搅拌式反应器的模拟与优化设计
优化高级氧化技术的反应器设计原理

优化高级氧化技术的反应器设计原理引言:高级氧化技术是一种重要的水处理技术,通过利用氧化剂产生的自由基来降解水中的有机物和污染物。
反应器是高级氧化技术实施过程中的关键设备,其设计原理对反应效果起到至关重要的作用。
本文将探讨优化高级氧化技术的反应器设计原理,以期提高反应效率和降低成本。
一、反应器类型选择在高级氧化技术中,常用的反应器类型包括搅拌式反应器、固定床反应器和流动床反应器等。
不同类型的反应器具有不同的特点和适用范围。
在选择反应器类型时,需考虑反应物质的特性、反应速率以及反应器的尺寸和操作要求等因素,以确保反应器能够更好地满足反应需求。
二、氧化剂的选择与投加方式高级氧化技术中常用的氧化剂包括臭氧、过氧化氢和高价态氧等。
在反应器设计中,需根据反应物质的特性和需求选择合适的氧化剂,并确定其投加方式。
氧化剂的选择和投加方式直接影响反应器的反应效率和运行成本。
三、反应器内部结构设计反应器的内部结构设计对反应效果具有重要影响。
在设计过程中,需考虑传质和传热的效果,以提高反应物质与氧化剂的接触效率。
常见的设计手段包括增加反应器的表面积、采用填料或增加搅拌装置等,以增强物质间的传质和传热效果。
四、反应器的操作参数控制反应器的操作参数对反应效果和经济性具有重要影响。
在实际运行过程中,需根据反应物质的特性和反应速率确定适宜的操作参数,如温度、压力、pH值和氧化剂投加量等。
合理的操作参数控制可以提高反应效率,降低能耗和成本。
五、反应器的尺寸设计反应器的尺寸设计直接影响反应物质的停留时间和反应效果。
在设计过程中,需根据反应物质的特性和反应速率确定合适的反应器体积和尺寸。
过小的反应器尺寸会导致停留时间不足,反应不完全;过大的反应器尺寸则会增加成本和能耗。
因此,合理的反应器尺寸设计是优化高级氧化技术的关键。
结论:通过合理选择反应器类型、氧化剂和投加方式,设计反应器的内部结构和操作参数,以及确定合适的反应器尺寸,可以有效优化高级氧化技术的反应器设计,提高反应效率和降低成本。
酯化反应器内搅拌器的优化设计

关 键 词 :循环 流 量 功率准 数
搅拌器
酯化反 应器
中 图 分 类 号 : Q3 0 5 T 2 .
文 献 识 别 码 :A
文 章 编 号 :1 0 — 0 1 2 0 ) 40 1 - 4 0 10 4 ( 0 2 0 — 0 60
聚 酯 生 产 中 的 酯 化 反 应 是 吸 热 反 应 , 反 应 在
收 稿 日期 ; 0 1 1 — 7 2 0 — 2 1 ;修 订 日 期 : 0 2 0 — 1 2 0 — 32 。
作者 简介 : 肖建 军 ( 9 2 ) 男 , 蒙 古 赤 峰 市 人 , 士 。 17一 , 内 硕
维普资讯
第 4期
肖建 军 等 . 化 反 应 器 内 搅 拌 器 的 优 化 设 计 酯
向流 动 , 此 一 般 将 其 置 于 导 流 筒 下沿 外 端 , 因 以增
大 导 流 筒 出 口处 的径 向流 动 从 而 加 大 反 应 器 内 的
循环流量 。
传 热 、 质 。 用 合 适 的 搅 拌 器 是 提 高 聚 酯 产 品 的 传 使
质 量 和 产 率 的关 键 因 素 之 一 l 。 _ 2 ] 笔 者 以 冷 模 试 验 为 基 础 , 循 环 流 量 为 着 眼 以 点 , 工 业 用 酯 化搅 拌 器 进 行 深 入 的 研 究 , 对 测试 了 酯 化 搅 拌 器 的 流 量 准 数 和 功 率 准 数 , 根 据 工 艺 并 要 求 设 计 了 新 的 搅 拌 桨 叶 型 式 , 得 了 较 好 的 效 取
肖建 军 包 雨 云 黄 雄 斌 施 力 田 杜 秋 杰 。
( .北 京 化 工 大 学 化 学 工 程 学 院 ,北 京 1 0 2 ; .仪 征 化 纤 股 份 有 限 公 司 ,江 苏 仪 征 2 1 0 ) 1 00 9 2 1 9 0
搅拌生物反应器混合特性的数值模拟与实验研究

2005 年 4 月 The Chinese Journal of Process Engineering Apr. 2005收稿日期:2004−07−29,修回日期:2004−09−27作者简介:洪厚胜(1965−),男,江西省鄱阳市人,博士,副教授,主要从事生化工程及生化反应器的研究.搅拌生物反应器混合特性的数值模拟与实验研究 洪厚胜, 张庆文, 万红贵, 欧阳平凯 (南京工业大学制药与生命科学学院,江苏 南京 210009)摘 要:以工程流体计算软件CFX −4.4为工具,对不同规模的机械搅拌生物反应器的混合特性进行数值模拟,研究了不同操作条件下反应器混合时间的变化规律. 采用pH 电极在位监测[H +]的方法实验测定混合时间. 模拟结果与实验测定值之间的误差随反应器容积增大而逐渐减小,对容积为25 m 3的反应器误差小于11.6%. 关键词:搅拌生物反应器;混合时间;计算流体力学;数值模拟中图分类号:TQ018 文献标识码:A 文章编号:1009−606X(2005)02−0131−041 前 言 尽管目前已开发出许多新型的生物反应器,但机械搅拌式生物反应器因其搅拌桨结构的多样性、混合与传质方面的高弹性而具有通用性强、操作范围宽等特点,在食品发酵、生物制药等生物技术行业中的应用仍占统治地位,而且这种趋势在近期不会改变[1]. 