切断刀前刀面的改进
机械制造基础课后题及参考答案

何谓切削用量三要素?它们与切削层参数有什么关系?切断刀的前角后角主偏角副偏角刃倾角什么是积屑瘤?它对加工过程有什么影响?如何控制积屑瘤的产生?答:在切削速度不高而又能形成连续性切屑的情况下,加工一般钢料或其它塑性材料时,常在前刀面切削处粘有剖面呈三角状的硬块。
其硬度通常是工件材料硬度的2~3倍,能够代替切削刃进行切削。
这部分冷焊在前刀面的金属称为积屑瘤。
积屑瘤对切削过程的影响:1)实际前角增大。
它加大了刀具的实际前角,可使切削力减小,对切削过程起积极的作用。
积屑瘤愈高,实际前角愈大。
2)使加工表面粗糙度增大。
积屑瘤的底部则相对稳定一些,其顶部很不稳定,容易破裂,一部分连附于切屑底部而排出,一部分残留在加工表面上,积屑瘤凸出刀刃部分使加工表面切得非常粗糙,因此在精加工时必须设法避免或减小积屑瘤。
3)对刀具寿命的影响。
积屑瘤粘附在前刀面上,在相对稳定时,可代替刀刃切削,有减少刀具磨损、提高寿命的作用。
但在积屑瘤比较不稳定的情况下使用硬质合金刀具时,积屑瘤的破裂有可能使硬质合金刀具颗粒剥落,反而使磨损加剧。
控制积屑瘤的主要方法有:1)降低切削速度,使温度较低,粘结现象不易发生;2)采用高速切削,使切削温度高于积屑瘤消失的相应温度;3)采用润滑性能好的切削液,减小摩擦;4)增加刀具前角,以减小切屑与前刀面接触区的压力;5)适当提高工件材料硬度,减小加工硬化倾向。
影响切削力的主要因素有哪些?试论述其影响规律。
答:实践证明,切削力的影响因素很多,主要有工件材料、切削用量、刀具几何参数、刀具材料刀具磨损状态和切削液等。
1)工件材料(1)硬度或强度提高,剪切屈服强度增大,切削力增大。
(2)塑性或韧性提高,切屑不易折断,切屑与前刀面摩擦增大,切削力增大。
2)切削用量(1)背吃刀量(切削深度)ap、进给量增大,切削层面积增大,变形抗力和摩擦力增大,切削力增大。
(2)切削速度vc :加工塑性金属时,切削速度Vc对切削力的影响规律如同对切削变形影响一样,它们都是通过积屑瘤与摩擦的作用造成的。
车刀刃磨技术2
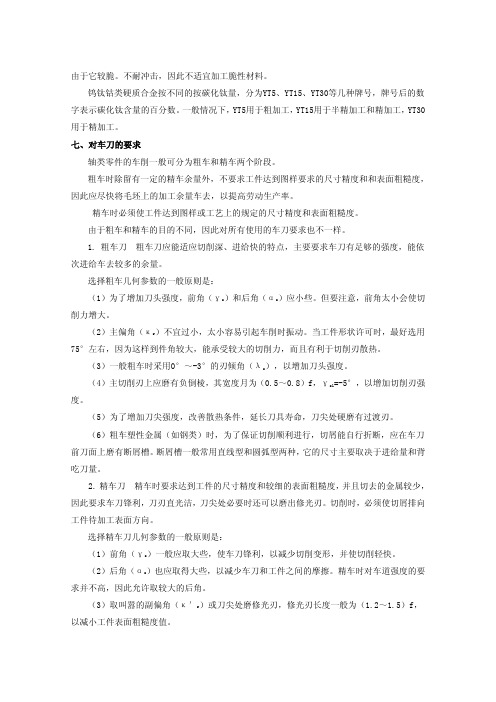
由于它较脆。
不耐冲击,因此不适宜加工脆性材料。
钨钛钴类硬质合金按不同的按碳化钛量,分为YT5、YT15、YT30等几种牌号,牌号后的数字表示碳化钛含量的百分数。
一般情况下,YT5用于粗加工,YT15用于半精加工和精加工,YT30用于精加工。
七、对车刀的要求轴类零件的车削一般可分为粗车和精车两个阶段。
粗车时除留有一定的精车余量外,不要求工件达到图样要求的尺寸精度和和表面粗糙度,因此应尽快将毛坯上的加工余量车去,以提高劳动生产率。
精车时必须使工件达到图样或工艺上的规定的尺寸精度和表面粗糙度。
由于粗车和精车的目的不同,因此对所有使用的车刀要求也不一样。
1. 粗车刀 粗车刀应能适应切削深、进给快的特点,主要要求车刀有足够的强度,能依次进给车去较多的余量。
选择粗车几何参数的一般原则是:(1)为了增加刀头强度,前角(γo)和后角(αo)应小些。
但要注意,前角太小会使切削力增大。
(2)主偏角(κr)不宜过小,太小容易引起车削时振动。
