综述铝电解槽焙烧启动期间影响槽寿命原因与对策
如何延长铝电解槽槽寿命

筑炉 材料 质 量是 很客 观 的 因
,
它 直接 关 系着 电解 槽 的生 产 素 .使 用前 要进 行 严格 检查 .杜
效率 和 成本 .我 国国 内的槽 寿命 绝使 用 劣质 品 例 如 :湖北 某公
平 均仅 1 0 天 左右 .远 远低 于 美 0 7
筑炉 丁艺 的选 取 大体 相仿 .
寿命 。
高的 .而且 异 常槽 A I 在热槽 、 C
压槽 、滚 铝 , 含炭 槽 中 大 量 生
子 比炉 帮 。
焙烧启动制度
电压 的管理 :启动 后根 据铝 水平 和槽温 情 况 .有计 划有 步骤
新 建 或 大 修 电 解 槽 都 必 须 经过 焙烧 启 动 焙 烧 的 主要 F 的 、 j
总 之 .启动 前期 的管理 必须 要 围绕 建立 好 的炉 帮来 展开 ,保
) 块 表 面温 度 高 于9 0 C 减 轻Na 项T 作内容 :1 检查现 场槽盖板 5 可 o
的破坏 作用 。启 动 温度 过低 ,会 及母 线绝 缘情 况 ,监 督 出铝 口保 证正 常 的打 壳下 料 .防 止 出现 氧
周后 降 到40 .6V.随后 根 据 分
子 比和槽温及 A 系数适 当提高部 E 分 电压 .始 终保 持 电解 槽 的热稳
定性。
化.预热槽体使其接近电解温良
如果焙 烧启 动制 度 不合 理 ,会严
电解 槽 日常维 护措 施
电解 槽 日常 维 护 措 施 包 括 5
重 影响 槽 寿命 。启 动时 .槽 底 碳
成.会加重对内衬的侵蚀 。
适 当的分 子 比控制 。分子 比 地 对 电压进 行 调整 .前 期要 快 ,
浅述铝电解槽寿命延长技术的应用与发展

浅述铝电解槽寿命延长技术的应用与发展摘要本文论述了铝电解槽寿命延长技术的应用与发展,为铝电解槽寿命延长技术走可持续发展的道路提供了一定的见解。
关键词铝电解槽;寿命延长技术;应用;发展1 引言我国通过近几年的技术进步电解槽寿命有了很大的提高,诸如某公司160kA、200kA铝电解槽寿命逐年提高。
其目前停槽寿命达到了1,680d左右,而且槽龄超过2,500d的电解槽也有一定的数量。
研究表明,影响铝电解槽寿命有以下5个环节。
其相对重要性比例为:电解槽设计20%筑炉材料10%、筑炉工艺20%、焙烧启动25%、生产管理25%。
我国几乎所有大型铝电解企业都采用焦粒焙烧启动技术。
在电解槽启动后设定合理的技术条件,经过一个稳定期后再使电解槽转入正常生产。
电解槽的稳定生产,不仅能高效低能耗,而且有利于延长电解槽寿命[1]。
2 对铝电解槽寿命延长技术应用的分析与认识2.1 影响电解槽寿命的因素有钠对阴极炭块的渗透、铝液的渗透、电解质的渗透,另外筑炉质量及原材料设计,启动后期管理、电解槽正常生产管理等等,都直接影响着槽寿命。
2.2 铝电解槽的焙烧启动技术对电解槽寿命的影响多年的生产实践证明,电解槽的运行寿命与电解槽的焙烧启动技术的选择有很大关系。
好的焙烧启动技术对延长电解槽的寿命是非常有益的。
现行的预焙电解槽焙烧启动技术大致可分为三种,即:铝液焙烧启动、焦粒焙烧启动和燃料焙烧启动。
2.3 电解槽停槽大修的几种原因图1列出了某公司1988年至2006年各年的槽寿命情况,由表可见电解槽寿命逐年提高,对各年的槽寿命情况进行了分类分析如图1所示。
