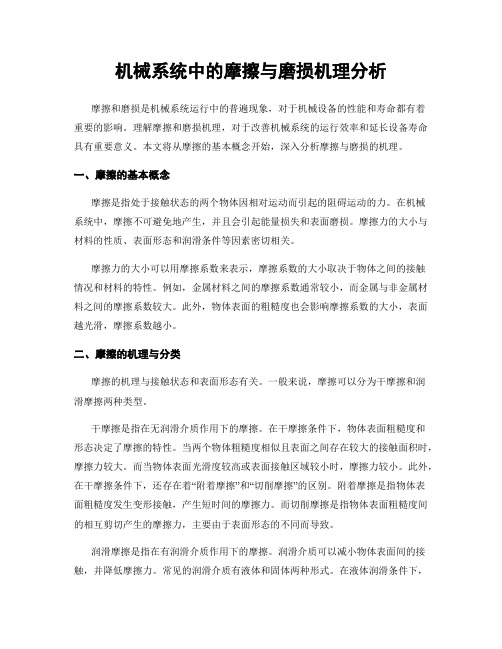
机械系统中的摩擦与磨损机理分析摩擦和磨损是机械系统运行中的普遍现象,对于机械设备的性能和寿命都有着重要的影响。
理解摩擦和磨损机理,对于改善机械系统的运行效率和延长设备寿命具有重要意义。
本文将从摩擦的基本概念开始,深入分析摩擦与磨损的机理。
一、摩擦的基本概念摩擦是指处于接触状态的两个物体因相对运动而引起的阻碍运动的力。
在机械系统中,摩擦不可避免地产生,并且会引起能量损失和表面磨损。
摩擦力的大小与材料的性质、表面形态和润滑条件等因素密切相关。
摩擦力的大小可以用摩擦系数来表示,摩擦系数的大小取决于物体之间的接触情况和材料的特性。
例如,金属材料之间的摩擦系数通常较小,而金属与非金属材料之间的摩擦系数较大。
此外,物体表面的粗糙度也会影响摩擦系数的大小,表面越光滑,摩擦系数越小。
二、摩擦的机理与分类摩擦的机理与接触状态和表面形态有关。
一般来说,摩擦可以分为干摩擦和润滑摩擦两种类型。
干摩擦是指在无润滑介质作用下的摩擦。
在干摩擦条件下,物体表面粗糙度和形态决定了摩擦的特性。
当两个物体粗糙度相似且表面之间存在较大的接触面积时,摩擦力较大。
而当物体表面光滑度较高或表面接触区域较小时,摩擦力较小。
此外,在干摩擦条件下,还存在着“附着摩擦”和“切削摩擦”的区别。
附着摩擦是指物体表面粗糙度发生变形接触,产生短时间的摩擦力。
而切削摩擦是指物体表面粗糙度间的相互剪切产生的摩擦力,主要由于表面形态的不同而导致。
润滑摩擦是指在有润滑介质作用下的摩擦。
润滑介质可以减小物体表面间的接触,并降低摩擦力。
常见的润滑介质有液体和固体两种形式。
在液体润滑条件下,摩擦系数较小,润滑膜的形成对减小摩擦力有重要作用。
而在固体润滑条件下,固体润滑剂填充物体表面间的空隙,减小物体之间的直接接触,从而减小摩擦力。
三、磨损的机理与分类磨损是指机械设备在长期运行过程中,表面材料的逐渐损失。
磨损的机理与摩擦密切相关。
常见的磨损形式有磨粒磨损、疲劳磨损和腐蚀磨损等。
磨损分类
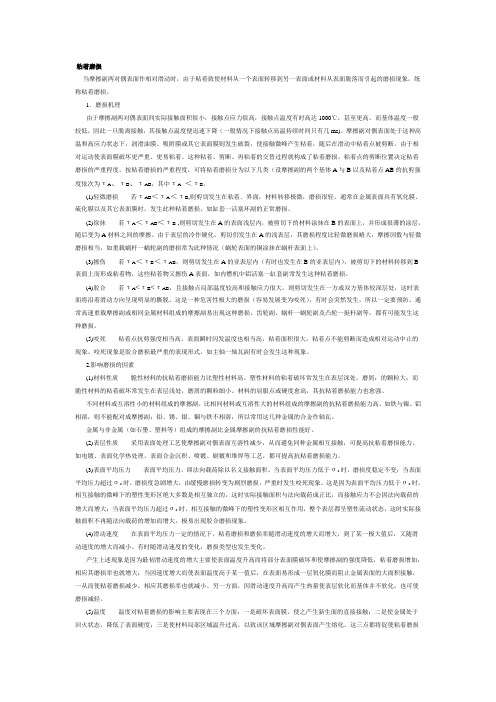
粘着磨损当摩擦副两对偶表面作相对滑动时,由于粘着致使材料从一个表面转移到另一表面或材料从表面脱落而引起的磨损现象,统称粘着磨损。
1.磨损机理由于摩擦副两对偶表面间实际接触面积很小,接触点应力很高,接触点温度有时高达1000℃,甚至更高,而基体温度一般较低,因此一旦脱离接触,其接触点温度便迅速下降(一般情况下接触点高温持续时间只有几ms)。
摩擦副对偶表面处于这种高温和高应力状态下,润滑油膜、吸附膜或其它表面膜则发生破裂,使接触微峰产生粘着,随后在滑动中粘着点被剪断。
由于相对运动使表面膜破坏更严重、更易粘着。
这种粘着、剪断、再粘着的交替过程就构成了粘着磨损。
粘着点的剪断位置决定粘着磨损的严重程度,按粘着磨损的严重程度,可将粘着磨损分为以下几类(设摩擦副的两个基体A与B以及粘着点AB的抗剪强度依次为τA、τB、τAB,其中τA<τB。
(1)轻微磨损若τAB<τA<τB,则剪切发生在粘着.界面,材料转移极微,磨损很轻。
通常在金属表面具有氧化膜、硫化膜以及其它表面膜时,发生此种粘着磨损,如缸套一活塞环副的正常磨损。
(2)徐抹若τA<τAB<τB ,则剪切发生在A的表面浅层内,被剪切下的材料涂抹在B的表面上,并形成很薄的涂层,随后变为A材料之间的摩擦。
