第七章 热压烧结2
《热压烧结》 (2)幻灯片

在不同种粉末之间比较颗粒系统的烧结活性时,不要忘记单 个颗粒的烧结活性即粉末晶体的自扩散性.综合考虑这两个因 素来确定烧结活性,有一个判据是值得注意的。
存着较多的空隙,如图7.1(a)。
图7.1 不同烧结阶段晶粒排列过程示意图
随着烧结温度的提高和时间的延长,开场产生颗粒间的键合和重 排过程,这时粒子因重排而相互靠拢,大空隙逐渐消失,气孔的总 体积迅速减少,但颗粒间仍以点接触为主,总外表积并没减小。
烧结
中期开场有明显的传质过程。颗粒间由点接触逐渐扩大为面 接触,粒界面积增加,固-气外表积相应减少,但气孔仍然 是联通的,此阶段晶界移动比较容易。在外表能减少的推 动力下,相对密度迅速增大,粉粒重排、晶界滑移引起的 局部碎裂或塑性流动传质,物质通过不同的扩散途径向颗 粒间的颈部和气孔部位填空,使颈部渐渐长大,并逐步减 少气孔所占的体积,细小的颗粒之间开场逐渐形成晶界, 并不断扩大晶界的面积,使坯体变得致密化,如图7.1(b) (c)。
烧结的主要目的是把颗粒系统烧结成为一个致密的晶体, 是向低能状态过渡。因此烧结前,颗粒系统具有的过剩的 外表能越高.这个过渡过程就越容易,它的烧结活性就越 大。
〔1〕本征过剩外表能驱 动力
可以用下述简单方法估计本征过剩外表能驱动力数量 级。假定烧结前粉末系统的外表能为Ep.烧结成一个致 密的立方体后的外表能为Ed,忽略形成晶界能量的消耗, 那么本征驱动力为:
1 固体粉末烧结的过程和特点 2 固体粉末烧结的本征热力学驱动力 3 固相烧结动力学 4 热压过程的根本规律
1 固体粉末烧结的过程和特点
热压烧结
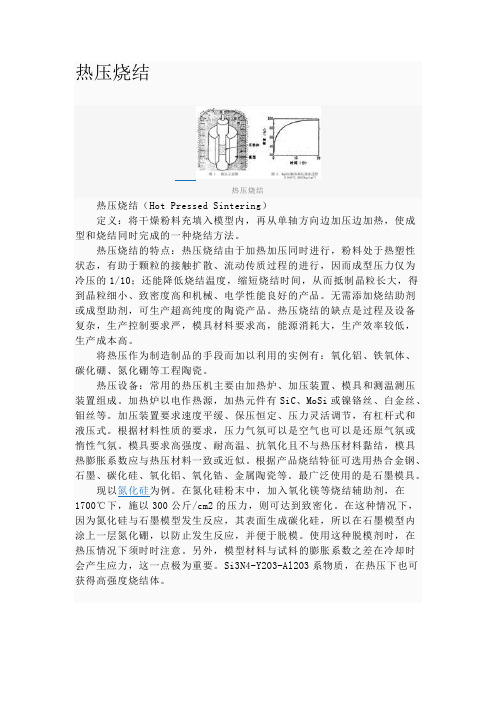
热压烧结热压烧结热压烧结(Hot Pressed Sintering)定义:将干燥粉料充填入模型内,再从单轴方向边加压边加热,使成型和烧结同时完成的一种烧结方法。
热压烧结的特点:热压烧结由于加热加压同时进行,粉料处于热塑性状态,有助于颗粒的接触扩散、流动传质过程的进行,因而成型压力仅为冷压的1/10;还能降低烧结温度,缩短烧结时间,从而抵制晶粒长大,得到晶粒细小、致密度高和机械、电学性能良好的产品。
无需添加烧结助剂或成型助剂,可生产超高纯度的陶瓷产品。
热压烧结的缺点是过程及设备复杂,生产控制要求严,模具材料要求高,能源消耗大,生产效率较低,生产成本高。
将热压作为制造制品的手段而加以利用的实例有:氧化铝、铁氧体、碳化硼、氮化硼等工程陶瓷。
热压设备:常用的热压机主要由加热炉、加压装置、模具和测温测压装置组成。
加热炉以电作热源,加热元件有SiC、MoSi或镍铬丝、白金丝、钼丝等。
加压装置要求速度平缓、保压恒定、压力灵活调节,有杠杆式和液压式。
根据材料性质的要求,压力气氛可以是空气也可以是还原气氛或惰性气氛。
模具要求高强度、耐高温、抗氧化且不与热压材料黏结,模具热膨胀系数应与热压材料一致或近似。
根据产品烧结特征可选用热合金钢、石墨、碳化硅、氧化铝、氧化锆、金属陶瓷等。
最广泛使用的是石墨模具。
现以氮化硅为例。
在氮化硅粉末中,加入氧化镁等烧结辅助剂,在1700℃下,施以300公斤/cm2的压力,则可达到致密化。
在这种情况下,因为氮化硅与石墨模型发生反应,其表面生成碳化硅,所以在石墨模型内涂上一层氮化硼,以防止发生反应,并便于脱模。
使用这种脱模剂时,在热压情况下须时时注意。
另外,模型材料与试料的膨胀系数之差在冷却时会产生应力,这一点极为重要。
Si3N4-Y2O3-Al2O3系物质,在热压下也可获得高强度烧结体。
材料合成技术与方法9-热压烧结

其中γ sv为固-气表面能(J/m2 )
Wm为晶体材料摩尔质量(g/mol)
S
为粉末比表面积(cm
p
2
/g)
d为致密固体密度(g/cm 3 )
粒度
粒子越细, 本征驱动力 越大,越易 烧结
材料合成技术与方法
(1)本征剩余表面能驱动力
单个颗粒烧结活性, 即粉末晶体的自扩散性
Dv (2a)3
≈1
Dv为体积扩散系数(cm2 /s) 2a为粉末粒度(µm)
出,对于不同物料和烧结条件,这 些过程并不是并重的,往往是某一 种或几种机理起主导作用。当条件
改变时可能取决于另一种机理。
材料合成技术与方法
对于一个不受应力的晶体,其空位浓度 Co是取决于温度T和形成空位所需的能量△Gf
C0
=
n0 N
=
exp(−
∆G f kT
)
6
材料合成技术与方法
若质点(原子或离子)的直径为δ,并近似地令
空位体积为δ3,在颈部区域每形成一个空位时,
毛细孔引力所做的功△W=γδ3/ρ。
故在颈部表面形成一个空位所需的能量应为
1.随烧结温度的升 高,比电导和抗拉 强度增加。
2.曲线表明,在颗 粒空隙被填充之前 (即气孔率显著下降 以前),颗粒接触处 就已产生某种键 合,使得电子可以 沿着键合的地方传 递,故比电导和抗 拉强度增大。
拉力(kg/cm3) (g/cm2)
密 度
