重介旋流器分选原理
重介旋流器分选原理
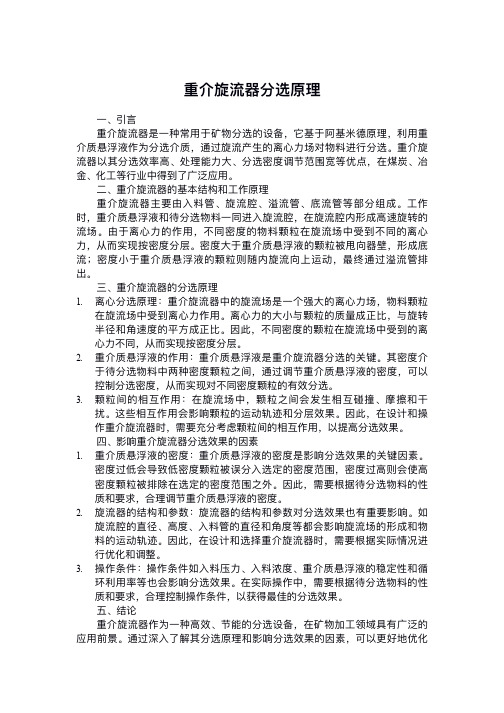
重介旋流器分选原理⼀、引⾔重介旋流器是⼀种常⽤于矿物分选的设备,它基于阿基⽶德原理,利⽤重介质悬浮液作为分选介质,通过旋流产⽣的离⼼⼒场对物料进⾏分选。
重介旋流器以其分选效率⾼、处理能⼒⼤、分选密度调节范围宽等优点,在煤炭、冶⾦、化⼯等⾏业中得到了⼴泛应⽤。
⼆、重介旋流器的基本结构和⼯作原理重介旋流器主要由⼊料管、旋流腔、溢流管、底流管等部分组成。
⼯作时,重介质悬浮液和待分选物料⼀同进⼊旋流腔,在旋流腔内形成⾼速旋转的流场。
由于离⼼⼒的作⽤,不同密度的物料颗粒在旋流场中受到不同的离⼼⼒,从⽽实现按密度分层。
密度⼤于重介质悬浮液的颗粒被甩向器壁,形成底流;密度⼩于重介质悬浮液的颗粒则随内旋流向上运动,最终通过溢流管排出。
三、重介旋流器的分选原理1.离⼼分选原理:重介旋流器中的旋流场是⼀个强⼤的离⼼⼒场,物料颗粒在旋流场中受到离⼼⼒作⽤。
离⼼⼒的⼤⼩与颗粒的质量成正⽐,与旋转半径和⻆速度的平⽅成正⽐。
因此,不同密度的颗粒在旋流场中受到的离⼼⼒不同,从⽽实现按密度分层。
2.重介质悬浮液的作⽤:重介质悬浮液是重介旋流器分选的关键。
其密度介于待分选物料中两种密度颗粒之间,通过调节重介质悬浮液的密度,可以控制分选密度,从⽽实现对不同密度颗粒的有效分选。
3.颗粒间的相互作⽤:在旋流场中,颗粒之间会发⽣相互碰撞、摩擦和⼲扰。
这些相互作⽤会影响颗粒的运动轨迹和分层效果。
因此,在设计和操作重介旋流器时,需要充分考虑颗粒间的相互作⽤,以提⾼分选效果。
四、影响重介旋流器分选效果的因素1.重介质悬浮液的密度:重介质悬浮液的密度是影响分选效果的关键因素。
密度过低会导致低密度颗粒被误分⼊选定的密度范围,密度过⾼则会使⾼密度颗粒被排除在选定的密度范围之外。
因此,需要根据待分选物料的性质和要求,合理调节重介质悬浮液的密度。
2.旋流器的结构和参数:旋流器的结构和参数对分选效果也有重要影响。
如旋流腔的直径、⾼度、⼊料管的直径和⻆度等都会影响旋流场的形成和物料的运动轨迹。
选煤常识-重介质旋流器

形式和以前的一样,时间为5月22日三产品重介质旋流器三产品重介质旋流器,用一种密度的悬浮液系统可选出三种最终产品,省掉了一套高密度悬浮液系统及设备,大大简化了工艺流程。
设备,投资和厂房体积均可降低15%以上。
一、大型无压三产品旋流器系统及特点1、大型无压三产品旋流器的结构、原理及工作过程(见图6—12)。
图6—12大型无压给料三产品旋流器是由一台圆筒形旋流器和一台圆筒圆锥旋流器串联而成的设备,原煤由刮板给入,一段旋流器悬浮液由泵给入。
其分选过程是重产物在旋流器内沿筒壁形成外螺旋由底流口排出,轻产物在旋流器中心形成内螺旋由溢流口排出,从低密度到高密度。
在第一段旋流器中不但可以把原煤分成两种产品,而且还把进入第二段旋流器的悬浮液浓缩到需要的密度。
重产品与浓缩后的悬浮液一起经连接管给入第二段旋流器进行再选,最终获得中煤和矸石。
2、大型无压给料三产品旋流器系统的特点①入洗粒度范围较宽,有效分选下限低。
跳汰机入料粒度50mm以下,分选下限0.5mm,而三产品旋流器入料粒度80mm以下,可有效分选到0.3mm。
②次生煤泥少。
