焊接夹具的设计的要求
焊装夹具定位设计技术标准
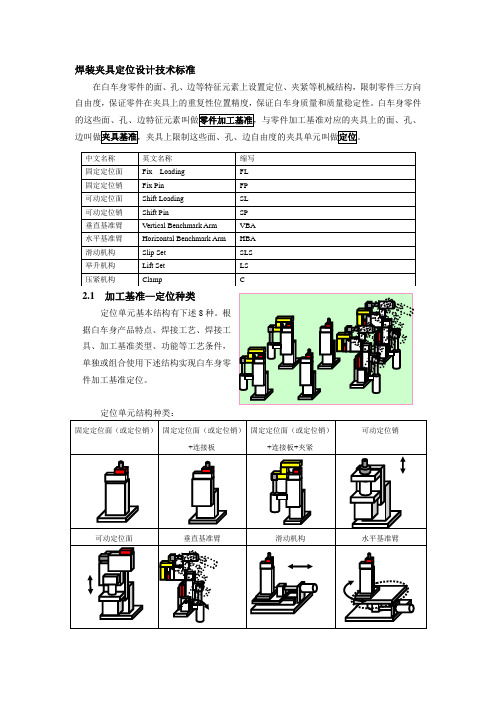
焊装夹具定位设计技术标准在白车身零件的面、孔、边等特征元素上设置定位、夹紧等机械结构,限制零件三方向自由度,保证零件在夹具上的重复性位置精度,保证白车身质量和质量稳定性。
白车身零件2.1 加工基准—定位种类定位单元基本结构有下述8种。
根据白车身产品特点、焊接工艺、焊接工具、加工基准类型、功能等工艺条件,单独或组合使用下述结构实现白车身零件加工基准定位。
定位单元结构种类:2.2定位单元构成定位单元通常由定位块(定位销)、连接板、支座、夹紧块、夹紧臂、铰链、气缸、导向8种基本功能件组成,复杂定位单元需要增加限位块、导轨、二层支座等功能件(如下图所示)。
2.3(白车身零件)加工基准加工基准需要同时满足四大工艺(冲压、焊装、涂装、总装)使用,具有一致性。
加工基准在产品设计时通过工艺评审,最终确定,是完整产品组成的一部分。
按零件面、孔、边的几何特征,加工基准可以划分为:面基准—S(s)、孔基准—H(h)、边基准—E(e);按零件上几何元素功能,加工基准可以划分为:正基准、辅助基准、变换基准等;结合上述两种划分方法,加工基准划分为以下13种,便于使用和管理。
2.4加工基准—定位单元位置精度不同加工基准的定位精度要求不同。
分为三类:孔基准—定位销、面(边)基准—定位块、特殊辅助面基准—定位块。
(1)孔基准—定位销◆孔基准类型:◆定位销、连接板孔配合公差:h7/H7◆ 定位销位置公差:±0.1mm◆ 定位销连接处直径公差:h7◆ 连接板孔直径公差:H7(2) 面基准—定位块◆ 面基准类型:◆ 定位块位置公差:±0.1mm(3) 特殊辅助面基准—定位块◆ 特殊辅助面基准类型:◆定位块位置精度:+0/-0.5㎜e2.5 加工基准—定位单元刚性为保证制造质量的稳定性,要求定位单元的定位件(块、销)装配后其工作方向位置变化<0.1mm 。
既要保证夹具骨架(平台)的结构刚性,还需要保证定位单元的结构刚性。
夹具设计规范

焊接夹具设计制造技术规范根据国外先进汽车车身装焊夹具公司对夹具设计的经验,并结合国内的具体情况,大连奥托技术有限公司制定了装焊夹具的设计制造技术规范,设计者应严格遵循。
1..装焊夹具的设计依据以汽车产品零部件图(数模最佳)、装焊工艺图、设计技术任务书、厂标件标准为设计依据,进行规范化、模块化设计。
2..装焊夹具设计通则装焊夹具设计采取模块化方式,按照装焊工艺图进行,以满足焊接工艺要求,夹具设计图画法应贯彻国家机械制图标准。
夹具操作方便,设计完成后的工装系统必须符合人机工程学的要求。
夹具应有足够的装配、焊接空间,焊点在布置时应易接近。
夹具本身必须有良好的制造工艺性和较高的机械效率。
3..装焊夹具设计规范及要求总图设计总图上应标注:夹具轮廓尺寸、操作高度、坐标线(尽量与汽车坐标线统一),坐标基准刻线或坐标基准孔、各部件的安装位置、气缸位置、所有定位尺寸坐标基准孔应相对于坐标线标注,在图中按汽车产品件在汽车中的实际位置建立汽车坐标,其基准线用○>符号表示;同时按夹具的基础建立坐标系,其基准线用○=符号表示。
在夹具上有产品图的摆放位置,并用细双点划线绘出。
焊点位置用○+表示。
设计时应注意焊点的坐标位置,必须留有充分的焊钳工作空间位置,便于施焊。
用双点划线表示焊钳的外形。
总图上还应包括夹具的操作步骤,并且特殊步骤必须详细说明。