2.4 电解槽破损原因分析对某公司停槽情况进行分析,造成电解槽破损的主要因素主要有以下几种:①钠渗透膨胀;②热冲击;③冲蚀坑;④冷捣糊的质量和扎固质量,造成脱落或冲刷、磨损、裂缝,使电解质进入阴极底部引起破损;⑤侧部人造伸腿脱落,侧部漏炉等,以上电解槽破损原因作者认为与焙烧启动、生产管理和操作有很大的3 依靠技术进步,以促进铝电解槽寿命延长技术的可持续发展3.1 焙烧和启动(1)焦粒焙烧方法的有效应用电解槽寿命其实就是电解槽内衬的寿命。
延长预焙铝电解槽寿命的技术方案和对策

年停措 的槽 毒帝 情蕊 鹰班攫 蓐 因 谱 鞯 了 长 延 铝电 I I 糖寿审 的黩 拳 方案 . 杀枉 由 了避一 妒延
长槽毒幸l棱 采疆花秘昔董. 的
自
圈■—●—— ●—●■—● ——一
箍 电解 槽 ;槽 寿命 :电 旰l庶 搬 } 拳方 案 糟 撞
面 — l}T T 7 l 『 r l 1. 8
Sevc i s r u in Co dio f de R d c in P t r ie L f Diti to n t n o I l e u to o s m e b i Qig a rn h Si e 2 0 n h iB a c n 00 c
枷 l 0 0 a l 。∞ ∞口 : 】∞ 一5 2 I 『 l m : ∞。
良好 .无发现礁损现象 如O 0—2 3 年停 能 略形成 坚固的 炉帮 ,更为 主要的 是其 (3  ̄ 措几平均 为铝 液焙烧槽 .停槽槽龄较低 。 鞍 高的槽 温减 少钠对 阴投嶷块 的侵 蚀渗 20 0 5年三系列采 用了混 合料焙烧方法 ,是 透 从而减 少朋 授炭块 因钠的 吸收局 部 将煅后 焦、石墨粉按 一定比侧混合作为焙 膨 l而产 生内应 力 ,这 为 电解榷 使嗣寿 j 长
厦 ,有 毹炉 浒i t }
寰块底鄯
扎固 幅
抗取丁丈量电肌 获直层和譬涯层・嘲收费块向上l起一 I 律戒炉毫
垂起并 蛙成 胡撮 嵌辣裂 开 。抟喇椒 有烈 向硪 簟向 I曩 l 撮扎 圈■ 蒋 伸穗 I嚣 I
耐火砖、保薯韩 橹蠹镕#
毋渣 电■晨并己发生化举反彦,变质。 瘫形骶 向 卅凸出.|部l爨, 目 上 I t L 掂。礴刊● 蕾固疆内柑裱
命的 延长起 了关键性 作用 23 2 .3 艺技术条件的优化保持
电解槽寿命管理

相对误差
0.715497 0.689759 0.61827
Dmn 误差
0.208327 0.255606 0.24596
4
5 6 7 8 9 10 11 12 13 14 15 16
1080
1099 1281 1366 1543 1565 1621 1671 1714 2562 2611 2672 3164
17
3317
3136.42
180.5801
0.054441
0.070292
51
国内现有提高预焙铝电解槽寿命的 技术和措施
国内现有提高预焙铝电解槽寿命 的措施是对症下药,也就是根据对现 有槽情况的分析结果,有针对性的采 取措施。目前主要有以下一些:
52
⑴ 改变阴极不合理结构:如增加伸 缩缝,改变侧部“圈樑”结构;加工 面宽度应根据有关情况通过试验而定, 不能照搬外国的数据。
27
② 由于电解质渗透和长期使用,耐火和 保温材料性能改变,槽无法在正常条件下 运行。 槽侧块由于磨蚀和氧化等原因而逐步 损坏,造成测部漏炉。 材料质量和操作条件、设计是其决定因 素。
28
消灭非正常破损、降低早期破损 率、延长正常破损期是提高槽寿 命的关键。
