磨损及磨损原理-第二讲分析
磨损及磨损机理

磨损及磨损机理第三章磨损及磨损机理概述物体摩擦表面上的物质,由于表面相对运动而不断损失的现象称磨损。
在一般正常工作状态下,磨损可分三个阶段:a.跑合(磨合)阶段:轻微的磨损,跑合是为正常运行创造条件。
b.稳定磨损阶段:磨损更轻微,磨损率低而稳定。
C.剧烈磨损阶段:磨损速度急剧增长,零件精度丧失,发生噪音和振动,摩擦温度迅速升高,说明零件即将失效。
(如图3.1)摩擦行程(时间)图3.1 磨损三个机件磨损是无法避免的。
但,如何缩短跑合期、延长稳定磨损阶段和推迟剧烈磨损的到来,是研究者致力的方向。
影响磨损的因素很多,例如相互作用表面的相对运动方式(滑动,滚动,往复运动,冲击),载荷与速度的大小,表面材料的种类,组织,机械性能和物理-化学性能等,各种表面处理工艺,表面几何性质(粗糙度,加工纹理和加工方法),环境条件(温度、湿度、真空度、辐射强度、和介质性质等)和工况条件(连续或间歇工作)等。
这些因素的相互影响对于磨损将产生或正或负的效果,从而使磨损过程更为复杂化。
磨损过程涉及到许多不同的学科领域,由于具有跨学科的性质,至今还很难将它的规律解释清楚。
已经有很多学者对磨损进行了大量的研究。
如20 世纪20 年代,汤林森提出了分子磨损的概念,他认为两个粗糙表面在接触摩擦过程中相互接近,而一个表面上的原子被另一个表面俘获的现象就是磨损。
霍尔姆在上述基础上作了进一步的发展,他指出摩擦材料的压缩屈服极限Ob(即硬度)对耐磨性的影响很大。
50年代初,奥贝尔(Oberle)从表层材料的机械破坏着眼,联系“切削”过程来解释磨损,他认为影响磨损的主要因素除硬度H 外,还有材料的弹性模量E。
处在弹性极限内的,变形越大,机械破坏越少,并提出用模数(m = E/H x 105)来反映材料的耐磨性,m 值高则耐磨性好。
冯(Feng)提出了机械性质相近的两表面上机械嵌锁作用导致界面上既粘连又犁削的观点。
布洛克但lok)认为软钢表面变得粗糙和发生塑性变形,是由于应力过高而引起的。
磨损及磨损理论

第一节 概 述
任何机器运转时,相互接触的零件之间都将因相对运动而产 生摩擦,而磨损正是由于摩擦产生的结果。由于磨损,将造成 表层材料的损耗,零件尺寸发生变化,直接影响了零件的使用 寿命。从材料学科特别是从材料的工程应用来看,人们更重视 研究材料的磨损。据不完全统计,世界能源的1/3~1/2消耗 于摩擦,而机械零件80%失效原因是磨损。
表表面面存存在在明明显显粘粘着着痕痕迹迹和和材材料料转转移移,,有有较较大大粘粘着着坑坑块,块在,高在速高重速 载重下载,下大,量大摩量擦摩热擦使热表使面表焊面合焊,合撕,脱撕后脱留后下留片下片片粘片着粘坑着。坑。
黏黏着着坑坑密密集集,,材材料料转转移移严严重重,,摩摩擦擦副副大大量量焊焊合合,,磨磨损急损剧急增剧加增,加, 摩摩擦擦副副相相对对运运动动受受到到阻阻碍碍或或停停止止。。 材材料料以以极极细细粒粒状状脱脱落落,,出出现现许许多多““豆豆斑斑””状状凹凹坑坑。。
