教你任何设置注塑机合模参数
第43:注塑成型条件设定方法

第43问注塑成型条件设定方法一、开合模参数的设定方向:连续生产中,必须考虑工艺在今后生产中的稳定性,所以,开关模的参数设定必须保证开合模动作平稳设备不晃荡。
在产品取出方便的条件下,开关模位置越短越好。
低压保护设定,保证产品在模腔里合模起不到高压而报警,确保模具不会被压坏;高压锁模力最好设定低些,保证PL面不出披锋为止;设定太高,相反会有一定的坏处。
锁模力太高,易损坏模具;PL面排气不良,产品易困气烧焦;产品内应力大,出模后才可弃放;影响产品尺寸等。
具体的设定技巧:1.合模参数设定:以高压、慢速起步,短行程;中压、快速运行,导柱惯性到导套前;低压、匀速靠近腔面前;微压、低速惯性接触母模;高压、中速起高压合模。
有行位的模具,开模速度不可太快;2.开模参数设定:以高压、慢速离开母模;中压、快速运行惯性至终点前;高压、低速到开模终点。
3.低压保护位置与低压压力值的设定:接触模具的低压、低速设定必须能推动模具(特别是有弹簧或有行位的模具),但力量不能大于压坏产品的力(产品厚度被压至到原来的4/5所需要的力量);低压保护要调好,因为新模成品的形状与脱模情况不太了解;有抽蕊以及绞芽的模具,要先行手动试验,功能正常后方可用自动;4.高压锁模位置与高压锁模力的设定:高压位置设定方法。
(先不设定高压锁模力值,用前面设定的所有参数合模,模具会停在一个位置上,显示位置值将是实际的高压位置,在这位置上加上0.5㎜~1㎜就行)。
确认合模力是否充足:合模力(g)≥成形面投影面积(cm²)×模具内的平均压力(通常为400kg/cm²)。
合模力的大小计算可按《合模力设定方法》进行。
直压式机台需注意锁模力是否足够,肘节式机台注意十字头是否伸直,以防射出时模具后退,而出现大毛边涨坏模具;锁模力设定依据:最小锁模力=最高射出压力×(产品的投影面积+流道的投影面积);实际锁模力=最小锁模力×(1+5%~20%),再慢慢加到不出现毛边为止,闭模到30~50mm时,速度要转为慢速。
注塑机参数设置
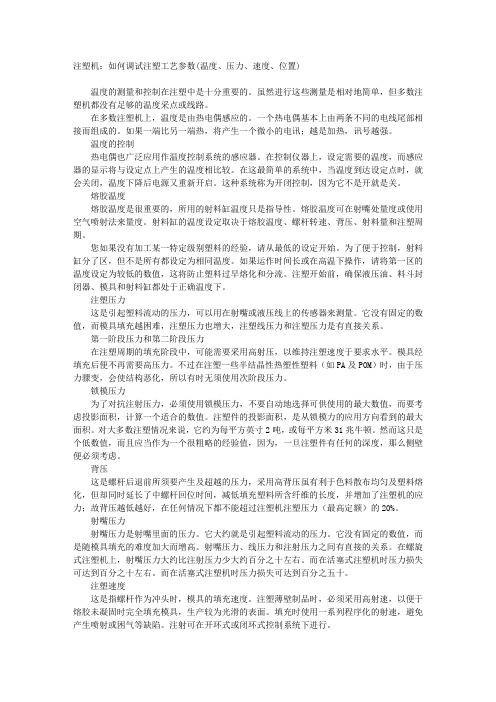
注塑机:如何调试注塑工艺参数(温度、压力、速度、位置)温度的测量和控制在注塑中是十分重要的。
虽然进行这些测量是相对地简单,但多数注塑机都没有足够的温度采点或线路。
在多数注塑机上,温度是由热电偶感应的。
一个热电偶基本上由两条不同的电线尾部相接而组成的。
如果一端比另一端热,将产生一个微小的电讯;越是加热,讯号越强。
温度的控制热电偶也广泛应用作温度控制系统的感应器。
在控制仪器上,设定需要的温度,而感应器的显示将与设定点上产生的温度相比较。
在这最简单的系统中,当温度到达设定点时,就会关闭,温度下降后电源又重新开启。
这种系统称为开闭控制,因为它不是开就是关。
熔胶温度熔胶温度是很重要的,所用的射料缸温度只是指导性。
熔胶温度可在射嘴处量度或使用空气喷射法来量度。
射料缸的温度设定取决于熔胶温度、螺杆转速、背压、射料量和注塑周期。
您如果没有加工某一特定级别塑料的经验,请从最低的设定开始。
为了便于控制,射料缸分了区,但不是所有都设定为相同温度。
如果运作时间长或在高温下操作,请将第一区的温度设定为较低的数值,这将防止塑料过早熔化和分流。
注塑开始前,确保液压油、料斗封闭器、模具和射料缸都处于正确温度下。
