第三章磨损及磨损机理
磨损及磨损理论

第一节 概 述
任何机器运转时,相互接触的零件之间都将因相对运动而产 生摩擦,而磨损正是由于摩擦产生的结果。由于磨损,将造成 表层材料的损耗,零件尺寸发生变化,直接影响了零件的使用 寿命。从材料学科特别是从材料的工程应用来看,人们更重视 研究材料的磨损。据不完全统计,世界能源的1/3~1/2消耗 于摩擦,而机械零件80%失效原因是磨损。
表表面面存存在在明明显显粘粘着着痕痕迹迹和和材材料料转转移移,,有有较较大大粘粘着着坑坑块,块在,高在速高重速 载重下载,下大,量大摩量擦摩热擦使热表使面表焊面合焊,合撕,脱撕后脱留后下留片下片片粘片着粘坑着。坑。
黏黏着着坑坑密密集集,,材材料料转转移移严严重重,,摩摩擦擦副副大大量量焊焊合合,,磨磨损急损剧急增剧加增,加, 摩摩擦擦副副相相对对运运动动受受到到阻阻碍碍或或停停止止。。 材材料料以以极极细细粒粒状状脱脱落落,,出出现现许许多多““豆豆斑斑””状状凹凹坑坑。。
所以磨损是机器最常见、最大量的一种失效方式。据调查轮,胎压联痕(SEM 邦德国在1974年钢铁工业中约有30亿马克花费在维修上,其5中000X) 直接由于磨损造成的损失占47%,停机修理所造成的损失与磨损 直接造成的损失相当,如果再加上后续工序的影响,其经济损失 还需加上10%一20%。
摩擦痕迹 (350X)
此时虽然摩擦系数增大,但是磨损却很小,材料迁移也不显著。通常 在金属表面具有氧化膜、硫化膜或其他涂层时发生轻微粘着摩损。
(2)涂抹:
粘着结合强度大于较软金属抗剪切强度,小于较硬金属抗剪切强度。 剪切破坏发生在离粘着结合面不远的较软金属浅层内,软金属涂抹在硬 金属表面。这种模式的摩擦系数与轻微磨损差不多,但磨损程度加剧。
(3)磨损比
《机械设计》第三节-摩擦-磨损-润滑
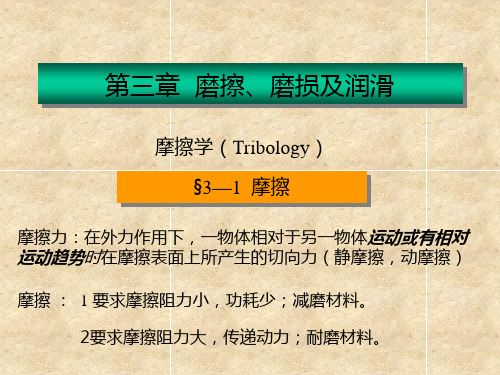
t
度不会继续改变,所占时
间比率较小
O
时间t
2、稳定磨损阶段
经磨合的摩擦表面加工硬化,形成了稳定的表面粗糙度,摩擦
条件保持相对稳定,磨损较缓,该段时间长短反映零件的寿命
3、急剧磨损阶段 经稳定磨损后,零件表面破坏,运动副间隙增大→动载振动
→润滑状态改变→温升↑→磨损速度急剧上升→直至零件失效
二、磨损的类型
弹性变形
流体摩擦(润滑)
塑性变形
边界膜
边界摩擦(润滑)—最低要求
边界膜 液体
液
混合摩擦(润滑)
边界膜
液体
一、干摩擦
摩擦理论: 库仑公式 Ff f () Fn
新理论:分子—机械理论、能量理论、粘着理论
简单粘着理论:
Ff
Ar B
Fn
sy
B
a
n
Ar Ari i 1
f () Ff B Fn sy
(3)条件粘度(相对粘度)—恩氏粘度
3、影响润滑油粘度的主要因素
(1)温度 润滑油的粘度随着温度的升高而降低
粘度指数VI ,35,85,110
(2)压力
p 0 ep
P>10MP时,随P↑→ηP↑
4、配油计算
K v vB vA vB
配油比
1、根据摩擦面间存在润滑剂的状况,滑动摩擦分
为哪几种? 2、获得流体动力润滑的基本条件是什么?
3、典型的磨损分哪三个阶段?磨损按机理分哪几 种类型?
4、什么是流体的粘性定律?
5、粘度的常用单位有哪些?影响粘度的主要因素是 什么?如何影响?
6、评价润滑脂和润滑油性能的指标各有哪几个?
