印刷电路板(P.C.B)制程的常见问题及解决方法(1)
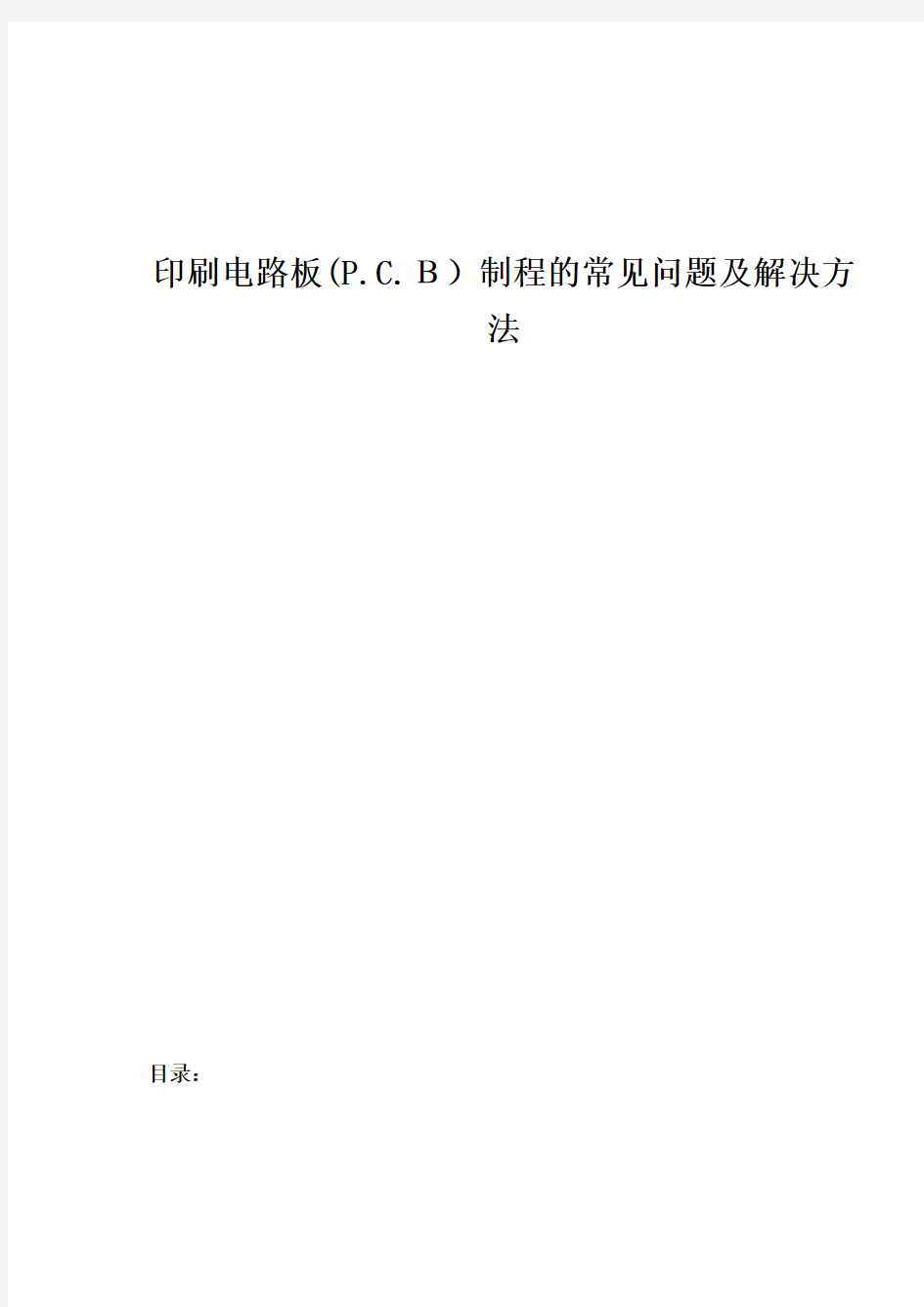

印刷电路板(P.C.B)制程的常见问题及解决方
法
目录:
(一)图形转移工
艺…………………………………………………………………………
……………2(二)线路油墨工
艺………………………………………………………………………
………………4(三)感光绿油工
艺…………………………………………………………………………
……………5(四)碳膜工
艺………………………………………………………………
(7)
(五)银浆贯孔工
艺…………………………………………………………………………
(8)
(六)沉铜(P T H)工
艺……………………………………………………………………………
………9
(七)电铜工
艺………………………………………………………………
………………………1 1 (八)电镍工
艺…………………………………………………………………
……………………1 2 (九)电金工
艺……………………………………………………………………
…………………1 3 (十)电锡工
艺…………………………………………………………………
……………………14(十一)蚀刻工艺………………………………………………………………………
………………1 5 (十二)有机保焊膜工艺…………………………………………………………………………
……1 5
(十三)喷锡(热风整平)艺…………………………………………………………………………
1 6 (十四)压合工艺………………………………………………………………………
(17)
(十五)图形转移工艺流程及原理………………………………………………………………20 (十六)图形转移过程的控制………………………………………………………………………
24
(十七)破孔问题的探讨………………………………………………………………………
(28)
(十八)软性电路板基础…………………………………………………………………………
(33)
(十九)渗镀问题的解决方法………………………………………………………………………
38
电池制程中异常质量问题分析解答
电池制程中异常质量问题分析解答 制造技术培训-生产中常见问题与解答 1、什么是锂离子电池制造过程? (1) 配膏:用专门的溶液和粘接剂分别与粉末状的正负极活性物质混合,经高速搅拌均匀后,制成浆状的正负极物质。 (2) 涂布:将制成的浆料均匀地涂覆在金属箔的表面,烘干,分别制成正负极极片。 (3)制片:将涂好的布裁成工艺要求的大小,压片,再焊极耳 (4) 装配:将正极片、隔膜、负极片顺序放好,经卷绕制成电池极芯,装入包装膜,再注入电解液、封口等工艺过程,即完成电池装配过程。 (5) 化成:用专用的电池充放电设备对成品电池进行充放电测试,对每一只电池都进行检测。筛选出合格的成品电池,待出厂。 (6)包装:按客户的要求,将电池组合出货 2、锂电池在生产中最为严格控制的因素之一是水,为什么? 答:只要电池里有微量的水就会使电池产生气体,使电池容量下降,放电效果差,因此,生产过程要严格控制水分。 3、在生产过程中哪些环节可能引入水份?如何有效控制? 答:在电池注液封口前,要求电芯非常干燥,真空干燥箱烘干后的电芯水分含量小于空气相对湿度5%的水分含量,由于空气湿度一般在60%~90%,所以,只要接触空气电芯就会吸水。注液室经过特殊处理,空气湿度可控制在25%以下,但还是大于电芯的水分含量,因此注液室也要缩短操作时间,减少电芯在空气中暴露时间 为了有效控制水分,从极片生产就开始控制,包括涂布烘干,烘干桥烘干,控制车间湿度,一直到装配裁隔膜烘干,控制车间湿度。总之一切要求干燥。我们洗手后要手干后再进车间,戴口罩防止口水喷到极片上等。 4、极片存放时间过长会造成什么后果?