注塑压力这是引起塑料流动的压力,可以用在射嘴或液压线上的传感器来测量。
它没有固定的数值,而模具填充越困难,注塑压力也增大,注塑线压力和注塑压力是有直接关系。
第一阶段压力和第二阶段压力在注塑周期的填充阶段中,可能需要采用高射压,以维持注塑速度于要求水平。
模具经填充后便不再需要高压力。
不过在注塑一些半结晶性热塑性塑料(如PA及POM)时,由于压力骤变,会使结构恶化,所以有时无须使用次阶段压力。
锁模压力为了对抗注射压力,必须使用锁模压力,不要自动地选择可供使用的最大数值,而要考虑投影面积,计算一个适合的数值。
注塑件的投影面积,是从锁模力的应用方向看到的最大面积。
对大多数注塑情况来说,它约为每平方英寸2吨,或每平方米31兆牛顿。
注塑成型生产时的各项参数设定

注塑成型生产时的各项参数设定1、事前确认及准备设定⑴确认材料干燥、模温及加热筒温度是否被正确设定并达到可加工状态。
⑵检查开闭模及顶出的动作和距离设定。
⑶射出压力(P1)设定在最大值的60%。
⑷保持压力(PH)设定在最大值的30%。
⑸射出速度(V1)设定在最大值的40%。
⑹螺杆转速(VS)设定在约60RPM。
⑺背压(PB)设定在约10kg/cm2。
⑻松退约设定在3mm。
⑼保压切换的位置设定在螺杆直径的30%。
例如φ100mm的螺杆,则设定30mm。
⑽计量行程比计算值稍短设定。
⑾射出总时间稍短,冷却时间稍长设定。
2、手动运转参数修正⑴闭锁模具(确认高压的上升),射出座前进。
⑵以手动射出直到螺杆完全停止,并注意停止位置。
⑶螺杆旋退进料。
⑷待冷却后开模取出成型品。
⑸重复⑴~⑷的步骤,螺杆最后停止在螺杆直径的10%~20%的位置,而且成型品无短射、毛边及白化,或开裂等现象。
3、半自动运转参数的修正⑴计量行程的修正[计量尽头]将射出压力提高到99%,并把保压暂调为0,将计量尽头S0向前调到发生短射,再向后调至发生毛边,以其中心点为选择位置。
⑵出速度的修正把PH回复到原水准,将射出速度上下调整,找启程生短射及毛边的个别速度,以其中心点为适合速度[本阶段亦可进入以多段速度对应外观问题的参数设定]。
⑶保持压力的修正上下调整保持压力,找启程生表面凹陷及毛边的个别压力,以其中心点为选择保压。
⑷保压时间[或射出时间]的修正渐渐延长保持时间,直至成型品重量明显稳定为明适选择。
⑸冷却时间的修正渐渐调降冷却时间,并确认下列情况可以充足:1、成型品被顶出、夹出、修整、包装不会白化、凸裂或变形。
2、模温能平衡稳定。
肉厚4mm以上制品冷却时间的简易算法:①理论冷却时间=S(1+2S)…….模温60度以下。
②理论冷却时间=1.3S(1+2S)…….模具60度以上[S表示成型品的最大肉厚]。
⑹塑化参数的修正①确认背压是否需要调整;②调整螺杆转速,使计量时间稍短于冷却时间;③确认计量时间是否稳定,可尝试调整加热圈温度的梯度。
教你任何设置注塑机合模参数

教你任何设置注塑机合模参数一,开始合模:1、开始合模压力:初设置值参考为25,当此压力过小而导致速度过慢时,可尝试增加速度,此压力过小,而使速度无法提高至需要时速度每次加+5尝试,注意,该压力设置较大时,会使动模板瞬间加高压改变静止状态变运动,至使动模板孔与拉杆产生巨大的摩擦力,久之加快了机器动模板孔与拉杆的磨损,影响到动模板运动的平稳性与精密度的下降,可能影响到个别对合模机构的精密要求较高模具的生产。
