堆焊层超声检测方法
超声波检测焊缝的几种常用方法
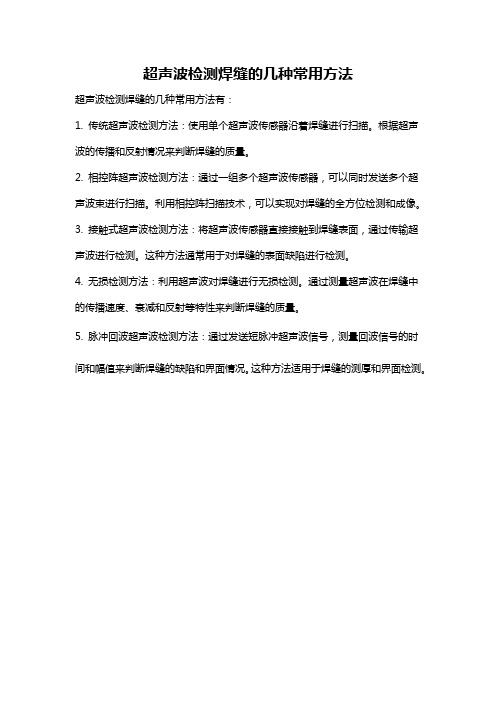
超声波检测焊缝的几种常用方法
超声波检测焊缝的几种常用方法有:
1. 传统超声波检测方法:使用单个超声波传感器沿着焊缝进行扫描。
根据超声波的传播和反射情况来判断焊缝的质量。
2. 相控阵超声波检测方法:通过一组多个超声波传感器,可以同时发送多个超声波束进行扫描。
利用相控阵扫描技术,可以实现对焊缝的全方位检测和成像。
3. 接触式超声波检测方法:将超声波传感器直接接触到焊缝表面,通过传输超声波进行检测。
这种方法通常用于对焊缝的表面缺陷进行检测。
4. 无损检测方法:利用超声波对焊缝进行无损检测。
通过测量超声波在焊缝中的传播速度、衰减和反射等特性来判断焊缝的质量。
5. 脉冲回波超声波检测方法:通过发送短脉冲超声波信号,测量回波信号的时间和幅值来判断焊缝的缺陷和界面情况。
这种方法适用于焊缝的测厚和界面检测。
超声波测焊点的操作流程
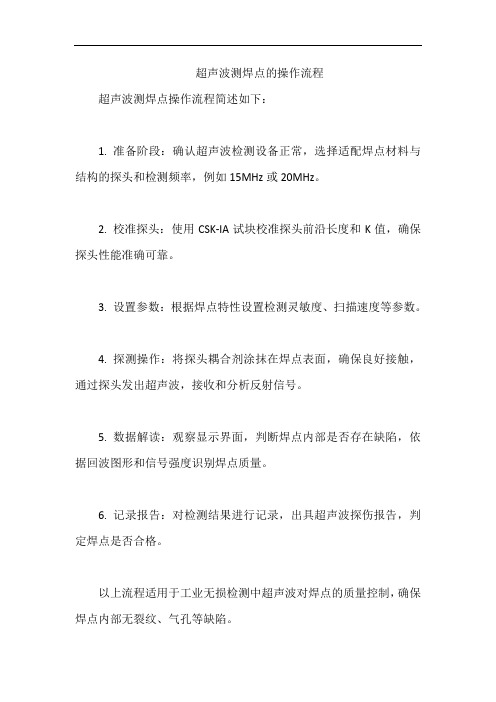
超声波测焊点的操作流程
超声波测焊点操作流程简述如下:
1. 准备阶段:确认超声波检测设备正常,选择适配焊点材料与结构的探头和检测频率,例如15MHz或20MHz。
2. 校准探头:使用CSK-IA试块校准探头前沿长度和K值,确保探头性能准确可靠。
3. 设置参数:根据焊点特性设置检测灵敏度、扫描速度等参数。
4. 探测操作:将探头耦合剂涂抹在焊点表面,确保良好接触,通过探头发出超声波,接收和分析反射信号。
5. 数据解读:观察显示界面,判断焊点内部是否存在缺陷,依据回波图形和信号强度识别焊点质量。
6. 记录报告:对检测结果进行记录,出具超声波探伤报告,判定焊点是否合格。
以上流程适用于工业无损检测中超声波对焊点的质量控制,确保焊点内部无裂纹、气孔等缺陷。
超声波从母材侧检测不锈钢堆焊层的研究

超声波从母材侧检测不锈钢堆焊层的研究文章介绍了当采用普通单晶直探头从母材侧检测堆焊层时,能发现堆焊层内不同深度以及堆焊层与母材界面上的φ9.5mm的平底孔。
研究表明随着探头频率的增加,平底孔回波与底面回波的幅值之比越高,即探头频率增加更有利于发现堆焊层缺陷,减少底面回波的干扰。
标签:堆焊层;母材侧;超声波;单晶直探头1各标准从母材侧检测堆焊层的要求NB/T 4730.3-2015允许从母材侧对堆焊层进行超声检测,ASME标准中也有从母材侧检测堆焊层的推荐试块。
以上两个标准中人工反射体均分布在堆焊层与母材界面上,说明从母材侧检测堆焊层与母材界面上的未结合缺陷是可行的。
但是从母材侧检测堆焊层内部未结合缺陷,在标准中没有明确的说明。