对总拼及较复杂的工装、带有自动焊的工装等,其设计必须采用三维设计。
定位块、压块的设计定位块尽量采用标准精铸ZG45#L形毛坯件加工,其厚度规定16mm,特殊情况及厂家有要求例外。
与定位板装配的结合面为基准面用○基表示,要求表面粗糙度为,定位面表面粗糙度为,定位面局部火焰淬火HRC40~45,安装挡片面加工表面粗糙度为,通常挡片安装在L板垂直面一侧定位板上,定位块为AB面情况下,安装在高面一侧,加工后表面喷漆处理,安装面定位面不喷漆,安装孔表面粗糙度为其余表面不加工。
压块尽量采用标准精铸ZG25L形毛坯件加工,其厚度规定16mm,特殊情况及厂家有要求例外。
夹具标准

3、 装配: 3.1. 紧固螺栓采用内六角螺栓,公制标准件,在钢板厚度允许条件下,内六角头应沉入钢板表面 。 紧固需带弹簧垫圈; 3.2. 尽量从上方和侧面安装螺栓; 3.3. 定位销采用GB120-86标准销,自带装卸螺孔; 4、检测 4.1. 零件的检测采用常规量具检测; 4.2. 部件的检测采用常规检测或3D检测; 4.3. 夹具的整体检测采用3D检测,并出具最终检测报告。 4.4 夹具精度: 4.4.1主定位销的位置度公差:±0.1㎜; 4.4.2定位销的加工精度:直径+0.00~-0.05mm; 4.4.3定位面的装配公差:±0.2㎜; 4.4.4 翻转定位机构的重复定位精度:±0.2㎜(Φ200处㎜); 4.5 移动单元: 4.5.1 带有轴承及防尘装置; 4.5.2.设有限位块; 4.5.3.大型移动机构(重量大于80Kg)采用直线轴承; 4.5.4.小型移动机构采用无油润滑轴承; 5 、定位夹紧单元:
5.1 定位销应二维可调,定位销带定位面的应三维可调; 5.2. 定位夹紧块在定位夹紧方向一维调节; 5.3. 尽可能采用标准支承、定位销、连接块、过渡块和限位块,做成易换、易调整、易维修; 6、 材料表面及热处理: 6.1定位块:一般采用16mm厚的钢板,特殊部位采用19mm厚的钢板,材料采用45钢,调质T235 和发黑处理; 6.2定位销:40Cr钢,表面氧化处理,淬火 HRC55-60 ; 6.3 支承座:采用铸钢支承座,为本公司标准支撑座。 7、夹紧方式: 7.1.采用气缸自动夹紧或嘉手的手动夹钳夹紧; 8、 铭牌及标牌: 8.1. 设备设有本公司铭牌及设备标牌; 8.2. 铭牌固定上底板上。铭牌上标明夹具名称、夹具图号、使用车型、验收日期、制造商名称等 , 使用厚度为1㎜的铝板制做; 9、油漆: 9.1 生产线工装夹具均喷涂磁漆(颜色由买主规定),定位面及定位销要求发黑处理,夹具基准 面 要求防锈处理; 9.2 用颜色区分固定零件和运动零件; 9.3 外购件、标准件、非金属材料、铝件等为本色,不油漆; 9.4 所有的表面氧化零件均不油漆。
汽车车身焊装夹具设计概述
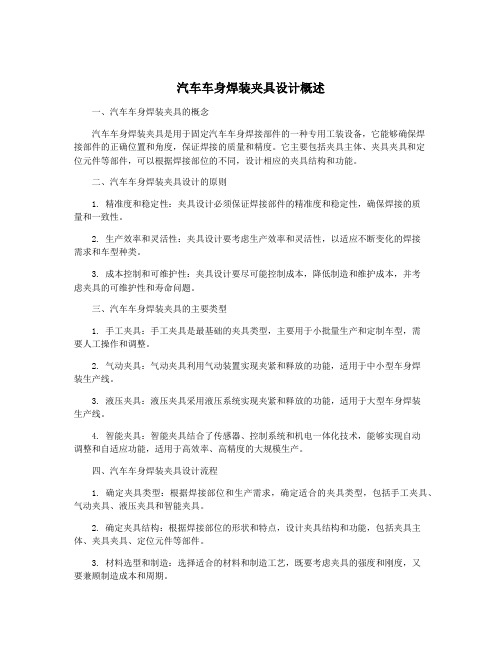
汽车车身焊装夹具设计概述一、汽车车身焊装夹具的概念汽车车身焊装夹具是用于固定汽车车身焊接部件的一种专用工装设备,它能够确保焊接部件的正确位置和角度,保证焊接的质量和精度。
它主要包括夹具主体、夹具夹具和定位元件等部件,可以根据焊接部位的不同,设计相应的夹具结构和功能。
二、汽车车身焊装夹具设计的原则1. 精准度和稳定性:夹具设计必须保证焊接部件的精准度和稳定性,确保焊接的质量和一致性。
2. 生产效率和灵活性:夹具设计要考虑生产效率和灵活性,以适应不断变化的焊接需求和车型种类。
