焦化(煤化工)行业焦炉煤气七大综合利用节能技术解析
焦炉煤气和转炉煤气综合利用新技术

焦炉煤气和转炉煤气综合利用新技术焦炉煤气和转炉煤气是冶金行业重要的副产品,它们的综合利用对于资源节约和环境保护具有重要意义。
随着科技的发展,焦炉煤气和转炉煤气的综合利用技术也在不断地更新和改进。
本文将就焦炉煤气和转炉煤气的综合利用新技术进行深入探讨。
焦炉煤气是在焦炉生产焦炭的过程中所产生的一种气体副产品,焦炉煤气的主要成分为一氧化碳、氢气和一些杂质气体。
传统的焦炉煤气综合利用方式主要是将其用作燃料进行燃烧,供热或发电。
但是在这个过程中,焦炉煤气中的一些有价值的成分并未得到有效的利用,同时还会产生大量的二氧化碳等环境污染物,造成资源浪费和环境污染。
为了更好地综合利用焦炉煤气和转炉煤气,减少资源浪费和环境污染,科研人员提出了许多创新的综合利用新技术。
下面将结合具体的技术案例进行介绍。
首先是对焦炉煤气的综合利用。
传统的焦炉煤气的利用方式主要为直接燃烧,但这样会导致大量的一氧化碳和二氧化碳的排放,造成资源浪费和环境污染。
近年来,一种被称为焦化负压干馏技术的新技术被引入到焦化行业。
该技术是利用高温微波和高温离子反应炉对焦炉煤气进行分解,将其中的一氧化碳转化为一氧化碳和氢气。
然后再通过一系列的纯净化工步将其纯净化成合成天然气或甲醇等清洁能源。
这种技术不仅可以实现焦炉煤气的高效利用,还可以将一氧化碳转化为有用的化学品,实现资源的最大化利用,并减少有害气体的排放。
除了以上介绍的两种技术外,还有许多其他的技术可以被应用于焦炉煤气和转炉煤气的综合利用中。
比如通过膜分离、化学吸收、化学催化等技术将煤气中的一氧化碳和氢气分离提纯,然后再将其转化为合成天然气、合成液体燃料或化工原料。
这些技术的应用不仅可以实现煤气中有价值成分的高效利用,还可以减少有害气体的排放,同时也可以为我国的清洁能源发展做出重要的贡献。
焦炉煤气和转炉煤气的综合利用技术是燃气领域的重要发展方向,其应用对于资源节约和环保有着重要的意义。
通过不断地研发和创新,相信在不久的将来,我国焦炉煤气和转炉煤气的综合利用技术将会取得更大的突破,为我国的清洁能源发展做出更大的贡献。
焦炉煤气和转炉煤气综合利用新技术

焦炉煤气和转炉煤气综合利用新技术焦炉煤气和转炉煤气是钢铁生产过程中产生的两种重要的工业燃料气体。
传统上,这两种煤气通常被分开利用,直至最近,人们才意识到对这两种煤气进行综合利用可以达到更高的能源利用效率和更低的环境污染。
为了更好地利用这两种煤气,科学家们不断在新技术方面进行研究和创新。
本文将探讨焦炉煤气和转炉煤气综合利用的新技术。
焦炉煤气和转炉煤气的特点和传统利用方式焦炉煤气是在焦化过程中产生的一种气体,主要成分是一氧化碳和氢气。
而转炉煤气则是在转炉冶炼过程中产生的煤气,主要成分是一氧化碳、氢气和二氧化碳。
这两种煤气既有相似之处,又有一定的差异。
传统上,焦炉煤气主要用于焦化炉内燃烧加热焦炭,而转炉煤气则主要用于提供转炉炼钢过程中所需的燃料。
这种分开利用的模式使得煤气的能量利用效率较低,且环境污染较严重。
新技术的应用为了更好地利用焦炉煤气和转炉煤气,科学家们提出了一些新技术。
可以将焦炉煤气和转炉煤气进行混合利用。
通过对两种煤气进行合理的混合比例调节,可以达到更高的能量利用效率。
可以对这两种煤气进行催化裂解和催化氧化转化,产生更多的燃料气体和减少有害的尾气排放。
可以通过先进的膜分离技术和吸附分离技术对这两种煤气进行分离,分别提取出其中的高值产品。
通过这些新技术的应用,可以更充分地利用焦炉煤气和转炉煤气,提高其能量利用效率,减少环境污染。
混合利用技术混合利用技术是对传统的煤气利用方式进行改进的重要技术之一。
