电机制造工艺学第二章 定子铁心的制造工艺
定子的生产过程
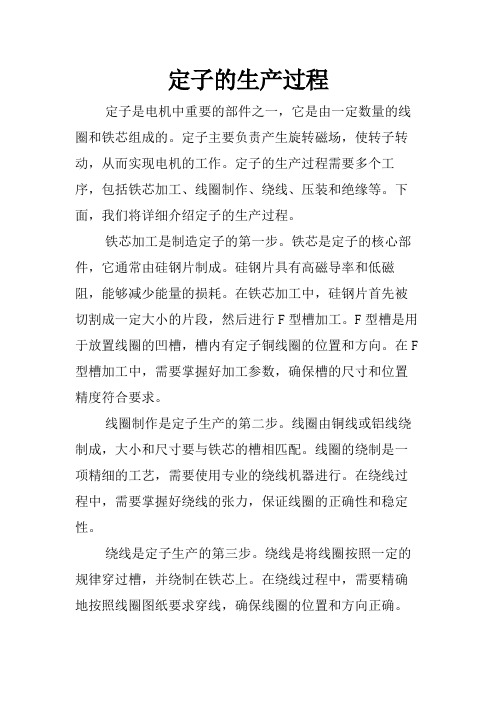
定子的生产过程定子是电机中重要的部件之一,它是由一定数量的线圈和铁芯组成的。
定子主要负责产生旋转磁场,使转子转动,从而实现电机的工作。
定子的生产过程需要多个工序,包括铁芯加工、线圈制作、绕线、压装和绝缘等。
下面,我们将详细介绍定子的生产过程。
铁芯加工是制造定子的第一步。
铁芯是定子的核心部件,它通常由硅钢片制成。
硅钢片具有高磁导率和低磁阻,能够减少能量的损耗。
在铁芯加工中,硅钢片首先被切割成一定大小的片段,然后进行F型槽加工。
F型槽是用于放置线圈的凹槽,槽内有定子铜线圈的位置和方向。
在F 型槽加工中,需要掌握好加工参数,确保槽的尺寸和位置精度符合要求。
线圈制作是定子生产的第二步。
线圈由铜线或铝线绕制成,大小和尺寸要与铁芯的槽相匹配。
线圈的绕制是一项精细的工艺,需要使用专业的绕线机器进行。
在绕线过程中,需要掌握好绕线的张力,保证线圈的正确性和稳定性。
绕线是定子生产的第三步。
绕线是将线圈按照一定的规律穿过槽,并绕制在铁芯上。
在绕线过程中,需要精确地按照线圈图纸要求穿线,确保线圈的位置和方向正确。
同时,在绕线过程中需要保持线的紧张度均匀,避免线圈出现松散或者交叉的情况。
压装是定子生产的第四步。
压装是指将线圈压入铁芯槽中。
在压装过程中需要掌握好压装力度和速度,确保线圈紧密地贴合槽内表面,避免出现空隙或者变形的情况。
同时,还需要保持压装过程的温度和湿度适宜,避免线圈或者铁芯受潮或者变形。
绝缘是定子生产的最后一步。
绝缘是将绝缘材料覆盖在线圈表面,确保线圈与铁芯之间相互隔离,避免出现短路或者漏电的情况。
在绝缘过程中,需要掌握好绝缘材料的质量和厚度,确保其能够承受定子在使用过程中所产生的加热和电压。
到此为止,定子的生产过程已经完成。
在生产过程中,需要考虑到其质量、效率、可靠性和经济性等方面的问题,并采取相应的措施保证其质量。
这些措施包括制定良好的工艺流程和质量控制流程,并引入先进的生产设备和检测手段,以提高生产效率和降低生产成本。
发电机定子工艺流程

发电机定子工艺流程首先,拆分定子元件是将发电机的定子进行拆分,分离出定子铁芯、线圈和其他附属元件。
拆分定子元件时需要非常小心,避免损坏定子的任何部分。
清洗定子元件是将拆分出来的定子元件进行清洗,以去除表面的污垢和油脂。
清洗时可以使用溶剂或者其他适当的清洗剂,轻轻刷洗定子元件的表面,并用清水冲洗干净。
修复定子元件主要是对定子铁芯进行必要的修复和处理。
如果发现定子铁芯有损坏、变形或者其他问题,需要进行修复。
修复的方法可以根据具体情况选择,比如使用热处理、冷压等方法进行修复。
磷化定子元件是将定子铁芯进行磷化处理,以增强铁芯的防腐蚀性能。
磷化处理可以通过热处理、化学处理等方法进行,将定子铁芯表面形成一层磷化膜,提高其耐腐蚀性和耐磨性。
涂覆定子元件是将定子铁芯进行涂覆、绝缘处理。
涂覆通常使用特殊的绝缘漆或胶进行,将定子铁芯表面进行绝缘处理,以避免在使用过程中发生绝缘破损。