由于表层的冷作硬化,剪切仍发生在A的浅表层,其磨损程度比轻微磨损略大,摩擦因数与轻微磨损相当,如重载蜗杆一蜗轮副的磨损常为此种情况(蜗轮表面的铜涂抹在蜗杆表面上)。
(3)擦伤若τA<τB<τAB,则剪切发生在A的亚表层内(有时也发生在B的亚表层内),被剪切下的材料转移到B 表面上而形成粘着物,这些粘着物又擦伤A表面,如内燃机中铝活塞一缸套副常发生这种粘着磨损。
(4)胶合若τA<τB<τAB,且接触点局部温度较高和接触应力很大,则剪切发生在一方或双方基体较深层处,这时表面将沿着滑动方向呈现明显的撕脱。
这是一种危害性极大的磨损(容易发展变为咬死),有时会突然发生,所以一定要预防。
航空发动机磨损机理分析及寿命评估

航空发动机磨损机理分析及寿命评估航空发动机是飞机的心脏,负责为飞机提供动力。
然而,随着使用时间的增长和使用次数的增多,航空发动机的磨损会逐渐加剧,从而影响其性能和寿命。
因此,了解航空发动机磨损的机理,并评估其寿命,对于确保飞机的安全和可靠性具有重要意义。
一、航空发动机磨损机理分析1.磨损的概念磨损是指在接触面上由于相对运动而导致的材料表面物质的逐渐丧失。
在航空发动机中,磨损是由于高温、高速、高压、腐蚀等因素的作用,导致材料表面的微小颗粒逐渐脱落而形成。
2.磨损的分类根据磨损形式的不同,磨损可以分为以下几种类型:(1)磨粒磨损:由于常温下颗粒杂质或高温下氧化产物的存在,使工作表面与磨料之间产生碰撞和磨擦,从而引起被磨损部分的材料脱落。
(2)表面疲劳磨损:在高速、高频率的疲劳循环作用下,工作表面出现因微小裂纹逐渐扩展引起的磨损。
(3)腐蚀磨损:由于化学介质的作用,使材料表面出现腐蚀,导致材料的表面产生颗粒状脱落,引起磨损。
3.磨损机理在航空发动机中,磨损主要是由于以下因素的共同作用所引起的:(1)高速、高温、高压的气流对叶片等工作表面的冲蚀作用。
(2)燃烧产物对高压涡轮和热门结构材料的腐蚀作用。
(3)磨损颗粒的积累和覆盖。
(4)机械振动和冲击、疲劳循环等。
4.磨损形态航空发动机中常见的磨损形态有以下几种:(1)划痕:指叶片和盘根等工作表面的表面产生细微划痕,进一步加剧表面磨损情况。
(2)点蚀:指机械表面出现颗粒状的点蚀,容易引起裂纹的扩展。
(3)抛光:指工作表面因反复摩擦而使表面光滑度提高,进一步加剧表面磨损情况。
二、航空发动机寿命评估寿命评估是指对航空发动机进行寿命预测和寿命评估,旨在确保发动机长期安全、可靠地运行。
由于航空发动机的寿命评估受到多种因素的影响,因此需要采取一些先进的技术手段,如结构预测、时变可靠性评估、损伤容限和定期检查等。
1.结构预测结构预测是预测航空发动机各部件的寿命,并对各部件进行安排和调度。
机械轴承磨损机理分析
机械轴承磨损机理分析引言机械轴承是现代机械工业中不可或缺的组成部分,用于支撑旋转设备。
然而,随着使用时间的增长,机械轴承会经历各种磨损,这对设备的可靠性和寿命产生了负面影响。
因此,深入了解机械轴承的磨损机理对于维护设备的正常运转至关重要。
本文将针对机械轴承的磨损机理进行分析。
一、摩擦磨损机理1.1 润滑磨损机械轴承在高速旋转时,可产生高温和高压,这会导致润滑剂的挥发。
润滑油的挥发会导致润滑膜的破裂,从而使金属之间直接接触,引起金属摩擦磨损。
此外,当润滑剂的黏度不足时,也会导致润滑效果不佳,增加机械轴承的摩擦磨损。
1.2 磨粒磨损机械轴承在长时间的运转中,会产生磨粒,这些磨粒会嵌入机械轴承中形成微小的凹痕,进而加剧机械轴承的摩擦磨损。