如果能验证从母材侧也能检测堆焊层内部未结合的缺陷,那从筒体侧(即母材侧)检测堆焊层的设想是切实可行的。
为了验证从母材侧探伤堆焊层的可行性,我们设计了如图1所示的超声波试块,即在堆焊层与母材界面以及堆焊层内部均布置不同深度的平底孔。
从图1可知,该试块不锈钢堆焊层厚度为8mm,在堆焊层与母材的熔合面(H=110mm)的区域布置一个φ9.5mm的平底孔,在堆焊层内布置了不同深度的φ9.5mm平底孔,距母材表面的深度分别为112mm,114mm,116mm。
界面上的平底孔模拟了实际产品中堆焊层与母材之间的未结合缺陷,堆焊层内的平底孔模拟了堆焊层层间的未结合性缺陷。
2 试验结果为了验证超声波检测能否发现堆焊层内部以及堆焊层与母材界面的平底孔,采用超声波检测常用的单晶直探头(2.5P20,频率为2.5MHz,晶片尺寸为20mm)放在试块母材侧进行试验,直探头能发现不同深度的平底孔。
见图2,图3。
试验结果可知,堆焊层内不同深度的?准9.5mm平底孔均清晰可见且伴随底波的出现,随着平底孔深度的增加,平底孔反射波与底波不断靠近。
如图2所示,当平底孔深度为110mm时,平底孔反射回波与底面回波可明显区分开,当平底孔深度H=116mm时几乎与底波融合到一起,平底孔回波与底面回波难以分辨,且底面回波的波高远远大于平底孔波高。
核反应堆压力容器堆焊层超声检测技术分析
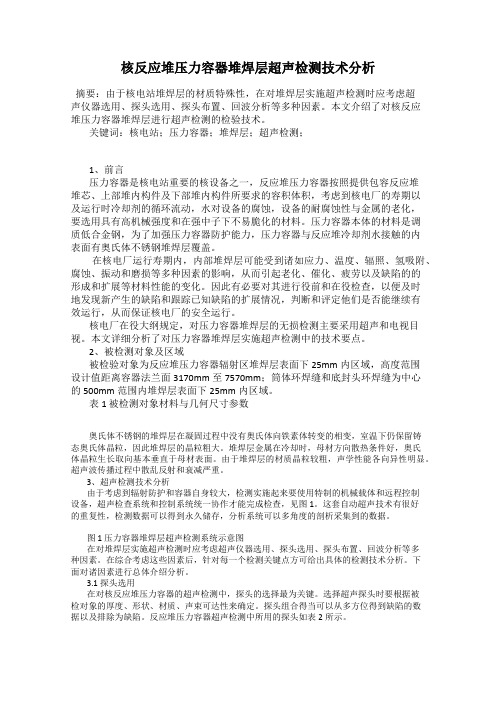
核反应堆压力容器堆焊层超声检测技术分析摘要:由于核电站堆焊层的材质特殊性,在对堆焊层实施超声检测时应考虑超声仪器选用、探头选用、探头布置、回波分析等多种因素。
本文介绍了对核反应堆压力容器堆焊层进行超声检测的检验技术。
关键词:核电站;压力容器;堆焊层;超声检测;1、前言压力容器是核电站重要的核设备之一,反应堆压力容器按照提供包容反应堆堆芯、上部堆内构件及下部堆内构件所要求的容积体积,考虑到核电厂的寿期以及运行时冷却剂的循环流动,水对设备的腐蚀,设备的耐腐蚀性与金属的老化,要选用具有高机械强度和在强中子下不易脆化的材料。
压力容器本体的材料是调质低合金钢,为了加强压力容器防护能力,压力容器与反应堆冷却剂水接触的内表面有奥氏体不锈钢堆焊层覆盖。
在核电厂运行寿期内,内部堆焊层可能受到诸如应力、温度、辐照、氢吸附、腐蚀、振动和磨损等多种因素的影响,从而引起老化、催化、疲劳以及缺陷的的形成和扩展等材料性能的变化。
因此有必要对其进行役前和在役检查,以便及时地发现新产生的缺陷和跟踪已知缺陷的扩展情况,判断和评定他们是否能继续有效运行,从而保证核电厂的安全运行。
核电厂在役大纲规定,对压力容器堆焊层的无损检测主要采用超声和电视目视。
本文详细分析了对压力容器堆焊层实施超声检测中的技术要点。