润滑油压分布
v1
v2
机械系统中的摩擦与磨损机理分析
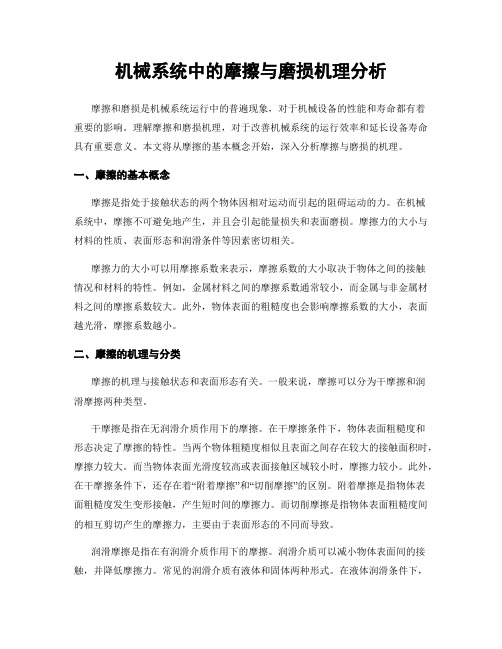
机械系统中的摩擦与磨损机理分析摩擦和磨损是机械系统运行中的普遍现象,对于机械设备的性能和寿命都有着重要的影响。
理解摩擦和磨损机理,对于改善机械系统的运行效率和延长设备寿命具有重要意义。
本文将从摩擦的基本概念开始,深入分析摩擦与磨损的机理。
一、摩擦的基本概念摩擦是指处于接触状态的两个物体因相对运动而引起的阻碍运动的力。
在机械系统中,摩擦不可避免地产生,并且会引起能量损失和表面磨损。
摩擦力的大小与材料的性质、表面形态和润滑条件等因素密切相关。
摩擦力的大小可以用摩擦系数来表示,摩擦系数的大小取决于物体之间的接触情况和材料的特性。
例如,金属材料之间的摩擦系数通常较小,而金属与非金属材料之间的摩擦系数较大。
此外,物体表面的粗糙度也会影响摩擦系数的大小,表面越光滑,摩擦系数越小。
二、摩擦的机理与分类摩擦的机理与接触状态和表面形态有关。
一般来说,摩擦可以分为干摩擦和润滑摩擦两种类型。
干摩擦是指在无润滑介质作用下的摩擦。
在干摩擦条件下,物体表面粗糙度和形态决定了摩擦的特性。
当两个物体粗糙度相似且表面之间存在较大的接触面积时,摩擦力较大。
而当物体表面光滑度较高或表面接触区域较小时,摩擦力较小。
此外,在干摩擦条件下,还存在着“附着摩擦”和“切削摩擦”的区别。
附着摩擦是指物体表面粗糙度发生变形接触,产生短时间的摩擦力。
而切削摩擦是指物体表面粗糙度间的相互剪切产生的摩擦力,主要由于表面形态的不同而导致。
润滑摩擦是指在有润滑介质作用下的摩擦。
润滑介质可以减小物体表面间的接触,并降低摩擦力。
常见的润滑介质有液体和固体两种形式。
在液体润滑条件下,摩擦系数较小,润滑膜的形成对减小摩擦力有重要作用。
而在固体润滑条件下,固体润滑剂填充物体表面间的空隙,减小物体之间的直接接触,从而减小摩擦力。
三、磨损的机理与分类磨损是指机械设备在长期运行过程中,表面材料的逐渐损失。
磨损的机理与摩擦密切相关。
常见的磨损形式有磨粒磨损、疲劳磨损和腐蚀磨损等。
7-材料磨损与耐磨材料(第3章粘着磨损)4详解
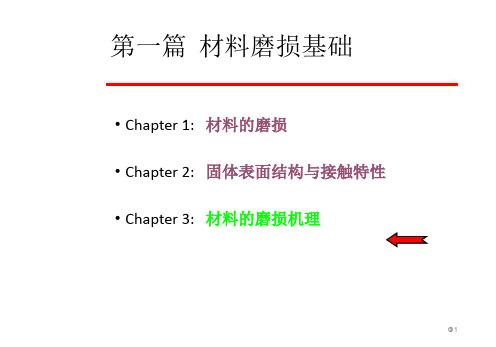
在以后的摩擦过程中,附着物碾转于对磨件的表面之 间,有些粘附物在反复的摩擦中可能由金属表面脱落下 来→磨屑。
9
§3.1.1 粘着磨损的概念
粘着磨损也称咬合(胶合)磨损。磨损产物通常呈小 颗粒状,从一物体表面粘附到另一个物体表面上,然 后在继续的摩擦过程中,表面层发生断裂,有时还发 生反粘附.即被粘附到另一个表面上的材料又回到原 来的表面上,这种粘附反粘附往往使材料以自由磨屑 状脱落下来。粘着磨损产物可以在任意的循环中形成。 粘着以后的断裂分离,并不一定在最初的接触表面产 生。
4
Chapter 3: 材料的磨损机理
图(d)为腐蚀磨损。它的主要特征是磨损表面有化 学反应膜或小麻点,但麻点比较光滑。磨损物为簿的 碎片或粉末,典型工件如船舶外壳、水力发电的水轮 机叶片等。
5
Chapter 3: 材料的磨损机理
• §3.1 • §3.2 • §3.3 • §3.4 • §3.5 • §3.6
10
§3.1 粘着磨损
• §3.1.1 粘着磨损的概念 • §3.1.2 粘着磨损一般规律 • §3.1.3 粘着磨损分类 • §3.1.4 粘着磨损表达式与定律 • §3.1.5 影响粘着磨损的因素
11
Hale Waihona Puke §3.1.2 粘着磨损一般规律
• 粘着磨损过程一般分为三个阶段: (1)跑合阶段亦称 磨合阶段(磨合磨损阶段); (2)稳定磨损阶段; (3)急 剧磨损阶段亦称破坏磨损阶段。如下图所示:
26
§3.1.3 粘着磨损分类
第一类胶合的相关因素: • 材料性能(表面物性、表面化性、表面力性);
• e.g.强度、塑性、韧性、氧化性等
第三章 模具失效形式及机理
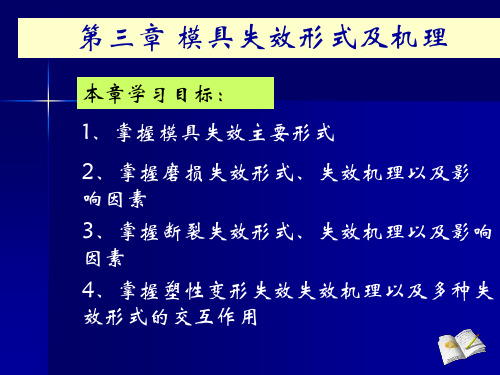
本章学习目标:
1、掌握模具失效主要形式
2、掌握磨损失效形式、失效机理以及影 响因素 3、掌握断裂失效形式、失效机理以及影响 因素 4、掌握塑性变形失效失效机理以及多种失 效形式的交互作用
模具的主要失效形式:
1.磨损失效 2.断裂失效 3.塑性变形失效
失效几率
早期失效
随机失效
图1-1 寿命特性曲线
耗损失效 使用时间
第一节 磨损失效
磨损:由于表面的相对运动,从接触表面 逐渐失去物质的现象。
磨损失效: 模具在服役时,与成形坯料接 触,产生相对运动,造成磨损。当该磨损使 模具的尺寸发生变化,或改变了模具的表面 状态使之不能继续服役时。
磨损的分类:
1.磨粒磨损(particle wear) 2.粘着磨损(adhesive wear) 3.疲劳磨损(fatigue wear) 4.气蚀和冲蚀磨损(cavitation erosion and wash-out wear)
图3-9 压力对磨损量的影响
d.磨粒尺寸与工件厚度的比值
工件厚度越大,磨粒越易嵌入工件,嵌入 越深,对模具的磨损越小。
磨粒 工件
( a) dm<t (b) dm=t (c) dm>t
图3-10 磨粒尺寸与工件厚度相对比值对磨损量的影响
提高耐磨粒磨损的措施 : a.提高模具材料的硬度 b.进行表面耐磨处理 c.采用防护措施
图3-8 相对硬度对磨损量的影响
当Hm=Ho时,如II区,为磨损软化状态, 此时的磨损率急剧增加,曲线上升很徒。
当Hm>Ho 时,如III区, 为严重磨损状 态,此时磨损 量较大,曲线 趋平。
图3-8 相对硬度对磨着模具与工件表面压力的增加,磨粒压入 模具的深度增加,磨损越严重。但当压力达到 一定值后,磨粒棱角变钝,磨损增加趋缓。
第三章 摩擦、磨损和润滑
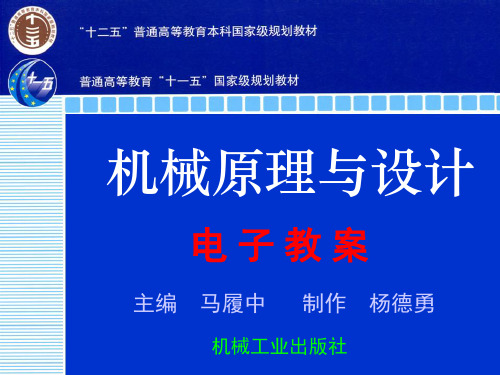
适当的润滑是减小摩擦、减轻磨损和降低能量消耗的有效手 段。
第一节 摩 擦
摩擦的种类 1)内摩擦:发生在物质内部,阻碍分子间相对运动的摩擦。 2)外摩擦:当相互接触的两个物体发生相对滑动或有相对滑
在液体摩擦状态下,其摩擦性能取决于流体内部分子之间的 粘滞阻力,故摩擦因数极小(约为0.001~0.008),是一种理想的 摩擦状态。摩擦规律也已有了根本的变化,与干摩擦完全不同。
四、混合摩擦
当两摩擦表面不能被具有压力的液体层完全分隔开,摩擦表 面间处于既有边界摩擦又有液体摩擦的混合状态称为混合摩擦。
边界膜有两大类:吸附膜和化学反应膜。吸附膜又分为物理 吸附膜与化学吸附膜。
物理吸附膜是由分子引力所 形成的。吸附膜吸附在金属表面 的模型如图2.3.4所示。
化学吸附膜是润滑油分子 以其化学键力作用在金属表面 形成保护膜,它的剪切强度与 抗粘着能力较低,但熔点较高 (约120°C)。所以,能在中等 速度及中等载荷下起润滑作用。
机械零件的磨损过程分为:磨合阶段、稳定磨损阶段和剧烈磨损 阶段。
按照磨损失效的机理,磨损主要有四种基本类型,即磨粒磨损、 粘着磨损、接触疲劳磨损和腐蚀磨损。
(1)磨粒磨损 外界进入摩擦表面间的硬质颗粒或摩擦表面上 的硬质凸峰,在摩擦过程中引起表面材料脱落的现象。特征是摩擦表 面沿着滑动方向形成划痕,在一些脆性材料上还会有崩碎和颗粒。
中心值列于表2.3.1。
