附录1 发动机部件计算公式
汽车发动机、传动系统及轮胎选型计算公式
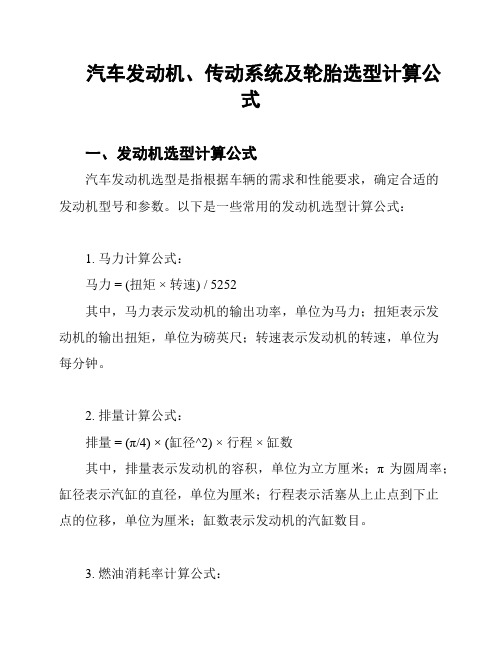
汽车发动机、传动系统及轮胎选型计算公式一、发动机选型计算公式汽车发动机选型是指根据车辆的需求和性能要求,确定合适的发动机型号和参数。
以下是一些常用的发动机选型计算公式:1. 马力计算公式:马力 = (扭矩 ×转速) / 5252其中,马力表示发动机的输出功率,单位为马力;扭矩表示发动机的输出扭矩,单位为磅英尺;转速表示发动机的转速,单位为每分钟。
2. 排量计算公式:排量= (π/4) × (缸径^2) ×行程 ×缸数其中,排量表示发动机的容积,单位为立方厘米;π为圆周率;缸径表示汽缸的直径,单位为厘米;行程表示活塞从上止点到下止点的位移,单位为厘米;缸数表示发动机的汽缸数目。
3. 燃油消耗率计算公式:燃油消耗率 = 发动机燃料消耗量 / 行驶里程其中,燃油消耗率表示单位行驶里程所消耗的燃料量,单位为升/百公里;发动机燃料消耗量表示发动机在单位时间内消耗的燃料量,单位为升/小时;行驶里程表示汽车的行驶里程,单位为公里。
二、传动系统选型计算公式传动系统选型是指根据发动机的转速和轮胎的直径等参数,确定适合的传动比和齿轮比。
以下是一些常用的传动系统选型计算公式:1. 传动比计算公式:传动比 = 输出轴转速 / 输入轴转速其中,传动比表示传动系统的转速比;输出轴转速表示传动系统输出轴的转速,单位为转/分钟;输入轴转速表示传动系统输入轴的转速,单位为转/分钟。
2. 齿轮比计算公式:齿轮比 = 齿轮2的齿数 / 齿轮1的齿数其中,齿轮比表示齿轮传动中两个齿轮齿数之比;齿轮2的齿数表示第二个齿轮的齿数;齿轮1的齿数表示第一个齿轮的齿数。
三、轮胎选型计算公式轮胎选型是指根据车辆的重量和行驶条件,选择合适的轮胎尺寸和负荷能力。
以下是一些常用的轮胎选型计算公式:1. 单位载荷计算公式:单位载荷 = 总重量 / 轮胎数量其中,单位载荷表示每个轮胎所承受的重量,单位为千克/轮胎;总重量表示车辆的总重量,单位为千克;轮胎数量表示车辆所使用的轮胎数量。
各部件的参数计算过程

P 工作机=FV/1000=2800×2/1000=5.6(KW)n 工作机=60×1000V/πD=60×1000×2/3.14×450=84.92(r/min)η总=η链×η齿×η卷筒×η轴承=0.92×0.98×0.96×0.993=0.859P 电需= P 工作机/η总=5.6/0.859=6.52(KW)P 电机应>P 电需 查表得 P 电机=7.5KW n 电机=960(r/min)η总= n 电机/ n 工作机=960/84.92=11.3取i 链=3.611.3=3.6×i 齿 i 齿=3.2P 工= P 电需×η齿=6.52×0.98=6.39(KW)n 工= n 电机/ i 齿=960/3.2=300(r/min)T 工=9.55×106×P 工/ n 工=9.55×106×6.39/300=203415(N.MM)解:1.选择齿轮精度等级,材料及齿数1) 链式选用滚子链2) 因载荷平衡传递功率较小,可采用软齿面齿轮,小齿轮选用45#钢,调质处理,大齿轮选用45#钢,正火处理,参考表10-1,取小齿轮硬度为217~255HBS;大齿轮硬轮为162~217HBS,计算后,取小齿轮硬度为240HBS;大齿轮硬度为190HBS3) 选小齿轮齿数Z 1=24,则Z2=I ×Z 1=3.2×24=77所以选大齿轮齿数为772.