装配定子是将定子铁芯和线圈等元件进行装配。
在装配过程中,需要将线圈绕制在定子铁芯上,并进行绝缘处理,确保定子铁芯和线圈的间隙、接触等方面的要求。
动平衡定子是为了保证定子转动时不产生过大的振动,需要进行动平衡处理。
动平衡可以通过在定子上加挂试重物,使定子在旋转时达到平衡状态。
最后,测试定子是将已经装配好的定子进行各项性能测试,包括绝缘电阻测试、电压耐受测试等。
测试的目的是确保定子的各项性能符合设计和使用要求。
综上所述,发电机定子的工艺流程包括拆分定子元件、清洗定子元件、修复定子元件、磷化定子元件、涂覆定子元件、装配定子、动平衡定子、测试定子等几个主要步骤。
通过这些步骤的操作,可以生产出质量可靠、性能稳定的发电机定子。
电机铁芯制作工艺

参考资料:《电机制造工艺学》湖南大学方日杰主编1995年《国外中小型电机制造工艺》 1973《电机制造工艺学》王永昌 1984《电机制造工艺学》胡志强主编.—北京:机械工业出版社,2011铁心是电机的有效部分之一,铁心制造工艺对电机的运行性能影响很大。
铁心制造工艺包括冲片制造和铁心压装两部分。
冲片的冲制属于冲压工艺范肩。
本章先介绍铁心冲片材料的种类及其应用,冲压工艺的一般问题,然后阐述铁心冲片制造、铁心压装、铁心创造质量的检查及其对产品质量的影响等问题。
由于软磁材料的磁导率高、磁滞损耗小和便于制造,因此,铁心一般均用软磁材料制造。
软磁材料的品种有普通碳素结构钢、硅钢片、电工纯铁和导磁合金等。
除直流电机和同步电机的磁极铁心常用普通碳素结构钢板制造外,电机铁心冲片最常用的材料是硅钢片,有些电机中也采用电工纯铁或导磁合金(如铁镍合金、铁锅台金等)。
硅钢片越薄,铁心损耗越小,但冲片的机械强度降低,铁心制造工时增加。
叠装后,由于冲片绝缘厚度所占的比例增加,使铁心的叠压系数降低,导致铁心的有效长度和截面积减小。
所以,在电机制适中不宜采用过薄的电工钢带(片),通常采用的厚度为0.5mm与0.35mm。
冷冲压工艺的特点1、操作简单。
主要依靠冲床和模具进行工作,操作者只做简单的送料工作,对操作者的技术水平要求较低。
2、精度可靠。
工件的尺寸精度主要决定于模具,而与操作者关系极小,因此工件的尺寸稳定,互换性好。
3、生产率高。
冲床工作速度快,冲压过程又便于实现机械化和自动化,生产率很高。
4、材料利用率高。
工件可套裁,冲压件只需经过少量切削,甚至无需切削加工使可直接使用。
5、模具制造周期校长,其制造费用较高。
6、工作噪声大。
冷冲压属于冲击性工作,每进行一次冲压,使发出一个响声。
冲剪车间是噪声公害的重灾区之一。
7、冲剪速度快、压力大,容易发生人身事故。
由于模具制造周期长和制造费用高,当工件数量不多时,采用冷冲压工艺是不经济的。
Y100L-2三相异步电动机定子铁心制造工艺(精)
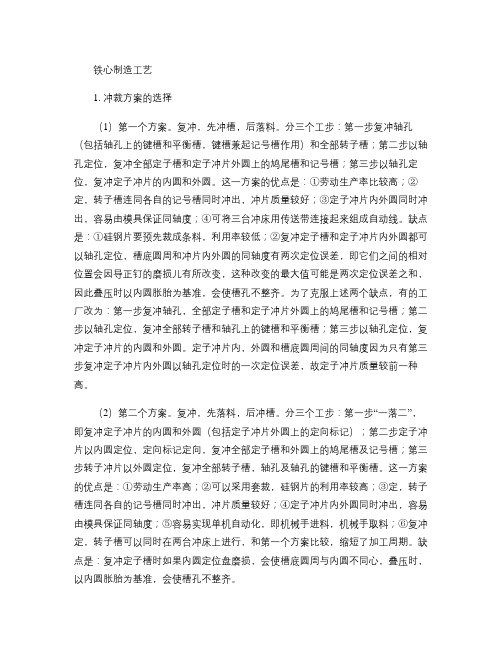
铁心制造工艺1. 冲裁方案的选择(1)第一个方案。
复冲,先冲槽,后落料。