答:极片存放时间过长,会造成电池性能下降。而且长时间放置会落尘,极片上出现灰尘等杂质,造成自放电大、微短路等后果。 5、极片上有浮粉会有什么问题? 答:极片上有浮粉在卷绕成电池以及注液后,浮粉会在电池中随着电解液的运动而运动,运动到某些容易出现问题的地方时,比如隔膜有缺陷的地方,将有可能造成电池出现微短路、自放电大等问题。 6、正、负极片压片的目的? 答:使活性物质与导电箔料接触紧密以及活性物质本身接触紧密,降低极片的厚度,提高电池体积的利用率,同时也降低了内阻,提高了电池的大电流放电性能。 7、压片厚度对电池性能有什么影响? 答:极片压片厚度达不到要求,首先会造成电池的厚度达不到要求。另外,极片压片厚度不同,活性物质中的紧密接触程度也会不一样,会造成电池性能的差别。 8、油性物质粘在极片上有什么问题? 答:油性物质粘在极片上有可能造成此处电解液不浸润,使活性物质反应不好。另外,油性物质对于电池来说是杂质,在电池中会出现破坏电池性能的一些反应,造成电池性能下降。 9、极片脱粉会导致电池性能出现什么问题? 答:极片脱粉会造成电池容量不够。另外,负极片脱粉还会造成安全问题,有可能电池枝晶短路起火燃烧。 10、极片表面有硬点、手印、不平滑对电池有哪些影响? 答:极片表面有硬点,在卷绕后,压电芯时很容易出现硬点穿透隔膜,造成电池短路。极片表面的手印是手上的汗液留下的痕迹,主要成分是人体分泌的一些盐分和油脂,和上面油性物质的危害相似。极片表面不平滑是极片厚度不均匀的表现,可能造成极片各个不同部位反应不均一的问题。 11、刮粉部位(箔料表面)不太干净,不平滑,轻微刮烂对电池有哪些影响? 答:刮粉部位箔料表面不太干净,主要会导致极耳焊接困难,焊接不上或者容易出现虚焊。刮粉部位箔料表面轻微不平滑对电池影响不大,如果出现打折的情况则可能在卷绕时刺穿隔膜。极片轻微刮烂容易在电芯受压时刺穿隔膜,造成短路。
手机组装常见工艺问题的分析
手机组装常见工艺问题的分析 手机组装中,常见工艺问题的分析。首先给大家一个宏观的信息。第一,手机板由于生产批量比较大,元件工艺兼容性比较好,就整个业界看,直通率比较高,平均超过99%以上。 焊接问题总的来说不多,主要集中在PCB、屏蔽框、连接器、EMI特殊器件。下面援引16个案例给大家介绍一下。第一个问题,PCB板分层。 分层主要原因有这么几个:第一,pcb制造工艺和材料。手机板用的是二次制压技术,这里面用的填充剂偏低,PCB容易造成分层。另外密集孔的地方如果没有排气孔,这个分层也是比较常见。 另外最常见原因,目前大家比较常见的就是吸潮。无铅工艺对温度比较敏感。这也是为什么我们以前做喷漆板的时候,材料存储器一般一年、几个月。现在手机板存储也就是三个月。以前都是用聚乙烯材料,现在手机板大部分采用铝格包装,主要解决吸潮问题。 第二,微盲孔引起的BGA大洞。这和我们设计有关系。比如手机板都是HDI技术,国内板厂,微盲空不填充,表面清洗的时候很容易清洗不干净,引起有机物分解,造成很大空洞。另外和我们制作的孔形有很大关系,里面的残留物比较难清洗。会出现大洞。 另外回盲孔对位对不准的话,穿错了,必然导致这样一个结果。一般有这么几个方面原因,第一,设计。第二,PCB制作工艺。国外很多板,向这种微盲孔基本上是半填铜、全填铜。基本上这个问题已经消失了,我们国内微盲孔基本都有空洞,但是大部分在可接受范围。 另外PCB板后期清洗也是很重要方面,我建议大家做手机板检验方面最好能增加这方面指标。 第三,次表面树脂开裂。这个主要原因是和PCB制作材料有很大关系,现在许多厂家采用高T板材,有一个很大特点,比较脆。另外有使用无卤板材,比较脆。 焊接的时候,如果温差很大的话,开裂就是有可能的。这样在一般厂家应该都会碰到这样的问题。我们在硬制板加工的时候,出了问题都是一批一批。 第四,电池插座移位。这个原因有很多,比如链条振动、风压不合适的话,会出现这些问题。更多原因还是在物料方面,在我们手机封面最主要是一个焊盘和引线宽度如果相差很多,我们没有作过多考虑,焊完的时候,焊膏用的比较多,可能把元件飘起来,振动对它的影响比较大。 第五,SIM卡插座变形。这个一个是跟板材有关系,有的材料吸潮,吸潮后很容易变形。变形本来就是一种缺陷。对手机来说,越来越薄,里面的空间很少,假如稍有变形,装都装不进去。这是很大的缺陷。 另外有一些元件会掉片,移位,手机板向这种sim卡也会造成这种情况,主要原因也可能是跟我们选用材料有关系。因为有的SIM卡掉,无非是有力把它拉下去,不同物料,有的物料它里面是挖空的,如果很实在的话,就不会掉。大家也会碰到这方面问题。另外也跟我们
制程质量异常报告单
制程质量异常报告单 单位车间班组日期年月日 异常事项 序号时间产品批号产品名称异常工序异常情况检验员1 2 3 1. 异常原因 2. 1. 改善措施 2. 改进检查时间及1. 状况2. 检验员质量管理部经理 生产操作质量检查表 操作人员姓名:填写日期:年月日检查项目实际情形备注 1.操作前的准备工作是否完成 2.是否按操作标准来操作 3.工作场所的布置是否适宜 4.通风、照明、温度等是否符合规定 5.附近环境是整洁 6.对异常状况是否掌握处理程序 7.是否有改进工作方法的意见与建议 1. 8.其他需提出的事项 2. 质检主管:检查人员:
车间:班组:填写日期:年月日 成品不合格加工不合格合格不合格日期产品名称批号产量不合格数 数率 产品质量抽样检测表 序号标准规定的指标名称及要求计量单位实验结果判定结论备注1 2 3 质量性能综合评 定结论 检测依据的标准名称及编号检测机构检测日期 附件目录 其他说明