2、开始合模速度:看实际,不过要注意动作不宜过快,该速度要与下一段合模动作具有连贯性的运动,而不是出现明显的停顿动作切换,最好是速度设置高,压力设置低,由压力控制速度。
二,低压合模:由低压低速推动模具,由需要安全保护的距离开始至模具完全闭合终止1、低压合模速度:看实际,速度要慢,过快的速度,就算有设置了低压,惯性运动仍然有巨大的撞击破坏力。
滑快位置偏移、顶针断出、、、、等出现意外硬障碍物时,而进入合模动作,在有效的低压慢度的合模保护参数条件之下,大大减小撞击的损伤。
其实可以这个速度为几十,然后不动它,再把压力开始调得很低比如5进行测试,以压力控制速度,再一步步加压至适合的合模保护速度。
2、低压合模压力:可以先把速度调得很高,压力调得很低例如5进行合模测试,因为压力低,就算速度设置很大,失去压力的支持,合模速度也不会很快的,以压力控制速度,在5的基础上,一点点往上加至理想的合模保护速度,以最低的压力合模。
3、低压合模开始位置:(即上一段合模终止位置)这个要根据模具大小与结构而设置大小差异较大的数值,一般为模具闭合前的5-20厘米之间,这个位置大家看着办。
很多人就是设置模具合得太近,就才开始用低压,应该提前得到低压保护的距离受到上一段较大压力速度冲击合模,滑快位置偏移、顶针断出、、、、等出现意外硬障碍物时,快猛撞击,这时低压保护无效,来迟了,(重点核心)、、、、4、低压合模终止位置(即高压锁模开始位置):此参数为模具刚好刚完全闭合的位置,即动模板前进已经到尽头停止了,调试时先调好低压压力和速度,再将位置设置为0,关门手动合模测试得出一个低压合模完全闭合位置数值,比如这个数值是2.2,这个数值的大小受电子尺设置调整、调模松紧、合模压力大小影响,并且这个数值会受到机器精度和模具表面细小杂物的影响等原因影响,每次合模可能会有小小变动,所以要将终止位置设置稍大一点点比如加0.2设置为2.4(参考加0.1-0.3),以最低的位置,精确保护模具,如果不把低压合模测试获得的位置数值设置大一点点的话,直接就用2.2,可能经常会出现低压合模位置大于2.2,低压位置结束不了而无法转到高压锁模。
注塑成型机的各项参数设定步骤
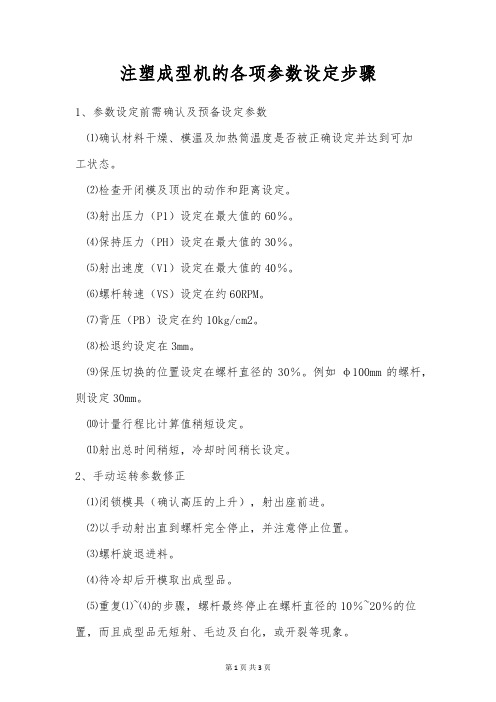
注塑成型机的各项参数设定步骤1、参数设定前需确认及预备设定参数⑴确认材料干燥、模温及加热筒温度是否被正确设定并达到可加工状态。
⑵检查开闭模及顶出的动作和距离设定。
⑶射出压力(P1)设定在最大值的60%。
⑷保持压力(PH)设定在最大值的30%。
⑸射出速度(V1)设定在最大值的40%。
⑹螺杆转速(VS)设定在约60RPM。
⑺背压(PB)设定在约10kg/cm2。
⑻松退约设定在3mm。
⑼保压切换的位置设定在螺杆直径的30%。
例如φ100mm的螺杆,则设定30mm。
⑽计量行程比计算值稍短设定。
⑾射出总时间稍短,冷却时间稍长设定。
2、手动运转参数修正⑴闭锁模具(确认高压的上升),射出座前进。
⑵以手动射出直到螺杆完全停止,并注意停止位置。
⑶螺杆旋退进料。
⑷待冷却后开模取出成型品。
⑸重复⑴~⑷的步骤,螺杆最终停止在螺杆直径的10%~20%的位置,而且成型品无短射、毛边及白化,或开裂等现象。
3、半自动运转参数的修正⑴计量行程的修正[计量终点] 将射出压力提高到99%,并把保压暂调为0,将计量终点S0向前调到发生短射,再向后调至发生毛边,以其中间点为选择位置。
