管壳式热交换器结构
16.第十六章 管壳式换热器
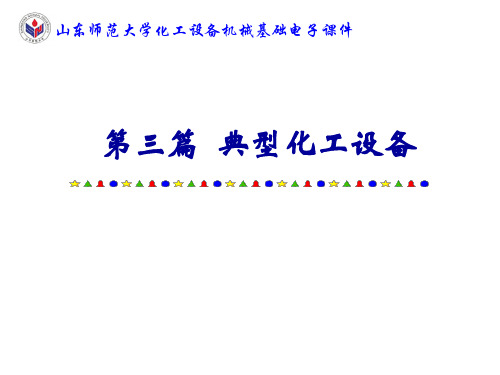
滚 柱 胀 杆
32
⑴胀接
要求管板硬度大于管子硬度,否则将管端退火后再胀接。
管板孔内开一个或两个环形槽,当胀管时管子产生塑性变 形,管壁被嵌入小槽内,可以提高连接强度和紧密性。 若管子用20钢, 则管板可选用什 么材料? 10、20、35、 Q235、Q255、 16Mn
33
胀接时管板上的孔可以是光孔,也可开槽。
FL t Et At FL s E S As
12
温差应力的产生
温差轴向力 F
t (t t ห้องสมุดไป่ตู้t 0 ) s (t s t 0 )
1 1 Et At E S AS
F 管壁内温差应力: t At F 壳壁内温差应力: s As
13
22
管箱与管程分程
管程分程常用的有1、2、4、6、8、10、12等。
23
三、管束
1.换热管的尺寸规格及材料
换热管管径越小,换热器单位体积的传热面积就越大,设 备就越紧凑,但制造麻烦。洁净的流体可取小管径;常用 的规格有Φ19×2、Φ25×2.5、Φ38×2.5、 Φ57×3.5等 规格。 管子材料,应根据设计压力、温度、介质腐蚀等选择,有 10 、 20、1Cr18Ni9Ti、Cu、Al等。对于低压、强腐蚀性 介质的换热器可选用石墨、聚四氟乙烯。 管子长度,推荐管长有1.0,1.5,2.0,2.5,3.0,4.5, 6.0,7.5,9.0,12.0m,其中以3m和6m最为普遍。
34
⑵焊接
优点: ①管板孔表面粗糙度要不高,管端不需退火和磨光。
②强度高,抗拉脱力强,气密性好。应用广泛。 缺点:①管子破漏需拆卸更换困难,一般堵死。 ②管子、管板间存在间隙,易出现缝隙腐蚀。
管壳式换热器的设计
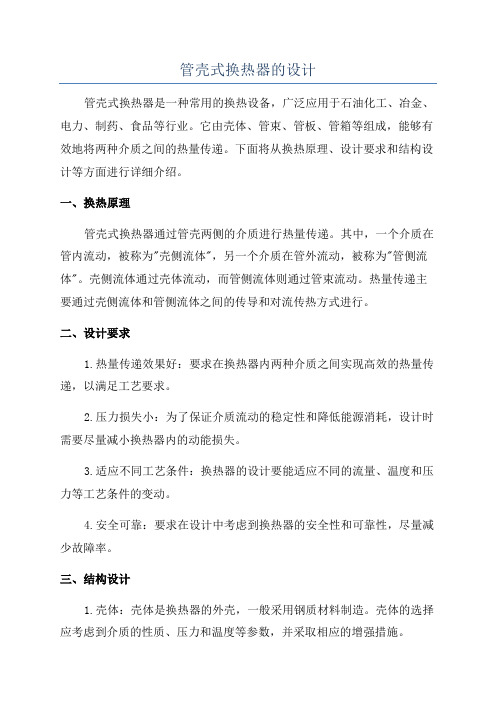
管壳式换热器的设计管壳式换热器是一种常用的换热设备,广泛应用于石油化工、冶金、电力、制药、食品等行业。
它由壳体、管束、管板、管箱等组成,能够有效地将两种介质之间的热量传递。
下面将从换热原理、设计要求和结构设计等方面进行详细介绍。
一、换热原理管壳式换热器通过管壳两侧的介质进行热量传递。
其中,一个介质在管内流动,被称为"壳侧流体",另一个介质在管外流动,被称为"管侧流体"。
壳侧流体通过壳体流动,而管侧流体则通过管束流动。
热量传递主要通过壳侧流体和管侧流体之间的传导和对流传热方式进行。
二、设计要求1.热量传递效果好:要求在换热器内两种介质之间实现高效的热量传递,以满足工艺要求。