29
五、影响槽寿命的因素
设计—磁、流动、热和应力场的合理化 施工质量和材料
4
槽寿命与吨铝大修费关系 1500
元/吨铝
1000 500 0 0 2 4 6 8 10 槽寿命(年) 系列1 系列2
5
因电流效率降低而增加的费用
吨铝增加费用(元/吨 铝)
300 200 100 0 0 1 2 3 4 5 电流效率降低(%)
6
槽电压上升与费用增加的关系 250
电解槽破损原因及破损槽运行措施
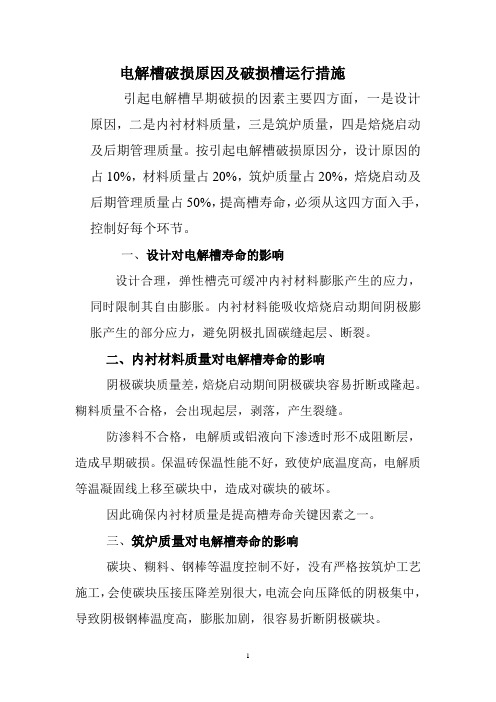
电解槽破损原因及破损槽运行措施引起电解槽早期破损的因素主要四方面,一是设计原因,二是内衬材料质量,三是筑炉质量,四是焙烧启动及后期管理质量。
按引起电解槽破损原因分,设计原因的占10%,材料质量占20%,筑炉质量占20%,焙烧启动及后期管理质量占50%,提高槽寿命,必须从这四方面入手,控制好每个环节。
一、设计对电解槽寿命的影响设计合理,弹性槽壳可缓冲内衬材料膨胀产生的应力,同时限制其自由膨胀。
内衬材料能吸收焙烧启动期间阴极膨胀产生的部分应力,避免阴极扎固碳缝起层、断裂。
二、内衬材料质量对电解槽寿命的影响阴极碳块质量差,焙烧启动期间阴极碳块容易折断或隆起。
糊料质量不合格,会出现起层,剥落,产生裂缝。
防渗料不合格,电解质或铝液向下渗透时形不成阻断层,造成早期破损。
保温砖保温性能不好,致使炉底温度高,电解质等温凝固线上移至碳块中,造成对碳块的破坏。
因此确保内衬材质量是提高槽寿命关键因素之一。
三、筑炉质量对电解槽寿命的影响碳块、糊料、钢棒等温度控制不好,没有严格按筑炉工艺施工,会使碳块压接压降差别很大,电流会向压降低的阴极集中,导致阴极钢棒温度高,膨胀加剧,很容易折断阴极碳块。
筑炉时带入水分过多,人造伸腿扎固质量差,都会在焙烧期间会形成很多的通道,电解质会沿通道向下渗透。
筑炉时内衬材料表面不水平,焙烧启动期间阴极各部分承受应力会不一样,很容易破坏阴极内衬,导致早期破损。
四、焙烧启动质量对槽寿命的影响焙烧期间,阳极电流分布不均会引起阴极表面温度有较大的差距,如果调整不及时,会形成恶性循环,导电多阳极导电越来越多,对应的阴极导电必然多,产生阴极局部温度过高,阴极碳块易产生裂缝,产生铝液通道。
启动期间,如果温度过高,渗透到阴极裂缝中的电解质不会凝固,利用电解质弥补阴极缺陷的可能性减小,导致阴极破损的可能性增加。
五、破损槽的维护措施1、确认破损的位置通过测量阴极电流分布,记录导电多的方钢位置,通过测量阴极钢棒温度,记录温度高于300度的方钢位置,通过测量炉底钢板温度,记录温度高于100度的区域,然后用铁钩检查阴极方钢温度高对应阴极区域、炉底温度高区域。
影响电解槽寿命因素研究
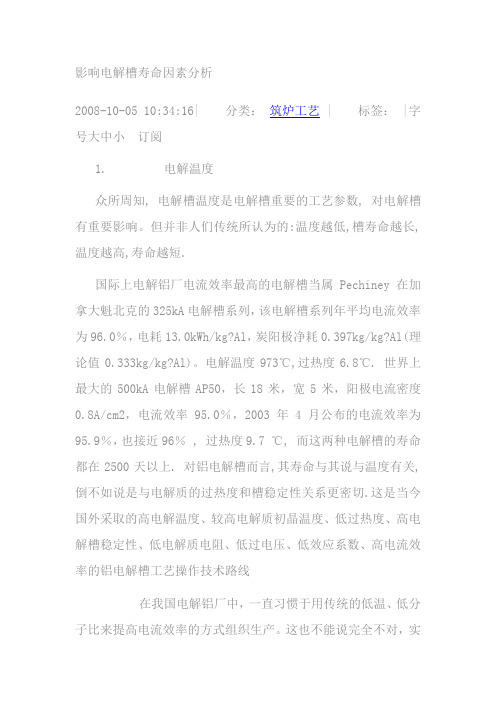
影响电解槽寿命因素分析2008-10-05 10:34:16| 分类:筑炉工艺 | 标签: |字号大中小订阅1. 电解温度众所周知, 电解槽温度是电解槽重要的工艺参数, 对电解槽有重要影响。
但并非人们传统所认为的:温度越低,槽寿命越长, 温度越高,寿命越短.国际上电解铝厂电流效率最高的电解槽当属Pechiney在加拿大魁北克的325kA电解槽系列,该电解槽系列年平均电流效率为96.0%,电耗13.0kWh/kg?Al,炭阳极净耗0.397kg/kg?Al(理论值0.333kg/kg?Al)。
