金属材料疲劳裂纹扩展速率实验指导书
E647 裂纹扩展速率作业指导书

ASTM E647-08 疲劳裂纹扩展速率试验作业指导书1.概述本测试方法为测定从接近门槛值到最大Kmax期间内非稳定控的疲劳裂纹扩展速率。
结果用裂纹顶端应力强度因子范围(ΔK)来表示。
能够按本方法进行试验的材料不受厚度或强度的限制,只要试验过程中试样厚度足够厚,以防止翘曲及其平面尺寸足以保持弹性变性占优势即可。
本测试方法需对带有预裂纹缺口试样施以循环加荷。
经视觉测量,或是其他等效的方法测量试样的裂纹尺寸,对疲劳循环函数进行数值分析,以建立裂纹扩展速率。
2.仪器2.1夹具和装卡装置--试样对夹具和装卡装置的要求在标准中已概述。
2.2 夹具的同心度-力的传递过程中,保持所有夹具有较高的同心度非常重要。
不对中能导致非对称开裂,特别是靠近门槛值测试,这可能导致无效的数据。
7. 试样形状、尺寸、制备7.1 试样标准---本方法使用的试样形状细节于本方法附录中给出。
从实际材料中取样,应力释放完全是不切实际的。
小心选择试样形状和尺寸,残余应力对于裂纹扩展特性的影响可以最小化。
选择样小比例品尺寸B/W, 可以减少分布于整个试样厚度上,垂直于裂纹扩展方向残余应力的作用。
这种形状的选择,可最大限度的减小由于裂纹弯曲度和裂纹前缘不规则引起的计算da/dN 和∆K的误差。
此外,作用于平行裂纹扩展方向的残余应力可能产生使裂纹尖端闭合或张开的力矩,这也可以混淆的测试结果。
在大多数情况下,残余应力引发了对裂纹扩展特性测量结果影响,可以通过选择一种对称样品形状使其最小化,即M(T)试样。
7.3 切口的制备—对标准试样加工缺口可用电火花、铣削、锯加工。
以下建议的缺口制备过程有利于不同材料疲劳裂纹的扩展。
7.3.1电火花加工---ρ< 0.25 mm(0.0010in) (ρ=缺口根部半径),高强钢(σys≥1175MPa/170ksi)、钛和铝合金。
7.3.2磨和铣----ρ≤0.075mm(0.003in) ,低中强度钢σys≤1175MPa/170ksi ,铝合金。
疲劳裂纹扩展速率

(5—7)
Kt ——理论应力集中系数, Kt >1;
K f ——疲劳缺口系数。
在高周疲劳时,大多数金属都对缺口十分敏
感;但在低周疲劳时,它们却对缺口不太敏感。
强度(或硬度)增加,q f 值增大。
试验证明,缺口形状对值有一定影响。缺口
愈尖锐,q f 值愈低。
5.3 疲劳裂纹扩展速率及疲劳门槛值
一、疲劳裂纹扩展曲线 二、疲劳裂纹扩展速率 三、疲劳裂纹扩展寿命的估算
一、表面状态的影响
二、残余应力及表面强化的影响
三、材料成分及组织的影响
一、表面状态的影响 (一) 应力集中
机件表面的缺口应力集中,往往是引起疲劳破坏的主要原
因。 (二) 表面粗糙度
表面粗糙度愈低,材料的疲 劳极限愈高;表面粗糙度愈高, 疲劳极限愈低。材料强度愈高, 表面粗糙度对疲劳极限的影响 愈显著。
值在2~4之间变化。
(四) 影响疲劳裂纹扩展速率的因素
1、应力比 r(或平均应力 m)的影响
2、过载峰的影响
在恒载裂纹疲劳扩展期内,适当的过载峰会使裂
纹扩展减慢或停滞一段时间,发生裂纹扩展的过载 停滞现象,并延长疲劳寿命。
3、材料组织的影响
一般是晶粒越粗大,其
Kth
越高,
da dN
越低
。
喷丸强化也能提高 Kth 。