反应器的混合时间是衡量其混合传质性能的重要指标,主要受反应器的结构与操作条件的影响[2],对反应器的设计放大及操作优化具有重要的参考价值.传统的混合时间测量方法主要有脱色法[3]、光学法[4]及电导法[5,6]等,这些测量方法都存在着一定的局限性,应用于大型生物反应器混合传质研究往往成本高、精度低、操作困难. 本工作用计算流体力学(Computational Fluid Dynamics ,简称CFD)技术对0.05, 1.0, 25.0 m 3三种规模的机械搅拌式生物反应器的混合行为进行数值模拟,研究在不同操作条件下混合时间的变化规律,并将模拟结果与实测结果进行比较,验证CFD 模拟技术用于机械搅拌生物反应器混合性能研究的可行性,以期为工程应用建立基础.2 实 验 2.1 实验设备 实验设备是常用的机械搅拌式通风发酵罐,又称标准罐,如图1所示,主要由椭圆封头、挡板、标准六平叶圆盘涡轮搅拌桨(Rushton 型)构成. 挡板与器壁间空隙取反应器内径的1%,具体尺寸见表1.位点A 及B 分别为测定混合时间时的加料点和监测点,加料点A 高度在上搅拌桨的上边缘位置,监测点B 高度约在下两个搅拌桨高度的中点处,两位点均在相邻两挡板之间的中点且离器壁0.1 m 左右处. 反应器内图1 机械搅拌生物反应器几何结构示意图Fig.1 Sketch of stirred biochemical reactor 表1 实验设备主要尺寸 Table 1 Main dimensions of experimental apparatus料液装填系数为78%. 2.2 混合时间测量方法 实验在25℃下进行,用HCl 溶液作为酸性示踪剂,在加料点A 处瞬间注入,同时通过安装在监测点B 处的pH 电极和与之相联的计算机记录液体pH 值的变化,从Tank dataTank 1 Tank 2 Tank 3 Liquid volume, V (m ) 0.05 1.0 25.0 Liquid height, H L (m) 0.5 1.42 4.0 Tank diameter, D T (m) 0.3 0.8 2.4 Number of baffles, N B 3 4 4 Number of impellers, N I 2 3 3 Baffle width, W (m) 0.03 0.06 0.24 Baffle depth, H B (m) 0.425 1.3 4.03 Impeller diameter, D I (m)0.125 0.28 0.75 Space between impellers, S I (m) 0.25 0.56 1.4 Bottom-impeller elevation, S B (m)0.025−0.165而反映液体中[H +]浓度的变化. 典型的[H +]变化过程如图2所示[7]. 一般混合过程中示踪剂浓度变化曲线的振幅随时间指数递减,而其频率与时间无关,混合时间可以从曲线上读出. 混合时间t m 是指示踪剂注入反应器至达到一定混匀程度的时间. 混匀程度的定义为0.5100%C Cm C ∝∝−∆=×. 通常认为m 达到95%时,流体即混合均匀,此时的混合时间常用t 95来表示.3 CFD数值模拟 3.1 基本原理 3.1.1 基本数学模型在工业生产常用的操作条件下,生物反应器内液体湍流运动可由时均方程组来描述,其流动守恒方程组由张量表示的通用形式描述如下:()()()k k k kv S t x x x φφφρφρφΓ∂∂∂∂+=+∂∂∂∂, 式中,φ表示质量组分、速度、压力、湍流动能、湍流耗散等变量,S φ为源项,Γφ为湍流扩散,在计算示踪剂浓度场时,Γφ=ρD φ+µT /σφ, D φ为示踪剂分子扩散系数,µT 为湍流动力粘度,其值取于速度场湍流k −ε双方程模型,σφ为湍流Prandtl 数. 3.1.2 混合时间模拟生物反应器中物料在混合过程中的浓度分布随时间变化的非稳态过程通常有两种数值计算方法,一种是联立所有方程进行求解,另一种是假设速度场稳定,单独进行流场计算. 本研究的混合时间计算采用后一种方法. 具体模拟分两步进行:第一步,用单物质模型计算稳态流场,模拟的单物质是水;第二步,在上述稳态流场的基础上引入双物质模型(如水和示踪剂)进行非稳态计算. 在加料点设置初始示踪剂的注入量,在计算过程中求解监测点示踪剂的浓度变化,当混匀程度达到95%时,即认为达到了完全混合. 这段时间就称为搅拌反应器的混合时间,记为t 95. 3.2 数值计算 3.2.1 几何模型的构建及网格划分对于带有六平叶圆盘涡轮桨及挡板的搅拌生物反应器,由于其结构的对称性,故可以用通过轴心的垂直截面将其分成对称的若干部分. 如1.0 m 3机械搅拌发酵罐就可以对称地分成两部分,只对其中一部分进行几何体构建及网格划分. 机械搅拌生物反应器中搅拌桨与挡板之间相对移动的动界面可采用滑移网格法处理. 