2、被检测对象及区域被检验对象为反应堆压力容器辐射区堆焊层表面下25mm内区域,高度范围设计值距离容器法兰面3170mm至7570mm;筒体环焊缝和底封头环焊缝为中心的500mm范围内堆焊层表面下25mm内区域。
表1 被检测对象材料与几何尺寸参数奥氏体不锈钢的堆焊层在凝固过程中没有奥氏体向铁素体转变的相变,室温下仍保留铸态奥氏体晶粒,因此堆焊层的晶粒粗大。
堆焊层金属在冷却时,母材方向散热条件好,奥氏体晶粒生长取向基本垂直于母材表面。
由于堆焊层的材质晶粒较粗,声学性能各向异性明显。
超声波传播过程中散乱反射和衰减严重。
3、超声检测技术分析由于考虑到辐射防护和容器自身较大,检测实施起来要使用特制的机械载体和远程控制设备,超声检查系统和控制系统统一协作才能完成检查,见图1。
堆焊层超声检测方法和质量分级

堆焊层超声检测方法和质量分级G.1 范围本附录适用于承压设备用奥氏体不锈钢、镍合金等堆焊层内缺陷、堆焊层与基材未结合缺陷和堆焊层层下缺陷的超声检测方法和质量分级。
G.2 检测方法G.2.1堆焊层检测一般应在堆焊层侧进行。
G.2.2堆焊层侧检测时,使用双晶直探头和纵波双晶斜探头进行。
G.2.3基材侧检测时,使用单晶直探头和纵波斜探头进行。
G.3 探头G.3.1双晶探头G.3.1.1双晶探头(直、斜)两声束间的夹角应能满足有效声场覆盖全部检测区域,使探头对该区域具有最大的灵敏度。
两晶片间隔声效果应保证良好。
G.3.1.2双晶探头会聚区应位于堆焊层和基材的结合部位。
探头标称频率为2MHz ~ 5MHz 。
斜探头折射角度一般应为70°左右,需要时也可以采用其他角度的探头,但不应小于60°。
G.3.2单晶直探头探头的直径一般不应超过φ30mm,标称频率为 2MHz ~5MHz 。
G.3.3纵波斜探头一般选择折射角45°( K1)的探头,其标称频率为2MHz ~ 5MHz 。
G.4 对比试块G.4.1对比试块堆焊层表面的状态应和工件堆焊层的表面状态相同。
G.4.2对比试块应采用与产品部件相同的焊接工艺堆焊,也可用被检材料的多余部分或延伸部位堆焊制成。
G.4.3双晶直探头检测采用T1型试块,基材厚度T至少应为堆焊层厚度的 2倍。
试块堆焊厚度应大于等于被检工件的堆焊层厚度。
T1型试块如图 G.1所示。
图 G.1 T1 型试块G.4.4纵波双晶斜探头检测采用T2型试块,基材厚度T至少应为堆焊层厚度的2倍。
试块堆焊厚度应大于等于被检工件的堆焊层厚度。
T2型试块如图 G.2所示。
图 G.2 T2 型试块G.4.4单晶直探头和纵波斜探头检测采用T3型试块。
被检工件基材厚度和试块基材厚度T差不应超过 10%。
T3型试块如图G.3所示。