3. 成本控制和可维护性:夹具设计要尽可能控制成本,降低制造和维护成本,并考虑夹具的可维护性和寿命问题。
三、汽车车身焊装夹具的主要类型1. 手工夹具:手工夹具是最基础的夹具类型,主要用于小批量生产和定制车型,需要人工操作和调整。
2. 气动夹具:气动夹具利用气动装置实现夹紧和释放的功能,适用于中小型车身焊装生产线。
3. 液压夹具:液压夹具采用液压系统实现夹紧和释放的功能,适用于大型车身焊装生产线。
4. 智能夹具:智能夹具结合了传感器、控制系统和机电一体化技术,能够实现自动调整和自适应功能,适用于高效率、高精度的大规模生产。
四、汽车车身焊装夹具设计流程1. 确定夹具类型:根据焊接部位和生产需求,确定适合的夹具类型,包括手工夹具、气动夹具、液压夹具和智能夹具。
2. 确定夹具结构:根据焊接部位的形状和特点,设计夹具结构和功能,包括夹具主体、夹具夹具、定位元件等部件。
3. 材料选型和制造:选择适合的材料和制造工艺,既要考虑夹具的强度和刚度,又要兼顾制造成本和周期。
4. 装配调试和调整:对设计好的夹具进行装配和调试,确保夹具的稳定性和精确度,以便进行后续的生产。
5. 生产应用和维护保养:将设计好的夹具投入生产应用,不断进行维护保养和改进优化,持续提高生产效率和质量。
五、结语汽车车身焊装夹具设计是汽车焊装工艺中非常重要的一环,它直接影响着汽车焊接质量和生产效率。
夹具设计要求
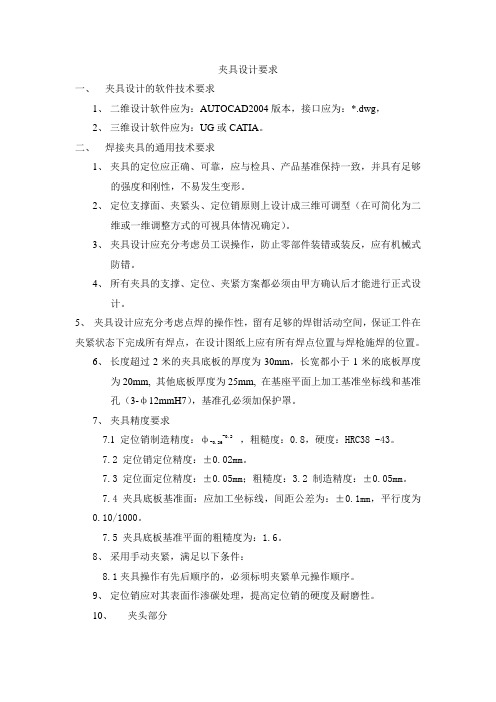
夹具设计要求一、夹具设计的软件技术要求1、二维设计软件应为:AUTOCAD2004版本,接口应为:*.dwg,2、三维设计软件应为:UG或CATIA。
二、焊接夹具的通用技术要求1、夹具的定位应正确、可靠,应与检具、产品基准保持一致,并具有足够的强度和刚性,不易发生变形。
2、定位支撑面、夹紧头、定位销原则上设计成三维可调型(在可简化为二维或一维调整方式的可视具体情况确定)。
3、夹具设计应充分考虑员工误操作,防止零部件装错或装反,应有机械式防错。
4、所有夹具的支撑、定位、夹紧方案都必须由甲方确认后才能进行正式设计。
5、夹具设计应充分考虑点焊的操作性,留有足够的焊钳活动空间,保证工件在夹紧状态下完成所有焊点,在设计图纸上应有所有焊点位置与焊枪施焊的位置。
6、长度超过2米的夹具底板的厚度为30mm,长宽都小于1米的底板厚度为20mm, 其他底板厚度为25mm, 在基座平面上加工基准坐标线和基准孔(3-ф12mmH7),基准孔必须加保护罩。
7、夹具精度要求7.1 定位销制造精度:ф-0.26-0.2 ,粗糙度:0.8,硬度:HRC38 -43。
7.2 定位销定位精度:±0.02mm。
7.3 定位面定位精度:±0.05mm;粗糙度:3.2 制造精度:±0.05mm。
7.4 夹具底板基准面:应加工坐标线,间距公差为:±0.1mm,平行度为0.10/1000。
7.5 夹具底板基准平面的粗糙度为:1.6。
8、采用手动夹紧,满足以下条件:8.1夹具操作有先后顺序的,必须标明夹紧单元操作顺序。
9、定位销应对其表面作渗碳处理,提高定位销的硬度及耐磨性。
10、夹头部分10.1夹具的运动部分应灵活,无卡滞现象,具有良好的操作性。
10.2夹钳采用台湾嘉手品牌,采用型号和质量需经甲方确认。
10.3手柄长度要合适,焊接手柄时应注意翻转角度的限位,理论上翻转角不超过1200 ,以防打开时伤人。
焊接夹具课程设计说明书.
