模具典型零件的加工工艺
《机械制造技术基础》教学大纲

《机械制造技术基础》教学大纲习惯专业:机械类各专业课程性质:必修课总学时:108总学分:6一、课程性质、目的与任务《机械制造技术基础》是模具设计与制造专业必修的一门专业基础课。
是一门集“教、学、做”一体化的课程。
该课程是以“典型零件机械加工工作过程”为主线,惯穿工艺规程制定与实施,有机融合了金属切削加工的基本知识及常用机床夹具的基本知识,而建设的一门综合性课程。
课程讲授了常用刀具的结构与选择、机械加工工艺规程、典型零件的加工工艺的编制、机械加工的质量分析、机械装配工艺、常用夹具的设计方法等内容。
并对各类刀具的特点,金属切削过程及其有关规律,工艺规程的制定,机械加工质量的概念,机械加工精度及其影响因素、装配工艺及其与机械加工工艺的关系,保证装配精度的方法,装配尺寸链的建立,进行了简要的介绍。
本课程在内容方面侧重于基础知识、基础理论与基本分析方法的讲授,在培养实践能力方面着重机械加工技能的基本训练。
使学生能正确地选择刀具与夹具,培养学生“机械加工工艺规程的制定与实施”的能力。
二、教学基本要求(一)知识教学目标1、掌握金属切削的基本原理、刀具几何参数的表示、切削用量的选择原则,熟悉各类刀具的特点,认识金属切削过程及其有关规律。
2、熟悉机床的要紧类型、性能特点及其工艺范围,具有合理选用机床的基本知识。
3、熟悉生产过程的基本概念;掌握工艺路线拟订的原则与步骤及零件加工工艺规程编制的通常方法;4、掌握“六点定位原则”及机械加工中零件的定位基准的选择;5、掌握“工艺尺寸链原理”及加工余量的确定与工艺尺寸链的计算,熟悉机械加工生产率与经济性,并能够进行工艺文件的初步规划。
6、掌握工件在夹具中定位与夹紧的基本原理及方法,掌握各类机床夹具的设计要点。
7、熟悉机械加工质量的概念,机械加工精度及其影响因素、机械加工表面质量及其影响因素。
8、熟悉装配工艺及其与机械加工工艺的关系,掌握保证装配精度的方法,熟悉装配尺寸链的建立,初步掌握装配工艺规程的制订。
模具典型零件的加工
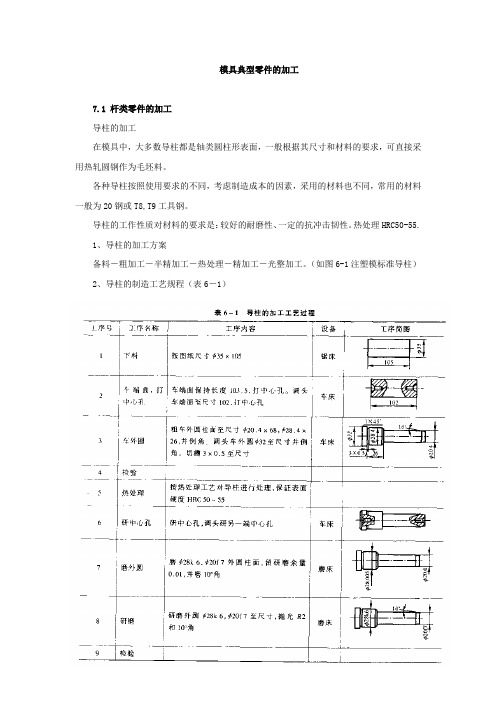
模具典型零件的加工7.1 杆类零件的加工导柱的加工在模具中,大多数导柱都是轴类圆柱形表面,一般根据其尺寸和材料的要求,可直接采用热轧圆钢作为毛坯料。
各种导柱按照使用要求的不同,考虑制造成本的因素,采用的材料也不同,常用的材料一般为20钢或T8,T9工具钢。
导柱的工作性质对材料的要求是:较好的耐磨性、一定的抗冲击韧性。
热处理HRC50-55.1、导柱的加工方案备料-粗加工-半精加工-热处理-精加工-光整加工。
(如图6-1注塑模标准导柱)2、导柱的制造工艺规程(表6-1)导柱的加工工序不是固定不变的,根据不同的生产类型、结构形式和尺寸精度、工厂设备情况,其工序的划分和工艺方法也就不同。
3、导柱加工过程中的定位一般采用设计基准和工艺基准重合的原则,在两端加工中心孔,以两中心孔轴线为各工序的定位基准,中心孔的形状和精度对导柱的加工质量有着直接的关系。
为了确保精加工时的精确定位作用,中心孔在热处理后必须进行对研和修整。
对研中心孔一般采用锥形砂轮或梅花顶尖:4、导柱的研磨一般对于配合精度要求较高的导柱,都要安排研磨工序,以提高表面质量和降低粗糙度。