此外,常用的还有比较法测定粘度,称为条件粘度(或相对粘 度)。我国常用的条件粘度为恩氏粘度,即在规定温度下200cm3的 油样流过恩氏粘度计的小孔(直径2.8 mm)所需时间(s)与同体积的 蒸馏水在20°C下流过相同小孔时间的比值即为该油样的恩氏粘度, 以符号°Et表示,其角标t表示测定时的温度。美国常用赛氏通用 秒(SUS),英国常用雷氏秒(R)作为条件湿或吸附于金属摩擦表面 形成边界膜的性能称为油性。吸附能力强,则愈有利于边界油膜的 形成,油性愈好。
机械运动中的摩擦与磨损分析
机械运动中的摩擦与磨损分析一、引言机械运动中的摩擦与磨损是一个广泛存在于各类设备与机械系统中的问题。
摩擦与磨损不仅会降低机械设备的效率,还会导致设备寿命的缩短,甚至引发设备故障。
因此,对于机械运动中的摩擦与磨损进行深入分析与研究具有重要意义。
二、摩擦与磨损的概念及影响因素1. 摩擦是指两个固体在接触表面上相互抵抗相对运动的力。
摩擦力的大小与接触面的粗糙度、物体质地以及表面润滑状况等因素相关。
2. 磨损是指固体表面因摩擦力或其他力的作用而磨掉一部分材料的现象。
磨损也与材料的硬度、接触面的负荷和速度等因素密切相关。
三、摩擦与磨损的分类与机理1. 滑动摩擦与磨损:两个物体表面在相对滑动时发生的摩擦和磨损。
滑动摩擦和磨损的机理主要是表面间的摩擦力和相互作用力集中在局部点上,使材料发生破坏。
2. 滚动摩擦与磨损:当两个物体在相互滚动时,由于接触点的轮廓不断改变,从而形成滚动摩擦,并引起表面磨损。
四、摩擦与磨损的预防与控制方法1. 优化设计:通过合理的材料选择、表面润滑处理以及接触面的几何形状设计,最小化摩擦与磨损的产生。
2. 润滑剂的使用:使用润滑剂可以减少物体表面之间的直接接触,从而降低摩擦和磨损。
润滑剂的选择应根据具体情况进行,常见的润滑方式包括干润滑、液体润滑和固体润滑等。
3. 表面处理技术:通过表面镀覆、喷涂、化学处理等方式对接触表面进行改性,提高表面的硬度、润滑性和抗磨性能。
4. 定期维护与保养:对机械设备进行定期保养和维护,及时更换磨损部件,增加机械运行的可靠性和寿命。
五、摩擦与磨损的测量和评估方法1. 摩擦力的测量:可以通过力传感器、压电传感器等装置来测量物体之间的摩擦力大小。
2. 磨损量的评估:可以通过测量设备表面的几何形状变化、重量损失、材料组织的变化等指标来评估磨损量。
六、案例分析:汽车发动机摩擦与磨损问题以汽车发动机为例,介绍摩擦与磨损在工程中的应用。
在发动机中,摩擦与磨损是一个重要的研究方向。
磨损的类型磨损机理表面疲劳磨损形成及影响因素
磨损的类型磨损机理表面疲劳磨损形成及影响因素磨损实际是接触表面随着时间增加和载荷作用损伤的累积过程。
自然界中不论机械零件,还是人造关节都存在着磨损。
可以说,磨损无处不在。
它直接影响着机器的运转精度和寿命。
据统计,每年全世界生产总值的近五分之二被摩擦磨损消耗掉了。
因此,开展系统的摩擦学设计,尽量减少或消除磨损,对人类具有重大意义。
前苏联学者进一步较全面地提出了区分磨损类别的方法。
他将磨损分为三个过程,依次为表面的相互作用两体摩擦表面的相互作用可以是机械的或分子的。
机械作用包括弹性变形、塑性变形和犁沟效应,可以是两体表面的粗糙峰直接啮合引起的,也可以是夹在中间的外界磨粒造成的。
表面分子的作用包括相互吸引和粘着,前者作用力小于后者。
表面层的变化在表面摩擦的作用下,表面层将发生机械的,组织结构的及物理的和化学的变化,这是由于表面变形、摩擦温度和环境介质等因素的影响造成的。
表面层的塑性变形会使金属冷作硬化而变脆,反复的弹性变形会使金属出现疲劳破坏。
摩擦热引起的表面接触高温可以使表层金属退火软化,而接触后急剧冷却将导致再结晶或固溶体分解。
外界环境的影响主要表现为介质在表层的扩散,包括氧化和其他化学腐蚀作用,因而会改变金属表面层的组织结构。