⑵出速度的修正把PH回复到原水准,将射出速度上下调整,找出发生短射及毛边的个别速度,以其中间点为适宜速度[本阶段亦可进入以多段速度对应外观问题的参数设定]。
⑶保持压力的修正上下调整保持压力,找出发生表面凹陷及毛边的个别压力,以其中间点为选择保压。
⑷保压时间[或射出时间]的修正逐步延长保持时间,直至成型品重量明显稳定为明适选择。
⑸冷却时间的修正逐步调降冷却时间,并确认下列情况可以满足:1、成型品被顶出、夹出、修整、包装不会白化、凸裂或变形。
2、模温能平衡稳定。
肉厚4mm以上制品冷却时间的简易算法:①理论冷却时间=S(1+2S)…….模温60度以下。
②理论冷却时间=1.3S(1+2S)…….模具60度以上[S表示成型品的最大肉厚]。
⑹塑化参数的修正①确认背压是否需要调整;②调整螺杆转速,使计量时间稍短于冷却时间;③确认计量时间是否稳定,可尝试调整加热圈温度的梯度。
注塑机的参数设置
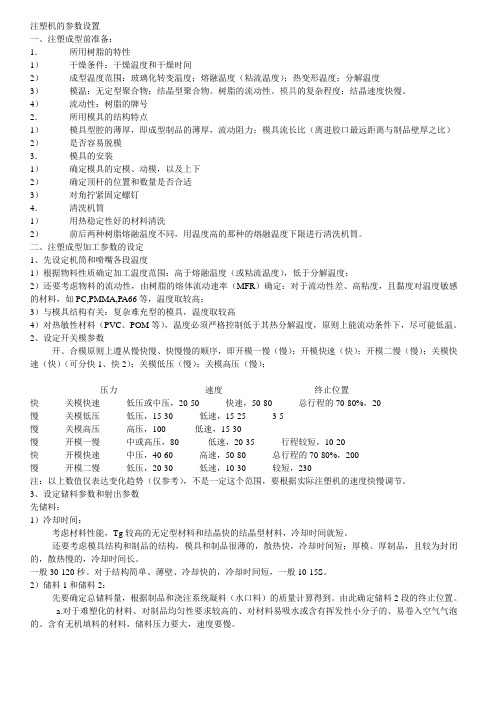
注塑机的参数设置一、注塑成型前准备:1.所用树脂的特性1)干燥条件:干燥温度和干燥时间2)成型温度范围:玻璃化转变温度;熔融温度(粘流温度);热变形温度;分解温度3)模温:无定型聚合物;结晶型聚合物。
树脂的流动性。
模具的复杂程度;结晶速度快慢。
4)流动性:树脂的牌号2.所用模具的结构特点1)模具型腔的薄厚,即成型制品的薄厚,流动阻力;模具流长比(离进胶口最远距离与制品壁厚之比)2)是否容易脱模3.模具的安装1)确定模具的定模、动模,以及上下2)确定顶杆的位置和数量是否合适3)对角拧紧固定螺钉4.清洗机筒1)用热稳定性好的材料清洗2)前后两种树脂熔融温度不同,用温度高的那种的熔融温度下限进行清洗机筒。
二、注塑成型加工参数的设定1、先设定机筒和喷嘴各段温度1)根据物料性质确定加工温度范围:高于熔融温度(或粘流温度),低于分解温度;2)还要考虑物料的流动性,由树脂的熔体流动速率(MFR)确定:对于流动性差、高粘度,且黏度对温度敏感的材料,如PC,PMMA,PA66等,温度取较高;3)与模具结构有关:复杂难充型的模具,温度取较高4)对热敏性材料(PVC、POM等),温度必须严格控制低于其热分解温度,原则上能流动条件下,尽可能低温。
2、设定开关模参数开、合模原则上遵从慢快慢、快慢慢的顺序,即开模一慢(慢);开模快速(快);开模二慢(慢);关模快速(快)(可分快1、快2);关模低压(慢);关模高压(慢);压力速度终止位置快关模快速低压或中压,20-50 快速,50-80 总行程的70-80%,20慢关模低压低压,15-30 低速,15-25 3-5慢关模高压高压,100- 低速,15-30慢开模一慢中或高压,80- 低速,20-35 行程较短,10-20快开模快速中压,40-60 高速,50-80 总行程的70-80%,200慢开模二慢低压,20-30 低速,10-30 较短,230注:以上数值仅表达变化趋势(仅参考),不是一定这个范围,要根据实际注塑机的速度快慢调节。
注射机的参数设定.
加工温度范围 180-250℃ 190-260℃ 175-260℃ 150-235℃ 230-290℃ 260-315 ℃ 230-290℃ 180-260℃ 270-300℃
分解温度(空气中) 270℃ 275℃ 305℃ 300℃ 300℃ 310℃ 300℃ 270℃ 320℃