磨粒的来源可以是机械轴承零件自身的磨损,也可以是外部进入的杂质进而破坏润滑膜,引发机械轴承的磨损。
二、疲劳磨损机理机械轴承在频繁加载和解载的工况下,会发生疲劳磨损。
疲劳磨损是由于材料的应力和载荷超过其疲劳极限,导致材料内部微小裂纹的形成和扩展。
这些微小裂纹在运行中不断扩展并最终导致材料的疲劳破裂。
因此,合理设计和控制机械轴承的负荷是减少疲劳磨损的关键。
三、腐蚀磨损机理3.1 酸性腐蚀磨损机械轴承在恶劣环境下,如高温、高湿等条件下,易受到酸性物质侵蚀。
酸性腐蚀会导致机械轴承表面的金属被蚀去,引起材料的腐蚀磨损。
因此,防止机械轴承接触酸性物质是减少腐蚀磨损的有效措施。
3.2 电化学腐蚀磨损当机械轴承在电解液中运行时,电解液中的电解质会与机械轴承表面产生电化学反应,引起表面材料的腐蚀磨损。
在这种情况下,合理选择电解液和防腐润滑剂,可以减少机械轴承的电化学腐蚀磨损。
四、其他因素对磨损机理的影响4.1 温度对磨损的影响温度是机械轴承磨损的重要因素之一。
当温度过高时,机械轴承的润滑剂会分解和蒸发,导致润滑效果不佳,进而加剧机械轴承的磨损。
因此,合理控制机械轴承的运行温度,选择适当的润滑剂,可以减少磨损。
磨损及磨损理论
粘着结合强度比两基体金属的抗剪强度都高,切应力高于粘着结合强度。 剪切破坏发生在摩擦副金属较深处,表面呈现宽而深的划痕。
此时表面将沿着滑动方向呈现明显的撕脱,出现严重磨损。如果滑动继 续进行,粘着范围将很快增大,摩擦产生的热量使表面温度剧增,极易出现 局部熔焊,使摩擦副之间咬死而不能相对滑动。 这种破坏性很强的磨损形式,应力求避免。
所以磨损是机器最常见、最大量的一种失效方式。据调查, 轮胎压痕(SEM 5000X) 联邦德国在1974年钢铁工业中约有30亿马克花费在维修上,其中 直接由于磨损造成的损失占47%,停机修理所造成的损失与磨损 直接造成的损失相当,如果再加上后续工序的影响,其经济损失 还需加上10%一20%。
摩擦痕迹 (350X)
1.6
磨损过程的一般规律:
1、磨损过程分为三个阶段:
表面被磨平, 实际接触面 积不断增大, 表面应变硬 化,形成氧 化膜,磨损 速率减小。
随磨损的增长,磨耗 增加,表面间隙增大, 表面质量恶 化,机件快速失效。
斜率就是磨损速率,唯一稳定值; 大多数机件在稳定磨损阶段(AB 段)服役; 磨损性能是根据机件在此阶段 的表现来评价。
(3)磨损比
冲蚀磨损过程中常用磨损比(也有称磨损率)来度 量磨损。
Hale Waihona Puke 材料的冲蚀磨损量(g或μ m 3) 磨损比= 造成该磨损量所用的磨料量(g)
它必须在稳态磨损过程中测量,在其它磨损阶段 中所测量的磨损比将有较大的差别。 不论是磨损量、耐磨性和磨损比,它们都是在一 定实验条件或工况下的相对指标,不同实验条件或 工况下的数据是不可比较的。
当材料产生塑性变形时,法向载荷W与较软材料的屈服极限σy之间的关系:
(1)
当摩擦副产生相对滑动,且滑动时每个微凸体上产生的磨屑为半球形。 其体积为(2/3)πa3,则单位滑动距离的总磨损量为:
磨损的类型磨损机理表面疲劳磨损形成及影响因素
磨损的类型磨损机理表面疲劳磨损形成及影响因素磨损实际是接触表面随着时间增加和载荷作用损伤的累积过程。
自然界中不论机械零件,还是人造关节都存在着磨损。
可以说,磨损无处不在。
它直接影响着机器的运转精度和寿命。
据统计,每年全世界生产总值的近五分之二被摩擦磨损消耗掉了。
因此,开展系统的摩擦学设计,尽量减少或消除磨损,对人类具有重大意义。