表面层的破坏形式有擦伤、点蚀、剥落、胶合、微观磨损。
近年来的研究普遍认为, 按照不同的机理对磨损来进行分类是比较恰当的。
通常可将磨损划分为个基本类型粘着磨损、磨粒磨损、表面疲劳磨损和腐蚀磨损。
虽然这种分类还不十分完善, 但概括了各种常见的磨损形式。
磨损机理通常从机理上可以把磨损分为粘着磨损,磨粒磨损,表面疲劳磨损,侵蚀磨损,腐蚀磨损和热磨损等。
粘着磨损相对运动的表面因存在分子间的吸引而在表面的微观接触处产生粘着作用,当粘着作用的强度大于材料内部的联接强度时,经过一定周期的接触就会产生磨损。
粘着磨损的磨损度常常是压力的函数,低压软表面或高压下都会产生严重的粘着磨损。
对于可以认为是同类材料的摩擦副表面,磨损常数趋于较大值,因为粘着作用的实质是原子或分子间产生了融合。
磨损及磨损理论
,
汇报人:
目录
01 添 加 目 录 项 标 题
02 磨 损 的 基 本 概 念
03 磨 损 理 论
04 磨 损 的 预 防 与 控 制
05 磨 损 的 检 测 与 评 定
Prt One
单击添加章节标题
Prt Two
磨损的基本概念
磨损的定义
磨损:物体表面在相对运动过程中产生的损耗和破坏 磨损类型:包括磨粒磨损、粘着磨损、腐蚀磨损、疲劳磨损等 磨损过程:包括初始阶段、稳定阶段、加速阶段和结束阶段 磨损影响因素:包括载荷、速度、温度、润滑、材料等
润滑:润滑不良会导致磨 损加剧
材料:材料的硬度、韧性 和耐磨性对磨损有直接影 响
环境:温度、湿度、腐蚀 性气体等环境因素也会影 响磨损
Prt Three
磨损理论
粘着磨损理论
粘着磨损是指两个接触表面 在相对滑动过程中由于粘着 作用而产生的磨损
粘着磨损理论是研究粘着磨 损现象的理论
粘着磨损理论主要包括粘着 磨损机理、粘着磨损模型和
磨损量的应用:在机械设计、材料察
磨损类型:磨粒磨损、粘着磨损、腐蚀磨损等 磨损程度:轻微磨损、中度磨损、严重磨损等 磨损部位:表面磨损、内部磨损、边缘磨损等 磨损特征:颜色变化、表面粗糙度、尺寸变化等
磨损性能的评定
磨损检测方法:光学显微镜、电子显微镜、X射线衍射等 磨损评定标准:磨损量、磨损率、磨损寿命等 磨损性能指标:耐磨性、抗磨性、耐蚀性等 磨损机理研究:摩擦学、材料科学、表面工程等
磨粒磨损理论
磨粒磨损:由硬质 颗粒引起的磨损
磨粒来源:自然界 中的砂石、金属颗 粒等
磨损过程:磨粒与 材料表面接触、摩 擦、剥落
磨损后果:材料表 面磨损、疲劳、断 裂等
摩擦和磨损ppt课件
当摩擦表面的不平度的尖峰相互作用的各点发生粘着后,在相对滑动时, 材料从运动副的一个表面转移到另一个表面,故而形成粘着磨损。
严重的粘着磨损会造成运动副咬死,不能正常运转 。
影响因素: ①同类摩擦副材料比异类材料容易粘着,如钢件运动副的 相对运动; ②脆性材料比塑性材料的粘着能力高; ③在一定范围内,零 件的表面粗糙度愈小,抗粘着能力愈强。
机械基础
§1-3 摩擦和磨损
摩擦和磨损
1
§1-4 摩擦与磨损
摩擦和磨损是自然界和社会生活中普遍存在的现象。 有时人们利用它们有利的一面,如车辆行驶、带传动等是利用
摩擦作用,精加工中的磨削、抛光等是利用磨损的有用方面。 由于摩擦的存在造成了机器的磨损、发热和能量损耗。 据估计目前世界上约有30%~50%的能量消耗在各种形式的摩擦 中,约80%的机器是因为零件磨损而失效。
磨损会影响机器的精度,强敌工作的可靠性,甚至促使机器提前报废。
摩擦和磨损
8
§1-4 摩擦与磨损 1. 磨损过程
磨
损 量
Q
磨 合
稳定磨损
剧烈磨损
0 t2
t1
时间t
0~t1 :磨合阶段 t1~t2:稳定磨损阶段
t2~~:剧烈磨损阶段
摩擦和磨损
9
§1-4 摩擦与磨损
1. 磨损过程
(1)磨合阶段