检查项目实际情形备注1.存放是否定位及是否整洁 2.温度、湿度、通风、照明是否适宜 3.是否备有消防设备 4.危险性物品是否与其他物品隔离 5.良品、不良品未经检验是否分别存放 6.实际的数量是否与账面符合 7.度量衡的器具是否精确 8.存放的地点是否有进出的管理 9.产品的质量是否发生变化 1. 10.其他需提出的事项 2. 自我质量控制检查表 编号:填写日期:年月日检查项目实际情形备注1.是否按检查标准检查 2.感官检查的限度(去掉)样本是否标准 3.检查的仪器、量规是否精准 4.是否有漏检情况 5.漏检的原因 6.对不合格品是否妥善处理 1. 7.其他需提出的情况 2. 质检主管:检查人员:
制程常见问题
SMT常见工艺问题简述 SMT常见工艺问题概述(一) 锡膏制程 (一)普通锡膏(63/37) 普通锡膏于制程中常见的工艺问题主要为以下几种: 元件竖立,短路,冷焊,偏移,锡珠 1.元件竖立 元件竖立又叫“曼哈顿效应“。主要是由于元件两端焊锡浸润不均匀,因此,熔融焊料的不够均衡的表面张力拉力就施加在元件的两端上,引发此类不良的原因较多,但主要有三大类。即: A.元件不良:元件两端电极氧化或附有异物,导致焊锡时上锡不良;基板材料导热性差,基板的厚度均匀性差;焊盘的热容量差异较大,焊盘的可焊性差异较大;锡膏中助焊剂的均匀性差或活性差。B.设计缺失:焊盘铜箔大小不一或一端连接有接地等较大的铜箔,造成回流时焊盘两端受热不均匀。C.制程缺失:制程缺失的因素很多。如两个焊盘上的锡膏厚度差异较大,锡膏太厚,印刷精度差,错位严重;预热温度太低;贴装精度差,元件偏移严重等。 以上三种成因中第一项就不用赘述了。只要严把进料和储存两关就好了。下面简述一下二,三两项成因的控制方法。 ——对于设计上的缺失,长期办法当然是修改设计方案。短期办法或没法修改方案的情况下,就需要从二个方面入手。一是通过更改钢网的开口设计来达到控制的目的。即将铜箔较小的一端焊盘网孔局部加大,使之与大铜箔大小比例为1:1。从而降低焊盘两端锡膏回流时的时间差;二是修改炉温曲线,即延长升温区(回流前)的时间,降低升温速率,使整块PCB上各点的温度尽量保持平衡。从而避免因回流时的温度不平衡而导致元件受力竖起。 ——制程缺失产生的原因就更多了。一个公司制程品质的好坏不在于有多么先进的设备,关键在于制程控制的方法和管理的力度上。好的控制方法应该从原材料的采购,进料的检验,储存环境和储存条件的设定等做起,每一环节都切实履行自己的职责,再到原物料的使用(包括使用环境,使用条件等工艺参数的设定)和设备的维护保养,校正以及参数设定,操作人员的培训和管理等,需要一个贯穿始终,环环相扣,职责分工明确又相互关联的控制系统。在各个职能部门和相关工作人员的通力协作下才能臻至理想状态。这一点,每个公司有每个公司的做法和不同的控制体系。具体的操作就是仁者见仁,智者见智了。 2.短路 短路这种不良现象多发于细间距IC的引脚之间,所以又叫“桥接“。当然也有CHIP件之间发生短路现象的,那是极少数。下面就细间距IC引脚间的桥接问题浅谈它的诚因及解决方法。 桥接现象多发于0.5mm及以下间距的IC引脚间,因其间距较小,故模板设计不当或印刷稍有疏漏就极易产生。 A.模板 依据IPC-7525钢网设计指南要求,为保证锡膏能顺畅地从网板开孔中释放到PCB焊盘上,在网板的开孔方面,主要依赖于三个因素: 1、)面积比/宽厚比>0.66 2、)网孔孔壁光滑。制作过程中要求供应商作电抛光处理。 3、)以印刷面为上面,网孔下开口应比上开口宽0.01mm或0.02mm,即开口成倒锥形,便于焊膏有效释放,同时可减少网板清洁次数。 具体的说也就是对于间距为0.5mm及以下的IC,由于其PITCH小,容易产生桥接,钢网开口方式长度方向不变,开口宽度为0.5~0.75焊盘宽度。厚度为0.12~0.15mm,最好使用激光切割并进行抛光处理,以保证开口形状为倒梯形和内壁光滑,以利印刷时下锡和成型良好。 B.锡膏 锡膏的正确选择对于解决桥接问题也有很大关系。0.5mm及以下间距的IC使用锡膏时应选择粒度在 20~45um,黏度在800~1200pa.s左右的,锡膏的活性可根据PCB表面清洁程度来决定,一般采用RMA级。
PCB各制程不良分析说明材料.docx
* * 各制程不良分析手册 站别号问题点定义原因分析标准 CU 1.IU 或 IIU 前板面药水污染等板面不洁造成结合不佳 1皮 2.电镀参数不合理导镀面结合粗糙不均不允许 起 泡 线 1.因刮伤或汗清洁不良 ,导致干膜 S/C 暗区产生条状凹痕无造成断路 ,且 2 状 2.因人造成或压膜不良造成干膜折痕不小于规范线缩 3.D/F 后站药水污染致 D/F 板暗区扩涨径之 20% 腰 线 1.IU 或 CUII 前处理不彻底 ,造成 CU 层之间结合不牢 3路 2.槽液温度过低等参数不当致 CU 层沉积粗糙 ,与前者之 CU 不允许分不能很好结合 层 3. D/F 湿影不彻底,导致铜层结合不好
* * 蚀 1.蚀刻参数未管控好线路间不超过 刻 2.流锡或剥膜不尽规范线径之4 不 3.IU 或 IIU 前干膜掉落 (刮落或与板面结合不牢 )20%, 且未造成 尽 4.干膜前板面沾胶短路 线 1.IU 或 CUII 前处理不彻底 ,造成 CU 面结合不牢 路 2.槽液温度过低等参数不当致 CU 层沉积粗糙 ,与前者之 CU 不允许5 分不能很好结合 层 3.D/F 湿影不彻底,导致铜层结合不好 电 脏 1. 干膜底片未清洁净 ,导致其明区沾污部分未被曝光固化 , 6 点 短 路即此线距部分会被镀上CU 及 sn/pb而造成短路 不允许 镀 CU 1.基材本身有针点凹陷不良 (检查基板表面 ) A 手指不允许 , 面 2.压合时 CU 皮表面沾尘或 PP 质量不良造成压合后此瑕玼板面每点不大7 凹 3.电镀铜时因槽液特别是光泽剂不正常导致CU 积不良。于 20mil, 不超 陷 (2.3. 可通过做切片观查 ,以作为参考 )过板厚的 1/5
