降低剩余氨水焦油含量的措施
陶瓷膜在焦化剩余氨水中除油的应用_冯江华

工业水处理 Industrial Water Treatment
Vol.26 No.12 Dec., 2006
陶瓷膜在焦化剩余氨水中除油的应用
冯江华, 李慧敏
( 安阳钢铁股份公司焦化厂, 河南 安阳 455000)
[ 摘要] 用陶瓷膜分离技术, 过滤安钢焦化厂回收车间剩余氨水中的焦油类物质。用正交实验分析方法确定刚玉 陶瓷膜过滤器的最佳使用条件, 包括温度、油质量浓度、流量及陶瓷膜过滤器的反冲洗时间。使过滤后的剩余氨水含 油质量浓度 < 60 mg /L。解决了焦化污水处理过程中, 因剩余氨水含油量过高而导致废水处理效果降低的问题。保证 焦化污水处理设备的正常运行, 改善处理效果, 确保外排水质达标。
含油量分析采用硫酸酸化废水至 pH < 2, 用石 油醚萃取剩余氨水中的油类物质, 蒸除石油醚后, 称 取质量获得。 1.2.3 工艺流程
陶瓷膜除油工艺流程见图 1。
图 1 陶瓷膜除油工艺流程
剩余氨水经泵送入换热器, 然后经转子流量计 进入陶瓷膜过滤器, 过滤器上部出轻质油, 中部出过 滤后的氨水, 下部设焦油类物质及反冲洗水的出口。 其中蒸汽和清水用于陶瓷膜过滤器的反冲洗再生, 冲洗液排入机械化澄清槽。
目前, 全世界的焦炭产量约为 3.2 ×108  ̄ 3.4 × 108 t /a, 国内的焦炭产量约为 1.2 ×108 t /a, 居世界第 一〔1〕。 伴随着焦化工业的发展, 焦化污水处理的问 题日益突出。焦化污水含有大量的剧毒物质, 可伤害 人体的呼吸系统、肝、肾、神经系统, 导致癌症, 直接 外排会造成严重的水体污染。因此, 各国对焦化污水 中有害物质的最高允许排放浓度均有严格的规定。
降低脱酚效率的同时增加了溶剂的消耗; 而用蒸汽 法脱酚时设备会堵塞。当进入生化装置时, 还会增加 生化系统的负担, 抑制微生物活性, 影响废水处理效 果。同时由于剩余氨水含油量高, 还造成了煤气净化 系统中设备堵塞严重, 特别是蒸氨的换热器和蒸氨 塔尤为严重, 缩短了设备的使用寿命, 增加了生产成 本, 恶化煤气净化指标。剩余氨水中的焦油类物质直 接进入地表水体会造成水体的富营养化, 严重恶化 水体环境, 给农业、渔业、人民身体健康带来极大危 害。因此, 在剩余氨水脱酚和蒸氨之前应先除油, 从 而改善焦化工业污水处理效果, 提高水资源的重复 利用率, 保护自然环境, 实现产业的可持续发展。
化过程中剩余氨水、富液除油新技术

中图分类号: 4 5 T5 . Q6
文献标识码: A
文章编号: 5 - 020) - 5 0 3 2( 60 0 - 2 4 0 8 5 0 3 0 2
A w h o g fr rmoa f m rl a n t nl y o e vl s pu m e e c o o i l r u s o
煤 气净化过程中剩余氛水、 富液除油新技术
刘国秀
( 山西焦化股份有限公司设计部, 山西 临汾01 6 46 ) 0
摘要 : 针对山西焦化股份有限公司9 万 t 焦炉易地改造工程中煤气净化车间剩余氨水、 0 / a 富液带油严重 , 造成蒸氨脱酸板 式换热器频繁堵塞的现象 , 采用气浮除油技术和微孔陶瓷过滤技术对剩余氨水 、 富液系统进行了改造。改造后系统运行稳定,
4
八 j
9 8 7. 1 6 7. 5 9 3.