在运转初期,摩擦副的接触面积较小,单位面积上的实际载荷较 大,磨损速度较快。随着磨合的进行,实际接触面积不断增大,磨损
因此,零件的磨损是决定机器使用寿命的主要因素。
摩擦和磨损
2
§1-4 摩擦与磨损
一、 摩擦
1. 定义:两物体的接触表面阻碍它们相对运动的机械阻力。 相互摩擦的两个物体称为摩擦副。
- 1、下载文档前请自行甄别文档内容的完整性,平台不提供额外的编辑、内容补充、找答案等附加服务。
- 2、"仅部分预览"的文档,不可在线预览部分如存在完整性等问题,可反馈申请退款(可完整预览的文档不适用该条件!)。
- 3、如文档侵犯您的权益,请联系客服反馈,我们会尽快为您处理(人工客服工作时间:9:00-18:30)。
第三章磨损及磨损机理概述物体摩擦表面上的物质,由于表面相对运动而不断损失的现象称磨损。
在一般正常工作状态下,磨损可分三个阶段:a.跑合(磨合)阶段:轻微的磨损,跑合是为正常运行创造条件。
b.稳定磨损阶段:磨损更轻微,磨损率低而稳定。
c.剧烈磨损阶段:磨损速度急剧增长,零件精度丧失,发生噪音和振动,摩擦温度迅速升高,说明零件即将失效。
(如图3.1)机件磨损是无法避免的。
但,如何缩短跑合期、延长稳定磨损阶段和推迟剧烈磨损的到来,是研究者致力的方向。
影响磨损的因素很多,例如相互作用表面的相对运动方式(滑动,滚动,往复运动,冲击),载荷与速度的大小,表面材料的种类,组织,机械性能和物理-化学性能等,各种表面处理工艺,表面几何性质(粗糙度,加工纹理和加工方法),环境条件(温度、湿度、真空度、辐射强度、和介质性质等)和工况条件(连续或间歇工作)等。
这些因素的相互影响对于磨损将产生或正或负的效果,从而使磨损过程更为复杂化。
磨损过程涉及到许多不同的学科领域,由于具有跨学科的性质,至今还很难将它的规律解释清楚。
已经有很多学者对磨损进行了大量的研究。
如20世纪20年代,汤林森提出了分子磨损的概念,他认为两个粗糙表面在接触摩擦过程中相互接近,而一个表面上的原子被另一个表面俘获的现象就是磨损。
霍尔姆在上述基础上作了进一步的发展,他指出摩擦材料的压缩屈服极限σb(即硬度)对耐磨性的影响很大。
50年代初,奥贝尔(Oberle)从表层材料的机械破坏着眼,联系“切削”过程来解释磨损,他认为影响磨损的主要因素除硬度H外,还有材料的弹性模量E。
处在弹性极限内的,变形越大,机械破坏越少,并提出用模数(m=E/H×105)来反映材料的耐磨性,m值高则耐磨性好。
冯(Feng)提出了机械性质相近的两表面上机械嵌锁作用导致界面上既粘连又犁削的观点。
布洛克(Blok)认为软钢表面变得粗糙和发生塑性变形,是由于应力过高而引起的。
拉宾诺维奇认为表面能与材料硬度之比,对于磨损是一个重要因素,它可能影响磨屑的大小。
赫鲁晓夫提出了硬质微凸体在软表面上犁沟的模式图。
有不少学者通过实验和观测发现,磨损是比原子量级大得多的数量级,大规模地发生着。
拉宾诺维奇和阿查德(Archard)分别指出,磨损颗粒大约具有如实际接触斑点直径那样的数量级。
拉宾诺维奇提出磨屑呈半球形,阿查德也认为磨屑具有一定的厚度。
在滑动或滚动过程中,表面微凸体反复承载而发生疲劳脱落的现象,有人把它看作是一种磨损,克拉盖尔斯基(Крагельский)提出了形成磨屑的数学模式,木村好次(Kimura)等人的观点也属于这一类。
苏(Suh)等人提出了由于应力重复作用和应变累积而引起材料转移的观点,他指出磨屑呈细片状而不是呈半球形,同时认为材料的整体性能(硬度)不是控制磨损的因素。
关于磨损现象的解释,不同的论点都从某一角度描述了磨损某一方面的状况。
还难以解释千变万化的磨损现象。
随着表面微观分析仪器及电子计算技术的发展,人们对磨损的研究也由宏观进入亚微观,进而进入微观研究;由静态到动态,由定性到定量。