当工件形状许可时,最好选用75°左右,因为这样到件角较大,能承受较大的切削力,而且有利于切削刃散热。
(3)一般粗车时采用0°~-3°的刃倾角(λs),以增加刀头强度。
(4)主切削刃上应磨有负倒棱,其宽度月为(0.5~0.8)f,γo1=-5°,以增加切削刃强度。
(5)为了增加刀尖强度,改善散热条件,延长刀具寿命,刀尖处硬磨有过渡刃。
(6)粗车塑性金属(如钢类)时,为了保证切削顺利进行,切屑能自行折断,应在车刀前刀面上磨有断屑槽。
断屑槽一般常用直线型和圆弧型两种,它的尺寸主要取决于进给量和背吃刀量。
2. 精车刀 精车时要求达到工件的尺寸精度和较细的表面粗糙度,并且切去的金属较少,因此要求车刀锋利,刀刃直光洁,刀尖处必要时还可以磨出修光刃。
切削时,必须使切屑排向工件待加工表面方向。
选择精车刀几何参数的一般原则是:(1)前角(γo)一般应取大些,使车刀锋利,以减少切削变形,并使切削轻快。
数控车床切断刀使用技巧

数控车床切断刀使用技巧数控车床切断刀是数控车床加工过程中常用的工具之一,其使用技巧对于工件的切削质量和加工效率有着重要影响。
下面将介绍数控车床切断刀的使用技巧。
首先需要注意的是,选择合适的切断刀。
数控车床切断刀通常有圆形、方形、三角形等不同形状,根据需要选择相应形状的切断刀。
同时,要选择刀具材料和刀具尺寸合适的切断刀,以保证切削效果。
切断刀的切削方向需要正确选择。
切断刀的切削方向应该与工件的切削方向一致,这样可以减小切削力,提高加工效率,并且避免产生毛刺和切割面破损等问题。
切断刀的进给量要适当控制。
切断刀的进给量过小会导致切削刀具没有充分参与切削,造成刀具磨损严重;进给量过大则会增加切削力,容易导致刀具断裂和工件变形等情况。
因此,在实际使用过程中需要根据工件材料和加工要求,合理控制切断刀的进给量。
切断刀的排屑要及时清理。
切断刀在加工过程中会产生大量的切屑,如果不及时清理就会造成切屑堆积,影响切削效果,甚至导致切断刀卡刃。
因此,在切削过程中应保持工件、机床和刀具的清洁,及时清理切屑。
切断刀的冲击要避免。
数控车床切断刀在切削过程中,尤其是在切断高硬度材料时,容易产生冲击载荷,对切断刀造成冲击。
为了避免冲击,可以通过降低切削速度、调整切断刀的前角和后角等方式来减小冲击。
切断刀的磨损要及时更换。
切断刀在长时间使用后会产生磨损,磨损严重的切断刀会严重影响加工质量和加工效率。
因此,一旦发现切断刀有磨损的情况,应及时更换切断刀,以保证切削效果。
总之,数控车床切断刀的使用技巧对于保证加工质量和提高加工效率至关重要。
通过选择合适的切断刀、正确选择切削方向、适当控制进给量、及时清理切屑、避免冲击载荷和及时更换磨损的切断刀等措施,能够有效提高数控车床切断刀的使用效果。
16--切断刀

主偏角
(Кг)
切断刀以横向进 给为主,因此 Кг=90°。为
防止切断时在工 件中心处留有小 凸台及使切断空 心工件不留飞边 ,可以把主切削
刃略磨斜些。
8
卷屑槽 0.75~1.5㎜
刀体长度
(L) L=h+(2~3)㎜
主切削刃宽度 a ≈(0.5~0.6)√d ㎜ (a)
11.10.2020
副偏角
(Кг′)
两个副偏角必须对称。 Кг′=1°~1°30′