按齿面接触强度设计由设计公式d 1t ≥2.32×[]⎪⎪⎭⎫ ⎝⎛H ±⨯⨯σ2113Z u u d T Kt φ1) 确定公式内的各计算数值①试选载荷系数kt=1.3②小齿轮传递转矩T 2=203415(N.MM)③因为是单级传动齿轮,齿轮为对称布置,取齿宽系数φd=1④查表得材料的弹性影响系数Z Z =189.8MPa.k⑤δHlim2=400MPa⑥计算应力循环次数N 1=60n 1 Lh=60×960×1×16×356×6=2.03×109N2=n1/ i 齿=2.03×109/3.2=6.3×108⑦由按疲劳寿命系数曲线查表得KHN1=0.90 KHN2=0.95⑧计算按接触疲劳许用应力(取安全系数S=1)[δH ]1=KHN 1×δHN lim1/S=0.90×625=563MPa[δH ]2=KH1N 2×δHN lim2/S=0.95×550=523MPa2) 计算①计算小齿轮分度圆直径d 1t 代入[δH ]中较小值d 1t ≥2.32[]⎪⎪⎭⎫ ⎝⎛H ±⨯⨯σ2113Z u u d T Kt φ=82.95mm②计算圆周速度VV=πd 1tn 1/60×1000=3.14×82.95×960/60×1000=4.2m/s③计算齿宽与齿高之比b/h模数mt=d1t/z1=82.95/24=3.46mm齿高h=2.25mt=2.25×3.46=7.79mmb/h=82.95/7.79=10.655.计算载荷系数根据V=4.2m/s >精度,查动载荷系数KV=1.18 直齿轮,假设KAFt/b <100N/mm由表查得KHd=KF2=1.1 KA=1.25查7级精度,小齿轮相对支承对称布置,得KH β=1.12+0.18φd 2+0.23×10-3b=1.3+20.486×10-3=1.32由b/h=10.65, KH β=1.32 查表得KF β=1.28故载荷系数K=KA ×KV ×KH α×KH β=1.25×1.18×1.1×1.32=2.142 按实际的载荷系数所算的分度圆直径d1=d1t 3kt K =97.5mm 计算模数m=d 1/z 1=97.5/24=4.063.按齿根弯曲强度设计弯曲强度的设计公式为m ≥32112])/[(dZ KT F YfaYsa φδ1) 确定公式内的各计算数值①查图得小齿轮的弯曲疲劳强度极限δFZ1=360 大齿轮的弯曲疲劳强度极限δFZ2=320 ②查图得弯曲疲劳寿命系数 KFN 1=0.85 KFN 2=0.88③计算弯曲疲劳许应力(取弯曲疲劳安全系数δ=1.4)[δF ]1=KFN 1×δFZ 1/S=0.85×360/1.4=218.57MPa[δF ]2=KF1N 2×δFZ 2/S=0.88×320/1.4=201.14MPa④计算载荷系数KK=KA ×KV ×KH α×KH β=1.25×1.18×1.1×1.35=2.19⑤查齿形系数YS a1=2.65 YS a2=2.13⑥查取应力校正系数YS a1=1.58 YS a2=1.84⑦计算大小齿轮得Y Fa ×Y Sa /[δF ]并加以比较Y Fa1×Y Sa1/[δF ]1=2.65×1.58/218.57=0.0192Y Fa2×Y Sa2/[δF ]2=2.13×1.84/201.14=0.0195大齿轮的数值大2) 设计计算M3≥32112])/[(dZ KT F YfaYsa φδ=2.5对此计算结果,由齿面接触疲劳强度计算的模数m 大于由齿根弯曲疲劳强度计算的模数,由于齿轮模数m 的大,主要取决于弯曲强度,所得承载能力,而齿面接触疲劳强度所决定的承载能力,仅与齿轮直径有关,可取由弯曲强度算得模数m=3(取近圆整数的标准值)按接触强度算得的分度圆直径d 1=82.95,算出小齿轮齿数Z 1=d 1/m=82.95/3=28大齿轮齿数Z 2=n ×Z 1=3.2×28=904.几何尺寸计算1)计算分度圆直径d 1=z 1×m=28×3=84mmd 2=z 2×m=90×3=270mm2)计算中心距a=(d 1+d 2)/2=(84+270)/2=177mm3) 计算齿轮宽度b=φd ×d1=1×84=84mm取β1=270mm β2=84mm验算Ft=2T 1/d 1=2×203415/84=4843.2NKAFt/b=1.25×4843.2/84=72N/mm <100N/mm所以合适3.