由于物料靠自重进入旋流器,介质液由泵沿切线给入,减少了物料之间的碰撞机率,且重产物运行路线短,从而可减少3—5%次生煤泥量,旋流器分选时间短,水量小,可减少泥化,更有利于易泥化煤的分选;可使浮选系统入料量大幅度减少,预计可减少1/4入浮煤泥量,从而降低了浮选的成本。
③分选精度高。
用三产品重介旋流器洗选,由于采用轴向中心给料,减少了界面上循环物料的干扰,提高了分选效果,一般Ep1≤0.04,Ep2≤0.06。
也使原煤分选易于控制,矸石损失降低,精煤产率提高。
与跳汰工艺相比,用三产品重介旋流器洗选,可提高产率5%左右,使矸石损失降至3%以下,而且可保证精煤质量。
④有利于实现自动化控制,减小工作量,降低劳动强度。
⑤整个系统简单有效。
下面是三产品重介旋流器流程示意图,图6—13。
图6—13⑥容易实现煤泥重介分选。
选煤厂无压三产品重介质旋流器分选技术

无 压给料分选过 程中 . 只有 重产 物单 向穿 越“ 分离锥面 ” 。 避免 了 有 压给料分选过 程中轻重产物 同时交错穿越 “ 分离锥面 ” 而产 生相互 干扰从而影 响分选精度 的弊端 2 . 4 重悬浮液介质 的性质更加容易控制 有压 给料 , 原煤 和重悬浮液介质 分别进入旋 流器 内. 从 而减少 了 原煤性质变化对悬浮液性质测量时的干扰 . 使悬 浮液 的性 质 自动测量 更加 的准确 , 也使得悬浮液 的性质更加容易控制 。
一 一
_
r n  ̄ . 3 . 0 %。
由图 1 计算可能偏差 : 段可能偏差 : E 。 = ( 5 1 一 8 1 , 2 : 0 . 0 2 5 二段可能偏差 : E ( 8 2 7 r8 2 = 0 . 0 6 3
一 ~
二段高密度分割错 配物曲线等误密度 为 8 e = 1 . 7 4 0 时 .轻产 品精 煤 中的错配量为 m h - - L 5 %。 重产 品中煤和矸石 的错配量为 m = 1 . 5 %。 错
一
2 无压三产 品重介质 旋流器的特点
2 一 无压给料 , 原煤在 自身重力作用下进入旋流器 进行 分选 . 不需要
泵送 . 减少矸石 泥化和次生煤 泥 量的产生 . 可以降低煤泥水的处 理负荷 2 . 3 精煤损失少 . 分选精度更 高
【 摘 要】 本文介绍了WT M C 1 2 0 0 / 8 5 0 型无压三产品重介质旋流器的工作原理及技术特点, 以及梁宝寺选煤厂如何通过实验研究、 数据分
析 与现 场改造相 结合 的方法来提 高无压三产品重介质旋流器的分选效果。
【 关键词】 工艺效果评价; 分选效果; 工艺指标
1 无压三产品重介质旋流器的工作原理
重介旋流器的原理和运行分析

洗选加工中心课题设计(论文)设计(论文)题目:重介旋流器的原理与运行分析姓名:蒋彦钦指导老师:李峰单位:补连塔选煤厂时间:2010年6月重介旋流器的原理与运行分析蒋彦钦(神东煤炭集团洗选加工中心,陕西省神木县大柳塔镇,719315)摘要:重介旋流器是一种分选效率高,分选粒级宽的重选设备,但由于其在离心立场中分选而流场与重力场中相比较比较复杂,本文分析了重介旋流器内介质流场的分布情况及其中心空气柱的形成原理并比较了离心立场中实现矿物分选与重力场中实现分选的区别。
由于影响重介旋流器运行的因素很多,但在实际运行控制中主要是调节入料压力和改变重介旋流器底流口大小来改变运行状态。