电解温度973℃,过热度6.8℃. 世界上最大的500kA电解槽AP50,长18米,宽5米,阳极电流密度0.8A/cm2,电流效率95.0%,2003年4月公布的电流效率为95.9%,也接近96% , 过热度9.7 ℃, 而这两种电解槽的寿命都在2500天以上. 对铝电解槽而言,其寿命与其说与温度有关,倒不如说是与电解质的过热度和槽稳定性关系更密切.这是当今国外采取的高电解温度、较高电解质初晶温度、低过热度、高电解槽稳定性、低电解质电阻、低过电压、低效应系数、高电流效率的铝电解槽工艺操作技术路线在我国电解铝厂中,一直习惯于用传统的低温、低分子比来提高电流效率的方式组织生产。
这也不能说完全不对,实验研究表明,低温、低电解质分子比确实有降低铝在电解质熔体中的溶解度和溶解速度,减少铝的溶解损失,显著提高电流效率的作用。
但低温、低电解质分子比的负面作用是,电解质成份的稳定性、热稳定性大大降低,由于电解质成份不稳定性增加,容易产生沉淀,而沉淀又不容易溶解,槽帮不结壳,伸腿过长、过大,造成水平电流大,槽电压不稳,铝水摆动大,效应系数多,电解质电阻大,反电动势高等缺点。
而不容易使低温、低分子比操作达到理想的提高电流效率的目的。
此外,由于电解槽的热稳定性降低,电解槽阴极内的电流分布不均,槽内衬应力不均匀,也容易降低电解槽的寿命。
浅谈对大型电解槽破损原因及延长槽寿命问题研究
浅谈对大型电解槽破损原因及延长槽寿命问题研究摘要:众所周知,槽寿命是现代铝电解生产技术高低水平的关键,其对企业的经济效益和社会效益具有直接的影响。
通过调查研究,我们发现,国内的电解槽的使用寿命大多都在1200天左右,个别的铝厂电解槽的使用寿命甚至不足1000天,这在一定程度上,对企业的发展具有明显的阻碍作用。
因此,我们有必要对大型电解槽进行认真的研究和分析,识别电解槽的种类和特征,从而进一步延长电解槽的使用寿命。
鉴于此,本文主要针对大型电解槽破损原因及延长寿命问题进行相关浅析,仅供参考。
关键词:大型电解槽;破损原因;延长;槽寿命;问题研究1、电解槽的破损原因及特征分析1.1 电解槽的破损原因早期电解槽的破损因素包括:设计因素、内衬材料的质量因素、筑炉质量因素、焙烧启动与后期的管理质量因素。
依据电解槽遭到破坏因素实际比例可了解到,设计因素占比10%、内衬材料的质量因素与筑炉质量因素均各自占比20%、焙烧启动与后期的管理质量因素占比50%。
而若想确保槽的使用寿命得以提升,就应当从源头上着手,严控各个节点。
①设计因素注重设计的科学合理性,弹性槽壳对于内衬的材料膨胀所产生应力缓冲作用,对其膨胀予以有效地限制。
内衬材料,可吸收启动焙烧时阴极膨胀所产生部分应力,防止阴极扎固的碳缝出现断裂或起层等问题状况。
②内衬材料的质量因素阴极碳块的质量相对较差,启动焙烧时阴极碳块极易有隆起或折断情况出现。
糊料质量若不达标,则会导致剥落、起层情况出现,甚至会出现裂缝问题;保温砖的保温性能若不佳,则炉底部温度会相对较高,其电解质等相应温凝固线会逐渐上移到碳块上,促使碳块被破坏。
故而,保证内衬材料的质量,属于提升槽实际使用寿命关键点,需得到充分重视。
③筑炉质量因素若钢棒、糊料、碳块等温控不佳,并能严格依据筑炉工艺开展施工操作,则会导致碳块压的接压降差较大,电流会集中于向压降低阴极,促使阴极钢棒的温度过于高,加剧膨胀,极易导致阴极碳块被折断。
(整理)电解槽焦粒焙烧启动中存在的问题及处理措施