5
注塑机主要参数的设定
15
注塑时间
注塑时间就是施加压力于螺杆的时间,包含塑 料的流动、模具充填、保压所需的时间;因此, 注塑时间、注塑速度和注塑压力都是重要的成型 条件,至于寻找正确的注塑时间可以用两种方法 进行:外观设定方法和重量设定方法。
16
射胶位置
射胶位置是注塑工艺中最重要的参数之一,射胶位 置一般是根据塑件和水口的总重量来确定的,有时 要根据所用的塑料种类、模具结构、产品质量等来 合理设定各段射胶的位置。
20
开模行程
A、二板模的开模行程
21
开模行程
B、三板模的开模行程
22
由于加工温度范围是指塑料在粘流态区域内可以进行注塑或挤出成型的温度因此可以视为炉嘴及出料炉的温度只有当塑料达到这个温度时才能顺利成加工温度范围分解温度空气中聚苯乙烯9015018025027095137190260275高压聚乙烯125110175260305低压聚乙烯12513015023530020164230290300665022526031550265230290300有机玻璃105180180260270聚碳酸酯150250270300320温度应根据塑料成型特性并考虑模具及制品结构特点而相应设定
4
注塑机主要参数的设定
常用塑料的加工温度范围如下表所示:
塑料 聚苯乙烯
ABS 高压聚乙烯 低压聚乙烯
注塑成型工艺参数的设置及其调整方法
注塑成型工艺参数的设置及其调整方法注塑成型工艺参数的设置及其调整方法一、注塑注塑成型工艺流程成型工艺流程成型工艺流程可以简单的表示如下可以简单的表示如下可以简单的表示如下::上一周期——闭模——填充——保压——回胶——冷却——开模——脱模——下一周期在填充保压降段,模腔压力随时间推移而上升,填充满型腔之后压力将保持在一个相对静态的状态,以补充由于收缩而产生的胶量不足,另外此压力可以防止由于注射的降低而产生的胶体倒流现象,这就是保压阶段,保压完了之后模腔压力逐渐下降,并随时间推移理论上可以降到零,但实际并不为零,所以脱模之后制品内部内存内应力,因而有的产品需经过后处理,清除残存应力。
所谓应力,就是来傅高子链或者链段自由运动的力,即弯曲变形,应力开裂、缩孔等。
二、注塑注塑成型成型成型的主要参数的主要参数1、料筒温度注塑胶料温度,熔体温度对熔体的流动性能起主要作用,由于塑胶没有具体的熔点,所谓熔点是一个熔融状态下的温度段,塑胶分子链的结构与组成不同,因而对其流动性的影响也不同,刚性分子链受温度影响较明显,如PC 、PPS 等,而柔性分子链如:PA 、PP 、PE 等流动性通过改变温度并不明显,所以应根据不同的材料来调校合理的注塑温度。
2、注射速度注射速度是熔体在炮筒内(亦为螺杆的推进速度)的速度(MM/S )注射速度决定产品外观、尺寸、收缩性,流动状况分布等,一般为先慢——快——后慢,即先用一个较的速度是熔体更过主流道,分流道,进浇口,以达到平衡射胶的目的,然后快速充模方式填充满整个模腔,再以较慢速度补充收缩和逆流引起的胶料不足现象,直到浇口冻结,这样可以克服烧焦,气纹,缩水等品质不良产生。
3、注射压力注射压力是熔体克服前进所需的阻力,直接影响产品的尺寸,重量和变形等,不同的塑胶产品所需注塑压力不同,对于象PA 、PP 等材料,增加压力会使其流动性显著改善,注射压力大小决定产品的密度,即外观光泽性。