根据工作条件选用深沟球轴承,轴承径向载荷Fr=p=2800N 轴承转速为960r/minFt=2T1/d1=2×203415/84=4843.2NFr= Ft×tanα=4843.2×tan200=1762.78N当量动载荷P=2800N轴承应有基本额定动载荷值C=P1000000=51699nL'/60h按照轴承样本计算手册选择6310轴承4.采用滚子链传动链齿数Z1\Z2根据V=2m/s选小链轮齿数Z1=28从动链齿轮Z2=I×Z1=3.2×28=90计算功率PcaPca=KA×P=1.25×6.39=8KW确定链条节数LP初定中心距a0=40p,则链节数为LP=Z×a0/P+(Z1+Z2)/2+P/ a0×(Z2-Z1/2π)2=80P/P+(17+43)/2+P/40P×[(43-17)/2π]2=80+30+17/40=110.43=110节确定链长L及中心距离aL=Lp×P/1000=111×15.875/1000=1.8Ma=p/4[(L P-(z1+z2)/2+2]zzz--+zLp-(22/)1[(812/)2[π=642mm5.轴的结构设计1)初步确定轴的最小直径,根据表,取A0=112dmin=A033P=52.1mm/3n3)根据轴向定位的要求确定轴的各段直径及长度①为了满足半联轴器的轴向定位要求I~Ⅱ段右端需制出一轴肩,故Ⅱ~Ⅲ段的直径dⅡ~dⅢ=62mm,左端用轴端挡圈定位,按轴端直径取挡圈直径D=65mm,半联轴器与轴配合的彀孔长度L=76mm,为了保证轴端挡圈只压在半联轴器上而不压在轴的端面上,故I~Ⅱ段的长度应比L1略短一些,取LI~Ⅱ=82mm②初步选择滚动轴承,固轴承同时受有径向力和轴向力的作用,故选用单列圆锥滚子轴承.参照工作要求表产品目录其轴承型号为30313,其尺寸为d×D×T=65×140×36故dⅢ-Ⅳ=65mm,LⅦ-Ⅷ=36mm,右端轴承的定位采用轴肩进行定位,由手册上查得30313型轴承的定位轴肩高度h=6mm,取dⅥ-Ⅶ=77mm③取安装齿轮处的轴段Ⅳ-V的直径dIV-V=70mmLIV-V=76mm,dV-VI=82mm,轴环宽度b≥1.4h,取L V-VI=12mm④轴承疬的总宽度为20mm,取盖的外端面与半联轴器右端面间的距离L=30mm,故LII-III=50mm⑤取齿轮距箱体内壁这距离a=16mm,C=20mm,取s=8mm,已知轴承宽度T=36mm,大齿轮毂长L=105LIII-IV=T+S+a+(80-76)=(36+8+16+4)mm=64mmL VI-VII=L+C+a+S-L VI-VI=105+20+16+8+-12=137mm5)求轴上的载荷支反力F FNH1=3327N FNH2=1675NFNV1=1869N FNV2=-30N弯曲M MH=236217 N.mmMv1=132699 N.mmMv2=-4140 N.mm总弯矩M1=13269922362172+=270938N.mmM2=414022362172+=236253N.mm扭矩T T3=960000N.m6)按弯矩合成应力校核轴的强度a=0.6δca= 3212aTM+/W=18.6MPa前已选定轴的材料为45#钢,调质处理,查得[δ-1]=60 MPa,因此δca<[δ-1]故安全.7)精确校核轴的疲劳强度①截面IV左侧危险校核抗弯截面系数W=0.1d3=0.1×653mm3=27463 mm3抗扭截面系数W T=0.2d3=0.2×653mm3=54925 mm3截面IV左侧的弯矩M为M=270938×(71-36)/71=133561 N.m截面IV上的扭矩T3为T3=960000 N.m截面上的弯曲应力δb=M/W=133561/27463=4.86MPa截面上的扭转切应力τT=T3/W T=960000/54925=17.48 MPa轴的材料为45#钢,调质处理,查得δB=640 MPaδ-1=275MPa τ-1=155 MPa截面上由于轴肩而形成的理论应力集中系数aδ及aτ按附表3-2查取r/d=2/65=0.031,D/d=70/65=1.08插值后可查得aδ=2.0 