前苏联学者进一步较全面地提出了区分磨损类别的方法。
他将磨损分为三个过程,依次为表面的相互作用两体摩擦表面的相互作用可以是机械的或分子的。
机械作用包括弹性变形、塑性变形和犁沟效应,可以是两体表面的粗糙峰直接啮合引起的,也可以是夹在中间的外界磨粒造成的。
表面分子的作用包括相互吸引和粘着,前者作用力小于后者。
表面层的变化在表面摩擦的作用下,表面层将发生机械的,组织结构的及物理的和化学的变化,这是由于表面变形、摩擦温度和环境介质等因素的影响造成的。
表面层的塑性变形会使金属冷作硬化而变脆,反复的弹性变形会使金属出现疲劳破坏。
摩擦热引起的表面接触高温可以使表层金属退火软化,而接触后急剧冷却将导致再结晶或固溶体分解。
外界环境的影响主要表现为介质在表层的扩散,包括氧化和其他化学腐蚀作用,因而会改变金属表面层的组织结构。
表面层的破坏形式有擦伤、点蚀、剥落、胶合、微观磨损。
近年来的研究普遍认为, 按照不同的机理对磨损来进行分类是比较恰当的。
通常可将磨损划分为个基本类型粘着磨损、磨粒磨损、表面疲劳磨损和腐蚀磨损。
虽然这种分类还不十分完善, 但概括了各种常见的磨损形式。
磨损机理通常从机理上可以把磨损分为粘着磨损,磨粒磨损,表面疲劳磨损,侵蚀磨损,腐蚀磨损和热磨损等。
粘着磨损相对运动的表面因存在分子间的吸引而在表面的微观接触处产生粘着作用,当粘着作用的强度大于材料内部的联接强度时,经过一定周期的接触就会产生磨损。
粘着磨损的磨损度常常是压力的函数,低压软表面或高压下都会产生严重的粘着磨损。
对于可以认为是同类材料的摩擦副表面,磨损常数趋于较大值,因为粘着作用的实质是原子或分子间产生了融合。
摩擦、磨损简介
磨损基本概念磨损是零部件失效的一种基本类型.通常意义上来讲,磨损是指零部件几何尺寸〔体积〕变小.零部件失去原有设计所规定的功能称为失效.失效包括完全丧失原定功能;功能降低和有严重损伤或隐患,继续使用会失去可靠性及安全性和安全性.1、磨损的分类:按照表面破坏机理特征,磨损可以分为磨料磨损、粘着磨损、表面疲劳磨损、腐蚀磨损和微动磨损等.前三种是磨损的基本类型,后两种只在某些特定条件下才会发生.磨料磨损:物体表面与硬质颗粒或硬质凸出物〔包括硬金属〕相互摩擦引起表面材料损失.粘着磨损:摩擦副相对运动时,由于固相焊合作用的结果,造成接触面金属损耗.表面疲劳磨损:两接触表面在交变接触压应力的作用下,材料表面因疲劳而产生物质损失.腐蚀磨损:零件表面在摩擦的过程中,表面金属与周围介质发生化学或电化学反应,因而出现的物质损失.微动磨损:两接触表面间没有宏观相对运动,但在外界变动负荷影响下,有小振幅的相对振动〔小于100μm〕,此时接触表面间产生大量的微小氧化物磨损粉末,因此造成的磨损称为微动磨损2、表征材料磨损性能的参量为了反映零件的磨损,常常需要用一些参量来表征材料的磨损性能.常用的参量有以下几种:<1>磨损量由于磨损引起的材料损失量称为磨损量,它可通过测量长度、体积或质量的变化而得到,并相应称它们为线磨损量、体积磨损量和质量磨损量.<2>磨损率以单位时间内材料的磨损量表示,即磨损率I=dV /dt <V为磨损量,t为时间〕.<3>磨损度以单位滑移距离内材料的磨损量来表示,即磨损度E=dV/dL <L为滑移距离〕.<4>耐磨性指材料抵抗磨损的性能,它以规定摩擦条件下的磨损率或磨损度的倒数来表示,即耐磨性=dt/dV或dL/dV.<5>相对耐磨性指在同样条件下,两种材料〔通常其中一种是Pb-Sn合金标准试样〕的耐磨性之比值,即相对耐磨性εw=ε试样/ε标样.