三、疲劳宏观断口特征
如图5-3典型疲劳断口具有三个形貌不同的区 域-疲劳源、疲劳区及瞬断区。
疲劳源是疲劳裂纹萌生的策源地。
疲劳区是疲劳裂纹亚稳 扩展所形成的断口区域。
瞬断区是裂纹最后失稳 快速扩展所形成的断口区域。
5.2 疲劳曲线及基本疲劳力学性能
一、疲劳曲线和对称循环疲劳极限 二、疲劳图和不对称循环疲劳极限 三、抗疲劳过载能力 四、疲劳缺口敏感度
材料疲劳裂纹的扩展

第六章 疲劳裂纹扩展的阻滞和瞬态过程 6.1 疲劳裂纹的闭合效应
6.1.1 塑性诱发裂纹闭合
第六章 疲劳裂纹扩展的阻滞和瞬态过程 6.1 疲劳裂纹的闭合效应
6.1.1 塑性诱发裂纹闭合
右示 意图表示 的典型柔 度曲线对 多种合金 都是适用 的。
第五节 疲劳裂纹的扩展
5.8 I—II复合型疲劳裂纹的扩展 之前所讨论的是延性固体的I型疲劳裂纹扩展 问题,现在开始研究复合型裂纹扩展。
第五节 疲劳裂纹的扩展 5.8 I—II复合型疲劳裂纹的扩展
5.8.1 复合型疲劳断裂图
高桦等人(1985)研究了 几种铁合金和有色金属疲 劳裂纹的扩展,他们用两 种不同几何形状的试样进 行双轴加载,一种是单边 缺口试样受非对称的四点 弯曲循环加载,另一种是 含倾斜中心裂纹板试样承 受双轴拉伸。
第六章 疲劳裂纹扩展的阻滞和瞬态过程
6.1 疲劳裂纹的闭合效应 还有其它的解释导致疲劳裂纹闭合的理论: (ⅰ)在疲劳裂纹内部形成的腐蚀层(氧化物诱 发的裂纹闭合);
(ⅱ)疲劳断裂面的显微粗糙(裂纹面粗糙诱发 的裂纹闭合);
(ⅲ)渗入裂纹内的粘性流体(粘性流体诱发的 裂纹闭合); (ⅳ)应力或应变诱发的裂纹顶端相变(相变诱 发的裂纹闭合)。
5.7.3 钝化扩展机制(第Ⅰ阶段)
第5节 疲劳裂纹的扩展
5.7 疲劳裂纹扩展的物理模型
5.7.5 钝化扩展机制(第Ⅱ阶段)
第5节 疲劳裂纹的扩展
5.7 疲劳裂纹扩展的物理模型
5.7.6 钝化扩展机制
( a ) 裂纹钝化扩展模型;( b ) 铜单晶疲劳裂纹扩展实例
第五节 疲劳裂纹的扩展
5.8 I—II复合型疲劳裂纹的扩展
通过III型疲劳裂纹扩展的研究, 发现了延性固体材料裂纹扩展具有 下列基本特征: 在高幅循环扭转作用下, 发生纯扭转裂纹扩展(径向), 它导致平面断口形貌,如 图(b)所示;
金属材料疲劳裂纹扩展速率试验方法

金属材料疲劳裂纹扩展速率试验方法疲劳裂纹扩展速率试验是评估金属材料疲劳断裂性能的重要手段之一。
其主要目的是通过测定金属材料在一定应力或应变下裂纹扩展速率,推断材料的疲劳断裂特性。
本文将详细介绍金属材料疲劳裂纹扩展速率试验方法。
一、实验基本原理金属材料在疲劳加载下会发生裂纹扩展,其速率是随时间变化的。
实验的基本原理是通过测量裂纹长度的变化,得出裂纹扩展速率,并通过相关的公式计算出疲劳寿命。
在实验过程中,通过施加交变载荷对试样进行疲劳加载,使其发生裂纹扩展现象。
然后使用裂纹测距仪或其他测量工具来测量裂纹长度的变化,并记录下应力或应变的变化情况。
最后,通过计算得出裂纹扩展速率以及疲劳寿命。
二、实验步骤1、试样制备试样的制备必须符合国际或国家标准,包括试样形状、尺寸、加工方法等。
试样的表面必须处理成光洁、平整,以消除位错、原子间缺陷等对裂纹扩展的影响。
2、装置组装实验所需装置包括疲劳试验机、负载传感器、数据采集卡等。