印制电路板制程简介
印制电路板制程简介 作者:佚名文章来源:PCB行业网站点击数:176 更新时间:2006-9-21
制程名称制程简介内容说明 印刷电路板 在电子装配中,印刷电路板(Printed Circuit Boards)是个关键零件。它搭载其它的电子零件并连通电路,以提供一个安稳的电路工作环境。如以其上电路配置的情形可概分为三类: 【单面板】将提供零件连接的金属线路布置于绝缘的基板材料上,该基板同时也是安装零件的支撑载具。 【双面板】当单面的电路不足以提供电子零件连接需求时,便可将电路布置于基板的两面,并在板上布建通孔电路以连通板面两侧电路。 【多层板】在较复杂的应用需求时,电路可以被布置成多层的结构并压合在一起,并在层间布建通孔电路连通各层电路。 内层线路 铜箔基板先裁切成适合加工生产的尺寸大小。基板压膜前通常需先用刷磨、微蚀等方法将板面铜箔做适当的粗化处理,再以适当的温度及压力将干膜光阻密合贴附其上。将贴好干膜光阻的基板送入紫外线曝光机中曝光,光阻在底片透光区域受紫外线照射后会产生聚合反应(该区域的干膜在稍后的显影、蚀铜步骤中将被保留下来当作蚀刻阻剂),而将底片上的线路影像移转到板面干膜光阻上。撕去膜面上的保护胶膜后,先以碳酸钠水溶液将膜面上未受光照的区域显影去除,再用盐酸及双氧水混合溶液将裸露出来的铜箔腐蚀去除,形成线路。最后再以氢氧化钠水溶液将功成身退的干膜光阻洗除。对于六层(含)以上的内层线路板以自动定位冲孔机冲出层间线路对位的铆合基准孔。 压合 完成后的内层线路板须以玻璃纤维树脂胶片与外层线路铜箔粘合。在压合前,内层板需先经黑(氧)化处理,使铜面钝化增加绝缘性;并使内层线路的铜面粗化以便能和胶片产生良好的粘合性能。叠合时先将六层线路﹝含﹞以上的内层线路
常见制程不良原因分1
常见制程不良原因分析 任何一个变压器在生产过程中,难免有或多或少的问题,发生的原因可能牵涉到设计,材料,工法,作业人员的疏忽…….等等,致制程出一些不良品,仅就我们本厂生产进的产品做一简单的探讨分析. 1.直流电阻(DCR)的问题 A.DCR过低 此种情形很少发生,造成可能的原因为: 1.线径用大了 2.规格订得不理想 3.圈数不足 4.用错骨架或DR CORE中径 虽然大部份的SPEC在DCR部份订MAX,当然也有SPEC是±?%,对于MAX的规格,往往会疏忽注意,因此我们在寻拉过程中就要留意我们的电阻,尤其是多根线并绕时的电阻,实测值是不是与指示卡定的规格相差很远.例如: SC5726-001A型号N3(2.3-1)=0.35*3根﹐DCR SPEC=20 MAX 正常值=12.8 断线1根后﹐DCR=19 .当遇到这样的情形的时候我们就要主动提出来要求工程收缩电阻范围. B.DCR过高 发生的原因: 1.线径用错 2.拉力过大,把线拉细 3.圈数太多 4.以mm(日规)线径取代了AWG(美规)线 5.铜皮引线焊点冷焊(包焊) 6.温度过高.铜线的温度系数是0.0039/℃,一奥姆的电阻,温度每上升一度其电阻增加0.0039Ω.(一般大家可 以接受的是25℃) 2.电感(INDUCTANCE)的问题 A.电感过高可能的原因 1.圈数是否多了 2.磁芯的选择是否错误 3.GAP是否磨太浅 4.磁芯来料本身的AL值过高 5.客户订的规格是否合理 6.没有GAP的磁芯组装含浸后电感一般不成线性略有上升 7.高μi值的磁芯,如滤波器类受烘干凡立水的温度影响,一般均会降低.所以我们通常采用80-90℃烘干式 或用自然阴干式. 8.对于有GAP磁芯若电感高一点点,可用砂纸磨磁芯中柱一下,以调整电感值符合规格. B.电感低的原因 1.圈数是否少了 2.磁芯的选择是否错误 3.GAP是否磨得太深 4.磁芯来料本身的AL值是否太低 5.客户订的规格是否合理 6.包磁芯胶纸太松,浸油后凡立水渗透到磁芯接合处
工艺研究与申报资料中常见问题分析
发布日期20071109 栏目化药药物评价>>化药质量控制 标题工艺研究与申报资料中常见问题分析 作者黄晓龙 部门 正文内容审评四部黄晓龙 近年来随着各种药害事件的不断发生,给广大人民的用药安全带来了极大的危害,也损害了整个制药行业的声誉。如何遏制这一事态的继续蔓延,从根本上保证人民的用药安全,引发了各有关方面的高度重视与积极思考。作为药品监管的环节之一,如何从药品研发的源头上采取必要的措施提高上市药品的质量,就成为我们必须思考的问题。回顾近年来国内药品注册申报资料发现,大部分研发单位在进行工艺研究时仍存在不少的问题,下面将针对一些常见问题谈如何加以解决。 问题之一是工艺研究不够全面和深入,不能保证申报工艺在大生产中的可行性。为解决此问题,申报单位首先要充分认识到工艺研究的重要性,并理解各工艺研究阶段的目的与意义,然后在实际研究过程中切实按照工艺研究的要求进行系统的研究:在小试阶段全面透彻地了解所采用工艺的各个方面,研究确定影响产品质量的关键工艺步骤与关键因素,并在此基础上进行工艺的筛选与优化;在中试阶段应模拟大生产的情况,根据小试研究的结果与已有的中试放大经验,在一定的规模上考察并确定拟在大生产中采用的仪器设备、工艺操作规范与操作参数范围、原材料与中间体的质控要求等;在工艺验证阶段则要在实际生产线上,按照中试放大确定的工艺考察大生产的可行性与重现性。最后再根据以上三个阶段的研究结果,综合确定拟上市药品的申报工艺。 问题之二是片面理解中试规模工艺研究的定义和目的,误认为只要产品的规模达到了一定的数量,如片剂达到了一万片即为中试规模。