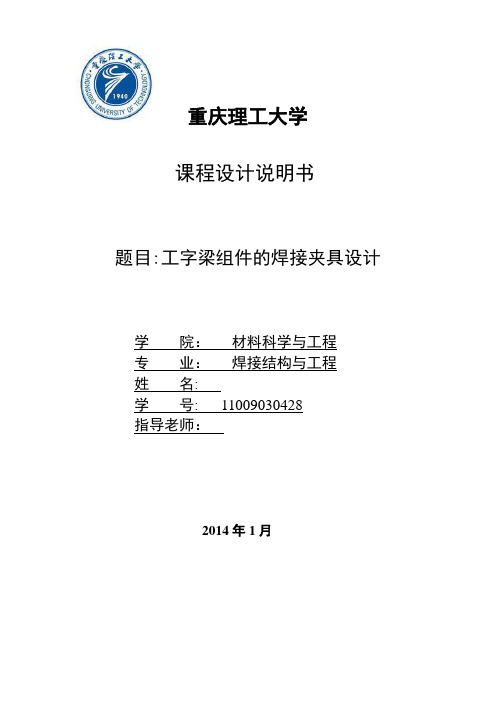
重庆理工大学课程设计说明书题目:工字梁组件的焊接夹具设计学院:材料科学与工程专业:焊接结构与工程姓名:学号: 11009030428指导老师:2014年1月序言 01。
对焊接工装夹具的设计要求 01.1焊接工装夹具的主要作用 (1)2。
焊接结构件的分析 (1)2。
1 焊接产品“钢梁组件”的重点技术要求分析: (1)2.2 采用合理的焊接顺序和方向 (2)3。
夹具设计方案的确定 (2)3。
1 在设计夹具体时应满足以下基本要求: (2)3.2 基准面的选择: (2)3.3 定位方式及元器件选择 (3)3.4 夹紧方式及元器件选择 (4)3。
5 装焊夹具结构 (5)3.6 装焊方案 (5)4。
主要零件设计的说明 (5)4。
1 夹具体 (5)4。
2 手动螺旋夹紧器 (5)4。
3 挡板 (6)4。
4 反变形装置 (6)4.5 垫板 (7)4。
6 销钉 (7)4.7 螺栓 (7)5. 装焊夹具使用说明 (7)5。
1 夹具的操作步骤: (7)5.2 夹具的结构特点: (7)5.3 夹具使用注意事项、保养及维护 (7)6。
本次课程设计总结、体会 (8)参考资料 (8)焊接工装夹具是将焊件准确定位并夹紧,用于装配和焊接的工艺装备.在焊接结构生产中,把用来装配进行定位焊的夹具称为装配夹具:而专门用来焊接焊件的夹具称为焊接夹具:把既用于装配又用于焊接的夹具称为装焊夹具.它们统称为焊接工装夹具。
1。
对焊接工装夹具的设计要求(1)焊接工装夹具应动作迅速,操作方便,操作位置应处在工人容易接近,最宜操的部位。
特别是手动夹具,其操作力不能过大,操作频率不能过高,操作高度应设在工人最容易用力的部位,当夹具处于夹紧装态时,应能自锁.(2)焊接工装夹具应有足够的装配焊接空间,不能影响焊接操作和焊工观察,不妨碍焊件的装卸,所有的定位原件和夹紧装置应与焊道保持适当距离或者布置在焊件的下方和侧面。
夹紧机构的执行元件应能够伸缩或转位.(3)夹紧可靠,刚性适当,夹紧时不破坏焊件的定位位置和几何形状,夹紧后不使焊件松动滑移,又不使焊件的拘束度过大,产生较大的应力。
焊装夹具的设计基本原则
在进行汽车时,其实有6-7成的工作为辅助和装夹工作。
虽然主要的操作是焊接,但是一个好的准备过程会使整个工艺过程更加顺畅,产品效果更好。
因为装夹是在焊接家具上完成的,因此夹具的设计起着很重要的作用。
在焊接过程中,合理的夹具结构,有利于合理安排流水线生产,便于平衡工位时间,降低非生产用时。
对具有多种车型的企业,如能科学地考虑共用或混型夹具,还有利于建造混型流水线,提高生产效率。
一、定位部件的设计原则1、定位基准统一原则:由于在车身制造中,每个制件要经过若干次装配、定位、夹紧的重复定位。
所以焊接夹具要求采用定位基准统一原则。
2、正确选择定位基准:一般将车身装配重要部位影响车身总成几何形状和尺寸的重要型面位置度要求高的工艺孔,作为夹具的定位基准。
定位基准孔一般采用产品数字模型上已有的孔或冲压工艺可保证的最稳定的工艺孔。
出于定位可靠性、制造工艺性、夹具经济性等几个因素的考虑,定位基准面一般优先选择平面,尽量避免选择曲面。
3、正确确定每个制件定位点数量:在设计中仍应该遵守六点定位原则。
但为克服薄板弹性变形,保征制件正确定位支撑点,允许出现过定位。
4、合理确定定位点的位置:首先将定位基准的孔和型面确定为定位点;其次将两个制件搭接处需要焊接的部位确定为定位点;另外将易变形处确定为定位点支撑。
同时,部件安装和结构设计要考虑焊钳的接近性,焊钳必须能在指定的焊点位置焊接。