图 G.3 T3 型试块G.5 灵敏度G.5.1采用T1型试块的校准a)检测堆焊层内缺陷时,将双晶直探头放在试块的堆焊层表面上,用试块上右侧 4个φ 3mm平底孔绘制距离 -波幅曲线,并以此曲线作为基准灵敏度;b)检测堆焊层层下缺陷时,将双晶直探头放在试块的堆焊层表面上,移动探头使其从试块上基材内φ 3mm平底孔获得最大波幅,调整衰减器使回波幅度为满刻度的 80%,以此作为基准灵敏度;c)检测基材与堆焊层未结合缺陷时,将双晶直探头放在试块的堆焊层表面上,移动探头使其从φ 10mm平底孔获得最大波幅,调整衰减器使回波幅度为满刻度的 80%,以此作为基准灵敏度。
第四节堆焊层超声波探伤
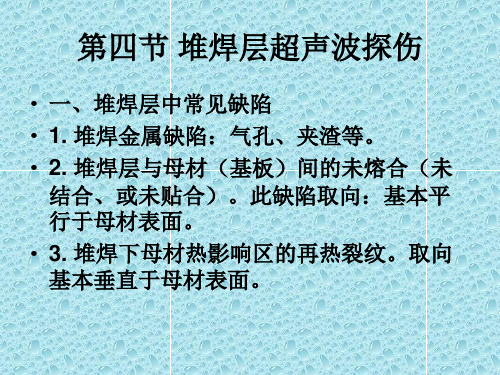
合、裂纹等。 • 探伤特点:大K值,短前沿,一次波探测根
部。
• 二、探测条件 • 1. 仪器 • 较窄始脉冲,始脉冲占宽≤2.5mm。 • 高分辨率。□CS-1、CS-2、CS-3、CS-4
试块上R5和R6.6圆弧回波横波分辨率≥6dB。
探头使Φ3平底孔最大回波达80%满幅。
• 2)双斜探头置T2试块堆焊层表面,移动探 头使Φ1.5mm长横孔最大回波达80%满幅。
• 3)纵波斜探头,在试块基板一侧移动探头 使Φ1.5mm长横孔最大回波达80%满幅。
• △扫查灵敏度比上述基准灵敏度高6dB。
④扫查方式:
• 探头在工件堆焊层一侧扫查时,双晶探头 隔声层平面应平行于堆焊方向,且在堆焊 方向和垂直于堆焊方向两个互相垂直方向 扫查。
含碱性。
• 三、探测准备 • 1. 入射点:在钢制CSK-ⅠA试块上测,或
在钢制(或铝制)半园试块上测。 • 2. 折射角: • 在铝制试块(JB/T4730-2005)上测。
tg 1 L
d
• 3. 扫描线比例
• ①可在JB/T4730-2005规定铝制Φ2×40长 横孔试块上调(按水平中深度调),为调 准确。
• ⑤ 缺陷测量 • 发现缺陷用6dB法测长和面积。 • ⑥ 验收 • 按JB/T4730-2005不允许存在缺陷直径大
于
• 40mm未结合部位。缺陷直径小于25mm的 未结合区评为Ⅰ级,允许存在。缺陷直径 在25mm~40mm范围内的未结合区评为Ⅱ 级,是否允许存在根据检测委托确定。
• 3. 堆焊层下母材热影响区再热裂纹及堆焊 层界面缺陷检测。
• 纵波比横波在柱子状方向衰减少,出现草 状回波少一些。
堆焊层超声波测厚探讨

( ri B i r o t. H i n j n a i,5 0 6 C ia Ha n o e .Ld , e ogi gH r n 10 4 , hn ) b l C l a b
第 5期 21 0 1年 9月
锅
炉
制
造
No 5 .