9
例
❖ 切断外径为64㎜,内孔为40㎜的空心工件,试计 算切断刀的主切削刃宽度和刀体长度。
解:根据公式:
a ≈(0.5~0.6)√d =(0.5~0.6)√64 = 4~4.8㎜ L=h +(2~3)㎜
=64-40/2 +(2~3)㎜ =14~15㎜
11.10.2020
11.10.2020
12
4、弹性切断刀
11.10.2020
13
5、车槽刀
一般外沟槽车刀的角度和形状与切 断刀基本相同。在车较窄的外沟槽时, 车槽刀的主切削刃宽度应与槽宽度相等 ,刀体长度要略大于槽深。
11.10.2020
14
三、切断刀和车槽刀的刃磨方法
刃磨前刀面
车刀前面对着砂轮磨削表面,同时磨出前角。
你来说
11.10.2020
19
切断刀的安装
1
安装时,刀头伸 出不宜过长,刀 柄中心线与工件 中心线必须垂直 ,以保证两副偏 角对称。.
11.10.2020
2
切断实心工件时, 刀尖必须对准工 件中心,否则崩刃 ,甚至刀体折断.
3
底面应平整,以 保证两侧副后角 对称。
切断与切槽
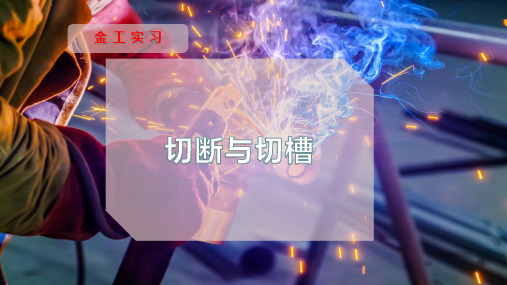
切断与切槽
图1-32 高速钢切断刀
切断与切槽
2)硬质合金切断刀
硬质合金切断刀如 图1-33所示,由于采用 高速切削,产生的热量 大,切削力大,使用时 必须充分加注切削液, 并要求工件装夹可靠。
图1-33 硬质合金切断刀
切断与切槽
3)弹性机夹式切断刀 为了减少刃磨时间和节约高速钢,可采用弹性机夹式切断刀,
金工实习
切断与切槽
图1-37 外槽的测量
切断与切槽
对于宽槽,一般先分段横向粗车,槽深留余量0.5 mm,最后一次横向车槽至所需深度,立即进行纵向 精车至槽宽的另一端。
对于宽度在50~100 mm甚至大于100 mm的外 槽,应先用弯头车刀车外圆的同时横向逐渐切入至槽 深,利用纵向进给车出槽宽,槽宽的两端再用切槽刀 接平。大宽度槽的两端面与槽底往往是圆弧连接,这 时切槽刀的两刀尖也应磨成相应的刀尖圆弧。
切断与切槽
1)整体式高速钢切断刀
如图1-32所示为整体式高速钢切断刀。它的强度高, 切削刃锋利,使用效果好,应用广泛,但刀具刃磨费时,切 削用量小。切断刀对刃磨后的几何角度要求较高,两副偏角 Kr′=1°~1.5°,两副后角αo′=1°~2°,后角αo≈8°,前刀面 切宽而浅的槽,前角γo=20°~30°,这样切削卷曲半径大, 切屑在切离工件后再卷屑,可避免切屑夹在槽内挤碎刀刃。 切断刀宽度b=2~4 mm,长度比切断长度略大2~5 mm, 两副后面要求对称、平直。
切断与切槽
3. 切断时的注意要点
切断时的注意要点如下: (1)车削过的表面容易进行切断,对悬伸工件要用顶 尖顶住或用中心架支撑,以增加工件刚度。切断位置距卡盘 或中心架近些,以免工件刚性不足而产生振动。 (2)选用比车外圆低的切削速度,用高速钢车刀车钢 材时,选择vc=20~40 m/min,并加切削液;车铸铁时选 vc=15~25 m/min。用硬质合金切断刀车钢材时,选 vc=80~120 m/min;车铸铁时选vc=60~100 m/min。
切断刀的对刀方法