系统中压蒸汽消耗量减少20 , .t 剩余氨水脱油率达到 8. / h 00 %以上; 过滤器后含油质量浓度降至 1 m 以下, 0 岁L 除油率稳定在 8.%以上, 00 过滤器后悬浮物质量浓度稳定在 2 m/ 以下。 0 L g
关链词 : 剩余氨水 ; 富液; 堵塞; 气浮除油; 微孔陶瓷过滤器
20 年9 04 月经该厂技术委员会审核, 确定了剩余氨
水除油工艺采用气浮除油技术 , 富液除油采用微孔 陶瓷过滤技术的改造方案, 将焦油氨水分离器剩余
理塔内沥青必须停车 2 次以上。为解决上述问题,
20 年该公司决定采用气浮除油技术对剩余氨水 05
进行除油, 采用孔陶瓷过滤技术对富液进行除油 的技术改造。
收稿日期二 0 - 4 2 2 6 0- 8 0
作者简介: 刘国秀( 7 一 , 大学, 1 1 )女, 9 工程师, 从事炼焦及煤化工工艺设计工作, 5 一 654, h n. 0 7 626 z f @ cm 3 4 y sa , g b i o
剩余氨水槽改造方案及安全措施

剩余氨水槽A改为沉淀槽技改方案由于上蒸氨塔剩余氨水焦油含量高,造成氨水过滤器,换热器及再沸器堵塞严重。
为降低其焦油含量特作以下技改:a)将两个剩余氨水槽其中一个改造为“中间沉淀槽”。
使氨水在该槽内有充足的时间静置,以除去其中的焦油。
示意图如下:自循环氨水槽b)将剩余氨水槽隔板恢复。
投产前一冶施工方擅自将剩余氨水槽隔板从中部以上开孔,(孔大小约150~200mm)导致剩余氨水不能有效静置。
故需将孔堵住。
化产车间2009-3-22剩余氨水槽改造动火安全措施主管副总经理:总工程师:安监部:生产技术部:调度室:消防部门:化产车间:编制:施工措施由于自冷鼓工段出来的剩余氨水含焦油较多,需增加沉降时间以达到将其中焦油去除的目的,故需将其中一台剩余氨水槽改造为中间沉淀槽。
施工时间:施工地点:冷鼓工段剩余氨水区域施工内容:将剩余氨水槽A改造为氨水中间沉淀槽安全负责人:安全监管人:影响范围:冷凝区域施工方案:1.提前准备无缝钢管,阀门,石棉板等施工材料。
2.提前将剩余氨水槽A中的剩余氨水抽空,并用蒸汽和热水对剩余氨水槽进行清洗,将其中的焦油和氨水清洗干净。
3.将剩余氨水槽A氨水进出口阀门处打盲板。
4.将剩余氨水槽A人孔打开,顶部放散打开,自然通风不少于1天。
5.施工前化验其中的气体成分,合格后方可进入。
6.进人前必须从人孔处对剩余氨水槽进行强制通风。
7.将剩余氨水槽A中的隔板上的孔进行恢复。
8.如下图进行焊接与A槽相连接的管道。
9.施工完毕后拆除剩余氨水槽A的进出口阀门。
10.将剩余氨水槽B中的氨水倒换至剩余氨水槽A。
动火前也同样对剩余氨水槽B进行处理。
11.恢复剩余氨水槽B的隔板,焊接与剩余氨水槽B相接的管道。
12.施工完毕后清理施工现场。
施工安全事项:1、进入剩余氨水槽必须遵守受限空间安全作业措施,高空作业和焊接必须遵守高空和电焊施工措施。
2、施工时所用的工具必须为铜质工具,若用铁制工具必须涂抹黄油,防止碰撞产生火花。
浅析降低剩余氨水含油的措施

1 现 状 分 析
我 厂 焦化 车间 氨水 除油采 用气 浮搅 拌刮板 式 除