BOI LER M ANUFACTURI NG
Sp2 I e . 01
文 章 编 号 : N 3—14 (0 10 0 5 0 C2 2 9 2 l )5— 0 0— 4
堆 焊 层 超 声 波 测 厚 探 讨
任伟涛 , 晶涛 , 孙 关会群
0 引 言
随着工业发展及保证各 项性能 , 各种大型设备
( 电、 型化 工 容器 等 ) 采用 奥 氏体 或者 镍基 核 大 均 堆 焊结构。 由于母 材厚 度不 同和堆 焊部 位 结构 多
石化 容器 中厚度 为 10 m 0 m左 右 的简 体 采用 内壁堆焊 , 时筒 体 的椭 圆度 允许公 差要求 较高 , 同 故 堆焊层 表 面未进 行 机 械加 工 , 母 材侧 进 行超 从
容器产 品堆焊 层 的超 声波ห้องสมุดไป่ตู้测厚方 法 , 以供 参考 。
1 堆 焊 层测 厚 面 的选 择
1 1 母 材一侧 表面 测厚 .
穿过堆 焊层 和母 材 时 , 在 结合 面上 产生 一 定量 会 的反射 回波 。超声 波测厚 就是利 用结合 面 的反 射 回波来 测定 堆焊层 的厚度 。
3 1 超 声波仪 器的选 择 . 按 相 关 技 术 文 件 , 焊 层 的 厚 度 控 制 在 堆
【特种设备高级考试】八、不锈钢堆焊层超声检测
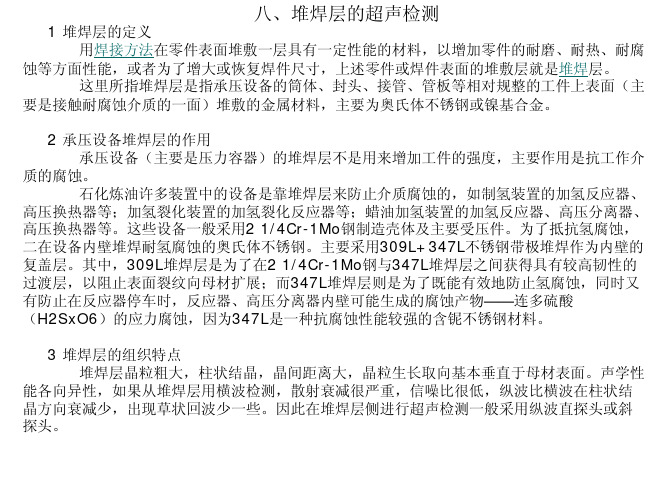
3) 对比试块 a 试块T1----堆焊层检测,基材厚度≥2δ b 试块T2----母材侧检测,基材厚度±10% c 试块T3-a)----母材侧检测界面未结合,基材厚度±10% d 试块T3-b)----堆焊层检测界面未结合,基材厚度≥2δ
T1型试块
T2型试块
T3型试块
4) 灵敏度校准 采用T1型试块的校准
a) 纵波双晶斜探头灵敏度的校准:将探头放在试块的堆焊层表面上,移动探 头使从φ1.5mm横孔获得最大反射波幅,调节衰减器使回波幅度为满刻度的 80%,以此作为基准灵敏度。
b) 双晶直探头灵敏度的校准:将探头放在试块的堆焊层表面上,移动探头使 其从φ3mm平底孔获得最大波幅,调整衰减器使回波幅度为满刻度的80%,以此 作为基准灵敏度。
ASME规范第Ⅴ卷规定,用直探头检测时,可以选择在基材侧或堆焊层侧进行 检测,但使用斜探头检测时则应在堆焊层进行。
2) 探头的选择 双晶探头: a) 双晶探头(直、斜)两声束间的夹角应能满足有效声场覆盖全部检测区
域,使探头对该区域具有最大的检测灵敏度。探头总面积不应超过325mm2, 频率2.5MHz,为了达到所需的分辨力,也可采用其他频率。两晶片间隔声效果 应保证良好。
八、堆焊层的超声检测
1 堆焊层的定义 用焊接方法在零件表面堆敷一层具有一定性能的材料,以增加零件的耐磨、耐热、耐腐
蚀等方面性能,或者为了增大或恢复焊件尺寸,上述零件或焊件表面的堆敷层就是堆焊层。 这里所指堆焊层是指承压设备的筒体、封头、接管、管板等相对规整的工件上表面(主