根据中试工艺研究的定义和目的可以知道,判断一个工艺是否达到了中试规模,主要是看该工艺是否真正模拟了大生产的实际情况,如设备、工艺流程、原材料的要求等,而所生产的样品数量仅是一个次要因素,并且样品数量也会随着品种的实际生产规模而变化,并不能所有的工艺都一概而论。根据ICHQ1A(R2)中的定义,中试规模的样品是指能够充分代表生产规模样品并模仿生产的实际情况而生产的样品。就固体口服制剂而言,其批量应为生产规模样品的十分之一或十万片(粒)(取其中的最大值)。例如,某片剂的工业化生产线的批量为一千万片,则中试规模的批量应为一百万片,而不是固定的十万片。这就进一步证明了判断中试规模的关键并不在于样品的数量。 问题之三是忽略工艺研究资料对药品技术评价的重要性,提供的相关申报资料过于简单。工艺研究作为药学研究的一部分,所研究确定的工艺的可控性与可行性直接关系到所生产药品的质量。如果工艺研究方面的申报资料过于简单,在药品注册前的技术评价中,就很难对申报工艺的可控性与可行性进行准确的评价,进而影响到对采用该工艺生产的药品的安全性与有效性的评价。从评价者的角度,要判断一个工艺的可行性,申报资料至少应包括以下几个方面的信息:①工艺设计的理论依据与文献;②小试工艺研究的综述与结论,包括对哪些工艺步骤与参数进行了研究与优化,具体的研究结果等;③中试放大研究的批次、规模、产品的质量,研究确定的仪器设备、工艺操作规范与操作参数范围、原材料与中间体的质控要求等;④工艺验证及结果;⑤对整个研究过程中所生产的批次、规模、产品的收率与质量等情况进行汇总;⑥对于制剂,还应提供剂型与处方设计的理论与实验依据、处方的筛选与优化过程、原辅料的来源与质量标准等;⑦最终确定的处方及详尽的工艺。只有在全面了解以上信息的基础上,药品技术审评人员才能分析判断所确定的申报工艺是否可控与可行。 总之,工艺研究是药品上市前研究的一个重要方面,只有经过详细、深入的工艺研究才
印刷电路板p c b制程的常见问题及解决方法
印刷电路板p c b制程的常见问题及解决方法 SANY标准化小组 #QS8QHH-HHGX8Q8-GNHHJ8-HHMHGN#
印刷电路板制程的常见问题及解决方法目录:
(一)图形转移工 艺……………………………………………………………… (2) (二)线路油墨工 艺……………………………………………………………… (4) (三)感光绿油工 艺……………………………………………………………… (5) (四)碳膜工 艺………………………………………………………… (7) (五)银浆贯孔工 艺……………………………………………………………… (8) (六)沉铜(P T H)工 艺………………………………………………………………… (9)
(七)电铜工 艺………………………………………………………… ……………………………1 1 (八)电镍工 艺………………………………………………………… ……………………………1 2 (九)电金工 艺………………………………………………………… ……………………………1 3 (十)电锡工 艺………………………………………………………… ……………………………1 4 (十一)蚀刻工艺……………………………………………………………… ………………………1 5 (十二)有机保焊膜工艺………………………………………………………………… ……………1 5
(十三)喷锡(热风整平)艺………………………………………………………………… ………1 6 (十四)压合工艺……………………………………………………………… (17) (十五)图形转移工艺流程及原 理……………………………………………………………… 20 (十六)图形转移过程的控 制……………………………………………………………… (24) (十七)破孔问题的探 讨……………………………………………………………… (28) (十八)软性电路板基 础……………………………………………………………… (33)
生产印制电路板的工艺流程简介
生产印制电路板的工艺流程简介 工厂生产印制电路板的工艺大致为:绘图→照相制版→感丝网→落料→图形转移→蚀刻→钻孔→刻板→孔化→抛光→镀金镀银→阻焊→助焊→修边→印字符图→出厂检验等15道工序。现分别简介如下: ①照相制版将用户提供的印制电路板导电图形图制成照相底片(照相底片也称工作底片,是用来把导电图形转印到印制电路板或丝网板的正片或负片)。 ②感丝网对用户提供的助焊图及字符图做网架,为对印制电路板做助焊、阻焊处理和印制字符图做准备。 ③落料根据图纸提供的印制电路板外形尺寸备板。 ④图形转移将导电图形由照相底片转移到印制电路板上。一般由感光机完成,将导电图形感光到已落好料的敷铜板上。 ⑤蚀刻俗称烂板,将感光好的敷铜板置于三氧化铁(Fe2Cl3)溶液或其他蚀刻液中腐蚀掉不需要的铜箔。 ⑥整板去毛刺,整形,开异形孔,初检。 ⑦刻板将未腐蚀干净的导电条、工艺线等用手工法除去。 ⑧孔化孔化,全称引线孔金属孔化。即在双面板或多层板引线孔和过孔内壁和基板两面上用电化学方法沉积金属,实现两个外层电路和内外层电路之间的电气连接。 ⑨抛光烘干后的表面处理,去除表面氧化层。
⑩镀金镀银根据用户要求,采用电或化学镀金或镀银,再抛光两次,清洗烘干。 ⑥阻焊采用丝网印制法,将阻焊剂涂覆在除焊盘和过孔盘以外的区域上。 ⑥助焊采用丝网印制法,在焊盘和过孔盘上上助焊剂。 ⑩印字符图采用丝网印制法,在印制电路板元件面上印上字符图。 ⑩修边将制好的印制电路板对外轮廓按尺寸进行加工。 ⑩检验对印制电路板进行目视检验(10倍放大镜)、印制图形连通性检验、绝缘电阻测量、可焊性试验、电镀层检验和粘合强度检验等。
高密度印制电路板(HDI)介绍.