这种方法将计算区域分为两部分,如图3所示,一部分包含了运动的搅拌桨叶,另一部分包含反应器的其他静止部分,两部分网格之间要求彼此独立,两者之间的物质、动量传递通过定义接触边界面的粘联来实现.网格划分采用在正交圆柱坐标下的结构化网格,同时采用分块网格技术,在反应器中心部位网格线较密、外围较疏,这也是由流动的特点决定的. 这样可以减少假扩散,对解的收敛和求解速度都十分有利. 其对应的3种反应器(0.05, 1.0, 25.0 m 3)几何体划分的网格总数分别为158268, 215712和246996,网格的划分对求解已经达到了无关性标准. 1.0 m 3反应器具体网格空间划分见图3所示.设定流体在反应器壁处的流动速度为0,即无滑移边界条件;假定流体表面与大气无摩擦,在反应器的液体表面采用所谓的自由滑移边界条件;在轮轴处采用无移动及轴对称设定. 3.2.3 数值求解整个方程组的求解通过流体工程软件CFX −4.4完(a)(b)第2期 洪厚胜等:搅拌生物反应器混合特性的数值模拟与实验研究 133 成,通过有限体积法将微分方程组离散成差分代数方程组后,各变量差分方程用沿主流方向逐线扫描的低松弛迭代求解. 压力−速度耦合求解采用SIMPLEC 算法.4 结果与讨论 对于大多数生化反应,物料的混匀效果和混合速率决定着反应效率和生产成本,对生物反应器的混合特性的研究具有现实意义. 在搅拌生物反应器中,物料的混合作用主要由主体流动、湍流及分子扩散这3种机理的协同作用引起. 图4所示是0.05 m 3反应器在230 r/min 的搅拌转速下不同时刻示踪剂浓度值的分布. 从图中可以很直观地观察到示踪剂的混合过程. 图5为不同体积搅拌生物反应器的混合时间模拟结果与实验结果的比较. 从图中可以看出,模拟结果在趋势上与实验结果有很好的一致性,随着搅拌转速的提高,反应器混合时间逐渐变小. 从图也清楚地看出数值模拟得到的搅拌混合时间均比实验验证值要大,产生此误差的原因有很多,主要是由采用的计算方法所引起的. 因为这种方法计算首先要假设流场稳定,而实际搅拌反应器内流场并不是稳定不变的,而是呈无规则变化的非稳态过程,但流场的不稳定可以促进传质的进行,从而使混合时间减小. 就这一点来看,本研究的模拟结果与Schmalzriedt 等[8]、Bujalski 等[9]所描述的情况基本一致. 混合时间的模拟与实验结果的误差比较见表2.图5 混合时间的模拟与实验结果比较Fig.5 Comparison between simulative and experimental mixing timest =20 s10020030040020406080100120140t 95 (s )R (r/min)6080100120140160100110120130140150160170R (r/min)14016018020022024040455055606570758085R (r/min)134 过 程 工 程 学 报 第5卷表2 混合时间的模拟与实验误差比较 Table 2 Comparison of deviations between simulative and experimental mixing timesTank 1 Tank 2 Tank 3 .50 230 400 150170 190 210 230 70 90 110 130 150 Simulation value (s) 137.5 27.9 18.0 81.9 72.2 64.6 57.2 51.1 167.4 151.1 135.3 118.3 105.0 Experiment value (s) 104.0 17.0 11.0 73.0 60.0 53.0 49.0 43.0 165.0 140.0 129.0 106.0 102.0 Deviation (%)32.264.1 63.612.220.321.916.7 18.8 1.5 7.94.911.6 2.9分析比较图5和表2所给数据还可以得知,它们的误差分别在64.1%, 21.9%及11.6%以下. 随着搅拌生物反应器容积的增大,数值模拟与实验结果之间的误差逐渐变小,模拟的可靠性逐渐增大. 对容积为25 m 3的工业规模的生物反应器,模拟与验证之间的误差值小于11.6%,完全符合当前数值模拟的工程应用要求. 产生这种现象可能是小反应器中流场的无规则周期性振荡更甚,偏离本研究数值计算的第一步流场稳定的假设条件更远所致.5 结 论 以流体工程软件CFX −4.4为工具,对不同规模的机械搅拌生物反应器的混合特性进行了数值模拟,建立了最大容积为25 m 3的工业规模冷模实验装置和混合时间测定方法,并对模拟结果进行了验证. 研究结果表明,本工作建立的数学模型及采用的算法是可行的;CFD 技术可用于机械搅拌式生物反应器混合传质的基础研究和反应器的优化设计及工程放大的应用研究.符号表:S L两搅拌桨间距 (m)W挡板宽度 (m)t 时间 (s) x k 坐标位置 (m) t m 混合时间 (s) ρ 流体密度 (kg/m 3)t 95 混匀程度95%的混合时间 (s) ∆C信号波峰值波动范围 (mol/L) v 流体质点的速度 (m/s) µT 湍流动力粘度 [kg/(m ⋅s)] V反应器体积 (m 3)σφ湍流Prandtl 数参考文献:[1] 赵学明. 