二、夹紧部件的设计原则1、正确确定夹紧点:对于薄板冲压件,夹紧点应作用在定位点上,一般将定位基准面、两个制件搭接处、易变形处的定位支撑点等位置确定为夹紧点。
避免在没有支撑处布置夹紧机构,与支撑点形成力偶,破坏制件在夹具中的定位。
2、正确确定夹紧力的作用方向:制件在夹具中的夹紧和定位是密切相关的。
夹紧力的作用方向就是向着定位支撑块。
通过定位支撑块的反作用力,使制件与定位块紧密接触。
3、正确决定夹紧力的大小:夹紧力大小应以能克服制件的弹性变形保证定位准确可靠为宜。
焊接夹具设计及制作标准
南京依维柯汽车有限公司第二车身厂焊接夹具设计制作标准编制:余水2010年3月22日焊接夹具设计及制造标准总体技术要求:1、所有的夹具均采用气动控制压紧及车型转换方式(特殊规定可采用手动压紧器压紧或不用压紧)。
2、夹具应保证可靠的定位,防止变形,确保装配焊接质量和精度达到产品质量要求。
3、夹具工艺性能优良:各部件装配调整方便、人工焊接易于操作、产品取放方便、有足够的操作空间、操作方便快捷。
4、夹具上产品的高度应在700~800mm之间,对于四周焊接作业困难的应增加360°旋转转盘装置(特殊情况要求还需增加旋转定位锁紧装置)。
5、所有夹具须满足生产纲领的要求。
一、焊接件技术要求:1、焊缝高度不得<5mm、不允许有虚焊脱焊现象、重要部位须采用连续焊缝。
2、焊后清理焊渣、焊缝磨平。
所有部件在焊接后须退火消除应力再进行机加工。
-二、夹具底板1、夹具底板台面全部加工完成后厚度≮20mm,底板与槽钢等加强板料焊接前应校平,留有吊运点或叉车搬运位置,焊后应经退火处理和校平后再进行机加工等后续作业,加工完成后应对台面涂油处理。
2、加强筋规格选用标准(长方形的取最大值):(1)当夹具台面≤1400mm×1400mm时,底板的加强筋应采用10#以上槽钢;(2)当夹具台面>1400mm×1400mm时,底板的加强筋应采用16#以上槽钢;(3)当夹具台面>2000mm×2000mm时,底板的加强筋应采用20#以上槽钢;(4)底座周边的槽钢开口向外,中间加强筋用槽钢的间距不得>700mm.。
3、夹具台面的基准孔及网格坐标线:(1)基准孔:夹具台面上应留有两个坐标系的检测用基准孔,每个方向为两组,每组两个孔,孔径为φ10mm,孔距100mm.(在基准孔附近安装标牌或刻上钢字码,注明坐标数值)(2)网格坐标线:网格坐标线应与产品设计的坐标线对应。
深度及宽度均为0.5mm,间距为200mm.4、夹具台面的周边轮廓尽量与产品零件的轮廓相似,不得有突出的锐角,并尽量往里收,方便操作。
焊接夹具设计规范
焊接夹具设计规范篇一:焊接夹具的设计的要求焊接夹具的设计的要求焊接工装是摩托车车架制作过程中的关键设备,其设计质量不仅直接影响车架的精度,而且也决定生产效率和工人的作业条件。
1 焊接工艺方案的确定1.1 准备工作主要研究原始资料,明确设计任务和进行必要的调查研究。
一般应具备下列原始资料。
a)车架的生产纲领(年产量)、生产性质与类型。
b)车架图纸、技术要求及其他相关件的装配关系。
c)车间的生产条件,如作业面积、动力供应及技术水平等。
d)相关技术标准、法规和本企业的发展目标。
1.2 工艺方案的设计在调查研究和对资料综合分析的基础上拟定车架的工艺方案(包括焊接工艺规程、工程计划表和结构草图等)。
需对下列内容进行构思和选择。
a)根据生产纲领等确定车架的生产节拍。
b)根据车架零部件的装配顺序、焊接方法、焊缝的位置及质量要求、生产节拍和各工序工时的均衡来规定生产组织形式和工艺路线的安排,包括划分车架零部件组焊的工序和所需焊接工装的数量及其在车间的布局。