所以磨损是机器最常见、最大量的一种失效方式。据调查轮,胎压联痕(SEM 邦德国在1974年钢铁工业中约有30亿马克花费在维修上,其5中000X) 直接由于磨损造成的损失占47%,停机修理所造成的损失与磨损 直接造成的损失相当,如果再加上后续工序的影响,其经济损失 还需加上10%一20%。
摩擦痕迹 (350X)
此时虽然摩擦系数增大,但是磨损却很小,材料迁移也不显著。通常 在金属表面具有氧化膜、硫化膜或其他涂层时发生轻微粘着摩损。
(2)涂抹:
粘着结合强度大于较软金属抗剪切强度,小于较硬金属抗剪切强度。 剪切破坏发生在离粘着结合面不远的较软金属浅层内,软金属涂抹在硬 金属表面。这种模式的摩擦系数与轻微磨损差不多,但磨损程度加剧。
(3)磨损比
磨损机理
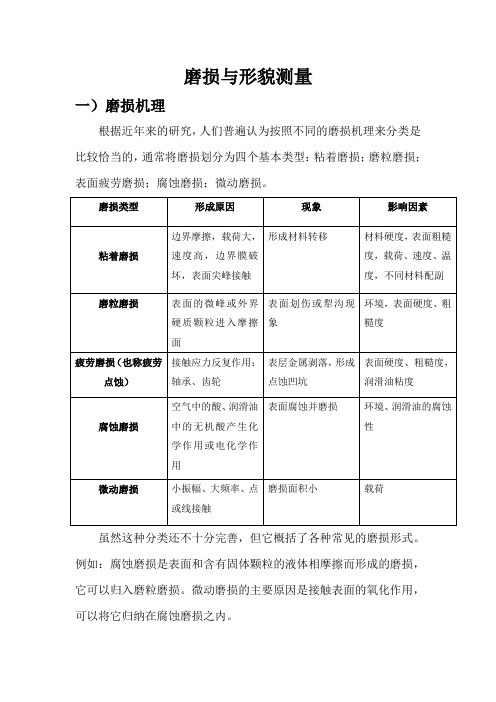
磨损与形貌测量一)磨损机理根据近年来的研究,人们普遍认为按照不同的磨损机理来分类是比较恰当的,通常将磨损划分为四个基本类型:粘着磨损;磨粒磨损;表面疲劳磨损;腐蚀磨损;微动磨损。
虽然这种分类还不十分完善,但它概括了各种常见的磨损形式。
例如:腐蚀磨损是表面和含有固体颗粒的液体相摩擦而形成的磨损,它可以归入磨粒磨损。
微动磨损的主要原因是接触表面的氧化作用,可以将它归纳在腐蚀磨损之内。
还应当指出:在实际的磨损现象中,通常是几种形式的磨损同时存在,而且一种磨损发生后住住诱发其它形式的磨损。
例如疲劳磨损的磨屑会导致磨粒磨损,而磨粒磨损所形成的新净表面又将引起腐蚀或粘着磨损微动磨损就是一种典型的复合磨损。
在微动磨损过程中,可能出现粘着磨损、氧化磨损、磨粒磨损和疲劳磨损等多种磨损形式。
随着工况条件的变化,不同形式磨损的主次不同。
二)典型的磨损过程(三阶段)1、磨合磨损过程在一定载荷作用下形成一个稳定的表面粗糙度,且在以后过程中,此粗糙度不会继续改变,所占时间比率较小。
2、稳定磨损阶段经磨合的摩擦表面加工硬化,形成了稳定的表面粗糙度,摩擦条件保持相对稳定,磨损较缓,该段时间长短反映零件的寿命。
3、剧烈磨损阶段经稳定磨损后,零件表面破坏,运动副间隙增大→动载、振动→润滑状态改变→温升↑→磨损速度急剧上升→直至零件失效。
三)摩擦表面的形态分析由于摩擦现象发生在表面层,表层组织结构的变化是研究摩擦磨损规律和机理的关键,现代表面测试技术已先后用来研究摩擦表面的各种现象。
1、摩擦磨损表面形貌的分析摩擦过程中表面形貌的变化可以采用表面轮廓仪和电子显微镜来进行分析。
表面轮廓仪是通过测量触针在表面上匀速移动,将触针随表面轮廓的垂直运动检测、放大,并且描绘出表面的轮廓曲线。
再经过微处理机的运算还可以直接测出表面形貌参数的变化。
目前常用的表面微观形貌分析设备为扫描电子显微镜。
电子扫描的图像清晰度好,并有立体感,放大倍数变化范围宽(20-20000倍),检测范围亦较大。
橡胶摩擦及磨损分析

橡胶摩擦及磨损分析橡胶是非常重要且用量很大的工业材料之一,据不完全统计,2000年我国橡胶总消耗量将达220万吨,摩擦学性能是橡胶制品的一项非常重要的指标,例如橡胶轮胎的耐磨性能、刹车性能和行车效率、密封件的耐磨性等。