4、模具温度模具温度,有些塑胶料由于结晶化温度高,结晶速度慢,需要较高模温,有些由于控制尺寸和变形,或者脱模的需要,要较高的温度或较低温度,如PC 一般要求60度以上,而PPS 为了达到较好的外观和改善流动性,模温有时需要160度以上,因而模具温度对改善产品的外观、变形、尺寸,胶模方面有不可抵估的作用。
注塑机合模参数设置的要求及注意事项
注塑机合模参数设置的要求及注意事项1.合模速度要控制在合理范围内。
合模速度过快会造成模具受力过大,容易导致模具损坏或者产生合模不良的情况;合模速度过慢则会延长注塑周期,影响生产效率。
因此,需要根据具体的注塑产品和模具情况,合理设置合模速度。
2.合模压力要适当调整。
合模压力过大会造成模具受力过大,容易导致模具变形或破裂;合模压力过小则会导致合模不紧密,产生塑件变形或者毛刺。
因此,需要根据塑件的材料、形状和尺寸等情况,合理设置合模压力。
3.合模位置要准确调整。
合模位置不准确会导致模具碰撞、模具破裂或者塑件变形。
因此,在设置合模位置时,需要根据模具和注塑机的具体情况,进行准确调整。
4.合模时间要合理控制。
合模时间过长会延长注塑周期,影响生产效率;合模时间过短则容易导致注塑产品质量不良。
因此,需要根据具体的注塑产品和模具情况,合理设置合模时间。
1.严格遵守注塑机的操作规程和操作流程,确保合模参数的设置符合机器的要求和安全标准。
2.在设置合模参数之前,需要对注塑机和模具进行检查和维护,确保设备和模具的良好状态。
3.根据注塑产品的要求,选择合适的合模速度、压力、位置和时间等参数,并进行逐步调整和试模,根据试模效果进行调整,确保注塑产品的质量和尺寸的稳定性。
4.合模过程中要注意观察合模动作和塑件的成形情况,及时调整合模参数,以确保合模过程的稳定性和塑件的质量。
5.注塑机合模参数设置需要经验丰富的操作工进行操作,对于初学者来说,可以请教经验丰富的技术人员进行指导。
总之,注塑机合模参数的合理设置对于注塑过程的顺利进行和产品质量的保证具有重要意义。
需要根据具体的产品要求和模具情况,选择合适的合模速度、压力、位置和时间等参数,并进行逐步调整和试模,以确保注塑产品的质量和生产效率的提高。
同时,需要严格遵守操作规程和注意操作安全,确保注塑机和模具的正常运行。
注塑机参数及安全调试指引
注塑机参数及安全调试指引(德马格)(总5页)--本页仅作为文档封面,使用时请直接删除即可----内页可以根据需求调整合适字体及大小--注塑机安全调试指引前言:为了更规范、更合理、更快速地完成注塑工艺参数调试,提高注塑机和模具使用寿命、减少修机和修模时间、减少机位人手、减少耗材,提升产品质量和提高生产效率,最终确保生产顺利和稳定,特制定此份注塑机安全调试指引。
一:注塑生产流程图生产流程图二:上模机台型号与模具大小是否匹配上模前需要根据模具大小,与机台容模厚度是否匹配,不可出现小机台上大模或大机台上很小的模。
按以下要求执行:1/2容模宽度≤模具宽度≤容模宽度上模前准备根据模具长度,将注塑机容模厚度设定在合适位置(较模具长度稍长即可),并将机台调至开模状态,之后将安全门打开;根据模具宽度,对于机台固定板上因夹马定位螺丝挡住上模的,则需要先将螺丝拧下来,往外移至合适位置。
最后将机械手调至外端,并将机台马达关闭。
调整容模厚度要求如下:将注塑机调到手动状态,合模,容模厚度是否与模具长度匹配,对于过短或过长,则需将注塑机打到调试状态,将容模厚度调试到与模具长度匹配为止。