通过对焦炉煤气和转炉煤气进行混合利用,可以提高煤气的能量利用效率,从而降低能源成本。
混合利用还可以减少有害气体的排放,对环境保护具有重要的意义。
混合利用技术需要进行煤气成分的精确分析和混合比例的合理确定,同时需要设计合适的燃烧设备和控制系统。
通过对混合利用技术的应用,可以实现对焦炉煤气和转炉煤气的更加高效利用。
催化转化技术膜分离和吸附分离技术综合利用优势综合利用焦炉煤气和转炉煤气的新技术具有众多优势。
焦炉煤气综合利用技术探讨
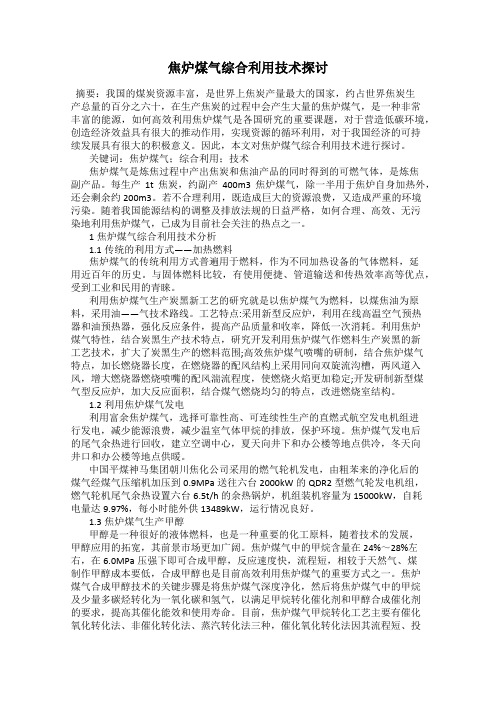
焦炉煤气综合利用技术探讨摘要:我国的煤炭资源丰富,是世界上焦炭产量最大的国家,约占世界焦炭生产总量的百分之六十,在生产焦炭的过程中会产生大量的焦炉煤气,是一种非常丰富的能源,如何高效利用焦炉煤气是各国研究的重要课题,对于营造低碳环境,创造经济效益具有很大的推动作用,实现资源的循环利用,对于我国经济的可持续发展具有很大的积极意义。
因此,本文对焦炉煤气综合利用技术进行探讨。
关键词:焦炉煤气;综合利用;技术焦炉煤气是炼焦过程中产出焦炭和焦油产品的同时得到的可燃气体,是炼焦副产品。
每生产1t焦炭,约副产400m3焦炉煤气,除一半用于焦炉自身加热外,还会剩余约200m3。
若不合理利用,既造成巨大的资源浪费,又造成严重的环境污染。
随着我国能源结构的调整及排放法规的日益严格,如何合理、高效、无污染地利用焦炉煤气,已成为目前社会关注的热点之一。
1焦炉煤气综合利用技术分析1.1传统的利用方式——加热燃料焦炉煤气的传统利用方式普遍用于燃料,作为不同加热设备的气体燃料,延用近百年的历史。
与固体燃料比较,有使用便捷、管道输送和传热效率高等优点,受到工业和民用的青睐。
利用焦炉煤气生产炭黑新工艺的研究就是以焦炉煤气为燃料,以煤焦油为原料,采用油——气技术路线。
工艺特点:采用新型反应炉,利用在线高温空气预热器和油预热器,强化反应条件,提高产品质量和收率,降低一次消耗。
利用焦炉煤气特性,结合炭黑生产技术特点,研究开发利用焦炉煤气作燃料生产炭黑的新工艺技术,扩大了炭黑生产的燃料范围;高效焦炉煤气喷嘴的研制,结合焦炉煤气特点,加长燃烧器长度,在燃烧器的配风结构上采用同向双旋流沟槽,两风道入风,增大燃烧器燃烧喷嘴的配风湍流程度,使燃烧火焰更加稳定;开发研制新型煤气型反应炉,加大反应面积,结合煤气燃烧均匀的特点,改进燃烧室结构。
1.2利用焦炉煤气发电利用富余焦炉煤气,选择可靠性高、可连续性生产的直燃式航空发电机组进行发电,减少能源浪费,减少温室气体甲烷的排放,保护环境。
焦化工序节能技术分析

焦化工序节能技术分析随着生产规模的扩大及工艺的变革,推广应用高压变频节能技术成为焦化工序节能的重要手段,对主要高压电机设备,以及已经应用了液力偶合器调速的电机设备进行变频调速技术改造。
到目前,完成了化产风机等11台〔套〕大型高压电机设备的变频技术改造,总功率为6550kW,在原来使用液力偶合器调速的基础上节电效率进一步提高,节电率达32.75%,年节电量为9.6×106kWh,节电效果显著。
另一方面,在各电气设备安装了无功补偿柜,应用就地补偿技术,实现了自动无功补偿,供电功率因数大大提高,2022年达9.53,2022年1~9月为9.65。
在实施节能技术改造项目的同时,通过工艺、管理优化等手段,不断降低焦化工序能耗。
1焦炉加热优化串级掌握〔OCC〕焦炉加热系统具有典型的大惯性、非线性、时变的冗杂特性。
2022年,从安徽工业高校引进了焦炉加热优化串级掌握〔OCC〕技术并应用于4、5号焦炉,在此基础上,自我开发推广应用到全部焦炉。
优化串级掌握系统对焦炉加热煤气、烟道吸力进行优化自动调整,实现焦炉炉温闭环掌握[6]。