高密度印制电路板(HDI)介绍 印刷电路板是以绝缘材料辅以导体配线所形成的结构性元件。在制成最终产品时,其上会安装积体电路、电晶体、二极体、被动元件(如:电阻、电容、连接器等)及其他各种各样的电子零件。藉著导线连通,可以形成电子讯号连结及应有机能。因此,印制电路板是一种提供元件连结的平台,用以承接联系零件的基的。 由于印刷电路板并非一般终端产品,因此在名称的定义上略为混乱,例如:个人电脑用的母板,称为主机板而不能直接称为电路板,虽然主机板中有电路板的存在但是并不相同,因此评估产业时两者有关却不能说相同。再譬如:因为有积体电路零件装载在电路板上,因而新闻媒体称他为IC板,但实质上他也不等同于印刷电路板。 在电子产品趋于多功能复杂化的前题下,积体电路元件的接点距离随之缩小,信号传送的速度则相对提高,随之而来的是接线数量的提高、点间配线的长度局部性缩短,这些就需要应用高密度线路配置及微孔技术来达成目标。配线与跨接基本上对单双面板而言有其达成的困难,因而电路板会走向多层化,又由于讯号线不断的增加,更多的电源层与接地层就为设计的必须手段,这些都促使从层印刷电路板(Multilayer Printed Circuit Board)更加普遍。 对于高速化讯号的电性要求,电路板必须提供具有交流电特性的阻抗控制、高频传输能力、降低不必要的幅射(EMI)等。采用Stripline、Microstrip的结构,多层化就成为必要的设计。为减低讯号传送的品质问题,会采用低介电质系数、低衰减率的绝缘材料,为配合电子元件构装的小型化及阵列化,电路板也不断的提高密度以因应需求。BGA (Ball Grid Array)、CSP (Chip Scale Package)、DCA (Direct Chip Attachment)等组零件组装方式的出现,更促印刷电路板推向前所未有的高密度境界。 凡直径小于150um以下的孔在业界被称为微孔(Microvia),利用这种微孔的几何结构技术所作出的电路可以提高组装、空间利用等等的效益,同时对于电子产品的小型化也有其必要性。 对于这类结构的电路板产品,业界曾经有过多个不同的名称来称呼这样的电路板。例如:欧美业者曾经因为制作的程序是采用序列式的建构方式,因此将这类的产品称为SBU (Sequence Build Up Process),一般翻译为“序列式增层法”。至于日本业者,则因为这类的产品所制作出来的孔结构比以往的孔都要小很多,因此称这类产品的制作技术为MVP (Micro Via Process),一般翻译为“微孔制程”。也有人因为传统的多层板被称为MLB (Multilayer Board),因此称呼这类的电路板为BUM (Build Up Multilayer Board),一般翻译为“增层式多层板”。 美国的IPC电路板协会其于避免混淆的考虑,而提出将这类的产品称为HDI (High Density Intrerconnection Technology)的通用名称,如果直接
生产印制电路板的工艺流程简介
生产印制电路板的工艺流程 简介 -标准化文件发布号:(9556-EUATWK-MWUB-WUNN-INNUL-DDQTY-KII
生产印制电路板的工艺流程简介 工厂生产印制电路板的工艺大致为:绘图→照相制版→感丝网→落料→图形转移→蚀刻→钻孔→刻板→孔化→抛光→镀金镀银→阻焊→助焊→修边→印字符图→出厂检验等15道工序。现分别简介如下:①照相制版将用户提供的印制电路板导电图形图制成照相底片(照相底片也称工作底片,是用来把导电图形转印到印制电路板或丝网板的正片或负片)。 ②感丝网对用户提供的助焊图及字符图做网架,为对印制电路板做助焊、阻焊处理和印制字符图做准备。 ③落料根据图纸提供的印制电路板外形尺寸备板。 ④图形转移将导电图形由照相底片转移到印制电路板上。一般由感光机完成,将导电图形感光到已落好料的敷铜板上。 ⑤蚀刻俗称烂板,将感光好的敷铜板置于三氧化铁(Fe2Cl3)溶液或其他蚀刻液中腐蚀掉不需要的铜箔。 ⑥整板去毛刺,整形,开异形孔,初检。 ⑦刻板将未腐蚀干净的导电条、工艺线等用手工法除去。 ⑧孔化孔化,全称引线孔金属孔化。即在双面板或多层板引线孔和过孔内壁和基板两面上用电化学方法沉积金属,实现两个外层电路和内外层电路之间的电气连接。 ⑨抛光烘干后的表面处理,去除表面氧化层。
⑩镀金镀银根据用户要求,采用电或化学镀金或镀银,再抛光两次,清洗烘干。 ⑥阻焊采用丝网印制法,将阻焊剂涂覆在除焊盘和过孔盘以外的区域上。 ⑥助焊采用丝网印制法,在焊盘和过孔盘上上助焊剂。 ⑩印字符图采用丝网印制法,在印制电路板元件面上印上字符图。 ⑩修边将制好的印制电路板对外轮廓按尺寸进行加工。 ⑩检验对印制电路板进行目视检验(10倍放大镜)、印制图形连通性检验、绝缘电阻测量、可焊性试验、电镀层检验和粘合强度检验等。
印刷电路板(P.C.B)制程的常见问题及解决方法(1)
印刷电路板(P.C.B)制程的常见问题及解决方 法 目录:
(一)图形转移工 艺………………………………………………………………………… ……………2(二)线路油墨工 艺……………………………………………………………………… ………………4(三)感光绿油工 艺………………………………………………………………………… ……………5(四)碳膜工 艺……………………………………………………………… (7) (五)银浆贯孔工 艺………………………………………………………………………… (8) (六)沉铜(P T H)工 艺…………………………………………………………………………… ………9
(七)电铜工 艺……………………………………………………………… ………………………1 1 (八)电镍工 艺………………………………………………………………… ……………………1 2 (九)电金工 艺…………………………………………………………………… …………………1 3 (十)电锡工 艺………………………………………………………………… ……………………14(十一)蚀刻工艺……………………………………………………………………… ………………1 5 (十二)有机保焊膜工艺………………………………………………………………………… ……1 5