2.压力损失小:为了保证介质流动的稳定性和降低能源消耗,设计时需要尽量减小换热器内的动能损失。
3.适应不同工艺条件:换热器的设计要能适应不同的流量、温度和压力等工艺条件的变动。
4.安全可靠:要求在设计中考虑到换热器的安全性和可靠性,尽量减少故障率。
三、结构设计1.壳体:壳体是换热器的外壳,一般采用钢质材料制造。
壳体的选择应考虑到介质的性质、压力和温度等参数,并采取相应的增强措施。
2.管束:管束是由多根管子组成的,一般采用金属材料或塑料制造。
管束的设计要考虑到介质对管材的腐蚀性、温度和压力等参数,同时也要考虑到换热面积的要求。
3.管板:管板位于管束两端,起到支撑和固定管束的作用,一般采用钢质材料制造。
管板的设计要考虑到壳侧和管侧流体的流动特性,并采用合适的孔洞布置,以保证流体的均匀流动。
4.管箱:管箱是安装在管板上的设施,主要用于集流壳侧流体并将其引导出换热器。
管箱的设计应考虑到壳侧流体的流动特性和流量等参数,以实现流体的顺畅流动。
在设计过程中,需要进行换热器的热力计算和结构力学计算,以确定壳体、管束和管板等部件的尺寸和选材。
同时,还需要根据不同工艺和使用条件的要求,进行热交换面积的计算和确定。
管壳式换热器的工作原理及结构

3 . u型管 式换热 器 u型 管式换 热 器仅有 一块 管板 。 它 是将 管子 弯成 u型 ,管子 两端 固定 在 同一 块管 板上 。由于 壳体 和管 子分 开 ,管束可 以 自由伸缩 ,不 会 因管壁 、壳壁 之间 的温 度差 而 产生 热应 力 ,热 补偿 性 能好 。管 程为
双管 程 ,流 程较 长 ,流速 较 高 ,传热 性能 好 ,承压 能力 强 。u型管 式 换热 器 ,一 般使 用高 温高 压 的情况 下 。尤其 在压 力较 高 的情况 下 ,在 弯管 段壁厚要 加厚 ,以弥 补弯 管后管壁 的减薄 。 如 壳程 需要 经常 清 洗 的管束 ,则要求 采 用正 方形排 列 ,一 般情 况 下都按 三 角形排 列 ,管程 为偶数 。
管壳式换热器结构设计
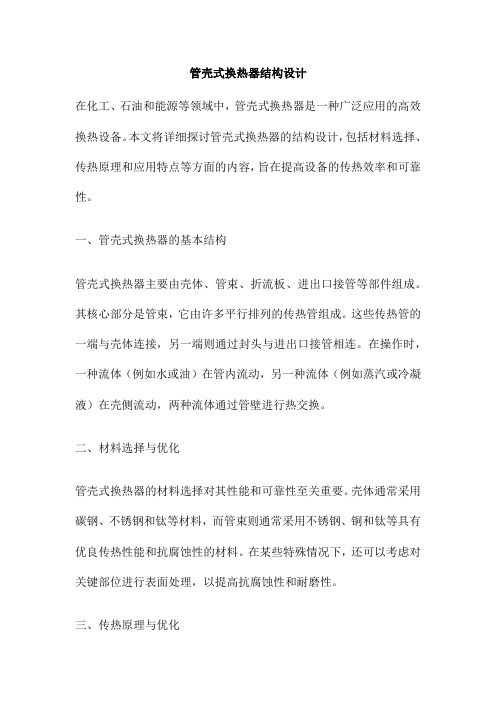
管壳式换热器结构设计在化工、石油和能源等领域中,管壳式换热器是一种广泛应用的高效换热设备。
本文将详细探讨管壳式换热器的结构设计,包括材料选择、传热原理和应用特点等方面的内容,旨在提高设备的传热效率和可靠性。
一、管壳式换热器的基本结构管壳式换热器主要由壳体、管束、折流板、进出口接管等部件组成。
其核心部分是管束,它由许多平行排列的传热管组成。
这些传热管的一端与壳体连接,另一端则通过封头与进出口接管相连。