滤 器 的氨水起 到搅 拌 作 用 , 使 过 滤 下 来 的焦 油 与 氨 水 不断混 合 , 焦油 不 容 易 沉 淀 ; 其次 , 氨 水 是 从 陶瓷 管 的管 程进 入 , 从 壳程 出来 , 造 成空 间狭 小 的管程 很 快 被焦 油充 满 , 增 加 了氨水 的含 油率 。
6 0
燃 料 与 化 工
F u e l& Ch e mi c a l Pr o c e s s e s
S e p . 2 01 3 V0 l _ 4 4 NO . 5
浅 析 降低 剩 余 氨水 含 油 的措 施
李少 源 孙 宝东 ( 南京 钢铁 联合 有 限公 司炼铁 新厂 ,a l t a r r e mo v e r a r e p r o v e d t h r o ug h pr o c e s s o p t i mi z a t i o n a n d e q ui p me n t i mp r o v e me n t t o r e d uc e t h e
持在 9 0 %左 右 。为 了连续 运行 , 设备 设 置 高 温 蒸 氨
处 理效 率急 剧下 降 , 外 排污 水不 达标 。
废水 ( 9 8~l 0 0 ℃) 作为反冲洗介质 , 保 证 了过 滤效 率 。通过 几年 的运 行 , 该 套 设 备 逐 渐 暴 露 出 一 些技
术 缺陷 。首先 , 由于氨 水进 口设 置在 最底 部 , 进 入 过
关 键 词 :剩 余 氨 水 ;焦 油 ;过 滤 器
中 图 分 类 号 :X 7 8 4 文 献 标 识 码 :B 文 章 编 号 :1 0 0 1 —3 7 0 9 ( 2 0 1 3 )0 5 — 0 0 6 0— 0 3
有效提高焦油氨水分离效率的措施
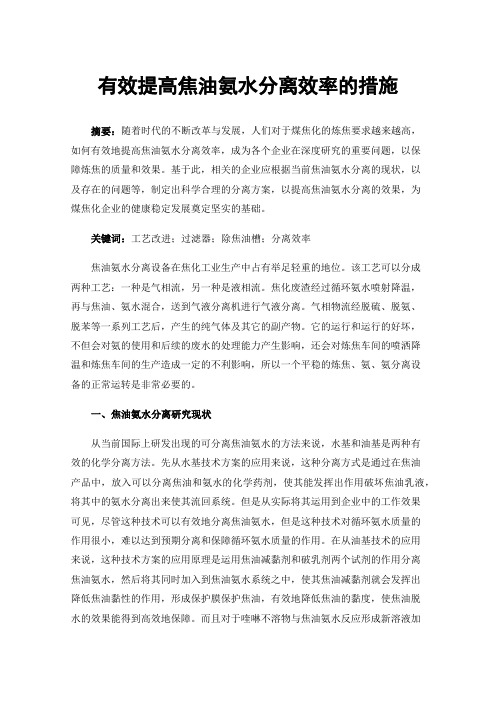
有效提高焦油氨水分离效率的措施摘要:随着时代的不断改革与发展,人们对于煤焦化的炼焦要求越来越高,如何有效地提高焦油氨水分离效率,成为各个企业在深度研究的重要问题,以保障炼焦的质量和效果。
基于此,相关的企业应根据当前焦油氨水分离的现状,以及存在的问题等,制定出科学合理的分离方案,以提高焦油氨水分离的效果,为煤焦化企业的健康稳定发展奠定坚实的基础。
关键词:工艺改进;过滤器;除焦油槽;分离效率焦油氨水分离设备在焦化工业生产中占有举足轻重的地位。
该工艺可以分成两种工艺:一种是气相流,另一种是液相流。
焦化废渣经过循环氨水喷射降温,再与焦油、氨水混合,送到气液分离机进行气液分离。
气相物流经脱硫、脱氨、脱苯等一系列工艺后,产生的纯气体及其它的副产物。
它的运行和运行的好坏,不但会对氨的使用和后续的废水的处理能力产生影响,还会对炼焦车间的喷洒降温和炼焦车间的生产造成一定的不利影响,所以一个平稳的炼焦、氨、氨分离设备的正常运转是非常必要的。
一、焦油氨水分离研究现状从当前国际上研发出现的可分离焦油氨水的方法来说,水基和油基是两种有效的化学分离方法。
先从水基技术方案的应用来说,这种分离方式是通过在焦油产品中,放入可以分离焦油和氨水的化学药剂,使其能发挥出作用破坏焦油乳液,将其中的氨水分离出来使其流回系统。
但是从实际将其运用到企业中的工作效果可见,尽管这种技术可以有效地分离焦油氨水,但是这种技术对循环氨水质量的作用很小,难以达到预期分离和保障循环氨水质量的作用。