(需要设定调试的速度为最大速度的10%-15%,方可进行容模厚度的调试)。
吊模将模具从地面或叉车上吊入机仓内,吊装前需检查模具吊装孔是否滑牙,起吊模具时需控制起吊速度和运输速度。
将模具吊起后(离地面高度15到20公分),平推至注塑机操作界面的对面,之后再将模具升高,至合适高度后,再平移至机台容模腔内,最后将模具降低,降低至进胶口与唧嘴基本持平。
需特别注意,吊环扭入深度必须在两倍直径以上。
对嘴将模具吊入机仓内,模具进胶口位置与炮嘴基本在一条线上,打开马达进行对嘴。
对炮嘴前,应先合模锁模----模具处于低压状态(位置在5MM-10MM),模具能够稍微活动即可。
再启动射座以15%-20%的速度进行操作,防止射嘴和模具撞击或碰伤。
且在微调模具上下时,唧嘴必须退后一段距离,避免唧嘴或模具损坏。
- 1、下载文档前请自行甄别文档内容的完整性,平台不提供额外的编辑、内容补充、找答案等附加服务。
- 2、"仅部分预览"的文档,不可在线预览部分如存在完整性等问题,可反馈申请退款(可完整预览的文档不适用该条件!)。
- 3、如文档侵犯您的权益,请联系客服反馈,我们会尽快为您处理(人工客服工作时间:9:00-18:30)。
教你任何设置注塑机合模参数
一,开始合模:
1、开始合模压力:初设置值参考为25,当此压力过小而导致速度过慢时,可尝试增加速度,此压力过小,而使速度无法提高至需要时速度每次加+5尝试,注意,该压力设置较大时,会使动模板瞬间加高压改变静止状态变运动,至使动模板孔与拉杆产生巨大的摩擦力,久之加快了机器动模板孔与拉杆的磨损,影响到动模板运动的平稳性与精密度的下降,可能影响到个别对合模机构的精密要求较高模具的生产。
2、开始合模速度:看实际,不过要注意动作不宜过快,该速度要与下一段合模动作具有连贯性的运动,而不是出现明显的停顿动作切换,最好是速度设置高,压力设置低,由压力控制速度。
二,低压合模:
由低压低速推动模具,由需要安全保护的距离开始至模具完全闭合终止
1、低压合模速度:看实际,速度要慢,过快的速度,就算有设置了低压,惯性运动仍然有巨大的撞击破坏力。
滑快位置偏移、顶针断出、、、、等出现意外硬障碍物时,而进入合模动作,在有效的低压慢度的合模保护参数条件之下,大大减小撞击的损伤。
其实可以这个速度为几十,然后不动它,再把压力开始调得很低比如5进行测试,以压力控制速度,再一步步加压至适合的合模保护速度。
2、低压合模压力:可以先把速度调得很高,压力调得很低例如5进行合模测试,因为压力低,就算速度设置很大,失去压力的支持,合模速度也不会很快的,以压力控制速度,在5的基础上,一点点往上加至理想的合
模保护速度,以最低的压力合模。
3、低压合模开始位置:(即上一段合模终止位置)这个要根据模具大小与结构而设置大小差异较大的数值,一般为模具闭合前的5-20厘米之间,这个位置大家看着办。
很多人就是设置模具合得太近,就才开始用低压,应该提前得到低压保护的距离受到上一段较大压力速度冲击合模,滑快位置偏移、顶针断出、、、、等出现意外硬障碍物时,快猛撞击,这时低压保护无效,来迟了,(重点核心)、、、、
4、低压合模终止位置(即高压锁模开始位置):此参数为模具刚好刚完全闭合的位置,即动模板前进已经到尽头停止了,调试时先调好低压压力和速度,再将位置设置为0,关门手动合模测试得出一个低压合模完全闭合位置数值,比如这个数值是2.2,这个数值的大小受电子尺设置调整、调模松紧、合模压力大小影响,