在一定范围内增大入料压力可以提高旋流器处理能力和分选效果,同时增强了浓缩作用使实际分选密度增大;改变底流口大小也是调节实际分选密度的一种手段,减小底流口大小可使实际分选密度增大而减小重介质的消耗。
但是不论是增大入料压力或是减小底流口大小都应控制在一定范围内否则将影响重介旋流器运行效果。
关键词:重介旋流器;重力选矿;离心力场1.前言随着重介质选煤技术的发展及其有着分选效率高,产出投入比高的优点;随着近年来煤炭市场经济的进一步发展,环境和用户对煤炭质量的要求越来越高,我国的重介质选煤方法的入选比重也逐步提高。
与其他选煤方法相比较,重介质选煤的分选精度是最高的,特别是利用重介旋流器使分选过程由传统的重力场转移到离心力场中来,有着可能偏差E小,分选粒级宽的优点,重介旋流器在重介选煤技术中有着很好的发展前景。
然而重介旋流器虽然在煤炭行业中有着比较成功的应用,但是由于其实践先于理论并且旋流器中的流场和影响因素比较复杂,因此本文将对重介旋流器的原理进行分析并对现场运行中的关键因素进行探讨。
2.原理分析由于重介旋流器经过几十年的发展,出现了许多不同设计,不同型号的产品,因此本文为了说明原理将以DSM重介旋流器(圆筒圆锥型重介质旋流器)为代表论述其原理。
无压三产品重介质旋流器工作原理

无压三产品重介质旋流器工作原理引言旋流器是一种重要的固液分离设备,在许多工业领域有着广泛的应用。
无压三产品重介质旋流器是近年来引入的一种新型旋流器,具有较高的分离效率和处理能力。
本文将详细介绍无压三产品重介质旋流器的工作原理及其应用。
旋流器的基本原理旋流器是通过高速旋转产生的离心力实现固液分离的设备。
其基本原理是将待处理的流体分为内旋流和外旋流两部分,随着流体在旋转过程中的离心力增大,固体颗粒被迫向内旋流移动,最终被集中排出。
传统旋流器的不足传统的旋流器存在一些问题,如分离效率低、易堵塞、处理能力有限等。
为了解决这些问题,无压三产品重介质旋流器应运而生。
无压三产品重介质旋流器的工作原理无压三产品重介质旋流器是在传统旋流器的基础上改进而来的。
它具有三个输出口,分别用于排出固相、液相和重介质。
其工作原理如下:1. 初始状态无压三产品重介质旋流器的初始状态为向旋流器内输入待处理的流体。
流体在旋流器内部形成一个旋转的涡流。
2. 内部分离随着旋转速度的增加,流体中的固相开始受到离心力的作用,向内旋流移动。
同时,重介质也会沉积在旋流器的底部。
3. 外部分离固相进一步向内旋流移动,最终通过固相排出口被集中排出。
液相则向外旋流移动,经过液相排出口排出。
4. 重介质回收重介质在旋流器底部积聚,经由重介质排出口排出,并进行回收和再利用。
无压三产品重介质旋流器的应用无压三产品重介质旋流器在多个领域有着广泛的应用,包括但不限于:1. 石油工业在石油开采过程中,常常需要进行固液分离。
无压三产品重介质旋流器可以高效地分离油水混合物,将固相和重介质分别排出,使油水分离更加彻底。
2. 矿山工业在矿山中,常常需要对含有矿石颗粒的水进行处理。
无压三产品重介质旋流器可以将固相颗粒和重介质分离,实现固液分离,从而提高矿石提取效率。
3. 食品加工在食品加工过程中,常常需要进行污水处理和固液分离。
无压三产品重介质旋流器可以高效地将固相和重介质分离,使污水净化更加彻底。
重介旋流器原理及操作
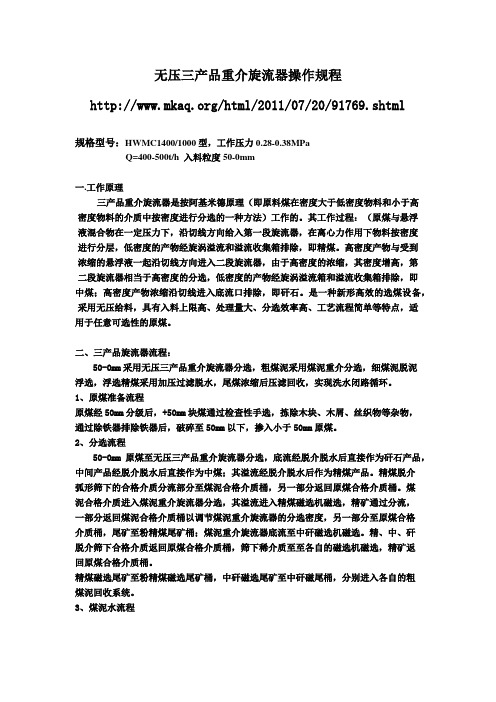