在从油基技术的应用来说,这种技术方案的应用原理是运用焦油减黏剂和破乳剂两个试剂的作用分离焦油氨水,然后将其同时加入到焦油氨水系统之中,使其焦油减黏剂就会发挥出降低焦油黏性的作用,形成保护膜保护焦油,有效地降低焦油的黏度,使焦油脱水的效果能得到高效地保障。
而且对于喹啉不溶物与焦油氨水反应形成新溶液加大分离难度的问题,也可以运用这种方式将其有效地分离,使其不会产生影响到其分离的问题,可有效地加强对分离效果的保证。
离心分离技术用于剩余氨水除油_刘燕

第29卷 第2期2007年4月四川冶金Sichuan MetallurgyVol.29 No.2Ap ril,2007离心分离技术用于剩余氨水除油刘 燕(攀枝花钢铁有限责任公司煤化工厂)【摘 要】 对于焦化厂冷凝系统剩余氨水带油的问题,从理论和实践分析了带油原因,并对剩余氨水除油方法进行了探讨。
【关键词】 剩余氨水 除油 离心分离THE CENTRI FUGAL SEPARATI ON USES I N THE SURP LUSA MMONI A WATER E L I M I NATI NG THE O I LL iu Yan(Pangang Gr oup Coal Chem ical Engineering Fact ory,Panzhihua Sichuan617022,China)[Abstract] By using the fact of tar exiscing in sur p lus a mmonia water the SCCP condensati on syste m, the reas on of tar existing in sur p lus a mmonia water is analyzed,and the method re moving tar is discussed.[Key words] sur p lus a mmonia water,detarring,centrifugal separati on1 前言攀钢煤化工厂二期煤气净化系统采用AS循环脱硫洗氨工艺,由于剩余氨水带油和悬浮物,造成系统换热器、洗涤塔、脱酸蒸氨塔堵塞,影响煤气净化效果。
为此,通过离心分离技术对剩余氨水进行了油水分离,由试验的结果表明,离心分离能使油和水得到很好的分离,基本上能解决后续的系统堵塞问题。
2 离心分离技术除油原理2.1 剩余氨水中焦油的存在形态分析剩余氨水是一个含有乳化液滴和胶体的复杂体系,其中所含焦油不溶于水,焦油是一种十分复杂的多组份混合物,特别是其中的有机物如酚类、吡啶碱等的分子结构中既含有亲油基,又含有亲水基,在细小的油滴表面上会形成亲油基向油滴内部、亲水基向水侧的定向排列,而将油滴保护起来。
专业论文焦化厂降低剩余氨水焦油含量的措施
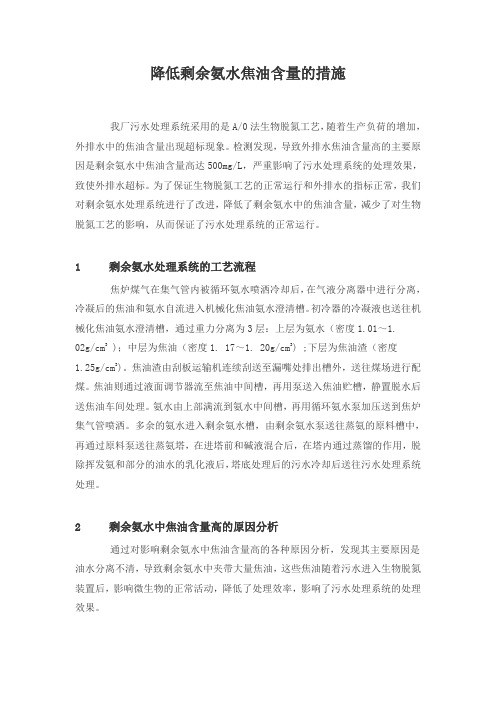
降低剩余氨水焦油含量的措施我厂污水处理系统采用的是A/0法生物脱氮工艺,随着生产负荷的增加,外排水中的焦油含量出现超标现象。
检测发现,导致外排水焦油含量高的主要原因是剩余氨水中焦油含量高达500mg/L,严重影响了污水处理系统的处理效果,致使外排水超标。