搅拌生物反应器的结构模型、放大及搅拌器改型 [J]. 化学反应工程与工艺, 1996, 12(1): 80−90.[2] 韦朝海,谢波,吴超飞,等. 三重环流生物流化床反应器的混合特性 [J]. 化学反应工程与工艺, 1999, 15(2): 174−178.[3] 武斌,戴干策. 搅拌槽内粘稠物系的混合过程 [J]. 高校化学工程学报, 1997, 11(2): 143−149.[4] 林猛流,王英琛,施力田. 激光法测定搅拌器的混合特性 [J]. 化学工程, 1986, 14(3): 52−56.[5] Nienow A W. On Impeller Circulation and Mixing Effectiveness inthe Turbulent Flow Regime [J]. Chem. Eng. Sci., 1997, 52(15): 2557−2565.[6] Manna L. Comparison between Physical and Chemical Methods forthe Measurement of Mixing Times [J]. Chem. Eng. J., 1997, 67(3): 167−173.[7] 戚以政,汪叔雄. 生化反应动力学与反应器,第二版 [M]. 北京:化学工业出版社, 1999. 391−392.[8] Schmalzriedt S, Reuss M. Application of Computational FluidDynamics to Simulations of Mixing and Biotechnical Conversion Processes in Stirred T ank Bioreactors [J]. Recents Progres en Genie des Procedes, 1997, 11(51): 171−178.[9] Bujalski W, Jaworski Z, Nienow A W. CFD Study of Homogenizationwith Dual Rushton Turbines Comparison with Experimental Results: Part II: The Multiple Reference Frame [J]. Chem. Eng. Res. Des., 2002, 80(A1): 97−104.Numerical Simulation and Experimental Study on Mixing Characteristics of Stirred BioreactorHONG Hou-sheng, ZHANG Qing-wen, WAN Hong-gui, OUYANG Ping-kai(College of Pharmacy and Life Science, Nanjing University of Technology, Nanjing, Jiangsu 210009, China )Abstract: By commercial CFD package CFX-4.4, mixing characteristics of stirred bioreactor were simulated and the mixing time variation under various operation conditions was investigated. The liquid mixing time was measured by means of detecting the concentration variety of [H +] with a pH probe. The deviation between simulation and experiment becomes smaller as the bioreactor volume is increased, and the error for 25 m 3 bioreactor is less than 11.6%.Key words: stirred bioreactor; mixing time; computational fluid dynamics; numerical simulationC ∝ 理想完全混匀浓度 (mol/L) m混匀程度 D I 搅拌桨直径 (m) N B 挡板个数 D T 反应器内径 (m) N L 搅拌桨个数 H B 挡板深度 (m) R 搅拌转速 (r/min)H L液位高度 (m)S B下搅拌桨距筒体底间距 (m)。
理想混合连续搅拌釜式反应器(CSTR)
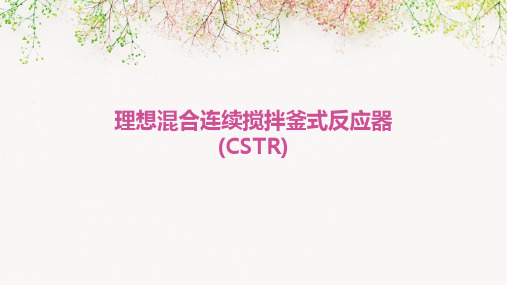
理想混合状态
物料在反应器内达到完全混合,不存在浓度和温度 的梯度分布。
反应器内各点的物料性质(如浓度、温度等)完全 相同,且随时间保持不变。
在理想混合状态下,反应器的性能达到最优,反应 效率和产物质量得到保证。
03
CSTR反应器的数学模型