分三个工步:第一步复冲轴孔(包括轴孔上的键槽和平衡槽,键槽兼起记号槽作用)和全部转子槽;第二步以轴孔定位,复冲全部定子槽和定子冲片外圆上的鸠尾槽和记号槽;第三步以轴孔定位,复冲定子冲片的内圆和外圆。
这一方案的优点是:①劳动生产率比较高;②定,转子槽连同各自的记号槽同时冲出,冲片质量较好;③定子冲片内外圆同时冲出,容易由模具保证同轴度;④可将三台冲床用传送带连接起来组成自动线。
缺点是:①硅钢片要预先裁成条料,利用率较低;②复冲定子槽和定子冲片内外圆都可以轴孔定位,槽底圆周和冲片内外圆的同轴度有两次定位误差,即它们之间的相对位置会因导正钉的磨损儿有所改变,这种改变的最大值可能是两次定位误差之和,因此叠压时以内圆胀胎为基准,会使槽孔不整齐。
为了克服上述两个缺点,有的工厂改为:第一步复冲轴孔,全部定子槽和定子冲片外圆上的鸠尾槽和记号槽;第二步以轴孔定位,复冲全部转子槽和轴孔上的键槽和平衡槽;第三步以轴孔定位,复冲定子冲片的内圆和外圆。
定子冲片内,外圆和槽底圆周间的同轴度因为只有第三步复冲定子冲片内外圆以轴孔定位时的一次定位误差,故定子冲片质量较前一种高。
(2)第二个方案。
复冲,先落料,后冲槽。
分三个工步:第一步“一落二”,即复冲定子冲片的内圆和外圆(包括定子冲片外圆上的定向标记);第二步定子冲片以内圆定位,定向标记定向,复冲全部定子槽和外圆上的鸠尾槽及记号槽;第三步转子冲片以外圆定位,复冲全部转子槽,轴孔及轴孔的键槽和平衡槽。
这一方案的优点是:①劳动生产率高;②可以采用套裁,硅钢片的利用率较高;③定,转子槽连同各自的记号槽同时冲出,冲片质量较好;④定子冲片内外圆同时冲出,容易由模具保证同轴度;⑤容易实现单机自动化,即机械手进料,机械手取料;⑥复冲定,转子槽可以同时在两台冲床上进行,和第一个方案比较,缩短了加工周期。
缺点是:复冲定子槽时如果内圆定位盘磨损,会使槽底圆周与内圆不同心,叠压时,以内圆胀胎为基准,会使槽孔不整齐。
定子生产工艺
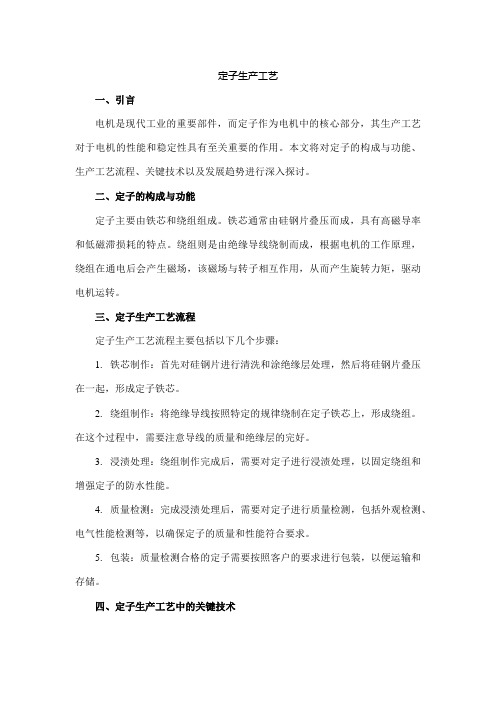
定子生产工艺一、引言电机是现代工业的重要部件,而定子作为电机中的核心部分,其生产工艺对于电机的性能和稳定性具有至关重要的作用。
本文将对定子的构成与功能、生产工艺流程、关键技术以及发展趋势进行深入探讨。
二、定子的构成与功能定子主要由铁芯和绕组组成。
铁芯通常由硅钢片叠压而成,具有高磁导率和低磁滞损耗的特点。
绕组则是由绝缘导线绕制而成,根据电机的工作原理,绕组在通电后会产生磁场,该磁场与转子相互作用,从而产生旋转力矩,驱动电机运转。
三、定子生产工艺流程定子生产工艺流程主要包括以下几个步骤:1.铁芯制作:首先对硅钢片进行清洗和涂绝缘层处理,然后将硅钢片叠压在一起,形成定子铁芯。
2.绕组制作:将绝缘导线按照特定的规律绕制在定子铁芯上,形成绕组。
在这个过程中,需要注意导线的质量和绝缘层的完好。
3.浸渍处理:绕组制作完成后,需要对定子进行浸渍处理,以固定绕组和增强定子的防水性能。
4.质量检测:完成浸渍处理后,需要对定子进行质量检测,包括外观检测、电气性能检测等,以确保定子的质量和性能符合要求。