为了保证生物脱氮工艺的正常运行和外排水的指标正常,我们对剩余氨水处理系统进行了改进,降低了剩余氨水中的焦油含量,减少了对生物脱氮工艺的影响,从而保证了污水处理系统的正常运行。
1 剩余氨水处理系统的工艺流程焦炉煤气在集气管内被循环氨水喷洒冷却后,在气液分离器中进行分离,冷凝后的焦油和氨水自流进入机械化焦油氨水澄清槽。
初冷器的冷凝液也送往机械化焦油氨水澄清槽,通过重力分离为3层:上层为氨水(密度1.01~1.02g/cm3 );中层为焦油(密度1. 17~1. 20g/cm3) ;下层为焦油渣(密度1.25g/cm3)。
焦油渣由刮板运输机连续刮送至漏嘴处排出槽外,送往煤场进行配煤。
焦油则通过液面调节器流至焦油中间槽,再用泵送入焦油贮槽,静置脱水后送焦油车间处理。
氨水由上部满流到氨水中间槽,再用循环氨水泵加压送到焦炉集气管喷洒。
多余的氨水进入剩余氨水槽,由剩余氨水泵送往蒸氨的原料槽中,再通过原料泵送往蒸氨塔,在进塔前和碱液混合后,在塔内通过蒸馏的作用,脱除挥发氨和部分的油水的乳化液后,塔底处理后的污水冷却后送往污水处理系统处理。
2 剩余氨水中焦油含量高的原因分析通过对影响剩余氨水中焦油含量高的各种原因分析,发现其主要原因是油水分离不清,导致剩余氨水中夹带大量焦油,这些焦油随着污水进入生物脱氮装置后,影响微生物的正常活动,降低了处理效率,影响了污水处理系统的处理效果。
3 改进方法为提高油水分离的效果,降低剩余氨水中焦油的含量,改善外排水的水质,我们从以下两个方面进行了改进。
3.1 延长油水分离时间为了延长油水分离时间,提高焦油氨水的分离效果,对鼓冷工序和蒸氨工序的焦油和氨水的分离系统进行了改造,增加了油水分离的过程。
焦化废水处理方法及方案

焦化废水是煤在高温干馏过程中以及煤气净化、化学产品精制过程中形成的废水,其中含有酚、氨氮、氰、苯、吡啶、吲哚和喹啉等几十种污染物,成分复杂,污染物浓度高、色度高、毒性大,性质非常稳定,是一种典型的难降解有机废水。
它的超标排放对人类、水产、农作物都构成了很大危害。
如何改善和解决焦化废水对环境的污染问题,已成为摆在人们面前的一个迫切需要解决的课题。
目前焦化废水一般按常规方法先进行预处理,然后进行生物脱酚二次处理。
但是,焦化废水经上述处理后,外排废水中氰化物、COD及氨氮等指标仍然很难达标。
针对这种状况,近年来国内外学者开展了大量的研究工作,找到了许多比较有效的焦化废水治理技术。
这些方法大致分为生物法、化学法、物化法和循环利用等4类。
1 生物处理法生物处理法是利用微生物氧化分解废水中有机物的方法,常作为焦化废水处理系统中的二级处理。
目前,活性污泥法是一种应用最广泛的焦化废水好氧生物处理技术。
这种方法是让生物絮凝体及活性污泥与废水中的有机物充分接触;溶解性的有机物被细胞所吸收和吸附,并最终氧化为最终产物(主要是CO2)。
非溶解性有机物先被转化为溶解性有机物,然后被代谢和利用[1]。
基本流程如图1所示。
图1 生物处理法基本流程但是采用该技术,出水中的CODCr、BOD5、NH3-N等污染物指标均难于达标,特别是对NH3-N污染物,几乎没有降解作用。