要是接触耐腐蚀介质的一面)堆敷的金属材料,主要为奥氏体不锈钢或镍基合金。
回波幅度为满刻度的80%,以此作为基准灵敏度。 b) 单直探头灵敏度的校准:将探头放在母材一侧,使φ10mm平底孔回波幅
- 1、下载文档前请自行甄别文档内容的完整性,平台不提供额外的编辑、内容补充、找答案等附加服务。
- 2、"仅部分预览"的文档,不可在线预览部分如存在完整性等问题,可反馈申请退款(可完整预览的文档不适用该条件!)。
- 3、如文档侵犯您的权益,请联系客服反馈,我们会尽快为您处理(人工客服工作时间:9:00-18:30)。
堆焊层超声检测方法
1.1堆焊层晶体结构的特点
当设备既要求具有较高的强度,又要求具有良好的耐腐蚀性时,往往在其表面堆焊一层具有上述性能的材料,如不锈钢或镍基合金等。
奥氏体不锈钢和镍基合金堆焊层在凝固过程中没有奥氏体向铁素体转变的相变,在室温下仍然保留铸态奥氏体晶粒。
因此晶粒较粗大,对超声波的衰减较为严重。
此外堆焊层金属在冷却时,母材方向散热条件好,因此奥氏体晶粒生长取向基本垂直于母材表面。
特别是采用带极堆焊工艺时,柱状晶更为典型,声学性能各向异性明显。
对于这种材料采用纵波直探头检测,声波沿柱状晶方向传播衰减较小。
而采用横波斜探头检测时,散射衰减就比较严重,显示屏上会出现草状回波,信噪比低。
1.2堆焊层中常见的缺陷
堆焊层中常见的缺陷有如下几种:
1.堆焊层内的缺陷,如气孔、夹杂、层间未熔合等;
2.堆焊层与基体(母材)间的未熔合(未结合缺陷),其取向基本上平行于母材表面;
3.堆焊层以下母材热影响区的再热裂纹,其取向基本上垂直于母材表面且垂直于堆焊方向。
7.4.3超声检测方法及探头的选择
1.3.1超声检测方法
1.采用双晶直探头和纵波双晶斜探头从堆焊层侧对堆焊层进行超声检测。
2.采用单直探头和纵波单斜探头从母材侧对堆焊层进行超声检测。
1.3.2探头的选择
1.单直探头探头面积一般不应超过625mm2,频率为2MHz~5MHz。
2.纵波斜探头探头频率为2MHz~5MHz,K L=tanβL=1的探头。
3.双晶探头双晶探头(直、斜)两声束之间的夹角应能满足有效声场覆盖全部检测区域,使探头对该区域具有最大的检测灵敏度。
探头总面积不得超过325 mm2,频率为2.5 MH Z,为了达到所需要的分辨力,也可以采用其他频率。
两晶片间隔声效果应保证良好。
纵波双晶斜探头的K=2.75(折射角K=tgβL=2.75,β0),焦点深度应位于堆焊层与母材的结合部位。
L=70
1.4检测堆焊层应用对比试块的要求和型号的选择
1.4.1对比试块的要求
对比试块应采用与被检工件材质相同或声学特性相近的材料,并采用相同的焊接工艺制成。
其母材、熔合面和堆
焊层中,均不得有大于或等于Φ2mm平底孔当量直径的缺陷存在。