提高橡胶制品的耐磨性和使用寿命,可以在节约能源、材料、润滑剂等方面带来相当可观的经济效益和社会效益。
橡胶是一种弹性模量很低、粘弹性很高的材料,因此橡胶的摩擦具有不同于金属和一般聚合物的特征。
橡胶与刚性表面在滑动接触界面上的相互作用力包括粘着和滞后两项,而其摩擦力也正是由这两部分组成:F = Fa + Fh式中Fa ——粘着摩擦力,Fh——滞后摩擦力。
粘着摩擦起因于橡胶与对偶面之间粘着的不断形成和破坏,滞后摩擦则是由表面微凸体使滑动橡胶块产生周期性变形过程中能量的耗散引起的。
当橡胶在坚硬光滑的表面上滑动时,摩擦力主要表现为粘着摩擦,根据弹性体摩擦的粘着理论,可以得出粘着摩擦力Fa为[6]:F a = K1S( E r/p r) tanδ (r<1)式中,K1——常数;S——滑动界面的有效剪切强度;p——正压力;E——储能模量;tanδ——损耗角正切(粘弹性参数)。
显然,橡胶的粘着摩擦与材料的损耗角正切tanδ成正比。
润滑剂的存在可以阻止橡胶与对偶间的直接接触,使粘着摩擦成分大大降低,滞后摩擦起主要作用。
根据弹性体滞后摩擦的松弛理论,可得出滞后摩擦力为[6]:F h = K2( p/E′) n tanδ (n≥1)式中,K2为与几何形状因子有关的常数。
滞后摩擦力也与tanδ成正比,所不同的是,滞后摩擦力与变形程度因子( p/E′) n成正比。
由此,橡胶的摩擦力可表示为F=[K1S(E′/p r)+K2(p/E′)n]tanδ金属和塑料磨损表面的特征是磨痕与摩擦方向平行,而橡胶磨损表面的磨痕却垂直于摩擦方向,并且磨痕在橡胶表面形成山脊状突起,突起之间间距相等,高度相同,形成所谓的磨损斑纹。
第二章-摩擦、磨损及润滑
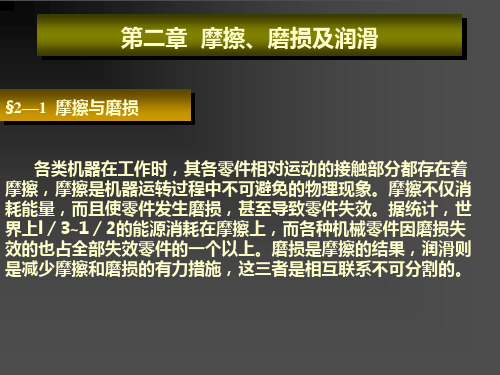
3、表面疲劳磨损
两摩擦表面为点或线接触时、由于局部的弹性变 形形成了小的接触区。这些小的接触区形成的摩擦副 如果受变化接触应力的作用,则在其反复作用下,表 层将产生裂纹。随着裂纹的扩展与相互连接,表层金 属脱落,形成许多月牙形的浅坑,这种现象称为疲劳 磨损,也称点蚀。
R2
p 弹性流体动力
润滑油压分布
赫兹压力分布
v1
x O
v2 缩颈
节流间隙 (油膜厚度)
3、流体静力润滑
油腔 节流器
(补偿元件) 油泵
油箱
四、润滑方法和润滑装置
油润滑的方法多种多样,其分类标准大概有两种:集中润滑 或分散润滑。
分散润滑比集中润滑简便。集中润滑需要一个多出口的润滑 装置供油,而分散润滑中各摩擦剔的润滑装置则是各自独立的。
4)闪点和燃点 5)极压性能
3)凝点 6)氧化稳定性
2、润滑脂 钙基润滑脂、钠基润滑脂、锂基润滑脂
性能指标:
1)针入度
2)滴点
3)安定性
3、固体润滑剂 石墨、二硫化钼、氮化硼 、蜡、 聚氟乙烯、 酚醛树脂
4、润滑剂的添加
二、粘性定律与润滑油的粘度
1、粘性定律
u
y
u=v O
牛顿粘性定律 η——流体的动力粘度
(1)O型密封圈 (2)V型密封圈 (3)Y型和U型密封圈 (4)L型密封圈
三、密封装置的选择
1.静密封较为简单,可根据压力、温度选择不同材料的垫片、 密封胶等