电解槽焦粒焙烧启动中存在的问题及处理措施摘要:电解槽投产首先要经过焙烧、启动节段,而焙烧启动质量对电解槽的寿命和经济运行有着深远的影响,因此采用合理的焙烧方法和启动制度十分重要。
本文通过对大型预焙电解槽的焦粒焙烧启动过程中存在的问题以及处理措施作一下分析和论述。
关键词:焦粒焙烧措施高残极槽寿命电解槽的焙烧、启动的成功与否对槽寿命和以后的正常生产有深远的影响,有关资料统计显示,因焙烧启动导致电解槽被迫停槽大修占总停槽数的20—35%左右,因此采用合理的焙烧方法和启动制度十分重要。
电解槽的焙烧方法主要有铝液焙烧法、燃料焙烧法、焦粒焙烧法等三种,当前由于焦粒焙烧相比较具有很大的优点而被国内各大铝厂普遍采用。
本文通过对200KA大型预焙电解槽的焦粒焙烧启动过程中存在的问题以及处理措施作一下具体的论述和分析。
1、改进铺焦粒、座阳极的方法焦粒焙烧进行得是否顺利,在很大程度上取决于焦粒铺的是否薄厚均匀,阳极底掌与焦粒接触是否充分,压实。
有些厂家由于在这一块做的不够,在通电过程中出现轻者阳极导电不均,偏流严重,阴极焙烧质量不均,重者引起多组阳极脱落甚至最终导致焙烧失败。
铺焦粒要求厚度一致,坐极一次到位,而在实际操作中由于导杆的垂直度达不到要求,小盒卡具挂勾间距又小,阳极很难一次坐到位,既便是多次重复,也不易达到阳极底掌与焦粒充分接触,有些阳极底掌与焦粒接触面积还不到50%。
且28块阳极的由于接触程度不一样就会使各极导电量大小不同,在通电过程中就容易出现偏流情况。
为了增加阳极底掌与阴极的接触面积,我厂采用以下方法:焦粒厚度2cm,用水平尺找平,座极时,以不压到人造伸腿为准,尽可能靠近大面外侧,这样,阳极导杆距大母线距离较远,就不容易与大母线接触,阳极靠自重压在焦粒上,阳极底掌完全与焦粒接触,然后再用钢管把阳极撬至紧贴大母线,这样在阳极滑动过程中会使焦粒压得更实,接触更好,提高了座极的质量。
通过这种方法,在通电中阳极电流分布均匀,焙烧电压低、下降快,阴极在焙烧过程中温度升速均匀,能大大提高阴极焙烧质量,对延长电解槽寿命是有益的。
铝电解槽焙烧影响槽寿命的探讨
铝电解槽焙烧影响槽寿命的探讨1预焙铝电解槽焙烧的目的和要求焙烧的目的:排除砌体水分,加热槽体;焦化炭块之间和阴极钢棒周围的糊料;使阴极接近或达到正常作业温度;焙烧期间熔化了的高分子比电解质渗入炉底,起到堵塞裂缝、修补缺陷的作用;加热阳极及装炉物料,使阳极温度达到生产温度,熔化物料,满足启动需要;满足电解槽内炭素材料对碱性物质的大量吸收。
焙烧的要求:均匀缓慢的加热电解槽阴极内衬、阳极以及装炉物料,使三者达到一定的温度条件,以利于下一步的启动操作。
2铝电解槽在焙烧期间产生破损的形式及原因分析2.1阴极炭块断裂或出现裂纹一般来说,阴极炭块断裂是与阴极炭块的长度方向相垂直的横向裂纹,裂纹的深浅不等,最深的地方可使阴极炭块横向断裂。
这种断裂的产生大都是电解槽在焙烧过程中阴极炭块局部电流密度过大、温度过高、热冲击过大所致。
2.2电解槽炉底中缝捣固糊与阴极炭块之间出现大的裂缝电解槽炉底阴极炭块之间主要使用捣固糊填充连接处缝隙。
在焙烧过程中,阴极炭块出现膨胀现象,而捣固糊出现收缩,正是这种收缩起到了吸收阴极炭块膨胀的作用,当焙烧温度不超过1200℃时,这种作用可以很好地体现出来,焙烧结束后,一般阴极炭块和烧成后的捣固糊之间有很小的缝隙或不出现缝隙。