aτ=1.31轴的材料的敏性系数为qδ=0.82, qτ=0.85kδ=1+qδ(aδ-1)=1+0.82×(2.0-1)=1.82kτ=1+qτ(aτ-1)=1+0.85×(1.31-1)=1.26尺寸系数εδ=0.67 扭转尺寸系数ετ=0.82βδ=βτ=0.92轴半径表面强化处理,即βq=1,得综合系数值kδ=( kδ/εδ+1)/(βδ+-1)=1.82/0.67+1/0.92-1=2.8kτ= (kτ/ετ+1)/(βτ+-1)=1.26/0.82+1/0.92-1=1.62ψδ=0.1~0.2,取ψδ=0.1ψτ=0.05~0.1,取ψτ=0.05计算安全系数Sca值Sδ=δ-1/(Kδδa+4δδm)=275/(2.8×4.86+0.1×0)=20.21Sτ=τ-1/(Kττa+4ττm)=155/(1.62×17.048/2+0.05×17.48/2)=10.62Sca= Sδ×Sτ/2δ=9.4>>S=1.5故可知其安全。
发动机部件计算公式

发动机部件计算公式发动机是汽车的核心部件,其性能直接影响到汽车的动力和燃油效率。
发动机由众多部件组成,如气缸、活塞、连杆、曲轴等。
在设计和制造发动机时,需要考虑各个部件之间的相互作用,以确保发动机的可靠性和性能。
1.气缸计算公式:气缸是发动机内燃过程的基本装置,其尺寸的选取对发动机的燃烧效率和动力特性有重要影响。
气缸计算公式包括气缸直径D和气缸行程S的选择。
气缸直径的选择与气缸的功率和转速有关,一般情况下,功率越大、转速越高,气缸直径就越大。
气缸行程的选择主要与发动机的转速在一定范围内有关。
行程较长有利于提高发动机的扭矩和低速性能,行程较短则有利于提高转速和高速性能。
计算公式如下:气缸直径(D)=(C/π)^(1/2)气缸行程(S)=2.2~2.5D其中C为发动机的歧管容积,π为圆周率。
2.活塞计算公式:活塞是发动机的运动部件,其结构和尺寸的设计直接影响到发动机的输出功率和燃油效率。
活塞计算公式主要包括活塞直径D、活塞行程H和活塞活塞冠高度的选择。
活塞直径的选择与发动机的功率、转速和气缸直径有关。
一般情况下,活塞直径与气缸直径之间取一个适当的比例,如1.3~1.6活塞行程的选择与发动机的功率和转速有关,一般情况下,行程较短有利于提高发动机的转速,行程较长有利于提高低速性能。
活塞冠高度的选择与发动机的燃烧室形状和燃油的喷射方式有关。
3.连杆计算公式:连杆是发动机的运动部件,其结构和尺寸的设计直接影响到发动机的输出功率和燃油效率。
连杆长度的选择与发动机的功率和转速有关,一般情况下,连杆长度与发动机的行程之间取一个适当的比例,如2.0~2.5连杆小头直径和连杆大头直径的选择与发动机的功率和气缸直径有关。
连杆角度和连杆挠曲的计算需要考虑到发动机的转速和挠曲的限制。
4.曲轴计算公式:曲轴是发动机的运动部件,其结构和尺寸的设计直接影响到发动机的输出功率和燃油效率。
曲轴主轴的直径和偏心量的选择与发动机的功率和转速有关。
发动机功率计算公式

发动机功率计算公式
发动机功率计算公式是一种计算发动机功率的重要工具,它可以帮助汽车发动机的设计者和用户更好的掌握发动机的性能。
发动机功率计算公式的基本原理是,发动机功率=机械功率+热功率,其中机械功率=排气量×燃料消耗量×排气压力×焓值。
排量是指每次活塞运动,活塞从最低点向上运动,活塞内容积的容积量。
燃料消耗量是指每次活塞运动所消耗的燃料量。
排气压力是指活塞上升时产生的压力。
焓值是指发动机燃烧时所释放的热量。
热功率是指发动机在燃烧时释放的热量,它的计算公式是热功率=排气量×燃料消耗量×焓值。
以上是发动机功率计算公式的原理,它可以帮助汽车发动机设计者更准确的判断发动机的功率性能,也可以帮助汽车用户更好的了解发动机的性能参数,从而更好的使用发动机。
此外,在发动机功率计算公式中,排量、燃料消耗量、排气压力和焓值也是汽车发动机性能参数的重要指标,它们也是汽车发动机设计者和用户重点关注的参数。
总之,发动机功率计算公式是一种重要的计算工具,它可以帮助汽车发动机设计者更准确的判断发动机的功率性能,也可以帮助汽车
用户更好的了解发动机的性能参数,从而更好的使用发动机。