物料平衡方程
进入反应器的物料流量与离开 反应器的物料流量相等,即输 入等于输出。
用于连续加入反应物和排出产物,实现连续化生产 。
工作流程
01
02
03
04
物料进入
反应物通过进料口连续加入反 应器内。
充分混合
在搅拌装置的作用下,物料在 反应器内充分混合,达到浓度 和温度的均匀分布。
反应进行
在适宜的反应条件下,物料在 反应器内进行化学反应。
产物排出
反应完成后,产物通过出料口 连续排出反应器。
100%
平均停留时间
表示物料在反应器内的平均停留 时间,影响反应器的生产能力和 产品质量。
80%
停留时间分布曲线
通过实验测定,可直观反映反应 器内物料的停留时间分布情况。
转化率与选择性
转化率
表示原料在反应器内转化为产 品的程度,是衡量反应器性能 的重要指标。
选择性
表示在给定转化率下,生成目 标产物的能力,反映反应器的 选择性能。
THANK YOU
感谢聆听
缺点与挑战
能耗较高
连续搅拌过程需要消耗大量能量,导致CSTR反应器的能耗相对较 高。
设备复杂度高
CSTR反应器结构复杂,涉及搅拌、传热、传质等多个过程,设备 设计、制造和维护难度较大。
放大效应
在将实验室规模的CSTR反应器放大至工业生产规模时,可能会遇到 放大效应问题,影响反应器的性能和产物质量。
化学反应器的设计及工艺优化

化学反应器的设计及工艺优化化学反应器是生产化学品和药品的重要装置,其设计和工艺优化对生产效率和质量具有重要影响。
本文将以某化工企业制备二氯化钛为例,探讨化学反应器的设计及工艺优化。
一、反应器设计1.1 物料选择在选择反应器物料时,应考虑其耐腐蚀性、导热性以及承受压力等因素。
针对本工艺,应选择耐腐蚀性好的材料,如不锈钢、陶瓷等。
1.2 容积计算容积是反应器设计中的一个重要参数,它决定了反应器的生产能力和成本效益。
在计算反应器容积时,需要考虑反应物的摩尔质量、反应的摩尔比、反应速率以及反应温度等因素,并根据化学平衡常数计算出反应物的理论输出量,最终得到反应器所需容积。
1.3 设计压力和温度反应器设计中还需考虑到设计压力和温度等参数。
工艺要求反应温度为150℃,反应压力为1.5 Mpa。
因此,反应器应根据这些参数来选择合适的设计参数。
二、工艺优化2.1 温度控制对于反应温度的控制,应根据反应的特性来确定加热方式、加热时间和加热速率等参数。
针对本工艺,可以采用内外循环水浴加热的方式来控制反应温度。
同时,可以利用反应器配备的温度控制装置和反应监测装置来实时监测反应温度,确保反应的稳定和可控。
2.2 搅拌控制搅拌是反应过程中的另一个关键参数,它直接影响到反应物的混合和传质。
在设计反应器搅拌时,需要考虑到反应物的黏度、流动性以及反应的速率等因素,以确保搅拌强度适宜。
对于本工艺,可以采用高速搅拌器来保证反应物的混合均匀。
2.3 底部排料底部排料也是反应器设计的一个重要环节,它直接影响到反应物的排出和产品收集的效率。
在设计反应器底部排料时,需要考虑到反应物的黏度、密度、流动性等因素,以确保排料顺畅。
针对本工艺,可以采用在反应器底部安装套筒的方式来实现底部排料。
2.4 生产效率优化除了反应器本身的优化,还需考虑到整个生产线的优化。
比如,在改进产品收集方式、优化原材料贮存方式、改善运输和储存条件等方面,都可以带来生产效率的提升和质量的保障。
反应器放大设计课件

反应器放大设计
12
常用的几何相似放大准则
着眼的过程
放大过程中需保持恒等的量(准则)
1. 均一系混合速度
(Qd/V)0.33 Pv0.16(与N0.81d0.32等效)
2. 分散相混合速度
Pv0.5~1.1
3. 对应的流速一定
Nd
4. 同一液滴直径
N3d2(与Pv等效)
➢ 取不同的放大准则可使过程能耗相差很大,必须予以重视。
➢ 保持Qd/V 恒定(即翻转次数恒定)的放大法是最耗能的放大法。
而保持Re恒定,一般不能重现过程结果。
➢ 实用的放大法是保持Pv恒定或Nd恒定,或取二者之间。
反应器放大设计
16
反应器传热能力变化(湍流)
槽径 放大 倍数
3 5 10 r
N3d2恒定
5. 使液滴分散的最小转速 N d1.1
6. 相际传质速度
N3 d2
7. 固液悬浮
Nd或N4 d3
8. 溶解速度
(Qd/V)0.24 Pv0.11或N3 d2
反应器放大设计
13
问题的提出:
• 反应器选型与设计强烈依赖经验和实 验,对其的优劣很难用理论预测。
• 逐级放大来以达到搅拌设备被要求的 传质、传热和混合,周期长、耗费大。
• 对釜的长径比、桨径/槽径比、叶片宽/槽径 比、叶片截面形状对NP、NC的影响,以及夹 套和内冷管的传热作了系统的研究。
反应器放大设计
29
混合参数的冷模研究
叶片截面 d/D
板截面 0.5
园角矩形 0.5
椭园
0.5
扁园
0.5
三叶后掠式叶轮的特性参数
b/D
生物反应器内搅拌器的优化设计
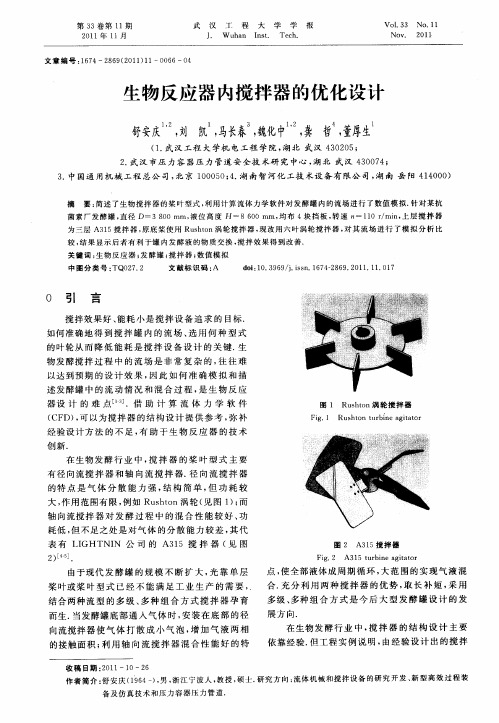
0 引 言
搅 拌效 果好 、 能耗 小 是搅 拌设 备 追 求 的 目标 . 如何 准确 地得 到搅 拌罐 内 的 流场 、 用 何 种 型 式 选
2) ]
.