c)实现某种功能拟采用的原理和相应的机构。
如定位与夹紧的方式和机构、焊件的翻转或回转等。
d)各工序所需工装的基本构成、车架零部件的定位、夹紧位置和总体布局,主要零部件的基本结构。
2 焊接工装的设计2.1 焊接工装的设计原则首先是焊接工装满足工艺技术要求,并应便于操作、安全、可靠及满足外观和经济上的要求。
2.2焊接工装的设计要求a)焊接工装应具有动作迅速、操作方便,操作位置应处在工人最容易接近、最易操作的部位。
特别是手动夹具,其操作力不能过大,操作高度应设在工人最易用力的部位,当夹具处于加紧状态时应能自锁,一般操作高度应控制在800~900mm。
b)焊接工装应有足够的装配、焊接空间,不能影响焊接操作和焊接观察,不妨碍焊件装卸。
所有定位元件和夹紧机构的执行元件应可调,即能伸缩和转位。
同时必须保证焊接机头的焊接可达性。
c)夹紧可靠,刚性适当。
加紧时不能破坏焊接件的定位位置和几何形状(如变形、凹陷、划伤等),且要保证夹紧后不能使焊件松动滑移,可以采取压头行程限位、加大压头接触面积或在压头上安装铜、铝、硬塑料衬垫等措施。
焊接夹具设计要点,注意事项
焊接夹具设计要点,注意事项一、一般情况BASE的设计和制造原则:夹具底座等结构件要求采用 Q235-A 板材和型材焊接而成, BASE 底板的焊缝采用非连续焊缝; BASE 板面 1M 以下板材厚度不低于20mm ,型材采用 10 号槽钢, 1M 以上要求板厚在 22 mm ~ 26mm ,型材采用16 号槽钢,焊后经热处理退火消除应力(不允许采用机械消除应力)并喷砂处理,定位块、夹紧块的常用材料及其处理方式:定位块、夹紧块必须采用优质 45# 钢并经热处理去除加工应力。
二、一般支撑块/压块(下型块/上型块)的材料及处理方式:采用45#钢,淬火处理(HRC38~42);夹紧块(上型块);三、一般定位销的材料及处理方式:定位销采用 40Cr ,并淬火和调质( HRC40-45 ),表面镀铬处理,保证其硬度和耐磨性;四、一般情况下夹具的操作高度:点焊夹具应为 750mm ~ 800mm ,总体原则要求符合人机工程要求,弧焊夹具为850mm ~ 950mm五、常用的汽车覆盖件的保护措施:装焊夹具设计时应考虑汽车覆盖件的外表面有防止出现焊点压痕的保护措施,保护板的材料选用 CuCrZr( 铬锆铜 ), 其有效板厚 10 ~ 12mm ,对刚性较差的大型零件应考虑工件抬起机构,对不便于施焊的焊点应设计焊钳导向机构,保证焊接点的准确位置六、一般设计时候气缸的预留行程是多少:气缸运动夹具设计时,气缸在压紧点处必须留有 3~ 5mm 运动行程,防止运动到端点。
七、一般情况下脚轮的选用原则:要求移动的焊装夹具配装脚轮,大型夹具(重量大于1.5吨)要求用 8 英寸铸铁滚轮,并且要求大型夹具有水平调整螺栓;中型夹具(重量大于0.8吨)要求用 6英寸PU脚轮,小型夹具要求用 4英寸PU脚轮(重量小于0.8吨)八、一样夹具的夹紧力要多少:一般情况下压紧位置要求有30kg的压紧力,弧焊夹具要求有50kg的压紧力;九、定位销形式的选择:一般情况下,选用1圆+1菱,特殊情况下可选用2圆销;十、夹具一般在什么情况下采用限位块:1、夹持臂上有基准销时。
- 1、下载文档前请自行甄别文档内容的完整性,平台不提供额外的编辑、内容补充、找答案等附加服务。
- 2、"仅部分预览"的文档,不可在线预览部分如存在完整性等问题,可反馈申请退款(可完整预览的文档不适用该条件!)。