发动机自配率计算公式
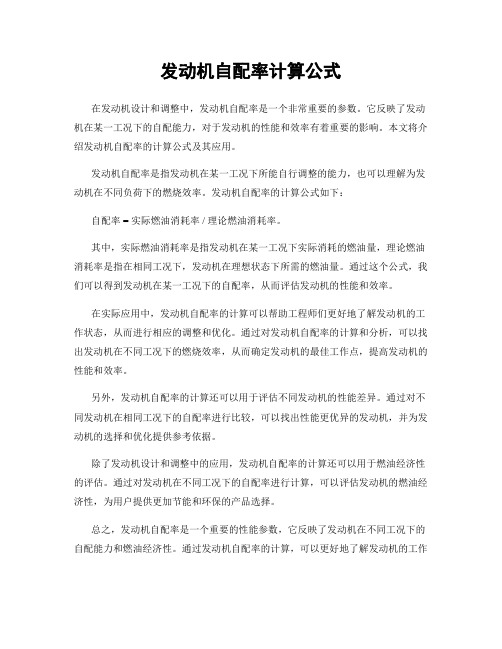
发动机自配率计算公式在发动机设计和调整中,发动机自配率是一个非常重要的参数。
它反映了发动机在某一工况下的自配能力,对于发动机的性能和效率有着重要的影响。
本文将介绍发动机自配率的计算公式及其应用。
发动机自配率是指发动机在某一工况下所能自行调整的能力,也可以理解为发动机在不同负荷下的燃烧效率。
发动机自配率的计算公式如下:自配率 = 实际燃油消耗率 / 理论燃油消耗率。
其中,实际燃油消耗率是指发动机在某一工况下实际消耗的燃油量,理论燃油消耗率是指在相同工况下,发动机在理想状态下所需的燃油量。
通过这个公式,我们可以得到发动机在某一工况下的自配率,从而评估发动机的性能和效率。
在实际应用中,发动机自配率的计算可以帮助工程师们更好地了解发动机的工作状态,从而进行相应的调整和优化。
通过对发动机自配率的计算和分析,可以找出发动机在不同工况下的燃烧效率,从而确定发动机的最佳工作点,提高发动机的性能和效率。
另外,发动机自配率的计算还可以用于评估不同发动机的性能差异。
通过对不同发动机在相同工况下的自配率进行比较,可以找出性能更优异的发动机,并为发动机的选择和优化提供参考依据。
除了发动机设计和调整中的应用,发动机自配率的计算还可以用于燃油经济性的评估。
通过对发动机在不同工况下的自配率进行计算,可以评估发动机的燃油经济性,为用户提供更加节能和环保的产品选择。
总之,发动机自配率是一个重要的性能参数,它反映了发动机在不同工况下的自配能力和燃油经济性。
通过发动机自配率的计算,可以更好地了解发动机的工作状态,评估发动机的性能和效率,为发动机的设计、调整和选择提供科学依据。
希望本文对您有所帮助,谢谢阅读!。
发动机参数百分比计算公式
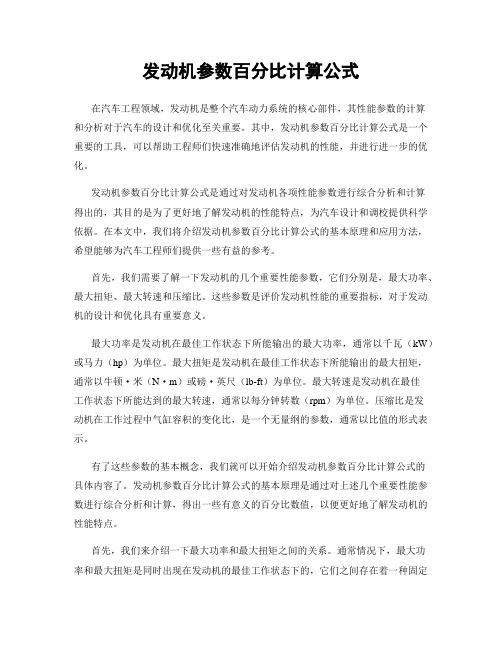
发动机参数百分比计算公式在汽车工程领域,发动机是整个汽车动力系统的核心部件,其性能参数的计算和分析对于汽车的设计和优化至关重要。
其中,发动机参数百分比计算公式是一个重要的工具,可以帮助工程师们快速准确地评估发动机的性能,并进行进一步的优化。
发动机参数百分比计算公式是通过对发动机各项性能参数进行综合分析和计算得出的,其目的是为了更好地了解发动机的性能特点,为汽车设计和调校提供科学依据。
在本文中,我们将介绍发动机参数百分比计算公式的基本原理和应用方法,希望能够为汽车工程师们提供一些有益的参考。
首先,我们需要了解一下发动机的几个重要性能参数,它们分别是,最大功率、最大扭矩、最大转速和压缩比。
这些参数是评价发动机性能的重要指标,对于发动机的设计和优化具有重要意义。
最大功率是发动机在最佳工作状态下所能输出的最大功率,通常以千瓦(kW)或马力(hp)为单位。
最大扭矩是发动机在最佳工作状态下所能输出的最大扭矩,通常以牛顿·米(N·m)或磅·英尺(lb-ft)为单位。
最大转速是发动机在最佳工作状态下所能达到的最大转速,通常以每分钟转数(rpm)为单位。
压缩比是发动机在工作过程中气缸容积的变化比,是一个无量纲的参数,通常以比值的形式表示。
有了这些参数的基本概念,我们就可以开始介绍发动机参数百分比计算公式的具体内容了。
发动机参数百分比计算公式的基本原理是通过对上述几个重要性能参数进行综合分析和计算,得出一些有意义的百分比数值,以便更好地了解发动机的性能特点。
首先,我们来介绍一下最大功率和最大扭矩之间的关系。
通常情况下,最大功率和最大扭矩是同时出现在发动机的最佳工作状态下的,它们之间存在着一种固定的关系,即最大功率=最大扭矩×最大转速/5252。
这个关系式是由功率和扭矩的定义公式推导而来的,它说明了最大功率和最大扭矩之间的内在联系。
接下来,我们来介绍一下最大转速和压缩比之间的关系。
A题-2013全国研究生数学建模竞赛A题

变循环发动机部件法建模及优化由飞机/发动机设计原理可知,对于持续高马赫数飞行任务,需要高单位推力的涡喷循环,反之,如果任务强调低马赫数和长航程,就需要低耗油率的涡扇循环。