图 2 A3 5搅 拌 器 l
Fi 2 A 31 u bne a ia o g. t r i g t t r 5
由于现代 发 酵 罐 的规 模 不 断 扩 大 , 靠 单 层 光 桨 叶或 桨 叶 型 式 已 经 不 能 满 足 工业 生 产 的 需 要 ,
舒 安 庆 , : 物 反 应 器 内搅 拌 器 的 优 化 设 计 等 生
器 往往难 以处 于最 佳 工 作 状 态 . 如 选 用 的 电机 例
MR F方法 是基 于稳 态 流 场 的计 算 方法 , 它是 采 用旋 转 坐标 系 和静 止坐 标 系两 个参 考 系分别 进 行计 算 , 由于 两个 参考 系没有 重 叠 的 区域 , 故不 需 要 进行 内外迭 代 , 而 减 少 了计 算成 本 . 从 因此本 文 选 用 MR F方法进 行模 拟 , 计算 区域 分 为两个 区 将
3 中国通用机械 工程 总公 司, . 北京 1 0 5 ;。 0 0 0 4 湖南 智河化 工技 术设 备 有限公 司, 湖南 岳 阳 4 4 0 ) 1 0 0
摘 要 : 述 了生 物 搅 拌 器 的 桨 叶 型 式 , 用 计 算 流 体 力 学 软 件 对 发 酵罐 内 的流 场 进 行 了数 值 模 拟 . 对 某 抗 简 利 针
侧进式搅拌反应器内流场的数值模拟

侧进 式搅 拌反 应器 内流场 的数 值模 拟
张 林 进 , 陈 功 国 , 叶 旭 初
( 京工 业 大学材 料科 学与 工程 学 院 材料 化 学 工程 国家重 点 实验 室。 江 苏 南京 20 0 ) 南 10 9
摘要:采用 汁靠流体力学 ( F C D)技术对某钢铁』 烟气脱硫吸收塔底部浆液池的侧进式搅 拌流场进行 了数 【 ’ 模拟,
1几何模型和模拟方法
1 . 何模型 I几
几何模 型是 按照某钢铁厂 烟气脱硫吸 收塔底 部浆液池 的实 际尺 寸建立 的,浆液池及搅拌 桨结构如 图 1
所 示 。浆液池底 部为平 底 ,直径 I 8 m,液位高度为 5 m,在距 离底面 l 5m 的平 面上周 向分布 5台侧进 式 - 2
搅 拌器 ,其 中 1 5 搅 拌器 的周 向分布角为 9 。 与 拌 0 ,其余相邻搅拌 器之间 的周 向分布角均为 6 . 。循环浆 7。 5
液 进 几位于 l 与 5 搅 拌器之 间,中心高度为 1 ≠ } } } . m,浆液 出几位于 2 搅 拌器附近 ,中心高度为 O5 0 ≠ } . m,在 2
.