5.包装:质量检测合格的定子需要按照客户的要求进行包装,以便运输和存储。
四、定子生产工艺中的关键技术1.叠片技术:硅钢片的叠压是定子生产中的关键技术之一。
叠压过程中需要控制压力和温度,以确保硅钢片之间的紧密贴合,同时防止硅钢片发生形变。
此外,硅钢片的涂层技术也是影响定子性能的关键因素之一。
2.绕组制作技术:绕组制作是定子生产中的另一关键技术。
在绕制过程中,需要控制导线的张力、排列和匝数等参数,以确保绕组的电气性能和机械性能符合要求。
此外,绕组绝缘层的完好也是影响定子性能的重要因素之一。
3.浸渍处理技术:浸渍处理是定子生产中的重要环节之一。
通过浸渍处理,可以固定绕组和增强定子的防水性能。
浸渍处理过程中需要控制温度、时间和压力等参数,以确保浸渍效果良好。
4.质量检测技术:质量检测是保证定子性能的重要环节之一。
通过外观检测、电气性能检测等技术手段,可以确保定子的质量和性能符合要求。
定子铁心压铸工艺流程

定子铁心压铸工艺流程As we delve into the process of stator core die casting, it is essential to comprehend the intricate steps involved in manufacturing this crucial component for electric motors. The stator core is a vital part of the motor, providing the necessary magnetic field for the rotation of the rotor. The die casting process is commonly used to create the stator core due to its efficiency and ability to produce complex shapes with high precision.当我们深入了解定子铁心压铸的过程时,了解制造电动机这一关键部件所涉及的复杂步骤至关重要。
定子铁心是电动机的重要组成部分,为转子的旋转提供必要的磁场。
压铸工艺通常用于制造定子铁心,因为它高效且能够以高精度生产复杂形状。
The first step in the stator core die casting process involves the design of the mold that will be used to create the stator core. The mold is typically made of steel and consists of two halves that come together to form the cavity where the molten metal will be poured. The design of the mold is crucial to ensure that the stator core is produced with the desired dimensions and specifications.定子铁心压铸过程的第一步是设计用于制造定子铁心的模具。