但至今仍不能算很完善。
本章主要讨论金属材料的磨损,关于非金属材料的磨损问题将稍加讲解。
磨损的情况和程度,用磨损率来表示。
磨损率是指单位时间,单位滑动距离、单位作功,或每一转、每一次摆动中表面材料的磨损量。
磨损量可用质量,体积或厚度来度量。
3.1磨损类型关于磨损的分类也有各种观点。
这里采用伯韦尔(Burwell)的观点根据磨损机理的不同,把粘着磨损,磨粒磨损、腐蚀磨损和表面疲劳列为磨损的主要类型,而把表面侵蚀,冲蚀等列为次要类型。
这些不同类型的磨损,可以单独发生,相继发生或同时发生(为复合的磨损形式)。
3.1.1粘着磨损摩擦副相对运动时,由于接触点上的固相焊合,接触表面的材料从一个表面转移到另一个表面的现象称为粘着磨损。
①粘着磨损机理由摩擦的粘着理论可知,金属表面微凸体在法向载荷的作用下,当顶端压力达到屈服强度时,就会发生塑性变形而使接触面扩大,直到实际接触面积大到足以支承外载荷时。
相对滑动时,界面膜破裂,就会在接触处形成“冷焊”接点。
继续滑动又会将接点剪断,随后再形成新的接点。
在不断的剪断和形成新的接点的过程中,发生了金属磨损。
磨损量的大小取决于节点处被剪断的位置。
如剪切发生在界面上,则磨损轻微;如发生在界面以下,则会使金属从一个表面转移到另一个表面。
继续摩擦时,这部分转移物就可能成为磨屑。
如表面有污染膜,吸附膜等表面膜存在时,磨损轻微。
由于表面膜的抗剪强度较低,接触点处的表面膜很容易遭到破坏,使新鲜的金属表面得以暴露,加上摩擦热的影响,金属间形成了很强的粘着,运动时必须剪断这些金属粘着点,造成表面损伤,严重时甚至可以咬死。
综上所述,可以将粘着磨损的过程作如下的描述:接触——塑性变形——表面膜(包括油膜)破裂——粘着(冷焊)——剪断接点——再粘着的循环过程。
②粘着磨损的分类根据剪断位置的不同,表面损伤程度的不同,又可将粘着磨损分为以下几个等级(如表3.1所列):表3.1 粘着磨损的分类类别 破坏现象损坏原因轻微磨损 剪切破坏发生在粘着结合面上,表面转移的材料极轻微粘着结合处强度比摩擦副的两基体金属都弱涂抹剪切破坏发生在离粘着结合面不远的较软金属浅层内,软金属涂抹在硬金属表面粘着结合处强度大于较软金属的剪切强度擦伤 剪切破坏主要发生在较软金属的亚表层内;有时硬金属亚表面也有划痕 粘着结合处强度比两金属基体都高,转移到硬面上的粘着物质又拉削软金属表面撕脱(深掘)剪切破坏发生在摩擦副一方或两方金属较深处粘着结合处强度大于任一基体的剪切强度,剪切应力高于粘着结合强度咬死摩擦副之间咬死,不能相对运动粘着结合处强度比任一基体金属的剪切强度都高,而且粘着区域大,剪切应力低于粘着结合强度③粘着磨损规律a.阿查德(Archard )的磨损量计算式他假设在一系列等高度,大小相仿的微凸体上形成磨屑(见图3.2)。
设单个微凸体的接触面积的半径为r ,面积为πr 2,则所支承的载荷N i =σb ·πr 2。
如滑动距离为一个直径长时,则剪断的半球状微凸体的体积ΔQ=2/3πr 3(半个球的体积)。
设n 为接触表面间的接触点数,则滑动了L 这么长距离后的总磨损量为:所受的载荷为N ,将Lr n r L r Q 323223ππ=•=∑2r n N b πσ••=L NQ bσ31=图3.2 阿查德的微凸体相遇模式代入上式,则得:以上是假定每个接触的微凸体都被剪断而形成磨屑(磨损量)。
而实际上尚有一个概率,用系数k 来表示:如滑动距离L 设为1个单位长度,将单位长度的磨损量定义为磨损率式中:Q 总磨损量; N 法向载荷; L 滑动距离; σb 材料的压缩屈服极限(硬度)。
根据以上结果,可以得出以下结论: ⑴.磨损量与滑动距离成正比;⑵磨损量与法向载荷成正比,而与表观面积无关; ⑶磨损量与较软材料的压缩屈服极限(硬度)成反比; ⑷滑动速度大体上对磨损量没有影响。