温度(°C) 图5 烧结温度对烧结体性质的影响
l一比电导 2一拉力 3一密度
结果与讨论:
3.温度继续升高, 物质开始向空隙传 递,密度增大。当 密度达到理论密度 的90~95%后,其 增加速度显著减 小,且常规条件下 很难达到完全致 密。说明坯体中的 空隙(气孔)完全排 除是很难的。
热压烧结原理

热压烧结原理热压烧结是一种常见的粉末冶金工艺,广泛应用于陶瓷、金属和塑料等材料的制备过程中。
它通过高温和高压的作用,将粉末颗粒紧密结合,形成致密的块状材料。
本文将介绍热压烧结的原理及其应用。
首先,热压烧结的原理是利用高温和高压使粉末颗粒之间产生扩散和结合。
在热压烧结过程中,首先需要将粉末颗粒在模具中进行成型,然后通过加热和施加压力使其结合成块状材料。
在高温下,粉末颗粒表面会产生液相,使得颗粒之间产生扩散,从而实现颗粒之间的结合。
同时,施加的压力可以使得颗粒之间更加紧密地结合,最终形成致密的块状材料。
其次,热压烧结的原理可以分为两个关键步骤,扩散和结合。
在高温下,粉末颗粒表面会产生液相,使得颗粒之间的扩散更加容易。
扩散过程中,颗粒之间会发生原子间的迁移,从而使得颗粒之间的结合更加牢固。
同时,施加的压力可以使得颗粒之间更加紧密地结合,从而提高材料的密度和强度。
热压烧结具有许多优点,首先是可以制备出高密度、高强度的材料。
由于热压烧结过程中颗粒之间的结合非常牢固,因此制备出的材料具有很高的密度和强度。
其次,热压烧结可以制备出复杂形状的材料。
通过设计不同形状的模具,可以制备出各种复杂形状的材料,满足不同工程需求。
此外,热压烧结还可以实现多种材料的复合制备,例如金属与陶瓷的复合材料,从而拓展了材料的应用领域。
总之,热压烧结是一种重要的粉末冶金工艺,通过高温和高压的作用,实现了粉末颗粒之间的紧密结合,制备出高密度、高强度的材料。
它在陶瓷、金属和塑料等材料的制备过程中具有重要的应用价值,为材料制备领域的发展提供了重要支持。
希望本文对热压烧结原理及其应用有所帮助,谢谢阅读。
热压烧结的优点

2.2 γA, 其中γ为界面能;A为总的比表面积。那么总界面能的减少为:
A A A
其中,界面能的变化(Δγ)是因为样品的致密化,比表面积的变化 是由于晶粒的长大。对于固相烧结,Δγ主要是固/固界面取代固/气界面。
a x r
蒸汽压差为:
V p p m s RTr
其中,γs为固相的表面能,Vm’为空位摩尔体积,Vm为固相的摩尔体积。由于上 述体积压力差、空位浓度差和蒸汽压差的存在,促使物质扩散。
烧结中的物质传输机理
物质扩散机理 1.晶格扩散 2.晶界扩散 3.粘性流动 4.表面扩散 5.晶格扩散 6.气相传输 蒸发-凝聚 气相扩散 材料部位 晶界 晶界 整体晶粒 晶粒表面 晶粒表面 晶粒表面 晶粒表面 接触部位 颈部 颈部 颈部 颈部 颈部 颈部 颈部 相关参数 晶格扩散率,Dl 晶界扩散率,Db 粘度,η 表面扩散率,Ds 晶格扩散率,Dl 蒸汽压差,Δp 气相扩散率,Dg
烧结的驱动力主要来源于由于颗粒表面曲率的变化而造成的体积压力差、空位 浓度差和蒸汽压差。对于图中的模型示意图,体积压力差ΔP为:
空位浓度差为:
2 1 1 s P Pa Pr s a r x r
, Vm s C v C v RTr
液相烧结(Liquid Phase Sintering,简写为LPS)是指在烧结包含多种粉 末的坯体中,烧结温度至少高于其中的一种粉末的熔融温度,从而在烧结过 程中而出现液相的烧结过程。
优点: 1)提高烧结驱动力。 2)可制备具有控制的微观结构和优化性能 的陶瓷复合材料
4.1 液相烧结的阶段
(a)液相烧结不同阶段的示意图(O:熔化;Ⅰ:重排;Ⅱ:溶解-沉淀;及Ⅲ:气孔排除)。 (b)在不同温度下,氧化铝-玻璃体系中,实际致密化作为烧结时间的函数所示
热压烧结
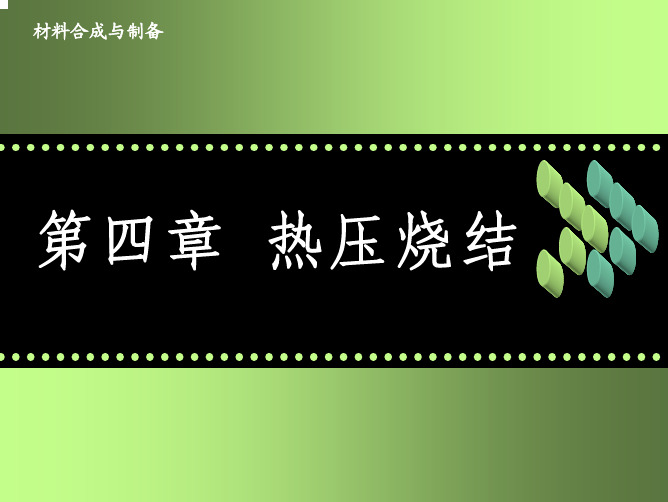
加压烧结
施加外压力的烧结, 施加外压力的烧结, 简称加压烧结 简称加压烧结 (applied ))or (appliedpressure pressure or (pressure—assisted (pressure—assisted sintering) sintering)
对松散粉末或粉末压坯同 对松散粉末或粉末压坯同 时施以高温和外压,则是 时施以高温和外压,则是 所谓的加压烧结 所谓的加压烧结 材料合成与制备
10
外力的引入:HP、HIP、 超高压烧结(纳米晶材料) 快速烧结技术 1 电固结工艺 2 热等静压(HIP) 3 微波烧结技术 4 激光烧结 5 等离子体烧结
材料合成与制备
12
(3)热压法容易获得接近理论密度、气孔率接近于零的烧 结体,容易得到细晶粒的组织,容易实现晶体的取向效应 和控制台有高蒸气压成分纳系统的组成变化,因而容易得 到具有良好机械性能、电学性能的产品。 (4)能生产形状较复杂、尺寸较精确的产品。
热压法的缺点是生产率低、成本高
材料合成与制备