电机工艺作业指导书

一、电机一般工艺流程
★特殊工序 ▲关键工序Leabharlann 二、定子制作1、定子铁心的制造
(1)、硅钢片
硅钢片分为热轧硅钢片和冷轧硅钢片。冷轧硅钢片与热轧硅钢片相比有以下优点:当沿着轧制方向交变磁化时,铁损会小得多,导磁性能也有所改善。
含硅量1%~2%钢片称为低硅钢片,磁导率高、韧性好、便于冲剪加工和轧制,常用于中小型电机、电器和变压器。含硅量3%~4%钢片称为高硅钢片,铁损较小、磁导率稍低、较脆、一般用于大型电机和变压器。
硅钢片厚度一般为0.35mm和0.5mm.
(2)、硅钢片的裁剪
(3)、冲片的技术要求
(3)、冲片制造工艺方案
(4)、定子铁心技术要求
(5)、保证铁心紧密度的工艺措施
(6)、保证铁心准确性的工艺措施
2第二章定子铁心的制造工艺
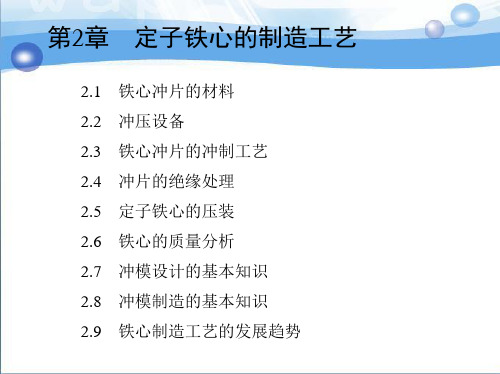
2.冲片加工自动流水线
由三台冲床组成的自动流水线,在我国已普遍 采用。先将整张的硅钢片在剪床(或滚剪机)上 裁成一定宽度的条料,由送料机构自动送入第 一台冲床,复冲轴孔(包括轴孔上的键槽和平衡 槽)和全部转子槽;然后由传料装置送入第二台 冲床,以轴孔定位复冲鸠尾槽、记号槽和全部 定子槽;最后,由送料机构送入大角度后倾安 装的第三台冲床,以轴孔定位,复冲定子冲片 的内圆和外圆。此时,转子冲片由台面孔落在 集料器上,定子冲片落入冲床后面的传送带或 集料器上。
2.3.4 冲片制造工艺方案的分析
1)用定子冲片内外圆一次冲出的模具来保证定 子铁心内外圆同轴度。 2)用复式冲模冲制时,为了保证铁心压装使相 同位置的槽对齐,必须同时冲出定子或转子槽 和各自的记号槽。 3)在半自动冲槽机上单冲定子槽时,可选定子 冲片外圆作基准,如第四方案;也可选轴孔作 基准,如第五方案。
5.尺寸精度
1.材料的利用率
在选择定子冲片外径时,除了满足电机电磁性 能的要求外,还应考虑材料的利用率;应该选 用合理的冲片直径,来提高硅钢片的利用率。
2.冲模的通用性
在考虑各种不同电机定、转子冲片的内径和外 径时,尽可能采用工厂标准直径,这样可以提 高冲模的通用性,减少冲模制造的数量。
3.槽形的选择
1.毛刺 2.同轴度
3.大小齿
4.槽形
1.毛刺
一般用千分尺测量或用样品比较法检查。按技 术条件规定,定子冲片毛刺不大于0.05mm, 复式冲时,个别槽形部分允许最大为0.08mm; 转子冲片毛刺不大于 0.08mm。毛刺大主要是 因为冲模间隙大和模刃变钝。间隙大有两种原 因:一种是冲模制造不符合质量要求,即间隙 没有达到合理尺寸;另一种是冲模在冲床安装 时不恰当,使冲模模刃周围间隙不均匀,这样 间隙大的一边就产生毛刺。
- 1、下载文档前请自行甄别文档内容的完整性,平台不提供额外的编辑、内容补充、找答案等附加服务。
- 2、"仅部分预览"的文档,不可在线预览部分如存在完整性等问题,可反馈申请退款(可完整预览的文档不适用该条件!)。