但是实验证明,磨损量与法向载荷成正比只适用于法向载荷较小的情况下,当载荷大到接触面上平均压应力超过3σb 时,磨损会急剧增大。
另外很多实验也表明,速度对于各种材料的不同磨损类型都存在着一定的影响。
同时,阿查德的公式中没有说明表面膜对粘着磨损的影响,计算式中没有反应出表面几何性质、表面加工状况、磨合等因素的影响。
L Nk Q bσ3=bN k L Q w σ3==b.吉本(Yoshimoto )与筑添(Tsukizoe )的计算式考虑到几何因素的影响,他们假定微凸体呈锥状。
锥底直径为2r ,高度不等,都具有相同的锥底角θ。
与理想平滑的表面摩擦(见图3.3)。
他们的推导思路和方法与阿查德相同。
唯每个微凸体的形状为锥体:则:总磨损量此式中考虑了几何性质的因素——tg θ,从式中可以看出,当表面越光滑(θ越大), tg θ越小,磨损量就越小。
经过试验证明,基本上与计算值相符。
c.罗厄(Rowe )对阿查德方程的修正罗厄考虑了表面膜的影响,有表面膜存在时金属直接接触的面积只是真实接触面积的一 部分。
即图3.3 吉本-筑添的表面接触模型N231h r Q π=∆θrtg h =0θπtg r Q 331=∆L Ntg Q bσθ61=1<=rmA A β2r n N b πσ••=θπθπtg r r L tg r n Q Q 3331231==∆=∑式中:β 称为表面膜分隔缺陷系数;A m 金属直接接触的面积;A r 真实接触面积(包括有表面膜分隔的面积)。
表面膜(包括油膜)缺损多时,β趋向于1。
表示几乎全是金属直接接触。
阿查德的磨损量计算公式为:罗厄的修正公式为:根据修正的粘着摩擦理论,真实接触面积 则式中:k m 为概率系数,但与阿查德的k 数值不同,主要是考虑了表面膜及几何因素等;μ 为摩擦系数;α 由剪切力引起的接触面积增大系数,它满足以下关系:σ2+ατf 2=σb 2 σ 压应力; τf 表面膜的剪切强度; σb 压缩屈服极限。
将上式写成:式中:k ’ 被定义为磨损系数。
与接触产生的概率、摩擦副的材料、几何性质、表面膜L A k L A k L A kQ r m m m r β===3()2121αμσ+=br NA ()LNk Q bm 2121αμσβ+=bNLk Q σ'=L A kL Nk Q r b 33=⎪⎪⎭⎫⎝⎛=σ的破损程度等因素有关。
从罗厄和阿查德的公式中都有说明磨损量与法向载荷成正比,与较软材料的硬度成反比。
这正好与粘着摩擦理论相一致。
在罗厄的修正公式中,包含了剪切力的影响和表面膜的影响。
如表面膜损伤系数很小,则磨损量就会大大降低。
d.威尔士(Welsh )的研究考虑了温度的影响。
威尔士认为,随着载荷与滑动速度的改变,会引起摩擦表面温度的升降,从而造成粘着磨损特征的明显变化(图3.4)。
⑴温度在T 1以下时,磨屑基本上是氧化物,属于轻磨损;⑵温度超过T 1,进入严重磨损,特征是磨屑由金属之间焊合后再剪断而产生的,表明此时表面上在轻载时建立的氧化膜破裂,磨损由亚表层的塑性变形造成。
T 1是从轻微磨损到严重磨损的转变点。
⑶当温度到达T 2后,由于表面温度相当高,约有90%的塑性变形能转为热能。
如果这些热保留在摩擦副中,则会出现高达1000℃的瞬现温升(约在10-3s 内)。
这样的温度足够引起表面层的相变(如出现“白层”结构)它将阻碍塑性变形的发展,并能帮助建立氧化膜。
这时的磨损率又显著下降。
⑷温度再升高到T 3,此时可使表面层迅速变成硬化状态。
在表面上形成氧化层为主要bN图3.4 粘着磨损的特征反应,而不发生金属转移。
所以磨损率又下降。
但他并没有解释为何到更高温度时磨损率又向上。