无压三产品重介旋流器操作规程/html/2011/07/20/91769.shtml规格型号:HWMC1400/1000 型,工作压力0.28-0.38MPaQ=400-500t/h 入料粒度50-0mm一.工作原理三产品重介旋流器是按阿基米德原理(即原料煤在密度大于低密度物料和小于高密度物料的介质中按密度进行分选的一种方法)工作的。
其工作过程:(原煤与悬浮液混合物在一定压力下,沿切线方向给入第一段旋流器,在离心力作用下物料按密度进行分层,低密度的产物经旋涡溢流和溢流收集箱排除,即精煤。
高密度产物与受到浓缩的悬浮液一起沿切线方向进入二段旋流器,由于高密度的浓缩,其密度增高,第二段旋流器相当于高密度的分选,低密度的产物经旋涡溢流箱和溢流收集箱排除,即中煤;高密度产物浓缩沿切线进入底流口排除,即矸石。
是一种新形高效的选煤设备,采用无压给料,具有入料上限高、处理量大、分选效率高、工艺流程简单等特点,适用于任意可选性的原煤。
二、三产品旋流器流程:50-0mm采用无压三产品重介旋流器分选,粗煤泥采用煤泥重介分选,细煤泥脱泥浮选,浮选精煤采用加压过滤脱水,尾煤浓缩后压滤回收,实现洗水闭路循环。
1、原煤准备流程原煤经50mm分级后,+50mm块煤通过检查性手选,拣除木块、木屑、丝织物等杂物,通过除铁器排除铁器后,破碎至50mm以下,掺入小于50mm原煤。
2、分选流程50-0mm原煤至无压三产品重介旋流器分选,底流经脱介脱水后直接作为矸石产品,中间产品经脱介脱水后直接作为中煤;其溢流经脱介脱水后作为精煤产品。
精煤脱介弧形筛下的合格介质分流部分至煤泥合格介质桶,另一部分返回原煤合格介质桶。
煤泥合格介质进入煤泥重介旋流器分选,其溢流进入精煤磁选机磁选,精矿通过分流,一部分返回煤泥合格介质桶以调节煤泥重介旋流器的分选密度,另一部分至原煤合格介质桶,尾矿至粉精煤尾矿桶;煤泥重介旋流器底流至中矸磁选机磁选。
精、中、矸脱介筛下合格介质返回原煤合格介质桶,筛下稀介质至至各自的磁选机磁选,精矿返回原煤合格介质桶。
无压给料三产品重介旋流器分选技术探究
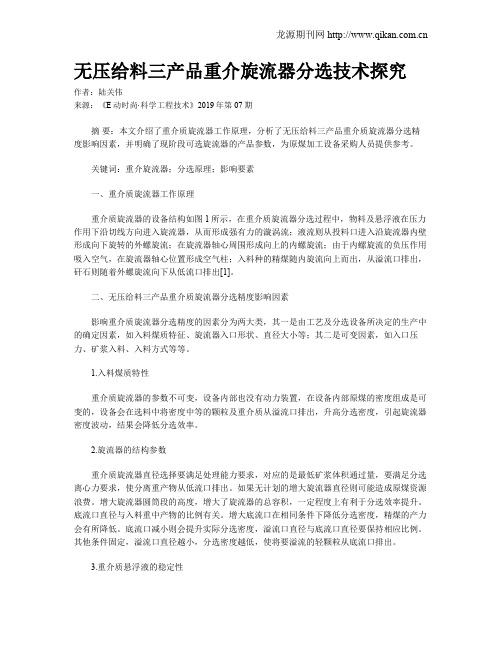
无压给料三产品重介旋流器分选技术探究作者:陆关伟来源:《E动时尚·科学工程技术》2019年第07期摘要:本文介绍了重介质旋流器工作原理,分析了无压给料三产品重介质旋流器分选精度影响因素,并明确了现阶段可选旋流器的产品参数,为原煤加工设备采购人员提供参考。
关键词:重介旋流器;分选原理;影响要素一、重介质旋流器工作原理重介质旋流器的设备结构如图1所示,在重介质旋流器分选过程中,物料及悬浮液在压力作用下沿切线方向进入旋流器,从而形成强有力的漩涡流;液流则从投料口进入沿旋流器内壁形成向下旋转的外螺旋流;在旋流器轴心周围形成向上的内螺旋流;由于内螺旋流的负压作用吸入空气,在旋流器轴心位置形成空气柱;入料种的精煤随内旋流向上而出,从溢流口排出,矸石则随着外螺旋流向下从低流口排出[1]。
二、无压给料三产品重介质旋流器分选精度影响因素影响重介质旋流器分选精度的因素分为两大类,其一是由工艺及分选设备所决定的生产中的确定因素,如入料煤质特征、旋流器入口形状、直径大小等;其二是可变因素,如入口压力、矿浆入料、入料方式等等。