在每个煤气换向周期自动检测一次火道温度,准时发觉炉温的波动准时调整加热煤气用量和相应吸力大小,使炉温能够以0.5h左右的时间间隔周期性地快速得到调整、修正,使煤气使用过量或缺乏的最大可能时间缩短为一个换向周期,与人工每4h测温一次、调整一次相比,大大地提高了炉温的稳定性和调整的准时性,焦炉横排温度和直行温度的匀称性进一步提高,直行温度可掌握在±7℃以内,到达最正确供热效果,可节省加热煤气耗量2%~3%,耗热量降低约90kJ/kg,实现了加热过程的自动、节能、优化的多重效果。
2低标温、低炉顶空间温度炼焦生产焦化工序的能耗构成中,焦炉热耗约占80%以上。
提高焦炉热工效率,是降低耗热量的主要措施,实施低标温炼焦是降低炼焦耗热的最直接手段。
标温降低后,炼焦耗热量降低了150kJ/kg,焦炉各炭化室中上部、及炉顶区的石墨渐渐剥离、脱落,传热系数提高,焦炭成熟状况良好〔见表3〕。
煤化工(焦化厂)焦炉煤气6大脱硫技术详解与脱硫工艺选择
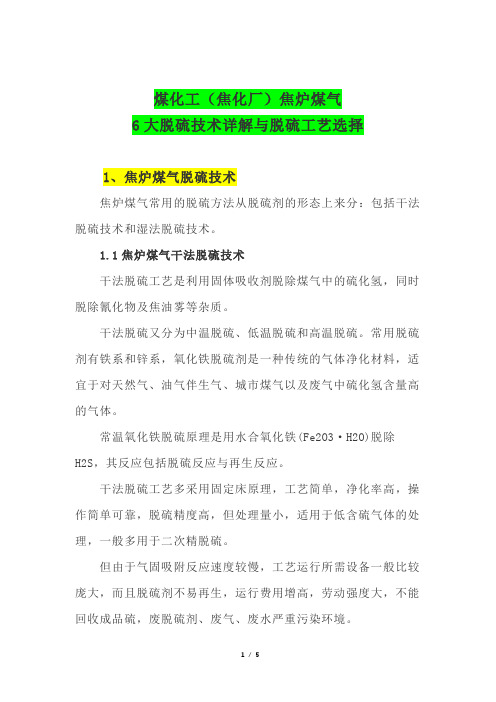
煤化工(焦化厂)焦炉煤气6大脱硫技术详解与脱硫工艺选择1、焦炉煤气脱硫技术焦炉煤气常用的脱硫方法从脱硫剂的形态上来分:包括干法脱硫技术和湿法脱硫技术。
1.1焦炉煤气干法脱硫技术干法脱硫工艺是利用固体吸收剂脱除煤气中的硫化氢,同时脱除氰化物及焦油雾等杂质。
干法脱硫又分为中温脱硫、低温脱硫和高温脱硫。
常用脱硫剂有铁系和锌系,氧化铁脱硫剂是一种传统的气体净化材料,适宜于对天然气、油气伴生气、城市煤气以及废气中硫化氢含量高的气体。
常温氧化铁脱硫原理是用水合氧化铁(Fe2O3·H2O)脱除H2S,其反应包括脱硫反应与再生反应。
干法脱硫工艺多采用固定床原理,工艺简单,净化率高,操作简单可靠,脱硫精度高,但处理量小,适用于低含硫气体的处理,一般多用于二次精脱硫。
但由于气固吸附反应速度较慢,工艺运行所需设备一般比较庞大,而且脱硫剂不易再生,运行费用增高,劳动强度大,不能回收成品硫,废脱硫剂、废气、废水严重污染环境。
1.2焦炉煤气湿法脱硫技术湿法工艺是利用液体脱硫剂脱除煤气中的硫化氢和氰化氢。
常用的方法有氨水法、单乙醇胺法、砷碱法、VASC脱硫法、改良 ADA法、TH 法、苦味酸法、对苯二酚法、HPF 法以及一些新兴的工艺方法等。
1.2.1 氨水法(AS法):氨水法脱硫是利用焦炉煤气中的氨,在脱硫塔顶喷洒氨水溶液(利用洗氨溶液)吸收煤气中 H2S,富含 H2S 和 NH3的液体经脱酸蒸氨后再循环洗氨脱硫。
在脱硫塔内发生的氨水与硫化氢的反应是:H2S+2NH3·H2O →(NH4)2S+2H2O。
AS 循环脱硫工艺为粗脱硫,操作费用低,脱硫效率在 90 %以上,脱硫后煤气中的 H2S 在200~500 mg·m-3。
1.2.2 VASC法:VASC法脱硫过程是洗苯塔后的煤气进入脱硫塔,塔内填充聚丙烯填料,煤气自下而上流经各填料段与碳酸钾溶液逆流接触,再经塔顶捕雾器出塔。
煤气中的大部分 H2S 和 HCN 和部分 CO2被碱液吸收,碱液一般主要是 Na2CO3或 K2CO3溶液。
焦化环保节能措施内容

焦化环保节能措施内容焦化行业是我国重要的能源工业,但同时也是环境污染比较严重的行业之一。
为了保护环境,节约能源资源,焦化企业需要采取一系列措施来推进环保和节能工作。
下面是焦化环保节能措施内容的详细介绍。
一、减少二氧化碳排放焦化企业在生产过程中,二氧化碳排放量比较大,对环境造成了不良影响。
据统计,焦化企业二氧化碳排放量占全国工业二氧化碳排放总量的10%以上。
因此,减少焦化企业二氧化碳排放,成为推进环保的重要途径。
•采用节能技术提高生产效率和产品质量,采用先进的技术改造和设备升级,减少窑炉能耗,从而减少二氧化碳排放。