2.回转运动密封装置较多,要根据工作速度、压力大小、温度高低 选择。使用较普遍的是O型、J型密封圈,低速时毡圈应用较广。
航空发动机磨损机理分析及寿命评估

航空发动机磨损机理分析及寿命评估航空发动机是飞机的心脏,负责为飞机提供动力。
然而,随着使用时间的增长和使用次数的增多,航空发动机的磨损会逐渐加剧,从而影响其性能和寿命。
因此,了解航空发动机磨损的机理,并评估其寿命,对于确保飞机的安全和可靠性具有重要意义。
一、航空发动机磨损机理分析1.磨损的概念磨损是指在接触面上由于相对运动而导致的材料表面物质的逐渐丧失。
在航空发动机中,磨损是由于高温、高速、高压、腐蚀等因素的作用,导致材料表面的微小颗粒逐渐脱落而形成。
2.磨损的分类根据磨损形式的不同,磨损可以分为以下几种类型:(1)磨粒磨损:由于常温下颗粒杂质或高温下氧化产物的存在,使工作表面与磨料之间产生碰撞和磨擦,从而引起被磨损部分的材料脱落。
(2)表面疲劳磨损:在高速、高频率的疲劳循环作用下,工作表面出现因微小裂纹逐渐扩展引起的磨损。
(3)腐蚀磨损:由于化学介质的作用,使材料表面出现腐蚀,导致材料的表面产生颗粒状脱落,引起磨损。
3.磨损机理在航空发动机中,磨损主要是由于以下因素的共同作用所引起的:(1)高速、高温、高压的气流对叶片等工作表面的冲蚀作用。
(2)燃烧产物对高压涡轮和热门结构材料的腐蚀作用。
(3)磨损颗粒的积累和覆盖。
(4)机械振动和冲击、疲劳循环等。
4.磨损形态航空发动机中常见的磨损形态有以下几种:(1)划痕:指叶片和盘根等工作表面的表面产生细微划痕,进一步加剧表面磨损情况。
(2)点蚀:指机械表面出现颗粒状的点蚀,容易引起裂纹的扩展。
(3)抛光:指工作表面因反复摩擦而使表面光滑度提高,进一步加剧表面磨损情况。
二、航空发动机寿命评估寿命评估是指对航空发动机进行寿命预测和寿命评估,旨在确保发动机长期安全、可靠地运行。
由于航空发动机的寿命评估受到多种因素的影响,因此需要采取一些先进的技术手段,如结构预测、时变可靠性评估、损伤容限和定期检查等。
1.结构预测结构预测是预测航空发动机各部件的寿命,并对各部件进行安排和调度。
刀具磨损原因及状况分析
刀具磨损原因及状况分析
(一)俱磨损的原因
于摩擦力的存在,加之金属切削过程中释放热能,被切金属层在刀具的切削刃和前刀面的推挤作用之下会铲生形,如此造成刀具滑移,从而变成切屑。
因刀具前刀面与切屑、具后面与工件已加工表面的摩擦,仍具在切削的过程中产生磨损。
高温同样在一定程度上影响了踌命:刀具在很高的切削温度下进行工作,刀刃材料容易变软,更加剧了俱切削部分的磨损。
当工件材料不同、切削用量不同时,具的磨损形式也不同。
(二)前刀面磨损
在使用刀具切削塑性材料时,刀具前面会因为切削厚度较大而受热量增加,励增大,刀具的前面被磨损,就会形成坑状磨损。
这些坑状磨损在切削过程中,逐渐加深变宽,并向刃方向扩展。
这样便容易导致崩刃。
所以,在切削塑性材料时,要刀具破损是在刀具的前面。
(三)后刀面磨损
反之,在切削塑性较低的材料时,切削深度较小,速度较低,具前面受的压励和摩擦不大.出现积屑瘤的可能性小。