1.入料煤质特性重介质旋流器的参数不可变,设备内部也没有动力装置,在设备内部原煤的密度组成是可变的,设备会在选料中将密度中等的颗粒及重介质从溢流口排出,升高分选密度,引起旋流器密度波动,结果会降低分选效率。
2.旋流器的结构参数重介质旋流器直径选择要满足处理能力要求,对应的是最低矿浆体积通过量,要满足分选离心力要求,使分离重产物从低流口排出。
如果无计划的增大旋流器直径则可能造成原煤资源浪费。
增大旋流器圆筒段的高度,增大了旋流器的总容积,一定程度上有利于分选效率提升。
底流口直径与入料重中产物的比例有关。
增大底流口在相同条件下降低分选密度,精煤的产力会有所降低。
底流口减小则会提升实际分选密度,溢流口直径与底流口直径要保持相应比例。
其他条件固定,溢流口直径越小,分选密度越低,使将要溢流的轻颗粒从底流口排出。
重介旋流器的工作原理

重介旋流器的工作原理旋流器是一种常用的固液分离设备,它通过利用液体在旋转流场中的离心力和离心力梯度的差异,将固体颗粒从液体中分离出来。
旋流器的工作原理可以分为两个方面:旋转流场的形成和固液分离的实现。
首先,旋转流场的形成是旋流器工作的基础。
旋流器通常由一个圆筒形的筒体和一个中心轴组成。
当液体从旋流器的进料口进入筒体时,由于中心轴的旋转,液体开始形成旋转流场。
在旋转流场中,液体呈现出高速旋转的状态,而固体颗粒则受到离心力的作用,向外部壁面移动。
同时,由于旋转流场的形成,液体在筒体内部形成了一个中心空旋涡和一个外部环状流动区域。
其次,固液分离是旋流器实现固液分离的关键过程。
在旋转流场中,固体颗粒受到离心力的作用,向外部壁面移动。
由于固体颗粒的质量和尺寸不同,它们在离心力的作用下会沿着不同的轨迹运动。
较大的固体颗粒由于惯性较大,会沿着外部环状流动区域向下沉积到底部,形成固体沉积物。
而较小的固体颗粒则会随着液体一起通过旋流器的溢流口排出。
通过调节旋流器的操作参数,如进料流量、旋转速度等,可以实现对固液分离的控制。
旋流器的工作原理可以通过以下几个方面来解释:1. 离心力的作用:旋流器中液体的旋转流场会产生离心力,离心力的大小与液体的旋转速度和液体颗粒的质量有关。
离心力的作用使得固体颗粒受到向外的力,从而向外部壁面移动。
较大的固体颗粒由于惯性较大,受到的离心力较大,因此会沉积到底部。
而较小的固体颗粒由于惯性较小,受到的离心力较小,因此会随着液体一起通过溢流口排出。
2. 旋转流场的形成:旋流器中的旋转流场是通过中心轴的旋转来实现的。
当液体从进料口进入旋流器时,中心轴的旋转使得液体开始形成旋转流场。
旋转流场的形成使得液体呈现出高速旋转的状态,从而产生离心力。
同时,旋转流场的形成还使得液体在筒体内部形成了一个中心空旋涡和一个外部环状流动区域。
固体颗粒受到离心力的作用,向外部壁面移动。
3. 固液分离的实现:旋流器通过调节操作参数,如进料流量、旋转速度等,可以实现对固液分离的控制。
- 1、下载文档前请自行甄别文档内容的完整性,平台不提供额外的编辑、内容补充、找答案等附加服务。
- 2、"仅部分预览"的文档,不可在线预览部分如存在完整性等问题,可反馈申请退款(可完整预览的文档不适用该条件!)。
- 3、如文档侵犯您的权益,请联系客服反馈,我们会尽快为您处理(人工客服工作时间:9:00-18:30)。
重介旋流器分选原理重介选在矿物分选中的作用重介选可用于矿物的预选和精选。
重介选的主要优点是效率高、理能力大、吨物料加工费低。