- 3、如文档侵犯您的权益,请联系客服反馈,我们会尽快为您处理(人工客服工作时间:9:00-18:30)。
焊接夹具的设计的要求
焊接工装是摩托车车架制作过程中的关键设备,其设计质量不仅直接影响车架的精度,而且也决定生产效率和工人的作业条件。
1 焊接工艺方案的确定
1.1 准备工作
主要研究原始资料,明确设计任务和进行必要的调查研究。
一般应具备下列原始资料。
a)车架的生产纲领(年产量)、生产性质与类型。
b)车架图纸、技术要求及其他相关件的装配关系。
c)车间的生产条件,如作业面积、动力供应及技术水平等。
d)相关技术标准、法规和本企业的发展目标。
1.2 工艺方案的设计
在调查研究和对资料综合分析的基础上拟定车架的工艺方案(包括焊接工艺规程、工程计划表和结构草图等)。
需对下列内容进行构思和选择。
a)根据生产纲领等确定车架的生产节拍。
b)根据车架零部件的装配顺序、焊接方法、焊缝的位置及质量要求、生产节拍和各工序工时的均衡来规定生产组织形式和工艺路线的安排,包括划分车架零部件组焊的工序和所需焊接工装的数量及其在车间的布局。
c)实现某种功能拟采用的原理和相应的机构。
如定位与夹紧的方式和机构、焊件的翻转或回转等。
d)各工序所需工装的基本构成、车架零部件的定位、夹紧位置和总体布局,主要零部件的基本结构。
2 焊接工装的设计
2.1 焊接工装的设计原则
首先是焊接工装满足工艺技术要求,并应便于操作、安全、可靠及满足外观和经济上的要求。
2.2焊接工装的设计要求
a)焊接工装应具有动作迅速、操作方便,操作位置应处在工人最容易接近、最易操作的部位。
特别是手动夹具,其操作力不能过大,操作高度应设在工人最易用力的部位,当夹具处于加紧状态时应能自锁,一般操作高度应控制在800~900mm。
b)焊接工装应有足够的装配、焊接空间,不能影响焊接操作和焊接观察,不妨碍焊件装卸。
所有定位元件和夹紧机构的执行元件应可调,即能伸缩和转位。
同时必须保证焊接机头的焊接可达性。
c)夹紧可靠,刚性适当。
加紧时不能破坏焊接件的定位位置和几何形状(如变形、凹陷、划伤等),且要保证夹紧后不能使焊件松动滑移,可以采取压头行程限位、加大压头接触面积或在压头上安装铜、铝、硬塑料衬垫等措施。
d)为使需要翻转的工操作安全和方便,应设置在任何角度都能自锁的保护装置。
e)在生产时,CO2气体保护焊会产生烟尘和熔融金属的飞溅物,这会损坏工装上外露的光滑定位面、滑动面和焊件的螺纹,故需要有遮掩等措施。
f)夹具的施力点应位于或近于焊件的支撑处,要防止支撑反力与夹紧力或重力形成力偶。
g)注意各种焊接方法在导热、导电、隔磁和绝缘等方面对夹具提出的特殊要求。
例如电阻焊时,需要考虑夹具的导电、导热和绝缘性能。
h)夹具上的定位器和夹紧机构的机构形式不宜过多,以利于制造和维护。
可采用气动等驱动方式,以提高生产效率和减小工人的劳动强度。
i)优先选用通用化、标准化的夹紧机构以及标准零部件来制作焊接工装夹具。
j)焊接工装作为焊接电源二次回路的组成部分,为避免因弧而发生工作表面的烧损,要使二次回路的一段从焊件最近一端引出,避免焊接电流从工装周身通过。
k)工装易损部位通常设计成可更换结构(如衬套等),且需热处理,表面硬度达到43~48HRC,检具不低于50HRC。
l)气动元器件的压力应可调,有转向阀、减压、过滤和润滑等功能;气动管路应布局合理,尽量不要布置在工作面上,且要采用耐高温的管子(防止焊接时烧伤);转向阀应布置在操作方便的地方。
m)焊接反变形理论的应用。
焊件的一些部位焊缝比较长或密集,易造成焊件取下后发生变形,可以把焊件在工装上强制反向变形后焊接,。