- 3、如文档侵犯您的权益,请联系客服反馈,我们会尽快为您处理(人工客服工作时间:9:00-18:30)。
图2-15 小型异步电动机定子冲片
2.3.2 冲片的技术要求
1)冲片的外径、内径、轴孔、槽形以及槽底直 径等尺寸,应符合图纸要求。 2)定子冲片毛刺不大于0.05mm。 3)冲片应保证内、外圆和槽底直径同心,不产 生椭圆度。 4)槽形不得歪斜,以保证铁心压装后槽形整齐。 5)冲片冲制后,应平整而无波浪形。
阻率较大、磁滞回线面积较小的薄板材料硅钢
片,经冲制和绝缘处理后叠压而成。硅钢片
的含硅量(质量分数)一般平均超过5%,
见表2-1。
表2-1 电工用硅钢片
2.1.2 热轧硅钢片和冷轧硅钢片
1.热轧硅钢片 热轧硅钢片的电磁性能见表2-2。
表2-2 热轧硅钢片电磁性能
2.冷轧硅钢片
冷轧硅钢片和热轧硅钢片比较,有明显的优点。即
2.复冲
每次冲出几个连续的轮廓线,能一次将轴孔、 轴孔上的键槽和平衡槽以及全部转子槽冲出, 或一次将定子冲片的内圆和外圆冲出。复冲的 优点是:劳动生产率高,冲片质量好。缺点是: 复式冲模制造工艺比较复杂,工时多,成本高, 并要求吨位大的冲床。复冲主要用于大批生产 中。
3.级进冲
将几个单式冲模或复式冲模组合起来,按照同一距 离排列成直线,上模安装在同一个上模座上,下模 安装在同一个下模座上,就构成一副级进式冲模。 图2-17为用级进式冲模冲制定、转子冲片的工步 示意图。
2.2.3 半自动冲槽机
图2-8 冲槽机的自动分度机构
2.2.4 油压机
铁心压装一般在 油压机上完成。 油压机的种类很 多,图2-11所示 是较简单的一种 油压机液压系统 图。通过滚压传 动可使活塞10带 动压板11上下滑 动来完成压装工 作。
图2-11 油压机液压系统图 1—滤油器 2—液压泵 3—溢流阀 4—换向阀 5—背压阀 6—单向阀 7—压力表 8—上横梁 9—液压缸 10—活塞 11—压板 12—工作台
当沿着轧制方向交变磁化时,冷轧硅钢片的铁损小
得多,导磁性能也有所改善。冷轧硅钢片电磁性能
见表2-3。
表2-3 冷轧硅钢片的电磁性能
2.2 冲压设备
2.2.1 剪床 2.2.2 冲床 2.2.3 半自动冲槽机 2.2.4 油压机
2.2.1 剪床
表2-4 电机常用材料的抗剪强度
图2-1 平口剪床
图2-2 斜口剪床
2.2.2 冲床
1.额定吨位 2.闭合高度 3.台面尺寸(长×宽)和台面孔尺寸 4.模柄孔尺寸
图2-6 曲轴冲床
1.额定吨位
冲床铭牌上规定的吨位为冲床的额定吨位。额 定吨位的大小,反映冲床的冲裁能力。在我国, 偏心冲床和曲轴冲床都已成系列生产,公称压 力可分为15个等级,即4t、6.3t、10t、16t、 25t、40t、63t、80t、100t、125t、160t、2 00t、250t、315t、400t。选择冲床时,必须 使冲床的额定吨位大于工件所需要的冲裁力。
2.闭合高度
1)冲模闭合高度。冲模闭合高度是指上、下模 在最低工作位置时的冲模高度(下模座下平面至 上模座上平面的高度)。