• Initial stage:烧结初期 • Intermediate stage:烧结中期 • Final stage:烧结后期
材料合成与制备
烧结 初期
粉料在外部压力作用下,形成一定形状的、 具有一定机械强度的多孔坯体。烧结前成型体中 颗粒间接触有的波此以点接触,有的则相互分开 ,保留着较多的空隙,如图7.1(a)。
材料合成与制备
20
烧结颈(sintering neck)的形成与长大(neck growth)
热压烧结法
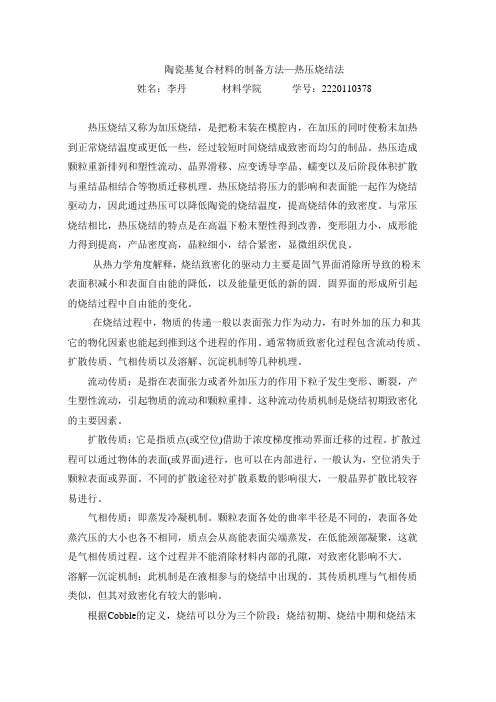
陶瓷基复合材料的制备方法—热压烧结法姓名:李丹材料学院学号:2220110378热压烧结又称为加压烧结,是把粉末装在模腔内,在加压的同时使粉末加热到正常烧结温度或更低一些,经过较短时间烧结成致密而均匀的制品。
热压造成颗粒重新排列和塑性流动、晶界滑移、应变诱导孪晶、蠕变以及后阶段体积扩散与重结晶相结合等物质迁移机理。
热压烧结将压力的影响和表面能一起作为烧结驱动力,因此通过热压可以降低陶瓷的烧结温度,提高烧结体的致密度。
与常压烧结相比,热压烧结的特点是在高温下粉末塑性得到改善,变形阻力小,成形能力得到提高,产品密度高,晶粒细小,结合紧密,显微组织优良。
从热力学角度解释,烧结致密化的驱动力主要是固气界面消除所导致的粉末表面积减小和表面自由能的降低,以及能量更低的新的固.固界面的形成所引起的烧结过程中自由能的变化。
在烧结过程中,物质的传递一般以表面张力作为动力,有时外加的压力和其它的物化因素也能起到推到这个进程的作用。
通常物质致密化过程包含流动传质、扩散传质、气相传质以及溶解、沉淀机制等几种机理。
流动传质:是指在表面张力或者外加压力的作用下粒子发生变形、断裂,产生塑性流动,引起物质的流动和颗粒重排。
这种流动传质机制是烧结初期致密化的主要因素。
扩散传质:它是指质点(或空位)借助于浓度梯度推动界面迁移的过程。
扩散过程可以通过物体的表面(或界面)进行,也可以在内部进行,一般认为,空位消失于颗粒表面或界面。
不同的扩散途径对扩散系数的影响很大,一般晶界扩散比较容易进行。
气相传质:即蒸发冷凝机制。
颗粒表面各处的曲率半径是不同的,表面各处蒸汽压的大小也各不相同,质点会从高能表面尖端蒸发,在低能颈部凝聚,这就是气相传质过程。
这个过程并不能消除材料内部的孔隙,对致密化影响不大。
溶解—沉淀机制:此机制是在液相参与的烧结中出现的。
其传质机理与气相传质类似,但其对致密化有较大的影响。
根据Cobble的定义,烧结可以分为三个阶段:烧结初期、烧结中期和烧结末期。
热压烧结Ti_3AIC_2材料在空气中的恒温氧化行为

中国科学E辑技术科学 2006, 36(5): 483~490 483 热压烧结T i3 AIC2材料在空气中的恒温氧化行为*徐学文①②李养贤①**梅炳初②朱教群②刘何燕①曲静萍①(①河北工业大学材料科学与工程学院, 天津 300130; ②武汉理工大学材料复合新技术国家重点实验室,武汉 430070)摘要研究了热压烧结的Ti3AlC2(含有2.8%(质量分数)的TiC)在900~1300℃空气中的恒温氧化行为. 结果表明, 该材料具有良好的抗高温氧化性能, 其氧化行为遵循抛物线规律. 随着温度升高, 氧化抛物线速率常数k p从900℃的1.39×10−10增大到1300℃的5.56×10−9 kg2·m−4·s−1,计算得到的氧化活化能为136.45 kJ/mol. 在900~1100℃时, 氧化产物为α-Al2O3和TiO2; 当温度达到1200℃时, TiO2开始部分地转变为Al2TiO5; 氧化温度升高到1300℃, Ti在氧化层中完全以Al2TiO5的形式存在. 氧化过程由Al3+和Ti4+的向外扩散和O2−的向内扩散控制. Al3+和Ti4+的快速向外扩散在基体与氧化层界面处导致大量的缺陷的形成.关键词铝碳化钛氧化性能动力学近年来, 一类三元层状化合物M n+1AX n吸引了研究者异乎寻常的关注[1~5], 其中, M是过渡族金属元素, A是IIIA或IV A族元素, X是C和/或N, n = 1, 2, 3. Ti3AlC2是M n+1AX n相中具有代表性的一种材料. Ti3AlC2属六方晶系, 空间群为D46h-P63/mmc, 其晶格参数为a=0.30753 nm和c=1.8578 nm, 理论密度为4.25 g·cm−3 [5]. 与其他M n+1AX n一样, Ti3AlC2兼具有金属和陶瓷的性能. 但作为一种高温结构材料, 还需要具备良好的抗高温氧化性能. Wang和Zhou研究了含有部分TiC的Ti3AlC2材料在500~1400 ºC空气中的氧化行为[6~8]. 研究发现, Ti3AlC2具有良好的抗高温氧化能力, 并且其氧化基本上符合抛物线规律. Barsoum以实验结果为依据建立了Ti3AlC2的分层氧化模型[9,10].