而且其它方法难以处理的物料,也能进行有效的分选。
作为预选设备,重介选是唯一能以0.1g·ml 密度差(即有用成分与无用成分的密度差)进行分选的一-种方法。
重介旋流器的出现不仅改善了分选效果,而且入选物料粒度下限可达到0·5ar m。
重介旋流器还能移处理细嵌布的入料矿物,而且使用范围还可扩展到以前认为不能够预精选的物料。
在煤炭工业研制出了自生重介系统(矿物细料作为分选介质)用于回收下限0.1ram的细粒入料。
选煤工业中斯研制出了直径为1.2m的粒度重介旋流器(LA RCODEM S),入料粒度为10—0.5mm,解决了粗粒煤和细粒煤须分别处理的问题,从而简化了流程。
几种使用中的旋流器类型用于重介选的主要有两种旋流器。
一类是标准旋流器,如荷兰的DSM旋流嚣,其结构与普通分级旋流器的不同处主要在于结构强度大及底流口直径一旋流器直径比大,特别是在处理大块入料时。
这主要反映在入料口和底流口直径上,其设计入抖粒度至少为25arm。
另一类是圆筒型旋流器,包括DWP,Tri,Flo和Lareodems于结构强度大及底流口直径一旋流器直径比大,特别是在处理大块入料时。
这主要反映在入料口和底流口直径上,其设计入抖粒度至少为25arm。
另一类是圆筒型旋流器包括DWP,Tri,Flo和Lareodems旋流器。
介质不是同矿物一起而是单独由泵打入倾斜放置的旋流器低端。
如图1所示,物料沿轴向给入(带极少量介质)旋流器的顶端}沉物则以控制的反压力沿旋流器筒俺切线方向排出,而浮物剐从旋流器的底部轴线方向排出。
TriFlo与DWP及大粒度重介旋流器主要区别是,Tri Flo由两个分选段组,第一段的溢流作为第二段的入料。
这,旋流器的第二段可以对第一段溢流产进行扫选(后一段的密度自然要比前一的密度略低,因第一段的溢流对第二段有稀释作用)。
另一方面,低密度段的入料介质也可以加以稀释,以加大两段闻的密度差,出两种产品(例如荧石一重晶石的分选),或者出精煤和中间产品(如低灰精煤和高灰精煤)。
DWP旋流器借助排料管来控制作用在沉物上的反压,而TriFio旋流器使用的是一个可调节的沉物排放箱,大粒度重介旋流器则使用旋涡器,这种旋涡器最初使用在英国沃赛尔旋流器上,是用于减小旋流器沉物排放口处所形成的过大旋涡。
很明显,安装使用上述所有这些排料设备在一定程度上都起双重作用。
第二类旋流器的工作原理是相似的,即矿物颗粒从中心给入,沉物颗粒沿着旋流器的周边移动到排料端。
而DSM旋流器正相反,入料沿切线方向给入,而低密度颗粒则向旋流器中心移动。
这两类旋流器的其它不同之处还在于,一类旋流器由于空气柱的附加限制,底流的流量也受到了限制,以致溢流量一底流量比值较大(一般为2:1~3:1)。
而另一类旋流器剐不同,即使是受底流反压力的作用,溢流一底流的流量比一般也为1:1。
根据对这些资料的客观分析,可以认为,用第二种类型旋流器时,入料类似于浮物排放(如精煤产品)是沿径向从某点给入的,将会提高回收率。
而对选矿来讲,使用第一类旋流器,有价值的精矿产品(通常是沉物)于是沿周边排除,回收率也会得到提高。
如果仅仅是很少一部分沉物需要回收的话,一部分多余的介质流入浮物中是有益的。
但是TriFlo旋流器毕竟具有两个分选段,和上述旋流器一样,总的流动情况及潜在的涡流产生源,对设备工作效率的限制有相同的影响。