图2-7 冲模闭合高度和冲床闭合高度 H′—冲模闭合高度 —冲床最大闭合高度
—冲床最小闭合高度
2)冲床闭合高度。冲床上的连杆可以通过螺纹调 节其长度,调节量为M。冲床闭合高度是指冲 床在M=0时(即连杆全部旋入时)从台面(包括台 面垫板)至下止点时滑块下平面间的距离。
第2章 定子铁心的制造工艺
2.1 铁心冲片的材料 2.2 冲压设备 2.3 铁心冲片的冲制工艺 2.4 冲片的绝缘处理 2.5 定子铁心的压装 2.6 铁心的质量分析 2.7 冲模设计的基本知识
2.1 铁心冲片的材料
2.1.1 硅钢片 2.1.2 热轧硅钢片和冷轧硅钢片
2.1.1 硅钢片
为了减小铁损,交流电机的定子铁心必须用电
图2-12 硅钢片的剪裁
1.规定最小的搭边量C
搭边量太大使利用率降低。搭边量太小,在送 料过程中硅钢片容易被拉断和容易被拉入凹模, 产生毛刺,并降低冲模寿命。还容易使定子冲 片产生缺角现象。 小型异步电动机冲片采用的搭边量C一般为5~ 7mm。
图2-14 混合套裁
2.合理选择定子铁心外径D
在电机设计中,定子铁心外径的选择要结合硅 钢片尺寸(a×b)和最小搭边量C来考虑,以保 证有较高的利用率。
13—底座
2.3 铁心冲片的冲制工艺
2.3.1 硅钢片的剪裁 2.3.2 冲片的技术要求 2.3.3 铁心冲片的冲制方法 2.3.4 冲片制造工艺方案的分析 2.3.5 冲片的质量检查及其分析 2.3.6 冲片的结构工艺性 2.3.7 冲片制造自动化概要
2.3.1 硅钢片的剪裁
1.规定最小的搭边量C 2.合理选择定子铁心外径D 3.实行套裁 4.充分利用余料
Байду номын сангаас
2.3.3 铁心冲片的冲制方法
1.单冲 2.复冲 3.级进冲
图2-16 小型异步电动机转子冲片
1.单冲
每次冲出一个连续的,最多有一个断口的轮廓 线,例如轴孔及键槽、一个定子槽或一个转子 槽。单冲的优点是:单式冲模结构简单,容易 制造,通用性好;生产准备工作简单;要求冲 床的吨位小。它的缺点是:冲制过程是多次进 行的,不可避免地会带来定子冲片内外圆同心 度的误差,以及定子槽和转子槽的分度误差, 因此冲片质量较差,劳动生产率不高。单冲主 要用于单件生产或小批生产中,能减少工装准 备的时间和费用。此外,在缺少大吨位冲床时, 也常常采用单冲。
图2-13 错位套裁
3.实行套裁
为了提高硅钢片的利用率,许多工厂实行 套裁。套裁就是合理安排冲片的位置。通 过减少外部余量来提高硅钢片的利用率。 套裁的方法有错位套裁(见图2-13)和合混 套裁(见图2-14)两种。混合套裁时,由于冲 片的直径不同将增加操作上和生产管理上 的困难,所以用得较少。
4.充分利用余料
表2-5 各种冲床的C值
3.台面尺寸(长×宽)和台面孔尺寸
在冲模设计和安装时,必须考虑台面尺寸和台 面孔尺寸。前者应能保证模具在台面上压紧; 后者应能保证冲孔的余料或工件能从台面孔落 下。
4.模柄孔尺寸
在冲模设计和安装时,必须考虑冲床滑块模柄 孔的尺寸。通常,模柄外径与模柄孔的配合采 用H7/d11。