其组装必须符合相关标准和要求,同时需要进行校准以保证实验的准确性。
3、实验参数配置实验参数包括加载频率、载荷幅值、初始裂纹长度等。
这些参数的选择需要根据试样材料、几何形状和实验条件等因素进行设计,并进行相关的调试和验证。
4、试样安装试样应固定在试验机上,确保其稳定、平衡和正确位置,以减少偏差和错误的影响。
同时应注意试样的安装方式必须符合标准,并严格遵守相关操作规程和安全操作要求。
5、实验数据采集实验数据采集包括载荷、位移、裂纹长度等多个参数。
这些参数应该在试验过程中全面、准确地进行采集和记录,并及时保存和处理。
6、数据分析和处理实验数据需要进行分析和处理,包括计算裂纹扩展速率、绘制裂纹扩展曲线、计算疲劳寿命等。
同时需要进行数据的统计和分析,以验证实验结果的可靠性和准确性。
三、实验注意事项1、实验人员必须严格遵守安全操作规范,保证安全操作。
2、试样的制备和安装必须符合标准和规范,以消除偏差、误差等影响。
金属材料疲劳裂纹扩展研究综述

内容摘要
海洋钢结构在海洋环境中承受着复杂的力学环境和疲劳载荷。疲劳裂纹扩展 是导致其结构破坏的主要原因之一,因此,对海洋钢结构的疲劳裂纹扩展进行准 确预报具有重要意义。本次演示主要探讨一种单一扩展率曲线模型在海洋钢结构 疲劳裂纹扩展预报中的应用。
一、单一扩展率曲线模型
一、单一扩展率曲线模型
单一扩展率曲线模型是一种基于应力强度因子和应力循环次数的关系来预测 裂纹扩展的方法。它假定裂纹扩展速率仅与应力强度因子幅值和应力循环次数有 关,而与应力的其它参数如平均应力、应力比等无关。这种模型的优点是能够用 一条曲线来描述裂纹扩展的全过程,简洁直观。
4、金属材料疲劳裂纹扩展的应用领域和未来研究方向
未来研究方向主要包括以下几个方面:首先是深入研究金属材料疲劳裂纹扩 展的机理和影响因素,以进一步揭示其本质和规律;其次是发展更加准确、高效 的研究方法和技术手段,以更好地模拟和分析材料的疲劳裂纹扩展行为;第三是 加强针对不同约束条件下的裂纹扩展模型和实验方法的研究,以更好地应用于实 际工程中;最后是拓展金属材料疲劳裂纹扩展的应用领域,如智能材料、生物医 用材料等领域,以发挥其更加广泛的作用。
在几何约束条件下,裂纹扩展模型主要考虑材料的几何特征、裂纹形状和扩 展方向等因素。在物理约束条件下,需要考虑材料的物理性质、力学性能和化学 成分等因素对裂纹扩展的影响。在工程约束条件下,需要考虑实际工程中材料的 服役条件、载荷形式和工作环境等因素对裂纹扩展的影响。
3、基于不同约束条件下的裂纹扩展模型和实验方法
主体部分
1、金属材料疲劳裂纹扩展的机 理和影响因素
1、金属材料疲劳裂纹扩展的机理和影响因素
金属材料疲劳裂纹扩展的机理主要包括应力腐蚀、疲劳裂纹扩展和断裂力学 等。应力腐蚀主要指在应力和腐蚀介质共同作用下,材料内部产生微裂纹并逐渐 扩展的现象。疲劳裂纹扩展则是在循环载荷作用下,材料内部初始裂纹发生疲劳 扩展的过程。断裂力学则是从材料的力学性能出发,研究裂纹扩展的规律和预测 材料的断裂行为。
金属材料疲劳裂纹扩展曲线的拟合方法研究
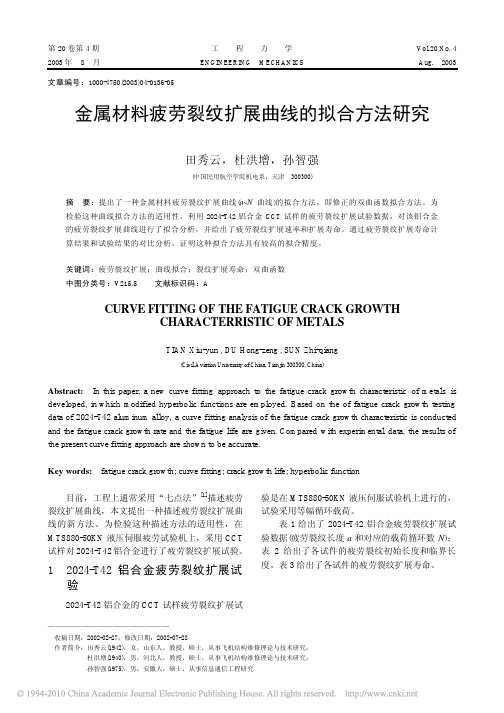