•优化生产工艺加强优化生产工艺,编制工艺流程图,降低二氧化碳排放,提高生产效率。
•发展清洁能源利用清洁能源替代煤炭资源,如风能、太阳能和水力能源等,降低能耗和二氧化碳排放。
二、降低废水、废气排放焦化生产会产生大量的废水和废气等废弃物,严重影响生态环境。
因此,对于废弃物的处理非常关键,降低废水、废气排放即成为焦化企业推进环保的重点。
•加强废气处理采用高效的废气治理设备,如脱硫、脱硝等,减少氮氧化物、二氧化硫等污染物的排放。
•推进废气资源化利用焦化废气中都含有一定的高值元素,如沥青、苯等,可以通过资源化利用降低环境污染。
焦化企业可以通过新技术新工艺,将废气元素转化为高价值产品,实现废物利用。
•提高污水处理效率灰渣的排放和废水的处理是影响环保的关键因素,采用高效处理设备,如厌氧池、好氧池、生物膜反应器等,过滤出一定的可再生水,达到环保防污的目的。
•收集焦炉煤气焦炉煤气中含有很多有价值的有机物,可以采用化学方法将有机物转化为商业产品而达到资源利用目的。
三、加强环保考核与制度建设环保考核是企业唯一的安全可靠之本。
焦化工业在环保考核中需要遵循严格的尺度,按照环保指标及时上报污染物排放信息、废物处理情况、环保、安全事故等信息。
•完善环保考核制度建立环境管理制度、环保考核等制度,宣传环保政策和法规,提升员工的环保意识和责任心。
焦化生产中大气污染物的控制技术
焦化生产中大气污染物的控制技术焦化是一种重要的工业生产过程,但其排放的大气污染物对环境和人体健康造成了严重的威胁。
因此,焦化生产企业需要采取有效的控制技术来降低大气污染物的排放。
本文将介绍几种常用的焦化大气污染物控制技术。
一、炉内减排技术1. 焦炉煤气净化技术焦炉煤气是焦化过程中产生的重要副产品,但其中含有大量的有害气体和颗粒物。
为了控制大气污染物的排放,焦化企业可以采用焦炉煤气净化技术对煤气进行处理,如湿法洗涤、干法净化等方法,从而达到去除有害气体和颗粒物的效果。
2. 延长焦炉清洗周期焦炉清洗是焦化生产中必不可少的环节,但在清洗过程中会产生大量的粉尘和废水。
因此,焦化企业可以采取措施延长焦炉清洗周期,减少清洗次数,从而降低粉尘和废水的排放。
二、末端减排技术1. 煤气净化末端技术煤气净化末端技术是焦化生产中控制大气污染物排放的重要手段之一。
焦化企业可以采用高效的除尘设备和脱硫设备对煤气进行处理,如电除尘器、布袋除尘器、湿法脱硫等技术,从而达到减少颗粒物和硫化物排放的目的。
2. 焦炉破碎末端技术焦炉破碎是焦化生产中产生粉尘的重要环节。
为了控制粉尘的排放,焦化企业可以采取粉尘抑制剂喷洒、加装高效除尘器等技术措施,从而减少破碎过程中的粉尘排放。
三、设备更新技术1. 采用高效低排放设备焦化企业可以通过更新设备来降低大气污染物的排放。
采用高效低排放设备可以提高生产效率的同时,减少排放的大气污染物的浓度和量。
2. 烟气脱硫技术改造焦化炉的烟气主要含有二氧化硫等有害气体,为了减少烟气中二氧化硫的排放,焦化企业可以进行烟气脱硫技术改造,如采用湿法脱硫技术、石灰石-石膏法脱硫技术等,有效地降低二氧化硫排放量。
总结起来,焦化生产中的大气污染物控制技术包括炉内减排技术、末端减排技术和设备更新技术。
通过采用这些技术,焦化企业可以有效地降低大气污染物的排放,保护环境和人体健康。
然而,为了进一步提高焦化生产的环境性能,还需不断推进技术的创新和应用,以实现绿色、低碳的焦化生产。
焦化厂节能
焦化厂节能技术:焦炉煤气再利用及深加工(可以加工成甲醇、甲酸等)高温余热综合利用发电项目(CDQ)低温烟气余热制冷技术(案例如下)变频改造项目焦化厂低温余热制冷节能技术就焦炉产物带出的热量而言,赤热焦炭的显热最大,荒煤气的显热居第二位,两者合计占焦炉总输出热量的65%~75%。