二、模柄与顶杆的加工模柄的设计已标准化,常用的模柄有:压入式、旋入式、凸缘式、槽形式和浮动式等,和顶杆一样都属于台阶轴类零件,材料选用45钢,热处理HRC40-45,这类零件一般也是采用中心孔作为精加工的定位基准,终加工采用精磨工艺并靠磨端面,保证端面跳动要求。
7.2 套类零件的加工模具中的套类零件主要有:导套、护套和套类凸模等。
导套的材料和导柱一样,一般采用圆钢下料,热处理要求为HRC58-62,制造工艺也不是固定的。
导套的加工方案:备料-粗加工-半精加工-热处理-精加工-光整加工。
7.3 板类零件的加工一、板类零件加工质量的要求模具中各种板类零件较多,如:模座、垫板、固定板、卸料板、推件板等等。
虽然形状、材料、尺寸精度和使用性能要求各不相同,但都是有平面和孔系组成,这类零件的加工质量要求主要有以下几点:①平行度和垂直度要求,一般均按GB1184-80的规定,具体公差执行冷冲模和塑料模的有关国家标准。
典型零件制造工艺

典型零件制造工艺一、前言典型零件制造工艺是机械制造领域中的重要内容,其涉及到材料的选择、加工方式的确定、设备的选择和加工精度等方面。
本文将详细介绍典型零件制造工艺,包括铸造、锻造、冲压、机加工等方面。
二、铸造铸造是指将金属或非金属熔化后倒入模具中,经过凝固后得到所需形状和尺寸的零件。
铸造分为砂型铸造、压力铸造和精密铸造等多种类型。
1. 砂型铸造砂型铸造是指用砂做模具,将熔化的金属倒入模具中,待冷却凝固后取出成型的一种方法。
其步骤包括:(1)设计模具:根据零件图纸设计好模具,并确定好每个部位所使用的材料。
(2)制作芯子:根据零件图纸制作好芯子,并在芯子表面涂上防粘剂。
(3)制作模板:根据设计好的模具尺寸和形状,在木板上切割出相应大小和形状的板块。
(4)制作模具:将制作好的模板放入砂箱中,把芯子放入模板内,再倒入一定数量的砂子,在表面压实。
(5)浇注铸件:在砂型上开孔,将熔化的金属倒入孔口中,待冷却后取出铸件。
2. 压力铸造压力铸造是指将金属液体通过高压喷射到模具中形成零件的一种方法。
其步骤包括:(1)设计模具:根据零件图纸设计好模具,并确定好每个部位所使用的材料。
(2)加热金属:将所需金属加热至液态状态。
(3)注射成型:将液态金属通过高压喷射到模具中,待冷却后取出铸件。
3. 精密铸造精密铸造是指采用特殊工艺,在高温下将金属液体注入陶瓷或合金型芯中进行凝固成型的一种方法。
其步骤包括:(1)设计模具:根据零件图纸设计好模具,并确定好每个部位所使用的材料。
(2)制作芯子:根据零件图纸制作好芯子,并在芯子表面涂上防粘剂。
(3)注射成型:将液态金属通过高压喷射到模具中,待冷却后取出铸件。
三、锻造锻造是指将金属材料加热至一定温度后,通过压力使其发生塑性变形的一种方法。
锻造分为自由锻造、模锻和冷锻等多种类型。
1. 自由锻造自由锻造是指在无模具的情况下,将金属材料加热至一定温度后,通过人工或机械压力进行塑性变形的一种方法。
【机械加工】典型模具零件的加工:导套

主要表面加工应注意: ①内孔Φ32H7,Ra0.2μm:工艺路线采用钻—粗镗—半精镗— 粗磨—精磨—研磨;选择万能外圆磨床;控制切削用量;充 分冷却。