从Ti3AlC2以及Ti3SiC2的氧化研究结果来看, 不同的制备条件和试样的杂质收稿日期: 2005-09-14; 接受日期: 2005-12-23*国家自然科学基金(批准号: 50172037)和教育部科学研究重点项目(批准号: 02052)资助** E-mail: nextnest@484 中国科学 E 辑 技术科学 第36卷与缺陷对材料的氧化性能有很大的影响[6~10]. 在作者等人的研究中, 通过热压法制备了高纯的Ti 3AlC 2材料[11,12]. 本文研究了制备材料在900~1300℃的恒温氧化行为, 分析了氧化规律.1 实验方法根据作者等人前期的研究工作, 以Si 为掺杂剂, 通过热压法合成了氧化实验用的Ti 3AlC 2试样[11,12]. 配制原始摩尔比为n (TiC)︰n (Ti)︰n (Al)︰n (Si) = 2.0︰1.0︰1.0︰0.2的混合粉料, 装入尺寸为40 mm × 40 mm, 表面涂有BN 的石墨模具内热压烧结. 工艺条件如下, 烧结温度: 1350℃, 升温速度: 50℃/min, 热压压力: 30 MPa, 保温时间: 2 h, Ar 保护. 烧结试样厚度约为10 mm. 采用Archimede 法测得试样的密度为4.18 g ·cm −3, k 值法测定试样中Ti 3AlC 2的质量百分数量为97.2 %, 杂质相为TiC. 氧化实验中采用的试样是用线切割方法得到的4 mm × 4 mm × 10 mm 的长条. 试样用1200目的SiC 砂纸磨平抛光至表面有金属光泽.恒温氧化增重实验在空气气氛的氧化炉中进行, 氧化温度为900~1300℃, 氧化总时间20 h. 试样置于炉中保温至要求的时间, 然后冷却至室温, 用精确度为±10−4 g 的分析天平称重, 并进一步分析试样的氧化动力学. 对氧化试样表面进行X 射线衍射(X-ray diffraction, XRD, Model D/MAX-RB, RIGAKU Corporation, Japan)分析, 以确定其相组成. 同时用扫描电子显微镜(scanning electron microscopy, SEM, Model JSM-5610LV , JEOL Ltd, Japan)观察氧化层的微观结构. 氧化层的化学成分用以上扫描电子显微镜自带的能谱仪(energy spectrometer, EDS, Model Phoenix, EDAX, USA)确定.2 实验结果与讨论2.1 氧化动力学图1(a)和1(b)所示分别为Ti 3AlC 2在900~1300℃空气中氧化时, 单位表面增重和单位表面增重的平方与氧化时间的关系. 由图可知, 在900~1300℃温度范围内, 随着氧化温度的升高和时间的延长, 试样的氧化增重缓慢增加. 在1300℃氧化20 h 后试样的单位表面增重也仅有1.98 × 10−2 kg/m 2. 研究者对M n AX n +1化合物中, 另一种典型的材料Ti 3SiC 2的高温氧化行为作了研究[12], 结果表明, 在1300℃氧化20 h 后, 试样的单位表面增重为 2.48 × 10−2 kg/m 2. 这表明Ti 3AlC 2具有比Ti 3SiC 2更优良的抗高温氧化性能. 由图1可知, 在900~1300℃, 单位表面氧化增重随时间抛物线上升, 而单位表面增重的平方与时间呈线性关系. 因此, Ti 3AlC 2在900~1300℃的恒温氧化动力学行为符合抛物线规律, 可以用以下公式表示: 2p ()W S k t c ∆=+, (1)第5期 徐学文等: 热压烧结Ti 3AlC 2材料在空气中的恒温氧化行为 485图1 900~1300℃氧化时, 单位表面增重(a)和单位表面增重的平方(b)与时间的关系其中, ∆W/S 是单位表面增重, k p 是抛物线速率常数, c 是常数.根据图1(b)计算的各温度下氧化抛物线速率常数k p 列于表 1. 随着氧化温度升高, k p 值随之升高. 为了更进一步研究Ti 3AlC 2的氧化动力学, 引入Arrhenius- type 公式来计算氧化反应的活化能. 方程如下:p 0exp()k k Q RT =−, (2)其中, k 0是指数前因子; Q 是活化能; R 是摩尔气体常数, 单位是J·mol -1·K -1; T 是绝对温度. 图2是根据Arrhenius 公式确定的ln k p -(1/T )曲线. 由此计算的平均氧化反 表1 抛物线速率常数列表氧化温度/℃抛物线速率常数k p /kg ·m ·s 9001.39×10−1010002.78×10−1011008.33×10−1012001.39×10−913005.56×10−9486 中国科学 E 辑 技术科学 第36卷图2 氧化温度与抛物线速率常数确定的Arrhenius 曲线应活化能Q eff 为136.45 kJ/mol. 计算值与其他研究者的结果175 kJ/mol 相近[7].2.2 氧化层相组成与微观结构分析为了进一步了解Ti 3AlC 2的氧化机制, 对氧化试样表面的氧化层进行了相组成和微观结构分析. 