双涵道变循环发动机可以同时具备高速时的大推力与低速时的低油耗。
变循环发动机的内在性能优势,受到了各航空强国的重视,是目前航空发动机的重要研究方向。
1 变循环发动机的构造及基本原理** 基本构造双涵道变循环发动机的基本构造见图1、图2,其主要部件有:进气道、风扇、副外涵道、CDFS涵道、核心驱动风扇级(CDFS)、主外涵道、前混合器、高压压气机、主燃烧室、高压涡轮、低压涡轮、后混合器、加力燃烧室、尾喷管。
双涵道模式下,选择活门和后混合器(后VABI)全部打开;单涵道模式下,选择活门关闭,后混合器关小到一定位置。
进气道风扇副外涵道前混合器核心驱动风扇级(CDFS)主外涵道高压压气机主燃烧室高压涡轮低压涡轮后混合器加力燃烧室尾喷管模式转换活门涡扇工作模式(图上半部分)涡喷工作模式(图下半部分)图1 变循环发动机的基本构造图2 双涵道变循环发动机结构示意图图中数字序号表示发动机各截面参数的下脚标各部件之间的联系如图3所示,变循环发动机为双转子发动机,风扇与低压涡轮相连,CDFS、高压压气机与高压涡轮相连,如图3下方褐色的线所示。
蓝色的线表示有部件之间的气体流动连接(图3中高压压气机后不经主燃烧室的分流气流为冷却气流,在本题中忽略不计)。
图3 变循环发动机工作原理图**工作原理变循环发动机有两种工作模式,分别为涡喷模式和涡扇模式。
发动机在亚音速巡航的低功率工作状态,风扇后的模式转换活门因为副外涵与风扇后的压差打开,使更多空气进入副外涵,同时前混合器面积开大,打开后混合器,增大涵道比,降低油耗,此时为发动机的涡扇模式。
发动机在超音速巡航、加速、爬升状态时,前混合器面积关小,副外涵压力增大,选择活门关闭,迫使绝大部分气体进入核心机,产生高的推力,此时为发动机的涡喷模式。
发动机功率的计算公式理解
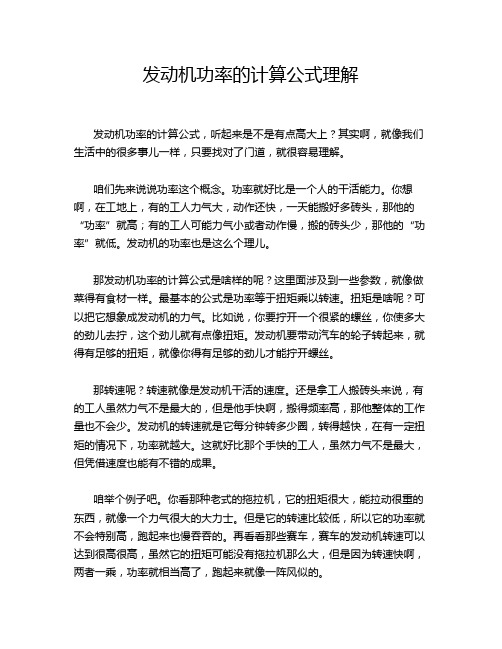
发动机功率的计算公式理解发动机功率的计算公式,听起来是不是有点高大上?其实啊,就像我们生活中的很多事儿一样,只要找对了门道,就很容易理解。
咱们先来说说功率这个概念。
功率就好比是一个人的干活能力。
你想啊,在工地上,有的工人力气大,动作还快,一天能搬好多砖头,那他的“功率”就高;有的工人可能力气小或者动作慢,搬的砖头少,那他的“功率”就低。
发动机的功率也是这么个理儿。
那发动机功率的计算公式是啥样的呢?这里面涉及到一些参数,就像做菜得有食材一样。
最基本的公式是功率等于扭矩乘以转速。
扭矩是啥呢?可以把它想象成发动机的力气。
比如说,你要拧开一个很紧的螺丝,你使多大的劲儿去拧,这个劲儿就有点像扭矩。
发动机要带动汽车的轮子转起来,就得有足够的扭矩,就像你得有足够的劲儿才能拧开螺丝。
那转速呢?转速就像是发动机干活的速度。
还是拿工人搬砖头来说,有的工人虽然力气不是最大的,但是他手快啊,搬得频率高,那他整体的工作量也不会少。
发动机的转速就是它每分钟转多少圈,转得越快,在有一定扭矩的情况下,功率就越大。
这就好比那个手快的工人,虽然力气不是最大,但凭借速度也能有不错的成果。
咱举个例子吧。
你看那种老式的拖拉机,它的扭矩很大,能拉动很重的东西,就像一个力气很大的大力士。
但是它的转速比较低,所以它的功率就不会特别高,跑起来也慢吞吞的。
再看看那些赛车,赛车的发动机转速可以达到很高很高,虽然它的扭矩可能没有拖拉机那么大,但是因为转速快啊,两者一乘,功率就相当高了,跑起来就像一阵风似的。
你要是对这个公式还是有点迷糊,咱再换个说法。
你把发动机想象成一个打水的辘轳。
扭矩就是你每次摇辘轳的劲儿,要是你劲儿大,就能带上来更多的水。
转速呢,就是你摇辘轳的速度,你摇得越快,那在一定时间里打上来的水就越多。
发动机的功率就像是你在一定时间里打水的总量。
理解了这个公式,对咱们平时用车或者研究发动机都有很大的好处。
比如说你想改装你的汽车,让它更有劲儿。
- 1、下载文档前请自行甄别文档内容的完整性,平台不提供额外的编辑、内容补充、找答案等附加服务。