此方法在新大洲公司的多个车型上应用,效果良好。
n)为便于焊接工装调试,需采用外销定位。
在车架量产后再增加内销定位。
管件定位要尽量采用U形定位,并把两限位面设计成可拆卸的。
o)安全可靠原则。
工装在使用期内要安全可靠,凡受力构件都应具有足够的强度和刚度,足以承受重力和因限制焊接变形而引起的各个方向的拘束力等。
p)工装应易于制造,投资少,制造成本低,回收期短。
在使用时能源消耗和管理费用少等。
2.3 焊接工装设计方案的确定
根据已确定的工艺方案和上述设计要求来确定焊接工装设计方案。
具体应从以下几个方面考虑。
a)焊件的整体尺寸和制造精度以及组成焊件的各个配件的形状、尺寸和精度。
其中形状和尺寸是确定夹具设计方案、夹紧机构类型和结构形式的主要依据,并直接影响其几何尺寸的大小;制造精度是选择定位其结构形式和定位器配置方案以及确定定位器本身制造精度和安装精度的主要依据。
b)焊装工艺对夹具的要求。
例如与装配工艺有关的定位基面、装配顺序和夹紧方向等对夹具结构提出的要求。
c)焊装作业应在同一夹具上全部完成,否则需设计补焊工装和工位。
2.4 焊接工装的设计
焊接工装一般由定位器、夹紧机构和夹具体3部分组成。
焊件在夹具中要有确定的位置,必须遵循物体定位的“六点定则”,并将焊件几何形状和尺寸比较规则和稳定的边、面、孔用定位器定位。
a)定位器定位器是保证焊件在夹举中获得正确装配位置的零件或部件,又称定位元件或定位机构。
定位器的结构主要有挡铁、支撑钉、定位销、U形铁(或V形铁)和定位样板五类。
其中挡铁和支撑钉用于平面的定位;定位销用于焊件装配孔的定位;U形铁(或V形铁)用于圆柱体和圆锥体焊件的定位,定位样板用于焊件予已定位焊件之间的给定定位。
对定位器的技术要求有耐磨度、刚性、制造精度和安装精度,其易磨损部位可做成可拆卸或可调的。
另外,定位器大多是固定的,也有一些为了便于焊件装卸,做成伸缩式和转动式的,并采用手动、气动或液压等方式驱
动。
b)夹紧机构夹紧机构对焊件起夹紧作用,是夹具组成中的关键部分。
在摩托车行业常中的有手动杠杆铰链夹紧器(夹钳)、手动螺旋杠杆夹紧器(螺纹)、手动凸轮(偏心)杠杆夹紧器、气动杠杆夹紧器、永磁夹紧器(磁铁)等。
焊检所需夹紧力可以通过模拟件或实验件进行试验确定,常根据经验估算夹紧力来选择适当的夹紧器。
在设计时,夹紧机构的夹紧力应能在一定范围内调节。
c)夹具体夹具体是在家具上安装定位器和夹紧机构以及承受焊件重力的部分,起支撑和连接作用。
其形状和尺寸取决于工件的外廓尺寸、各定位器及夹紧机构等的布置情况和加工性质。
其技术要求有:1)有足够强度和刚度;2)便于装配和焊接作业的实施;3)能将装焊好的焊件方便卸下;4)满足必要的导电、导热、通水、通气和通风条件;5)容易清除焊渣和油污等赃物;6)有利于定位和夹紧机构位置的调节与补偿;7)必要时还有反变形的能力。
d)夹具公差配合与技术条件的制定夹具公差应以产品图纸尺寸公差及技术要求、焊接工艺文件和车架工艺方案等为依据。
夹具图上需要标注公差的尺寸为影响定位精度的尺寸、有配合要求的尺寸和有定位要求的面等。
夹具零部件有配合要求的面等。
夹具零部件有配合要求的面、外定位销孔和有装配要求的尺寸公差一般为±0.02mm或±0.05mm;其他轴与孔的配合公差根据要求选定。
技术要求应规定是否需要热处理、不能由锐角毛刺、防锈要求和一些特殊安装要求。
焊接工装设计制造完成后还要进行必要的调试。
米
m 主单位10分米10厘米10毫米10丝米10忽米(也叫到或丝)10微米10纳米
所以1毫米=10丝米,1毫米=1000微米(缪),1丝=100微米。