并且这个数值会受到机器精度和模具表面细小杂物的影响等原因影响,每次合模可能会有小小变动,所以要将终止位置设置稍大一点点比如加0.2设置为2.4(参考加0.1-0.3),以最低的位置,精确保护模具,如果不把低压合模测试获得的位置数值设置大一点点的话,直接就用2.2,可能经常会出现低压合模位置大于2.2,低压位置结束不了而无法转到高压锁模。
不过更多人是设置模具还有数厘米距离或更长距离没有完全闭合就低压
终止,开始用高压了,低压保护无效,经常见到一些模具被意外带已经顶出了的形成品合模,钢材质模腔被压得变形。
(重点核心)、、、、
三、高压锁模
开始用高压推动机铰伸直将已经闭合了的模具锁压紧。
很多人就是设置模具没有完全闭合,就开始用高压了,低压保护失效(重点核心)、、、、
1、高压锁模压力:初设置值参考为60,当无法满足时,每次+10压力,压力太大,是没有必要的加大机器负荷、、、、
2、高压锁模速度:初设置值参考为25,当无法满足需要时,先尝试加大压力查看,不行后,才尝试加快速度,每次+10。
高压锁模不应该听到过大的响声,速度加快一倍,锁模机构摩擦损耗加大N倍。
大家要注意
上面我说的合模与锁模区别是,合模=动模板运动,锁模=用高压推动机铰伸直锁压紧已经闭合的模具,低压合模保护设置其实多数人就是在低压合模开始位置和终止位置没有做对,一是低压开始位置时模具靠得太近了,位置太小了,低压保护来得太迟,受到上一段(开始、快速、高速)较高较快的压力与速度影响。
二是低压终止位置结束得太早,当模具还有数厘米或更大的距离没有闭合,就终止结束低压保护了,转到高压锁模,这两个问题一般同时存在,这就成了低压合模保护位置过短,前被较大压力较快速度快速合模冲击威胁,后被高压锁模压力压迫两面夹击,就相当于低压合模保护无效形同虚设。
、、、、
在无效低压保护下,模具被压、撞坏可能会出现下列问题夹带障碍物以较高的压力合模=压模、夹带硬性障碍物较高的速度合模=撞模)
1、模具因结构较简单,合模压力也不是很大,压不坏。
2、模具被压,致使模具型精密度下降,使注塑成形条件发生变化,给工艺参数的调试加大难度。
3、模具被压,致使模具精密度下降,使成形产品的毛边加大、加多,加大了生产工人的工作强度与工作量,加速工人工作的疲劳, 产品的产量、质量、效率往下降。
工作对工作的喜欢度在下降,员工流动可能会因此而有少许加大。
4、模具被压,致使模具精密度下降,使成形产品的毛边加大、加多。
原定的人员已经无法满足工作对劳动力的需要,需要增加人手,使劳动力密集生产制造的产品,劳动力更加密集,增加人工支出,提高了产品生产制造成本。
5、模具被压、撞,致使模具受损坏以至无法生产,耽误生产,需要时间与费用对模具进行维修。
6、模具型腔光滑面被撞兼压伤,不管如何修补,也难以避免留下一个补痕,在成形产品上留下一个印记,对于组合成品起来属于在直视面的塑料件的,一个光滑的产品表面有一个修如过的痕迹,这就是一个美中的瑕
疵,产品质量与档次可能因此受影响。
7、模具被压、撞坏。
对坏模具进行烧焊、驳接、、、修修补补。
模具的质量与性能加速下降,模坏的发生率上升,增加模具的运作维护的成本支出。
随着修多、补多以及精密度的逐步下降,注塑模具的使用寿命最终会因在生产中没有得到好好地保护,而受到生产中意外撞击压迫地推残,最终寿命因此而缩短。