②外圆的Φ45r6,Ra0.4μm:在加工阶段的划分、机床的选用、 切削用量的控制方面与内孔加工相图。工艺路线采用粗车— 半精车—粗磨—精磨。
在常温下加工,并且不引起工件的化 学或物 相变化 ﹐称冷 加工。 一般在 高于或 低于常 温状态 的加工 ﹐会引 起工件 的化学 或物相 变化﹐
称热加工。冷加工按加工方式的差别 可分为 切削加 工和压 力加工 。热加 工常见 有热处 理﹐煅 造﹐铸 造和焊 接。 另外装配时常常要用到冷热处理。例 如:轴 承在装 配时往 往将内 圈放入 液氮里 冷却使 其尺寸 收缩, 将外圈 适当加 热使其 尺寸放 大,然
1992年投资为1000万美元。英国政府 也制订 了纳米 科学计 划。在 机械、 光学、 电子学 等领域 列出8个 项目进 行研究 与开发 。为了 加强欧
洲开发MEMS的力量,一些欧洲公司 已组成 MEMS开发集 团。
目前已有大量的微型机械或微型系统被 研究出 来,例 如:尖 端直径 为5
μm的微型镊子可以夹起一个红 血球, 尺寸为 7mm×7mm×2mm的微型 泵流量 可达250μl/min能开动 汽车, 在磁场 中飞行 的机器 蝴蝶, 以
7、零件的修研
导套的研磨加工,其目的在于进一步提高被加工表面 的质量,以达到设计要求。
在单件小批量生产中可以采用简单的研磨工具,如图 3.8所示。在普通车床上进行研磨。研磨时,由主轴带动研 磨工具旋转,手握在研具上的导套,作轴线方向的往复直 线运动。通过调节研具上的调整螺钉和螺母,可以调整研 磨套的直径,以控制研磨量的大小。
模具滑块的加工工艺与编程
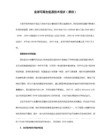
毕业设计(论文)题目:模具滑块的加工工艺与编程分院:机电学院专业:数控技术姓名:徐璐玲指导教师:贾相武2011年5月26日中文摘要随着科学技术飞速发展和经济竞争的日趋激烈,机械产品的更新速度越来越快,复杂形状的零件越来越多,精度要求越来越高,多品种、小批量生产的比重明显增加,激烈的市场竞争使产品研制生产周期越来越短,传统的加工设备和制造方法已难以适应这种多样化、柔性化与复杂形状零件的高速高质量加工要求。
数控技术及数控机床在当今机械制造业中的重要地位和巨大效益,显示了其在国家基础工业现代化中的战略性作用。
数控技术及数控机床的广泛应用,给机械制造业的产业结构、产品种类和档次以及生产方式带来了革命性的变化。
它所控制的通常是位置、角度、速度等机械量和与机械能量流向有关的开关量。
数控技术的产生依赖于数据载体和二进制形式数据运算的出现。
数控加工技术作为先进生产力的代表,在机械及相关行业领域发挥着重要的作用,机械制造的竞争,其实质是数控技术的竞争。
本次设计就是进行数控加工工艺分析模具滑块组合件,侧重于该零件的加工精度,主要设计内容有:完成该零件的工艺规程(包括工艺过程卡、工序卡和数控刀具卡)和主要配合形式的分析,并绘制零件图、装配图。
用G代码编制该零件的数控加工程序,在则学习计算机辅助制造(CAM)相关知识,并编制其构架。
其中此次毕业设计中的配合精度要求是重点和难点。