在操作时,一种流体(例如水或油)在管内流动,另一种流体(例如蒸汽或冷凝液)在壳侧流动,两种流体通过管壁进行热交换。
二、材料选择与优化管壳式换热器的材料选择对其性能和可靠性至关重要。
壳体通常采用碳钢、不锈钢和钛等材料,而管束则通常采用不锈钢、铜和钛等具有优良传热性能和抗腐蚀性的材料。
在某些特殊情况下,还可以考虑对关键部位进行表面处理,以提高抗腐蚀性和耐磨性。
三、传热原理与优化管壳式换热器的传热原理主要是通过对流传热和热传导的组合来实现的。
为了提高设备的传热效率,可以采用以下措施:1、改变折流板的形状和布置,以增加壳侧流体的湍流度。
2、选择具有高导热系数的材料,以提高管壁的热传导性能。
3、适当增加管束数量和布置密度,以增加传热面积。
四、应用特点与优势管壳式换热器在各种工业领域中得到了广泛应用,主要特点有:1、结构紧凑,占地面积小,易于布置。
2、材料选择广泛,适用于各种不同的工艺条件和腐蚀性介质。
3、传热效率高,能够实现两种流体的有效热交换。
4、制造工艺成熟,操作维护方便,使用寿命较长。
五、结论本文对管壳式换热器的结构设计进行了全面分析,包括材料选择、传热原理和应用特点等方面的内容。
通过合理的结构设计,可以显著提高管壳式换热器的传热效率和可靠性,使其在各种工业领域中发挥更加重要的作用。
随着技术的不断进步,管壳式换热器的设计和制造水平也将不断提升,为工业生产带来更大的价值。
六、展望随着工业生产的不断发展和能源紧缺的压力日益增大,管壳式换热器的应用前景更加广阔。
管壳式换热器结构介绍

3、管壳程流体的确定
主要根据流体的操作压力和温度、可以利用的压力降、结构和腐蚀 特性,以及所需设备材料的选择等方面,考虑流体适宜走哪一程。下面 的因素可供选择时考虑:
适于走管程的流体有水和水蒸气或强腐蚀性流体;有毒性流体;容易 结构的流体;高温或高压操作的流体等。
1、管壳式换热器结构介绍
管壳式换热器:是以封闭在壳体中管束的壁面作为传热面的间 壁式换热器,这种换热器结构较简单、操作可靠,可用各种结构材 料(主要是金属材料)制造,能在高温、高压下使用,是目前应用 最广的类型。(设计制造遵循标准:国外 TEMA ASME 国内 GB151、GB150)
换热器封头选取原则
换热器折流板
单弓形折流板:优点是可以达到最大的错流,缺点是压降较高,且窗口 的管束容易发生振动;设计要点是折流板圆缺率在17%-35%之间,折流 板间距在0.2-1.0倍的壳径。此种类型折流板适用于大部分场合。
NITW:该折流板窗口不布管,管少,需要的壳体直径大。设计要点:15%的 折流板圆缺率。适合的场合是气体振动和压降受限。
谢谢!