Abstract: In this paper, a new curve fitting approach to the fatigue crack growth characteristic of metals is developed, in which modified hyperbolic functions are employed. Based on the of fatigue crack growth testing data of 2024-T42 aluminum alloy, a curve fitting analysis of the fatigue crack growth characteristic is conducted and the fatigue crack growth rate and the fatigue life are given. Compared with experimental data, the results of the present curve fitting approach are shown to be accurate. Key words: fatigue crack growth; curve fitting; crack growth life; hyperbolic function 目前,工程上通常采用“七点法”[1]描述疲劳 裂纹扩展曲线,本文提出一种描述疲劳裂纹扩展曲 线的新方法。为检验这种描述方法的适用性,在 MTS880-50KN 液压伺服疲劳试验机上,采用 CCT 试样对 2024-T42 铝合金进行了疲劳裂纹扩展试验。 验是在 MTS880-50KN 液压伺服试验机上进行的, 试验采用等幅循环载荷。 表 1 给出了 2024-T42 铝合金疲劳裂纹扩展试 验数据(疲劳裂纹长度 a 和对应的载荷循环数 N); 表 2 给出了各试件的疲劳裂纹初始长度和临界长 度。表 3 给出了各试件的疲劳裂纹扩展寿命。
金属材料疲劳裂纹扩展速率实验
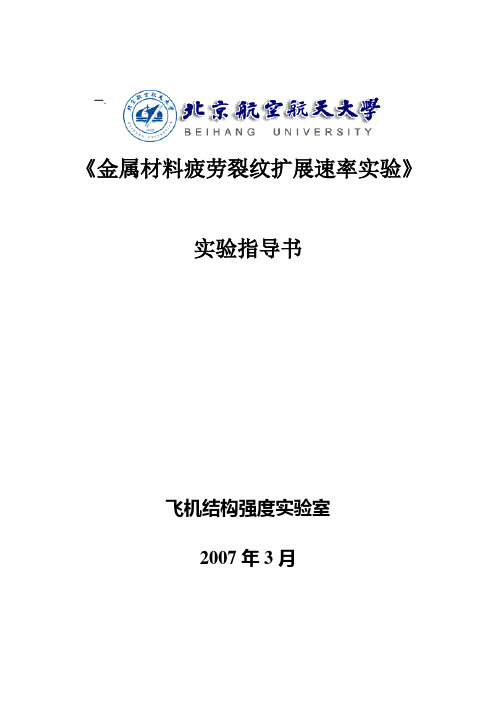
一.《金属材料疲劳裂纹扩展速率实验》实验指导书飞机结构强度实验室2007年3月金属材料疲劳裂纹扩展速率实验1 试验目的1.了解疲劳裂纹扩展试验的基本原理2.掌握金属材料疲劳裂纹扩展速率试验测定方法 3.掌握疲劳裂纹扩展试验测定装置的使用方法 4.掌握疲劳裂纹扩展数据处理方法 2 基本原理结构在交变载荷的作用下,其使用寿命分为裂纹形成寿命和裂纹扩展寿命两部分。
裂纹形成寿命为由微观缺陷发展到宏观可检裂纹所对应的寿命,裂纹扩展寿命则是由宏观可检裂纹扩展到临界裂纹而发生破坏这段区间的寿命,裂纹扩展由断裂力学方法确定。
2.1疲劳裂纹扩展速率裂纹扩展速率dN da ,即交变载荷每循环一次所对应的裂纹扩展量,在疲劳裂纹扩展过程中,dN da 不断变化,每一瞬时的dN da 即为裂纹长度a 随交变载荷循环数N 变化的N a -曲线在该点的斜率。
裂纹扩展速率dN da 受裂纹前缘的交变应力场的控制,主要是裂纹尖端的交变应力强度因子的范围K ∆和交变载荷的应力比R 。
线弹性断裂力学认为,在应力比不变的交变载荷的作用下,dN da 随K ∆的变化关系在双对数坐标系上呈图1所示的形状。