第=类旋流器系统的一个实际优点是,旋流器入口及旋流器筒壁的磨损可大大减小,特别是在矿右中含硬度高的低密度成分的情况卞。
影响分选效果的因素在探讨影响旋流器分选效果的因素前,需要说明的是,采用旋流器的主要优点是其中的固体颗粒可受到加速度的影响。
作用在旋流器径向上的加速度因数z与等效重力有关,并由下式表示,即·Z=W2R/9.85式中w一旋流器内颗粒的角速度,S-1,R一旋流器的半径,m。
W=V/RR式中V一切向速度,ms-1Z和w都受颗粒在旋流器内部所处位置的影响,通常在旋流器筒壁处达到最小值,而在接近旋流器中心处达到最大值。
入料压力55kpa时,在一直径250arm重介旋流器的中间点(距中,~62mm)处的等效重力值约为20左右。
如上文所述,介质的粘度和稳定性都影响分选效果。
粘度的影响很明显,它会限制入选颗粒的径向速度,致使邻近密度的颗粒因滞留时间短不能够正确地进入滥流或底流。
这也是分选细粒物料时介质分选密度与颗粒的分配密度(Y/D—o)比值加大的原因。
介质稳定性的影响就不太明显,虽然可以概括地说,浮物和沉物密度有较大的密度差时,颗粒会聚集在中间密度范围区。
有证据表明·如果在旋流器中保持一种层流状态,介质的流态类似于浓缩帆中的重矿浆。
图2所示为旋漉器径向断面以及根据实验室沉降试验所绘制的介质分配剖面图。
由图中可看出接近旋流器核心部分是清水,这可为浓缩介质旋漉器的实践所证实。
然后是一个密度渐增医,该区主要是细粒介质。
紧接着是一个密度基本恒区。
有证据表明·如果在旋流器中保持一种层流状态,介质的流态类似于浓缩帆中的重矿浆。
图2所示为旋漉器径向断面以及根据实验室沉降试验所绘制的介质分配剖面图。
由图中可看出接近旋流器核心部分是清水,这可为浓缩介质旋漉器的实践所证实。
然后是一个密度渐增医,该区主要是细粒介质。
紧接着是一个密度基本恒定区。
随着介质离折程度的加大,清水区和低密度区的深度也逐渐增加。
因此,在正常操作条件下,DSM旋沉器的恒定密度区内,有一轴向零速环。
低密度区在离的影响下越过轴向零速区域前,分选密度接近底流密度,而在越过轴向零造区域后,分选密度将相对于底流密度而加大,这可由图8得到说明,在动态曲线的斜率比较高的速率增长的起始点处,旋流器的分配密度D。
曲线与底流曲线相脱离。
这一点与底流密度(Pu)在介质的析离作用下,开始稳定的一点重台。
由于分选区内细粒介质相对粒度较高,分选效率也从该点处开始下降。
DSM旋流器在介质稳定的条件下,分选不同粒级的颗粒时,介质对分选密度和分选效果的影响遵循一定的规律,如图4所示。
在选最粗的粒级时,分选密度n(相当于底流密度Pu)等于D o,但此后D。
将随着颗粒粒度的减小而加大。
当颗粒粒度减小时,分选效率也随之降低(E值增加)。
在圆筒形旋流器中,较大一部分介质被带入沉物中,因此旋流器溢流和底流间的密度差也加大,反之亦然。
这说明沉物反压对介质的流动形态有一定影响,而最终又将影响介质的分配。
沉物反压力也可以使轴向零速区沿径向向内部移动,这将导致分选密度的降低和介质析离程度的减小。
一般认为,要使介质既具备一定的稳定性又具有不太高的粘度,这本身就是矛盾的。
在很多情况下,要作折衷处理,使介质保持在一定的粘度和稳定性限度内,这可以通过联机粘度测定或根据底、溢流密度差进行控制来实现。
除了利用介质自身性质外,使用分散剂也能改变介质的牯度。