K型壳体:主要用于管程热介质,壳侧蒸发的工况,在废热回收条件下使 用。
X型壳体:冷热流体属于错流流动,其优点是压降非常小,当采用其他壳 体发生振动,且通过调整换热器参数无法消除该振动时可以使用此壳体 形式,其不足之处是流体分布不均匀,X型壳体并不经常使用。
在化工工艺手册中,I型壳体类型可EDR软件中的不是同一种壳体, 其形式见I1,它的使用方式仅有一种搭配,就是BIU,U型管换热器。
螺纹管性能特点
在管子类型中,螺纹管属于管外扩展表面的类型,在普通换热管外 壁轧制成螺纹状的低翅片,用以增加外侧的传热面积。螺纹管表面积比 光管可扩展1.6-2.7倍,与光管相比,当管外流速一样时,壳程传热热阻 可以缩小相应的倍数,而管内流体因管径的减小,则压力降会略有增大。 螺纹管比较适宜于壳程传热系数相当于管程传热系数1/3-3/5的工况。
22管壳式换热器的结构计算

22管壳式换热器的结构计算管壳式换热器是一种常见的热交换设备,广泛应用于石化、冶金、化工等各个领域。
它由外壳(壳体)、管束、端盖和密封件等组成。
下面将介绍管壳式换热器的结构计算。
1.外壳(壳体)的计算:外壳是管壳式换热器的主体部分,它直接承受介质的压力。
外壳的计算需要考虑外径、壁厚、材料强度等因素。
计算公式为:P=2×t×σ/[(D-d)×η]其中,P为外壳所承受的最大压力;t为外壳的壁厚;σ为外壳所采用材料的允许应力;D为外壳的外径;d为外壳的内径;η为环向系数。
2.管束的计算:管束是管壳式换热器中用于传送热量的部分,它由多个平行布置的管子组成。
管束的计算需要考虑管子的长度、外径、壁厚等因素。
计算公式为:P=2×t×σ/[(D-d)×η]其中,P为管束所承受的最大压力;t为管子的壁厚;σ为管子所采用材料的允许应力;D为管子的外径;d为管子的内径;η为环向系数。
3.端盖的计算:端盖是管壳式换热器的两端部分,它通常由钢板制成。
端盖的计算需要考虑其结构的强度和稳定性。
计算公式为:t=K√(P×h×b^3/(2×σ))其中,t为端盖的壁厚;K为系数(一般取值为0.5-1);P为端盖所承受的最大压力;h为端盖的高度;b为端盖的宽度;σ为端盖所采用的材料的允许应力。
4.密封件的计算:密封件用于确保管壳式换热器的密封性能。
密封件的计算需要考虑其材料的强度和弹性。
计算公式为:F=P×A其中,F为密封件所承受的最大力;P为密封件所承受的最大压力;A为密封件的面积。
需要注意的是,以上计算公式中的参数需要根据具体的工程情况和设计要求进行确定。
在进行结构计算时,还需要遵循相关的安全规范和标准,确保管壳式换热器的安全性能。
同时,针对不同的应用场景和介质特性,还需要进行其他方面的计算和设计,如换热面积的确定、流体动力学计算等。
管壳式热交换器
2.5.2 流体温度和终温的确定
• 在换热器设计中加热剂或冷却剂出口温度需由设计 者确定。如冷却水进口温度需依当地条件而定,但 出口温度需通过经济权衡作出选择。在缺水地区可 使出口温度高些,这样操作费用低,但使传热平均 温差下降,需传热面积增加使得投资费用提高,反 之亦然。根据经验一般应使∆tm大于10℃为宜, 此外若工业用水作为冷却剂出口温度不宜过高,因 工业用水中所含的盐类(主要CaCO3,MgCO3,CaSO4、 MgSO4等)的溶解度随温度升高而减小,若出口温度 过高,盐类析出,形成垢层使传热过程恶化,因此 一般出口温度不超过45℃。所以应根据水源条件, 水质情况等加以综合考虑后确定。水源严重缺乏地 区可采用空气作为冷却剂,但使传热系数下降。对 于加热剂可按同样原则选择出口温度
一、管、壳程介质的配置 有利于传热、压力损失小。具体如下: 1、流量小、粘度大的流体走壳程较好。 2、温差较大时,K大的流体走壳程。 3、与外界温差大的流体走管程。 4、饱和蒸汽走壳程。 5、含杂质流体走管程。 6、有毒介质走管程。 7、压降小走壳程。 8、高温、高压、腐蚀性强的流体走管程。
2.5.1 流体在换热器中内的流动 空间选择
管程变化对阻力影响
• 对同一换热器,若由单管程改为两管程, 阻力损失剧增为原来的8倍,而强制对流 传热、湍流条件下的表面传热系数只增 为原来的1.74倍;若由单管程改为四管程, 阻力损失增为原来的64倍,而表面传热 系数只增为原来的3倍。由此可见,在选 择换热器管程数目时,应该兼顾传热与 流体压降两方面的得失。
– 见公式2.21
2.3 管壳式换热器的传热计算
• • • • • 一、热力设计任务 1.合理的参数选择及结构设计 2.传热计算和压降计算 热力设计:设计计算,校核计算。 设计计算:已知传热量Q,换热工质工作 参数(进、出口温度),求F和结构形式。 • 校核计算:已知换热器的具体结构、某 些参数来核定另一参数。
管壳式热交换器(PPT课件)
管外纵流条件下,管外传热系数为光管的1.6倍.