(十三)喷锡(热风整平)艺………………………………………………………………………… 1 6 (十四)压合工艺……………………………………………………………………… (17) (十五)图形转移工艺流程及原理………………………………………………………………20 (十六)图形转移过程的控制……………………………………………………………………… 24 (十七)破孔问题的探讨……………………………………………………………………… (28) (十八)软性电路板基础………………………………………………………………………… (33) (十九)渗镀问题的解决方法……………………………………………………………………… 38
印制电路板常见结构
印制电路板常见结构以及PCB抄板PCB设计基础知识 印制电路板(PCB)的常见结构可以分为单层板(single Layer PCB)、双层板(Double Layer PCB)和多层板(Multi Layer PCB)三种。 一、单层板single Layer PCB 单层板(single Layer PCB)是只有一个面敷铜,另一面没有敷铜的电路板。元器件一般情况是放置在没有敷铜的一面,敷铜的一面用于布线和元件焊接,如图所示。 二、双层板Double Layer PCB 双层板(Double Layer PCB)是一种双面敷铜的电路板,两个敷铜层通常被称为顶层(Top Layer)和底层(Bottom Layer),两个敷铜面都可以布线,顶层一般为放置元件面,底层一般为元件焊接面,如图所示。 三、多层板Multi Layer PCB 多层板(Multi Layer PCB)就是包括多个工作层面的电路板,除了有顶层(Top Layer)和底层(Bottom Layer)之外还有中间层,顶层和底层与双层面板一样,中间层可以是导线层、信号层、电源层或接地层,层与层之间是相互绝缘的,层与层之间的连接往往是通过孔来实现的。以四层板为例,如图2 3 4 所示。这个四层板除了具有顶层和底层之外,内部还具有一个地层和一个图2 3 4 四层板结构 尽管Protel DXP支持72层板的设计,但在实际的应用中,一般六层板已经能够满足电路设计的要求,不必将电路板设计成更多层结构。 Prepreg&core
Prepreg:半固化片,又称预浸材料,是用树脂浸渍并固化到中间程度(B 阶)的薄片材料。半固化片可用作多层印制板的内层导电图形的黏结材料和层间绝缘。在层压时,半固化片的环氧树脂融化、流动、凝固,将各层电路毅合在一起,并形成可靠的绝缘层。 core:芯板,芯板是一种硬质的、有特定厚度的、两面包铜的板材,是构成印制板的基础材料。 通常我们所说的多层板是由芯板和半固化片互相层叠压合而成的。而半固化片构成所谓的浸润层,起到粘合芯板的作用,虽然也有一定的初始厚度,但是在压制过程中其厚度会发生一些变化。 通常多层板最外面的两个介质层都是浸润层,在这两层的外面使用单独的铜箔层作为外层铜箔。外层铜箔和内层铜箔的原始厚度规格,一般有0.5OZ、1OZ、2OZ(1OZ约为35um或1.4mil)三种,但经过一系列表面处理后,外层铜箔的最终厚度一般会增加将近1 OZ左右。内层铜箔即为芯板两面的包铜,其最终厚度与原始厚度相差很小,但由于蚀刻的原因,一般会减少几个um。 多层板的最外层是阻焊层,就是我们常说的“绿油”,当然它也可以是黄色或者其它颜色。阻焊层的厚度一般不太容易准确确定,在表面无铜箔的区域比有铜箔的区域要稍厚一些,但因为缺少了铜箔的厚度,所以铜箔还是显得更突出,当我们用手指触摸印制板表面时就能感觉到。 当制作某一特定厚度的印制板时,一方面要求合理地选择各种材料的参数,另一方面,半固化片最终成型厚度也会比初始厚度小一些。下面是一个典型的6层板叠层结构(iMX255coreboard):
制程常见问题分析
SMT常见工艺问题简述(已点击1239次) 以下是我结合自己多年的实践经验,把零星收集的一些与工艺有关的文章经过整理后所得。希望对大家有一点帮助。 SMT常见工艺问题概述(一) 锡膏制程 (一)普通锡膏(63/37) 普通锡膏于制程中常见的工艺问题主要为以下几种: 元件竖立,短路,冷焊,偏移,锡珠 下面就这几种常见的现象简述一下控制的心得体会。 1.元件竖立 元件竖立又叫“曼哈顿效应“。主要是由于元件两端焊锡浸润不均匀,因此,熔融焊料的不够均衡的表面张力拉力就施加在元件的两端上,引发此类不良的原因较多,但主要有三大类。即: A.元件不良:元件两端电极氧化或附有异物,导致焊锡时上锡不良;基板材料导热性差,基板的厚度均匀性差;焊盘的热容量差异较大,焊盘的可焊性差异较大;锡膏中助焊剂的均匀性差或活性差。B.设计缺失:焊盘铜箔大小不一或一端连接有接地等较大的铜箔,造成回流时焊盘两端受热不均匀。C.制程缺失:制程缺失的因素很多。如两个焊盘上的锡膏厚度差异较大,锡膏太厚,印刷精度差,错位严重;预热温度太低;贴装精度差,元件偏移严重等。 以上三种成因中第一项就不用赘述了。只要严把进料和储存两关就好了。下面简述一下二,三两项成因的控制方法。 ——对于设计上的缺失,长期办法当然是修改设计方案。短期办法或没法修改方案的情况下,就需要从二个方面入手。一是通过更改钢网的开口设计来达到控制的目的。即将铜箔较小的一端焊盘网孔局部加大,使之与大铜箔大小比例为1:1。从而降低焊盘两端锡膏回流时的时间差;二是修改炉温曲线,即延长升温区(回流前)的时间,降低升温速率,使整块PCB上各点的温度尽量保持平衡。从而避免因回流时的温度不平衡而导致元件受力竖起。 ——制程缺失产生的原因就更多了。一个公司制程品质的好坏不在于有多么先进的设备,关键在于制程控制的方法和管理的力度上。好的控制方法应该从原材料的采购,进料的检验,储存环境和储存条件的设定等做起,每一环节都切实履行自己的职责,再到原物料的使用(包括使用环境,使用条件等工艺参数的设定)和设备的维护保养,校正以及参数设定,操作人员的培训和管理等,需要一个贯穿始终,环环相扣,职责分工明确又相互关联的控制系统。在各个职能部门和相关工作人员的通力协作下才能臻至理想状态。这一点,每个公司有每个公司的做法和不同的控制体系。具体的操作就是仁者见仁,智者见智了。 2.短路 短路这种不良现象多发于细间距IC的引脚之间,所以又叫“桥接“。当然也有CHIP件之间发生短路现象的,那是极少数。下面就细间距IC引脚间的桥接问题浅谈它的诚因及解决方法。 桥接现象多发于0.5mm及以下间距的IC引脚间,因其间距较小,故模板设计不当或印刷稍有疏漏就极易产生。 A.模板 依据IPC-7525钢网设计指南要求,为保证锡膏能顺畅地从网板开孔中释放到PCB焊盘上,在网板的开孔方面,主要依赖于三个因素: 1、)面积比/宽厚比>0.66 2、)网孔孔壁光滑。制作过程中要求供应商作电抛光处理。 3、)以印刷面为上面,网孔下开口应比上开口宽0.01mm或0.02mm,即开口成倒锥形,便于焊膏有效释放,同时可减少网板清洁次数。 具体的说也就是对于间距为0.5mm及以下的IC,由于其PITCH小,容易产生桥接,钢网开口方式长度方