摩擦基本概念当物体与另一物体沿接触面的切线方向运动或有相对运动的摩擦趋势时,在两物体的接触面之间有阻碍它们相对运动的作用力,这种力叫摩擦力.接触面之间的这种现象或特性叫"摩擦".摩擦有利也有害,但在多数情况下是不利的,例如,机器运转时的摩擦,造成能量的无益损耗和机器寿命的缩短,并降低了机械效率.因此常用各种方法减少摩擦,如在机器中加润滑油等.但摩擦又是不可缺少的,例如,人的行走,汽车的行驶都必须依靠地面与脚和车轮的摩擦.在泥泞的道路上,因摩擦太小走路就很困难,且易滑倒,汽车的车轮也会出现空转,即车轮转动而车厢并不前进.所以,在某些情况下又必须设法增大摩擦,如在太滑的路上撒上一些炉灰或沙土,车轮上加挂防滑链等.3.〔个人或党派团体间〕因彼此厉害矛盾而引起的冲突.|| 也作磨擦.摩擦种类摩擦的类别很多,按摩擦副的运动形式摩擦分为滑动摩擦和滚动摩擦,前者是两相互接触物体有相对滑动或有相对滑动趋势时的摩擦,后者是两相互接触物体有相对滚动或有相对滚动趋势时的摩擦;按摩擦副的运动状态摩擦分为静摩擦和动摩擦,前者是相互接触的两物体有相对运动趋势并处于静止临界状态时的摩擦,后者是相互接触的两物体越过静止临界状态而发生相对运动时的摩擦;按摩擦表面的润滑状态,摩擦可分为干摩擦、边界摩擦和流体摩擦.摩擦又可分为外摩擦和内摩擦.外摩擦是指两物体表面作相对运动时的摩擦;内摩擦是指物体内部分子间的摩擦.干摩擦和边界摩擦属外摩擦,流体摩擦属内摩擦.干摩擦摩擦副表面直接接触,没有润滑剂存在时的摩擦.常用库仑摩擦定律表达摩擦表面间的滑动摩擦力F、法向力N和摩擦系数f间的关系:f=F/N.钢对钢的f值在大气中约为0.15~0.20,洁净表面可达0.7~0.8.根据英国的F.P.鲍登等人的研究,极为洁净的金属〔表面上的气体用加热、电子轰击等方法排除〕在高真空度的实验条件下,表面接触处被咬死,f值可高达100.这种极为洁净的金属表面一旦与大气相接触便立即被污染或氧化,从而使f值显著下降.静摩擦的测定方法有倾斜法和牵引法.①倾斜法:把重力为N的欲测物体放在对偶材料的斜面上,逐渐增加斜面的倾角,测得物体开始滑动时的倾角θ<摩擦角>,由此求得摩擦系数f=tgθ.②牵引法:把重力为N 的欲测物体放在对偶材料的平面上,以力P牵引,物体开始滑动时的力F就是最大的静摩擦力〔此时F=P〕,由此求得摩擦系数f=F/N.接触面粗糙程度决定摩擦力大小动摩擦可在各类型试验机上〔如往复式摩擦磨损试验机、旋转圆盘-销式摩擦磨损试验机和四球式摩擦试验机〕测定,为此在试验机上装设测定摩擦力或摩擦力矩的机构,先测出摩擦力,而后换算出摩擦系数.常见的测量方法有杠杆法、弹簧法和电测法等.测定时需要确保清洁,否则会影响所测的摩擦力.边界摩擦和流体摩擦边界润滑状态下的摩擦称为边界摩擦.边界摩擦系数低于干摩擦系数.边界摩擦状态下的摩擦系数只取决于摩擦界面的性质和边界膜的结构形式,而与润滑剂的粘度无关.流体润滑状态下的摩擦称为流体摩擦.这种摩擦是流体粘性引起的.其摩擦系数较干摩擦和边界摩擦为低.。
- 1、下载文档前请自行甄别文档内容的完整性,平台不提供额外的编辑、内容补充、找答案等附加服务。
- 2、"仅部分预览"的文档,不可在线预览部分如存在完整性等问题,可反馈申请退款(可完整预览的文档不适用该条件!)。
- 3、如文档侵犯您的权益,请联系客服反馈,我们会尽快为您处理(人工客服工作时间:9:00-18:30)。