迅速 增 加 , 当转 速 人于 等 _ 2 / n州 ,该处 速 率接 近 或 达到 ・r 上 速 率 的最 人 位 ,有 利 避 免 l心 区底 部 的 :10 r mi I 心线 J l I 固相 沉 积 。随着 芹偏 加度 的增 人 ,-心 漩 涡 区域 外 扩 ,t心 线 上底 部 的速 牢 有 所 减 小 .而 相 邻 桨 叶之 问 下 部 的速 率 I 一 I 一 略有 增 _ 。下偏 角 度 的增 大 ,使得 卡邻 桨 Ⅱ之 下部 的速 率 略 有减 小 ,而 过 大的 下 偏 角度 使 得搅 拌 桨 丰作 用 无法 『 J I J H 1 直 接 作用 到 支撑 村 内部 , 导致 ・I 上 底 部的 速 减 小 。 『 线 . 年
- 1、下载文档前请自行甄别文档内容的完整性,平台不提供额外的编辑、内容补充、找答案等附加服务。
- 2、"仅部分预览"的文档,不可在线预览部分如存在完整性等问题,可反馈申请退款(可完整预览的文档不适用该条件!)。
- 3、如文档侵犯您的权益,请联系客服反馈,我们会尽快为您处理(人工客服工作时间:9:00-18:30)。
搅拌式反应器的模拟与优化设计摘要在综述了计算流体力学(CFD)技术在搅拌式反应器中的研究进展的基础上,着重讨论了搅拌式反应器中流场的模拟方法, 包括“黑箱”模型法、内外迭代法、多重参考系法和滑移网格法, 并指出了CFD技术的发展方向。
在此基础上, 对反应器内流场的数学模型进行了介绍与评价。
最后提出应用人工神经网络技术与遗传算法, 优化生物反应的工艺操作条件, 并结合CFD技术, 实现生物反应器的结构优化, 从而达到对生物反应系统整体优化的目的, 以指导实验与工业生产。
关键词计算流体力学,搅拌式反应器,数值模拟,人工神经网络,优化设计Simulation and optimization design ofStirred reactorAbstract:Base on the overview of computational fluid dynamics (CFD) technology in the stirred reactor research,we focused on the mixing reactor simulation of the flow field, including "black box" model of law, internal and external iteration, multiple reference frame method and the sliding mesh method, and pointed out the direction of development of CFD technology. On these basis,we described and evaluated the reactor flow mathematical model.We concludes with the application of artificial neural network and genetic algorithm to optimize the process operating conditions, biological response, and results combined CFD technology to achieve optimization of the structure of the bioreactor, so as to achieve overall optimization of the bioreactor system aims to guide experiments and industrial production.Keyword: computational fluid dynamics, stirred reactor, numerical simulation, artificial neural networks, optimization第1章前言搅拌式反应器( Stirred Tank Reactor, STR)因其结构灵活、操作方式多样等特点, 广泛应用于生物化工、冶金、食品、医药及环境等领域。
搅拌的目的一般分为液液混合、气泡分散、颗粒悬浮、强化传热以及加速化学反应等。
根据不同的搅拌目的,所确定的最佳反应器几何结构和搅拌桨型式也会有所不同。
工业中最常用的带挡板搅拌式反应器(Baf-fled Stirred Tank Reactor, BSTR) , 结构如图1所示。
图1搅拌式反应器结构特征尺寸尽管搅拌式反应器的结构比较简单, 但反应器内的流体流动和混合过程却很复杂。
由于反应器的设计和放大主要依靠经验方法, 设计周期长、偏差大等问题带来了巨大的经济损失。
如何准确地描述和模拟反应器内的混合过程及流动状况, 为其优化设计和放大提供理论指导, 是生物反应器技术研究的一个重要发展方向[1]。
20世纪70年代以来,随着计算流体力学( Computational Fluid Dynamics,CFD)技术的发展,利用数值模拟的方法来获得搅拌式反应器内流动和混合的信息已经成为现实。
该数值方法是通过建立各种条件下的基本守恒方程(包括质量、动量以及能量方程等),结合初始条件、边界条件和数值计算方法,实现模拟真实过程中各种场如流场、温度场、浓度场等的分布, 以达到对过程的设计、优化、控制和放大的目的。
同时, 伴随着PIV粒子成像测速技术的发展, P IV实验所获得的大量数据, 为搅拌式反应器内的数值模拟提供了真实可靠的依据和检验标准。
可以说,CFD技术将对生物反应器的开发带来革命性的变化[2]。
第2章模拟方法2.1 搅拌式反应器内CFD的发展趋势随着计算机计算能力的不断提高, 以及在湍流模型和计算方法等方面的不断改善, 尤其是大型通用CFD软件的日趋成熟。