这时刀具后面屿工件表面的摩擦较大,所以刀具的磨损主要在刀具后面。
切削脆性材料时,前面的温度不高,主要的磨损也在刀具的后面。
(四)前后共同磨损
进给量和切削速度都在中等时,俱会同时遭受前面的坑状磨损和主后面的磨损,共同造成崩刃。
第 1 页共 1 页。
磨损及磨损理论
由n个半径为a的相同微凸体承受。
则当材料产生塑性变形时,法向载荷W与较软材料
的屈服极限σs之间的关系:
(1)
当摩擦副产生相对滑动,且滑动时每个微凸体上产
生的磨屑为半球形,其体积为(2/3)πa3,则单位滑动
距离的总磨损量(即磨损率,通常用于判断材料磨损
的快慢程度)为:
b.三体磨粒磨损 外界磨粒移动于两摩擦表面之间, 类似于研磨 作用, 称为三体磨粒磨损。 通常三体磨损的磨粒与金属表面产生极高的接 触应力, 往往超过磨粒的压溃强度。这种压应 力使韧性金属的摩擦表面产生塑性变形或疲劳, 而脆性金属表面则发生脆裂或剥落。
② 按摩擦表面所受的应力和冲击的大小分为凿削
b.高应力碾碎式磨粒磨损
这类磨损的特点是应力高,磨料所受的应力超过 磨料的压碎强度,当磨料夹在两摩擦表面之间时, 局部产生很高的接触应力,这种压应力使韧性金 属的摩擦表面产生塑性变形或疲劳, 而脆性金属 表面则发生脆裂或剥落。 同时磨料不断被碾碎,被碾碎 的磨料颗粒呈多角形,擦伤金 属,在摩擦表面留下沟槽和凹 坑。 如矿石粉碎机的颚板、 轧碎机滚筒等表面的破坏。
** 接触-塑性变形-粘着-剪断粘着点-材料转移再粘着,循环不断进行,构成粘着磨损过程。
(3)四种典型的粘着磨损
根据粘着点的强度和破坏位置不同,粘着磨损有几 种不同的形式,从轻微磨损到破坏性严重的胶合 磨损。它们的磨损形式、摩擦系数和磨损度虽然 不同,但共同的特征是:出现材料迁移,以及沿滑动方
向形成程度不同的划痕。
2、磨粒(磨料)磨损
(1)定义 外界硬颗粒或者对磨表面上的硬突起物或粗糙峰在摩
擦过程中引起表面材料脱落的现象, 称为磨粒磨损。 例如:掘土机铲齿、犁耙、球磨机衬板等的磨损都是
磨损及磨损理论
粘着结合强度比两基体金属的抗剪强度都高,切应力高于粘着结合强度。 剪切破坏发生在摩擦副金属较深处,表面呈现宽而深的划痕。
此时表面将沿着滑动方向呈现明显的撕脱,出现严重磨损。如果滑动继 续进行,粘着范围将很快增大,摩擦产生的热量使表面温度剧增,极易出现 局部熔焊,使摩擦副之间咬死而不能相对滑动。 这种破坏性很强的磨损形式,应力求避免。
所以磨损是机器最常见、最大量的一种失效方式。据调查, 轮胎压痕(SEM 5000X) 联邦德国在1974年钢铁工业中约有30亿马克花费在维修上,其中 直接由于磨损造成的损失占47%,停机修理所造成的损失与磨损 直接造成的损失相当,如果再加上后续工序的影响,其经济损失 还需加上10%一20%。
摩擦痕迹 (350X)
1.6
磨损过程的一般规律:
1、磨损过程分为三个阶段:
表面被磨平, 实际接触面 积不断增大, 表面应变硬 化,形成氧 化膜,磨损 速率减小。
随磨损的增长,磨耗 增加,表面间隙增大, 表面质量恶 化,机件快速失效。