当电流分布严重不均、局部温度超过1200℃时,阴极炭块不再膨胀,而是随着温度的升高而发生收缩,烧成后的捣固糊也是随着温度的升高而收缩,这样,阴极炭块之间的捣固糊不再起到吸收阴极炭块膨胀的作用,而使阴极炭块与捣固糊之间的缝隙越来越大。
2.3阴极炭块与边部捣固糊在焙烧过程中出现缝隙在新建的或大修后的电解槽焙烧过程中,若操作不当,在阴极炭块与边部捣固糊之间也会出现裂缝,其裂缝的生成机理与本文2.2节炉底中缝捣固糊与阴极炭块之间出现裂缝的机理是一样的。
2.4人造伸腿出现横向收缩裂纹与侧部炭块的早期破损槽底部阴极炭块与侧部炭块之间是由较宽较厚的捣固糊填充并捣实,而这捣实的炭素糊为无头无尾的封闭环型体构成的电解槽人造伸腿。
电解槽的焙烧启动和后期管理
电解槽的焙烧启动和后期管理电解槽的预热焙烧与启动是铝电解生产中的两个重要阶段,新建或二次启动的电解槽在进入生产前,要经过焙烧与启动过程。
电解槽的焙烧启动虽然只有短短的几天,但对电解槽启动后的工作状态产生重大影响,尤其是对电解槽的寿命产生决定性的影响,因此必须足够的重视。
一.焙烧所谓焙烧(对于预焙槽而言,又称为预热),就是利用置于铝电解槽阴、阳两极间的发热物质产生热量,使电解槽阳极、阴极(含内衬)的温度升高。
电解槽预热焙烧的目的主要有:1.1 预热阴极。
阴极碳块间边缝和槽周边的扎糊进行烧结焦化,形成密实的碳素槽膛。
1.2 烘干电解槽内衬。
通过一定时间的缓慢加热排除槽体内耐火材料、保温材料等砌体的水分,提高槽膛温度,使阴、阳极温度接近或达到电解槽正常生产温度。
1.3 预焙槽的预热焙烧方法主要有:1.铝液预热法;2.焦粒焙烧法;3.石墨粉焙烧法;4.燃料预热法。
焦粒焙烧现在大型预焙槽的焙烧大部分采用焦粒焙烧法,焦粒焙烧相比铝水焙烧可避免铝液对槽内衬材料的冲击,同时电解质提前进入从而阻挡了铝液从炉底及侧部缝隙向外渗透。
根据我们厂实际焙烧的方法,我们这种来主要探讨一下焦粒焙烧法。
焦粒焙烧法是在阴、阳极之间铺上一层煅烧过的焦炭颗粒,其厚度为15-20mm。
如果炉底平整,焦粒厚度可为10-20mm。
焦粒粒度在1-5mm之间,严格控制1mm一下的焦粉。
1.焙烧前准备工作1.1铺焦与放阳极要求及影响电解槽焙烧前要求铺焦,对于焦粒的铺设有严格的要求,铺焦所用的焦粒粒度为1~5mm,要求铺焦平整,阳极自然下落后与焦粒充分接触,可用钢板尺检查焦粒与阳极底掌是否接触完全,对于接触面积小的应重新调整阳极导杆位置,尽可能使阳极底掌与阴极碳块接触面积较大。
放下阳极后,可将阳极周围焦粒向填充不实的部位塞进去。
保证阳极与阴极底掌完全接触。
实际铺焦过程中经常容易出现这样的问题,作业人员为保证阳极导杆与阳极大母线之间缝隙较小,铺焦过程中往往将阳极外侧焦粒铺的比内侧稍厚一点,这样阳极碳块放下后阳极导杆向大母线方向倾斜,容易保证阳极导杆与大母线的间隙较小,但这种铺焦方式会为以后的焙烧启动工作带来麻烦,具体表现在由于阳极外侧焦粒较厚,阳极外侧接触好,通电焙烧后外侧电流就比内侧大,外侧发热量多导致冰晶石靠槽帮一侧先熔化,靠中缝侧由于发热量少中缝冰晶石熔化速度慢,由于中缝熔化差,不具备启动条件造成焙烧时间被迫延长情况发生。
- 1、下载文档前请自行甄别文档内容的完整性,平台不提供额外的编辑、内容补充、找答案等附加服务。
- 2、"仅部分预览"的文档,不可在线预览部分如存在完整性等问题,可反馈申请退款(可完整预览的文档不适用该条件!)。