印刷电路板制程简介
一、印刷电路板制程简介: 在电子装配中,印刷电路板(Printed Circuit Boards)是个关键零件。它搭载其它的电子零件并连通电路,以提供一个安稳的电路工作环境。如以其上电路配置的情形可概分为三类: 【单面板】将提供零件连接的金属线路布置于绝缘的基板材料上,该基板同时也是安装零件的支撑载具。 【双面板】当单面的电路不足以提供电子零件连接需求时,便可将电路布置于基板的两面,并在板上布建通孔电路以连通板面两侧电路。 【多层板】在较复杂的应用需求时,电路可以被布置成多层的结构并压合在一起,并在层间布建通孔电路连通各层电路。
二、制程说明:
【内层线路】铜箔基板先裁切成适合加工生产的尺寸大小。基板压膜前通常需先用刷磨、微蚀等方法将板面铜箔做适当的粗化处理,再以适当的温度及压力将干膜光阻密合贴附其上。将贴好干膜光阻的基板送入紫外线曝光机中曝光,光阻在底片透光区域受紫外线照射后会产生聚合反应(该区域的干膜在稍后的显影、蚀铜步骤中将被保留下来当作蚀刻阻剂),而将底片上的线路影像移转到板面干膜光阻上。撕去膜面上的保护胶膜后,先以碳酸钠水溶液将膜面上未受光照的区域显影去除,再用盐酸及双氧水混合溶液将裸露出来的铜箔腐蚀去除,形成线路。最后再以氢氧化钠水溶液将功成身退的干膜光阻洗除。对于六层(含)以上的内层线路板以自动定位冲孔机冲出层间线路对位的铆合基准孔。 【多层板压合】完成后的内层线路板须以玻璃纤维树脂胶片与外层线路铜箔黏合。在压合前,内层板需先经黑(氧)化处理,使铜面钝化增加绝缘性;并使内层线路的铜面粗化以便能和胶片产生良好的黏合性能。叠合时先将六层线路﹝含﹞以上的内层线路板用铆钉机成对的铆合。再用盛盘将其整齐叠放于镜面钢板之间,送入真空压合机中以适当之温度及压力使胶片硬化黏合。压合后的电路板以X光自动定位钻靶机钻出靶孔做为内外层线路对位的基准孔。并将板边做适当的细裁切割,以方便后续加工。 【钻孔】将电路板以CNC钻孔机钻出层间电路的导通孔道及焊接零件的固定孔。钻孔时用插梢透过先前钻出的靶孔将电路板固定于钻孔机床台上,同时加上平整的下垫板(酚醛树酯板或木浆板)与上盖板(铝板)以减少钻孔毛头的发生。 【镀通孔】【一次铜】 在层间导通孔道成型后需于其上布建金属铜层,以完成层间电路的导通。先以重度刷磨及高压冲洗的方式清理孔上的毛头及孔中的粉屑,再以高锰酸钾溶液去除孔壁铜面上的胶渣。在清理干净的孔壁上浸泡附着上锡钯胶质层,再将其还原成金属钯。将电路板浸于化学铜溶液中,借着钯金属的催化作用将溶液中的铜离子还原沉积附着于孔壁上,形成通孔电路。再以硫酸铜浴电镀的方式将导通孔内的铜层加厚到足够抵抗后续加工及使用环境冲击的厚度。 【外层线路】【二次铜】 在线路影像转移的制作上如同内层线路,但在线路蚀刻上则分成正片与负片两种生产方式。负片的生产方式如同内层线路制作,在显影后直接蚀铜、去膜即算完成。正片的生产方式则是在显影后再加镀二次铜与锡铅(该区域的锡铅在稍后的蚀铜步骤中将被保留下来当作蚀刻阻剂),去膜后以碱性的氨水、氯化铜混合溶液将裸露出来的铜箔腐蚀去除,形成线路。最后再以锡铅剥除液将功成身退的锡铅层剥除(在早期曾有保留锡铅层,经重镕后用来包覆线路当作保护层的做
印刷线路板入门知识及生产工艺流程
印刷线路板入门知识及生产工艺流程 印刷线路板,英文缩写P CB(是Pr inted Circuie Board的简称),由于印制线路板基本是以环氧树脂为基材的,因此业界反到不提其全称环氧印刷线路板,通常只提印刷线路板,或英文缩写P CB。据中国环氧树脂行业协会专家介绍,通常把在绝缘材上,按预定设计制成印制线路、印制元件或两者组合而成的导电图形称为印制电路。在绝缘基材上提供元器件之间电气连接的导电图形,称为印制线路。这样就把印制电路或印制线路的成品板称为印制线路板,亦称为印制板或印制电路板。而这个绝缘基材就是环氧树脂。 环氧印刷线路板,几乎我们能见到的电子设备都离不开它,小到电子手表、计算器、通用电脑,大到计算机、通迅电子设备、军用武器系统,只要有集成电路等电子无器件,它们之间电气互连都要用到它。它提供集成电路等各种电子元器件固定装配的机械支撑、实现集成电路等各种电子元器件之间的布线和电气连接或电绝缘、提供所要求的电气特性,如特性阻抗等。同时为自动锡焊提供阻焊图形;为元器件插装、检查、维修提供识别字符和图形。 它是如何制造出来的呢?我们打开通用电脑的健盘就能看到一张软性薄膜(挠性的绝缘基材),印上有银白色(银浆)的导电图形与健位图形。因为通用丝网漏印方法得到这种图形,所以我们称这种印制线路板为挠性银浆印制线路板。而我们去电脑城看到的各种电脑主机板、显卡、网卡、调制解调器、声卡及家用电器上的环氧印制电路板就不同了。它所用的基材是由纸基(常用于单面)或玻璃布基(常用于双面及多层),预浸酚醛或环氧树脂,表层一面或两面粘上覆铜簿再层压固化而成。这种线路板覆铜簿板材,我们就称它为刚性板。再制成印制线路板,我们就称它为刚性印制线路板。 单面有印制线路图形的,我们称单面印制线路板;双面有印制线路图形,再通过孔的金属化进行双面互连形成的印制线路板,我们就称其为双面板。如果用一块双面作内层、二块单面作外层或二块双面作内层、二块单面作外层的印制线路板,通过定位系统及绝缘粘结材料交替在一起且导电图形按设计要求进行互连的印制线路板就成为四层、六层印制电路板了,也称为多层印制线路板。现在已有超过100层的实用环氧印制线路板了。 环氧印制线路板的生产过程较为复杂,它涉及的工艺范围较广,从简单的机械加工到复杂的机械加工,有普通的化学反应还有光化学电化学热化学等工艺,计算