切断刀的对刀方法切断刀是工业生产中常用的一种切割工具,它的使用方法和对刀技巧直接影响到切割效果和工作安全。
正确的对刀方法不仅可以提高工作效率,还可以延长刀具使用寿命,降低切割成本。
下面我们来详细介绍一下切断刀的对刀方法。
首先,准备工作。
在进行对刀之前,需要先将切断刀清洁干净,确保刀具表面没有杂质和油污。
同时,检查刀具的刀片是否磨损严重,如果磨损严重需要及时更换刀片,以免影响切割效果。
其次,选择合适的对刀工具。
对刀工具的选择直接关系到对刀的精度和效果。
常用的对刀工具有对刀尺、对刀块等,根据刀具的尺寸和形状选择合适的对刀工具进行对刀。
然后,进行对刀操作。
将对刀工具固定在工作台上,将切断刀放置在对刀工具上,调整切断刀的位置,使刀片与对刀工具接触,然后用手轻轻拉动切断刀,直至刀片与对刀工具完全接触。
在对刀的过程中,需要注意刀片与对刀工具之间的接触情况,确保刀片完全贴合对刀工具。
接着,进行刀片的调整。
对刀完成后,需要进行刀片的微调,以确保刀片的切割角度和位置符合要求。
通过调整刀具的固定螺丝或调整螺丝来实现刀片的微调,直至达到理想的切割效果。
最后,进行刀具的试切。
对刀完成后,需要进行试切操作,以检验刀具的对刀效果。
在试切过程中,需要留意切割面的光洁度和切割线的直线度,确保切割效果符合要求。
总之,切断刀的对刀方法是一个重要的工艺环节,正确的对刀方法可以提高切割效率,保障切割质量,延长刀具使用寿命,减少切割成本。
因此,操作人员在进行切断刀的对刀时,需要严格按照操作规程进行,确保对刀的准确性和可靠性。
16切断刀
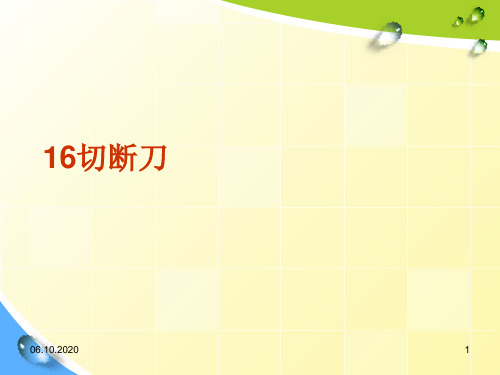
06.10.2020
12
16切断刀
06.10.2020
13
5、车槽刀
一般外沟槽车刀的角度和形状与切 断刀基本相同。在车较窄的外沟槽时, 车槽刀的主切削刃宽度应与槽宽度相等, 刀体长度要略大于槽深。
06.10.2020
14
16切断刀
刃磨前刀面
车刀前面对着砂轮磨削表面,同时磨出前角。
刃磨左侧副后刀面
两手握刀,车刀前刀面向上,同时磨出左侧副后角 和副偏角。
刃磨右侧副后刀面
两手握刀,车刀前刀面向上,同时磨出右侧副后角 和副偏角。
刃磨主后刀面
两手握刀,车刀前刀面向上,同时磨出主后角。
06.10.2020
15
a 刃磨左侧副后刀面同时磨出左侧副后角和副偏角。 b 刃磨右侧副后刀面同时磨出右侧副后角和副偏角。 c 刃磨主后刀面同时磨出主后角。 d 刃磨前刀面同时磨出前角。
06.10.2020
7
1、高速钢切断刀的几何角度
前角
( γ。)
切断中碳钢材料 是γ。=20°~ 30°,切断铸
铁材料时γ。 06.10.2020 =0°~10°。
后角
(а。)
切断塑性材料时 取大些,切断脆 性材料时取小些,
一般取а。 =6°~8°。
副后角
(а′。)
主偏角
(Кг)
切断刀以横向进 给为主,因此
06.10.2020
16
16切断刀
a: 正确 b:卷屑槽磨得过深,前角过大,其刀头强度差,容易折断。
C:前面磨得低或磨成阶台形,这种刀切削不顺利,排屑困难,切削 负荷大增,刀头容易折断。
06.10.2020
17
16切断刀
06.10.2020
刀具