- 3、如文档侵犯您的权益,请联系客服反馈,我们会尽快为您处理(人工客服工作时间:9:00-18:30)。
综述铝电解槽焙烧启动期间影响槽寿命的原因与对策摘要:针对电解槽焙烧启动期间造成铝电解槽破损的问题,我们从焙烧工艺和设备进行了不断探索,严抓筑炉和焙烧启动操作质量,进一步延长了电解槽槽寿命。
本文分析了焙烧期间阴极内衬破损的形式及其原因,在此基础上采取了相应的对策,为改善阴极内衬在焙烧启动期间破损的现象、延长铝电解槽槽寿命收到了良好的效果。
关键词:铝电解槽;焙烧启动;槽寿命;破损形式分析;对策1预焙铝电解槽焙烧的目的和要求
焙烧的目的:排除砌体水分,加热槽体;焦化炭块之间和阴极钢棒周围的糊料;使阴极接近或达到正常作业温度;焙烧期间熔化了的高分子比电解质渗入炉底,起到堵塞裂缝、修补缺陷的作用;加热阳极及装炉物料,使阳极温度达到生产温度,熔化物料,满足启动需要;满足电解槽内炭素材料对碱性物质的大量吸收。
焙烧的要求:均匀缓慢的加热电解槽阴极内衬、阳极以及装炉物料,使三者达到一定的温度条件,以利于下一步的启动操作。
2铝电解槽在焙烧期间产生破损的形式及原因分析
2.1阴极炭块断裂或出现裂纹
一般来说,阴极炭块断裂是与阴极炭块的长度方向相垂直的横向裂纹,裂纹的深浅不等,最深的地方可使阴极炭块横向断裂。
这种断裂的产生大都是电解槽在焙烧过程中阴极炭块局部电流密度过大、温度过高、热冲击过大所致。
2.2电解槽炉底中缝捣固糊与阴极炭块之间出现大的裂缝
电解槽炉底阴极炭块之间主要使用捣固糊填充连接处缝隙。
在焙烧过程中,阴极炭块出现膨胀现象,而捣固糊出现收缩,正是这种收缩起到了吸收阴极炭块膨胀的作用,当焙烧温度不超过1200℃时,这种作用可以很好地体现出来,焙烧结束后,一般阴极炭块和烧成后的捣固糊之间有很小的缝隙或不出现缝隙。
当电流分布严重不均、局部温度超过1200℃时,阴极炭块不再膨胀,而是随着温度的升高而发生收缩,烧成后的捣固糊也是随着温度的升高而收缩,这样,阴极炭块之间的捣固糊不再起到吸收阴极炭块膨胀的作用,而使阴极炭块与捣固糊之间的缝隙越来越大。
2.3阴极炭块与边部捣固糊在焙烧过程中出现缝隙
在新建的或大修后的电解槽焙烧过程中,若操作不当,在阴极炭块与边部捣固糊之间也会出现裂缝,其裂缝的生成机理与本文2.2节炉底中缝捣固糊与阴极炭块之间出现裂缝的机理是一样的。
2.4人造伸腿出现横向收缩裂纹与侧部炭块的早期破损
槽底部阴极炭块与侧部炭块之间是由较宽较厚的捣固糊填充并捣实,而这捣实的炭素糊为无头无尾的封闭环型体构成的电解槽人造伸腿。
在焙烧过程中,槽内温度在500℃范围内,由于黏结剂中的碳氢化合物分解,且捣固糊尚处于塑性状态,会使捣固糊的体积产生膨胀;槽内温度超过500℃之后,固化后的捣固糊随温度的升高而收缩,焙烧后产生横向裂纹是不可避免的。
2.5捣固糊剥皮分层
在电解槽焙烧过程中,中缝和边缝的捣固糊出现剥皮和分层的现象偶有发生,这种情况的发生大多与捣固糊黏结剂的成分和配比及捣固时的操作方法和质量有关。
青海分公司铝电解槽的焙烧启动是采用焦粒焙烧工艺,其工艺相对铝液焙烧启动工艺来说,避免了高温铝液对阴极炭素材料产生较大的瞬间热冲击。
但存在一些缺点:阳极电流分布不均,局部热冲击较大;焙烧温度梯度较大,升温过快;焙烧时间短,物料不能充分熔化;启动温度较低且不易启动,一般平均在780~870℃。
正是这些原因导致铝电解槽在焙烧启动期间出现上述几种破损形式。
3实施对策
3.1焙烧发热阻和焦粒铺设方法的改进