荒煤气带出显热的回收,对焦化厂节能降耗提高经济性具有非常重要的作用!从炭化室导出的荒煤气排出温度约700℃~800℃,有的甚至高达1000℃,其中含有许多焦油气、苯类蒸气、水蒸气、氨蒸气以及硫化氢等。
在高温下,这些化学产品不能回收,杂质不能除去,一定要降低煤气的温度才能有效地进行煤气精制和回收化学产品。
另外,高温气体体积大,管道直径需要增大,鼓风机的负荷及能量增加。
高温气体在管道内输送是危险的,也不允许进入煤气鼓风机。
因此,为了回收化学产品和净化煤气,为了安全和合理输送煤气,在煤气进入鼓风机之前要进行初步冷却。
通常,高温段降温采用循环氨水通过喷头强烈喷洒进行,当细雾状的氨水与煤气充分接触时,高温煤气放出大量显热,使氨水雾滴迅速升温和汽化,将煤气温度降到80~85℃。
但仍过高,焦油气和水气尚未完全冷凝下来。
为了进一步回收化学产品,便于输送和减少煤气风机的动力消耗,在鼓风机前将煤气通过初冷器进一步冷却。
中温段通常采用冷却塔循环水降温。
末段通常采用制冷机提供16℃冷水再次降温,最终使荒煤气温度降至21℃左右,此时,轻质焦油和氨水就冷凝下来。
然后再进入化产车间,再次对萘、焦油、粗苯等进行分离。
案例包钢焦化厂低温余热制冷系统节能技术改造包钢焦化厂是我国西北地区最大的焦炭生产企业,1958年建厂的老煤化工生产企业,经过多年的快速发展,目前企业焦炭产能达到360万吨。
近几年,该厂致力于打造绿色形象,建设环境友好型企业。
该企业对所有废水都进行无害化处理,并回收利用,实现了清洁生产。
回收利用粗煤气冷却采暖段的废热代替原工艺蒸汽型制冷机提供冷冻水每年可以节省蒸汽8.64万吨/年每年可以节约标煤8962吨/年产生经济效益518.4万元/年1、计算依据由于原系统蒸汽型溴化锂机组已使用十多年,机组制冷效率下降,蒸汽耗量增加。
焦炉煤气净化工艺节能技术探讨
焦炉煤气净化工艺节能技术探讨发布时间:2023-02-02T01:02:53.372Z 来源:《中国科技信息》2022年9月第18期作者:李艳涛金林[导读] 随着社会的快速发展,天然气的总需求量在不断增加李艳涛金林东钢铁集团日照有限公司山东日照 276800摘要:随着社会的快速发展,天然气的总需求量在不断增加,目前国内天然气的产量难以满足社会的需求,需要使用焦炉煤气来有效缓解天然气气荒。
焦炉煤气中含有甲烷乙烯等大量有毒有机物,容易造成环境污染,在焦炉煤气的净化过程中,存在着严重的资源浪费。
为了有效提高焦炉煤气净化中的能源利用,实现焦炉煤气净化,需要经过高温干馏才能把煤气中多余成分去掉,这种方式需要花费大量人力物力。
因此,本文分析了目前焦炉煤气净化工艺节能的现状,并结合实际应用情况。
进一步分析了焦炉煤气净化工艺节能技术。
关键词:焦炉煤气净化工艺;节能技术;探讨;应用引言:焦炉煤气是一种含有多种可燃性气体的高热值煤气,又被成为焦炉气。
在烟煤炼成焦用煤的过程中,会产生焦炭和焦油,还有焦炉煤气,它是炼焦工业中的副产品,主要成分是氢气和甲烷,并含有少量的二氧化碳,一氧化碳,氮气,氧气和其他烃类。
焦炉煤气生产是我国化工生产过程中的重要工艺,传统的焦炉煤气净化已经难以满足焦炉煤气的用量需求,尽管采用方式和措施来不断改进焦炉煤气净化工艺,焦炉煤气的净化效果仍然没有得到改善。
近年来,焦炉煤气的净化效果受到社会的高度重视,企业根据实际情况,大量引入国外先进净化节能技术进行融合应用,并对净化设备和材料进行革新,不仅提升了焦炉煤气的净化效率,还改善了环境污染。
一、焦炉煤气净化工艺节能技术现状焦炉煤气是工业燃气中常见的燃料,是工业企业基本运行的基础,不仅影响工业的经济发展,还会造成环境污染。
由于地质条件差异,导致焦炉煤气的成分含量不同,所以在工业企业使用之前,需要进行净化处理。