关键词:工艺分析,数控加工,数控编程,三维造型目录一、概述 (4)1.1数控机床的优点 (4)1.2数控加工技术的发展趋势 (4)二、加工前的准备 (5)2.1零件图的分析 (5)2.1.1分析图样 (5)2.2加工工序划分的原则 (8)2.3加工设备的选用 (8)2.4确定装夹方案和选用夹具 (9)2.4.1定位原理 (9)2.4.2坐标系的设定 (9)2.4.3定位装夹的基本原则 (9)2.4.4选择夹具的基本原则 (10)2.5选择刀具 (10)2.6切削用量的确定 (11)三、数控加工工艺的编制 (12)3.1加工工艺的基本特点 (12)3.2数控加工工艺分析主要包括的内容 (12)3.3数控加工工艺分析的一般步骤及方法 (13)3.4加工方法的选择与加工方案的确定 (13)3.4.1加工方法的选择 (13)3.4.2数控加工零件工艺性分析 (13)3.4.3零件1加工分析 (14)3.4.4零件2加工分析 (17)3.5工序与工步的划分 (19)3.5.1工序的划分 (19)3.5.2工步的划分 (20)3.6加工路线的确定 (20)四、数控加工 (20)4.1加工工艺过程卡 (20)4.2程序 (22)4.2.1数控加工程序 (22)4.2.2数控加工程序 (30)五、总结 (34)六、致谢 (35)参考文献: (35)前言本课题的设计意义在于数控加工工艺分析,编制程序,在期间将发现的问题及时更正,将技术更新,充分将数控技术发挥到相应水平。
电子课件-《模具零件制造技术》A02-2660 模块四 典型模具零件加工工艺制定课题二 注塑模主要零件加工工艺

任务实施
(7)工件进行淬火、回火热处理,调整零件的性能,使 硬度达到要求。
(8) 采用平面磨削,精磨工件外表面,至图样要求的形 状和尺寸精度。一般外形尺寸尽量控制在上极限尺寸,留 适当的余量,便于后续的修正与调整。
(9)根据型腔要求,电火花放电成形加工内表面。一般 应尽量加工至下极限尺寸,留适当的余量(如果型腔需镀层, 还应考虑镀层厚度),便于研磨、抛光及后续的修正。
任务实施
一、工艺分析
注塑模型腔是注塑模中主要的工作零件之一。型 腔的铣削加工和电火花成形加工是塑料模具成形零件 必不可少的加工工序;对具有复杂空间曲面型腔的铣 削,通常采用数控铣床或加工中心;电火花成形加工常 放在对型腔淬火与回火后作为精加工。所以这两道加 工工序是型腔加工工艺过程中比较关键的工序。
(退火)→半精加工→调质→精加工→光整加工+火焰淬火、渗 氮、镀铬、镀钛→装配前修整。
工艺特点:成形零件尺寸精度有一定的要求,但钢材硬度要 求不高。
相关知识
(3)工艺路线:备料(锻件)→热处理(正火)→粗 加工→热处理(退火)→半精加工→表面处理(渗碳)→ 热处理(淬火与回火)→光整加工+表面处理(镀铬等) →装配前修整。
相关知识
2.典型工艺路线
注塑模成形零件的加工工艺过程和各工序的安排通常根 据成形零件的要求和特点有四种情况可供选择。
(1)工艺路线:备料(锻件)→退火→粗加工→ 热处理 (退火)→半精加工→淬火与回火→精加工→光整加工→表面 处理(渗氮、镀铬、镀钛等)→装配前修整。
工艺特点:成形零件的尺寸精度要求较高,钢材全淬硬。 (2)工艺路线:备料(锻件)→退火→粗加工→ 热处理
工艺特点:成形零件的尺寸精度要求不高,但要求钢材 全淬硬。