ⅠⅡⅢlog (∆K )∆K c∆K thlog(d a /d N )图1 d d a N K -∆曲线形状K dN da ∆-曲线分成三个阶段:低速扩展段I 、稳定扩展段II 和快速扩展段III ,阶段I 存在的垂直渐进线th K K ∆=∆称为裂纹扩展门槛值,当th K K ∆<∆时裂纹停止扩展,阶段III 存在的垂直渐进线c K K ∆=∆为材料的断裂韧度。
阶段III 对应的裂纹扩展寿命在整个裂纹扩展过程中所占的比例很小,对使用寿命的影响也很小,因此建立描述裂纹扩展速率的公式时主要考虑裂纹扩展的I 、II 阶段。
常用的描述裂纹扩展速率的公式有Paris 公式(式1)、Walker 公式(式2)、Forman公式(式3)、Hartman 公式(式4)、Klesnil 公式(式5)、IAB 公式(式6)等。
ISO 12108-2002 金属材料 疲劳试验疲劳裂纹扩展方法

ISO 12108-2002 金属材料疲劳试验疲劳裂纹扩展方法
(一) ISO 12108-2002
标准英文名称:Metallic materials –Fatigue testing –Fatigue crack growth method 标准中文名称
金属材料疲劳试验疲劳裂纹扩展方法
适用范围
适用于金属材料疲劳裂纹扩展速率和疲劳裂纹扩展门槛值的测定。
应用于材料检验,失效分析,质量控制,选材及新金属材料研发等方面。
试验原理
对预疲劳裂纹缺口试样施加力循环,测量裂纹扩展增量Δa,得到da/dN ΔK 数据点,测定4 / 6疲劳裂纹扩展速率和门槛值。
测定性能参数
疲劳裂纹扩展速率da/dN
疲劳裂纹扩展门槛值ΔKth
试验程序
1)测量试样尺寸;
2)试样预制疲劳裂纹;
3)采用恒力幅增K 试验方法测定疲劳裂纹扩展速率大于10-5mm/cycle 材料的疲劳裂纹长度a 和力循环数N。
采用降K 方法测定疲劳裂纹扩展速率小于10-5mm/cycle 材料的疲劳裂纹长度a 和力循环数N;
4)采用割线方法,或者,对于增K 试验,采用拟合递增多项式a-N 曲线求导方法确定扩展速率。
采用线形回归方法确定扩展速率相应为10-8mm/cycle 时的应力强度因子范围为疲劳裂纹扩展门槛值。
结果及试验报告
国际标准编号;
材料名称、试样标识、取样方向部位;
试样形状和尺寸;
试样力学性能;
力变量(包括力范围,力比值,加力波形和频率);试验环境参数(包括温度,介质,湿度);
数据处理方法;
测定的性能结果。
试验设备:。
- 1、下载文档前请自行甄别文档内容的完整性,平台不提供额外的编辑、内容补充、找答案等附加服务。
- 2、"仅部分预览"的文档,不可在线预览部分如存在完整性等问题,可反馈申请退款(可完整预览的文档不适用该条件!)。
- 3、如文档侵犯您的权益,请联系客服反馈,我们会尽快为您处理(人工客服工作时间:9:00-18:30)。
一.《金属材料疲劳裂纹扩展速率实验》实验指导书飞机结构强度实验室2007年3月金属材料疲劳裂纹扩展速率实验1 试验目的1.了解疲劳裂纹扩展试验的基本原理2.掌握金属材料疲劳裂纹扩展速率试验测定方法 3.掌握疲劳裂纹扩展试验测定装置的使用方法 4.掌握疲劳裂纹扩展数据处理方法 2 基本原理结构在交变载荷的作用下,其使用寿命分为裂纹形成寿命和裂纹扩展寿命两部分。
裂纹形成寿命为由微观缺陷发展到宏观可检裂纹所对应的寿命,裂纹扩展寿命则是由宏观可检裂纹扩展到临界裂纹而发生破坏这段区间的寿命,裂纹扩展由断裂力学方法确定。