- 2、"仅部分预览"的文档,不可在线预览部分如存在完整性等问题,可反馈申请退款(可完整预览的文档不适用该条件!)。
- 3、如文档侵犯您的权益,请联系客服反馈,我们会尽快为您处理(人工客服工作时间:9:00-18:30)。
附录1 发动机部件计算公式
1 基础知识
1)空气、燃气的焓、熵公式见附录2。
2)气动函数、、、计算公式见附录3。
2 变循环发动机各部件的计算公式
2.1 进气道
2.1.1 已知:发动机飞行高度、飞行马赫数。
2.1.2 计算过程
1)计算标准大气条件下环境压力(静压),环境温度(静温)。
当高度时:
(2.1)
其中,高度的单位为,温度的单位为,压力的单位为bar。
2)进气道进口的总温总压:
(2.2):气体绝热指数,纯空气,燃气。
3)计算进气道总压恢复系数:
(2.3)
4)计算进气道出口总温总压:
(2.4)
2.2 压气机
双涵道变循环发动机中三个压气机部件,分别是风扇、CDFS和高压压气机,这三个压气机部件采用同一种计算方法。
2.2.1 已知
压气机进口总温T in*、总压P in*、压气机的压比函数值、物理转速、压气机导叶角度。
2.2.2 计算过程
1)计算压气机换算转速:
(2.5)其中,风扇:,CDFS:,高压压气机:。
为压气机进口总温。
2)计算压气机增压比、效率和换算流量
压气机的增压比、效率和换算流量分别是其换算转速和压比函数值及导叶角的函数。
(2.6)压气机增压比、效率和换算流量的求法如下:
(1)附录4分别给出了风扇、CDFS,高压压气机的特性数据。
利用线性插值法计算出压气机的换算转速为、压比函数值为时的特性图上的增压比、效率和换算流量。
(2)将(1)求的特性图上的增压比、效率和换算流量代入(2.7)修正后得到压气机的增压比、效率和换算流量:
(2.7)分别是增压比、效率和换算流量的修正系数。
风扇、CDFS、高压压气机这三个值均分别取1,1,0.01;CDFS导叶角变化范围:,风扇和高压压气机的导叶角变化范围:;风扇:,CDFS: ,高压压气机:。
3)计算压气机出口参数
压气机出口总压:;
计算进口熵:,进口焓:;
压气机出口理想熵:,这里,是气体常数;
由压气机出口理想熵,计算压气机出口理想总温:;
计算压气机出口理想焓:;
根据公式计算压气机出口焓;
由压气机出口焓求压气机出口总温:;
计算压气机流量:
(2.8)
其中,风扇:,CDFS:,高压压气机:;
计算压气机功和功率:
(2.9) 2.3 主燃烧室
2.3.1 已知
主燃烧室进口总温、总压、空气流量、主燃烧室出口温度。
2.3.2 计算过程
1)根据公式求出主燃烧室出口油气比,其中,和分别主燃烧室进出口焓,燃烧效率,燃油热值;
2)燃油流量;
3)出口总压,主燃烧室总压恢复系数。
2.4 涡轮
2.4.1 已知:涡轮进口总温、总压、涡轮的压比函数值、物理转速、
涡轮导叶角度。
2.4.2 计算过程
1)求涡轮换算转速
(2.10)其中,高压涡轮:,低压涡轮:。
涡轮的增压比、效率和换算流量分别是其换算转速和压比函数值及导叶角的函数。
(2.11)2)涡轮的增压比、效率和换算流量的求法如下:
(1)附录4分别给出了高压涡轮、低压涡轮的特性数据。
利用线性插值法计算出涡轮的换算转速为、压比函数值为时的特性图上的增压
比、效率和换算流量。
(2)将(1)求的特性图上的增压比、效率和换算流量代入(2.12)修正后得到涡轮的增压比、效率和换算流量:
(2.12)分别是涡轮增压比、效率和换算流量的修正系数。
高压涡轮、低压涡轮这三个值均分别取1,1,0.01;高、低压涡轮导叶角变化范围:;高压涡轮:,低压涡轮:。
3)根据涡轮换算流量计算涡轮流量:
(2.13)其中,高压涡轮:,低压涡轮:。
4)涡轮出口总压;
5)涡轮出口总温根据下面公式(2.14)求出。
(2.14)其中:高压涡轮平均等压比热,低压涡轮平均等压比热,为气体常数。
6)求涡轮进口焓,其中为涡轮进口油气比;
7)求涡轮出口焓;
8)涡轮功和功率:
(2.15)其中,为涡轮机械效率.