焦炉煤气净化的目的是去除其中的有害成分和杂质,避免在使用过程中造成安全事故。
焦炉煤气综合利用
焦化产业由于受钢铁产能削减的影响,已经面临生存考验。
目前,焦化行业已经开始对焦炭下游副产品的深加工进行挖潜,包括化产、苯加氢、焦油加氢以及焦炉煤气综合利用等。
其中,焦炉煤气综合利用方式很多,在此简单做个总结。
1 焦炉煤气甲烷化制取SNG或者LNG焦炉煤气甲烷化技术是近几年才开始实现工业化应用,工艺技术分为高温和中低温两种主流工艺,反应器的形式主流是绝热式,恒温反应器国内有报道。
焦炉煤气甲烷化制取LNG,大约2.55-2.7标方焦炉煤气制取1标方合成天然气,综合能耗1.0-1.1度电。
同时富裕大约20%的氢气。
2 焦炉煤气作为化工原料生产甲醇、合成氨该技术已经完全成熟,工业化应用很广泛,由于甲醇、合成氨市场价格的影响,近期基本不选择这种方式。
现在,已经有该类项目开始着手技改,将焦炉煤气制取甲醇装置改造为“双甲”(甲醇、甲烷)联产装置。
“双甲”工艺有几种争议性方案:a 完全不不改变原甲醇装置设备、工艺路线、运行方式,只是增加煤制气获得碳源,以新增碳源和甲醇驰放气为原料合成天然气。
这种模式的优点是两种产品调节比例大,投资省,技改期间不影响原装置运行。
b 焦炉煤气先提取甲烷、同时停原甲醇装置的转化工序;新增煤制气作为甲醇合成所需的碳源。
这种模式需要对原甲醇装置设备作较大的调整或者更换,建设期间甲醇装置需要停运。
技改的投资预计比前者较大。
3 焦炉煤气综合利用煤焦油馏分加氢制取轻质燃油焦炉煤气提氢,氢气作为煤焦油馏分加氢的原料,剩余气体它用。
4 焦炉煤气综合利用煤焦油馏分加氢制取轻质燃油联产LNG一种适用于焦炉煤气为氢源的煤焦油馏份加氢改质精制联产LNG工艺成功将焦炉煤气综合利用的两种主流产品——煤焦油加氢制取轻质燃油及LNG融为一体。
实现了焦炉煤气资源利用最大化,具有产品结构合理、投资省、运行费用低等优点。
同时,可满足原料焦炉煤气负荷波动下及产品需求变化状况下的自由调节。
本工艺的另外一个优势是煤焦油加氢制取轻质燃油及LNG生产可实现单独独立运行。
- 1、下载文档前请自行甄别文档内容的完整性,平台不提供额外的编辑、内容补充、找答案等附加服务。
- 2、"仅部分预览"的文档,不可在线预览部分如存在完整性等问题,可反馈申请退款(可完整预览的文档不适用该条件!)。
- 3、如文档侵犯您的权益,请联系客服反馈,我们会尽快为您处理(人工客服工作时间:9:00-18:30)。
焦化(煤化工)行业
焦炉煤气七大综合利用节能技术解析
目录
一、总则 (3)
二、焦炉煤气用作气体燃料 (3)
三、利用焦炉煤气发电 (4)
1、蒸汽发电,热电联产供热与发电兼用: (4)
2、焦炉煤气用于燃气轮机发电: (5)
3、燃气——蒸汽联合循环发电技术(CCPP): (5)
4、用煤气内燃机带动发电机发电: (5)
四、利用焦炉煤气制氢 (6)
五、焦炉煤气用于生产直接还原铁 (7)
六、焦炉煤气用于高炉喷吹炼铁 (7)
七、焦炉煤气作为化工原料生产合成气 (8)
1、焦炉煤气制合成氨——尿素 (8)
2、焦炉煤气生产甲醇 (8)
3、焦炉煤气提取或合成天然气 (9)
八、焦炉煤气直接生产合成气 (9)
一、总则
焦炉煤气除部分返回焦炉加热外,剩余主要作为城市煤气,还有相当数量的焦炉煤气会通过火炬燃烧放空。
据估计每年约有350×108m3以上的焦炉煤气未被有效利用而付之一炬,这不仅造成环境污染,还浪费了大量能源。
根据焦炉煤气的特点(含氢量高),我国焦化行业应进一步开发出符合企业特点的应用技术,进而实现煤气资源的优化开发利用,增加焦炉煤气的利用价值,增强炼焦行业的整体竞争力。
焦炉煤气利用程度不断提高,在开发利用技术方面进行了一系列探索,本文总结出七种常用的焦炉煤气综合利用节能技术。