模具制造工艺
Page 9
模具材料的使用性能要求
• (1)硬度和耐磨性 这是最基本的性能要求。有了
一定的硬度和耐磨性,才能使模具在特定的工作条件下 ,保持形状和尺寸的稳定而不迅速发生变化。
• (2)强度、塑性和韧性 要求模具材料具有良好的
塑性,提高其抗脆断能力;要求具有高强度、高韧性和 高的抗疲劳强度,满足模具在工作时能承受高压和冲击 循环载荷。
Page 2
模具的基本结构与组成
• 材料成形模具的分类
• 1、冲压模 包括冲裁模、单工序模、复合模、级进模、汽车覆盖 件冲模、硬质合金冲模等。 • 2、塑料成型模具 包括注射模、压缩模、挤塑模、吹塑模、发泡 模等。 • 3、橡胶制品成型模 • 4、玻璃制品成型模 • 5、陶瓷模具 包括压缩模、注射模等。 • 6、锻造成形模具 • 7、压铸模 可按压室温度分为冷压室压铸机用压铸模、热压室压 铸机用压铸模。 • 8、铸造金属型模具 • 9、粉末冶金成型模 • 10、通用模具和经济模具
Page 6
模具与成形设备的连接
• 在确定了成形工艺和成形设备类型后,模具设计时,需 要对所选设备进行公称压力、工作速度、工作行程、连 接部位接口的几何尺寸等参数进行校核计算。模具与设 备通过模架(或模板)与设备相连,首先需要确定模具 与设备的连接形式和接口尺寸,模具的连接形式根据成 形工艺过程和成形设备的不同可采用螺钉、压板、或是 模柄等连接形式。接口尺寸是指模具外形结构形状及尺 寸与设备滑块和工作台面尺寸、设备工作行程、滑块最 大移动距离(设备开口高度或宽度)、送料所需空间和 取件所需空间等相应尺寸的匹配和适应性。模具结构尺 寸中,与设备相连的主要尺寸是模具闭合高度或模具厚 度,在设计时还要考虑它们与设备滑块工作行程之间的 关系。
典型加工工艺总结
典型加工工艺总结
一、简介
加工工艺是将原材料转化为成品的过程,涉及到一系列的机械和物理操作。
不同的材料、产品类型和制造要求需要不同的加工工艺。
在制造业中,加工工艺的选择、优化和创新对于提高产品质量、降低成本、增强市场竞争力至关重要。
二、典型加工工艺
1. 铸造工艺:铸造是一种将液态金属倒入模具中,待其冷却凝固后形成所需形状的工艺。
铸造工艺广泛应用于生产各类金属零件,如铸铁、铸铝等。
2. 锻造工艺:锻造是将热塑性状态的金属坯料通过压力加工制成所需形状和大小的工艺。
锻造可以提高金属的机械性能,广泛用于制造飞机、汽车和船舶等重型设备的零部件。
3. 焊接工艺:焊接是一种通过熔融金属或焊料,将分离的金属连接成一个整体的工艺。
焊接具有工艺简单、成本低等优点,广泛应用于建筑、造船、汽车制造等领域。
4. 切削加工工艺:切削加工是通过切削工具去除材料,形成所需形状和尺寸的工艺。
切削加工包括铣削、车削、钻孔等多种操作,广泛应用于机械制造、电子设备等领域。
5. 表面处理工艺:表面处理是对产品表面进行涂装、电镀、喷涂等处理的工艺。
表面处理可以提高产品的美观度、耐腐蚀性和耐磨性,广泛应用于建筑、家具、汽车等行业。
三、总结
加工工艺是制造业的核心,对于产品的质量和性能至关重要。
在实际生产中,需要根据原材料的性质、产品的要求以及生产条件等因素,选择合适的加工工艺。