磨损及磨损机理第三章磨损及磨损机理概述物体摩擦表面上的物质,由于表面相对运动而不断损失的现象称磨损。
在一般正常工作状态下,磨损可分三个阶段:a.跑合(磨合)阶段:轻微的磨损,跑合是为正常运行创造条件。
b.稳定磨损阶段:磨损更轻微,磨损率低而稳定。
C.剧烈磨损阶段:磨损速度急剧增长,零件精度丧失,发生噪音和振动,摩擦温度迅速升高,说明零件即将失效。
(如图3.1)摩擦行程(时间)图3.1 磨损三个机件磨损是无法避免的。
但,如何缩短跑合期、延长稳定磨损阶段和推迟剧烈磨损的到来,是研究者致力的方向。
影响磨损的因素很多,例如相互作用表面的相对运动方式(滑动,滚动,往复运动,冲击),载荷与速度的大小,表面材料的种类,组织,机械性能和物理-化学性能等,各种表面处理工艺,表面几何性质(粗糙度,加工纹理和加工方法),环境条件(温度、湿度、真空度、辐射强度、和介质性质等)和工况条件(连续或间歇工作)等。
这些因素的相互影响对于磨损将产生或正或负的效果,从而使磨损过程更为复杂化。
磨损过程涉及到许多不同的学科领域,由于具有跨学科的性质,至今还很难将它的规律解释清楚。
已经有很多学者对磨损进行了大量的研究。
如20 世纪20 年代,汤林森提出了分子磨损的概念,他认为两个粗糙表面在接触摩擦过程中相互接近,而一个表面上的原子被另一个表面俘获的现象就是磨损。
霍尔姆在上述基础上作了进一步的发展,他指出摩擦材料的压缩屈服极限Ob(即硬度)对耐磨性的影响很大。
50年代初,奥贝尔(Oberle)从表层材料的机械破坏着眼,联系“切削”过程来解释磨损,他认为影响磨损的主要因素除硬度H 外,还有材料的弹性模量E。
处在弹性极限内的,变形越大,机械破坏越少,并提出用模数(m = E/H x 105)来反映材料的耐磨性,m 值高则耐磨性好。
冯(Feng)提出了机械性质相近的两表面上机械嵌锁作用导致界面上既粘连又犁削的观点。
布洛克但lok)认为软钢表面变得粗糙和发生塑性变形,是由于应力过高而引起的。
拉宾诺维奇认为表面能与材料硬度之比,对于磨损是一个重要因素,它可能影响磨屑的大小。
赫鲁晓夫提出了硬质微凸体在软表面上犁沟的模式图。
有不少学者通过实验和观测发现,磨损是比原子量级大得多的数量级,大规模地发生着。
拉宾诺维奇和阿查德(Archard) 分别指出,磨损颗粒大约具有如实际接触斑点直径那样的数量级。
拉宾诺维奇提出磨屑呈半球形,阿查德也认为磨屑具有一定的厚度。
在滑动或滚动过程中,表面微凸体反复承载而发生疲劳脱落的现象,有人把它看作是一种磨损,克拉盖尔斯基(Kpare夬》提出了形成磨屑的数学模式,木村好次(Kimura) 等人的观点也属于这一类。
苏(Suh)等人提出了由于应力重复作用和应变累积而引起材料转移的观点,他指出磨屑呈细片状而不是呈半球形,同时认为材料的整体性能(硬度)不是控制磨损的因素。
关于磨损现象的解释,不同的论点都从某一角度描述了磨损某一方面的状况。
还难以解释千变万化的磨损现象。
随着表面微观分析仪器及电子计算技术的发展,人们对磨损的研究也由宏观进入亚微观,进而进入微观研究;由静态到动态,由定性到定量。
但至今仍不能算很完善。
本章主要讨论金属材料的磨损,关于非金属材料的磨损问题将稍加讲解。
磨损的情况和程度,用磨损率来表示。
磨损率是指单位时间,单位滑动距离、单位作功,或每一转、每一次摆动中表面材料的磨损量。
磨损量可用质量,体积或厚度来度量。
3.1磨损类型关于磨损的分类也有各种观点。
这里采用伯韦尔(Burwell)的观点根据磨损机理的不同,把粘着磨损,磨粒磨损、腐蚀磨损和表面疲劳列为磨损的主要类型,而把表面侵蚀,冲蚀等列为次要类型。