2.5 涵道
2.5.1 已知
涵道进口总温、总压、流量、总压恢复系数。
2.5.2 计算过程
, 其中总压恢复系数
2.6 前混合器,选择活门,副外涵道建模
图1包含模式选择活门、副外涵道及CDFS涵道,高压压气机等。
图1 变循环发动机局部简图
图中数字序号表示发动机各截面参数定义的下脚标
2.6.1 已知
混合器两股参混气流参混前的总温、总压,副外涵、CDFS涵道出口面积和CDFS涵道出口流量。
2.6.2 计算过程
在已经给定副外涵、CDFS涵道出口面积的情况下,
1)CDFS涵道气流根据流量公式求出和,其中CDFS涵道出口面积,为CDFS涵道出口总压,为CDFS涵道出口总温,气动函数的定义及流量系数的取值见附录3;
2)由求出CDFS涵道出口静压;
3)由前混合器静压平衡和,求出和,为副外涵道出口总压;
4)由流量公式计算出副外涵道出口的流量。
其中副外涵面积(选择活门面积),为副外涵出口总温,为流量系数见附录3;
5)由下列公式(2.16)求出前混合器出口总温、总压、流量。
是由(2.16)的第二个公式求出的。
(2.16)
其中:,为前混合器出口焓,为前混合器CDFS涵道出口焓,为前混合器副外涵出口焓,为前混合器副外涵出口流量,为前混合器CDFS涵道出口流量,气动函数、的定义见附录3。
提示:,参考附录3。
2.7 后混合器
2.7.1 已知
混合器两股参混气流参混前的总温、总压、流量、面积。
2.7.2 计算过程
1)内涵气流根据流量公式求出和,其中内涵出口面积,为内涵出口总压,为内涵出口总温;
2)外涵气流根据流量公式求出和,其中外涵出口面积,为外涵出口总压,为外涵出口总温;
3)计算内涵静压,计算外涵静压;
4)由下列公式(2.17)求出混合器出口总温、总压、流量。
是由(2.17)的第二个公式求出的。
(2.17)其中:,为后混合器出口焓,为后混合器内涵出口焓,为后混合器外涵出口焓,为后混合器内涵出口流量,为后混合器外涵出口流量,气动函数、的定义见附录3。
注:必要时,后混合器出口总面积保持不变,内涵出口面积,外涵出口面积可以微调。
2.8 加力燃烧室
(2.18)
其中、分别为进出口总压,、分别为进出口总温,、分别为进出口流量,为总压恢复系数。
2.9 尾喷管
本文采用拉瓦尔(收敛-扩张)尾喷管(如图2所示)进行计算。
图2 拉瓦尔尾喷管示意图
提示:在拉瓦尔尾喷管中,任意截面总温、总压、流量均不变,则由流量公式可以得到:
因此在已知任意截面的面积或者,就可以求出该截面的参数。
拉瓦尔尾喷管有三种工作状态:临界、亚临界和超临界。
当处于临界时,尾喷管喉部,喉部之后气流变为超音速气流,尾喷管出口静压与大气压相等(完全膨胀);处于超临界时,喉部,此时尾喷管出口面积会自动改变(增大)使尾喷管出口静压与大气压相等,使尾喷管变为临界状态,但尾喷管出口面积有最大限制,当到达最大限制值时,尾喷管出口静压不能与大气压相等,则通过重新计算出口参数;处于亚临界时,喉部,喉部之后不能加速到超音速。
2.9.1 已知
尾喷管进口总温、总压、流量、大气环境压力(大气环境压力见进气道中公式(2.1))。
2.9.2 计算过程
1)计算尾喷管喉道面积,出口面积。
假设尾喷管始终处于临界或超临界状态,即速度系数。
(1)由流量公式计算出;
(2),计算出,并求出;
(3)由流量公式计算出;
(4)判断(这里),如果是,则,利用流量公式重新计算。
2)计算尾喷管出口静温;
3)尾喷管出口气流速度,其中:,焓和焓分别由尾喷管出口总温和静温求出。
3 计算发动机性能参数
1)推力:。
其中是发动机总燃气流量,包括进口空气流量和燃油流量之和,为总的空气流量,是飞行速度,可以根据求得,其中是大气静温,是尾喷管出口静压,是大气环境静压,是尾喷管出口面积,为气体绝热指数,为气体常数。
2)单位推力:。
3)耗油率:,其中是主燃烧室的燃油流量,是推力。