图3所示为900~1300℃时, 经过20 h 氧化后得到试样的XRD 图谱. 在900~1200℃, 试样的主晶相仍然是Ti 3AlC 2, 随着氧化温度升高, Ti 3AlC 2衍射峰强度逐步下降. 当氧化温度升高到1300℃后, 试样的主晶相转变为α- Al 2O 3, 但其中还存在大量的Ti 3AlC 2. 这种实验现象表明, 各温度下经过20 h 氧化后, 产生的氧化层极薄, 从另一方面证明了具有良好的抗高温氧化能力. 在900℃时, 氧化产物主要是TiO 2和α-Al 2O 3, 随着温度升高, α-Al 2O 3的衍射峰强度显著上升, 而TiO 2的衍射峰强度则下降; 至1200℃时, 出现Al 2TiO 5的衍射峰, 当氧化温度达到1300℃后, TiO 2完全转变为Al 2TiO 5, 发生的反应如下:23225Al O TiO Al TiO +→ (3)一般认为, 几种致密的氧化膜, 诸如Al 2O 3, Cr 2O 3, TiO 2和SiO 2等, 能明显提高材料的抗高温氧化能力. 在Ti 3AlC 2试样表面形成的组分为α-Al 2O 3和TiO 2的氧化膜, 使材料具有良好的耐高温氧化能力.图4所示分别为Ti 3AlC 2在900和1300℃恒温氧化20 h 后, 试样抛光面的扫描照片. 由图可知, 在900℃时, 氧化层极薄, 并与基体紧密结合, 界面几乎不可分辨. 至1300℃时, 氧化层厚度急剧增大, 约为12~15 µm, 于界面处可以观察到孔洞存在, 表明在1300℃时开始剧烈氧化, 这与以上的动力学结果吻合. EDS 研究表明, 1200和1300℃的氧化层成分以α-Al 2O 3为主, 同时有极少量的Ti 的氧化物TiO 2和/或Al 2TiO 5. 假定氧化层中Ti 以Al 2TiO 5的形式存在, 则1200℃时, 氧第5期 徐学文等: 热压烧结Ti 3AlC 2材料在空气中的恒温氧化行为 487图3 不同温度下氧化20 h 后, 试样的XRD 图谱化层中α-Al 2O 3和Al 2TiO 5的含量分别为77.69%和22.31%(质量分数), 1300℃时两者的含量分别为96.54%和3.46%(质量分数).2.3 讨论以上实验部分说明了Ti 3AlC 2具有良好的抗高温氧化性能. 下面就其氧化机制作初步探讨.在氧化的初始阶段, 当试样在较低的温度下和较短的时间内暴露于空气中时, 试样表面直接发生氧化反应, 其反应方程如下:32222324Ti AlC 23O 12TiO 2Al O 8CO (g)+=++. (4) 从热力学角度来看, Al 比Ti 更加容易氧化, 因此在试样表面会形成更多的Al 2O 3晶核. 但由于Al 2O 3晶体的生长速度比TiO 2小得多, 所以最初的氧化层以TiO 2为主, 其中夹杂有部分Al 2O 3. 这一点图3给出了明显的证明, 在900℃时, 即使氧488中国科学E辑技术科学第36卷图4 不同温度恒温氧化20 h得到的试样截面形貌(a) 900℃, (b) 1300℃化了20 h, 所得的产物仍然以TiO2为主, 而α-Al2O3的衍射峰极弱.当表层的氧化膜达到一定的厚度之后, 氧化过程将由扩散控制. 根据以上的分析, 在扩散开始阶段, 扩散介质主要由TiO2组成. 一般地, O或O2−在TiO2中的本征扩散系数很小, 几乎是不可测定的[13,14]. 研究者发现, O2−在TiO2中的扩散速度D O与氧分压p O无关, 而主要是由其中存在的100~200 ppm的Al2O3杂质产生的外在空位浓度决定的[15]. 因此, 在氧化的最初始阶段溶解在TiO2中的极少量的Al3+离子使氧空位浓度上升, 促进了O2−向内扩散. 同时, 氧化试样中存在的制备缺陷, 如气孔等, 也会加速扩散. 因此, 氧化的扩散过程包括Al3+和Ti4+的向外扩散及O2−的向内扩散, 但Al3+的扩散速度远远高于O2−或Ti4+的扩散速度[13]. 因此, 在这一过程中Al3+从低氧分压向高氧分压处的扩散是主导的扩散过程, 氧化较长时间后, 所得的氧化产物以Al2O3为主, 仅有极少量的TiO2. 在2.2节中, 对1300℃氧化20 h所得氧化层的EDS分析结果也证明了以上的讨论.Al3+和Ti4+的向外快速扩散, 以及材料自身存在的少量缺陷, 会使氧化反应界面处产生由裂纹和气孔等组成的缺陷层. 图5中粗箭头所示为氧化层与基体界第5期 徐学文等: 热压烧结Ti3AlC2材料在空气中的恒温氧化行为 489图5 氧化层与基体交界处的缺陷层面的缺陷, 小箭头所示为烧结时产生的气孔等缺陷.3结论Ti3AlC2在900~1300℃的空气中氧化20 h符合抛物线规律, 氧化抛物线速率常数分别为 1.39×10−10, 2.78×10−10, 8.33×10−10, 1.39×10−9和 5.56×10−9 kg2·m−4·s−1. 计算的氧化活化能Q eff为136.45 kJ/mol. 