3.1.1焙烧发热阻的改进原来单用煅后焦作为发热阻进行通电焙烧电解槽,现将这种发热阻改为煅后焦和石墨碎的混合料(配比为7∶3)作为发热阻进行通电焙烧,从而大大减少了通电初期对电解槽阴极的热冲击。
3.1.2铺设方法的改进原来焦粒的铺设方法是采用栅栏框法和铝框法,在阳极正投影的阴极表面铺设一层20~25mm的长方体焦粒床,这种铺设方法由于阳极本身质量的缺陷等原因,致使阳极底面和焦粒层不能充分接触。
为增加阳极底面与焦粒的接触面积,改善阳极电流分布,降低冲击电压,在阳极正投影的阴极表面设计使用焦粒筛,将焦粒层铺设成由368个高为30mm的圆锥体排列成阳极底面大小的长方形(如图1所示)。
这种铺设方法一方面利用
小而密集的圆锥焦粒体填补找平阳极底面凹凸;另一方面,阳极局部挤压焦粒层时,由于锥体之间存在较大空隙,被挤压的焦粒向周围空隙扩散,使阳极底掌其余部分与其他圆锥焦粒体进一步接触,有效地增加了阳极底面与焦粒层的接触面积。
3.2分流器的改
进与分流器拆除制度的完善为了减小通电初期对电解槽阴极的冲击,将原来的4套分流器采用8套分流器进行代替分流(即由原来的单组分流片改为现在的两组分流片,见图2a);并在安装之前对分流器与立柱母线的接触部位进行仔细打磨(见图2b)达到除锈、除尘的目的,使之充分接触,导电良好,有利于分流。
3.3延长焙烧时间,提高启动温度
预焙铝电解槽焙烧启动条件:启动前焙烧温度必须达到950℃左右、液体电解质高度达到20cm以上,方可启动。
这样可保证电解槽的整个阴极内衬完全焙烧,减少对阴极内衬的热冲击。
原来电解槽焙烧时间为3天(72h),平均启动温度为780~870℃,液体电解质量少,达不到启动条件,启动时存在一定的困难,如灌入的液体电解质对电解槽阴极尤其是边部炭糊和侧炭的冲击较大。
为达到理想的启动条件,经试验,将电解槽焙烧时间延长至4天(96h),电解槽达到了较为理想的焙烧启动条件,焙烧平均启动温度达到890~960℃,物料熔化较为完全,液体电解质量增加,电解槽启动容易,电解质也容易灌进去,消除了启动时抬电压阳极脱离电解质发生断路等安全隐患,同时,对电解槽阴极及边部炭糊和炭
块的冲击较小。
另外,焙烧期间能产生足够的电解质液,可从中析出高分子冰晶石和刚玉α-al2o3组成坚硬的固体结壳,均匀覆盖在这种具有横向裂纹的捣固糊烧成体与侧部炭块上面形成炉膛。
4结束语
铝电解槽焙烧启动质量的好坏直接影响到电解槽的槽寿命。
我们充分利用停开槽的机会,针对焙烧期间阴极出现破损的形式,分析查找影响因素,并实施相应的对策,为改善阴极内衬在焙烧期间破损的现象、延长铝电解槽槽寿命收到了良好的效果:(1)降低了通电焙烧的冲击电压,降低了对阴极的瞬间热冲击。
(2)减小了焙烧温度梯度,使其阴极内衬温度缓慢升高。
(3)改善阳极电流分布不均的状况,减少了阴极内衬的局部热冲击。
(4)提高了焙烧启动温度,降低了启动过程中高温对内衬的瞬间热冲击;焙烧物料熔化较完全,电解质高度增加至20cm以上,使得高分子比电解质填充阴极内衬的裂缝,覆盖在整个阴极内衬,阻断铝液渗漏通道,起到防护整个阴极内衬被侵蚀的作用。
参考文献:
[1]赵无畏.现代预焙电解槽焦粒预热焙烧启动研究[j].轻金属,2003,(2):34.
[2]邱竹贤.铝电解原理与应用[m].徐州:中国矿业大学出版社,1998.
[3]邱竹贤.预焙槽炼铝(3版)[m].北京:冶金工业出版社,2005.。