2.1疲劳裂纹扩展速率裂纹扩展速率dN da ,即交变载荷每循环一次所对应的裂纹扩展量,在疲劳裂纹扩展过程中,dN da 不断变化,每一瞬时的dN da 即为裂纹长度a 随交变载荷循环数N 变化的N a -曲线在该点的斜率。
裂纹扩展速率dN da 受裂纹前缘的交变应力场的控制,主要是裂纹尖端的交变应力强度因子的范围K ∆和交变载荷的应力比R 。
线弹性断裂力学认为,在应力比不变的交变载荷的作用下,dN da 随K ∆的变化关系在双对数坐标系上呈图1所示的形状。
ⅠⅡⅢlog (∆K )∆K c∆K thlog(d a /d N )图1 d d a N K -∆曲线形状KdN da ∆-曲线分成三个阶段:低速扩展段I 、稳定扩展段II 和快速扩展段III ,阶段I 存在的垂直渐进线th K K ∆=∆称为裂纹扩展门槛值,当th K K ∆<∆时裂纹停止扩展,阶段III 存在的垂直渐进线c K K ∆=∆为材料的断裂韧度。
阶段III 对应的裂纹扩展寿命在整个裂纹扩展过程中所占的比例很小,对使用寿命的影响也很小,因此建立描述裂纹扩展速率的公式时主要考虑裂纹扩展的I 、II 阶段。
常用的描述裂纹扩展速率的公式有Paris 公式(式1)、Walker 公式(式2)、Forman公式(式3)、Hartman 公式(式4)、Klesnil 公式(式5)、IAB 公式(式6)等。
d d ()na N C K =∆(1)()max d d 1nma N C R K ⎡⎤=-⎣⎦(2) ()()d d 1nc a N C K K R K =∆--∆⎡⎤⎣⎦(3) ()d d nth a N C K K =∆-∆(4) ()d d nnth a N C K K =∆-∆(5)()()d d 1nnth c a N C K K K R K =∆-∆--∆⎡⎤⎣⎦(6)Paris 公式由于形式简单,一直得到广泛的应用,它能够较好的描述裂纹扩展的第II 阶段。
Walker 公式也主要用于描述裂纹扩展的第II 阶段,它是Paris 公式的改型,增加了对应力比R 的考虑。
Forman 公式可以更好的描述裂纹扩展的第III 阶段。
Hartman 公式和Klesnil 主要用于描述第I 阶段的裂纹扩展规律。
IAB 公式可以全面的描述裂纹扩展的三个阶段,但公式的复杂性就定了它在工程应用中不多。
2.2 影响疲劳裂纹扩展的因素1.与材料有关的影响因素(1)材料产品的类型。
如板材、挤压件、锻件等。
对于相同的材料,若产品类型不同,则dN da 会有明显的差别。
(2)热处理工艺。
材料成分相同,但热处理工艺不同,会导致材料的微观组织的差别,从而影响材料对裂纹扩展的阻力,造成dN da 的不同。
(3)厚度。
由相同材料制成的构建,厚度不同,则在裂纹尖端附近材料处于不同的应力状态,随着厚度的增加,dN da 呈加大的趋势。
2.与环境有关的因素(1)腐蚀介质。
腐蚀疲劳裂纹扩展包含两部分裂纹扩展机制,应力腐蚀作用下的裂纹长度随时间的扩展速率和交变载荷所引起的疲劳裂纹扩展。
通常腐蚀条件下的裂纹扩展速率会高于惰性气体环境(干燥空气)中的疲劳裂纹扩展速率,并与加载频率和波形有关。
(2)温度。
因为材料的塑性行为与温度有关,在较高的温度下,循环塑性变形易于进行,dN da 将增大。
高温下的疲劳裂纹扩展速率也与加载频率和波形有密切关系。