近年来,人们从微生物、反应器及工艺流程几方面着手,研究开发了生物强化技术:生物流化床,固定化生物处理技术及生物脱氮技术等。
这些技术的发展使得大多数有机物质实现了生物降解处理,出水水质得到了很大改善,使得生物处理技术成为一项很有发展前景的废水处理技术。
合肥钢铁集团公司焦化厂、安阳钢铁公司焦化厂、昆明焦化制气厂采用A/O (缺氧/好氧)法生物脱氮工艺,运行结果表明该工艺运行稳定可靠,废水处理效果良好,但是处理设施规模大,投资费用高。
上海宝钢焦化厂将原有的A/O生物脱氮工艺改为A/OO工艺,污水处理效果优于A/O工艺[2],运行成本有所降低,效果明显。
- 1、下载文档前请自行甄别文档内容的完整性,平台不提供额外的编辑、内容补充、找答案等附加服务。
- 2、"仅部分预览"的文档,不可在线预览部分如存在完整性等问题,可反馈申请退款(可完整预览的文档不适用该条件!)。
- 3、如文档侵犯您的权益,请联系客服反馈,我们会尽快为您处理(人工客服工作时间:9:00-18:30)。
降低剩余氨水焦油含量的措施
崔保华介清涛张化强李增喜王宏顺杨光丽
(安阳钢铁股份有限公司焦化厂,安阳455004)
我厂污水处理系统采用的是A/0法生物脱氮工艺,随着生产负荷的增加,外排水中的焦油含量出现超标现象。
检测发现,导致外排水焦油含量高的主要原因是剩余氨水中焦油含量高达500mg/L,严重影响了污水处理系统的处理效果,致使外排水超标。
为了保证生物脱氮工艺的正常运行和外排水的指标正常,我们对剩余氨水处理系统进行了改进,降低了剩余氨水中的焦油含量,减少了对生物脱氮工艺的影响,从而保证了污水处理系统的正常运行。
1 剩余氨水处理系统的工艺流程
焦炉煤气在集气管内被循环氨水喷洒冷却后,在气液分离器中进行分离,冷凝后的焦油和氨水自流进入机械化焦油氨水澄清槽。
初冷器的冷凝液也送往机械化焦油氨水澄清槽,通过重力分离为3层:上层为氨水(密度1.01~1. 02g/cm3);中层为焦油(密度1. 17~1. 20g/cm3) ;下层为焦油渣(密度1.25g/cm3)。
焦油渣由刮板运输机连续刮送至漏嘴处排出槽外,送往煤场进行配煤。
焦油则通过液面调节器流至焦油中间槽,再用泵送入焦油贮槽,静置脱水后送焦油车间处理。
氨水由上部满流到氨水中间槽,再用循环氨水泵加压送到焦炉集气管喷洒。
多余的氨水进入剩余氨水槽,由剩余氨水泵送往蒸氨的原料槽中,再通过原料泵送往蒸氨塔,在进塔前和碱液混合后,在塔内通过蒸馏的作用,脱除挥发氨和部分的油水的乳化液后,塔底处理后的污水冷却后送往污水处理系统处理。
2 剩余氨水中焦油含量高的原因分析
通过对影响剩余氨水中焦油含量高的各种原因分析,发现其主要原因是油水分离不清,导致剩余氨水中夹带大量焦油,这些焦油随着污水进入生物脱氮装置后,影响微生物的正常活动,降低了处理效率,影响了污水处理系统的处理效果。
3 改进方法
为提高油水分离的效果,降低剩余氨水中焦油的含量,改善外排水的水质,我们从以下两个方面进行了改进。
3.1 延长油水分离时间
为了延长油水分离时间,提高焦油氨水的分离效果,对鼓冷工序和蒸氨工序的焦油和氨水的分离系统进行了改造,增加了油水分离的过程。
(1)鼓冷工序增加焦油氨水分离槽。
鼓冷工序的焦油和氨水分离只是在机械化焦油氨水澄清槽中进行,分离时间短,效果不好。