二、焦炉煤气用作气体燃料
焦炉煤气是优质的中热值气体燃料,其热值为17兆焦~19兆焦/标准立方米,煤气的主要成分(体积百分比)为氢55%~60%、甲
烷23%~27%、一氧化碳5%~8%,含两个以上的碳原子的不饱和烃2%~4%,以及少量的二氧化碳、氮、氧等。
由于我国油气资源缺乏,为解决大中城市民用燃气紧张的问题,20世纪80年代焦炉煤气曾一度广泛应用于民用燃气领城。
目前,在天然气还没有通达而焦化行业有一定基础的地区,焦炉煤气仍是民用煤气和其他工业生产的主要气体燃料提供者。
如将焦炉煤气用作陶瓷厂窑炉的加热燃料,生产出优质的陶瓷制品。
此外,焦炉煤气还可用作水泥和玻璃等工业生产的燃料。
三、利用焦炉煤气发电
由于焦炉普遍采用了高效的烟气余热回收技术,约有50%~55%的焦炉煤气富余,我国许多焦化企业将剩余的焦炉煤气用于发电。
焦炉煤气发电有三种方式,分别为蒸汽发电(热电联产)、燃气轮机发电和内燃机发电,目前这几种发电方式在国内均有应用,技术成熟。
如果焦化企业与高电耗生产匹配或与发供电企业联营,且上网电价合适,焦炉煤气用于发电可作为优先选择的技术路之一。
其运行与管理简便,生产作业间长,可采取多种方式,企业收益稳定。
1、蒸汽发电,热电联产供热与发电兼用:
蒸汽发电由锅炉-凝气式气轮机-发电机组成。
该工艺以焦炉
煤气作为热源燃烧锅炉,生成高压蒸汽,用以带动汽轮机、发电机而发电。
蒸汽发电技术过关、成熟可靠。
在我国焦化行业应用较广泛,但其系统复杂、占地面积大、启动时间长。
2、焦炉煤气用于燃气轮机发电:
燃气轮机发电是用焦炉煤气直接燃烧,驱动燃气轮机以带动发电机发电。
燃气轮机发电机组设备紧凑、占地少、效率高、效益好、启动速度快。
不过,燃气轮机运行一段时间后必须远距离运回制造厂检修,因此需要较多的备品,要求工人有较高的技术素质。
3、燃气——蒸汽联合循环发电技术(CCPP):
该技术的基本原理是将剩余的焦炉煤气和回收的高炉煤气经净化、混合、加压后送往燃气轮机燃烧、膨胀做功,带动燃气轮发电机组发电。
同时燃气轮机排放的高温烟气加热余热锅炉,产生蒸汽,带动蒸汽轮发电机组,形成联合循环发电。
燃气——蒸汽联合发电是热能资源的高效梯级综合利用,其发电效率高达45%以上,实现了钢电联产,目前多家钢厂都在使用该技术。
4、用煤气内燃机带动发电机发电:
一些焦化厂采用煤气内燃机发电。
可供选择的焦炉煤气内燃
机发电机组有400千瓦、500千瓦、1200千瓦和2000年瓦。
目前焦化行业大多采用的是500千瓦焦炉煤气内燃机发电机组。
按焦炉煤气热值(低热值)16720千焦/立方米计算,1立方米焦炉煤气可发电1.1千瓦时。
四、利用焦炉煤气制氢
焦炉煤气中的氢含量达55%~60%,是重要的氢资源提供者。
目前,焦炉煤气制氢的主要方法是采用变压吸附技术(PSA)从冷焦炉煤气中分离氢气,该工艺生产的氢气纯度可达99.99%,钢铁企业先后建设了多套100立方米/时至5000立方米/时、纯度为99.999%的焦炉煤气变压吸附制氢装置,其中投产运行时间最长的一套已达20多年。
钢铁企业采用PSA从焦炉煤气中分离氢气,用作轧钢厂保护性气体。
据了解,钢铁行业每年提供约40亿标准立方米氢气供应给燃料电池行业使用,通过改进工艺,未来其供应量将进一步增加。
另外,由于大多数钢厂位于城市中心附近,所以未来城市所需的大部分清洁能源可由钢厂负责供应。
随着氢电池开发、应用成本的降低,利用炼焦煤气提氢将成为焦炉煤气资源化利用的新亮点。
采用炼焦煤气生产氢气将是未来炼焦煤气资源化应用的新途
径。
五、焦炉煤气用于生产直接还原铁
传统的炼铁工业完全依靠碳为还原剂,随着炼焦煤和焦炭资源的日益短缺,业界正在开发资源节约、环境友好的氢冶金,用焦炉煤气直接还原铁是氢冶金重要的应用技术之一。