斜率就是磨损速率,唯一稳定值; 大多数机件在稳定磨损阶段(AB 段)服役; 磨损性能是根据机件在此阶段 的表现来评价。
(3)磨损比
冲蚀磨损过程中常用磨损比(也有称磨损率)来度 量磨损。
Hale Waihona Puke 材料的冲蚀磨损量(g或μ m 3) 磨损比= 造成该磨损量所用的磨料量(g)
它必须在稳态磨损过程中测量,在其它磨损阶段 中所测量的磨损比将有较大的差别。 不论是磨损量、耐磨性和磨损比,它们都是在一 定实验条件或工况下的相对指标,不同实验条件或 工况下的数据是不可比较的。
当材料产生塑性变形时,法向载荷W与较软材料的屈服极限σy之间的关系:
(1)
当摩擦副产生相对滑动,且滑动时每个微凸体上产生的磨屑为半球形。 其体积为(2/3)πa3,则单位滑动距离的总磨损量为:
摩擦学原理第章磨损理论
摩擦学原理第章磨损理论本文将讨论摩擦学原理中的磨损理论。
磨损是指两个物体表面接触,因相对运动或静止而引起的表面质量减少或形状变化。
因此,磨损是一种不可避免的表面现象。
在制造过程中对磨损进行研究是极其重要的,因为磨损会导致成本增加,使得设备和部件的寿命减少。
因此,磨损理论对于工程师来说是非常重要的。
磨损机理磨损的机理可以分为三种类型:粘着磨损粘着磨损是指表面接触时,两个物体的接触点出现局部的塑性形变,导致两个物体表面产生能够在断裂时撕裂的结合力。
这种磨损主要出现在金属材料中。
它的形成是由于两个表面间的粘着摩擦力超过了物体表面的材料强度而引起的。
磨粒磨损磨粒磨损是指在表面接触过程中,其中一个物体表面的硬颗粒形成的极高应力,在另一物体表面的损耗机制下形成切削或剥落的表面损伤。
这种磨损主要出现在有磨料的环境中。
疲劳磨损疲劳磨损是指在表面接触中受到重复载荷作用的物体表面,由于载荷的作用,表面形成微小的裂纹,这些裂纹随着时间的推移逐渐扩大,最终导致断裂。
这种磨损主要出现在金属材料中。
磨损测试了解磨损机理对于测试磨损有很大的帮助。
使用标准试验程序,可以评估不同材料之间的磨损率和耐磨性能。
在磨损测试过程中,机器将不同材料的样本表面接触,并测量它们之间的摩擦力和磨损量。
这些测试可以通过摩擦器、磨损测试机等设备来完成。
磨损控制由于磨损对机械设备和部件的寿命和成本都有很大的影响,控制磨损已成为一个非常重要的问题。
磨损控制采取各种方法,包括材料的使用、表面涂层、润滑剂、设计和运行条件的优化等。
下面我们将简单介绍这些方法的一些方面。
材料的选择材料的选择对于磨损控制至关重要。
选择适合特定应用的材料,可以延长生命周期,增加效率,降低维护成本。
通常使用高硬度、高耐磨损的金属、陶瓷和聚合物等材料来提高材料的耐磨性能。
表面涂层涂层是一种能够提高材料表面耐磨性能和摩擦系数的方法。
涂层可以使材料表面粗糙度减小,并降低摩擦力。
常用的涂层材料有核化镀层、磷化处理和高分子膜等。
- 1、下载文档前请自行甄别文档内容的完整性,平台不提供额外的编辑、内容补充、找答案等附加服务。
- 2、"仅部分预览"的文档,不可在线预览部分如存在完整性等问题,可反馈申请退款(可完整预览的文档不适用该条件!)。