这些不同类型的磨损,可以单独发生,相继发生或同时发生(为复合的磨损形式)。
3.1.1粘着磨损摩擦副相对运动时,由于接触点上的固相焊合,接触表面的材料从一个表面转移到另一个表面的现象称为粘着磨损。
①粘着磨损机理由摩擦的粘着理论可知,金属表面微凸体在法向载荷的作用下,当顶端压力达到屈服强度时,就会发生塑性变形而使接触面扩大,直到实际接触面积大到足以支承外载荷时。
相对滑动时,界面膜破裂,就会在接触处形成“冷焊”接点。
继续滑动又会将接点剪断,随后再形成新的接点。
在不断的剪断和形成新的接点的过程中,发生了金属磨损。
磨损量的大小取决于节点处被剪断的位置。
如剪切发生在界面上,则磨损轻微;如发生在界面以下,则会使金属从一个表面转移到另一个表面。
继续摩擦时,这部分转移物就可能成为磨屑。
如表面有污染膜,吸附膜等表面膜存在时,磨损轻微。
由于表面膜的抗剪强度较低,接触点处的表面膜很容易遭到破坏,使新鲜的金属表面得以暴露,加上摩擦热的影响,金属间形成了很强的粘着,运动时必须剪断这些金属粘着点,造成表面损伤,严重时甚至可以咬死。
综上所述,可以将粘着磨损的过程作如下的描述:接触——塑性变形——表面膜(包括油膜)破裂——粘着(冷焊)——剪断接点——再粘着的循环过程。
②粘着磨损的分类根据剪断位置的不同,表面损伤程度的不同,又可将粘着磨损分为以下几个等级(如表 3.1所列):表3.1粘着磨损的分类③粘着磨损规律a.阿杳德(Archard )的磨损量计算式他假设在一系列等高度,大小相仿的微凸体上形成磨屑(见图3.2)。
设单个微凸体的接触面积的半径为r,面积为n2,则所支承的载荷N i= a, • n2。
如滑动距离为一个直径长时,则剪断的半球状微凸体的体积ZQ=2/3nr (半个球的体积)。
设n为接触表面间的接触点数,则滑动了L这么长距离后的总磨损量为:L 二r 2 n L 2r 3所受的载荷为N , ^1—L 以上是假定每个接触的微凸体都被剪断而 形成磨屑(磨损量)。
而实际上尚有一个概率,Q =3£L 用系数k 来表示:Q kNw =-L 3叭如滑动距离L 设为1个单位长度,将单位长度的磨损量定义为磨损率式中:Q 总磨损量;N 法向载荷;L 滑动距离; Cb 材料的压缩屈服极限(硬度)。
根据以上结果,可以得出以下结论:Q 八 2丁33 上式, 则得:图3.2 阿查德的微⑴.磨损量与滑动距离成正比;⑵磨损量与法向载荷成正比,而与表观面积无关;⑶磨损量与较软材料的压缩屈服极限(硬度)成反比;⑷滑动速度大体上对磨损量没有影响。
但是实验证明,磨损量与法向载荷成正比只适用于法向载荷较小的情况下,当载荷大到接触面上平均压应力超过3 ob时,磨损会急剧增大。
另外很多实验也表明,速度对于各种材料的不同磨损类型都存在着一定的影响。
同时,阿查德的公式中没有说明表面膜对粘着磨损的影响,计算式中没有反应出表面几何性质、表面加工状况、磨合等因素的影响。
b. 吉________ 本(Yoshimoto 与筑添(Tsukizoe的计算式考虑到几何因素的影响,他们假定微凸体呈锥状。
锥底直径为图3.3 吉本-筑添的2r,高度不等,都具有相同的锥底角0O 与理想平滑的表面摩擦(见 图 3.3)O 他们的推导思路和方法与阿查德相同。
唯每此式中考虑了几何性质的因素— tg e,从 式中可以看出,当表面越光滑(e 越大),tg e 越 小,磨损量就越小。