传递热量相同,泵功率相同,取代光管,节约材 料30%-50%
螺旋槽
主要用于强化管内气体或液体的传热,强化管内液
体的沸腾或管内外蒸气的冷凝,管内传热系数为光管 传热系数的1.5-2.0倍;管外传热系数为光管传热系数 的1.5倍.
缩放管
波纹管
波纹管优点
(4)填料函式换热器
填料函式换热器 1.纵向隔板;2.浮动管板;3.活套法兰;4.部分剪切环;5.填 料压盖;6.填料;7.填料函
填料函式密封
缺点:填料处易泄漏。 优点:结构简单,加工制造方便,造价低,管内和管
间清洗方便 适用场合:4MPa 以下,且不适用于易挥发、易燃、易 爆、有毒及贵重介质,使用温度受填料的物性限制。
带膨胀节的固定管板式换热器 图7-3 带补偿器的固定管板式换热器
(2) U形管式换热器
U形管式换热器 1.中间挡板;2.U形换热管;3.排气口;4.防冲板;5.分程隔板
U形管式换热器
U型管式换热器 图7-6 U形管式换热器 优点:结构简单,价格便宜,承受能力强,不会产生热应力。 缺点:布板少,管板利用率低,管子坏时不易更换。 适用场合:特别适用于管内走清洁而不易结垢的高温、高压、 腐蚀性大的物料。
第二章 管壳式热交换器
间壁式热交换器
管式热交换器
管壳式、套管式、螺旋管式等
板式热交换器
延伸表面热交换器
蓄热式热交换器
管壳式换热器
2.1 管壳式换热器的分类
基本类型 固定管板式换热器
U形管式换热器 浮头式换热器 填料函式换热器
(1)固定管板式换热器
管壳式换热器
弓形折流板的排列
弓形折流板尺寸:缺口大小(高度h)和板间距B
管壳式换热器的类型、标准与结构
缺口大小:按切去弓形弦高占壳体内径百分比(h/Di)来确定
单相换热:h/Di=(20-25)% 壳程蒸发:h/Di=45% 壳程冷凝:h/Di=(25-45)%。
等边三角形法
同心圆法
正方形法
管壳式换热器的类型、标准与结构
等边三角形排列:传热性能好,但流动阻力大; 同心圆排列:紧凑,布管均匀,但制造和装配比较困难;
正方形排列:清洗方便,流动阻力小,但传热性能差。
组合排列:用于多管程换热器中,每一程都采用等边三角形排列,而 在各程相邻管排间,为便于安装隔板,则采用正方形排列。 转角排列:(1)流体流动方向与三角形一边平行的转角等边三角形排 列;(2)流体的流动方向与正方形一条对角线垂直的转角正方形排列
管壳式换热器
管壳式换热器的类型、标准与结构
1) 固定管板式换热器
结构:将管子两端固定在位于壳体两端的固定管板上,管板与 壳体固定在一起。
特点:
(1)结构比较简单、重量轻,成本低,在壳程程数相同的条件 下可排的管数多; (2)壳程不能检修和清洗,因此,宜于不易结垢和清洁的流体 换热; (3)当管束与壳体的温差太大而产生不同的热膨胀时,常会使 管子与管板的接口脱开,从而发生流体的泄漏。
安装:焊接在管箱上,在管板上设分程隔板槽,槽的宽度、深度
及拐角处的倒角等均有具体规定。
管壳式换热器的类型、标准与结构
常见管板分程布置
管壳式换热器的类型、标准与结构
折流板和支持板
作用:(1)使流体横掠管束,增大传热系数;(2)支撑管束;
管壳式换热器的工作原理及结构
管壳式换热器的工作原理及结构(山东华昱压力容器有限公司,济南250305)随着今天快速发展的科技,换热器已广泛运用于我国各个生产区域,换热器跟人们生活一脉相连。
用来热交换的机械设备就是所谓的换热器。
本文综述了管壳式换热器的工作原理及结构。