(2)刃磨的步骤与方法现以主偏角为90。的钢料车刀(YTl5)为例,介绍手工刃磨的步骤,
4)磨断屑槽。为使切屑碎断,一般要在车刀前面磨出断屑槽。断屑槽有三种形状,即直线形、圆弧形和直线圆弧形。如刃磨圆弧形断屑槽的车刀,必须先把砂轮的外圆与平面的交角处用修砂轮的金钢石笔(或用硬砂条)修整成相适应的圆弧。如刃磨直线形断屑槽,砂轮的交角就必须修整得很尖锐。刃磨时,刀尖可向下或向上移动。
1 高碳钢:
高碳钢车刀是由含碳量0.8%~1.5%之间的一种碳钢,经过淬火硬化后使用,因切削中的摩擦四很容易回火软化,被高速钢等其他刀具所取代。一般仅适合于软金属材料之切削,常用者有SK1,SK2、、、、SK7等。
2 高速钢:
高速钢为一种钢基合金俗名白车刀,含碳量0.7~0.85%之碳钢中加入W、Cr、V及Co等合金元素而成。例如18-4-4高速钢材料中含有18%钨、4%铬以及4%钒的高速钢。高速钢车刀切削中产生的摩擦热可高达至6000C,适合转速1000rpm以下及螺纹之车削,一般常用高速钢车刀如SKH2、SKH4A、SKH5、SKH6、SKH9等。
M类介于P类与M类之间,适于切削靭性较大的材料如不?袗?等,此类刀柄涂以黄色来识别之。
5 陶瓷车刀:
陶瓷车刀是由氧化铝粉未,添加少量元素,再经由高温烧结而成,其硬度、抗热性、切削速度比碳化钨高,但是因为质脆,故不适用于非连续或重车削,只适合高速精削。
- 1、下载文档前请自行甄别文档内容的完整性,平台不提供额外的编辑、内容补充、找答案等附加服务。
- 2、"仅部分预览"的文档,不可在线预览部分如存在完整性等问题,可反馈申请退款(可完整预览的文档不适用该条件!)。
- 3、如文档侵犯您的权益,请联系客服反馈,我们会尽快为您处理(人工客服工作时间:9:00-18:30)。
切断刀前刀面的改进
摘要:文章介绍了车床用切断刀前刀面的改进措施。
通过前刀面几何形状的改变,可能增强刀关的刚性及延长使用寿命。
关键词:前刀面;形状;刚性;寿命;刃磨方式
金属切削刀具的种类很多,且各不相同。
但一把典型的刀具主要由刀头和刀体两大部分组成,刀头部分主要用来完成切削工作,又称切削部分,刀柄部分主要用来把刀夹持在刀架上。
而刀具的主要部分主要是指切削部分,它通常是由若干个面、刀刃和刀尖成组。
我们把它称为刀具几何参数,合理选择刀具几何参数能保证加工质量、提高生产率和降低成本。
具体的参数如下图1所示。
①前刀面:刀具上切屑流过的表面。
②主后刀面:与工件上过渡表面相对的表面。
③副后刀面:与工件已加工表面相对的表面。
④主切削刃:前刀面和主后刀面的相交部位,完成主要的切削工作。
⑤副切削刃:前刀面和副后刀面的相交部位,它配合主切削刃完成少量的切削工作。
⑥刀尖:主切削刃和副切削刃联结部分。
为了提高刀尖强度,延长车刀寿命,很多刀具将刀尖磨成圆弧型或直线型。
⑦修光刃:为了减小工件的表面粗糙度,通常在近刀尖处的副刀刃上一小段平直的刀刃,在安装刀具时这一小段平直的刀刃必须与进给方向平行,且长度控制在(1.2~1.5)f(f为切削进给量)以内,才能起到修光的作用。
在以上所述的刀具参数中,前角起了关键性的作用。
1前角的作用