CFD方法用于研究搅拌式反应器内的流动显示出强大的生命力, 越来越多的研究者开始关注并涉足CFD领域。
近年来, 在研究搅拌式反应器内的流动方面, CFD 的最新进展主要体现在以下几方面。
2.1.1 从结构化网格到非结构化网格在CFD研究中, 对几何体进行建模与网格划分的前处理过程是很重要的。
网格划分将直接影响到以后的求解计算过程, 高质量的网格容易收敛,从而减少机时, 提高计算精度。
随着CFD研究的不断深入, 需要解决的问题不再局限于简单的几何构型, 需要对各种复杂的结构进行研究。
然而要对复杂几何构型进行结构化网格划分非常困难, 有时甚至是不可能的。
鉴于此,可以采用简化构型的方法使其可以适应结构化网格, 这显然不是令人满意的方法。
结构化网格在很大程度上限制了CFD在工业中的应用。
近年来人们逐渐重视研究另一类网格———非结构化网格。
非结构化网格的基本思想基于如下假设: 四面体是三维空间最简单的形状, 任何空间区域都可以被四面体单元所填满, 即任何空间区域都可以被以四面体为单元的网格所划分。
由于非结构网格舍去了结构化网格节点的结构性限制, 易于控制网格单元的大小、形状及网格点的位置, 因此比结构化网格具有更大的灵活性, 对复杂外形的适应能力非常强。
正因为如此, 非结构网格技术在20世纪80年代末、90年代初得到了迅速的发展。
非结构网格在汽车、航天等领域的应用已经比较广泛, 在化工方面尤其是搅拌式反应器方面的应用还很少。
1998 年Naude[3]利用FLUENT软件使用非结构化网格计算了一种轴流式搅拌桨(LUMPPLB)的三维流场, 并将计算结果和实验数据进行了比较。
计算采用了多重参考系(MRF) 法, 由于MRF法是稳态计算, 计算中考虑了三种不同的桨叶和挡板的相对位置, 对三个计算结果取平均值后再与实验数据进行比较。
2.1.2 大涡模拟和直接数值模拟对湍流问题最真实的描述是直接求解N-S方程, 即直接数值模拟(DNS) 。
但是受到计算机计算能力的限制, 现在还只能计算低雷诺数和简单几何条件的问题, 到解决工程实际问题还有距离。
大涡模拟方法最早是由气象学家Smagornky[4]在1963年提出的, 所研究的问题是全球天气预报问题。
后来这种方法被应用于解决工程问题。
大涡模拟的基本思想是包括脉动运动在内的湍流瞬时运动通过某种滤波方法分解成大尺度运动和小尺度运动两部分。
大尺度量通过数值求解运动微分方程直接计算出来; 小尺度运动对大尺度运动的影响将在运动方程中表现为类似雷诺应力一样的应力项, 称之为亚格子雷诺应力。
将通过建立模型来模拟, 成为亚格子尺度模型( Subgrid Scale Mode) 。
从一定意义上讲, 大涡模拟是介于直接数值模拟与一般模式理论之间的折中物。
2.1.3 多相流动的数值模拟对搅拌式反应器内多相体系流动场的研究还很缺乏, 但在近几年的发展却非常迅速。
Morud[5]计算了Rushton涡轮的气液两相流动场, 并将计算的气相速度与LDA测量结果进行了比较, 桨叶区径向速度结果吻合较好, 轴向速度计算结果偏高。
Friberg[6]将Morud的计算从二维扩展到三维, 在三个方向均得到了较好的计算结果, 而且在计算中还捕捉到了位于叶轮后方的气穴。
最近, Wu采用欧拉- 拉格朗日法计算了双层涡轮桨搅拌槽内的气液两相流动, 其计算结果虽然没有与实验数据进行定量比较, 但该方法却是令人鼓舞的。
2.2 搅拌式反应器的模拟方法CFD技术的每一次发展都可以从模拟搅拌式反应器的应用中体现出来。
搅拌式反应器内的流场是非常复杂的, 从数值模拟的观点来看, 模拟搅拌式反应器所面临的挑战是液面、槽壁、挡板、搅拌桨和搅拌轴所围成的流动域是随时间变化的, 这是与化工过程中其它反应器的一个差别。
为了解决旋转的桨叶与静止的挡板之间的相互作用, 许多研究者提出了各自不同的解决方法。
这个过程就是CFD技术不断发展完善的过程。
这些方法主要有:“黑箱”模型法、内外迭代法、多重参考系法和滑动网格法等。
2.2.1“黑箱”模型法“黑箱”模型法( Impeller Boundary Condition,IBC), 又称搅拌桨边界条件法, 作为最早的模拟搅拌式反应器的方法, 它是将叶轮扫过的区域从计算域中扣除, 而叶轮产生的搅拌流动场以实验数据作为边界条件代替。
1982 年Harvery[7]第一次采用这种方法计算了涡轮搅拌桨的二维流动场, 并与实验数据作了对比, 取得了一定成功。
可以看出, 这种基于实验的数值模拟方法, 其局限性在于: 边界条件的确定一般离不开实验数据; 一套桨叶区域边界条件只能用于与实验条件几何相似的体系。
受这些条件的限制, CFD 仍然不能成为独立的设计工具。
2.2.2 内外迭代法图2 内外迭代法Σ1—内域Σ2—外域1994 年B rucato[8]提出了“内外迭代法”( Inner - OuterMethod, IO)。
它是将计算域分成内、外两个重叠的区域, 如图2所示。
内域Σ1包括旋转的桨叶, 外域Σ2包括静止的挡板, 内域的计算在以搅拌桨速度旋转的参考系内进行, 外域的计算在静止坐标系下进行, 通过在两个区域间的交替迭代计算最终获得整个计算域的收敛结果。
内外迭代法比起“黑箱”模型法有了很大的进步, 不再需要实验数据, 实现了搅拌反应器流动场的整体模拟。
通过对某些搅拌桨流动场的计算, 证明该方法完全可以用于搅拌式反应器流动场的数值模拟。
但计算时仍然需要试差迭代, 收敛速度慢, 所以未能被商业软件采用, 在一定程度上限制了该方法的普及应用。
2.2.3 多重参考系法1994年Luo[9]提出了一种稳态流动场的计算方法, 它采用两个参考系进行计算, 桨叶所在区域是以桨叶速度旋转的参考系, 其它区域使用静止参考系, 用来计算叶轮区以外的流动场。