标签:管壳式换热器;工作原理;结构1 管壳式换热器的工作原理属于间壁式换热器的就是管壳式换热器,其换热管内组成的流体通道称为管程,换热管外组成的流体通道称为壳程。
管程以及壳程分别经过2个不一样温度的流体时,温度相对高的流体经过换热管壁把热量传递给温度相对低的流体,温度相对高的流体被冷却,温度相对低的流体被加热,进而完成两流体换热工艺的目标。
(工作原理和结构见图1)管壳式换热器关键由管箱、管板、管子、壳体以及折流板等组成。
一般圆筒形为壳体;直管或U形管为管子。
为把换热器的传热效能提高,也能使用螺纹管、翅片管等。
管子的安排有等边三角形、正方形、正方形斜转45°以及同心圆形等几种方式,最为常见的是前面三种。
依照三角形部署时,在一样直径的壳体内能排列相对多的管子,以把传热面积增加,但管间很难用机械办法清洗,也相对大的流体阻力。
在管束中横向部署一些折流板,引导壳程流体几次改变流动目标,管子有效地冲刷,以把传热效能提高,同时对管子起支承作用。
弓形、圆形以及矩形等是折流板的形状。
为把壳程以及管程流体的流通截面减小、流速加快,以把传热效能提高,能在管箱以及壳体内纵向安排分程隔板,把壳程分为二程以及把管程分为二程、四程、六程以及八程等。
管壳式换热器的传热系数,水换热在水时为1400~2850瓦每平方米每摄氏度〔W/(m(℃)〕;气体用水冷却时,为10~280W/(m(℃);水蒸汽用水冷凝时,为570~4000W/(m(℃)。
2 管壳式换热器依据结构特征能分为下面2类2.1 刚性构造的管壳式换热器:固定管板式是这种换热器的另一个名称,一般能可分为单管程以及多管程2种。
在两块管板上换热器的管端以焊接、胀接、胀焊并用的办法固定,而管板则以焊接的办法以及壳体相连。
- 1、下载文档前请自行甄别文档内容的完整性,平台不提供额外的编辑、内容补充、找答案等附加服务。
- 2、"仅部分预览"的文档,不可在线预览部分如存在完整性等问题,可反馈申请退款(可完整预览的文档不适用该条件!)。
- 3、如文档侵犯您的权益,请联系客服反馈,我们会尽快为您处理(人工客服工作时间:9:00-18:30)。
整圆型折流板
即能支撑管子,又能让流体流过管孔,流体从间隙 流过时,产生射流,形成湍流,强化壳程传热同时 对管子有冲刷和自清洁作用,从而消除管子结垢和 垢下腐蚀。
折流杆
图1 折流杆的结构形式
折流杆式支承结构
管壳式换热器中代替折流板的折流杆式支 承结构
(1)使换热器壳程流体的流动方向主要呈 轴向流动,消除了弓形折流板造成的传热 死区。
4、分程隔板 优点:
1、改善长管结构 2、提高流速,增强对流换热 缺点:
1、结构复杂,工作稳定性差 2、阻力增大 3、隔板占去位置,减少换热管布置 4、隔板位置在壳程会形成短路空间,不利于 流体充分换热
5、流体穿过隔板垫片短路的机会增多
4、分程隔板
管壳式热交换器结构
纵向隔板 作用:壳程分程 设置要求:在U形管壳式热交换器中常用,一般 不超过两块 优点:增强湍流流动,提高流速,强化传热 缺点:1、结构复杂,安装难度大 2、阻力增大 3、容易泄漏 4、隔板两侧存在热泄漏
(2)由于壳程介质为轴向流动,没有弓形 折流板那么多转向和缺口处的节流效应, 因而流动阻力比较小,一般为传统弓形折 流板的50%以下,达到了节能的效果。
(3)结垢速率变慢,延长了操作周期。
(4)消除了弓形折流板造成的局部腐蚀和磨 损(或切割)破坏,改善了换热管的支承情 况和介质的流动状态,消除或减少了因换热 管的振动而引起的管子破坏,延长了换热器 的使用寿命。
立式热交换器取4~6。
2.1 管壳式热交换器的结构
2、管子在管板上的固定与排列