在900~1100℃时, 氧化产物为α-Al2O3和TiO2; 当温度达到1200℃时, TiO2开始部分地转变为Al2TiO5; 氧化温度升高到1300℃, Ti在氧化层中完全以Al2TiO5的形式存在. 氧化过程由Al3+和Ti4+的向外扩散及O2−的向内扩散控制. Al3+和Ti4+的快速扩散, 会使氧化层与基体交界处形成由气孔和裂纹等组成的缺陷层.参考文献1 Barsoum M W, El-Raghy T. Synthesis and characterization of a remarkable ceramic: Ti3SiC2. J Am CeramSoc, 1996, 79(7): 1953―19562 Barsoum M W, Yaroschuck G, Tyagi S. Fabrication and characterization of M2SnC (M=Ti, Zr, Hf and Nb).490中国科学E辑技术科学第36卷Scr Mater, 1997, 10: 1583―15913 Procopio A T, Barsoum M W, El-Raghy T. Characterization of Ti4AlN3. Matall Mater Trans, 2000, 31A(12):333―3374 Sun Z M, Yan S L, Hashimoto H. Ti3SiC2 powder synthesis. Ceram Inter, 2004, 30: 1873―18775 Barsoum M W. The M N+1AX N phases: a new class of solids; thermodynamically stable nanolaminates. ProgSolid St Chem, 2000, 28: 201―2816 Wang X H, Zhou Y C. Oxidation behavior of TiC-containing Ti3AlC2 based material at 500~900 °C in air.Mat Res Innovat, 2003, 7: 381―3907 Wang X H, Zhou Y C. Oxidation behavior of Ti3AlC2 at 1000-1400 °C in air. Corrosion Science, 2003, 45:891―9078 Wang X H, Zhou Y C. Oxidation behavior of Ti3AlC2 powders in flowing air. J Mate Chem, 2002, 12 (9):2781―27859 Barsoum M W. Oxidation of Ti n+1AlX n where n=1~3 and X is C, N, part I: Model. J Electrochem Soc, 2001,148(8): 544―55010 Barsoum M W. Oxidation of Ti n+1AlX n where n=1~3 and X is C, N, part II: Experimental results. JElectrochem Soc, 2001, 148(8): 551―56211 Zhu J Q, Mei B C, Xu X W, et al. Synthesis of high-purity Ti3SiC2 and Ti3AlC2 by HP. J Mater Sci Lett,2003, 22(15): 1111―111212 Zhu J Q, Mei B C, Xu X W, et al. Effect of aluminum on the reaction synthesis of ternary carbide Ti3SiC2.Scr Mater, 2003, 49: 693―69713 Ikeda J A, Chiang Y M. Space charge segregation at grain boundaries in titanium dioxide: I, relationshipbetween lattice defect chemistry and space charge potential. J Am Ceram Soc, 1993, 76: 2437―244614 Ikeda J A, Chiang Y M. Space charge segregation at grain boundaries in titanium dioxide: II, modelexperiments. J Am Ceram Soc, 1993, 76: 2447―245415 Haul R, Dumbgen G. Sauerstoff-selbstdiffusion in rutilkristallen. J Phys Chem Solids, 1965, 26(1): 1―10。