图5所示为某些化学药剂对介质粘度及沉降速度的影响,如石灰(通常用作抑制剂)可减缓牯泥的沉降速度,但可相应地增加介质牯度。
硅化钠在低浓度时可大大增加沉降速度,但在高浓度时,却显著降低沉降速度但不影响粘度。
偏磷酸盐在浓度比较低时(小于1g/t),既能降低牯度也能加大稳定性。
碳酸钠、硼砂、磷酸钠也如此。
尽管这些资料主要涉及的是泥层的沉降速度,而不是泥层内部的沉降速度。
但这些资料说明使用某些药剂确实能改善生产效率或者扩大给定介质的适用范围。
但是,除了药剂本身也是防腐抑制剂外(如NaNO),由于成本的关系,这些辅加药剂也只限于在为数不多的系统内使用,如细颗粒的分选,高密度分选和贵重物料的分选等。
除了介质本身性质外,重介旋流器的效率也与入口压力.流量及旋流器几何尺寸有关。
孟格勒斯确定了标准给料压头H=9D(这里D是旋流器的直径)情况下的E值与旋流器直径关系,井指出直径6OO一200arm旋流器的效率有明显增加。
他认为这是小直径旋流器中离心加速度也大的缘故。
增加离心加速度固然能得到明显的效果(对250arm旋流器来说,从入口到中心的典型离心加速度值为5~420g),但旋流器的入料矿浆流量有一个上限值。
若超出此个上限值,则有造成出现紊流和介质流动特性变化的可能性。
而这个上限值又明显地取决于旋流器的几何尺寸。
在芒特·艾萨半工业性试验厂内就入料压力对DW P旋流器工作情况的影响进行了研究,并证实,随着旋流器入料口压力的增大,密度差(Pu —Po),分选密度差(d一y。
)和E值将减小。
在压力超过一定限度(1l5Pa或20D)后,情况正好相反。
但是,进入底流和溢流的相对体积流量对Pu~Po或d o—ys值的影响情况,目前尚无评定资料。
司托森奈发现,分选细粒煤时,可通过改变底流口直径的方法来控制产率,麻流量以及分选密度。
戴维斯也确定了底流口直径对分选效率的影响但他发现,介质粘度(取决于粘泥含量)也影响底漪的分配量及底流密度,从而也影响分选密度和分选效率。
由上文所述可以靖楚地看出,介质体积流量的分配方法是很多的。
介质体积流量的分配对分选效率和密度差都有显著的影响发展前景重介旋流器分选技术有可能扩展到新的矿物分选领域。
目前,重介旋流器在煤炭行业扩展到分选细粒级的趋势,很可能转移到其它矿业界。
使用自生介质的技术对矿业系统不适尉,而且从细粒人料中回收细粒介质也是一个主要的技术难题。
以低密度的介质分选细粒入料(由于d。
一y。
增加)可以减少运转费用。
这一技术显然适用于尾矿堆的再处理。
其他发展领域是高密度分选。
目前,铬铁矿的高密度分选最受欢迎,所采用的分选密度高述3.6g·ml_。
这已基本上接近硅铁使用极限。
TriFlo和大粒度重介旋流器的发展进一步加大了这一工艺灵活性,不仅扩大了分选范围,同时还扩大了同一分选机内颗粒的分选密度范围和粒度范围。
未来的进展可能主要是对不同类型旋流器物理原理的进一步了解。
这一点将通过现象模型的发展和配备更加先进的自动控制系统来实现。
圆筒形旋流器的模型尤为缺少。
介质的粘度和稳定性对分选效率、分选过程、分选密度羞以及这些参数与介质分配量的相互联系仍需要作重点研究。
在处理细粒级物料、进行高密度分选以及有用成分和矸石的密度差较小情况下,分选效果、分选过程,密度差等参数是十分重要的。
刘晨宏摘译白《采矿和采石》,1988年,第1O期,第41一46页李清华校。