管子外形: 尽量采用光管。特殊管形在强化换热等特殊场合才
有应用。 管子直径:
尽量采用标准管径,在结构和经济性方面均有 好处; 管子长度:
尽量采用标准管长或将其等分。 管子材料:
应根据工作压力、温度和介质腐蚀条件确定, 可选用碳钢、不锈钢、铜、塑料和石墨等。
弓形折流板 1、布置: 上下方向交替排列
气相或液相清洁物料时适用 左右方向交替排列
气、液共存或流体中带有固体物料时适用
管壳式热交换器结构
弓形折流板 2、结构设计:
间距:间距过小,阻力过大;间距过大, 不能充分横掠,换热效果差,具体见P50表 2.5 缺口高度:弦高取壳体内径20~45%,一 般取25% 厚度:一般较管壁厚一倍,最薄约3mm, 见P50表2.6.
2.1 管壳式热交换器的结构
1、壳体
壳体型式在传热计算之前确定,是管子、管板设计 的基础
设计要求:满足强度、刚度、稳定性、耐久性、 节约材料等要求,制造、安装、运输、 维修力求方便
设计方法: 内径按标准选取,无缝钢管159、273、325; 钢板卷制400、500、600、800及以上。 选用合理长径比,一般取4~25,通常选用6~10,
管板厚度受材料强度、介质压力、温度和压差、温 差以及管子和外壳的固定方式和受力状况等因素影 响。如何选取按照国标GB151-99规定执行。
2.1 管壳式热交换器的结构
3、管板
管板与管子用胀接法连接时,管板的最小厚度(不包括腐 蚀裕量)规定,见下表;
当用焊接法连接时,最小厚度要满足结构设计和制造的要 求且不小于12mm.
螺旋折流板
■通常普通的弓形折流 板能造成曲折的流道 系统(Z字形流道), 这样会导致较大的死 角和相对高的返混。
■提出了一种新方案, 即建议采用螺旋状折 流板
■设计原理:将圆截面 的特制板安装在“拟 螺旋折流系统”中, 每块折流板占换热器 壳程中横剖面的四分 之一,其倾角朝向换 热器的轴线,即与换 热器轴线保持一定倾 斜度。相邻折流板的 周边相接,与外圆处 成连续螺旋状。
2、管子在管板上的固定与排列
管子间距
管板上两根管子中心线的距离称为管间距, 其大小主要与管板强度和清洗管子外表所需间隙、 管子固定方式等有关。
间距太小,不能保证焊接质量和胀管强度要 求;钢制管壳式热交换器最小管间距按书中表2.3 所示。
2、管子在管板上的固定与排列 8)布管限定圆 布管限定圆是由于热交换器 管束外缘需要受壳体内径限 制而提出的一个定义,进行 热力计算时需要应用,其数 值根据壳体内径和热交换器 结构型式确定。
管壳式热交换器结构
支持板 没有折流板安装要求时,可以布置一
定数量的支持板来支撑换热管,防止产生 过大挠度。见P50表2.6
管壳式热交换器结构
挡管 设置在分程隔板后面,防止壳程流体流
动短路影响换热效果。
管壳式热交换器结构
旁路挡板 减小管束外环间隙的流动短路,用在浮
头式热交换器中。
管壳式热交换器结构
防冲板和导流筒
设置防冲板和导流筒遵循的条件 (a)非腐蚀性的单相流体,ρυ2>2230kg/(m s2)。 (b)其他流体,包括沸点下的液体, ρυ2>740kg/(m s2)。
有腐蚀或有磨蚀的气体、蒸汽及汽液混合物,应设防冲 板。
当壳程进出口接管距管板较远,流体停滞区过大时, 应设置导流筒,以减小流体停滞区,增加换热管的有效换热 长度。
管壳式热交换器结构
导流筒
作用:(1)流体均匀流入 (2)防止冲刷 (3)减小接管处的死区
课后总结
管壳式热交换器基本部件有哪些,选 用原则和优缺点分析?结构部件有哪 些,设计原则和功能分析?