(3)加载频率和波形。
在惰性环境(干燥气体)和室温条件下,在常用的加载频率内,频率对dN da 的影响不显著。
在惰性环境与室温下载荷波形对dN da 的影响也不明显。
在相同的腐蚀介质和(或)高温条件下,通常频率越低,dN da 越大,且变化比较显著,波形的影响也不可忽略,一次循环中较大在和施加的时间越长,则dN da 越大。
3 试验装置和试样本试验是测定金属材料在试验室空气环境下裂纹稳定扩展阶段的裂纹扩展速率。
3.1 试验装置疲劳裂纹扩展速率试验允许在不同类型的拉压疲劳试验机上进行,但必须满足:1)使试样受载对称分布;2)在静态下校正载荷,其误差不超过%1±,示值变动度不超过1%;在动态下校正载荷,其误差不超过%3±;3)带有准确的计数装置。
CT 试样的加载装置为U 型夹具,其材料的条件屈服强度2.0σ应大于980.72m MN ,销钉与销孔间隙应设计得使摩擦减至最小。
CCT 试样的加载装置应保证在整个试验过程中试样工作区域内应力均匀分布,为限制屈曲,薄板试样必须采用约束导板。
3.2 试样金属材料的疲劳裂纹扩展试验可以采用标准CT (图2)试样或标准CCT (图3)试样。
试样厚度:对于CT 试样而言,推荐厚度范围为420W B W ≤≤(mm W 25≥);对于CCT 试样,推荐试样厚度上限为W ,所必要的最小厚度要能避免屈曲。
试样宽度:为测得有效的试验数据,应根据材料的条件屈服强度2.0σ以及预期的最大应力强度因子的极限值L K max 和CT 试样的W a 或CCT 试样的W a 2极限值选择试样的最小可宽度W 。
试样切口:CT 试样的切口长度n a 应不小于W 2.0。
CCT 试样的切口前缘到中心的距离n a 应不小于中心孔径的3倍,当采用柔度法测量裂纹长度时,建议中心裂纹长度n a 2不小于W 2.0。
试样切口可通过铣切、线切割和其他方法加工而成。
试样不可避免地会存在残余应力,它有可能引起疲劳裂纹扩展速率的变化。
通过选择合适的试样形状和尺寸及合理的试样加工与热处理工艺等,使残余应力对疲劳裂纹扩展速率的影响尽量减小。
疲劳裂纹扩展速率并非总是与试样的几何形状无关,试样厚度的变化对疲劳裂纹扩展速率的影响有可能增大、减小或保持不变,因此,对试样的厚度效应应当引起注意。
2-φ 0.25W+0.05图2 标准CT试样图2-φ W/3图3 mm≤的标准CCT试样图W754 试验过程4.1 试样尺寸测量用精度为0.01mm的量具在试样的韧带区域三点处测量厚度B,取平均值。
用精度不低于0.001W的量具在试样的裂纹所在截面附近测量宽度W。
4.2 预制疲劳裂纹预制疲劳裂纹时应使最大载荷max P 的误差控制在%5±以内,预制疲劳裂纹最后一级的最大载荷不得超过开始记录试验数据时的最大载荷值,须把较高的载荷分级降到试验最大载荷,每级下降率不得大于%20。
为防止试验时的瞬变效应,每一级加载范围应使裂纹长度扩展量不小于()()22.0max 3σπK ',其中maxK '为上一级载荷最后的最大应力强度因子max K 值。
在前后表面上从切口顶端到疲劳裂纹尖端测量裂纹长度(CCT 试样前后表面均要测左右两个裂纹长度),测量应准确到0.1mm 或0.002W 中较大的一个,所测各个裂纹长度均应大于0.1B 和缺口宽度h ,但不得小于2.5mm 。