经过试验证明,基本上与计 算值相符。
c 罗厄(Rowe )对阿杳德方程的修正 罗厄考虑了表面膜的影响,有表面膜存在时 金属直接接触的面积只是真实接触面积的一 ■- =Am ::: 1 部 Ar 分。
即1 2. Q =—r 3 h 。
h o = rtg v则: N = n ・;「b ・…r 2 Q 八 Q : 1 二 3tg 二r 3tg)1 N QL 6 H 总 磨损 个微凸体的形状为锥体: 3 2r 3 :式中:3称为表面膜分隔缺陷系数;A m金属直接接触的面积;A r真实接触面积(包括有表面膜分隔的面积)。
表面膜(包括kfN'i k 油膜)缺损多时,3趋向于1。
Q^HT A丄表示几乎全是金属直接接触。
阿查德的磨损量计算公式为:罗厄的修正kQ = § 厲 L = J Am L = J 卩厲 L 公式为:根据修正的粘着摩真实接触面积贝IQ =km 1亠仁:」2 L擦理论,式中:k m为概率系数,但与阿查德的k 数值不同,主要是考虑了表面膜及几何因素等;卩为摩擦系数;a由剪切力引起的接触面积增大系数,它满足以下关系:o2+ a f T= ob2a 压应力; T 表面膜的剪切强度; a 压缩屈服极限。
Q =k NL%将上 式写成:式中:k '被定义为磨损系数。
与接触产生 的概率、摩擦副的材料、几何性质、表面膜的破 损程度等因素有关。
N%从罗厄和阿查 德的公式中都有说明磨损量与法向载荷成正比,与较软材料的硬10 ■d.威尔士( Welsh )的研究度成反比。
这正好与粘着 摩擦理论相一致。
在罗厄 的修正公式中,包含了剪 切力的影响和表面膜的影响。
如表面膜损伤系数很小,则磨损量就会大大降 低。
110T * ■Iz 110-10XQ 1W 報荊[Nj图3.4 粘着磨考虑了温度的影响。
威尔士认为,随着载荷与滑动速度的改变,会引起摩擦表面温度的升 降,从而造成粘着磨损特征的明显变化(图3.4)⑴温度在T i 以下时,磨屑基本上是氧化物, 属于轻磨损;⑵温度超过T i ,进入严重磨损,特征是磨 屑由金属之间焊合后再剪断而产生的, 表明此时 表面上在轻载时建立的氧化膜破裂,磨损由亚表 层的塑性变形造成。
T i 是从轻微磨损到严重磨损 的转变点。
⑶当温度到达T 2后,由于表面温度相当高, 约有90%的塑性变形能转为热能。
如果这些热 保留在摩擦副中,则会出现高达 1000 C 的瞬现 温升(约在10-3s 内)。
这样的温度足够引起表面 层的相变(如出现“白层”结构)它将阻碍塑性 变形的发展,并能帮助建立氧化膜。
这时的磨损 率又显著下降。
⑷温度再升高到T 3,此时可使表面层迅速 变成硬化状态。
在表面上形成氧化层为主要反 应,而不发生金属转移。
所以磨损率又下降。
但他并没有解释为何 到更高温度时磨损率又向 上。
图3.5 磨损的转O■& 10>.严蛋磨扭e查尔德(Child)的研究他研究了载荷与速度对软钢-软钢无润滑条件下的磨损状态(见图3.5),表明磨损随工作条件的改变而发生转化。
⑴在低速低载荷范围(A区),金属表面发生硬化,并降低了粗糙度。
在氧化膜的保护下,磨损基本上属于氧化膜的机械磨损。
⑵速度和载荷稍高(B区),氧化膜有可能破裂而产生严重的金属转移及磨损。
⑶在更高的速度下(C区),由于摩擦热引起氧化及相变硬化,又恢复了氧化膜的保护作用。
⑷当速度再提高(D区),由于温度升高,严重的表面软化现象又可以引起严重磨损。
⑸速度再高(E区),则又出现氧化膜起主导作用的现象。
这两个试验表明了温度对磨损的重要作用。