同时,随着科技的不断发展,加工工艺也在不断创新和改进,以提高生产效率、降低成本并满足市场的多样化需求。
典型零件的选材及加工工艺路线分析讲解材料
轻量化
减轻材料重量,提高产品机动性,降低能源 消耗和排放。
环保化
发展可再生、可回收、可降解的材料,减少 对环境的污染。
智能化
研究具有自适应、自修复、自感应等功能的 智能材料。
新材料的研究与开发
碳纤维复合材料
具有高强度、轻质、耐高温等优点,广 泛应用于航空航天、汽车等领域。
高分子合成材料
具有优良的化学稳定性、绝缘性、耐 磨性等,在建筑、电子、化工等领域
03
材料的应用与发展趋势
材料的应用领域
01
航空航天
用于制造飞机、火箭等高强度、轻 质材料。
建筑领域
用于制造桥梁、高层建筑等高强度、 高耐久性材料。
03
02
汽车工业
用于制造发动机、变速器等耐磨、 耐高温材料。
电子产品
用于制造集成电路、晶体管等精密、 小型化材料。
04
材料的发展趋势
高性能化
提高材料的强度、硬度、耐高温等性能,以 满足更高要求的工业应用。
可加工性原则
材料应具有良好的可加工性, 以便于零件的制造和加工。
可维修性原则
材料应易于维修和更换,以提 高零件的使用寿命和降低维修 成本。
常用材料介绍
钢铁
钢铁是机械制造业中应用最广泛的材料之一,具 有高强度、良好的韧性和耐磨性。
铜及铜合金
铜及铜合金具有良好的导电性、导热性、耐腐蚀 性和加工性能,广泛应用于电气、电子、化工等 领域。
实例二:齿轮类零件的选材与加工工艺
灰铸铁
用于制造一般用途的齿轮,如减速器齿轮等。
球墨铸铁
用于制造高强度、高耐磨性的齿轮,如汽车变速毛坯准备
根据零件材料和尺寸要求,准备毛坯。
粗加工
典型零件加工工艺(轴和套筒)
25
1)主要表面及其精度要求 ①支承轴颈
是两个锥度为1:12的圆锥面,分别与两个双列 短圆锥轴承相配合。
支承轴颈是主轴部件的装配基准,其精度直接 影响主轴部件的回转精度,尺寸精度一般为IT5。
主轴两支承轴颈的圆度允差和对其公共轴线的 斜向圆跳动允差均为0.005 mm,表面粗糙度Ra值不 大于0.63µm。
21
热处理工序的安排
结构尺寸不大的中碳钢普通轴类锻件,一般在切削加工 前进行调质热处理。
对于重要的轴类零件(如机床主轴),则:
一般在毛坯锻造后安排正火处理,达到消除锻造应 力,改善切削性能的目的;
粗加工后安排调质处理,以提高零件的综合力学性 能,并作为需要表面淬火或氮化处理的零件的预备热处 理;
5
二、轴类零件的材料和毛坯
1、轴类零件的常用毛坯:
①光轴、直径相差不大的阶梯轴常采用热轧或 冷拉的圆棒料;
②直径相差较大的阶梯轴和比较重要的轴大都 采用锻件。
③当轴的结构形状复杂或尺寸较大时,也有采
用铸件的。
自由锻
中小批
毛坯锻造
模锻
大批大量
6
2、轴类零件的材料:
1)一般轴类零件:45钢应用最多,一般须经调
轴上有相对运动的轴颈和经常拆卸的表面,需要进
行表面淬火处理,安排在磨削前。或在粗磨后、精磨前
渗氮处理
22
四、 机床主轴加工工艺及其分析
23
24
(1)零件分析 对机床主轴的共同要求是必须满足机床
的工作性能:即回转精度、刚度、热变形、 抗振性、使用寿命等多方面的要求。
车床主轴是带有通孔的多阶台轴,普通 精度等级,材料为45钢。
9
顶尖的实施