试块堆焊层表面状态应和工件堆焊层的表面状态相同。
1.4.2试块型号的选择
1.从堆焊层侧检测采用T1型试块,其母材厚度T至少应为堆焊层厚度的两倍,如图1.34所示。
图1.34 T1型试块
2.从母材侧进行检测采用T2型试块,母材厚度T与被检母材的厚度差不得超过10%。
如图1.35所示。
如果工件厚度比较大,则该试块的长度应能满足检测要求。
图1.35 T2型试块
3.检测堆焊层与母材之间的未结合,采用T3试块。
当从母材侧进行检测时,采用T3(a)型试块,被检测工作的母材厚度与试块母材厚度差不应超过10%。
当从堆焊层侧检测时,采用T3(b)型试块,试块的母材厚度至少应为堆焊厚度的两倍。
T3型试块如图1.36所示。
图1.36 T3型试块
1.5检测灵敏度校准
1.5.1采用T1型试块灵敏度的校准
1.纵波双晶斜探头灵敏度的校准
将探头放置在试块堆焊层的表面上,移动探头使从Φ1.5mm横孔上获得最大反射波,调节衰减器使回波幅度为显示屏满刻度的80%,以此作为基准灵敏度。
2.双晶直探头灵敏度的校准
将探头放置在试块堆焊层的表面上,移动探头使其从Φ3mm平底孔上获得最大波幅,调整衰减器使回波幅度为显示屏满刻度的80%,以此作为基准灵敏度。
1.5.2采用T2型试块灵敏度的校准
1.单直探头灵敏度的校准
将单直探头放置在母材一侧,使Φ3mm平底孔回波幅度为显示屏满刻度的80%,以此作为基准灵敏度。
2.纵波斜探头灵敏度的校准
将探头放置在试块母材的表面上,移动探头使从Φ1.5mm横孔上获得最大反射波,调节衰减器使其回波幅度为显示屏满刻度的80%,以此作为基准灵敏度。
1.5.3采用T3型试块灵敏度的校准
1.单直探头灵敏度的校准
将探头放置在母材一侧,如图1.36(a)所示,使Φ10mm
平底孔回波幅度为显示屏满刻度的80%,以此作为基准灵敏度。
2.双晶直探头灵敏度的标准
将探头放置在堆焊层一侧,如图1.36(b)所示,使Φ10mm平底孔回波幅度为显示屏满刻度的80%,以此作为基准灵敏度。
1.6扫查方法
1.6.1.根据检测的对象,分别在母材一侧或堆焊层一侧进行扫查。
如果对检测结果有怀疑时,也可从另一侧进行补充检测。
1.6.
2.扫查灵敏度应在基准灵敏度的基础上再提高6dB。
1.6.
3.采用双晶斜探头检测时应在堆焊层表面按90°方向进行两次100%扫查;采用双晶直探头检测时应垂直于堆焊层方向进行扫查。
且在扫查时,应保证双晶探头隔声层平行于堆焊方向。
1.6.4.缺陷当量尺寸应按6dB法确定其边界。
1.6.5.堆焊层下母材热影响区再热裂纹的检测,此种缺陷基本上垂直于检测面,危害性大,一般采用纵波双晶斜探头从堆焊层侧进行检测,缺陷检出率高,效果好。
1.7 JB/T4730.3(5.2)-2005标准质量等级评定
堆焊层质量等级评定见表1.8
表1.8 堆焊层质量分级。