若前后表面裂纹长度测量值之差超过0.25B 或左右两侧裂纹长度测量值之差超过0.025W ,则试验无效。
4.3 疲劳裂纹扩展试验在试验载荷下记录若干个循环数及其对应的裂纹长度。
试验中应注意:1)应保持在和稳定和避免过载迟滞效应;2)当存在环境影响时,必须考虑载荷水平、频率和波形的影响;3)若长时间中断试验,而中断后的裂纹扩展速率比中断前小,则试验无效;4)试验中任何一点平均穿透疲劳裂纹与试样对称平面的偏离大于5度,此点数据无效;5)在试验中某一点处前后表面裂纹长度测量值相差超过0.025W ,则此点数据无效。
4.4 裂纹长度测量裂纹长度的测量可以采用目测法、柔度法、点位法等,这里采用目测法进行测量。
用目测法或等效的方法测量疲劳裂纹长度时,测量精度应不低于0.1mm 及0.002W 中较大的一个。
测量裂纹长度最好在不中断试验的情况下进行,若需中断试验测量时,应满足:1)中段时间应减至最少;2)为增加裂纹尖端的清晰度,可加静载,其值应小于最大试验载荷。
裂纹增量a ∆的测量间隔应使K dN da ∆-数据点接近均匀分布。
在任何情况下,最小的a ∆应为0.25mm 或10倍于裂纹长度测量的精度,取两者中的较大值。
用目测法测量裂纹长度时,当W B 小于0.15时,只需在一个表面上测量裂纹长度,对CCT 试样要在左右两侧的两裂纹长度,取平均值。
当W B 大于0.15时,则需在前后两个表面上测量裂纹长度,取平均值,对于CCT 试样则需要在前后表面的左右两侧测量四个裂纹长度,取平均值。
5 试验结果处理5.1 裂纹曲率的修正试验结束之后检验断口,以确定裂纹前缘曲率范围,若需要进行曲率修正,且裂纹前缘线条明显,则至少在两个位置(例如预制裂纹和极限裂纹)测量厚度方向()B 41、()B 21、()B 43三点处的裂纹长度,其平均值与试验记录的相应裂纹长度之差即为曲率修正量。
在任何一个位置上,由平均裂纹长度计算出的应力强度因子和由试验裂纹长度计算出的应力强度因子相差大于5%,则需要进行曲率修正。
裂纹曲率修正量不是一个恒量,当它随裂纹伸长而单调增加或减少时,则采用线性内插法修正中间各数据点。
5.2 疲劳裂纹扩展速率的确定由()N a ,数据得到dN da 时,建议采用递推多项式方法进行局部拟合求导,以确定疲劳裂纹扩展速率和裂纹长度的拟合值队任一试验数据点()i 即前后各几点,共()12+n 个连续数据点,采用如下二次多项式进行拟合求导:22122110ˆ⎪⎪⎭⎫⎝⎛-+⎪⎪⎭⎫ ⎝⎛-+=CC N b CC N b b a i i i(7) 式中,1121+≤-≤-C C N i ,()n i n i N N C -++=211,()n i ni N N C -+-=212,ni n i a a a +-≤≤系数0b 、1b 、2b 是在()n i n i a a +-,区间按最小二乘法(即使裂纹长度观测值与拟合值之间的偏差平方和最小)确定的回归参数。
拟合值i aˆ是对应于循环数i N 上的拟合裂纹长度。
参数1C 、2C 是用于变换输入数据,以避免在确定回归参数时的数值计算困难。
在i N 处的裂纹扩展速率由(7)式求导而得:()221211ˆ2C C N b C b dN da i a i-+=⎪⎭⎫⎝⎛ (8)利用对应于i N 的拟合裂纹长度i aˆ计算与dNda 值相对应的K ∆。