- 3、如文档侵犯您的权益,请联系客服反馈,我们会尽快为您处理(人工客服工作时间:9:00-18:30)。
6.在大气中,振幅很小时(如0.012mm),钢的微动磨 损 量基本与振动频率无关,但在较大振幅时,随振动 频率 的增加,微动磨损量有减小的倾向。
2. 微动疲劳
(1)微动疲劳的特征与诊断
微动疲劳是指因微动而萌生裂纹源,并在交变应力下 裂纹扩展而导致疲劳断裂的破坏形式。 特征一:出现位置:微动接触区或其影响区内。
循环数一定时,低频微动比高频损伤大;
材料流失量随负荷和振幅而增加; 低于室温比高于室温的磨损严重;
空气环境比湿空气中损伤大。
微动的三体理论 微动的三体理论认为磨屑的产生可看成是两 个连续和同时发生的过程: ① 磨屑的形成过程 接触表面粘着和塑性变形,并伴随强烈的加工 硬化; 加工硬化使材料脆化,白层同时形成,随着白 层的破碎,颗粒剥落; 磨粒(三体磨粒)被碾碎,并发生迁移,迁移过 程取决于颗粒的尺寸、形状和机械参数(如振 幅、频率、载荷等)。
特征二:裂纹扩展的阶段性。 将遭受微动疲劳的部件在 断裂之前沿微动方向剖开,可 看到受微动影响的亚表层产生 的疲劳裂纹。裂纹在近表面处 扩展受材料晶界或缺陷影响, 较深处为穿晶裂纹。
碳钢微动疲劳时表面损伤疲劳裂 纹扩展 循环次数 104,×400
诊断: 只要断口具有疲劳破坏特 征,裂纹源发生于微动磨痕, 裂纹扩展呈现阶段性即可确 认为微动疲劳破坏。
(3)微动摩擦力和疲劳应力的协同作用将导致裂纹的萌
生和加速其扩展。 拐点是微动作用的终止点 疲劳裂纹扩展的起始点
一般来说,当微动疲劳裂纹深入到表面1mm后,其扩展和 断裂过程将完全按一般的疲劳规律进行。
(4)影响微动疲劳的因素
1. 法向压力
疲劳强度随着微动处 承受的法向压力的增 加而下降。当压力达
左图为303不 锈钢轴表面产 生微动腐蚀后 的照片。
在外观上,微动磨损的表面 特征是黑色金属上有褐红色斑点 且临近区域被抛光,因为硬质铁 氧化体磨屑具有研磨作用。
微动磨损的发生过程: 微动磨损基本上属于粘着磨损和磨粒磨损的混合机理:
• 载荷使微凸体产生粘着磨损,而往复运动引起断裂并产生 磨屑。微动与腐蚀通常是同时发生的,被称作微动腐蚀。 • 例如,当钢磨粒产生后,出生的磨粒表面被氧化成Fe2O3, 形成褐红色粉末,这些氧化颗粒具有研磨性,由于表面之 间的紧配合和小振幅往复运动(约为几十微米),界面接 触没有暴露的机会,因而磨粒很难逃逸出摩擦表面,后续 的往复运动就会产生磨粒磨损和氧化. 往复运动通常来自 外部振动,但多数情况是接触界面的某个表面承受周期应 力(或疲劳)的结果,这将引发早起疲劳裂纹而产生更大 的微动磨损,称为微动疲劳。
微动磨损的特征
具有引起微动的振动源(机械力、电磁场、冷热循环等),流体运 动所诱发的振动; 磨痕具有方向一致的划痕、硬结斑和塑性变形以及微裂纹; 磨屑易于聚团、含有大量类似锈蚀产物的氧化物。
微动磨损机理主要解释下列实验现象:
真空或惰性气氛中微动损伤较小; 微动产生的磨屑主要由氧化物组成;
若氧化物能牢固地粘附在金属表面,则可减轻磨损