- 1、下载文档前请自行甄别文档内容的完整性,平台不提供额外的编辑、内容补充、找答案等附加服务。
- 2、"仅部分预览"的文档,不可在线预览部分如存在完整性等问题,可反馈申请退款(可完整预览的文档不适用该条件!)。
- 3、如文档侵犯您的权益,请联系客服反馈,我们会尽快为您处理(人工客服工作时间:9:00-18:30)。
材料合成与制备
31
从化学反应的角度看,可分为相变热压烧结、分解 热压烧结,以及分解合成热压烧结三种类型。从能量及 结构转变的过程看,在多晶转变或煅烧分解过程中,通 常都有明显的热效应,质点都处于一种高能、介稳和接 收调整的超可塑状态。此时,促使质点足够的机械应力, 以诱导、触发、促进其转变,质点便可能顺利地从一种 高能介稳状态,转变到另一种低能稳定状态,可降低工 艺难度、完成陶瓷的致密烧结。其特点是热能、机械能、 化学能三者缺一不可,紧密配合促使转变完成。
规律是重要的。
材料合成与制备
24
7.2.3热压烧结的适用范围
热压烧结与常压烧结相比,烧结温度要低得多,而且 烧结体中气孔率低,密度高。由于在较低温度下烧结,就 抑制了晶粒的生长,所得的烧结体晶粒较细,并具有较高 的机械强度。热压烧结广泛地用于在普通无压条件下难致 密化的材料的制备及纳米陶瓷的制备。 例 : 纳 米ZrO2 ( 3Y ) 粉 体 采用 溶 胶 - 凝胶 法 制 备 , 经 550℃温度煅烧2h,获得粒径约40nm的ZrO=(3Y)粉体。 将 粉 体 臵 于 氧 化 铝 磨 具 中 , 加 载 23MPa 的 外 压 后 , 以 20℃/min的速度升温到1300℃,保温1h后以10℃/min的 速度降至室温,获得的致密的纳米Y-TZP陶瓷,晶粒尺寸 约为90nm。
粉末 Cu Ni W Al2O3
粉末粒度越粗,比表面越小,本征表面能驱动力就越小; 而粒度越细,比表面越大,本征表面能驱动力就越大。
这也是实际烧结中细粉比粗粉易于烧结的原因
材料合成与制备
13
在不同种粉末之间比较颗粒系统的烧结活性时,不要忘记单 个颗粒的烧结活性即粉末晶体的自扩散性.综合考虑这两个因 素来确定烧结活性,有一个判据是值得注意的。
Burke指出,要想在适当的烧结时间内获得烧结体的充分致密化, 粉末颗粒系统应当满足下式关系:
DV 1 3 2a
式中 Dv——体积扩散系数,cm2/s; 2a——粉末粒度,μm。
材料合成与制备
14
例如,Dv的数量级为10-12cm2/s,则粉末粒度要在lμm左右。 如果Dv 太低,则某些共价键材枓(如Si的Dv 为10-14cm2/s) 若要充分地烧结致密化就要求使用粒度0.5μm左右的粉末。 一般金属粉末的Dv比陶瓷粉末的Dv大,因而金属粉末的粒 度可以粗些.而陶瓷则须细粉末才能获得好的烧结结果,
材料合成与制备
25
在现代材料工业中,用粉体原料烧结成型的产业有两 类,一个是粉末冶金产业,一个是特种陶瓷产业。 所使用的烧结工艺方法主要有两种,一种是冷压成型 然后烧结:另一种是热压烧结。 实验证明,采用真空热压烧结可以使产品无氧化、低 孔隙、少杂质、提高合金化程度,从而提高产品的综合性 能
材料合成与制备
4
1
固体粉末烧结的过程和特点
坯体烧结后在宏观上的变化是:体积收缩,致密度 提高,强度增加 因此烧结程度可以用坯体收缩率、气孔率或体积密度 与理论密度之比等来表征。 在热力学上,所谓烧结是指系统总能量减少的过程。
材料合成与制备
5
一般烧结过程,总伴随着气孔率的降低,颗粒总表 面积减少,表面自由能减少及与其相联系的晶粒长大 等变化,可根据其变化特点来划分烧结阶段。
材料合成与制备
10
(1)本征过剩表面能驱动力
可以用下述简单方法估计本征过剩表面能驱动力数量 级。假定烧结前粉末系统的表面能为Ep.烧结成一个致 密的立方体后的表面能为Ed,忽略形成晶界能量的消耗, 则本征驱动力为:
E E P E d
材料合成与制备
11
代入晶体材料的摩尔质量Wm(g/mol),固-气表面能 γsv(J/m2),粉末比表面Sp(cm2/g),致密固体密度d(g/cm3), 则有:
材料合成与制备
9
2
固体粉末烧结的本征热力学驱动力
致密的晶体如果以细分的大量颗粒形态存在,这个颗 粒系统就必然处于一个高能状态.因为它本征地具有发达 的颗粒表面,与同质量的未细分晶体相比具有过剩的表面 能。 烧结的主要目的是把颗粒系统烧结成为一个致密的晶 体,是向低能状态过渡。因此烧结前,颗粒系统具有的过 剩的表面能越高.这个过渡过程就越容易,它的烧结活性 就越大。
材料合成与制备
29
热等静压强化了压制和饶结过程.降低烧结温度,消 除空隙,避免晶粒长大,可获得高的密度和强度。同热 压法比较,热等静压温度低,制品密度提高。
下在粉料中可能发生的某种化学反应过 程。因势利导,加以利用的一种热压烧结工艺。也就是指 在烧结传质过程中,除利用表面自由能下降和机械作用力 推动外,再加上一种化学反应能作为推动力或激活能。以 降低烧结温度,亦即降低了烧结难度以获得致密陶瓷。