图1和图2示出了改进前后的焦油氨水分离流程。
图2 改进后的焦油氨水分离流程
如图2 所示,焦油和氨水的混合液进入机械化焦油氨水澄清槽,槽底部的焦油和氨水的混合液用泵抽送至新增加的焦油氨水分离槽,在该槽中焦油和氨水的静置时间长达10h,底部的焦油通过锥形管流入焦油中间槽。
氨水从顶部满流
管溢出与从机械化焦油氨水澄清槽顶部分离出的氨水汇合后送往循环氨水槽。
从焦油氨水分离槽中间的乳化液送往横管式初冷器循环洗萘。
通过上述改造后,剩余氨水和焦油的混合液在机械化焦油氨水澄清槽分离后,再在焦油氨水分离槽中进行二次分离,延长了分离时间,可使分离时间延长了10min,有效地提高了油水分离的效果。
(2)将蒸氨工序的原料槽改为除焦油槽。
在蒸氨工序中,从鼓冷来的剩余氨水直接进入两个并联的原料槽中,再由两个槽的底部用泵送往蒸氨塔。
致使剩余氨水没有经过任何处理而直接进入蒸氨塔中。
改造后将原两个原料槽中的一个改造为除焦油槽,如图3 所示,从鼓冷来的剩余氨水首先进入除焦油槽中,在此槽中通过重力作用进行静置分离,满流后的氨水通过管道自流入原料槽中,这样在剩余氨水进入蒸氨塔前进行了一次分离,增加了分离时间,可将氨水中所夹带的焦油进一步分离。
图3 改进后的蒸氨工艺流程图
经上述改造后,从鼓冷来的剩余氨水在除焦油槽中停留时间达到了10min,延长了油水分离时间,有效地改善了剩余氨水的水质。
通过两次改造,使焦油和氨水的分离时间延长了20min,增强了分离的效果。
3.2 降低剩余氨水中的焦油含量
为降低剩余氨水中焦油的含量,加强了对剩余氨水槽和原料除焦油槽的放油管理,定期对其进行放油。
(1)加强对剩余氨水槽的放油。
从循环氨水槽中出来的氨水进入剩余氨水槽,在此,氨水与焦油在重力作用下分离,焦油沉积在剩余氨水槽的底部,经过长时间的积累后,焦油的液位不断升高,如果不及时排出,焦油就会带入氨水系
统,致使氨水含油偏高。
为此规定剩余氨水槽每天进行放油,在放油时以看到氨水时为止。
(2)增强对蒸氨除焦油槽的放油。
从剩余氨水槽来的剩余氨水首先进入蒸氨新增加的除焦油槽中,如不及时排出除焦油槽底部沉积的轻质焦油,也会随原料氨水进入后续处理系统中。
因而,我们针对除焦油槽制定了定期的排放制度,以使焦油和分离后的氨水得到彻底分开。
规定除焦油槽放出的轻质焦油送至煤气终冷器进行循环洗萘,这样既排放出了焦油,又可以降低终冷器的阻力。
排放制度规定:每天白、中班各一次,在放油时以看到氨水时为止,将其中所含的焦油全部放完。
4 改进效果
对改进后的数据统计表明,剩余氨水中的焦油平均含量小于300mg/L,一般可控制在200mg/L, 远低于改进前的500 mg/L,见图4 。
大幅度减少了剩余氨水中的焦油含量,改善了剩余氨水的水质,为生物脱氮工艺提供了合格稳定的原料水。
既降低了生物脱氮工艺的处理成本,而且也回收了剩余氨水中的焦油。
图4 改进前后剩余氨水中焦油含量对比图
5 结论
通过对剩余氨水处理系统的改进,大大地降低了剩余氨水中的焦油含量,为生物脱氮工艺提供了合格稳定的原料水,保证了生物脱氮工艺的正常运行,使得外排水含油量达到了排放的标准,保证了外排水各项指标的正常,减少了外排水对环境造成的污染,因而具有较好的经济效益和社会效益。