小直径管?长管?管子排列?
2、管子在管板上的固定与排列 管子在管板上的固定
胀接法: 工作参数较低,使用压力低于4MPa,温度低
于300℃。
焊接法: 高温高压条件下
其它:爆炸胀接、爆炸焊接、液压胀管、粘胀法等
2、管子在管要的强度,而且管子和管板的连 接要坚固和紧密; 2)设备要尽量紧凑,以便减小管板和壳体的直径, 并使管外空间的流通截面减小,提高管外流体的流 速。 3)制造、安装和修理、维护简便。
DL Di 2b1 b2 b
b 当Di 1000mm时,b 3mm;当Di 1000 ~ 2600时,b 4mm b1 Di 600mm时,b1 3mm;Di 600mm时,b1 5mm b2 b2 bn 1.5mm bn Di 700mm时,bn 10mm;Di 700mm时,bn 13mm.
管壳式热交换器结构
弓形折流板 3、安装固定:
配套结构: 拉杆、定距管
拉杆单侧固定, 用螺纹拧入管板, 定距管确定折流 板间距,最后一 块折流板用螺母 固定。
管壳式热交换器结构
弓形折流板 拉杆直径和数量:见P51表2.7,最小直径
10mm,最少数量4根。(计算时要考虑拉 杆所占流通截面面积)
管壳式热交换器结构
折流板 作用:使流体横流过管束,增强换热 支撑管束,防止管束振动和弯曲
设置要求:由于折流板只是限制流动,所 以折流板和壳体间可以存在漏流,因而在 结构布置及安装上较易实现。
管壳式热交换器结构
折流板的形式 弓形折流板(最常用)
盘环形折流板 扇形折流板 管孔形折流板
管壳式热交换器结构
2.1 管壳式热交换器的结构
3、管板
2.1 管壳式热交换器的结构
4、分程隔板
作 用:管程分程 设置要求:
1、每一程管数大致相等,保证流通截面积一致,减少阻力 损失。 2、隔板形状力求简单,密封长度尽量短 3、所采取的程数有1、2、4、6、8、10、12 等七种程数。 4、设计中避免温度交叉现象 5、相邻程间平均壁温不超过28℃.
2、管子在管板上的固定与排列
管子排列 常用排列方式: 1)等边三角形排列(正六角形排列法)法、同心 圆排列法和正方形排列法。
2、管子在管板上的固定与排列
组合排列
在多管程热交换器 中,多可采用组合 排列,由于分程隔 板占据布管空间, 实际布管需要作图 确定;
2、管子在管板上的固定与排列
转角排列法
2、管子在管板上的固定与排列 8)布管限定圆
对于固定管板,U型管 热交换器
DL Di 2b3
b3 固定管板式,U型管式热交换器管束 最外层换热管表面至壳体内壁的最短距离 b3 0.25d且不小于8mm。
2.1 管壳式热交换器的结构
3、管板 作用:布管,分隔不同的换热介质(非传热部件) 管板与壳体的连接分可拆和不可拆两种