由于氢的还原潜能是一氧化碳的14倍,大力开发焦炉煤气直接还原铁,可以大大降低炼铁过程对炼焦煤和焦炭的消耗。
直接还原铁生产技术的关键在于还原性气体(70%H2和30%C0)的制备,而焦炉煤气中H2和甲烷含量分别在55%~60%和23%~27%,只需将焦炉煤气中的甲烷进行裂解(重整)即可获得74%的H2和25%的CO,以此作为直接还原生产海锦铁的还原性气体非常廉价。
用焦炉煤气生产直接还原铁的研究以HYL-ZR(自重整)工艺技术为基础,其通过在自身还原段中生成还原气体而实现最佳的还原效率,因此,该工艺无需使用外部重整炉设备或者其他的还原气体生成系统。
采用HYL-ZR(自重整)工艺用焦炉煤气生产直接还原铁的生产成本较低,直接还原铁的金属率可达94%。
六、焦炉煤气用于高炉喷吹炼铁
高炉喷吹含氢介质强化氢还原已成为当今冶炼工艺的热点。
首先,无论从热力学还是从动カ学条件看,高温下氢作为铁
氧化物的还原剂比一氧化碳更具优势;
其次,氢还原的气态产物是水蒸气而不是二氧化碳,故喷吹含氢介质可减少二氧化碳的产生量。
炼焦过程中,煤炭72%~78%生成焦炭,15%~18%生成焦炉煤气。
在炼铁过程中,焦炭的还原当量与焦炉煤气的还原当量之比为1:1,因为H2的还原潜能与CO的还原潜能之比为14:1。
因此,将焦炉煤气通入高炉中同样可以炼铁,相当于提高了炼焦煤资源的利用率,可缓解炼焦煤资源供应紧张的问题。
与天然气相比,焦炉煤气的还原性能更好。
有国家已把高炉喷吹焦炉煤气作为节能减排关键技术进行开发,目前我国也已开始了高炉喷吹焦炉煤气的研究,钢铁联合企业的焦化厂应关注该技术的发展。
七、焦炉煤气作为化工原料生产合成气
近年来随着科技的进步与广大企业的勇于探素,焦炉煤气的应用领域拓展到制化肥、甲醇-二甲醚、提取甲烷制LNG和合成甲烷等。
1、焦炉煤气制合成氨——尿素
有焦化厂率先开发了焦炉煤气热裂解技术用于制纯氢,与空分氮气合成氨,进而生产尿素。
2、焦炉煤气生产甲醇
每生产1吨甲醇可消耗焦炉煤气2000立方米~2200立方米,对富余的炼焦煤气消费非常可观。
以焦炉煤气生产甲醇500万吨计算,就可以消耗焦炉煤气100亿~120亿立方米。
因此,利用焦炉煤气制甲醇、二甲醒、人造汽油等资源化开发利用比作为燃料具有更大的经济和社会效益。
为推进甲醇燃料的应用,先后出台了M15、M85等甲醇汽油标准,已经开始甲醇汽油的车用试点。
3、焦炉煤气提取或合成天然气
在焦炉气组成中,甲烷含量约23%~27%,一氧化碳和二氧化碳含量占近10%,其余为氢和少量氮,因此焦炉气通过甲烷化反应,可以使绝大部分一氧化碳和二氧化碳转化成甲烷,得到主要含氢、甲烷、氮的混合气体,经进一步分离提纯后可以得到甲烷体积在90%以上的合成天然气(SNG),再经压缩得到压缩天然气(CNG)或经液化得到液化天然气(LNG)。
焦炉煤气深度净化后经甲烷化生产天然气(SNG/CNG/LNG)的技术,具有投资小、消耗低、无污染、能量利用率高等优势,是焦化企业较佳的选择。
八、焦炉煤气直接生产合成气
在焦化生产中,从炭化室经上升管逸出的650℃~700℃的荒煤气,在桥管和集气管中被大量喷洒的70℃~75℃循环氨水却
至80℃~85℃,接着又在初冷器中被冷却水冷却到25C~40℃、650℃~700℃的高温荒煤气所带出的显热相当于炼焦过程总热量的32%,这部分能量几乎未被利用而浪费。
为充分利用这部分热量,建立生产两种产品——焦炭和还原性气体的焦化厂,即高温荒煤气从炭化室逸出后不冷却,直接进入热裂解炉、将焦炉煤气中的煤焦油、粗苯、氨、萘等有机物热裂解成以CO和H2为主要成分的合成气体。
这种合成气体可以作为生产合成氨、生产甲醇-二甲醚等的原料气,也可以生产直接还原铁。