前角的作用特点为:影响刀具的锋利、切削力的大小、切屑的变形;影响刀具的强度、受力和散热;影响工件的加工质量。
具体来说增大前角能使切削变形和摩擦减小,故切削力小、切削热少,工件表面质量高。
但前角过大,刀具强度降低,散热体积减小,刀具耐用度下降。
减小前角,刀具强度提高,切削变形增大,易断屑。
但前角过小,会使切削力和切削热增加,刀具耐用度降低。
所以在一般情况下,前角的选择原则是:在刀具强度许可的条件下,尽量选用大的前角(为了减少误差,保证工件的加工精度,成形刀应取较小的前角)。
2前刀面形状的种类
车削塑性金属材料时,根据加工要求来可靠地控制切屑的流向、卷曲和折断,是十分重要的问题,处理不当就会影响生产的顺利进行。
经常停车清除切屑,会增加辅助时间,使切拉毛工件表面,以及影响操作者的安全等。
对自动机床或数控机床,加工中,不断屑甚至会影正常生产。
如图2所示,它可以刃磨成直线圆弧形、直线型、全圆弧形等。
3切断刀概述
切断主要是以横向进给为主,前端是主切削刃,两侧是两条副切削刃,为了减少工件材料的浪费,使刀具能切到工件的中心,切断刀的主切削刃通常刃磨得比较窄,刀头较长,因此相对于其它刀具来说,强度及刚性较差。
图3为高速钢切断刀的几何参数。
切断刀使用。
切断刀主要用于切断工件,它的使用如上图4所示。
切断刀的刃磨。
切断刀的刃磨是车工的基本技能之一,相对于外圆车刀的刃磨难度更大。
特别前刀面的刃磨,前刀在刃磨质量的好坏直接会影响到刀具的切削性能与使用寿命。
如图5所示。
如图5所示切断刀的断屑槽不宜刃磨太深,一般为0.75~1.5 mm,如图5(a)。
断屑槽刃磨太深,其刀头强度差,容易折断。
如图5(b),更不能把前刀面磨成低或磨成台阶形。
如图5(c),这种刀切削不顺利,排屑较困难、切削负荷大,刀头强度变差,容易折断。
4切断刀前刀面的改进
①采用传统的刃磨方式进行刃磨的切断刀前刀面(如图6、图7所示)。
刃磨和研磨比较困难,而且难于保证刃磨后前刀面的平面度;刀具在刃磨时往往容易把槽刃磨得较深,削弱了刀头的强度;刀具磨损后可重磨次数相对少,刀具使用寿命相对短;由于槽刃磨得较深,在加工过程中往往容易用引起扎刀。
②采用改进刃磨方式进行刃磨的切断刀前刀面(如图8、图9所示)。
分析了以上采用传统的刃磨方式进行刃磨的切断刀前刀面,从而提出改变切断刀前刀面形状来达到要求的方案。
改进后的切断刀经过反复的试验和在生产中的应用,得到的优点如下:
①径向前角相对比较小,加强了切断刀的刚性。
②这样的车刀容易刃磨和研磨,刃磨时容易用达到面平刃直且锋利。
③由于刀具面平刃直且锋利,在;加工过程中不容易引起振动。
④车刀在切削时实际是进行刮削切削,可使切屑成纸片状。
⑤刀具磨损后可重磨次数多。
通过对改进后的切断刀进行切削效果对比试验后,结果如表1所示。
进一步验证了改进后的切断刀优点显著,有推广应用价值。
5切断刀前刀面刃磨方法的改进对其它刀具前刀
面的延伸
对于切断刀前刀面的改进方法不仅可以应用在切断刀上,还可以应用在其它的刀具,如外螺纹车刀、内螺纹车刀,如果应用在这些刀具除了能具备切断刀上的所有优点外,还可提高所加工的螺纹形状精度,如图10、11所示。
参考文献:
[1] 刘培德,余新萍.金工实习[M].北京:高等教育出版社,2003.。