4.零件金属氧化物的硬度与金属的硬度之比较大时,容 易剥落成为磨粒,增加磨损;
5.一般湿度增大则磨损下降,在界面间加入非腐蚀性润 滑剂或对钢进行表面处理,可减小微动磨损; 如对钢铁而言,相对湿度大于50%时,表面生成 Fe2O3•H2O薄膜,他比通常的Fe2O3软,具有较低的磨损率。
磨损及磨损原理
——第二讲
题纲
一 .概 述 二 .粘着磨损 三 .磨粒磨损 四 .疲劳磨损 五.其他形式的磨损(补充) 微动磨损 六 .磨损的转化与复合 七.磨损的控制与预防
五.磨损的主要类型(补充)
微动磨损(Fretting Corrosion)
1.微动磨损定义
在相互压紧的金属表面间由于小振幅振动而产生的一 种复合型式的磨损。在有振动的机械中,螺纹联接、花键 联接和过盈配合联接等都容易发生微动磨损。 微动磨损的机理:摩擦表面间的法向压力使表面上的 微凸体粘着。粘合点被小振幅振动剪断成为磨屑,磨屑接 着被氧化。被氧化的磨屑在磨损过程中起着磨粒的作用, 使摩擦表面形成麻点或虫纹形伤疤。这些麻点或伤疤是应 力集中的根源。 根据被氧化磨屑的颜色,往往可以断定是否发生微动 磨损。如被氧化的铁屑呈红色,被氧化的铝屑呈黑色,则 振动时就会引起磨损。
(2)微动疲劳曲线(交变应力与循环周次曲线)
评定材料微动疲劳性能 的主要方法是在微动条 件下测定其应力(s)— 循环数(N)曲线,称为 s—N曲线。
低碳钢的平面弯曲 疲劳曲线
这是微动疲劳的一般规律: (1)微动造成疲劳强度明显下降.这里普通疲劳极限为233MN/m2,微动 动疲劳极限下降57.7%。 (2)在高应力低循环数时,微动对疲劳强度的影响较小,而当应力较低, 循环数增加时,疲劳强度降低的比例也增加; (3)尽管在高循环次数下,微动疲劳强度降至很低值.仍有一确定的疲劳 极限,在该值上,循环数可达107次以上,即使进一步增加循环数疲劳强 度不再降低.
③磨屑剥落,二体接触 逐渐变成三体接触, 因第三体的保护作用,
粘着受抑制,摩擦系
数降低; ④磨屑连续不断地形成和排除,其成分和接触表 面随时间改变,形成和排出的磨屑达到平衡, 微动磨损进入稳定阶段。
影响微动磨损的因素
1.在一定范围内磨损率随载荷增加而增加,超过某极大 值后又逐渐下降; 2.温度升高则磨损加速; 3.抗粘着磨损好的材料抗微动磨损也好; 螺纹联接加装聚四氟乙烯垫圈也可减小微动磨损。
到一定数值时,疲劳
强度基本不变。
2. 微动振幅 微动疲劳寿命随振幅的增大而减小。当达到一临 界值时,微动疲劳寿命达到最低值,此后随振幅 继续增大寿命反而延长。
ቤተ መጻሕፍቲ ባይዱ
② 磨屑的氧化过程
起初磨屑呈轻度氧化,仍为金属本色,粒度
为微米量级(约1μm);
在碾碎和迁移过程中进一步氧化,颜色变成
灰褐色,粒度在亚微米量级(约0.1μm);
磨屑深度氧化,呈红褐色,粒度进一步减小
为纳米颗粒(约10nm) ,
利用三体理论来解释钢铁材料微动摩擦系数随循环 周次的变化过程: ①接触表面膜去除, 摩擦系数较低; ②二体接触,发 生粘着,摩擦 系数上升。并 伴随材料组织 结构变化;