7.1热压烧结的发展
1826年索波列夫斯基首次利用常温压力烧结的方法得到 了白金。而热压技术已经有70年的历史,热压是粉末冶金 发展和应用较早的一种热成形技术。 1912年,德国发表了用热压将钨粉和碳化钨粉制造致密 件的专利。
1926~1927年,德国将热压技术用于制造硬质合金。
从1930年起,热压更快地发展起来,主要应用于大型硬
材料合成与制备
17
颗粒之间接触的直接结果是颈部出现了曲率半径; Laplace和Young以弯曲液体表面为例,给出了表面的曲 率半径、表面张力和表面所受的应力差值。
1 1 R R 2 1
式中R1与R2——表面上相互垂直的两个曲线的 曲率半径,称为主曲率半径。
材料合成与制备
16
烧 结 开 始 时 ,孔洞的形状并不是球形 ,面是由尖角 形.圆滑菱形.近球形莲浙向球形过渡,如图7-2所示。 此时,孔洞的收缩必然伴随着颗粒捶触区的扩展。这 个接触区最先被称作金属颗粒之间的“桥”.旋即被 Kuczynski,定义为颈(neck)。
图7.2 不加压固相烧结空洞形状变化示意
23
在加压烧结第二阶段(也可称为烧结末期),上述机制 仍然存在.只不过孔洞成为孤立的闭孔,位于晶界相交处。 同时,并不排除在晶粒内部孤立存在的微孔。 在第一阶段发生的塑性屈服是一个快过程,而蠕变是 一个慢过程。通常的压力烧结的应力水平还不足以使材料
全部屈服发生塑性流动。因而研究压力烧结的蠕变致密化
7
烧结 中期 开始有明显的传质过程。颗粒间由点接触逐渐扩大为
面接触,粒界面积增加,固-气表面积相应减少,但气孔仍 然是联通的,此阶段晶界移动比较容易。在表面能减少的 推动力下,相对密度迅速增大,粉粒重排、晶界滑移引起 的局部碎裂或塑性流动传质,物质通过不同的扩散途径向
颗粒间的颈部和气孔部位填空,使颈部渐渐长大,并逐步
这与烧结经验是完全吻合的。
材料合成与制备
15
(2)本征Laplace应力
除了松散烧结(也称重力烧结)之外,粉末总是在 被压制成某种形状的压坯后再进行烧结的;这样的颗粒 系统就有另外两个本征的特点:颗粒之间的接触相颗粒 之间存在着“空隙”或称孔洞;系统表面的减少。自由 能的降低主要是通过孔洞的收缩来实现的。
烧结初期
烧结中期
烧结后期
材料合成与制备
6
烧结 初期
粉料在外部压力作用下,形成一定形状的、 具有一定机械强度的多孔坯体。烧结前成型体中 颗粒间接触有的波此以点接触,有的则相互分开 ,保留着较多的空隙,如图7.1(a)。
图7.1 不同烧结阶段晶粒排列过程示意图
随着烧结温度的提高和时间的延长,开始产生颗粒间的键合和 重排过程,这时粒子因重排而相互靠拢,大空隙逐渐消失,气孔的 总体积迅速减少,但颗粒间仍以点接触为主,总表面积并没减小。 材料合成与制备
对松散粉末或粉末压坯同 时施以高温和外压,则是 所谓的加压烧结 材料合成与制备
2
热压是指在对臵于限定形状的石墨模具中的松散粉末或对
粉末压坯加热的同时对其施加单袖压力的烧结过程。 热压的优点:
热压时,由于粉料处于热塑性状态,形变阻力小,易于
塑性流动和致密化,因此,所需的成型压力仅为冷压法的 1/10,可以成型大尺寸的A12O3、BeO、BN和TiB2等产品。 由于同时加温、加压,有助于粉末颗粒的接触和扩散、 流动等传质过程,降低烧结温度和缩短烧结时间,因而抑制 了晶粒的长大。
1 1 x
式中负号表示ρ从孔洞内计算,正号表示x在颗 粒内计算半径值。
材料合成与制备
20
一般可以把这类加压烧结分成两大阶段来认识。Ashby把这 两个阶段分为孔隙连通阶段相孤立孔洞阶段。图8.5是这两个阶 段的示意图。
材料合成与制备
21
材料合成与制备
22
质合金制品、难熔化合物和现代陶瓷等方面。
材料合成与制备
1
烧结过程可以分为两大类:
不加压烧结 加压烧结
不施加外压力的烧结,
简称不加压烧结 (pressureless sintering)
施加外压力的烧结, 简称加压烧结 (applied pressure) or (pressure—assisted sintering)
2/3 Wm E SV W mS p 6 d
由于
> W mS p > 6 Wm d
2/3
,则可近似为
svWm S p
材料合成与制备
12
表7-1 典型粉末的本征驱动力ΔE及计算参考数值 粒度 /µ m 150 10 0.3 0.2 比表面积 km2·-1 g 5×102 4×103 104 105 固体密度 kg· -1 mol 8.9 8.9 19.3 4.0 摩尔质量 kg· -1 cm 63.55 58.69 183.86 102.0 γsv/J·mol-1 1.6 1.9 2.9 1.5 本征 驱动力 5.1 4.5×10 5.3×102 1.5×103
减少气孔所占的体积,细小的颗粒之间开始逐渐形成晶界, 并不断扩大晶界的面积,使坯体变得致密化,如图7.1(b)