甲醇裂解制氢
甲醇裂解制氢装置VPSA脱碳部分的操作规程

甲醇裂解制氢装置VPSA脱碳部分的操作规程一、VPSA部分介绍1.装置规模公称产氢能力:10000Nm3/h;装置操作弹性:60〜110%;年生产时数:8000小时2.装置组成本单元由10台脱碳吸附塔和3台真空泵等设备组成。
3.工艺流程来自甲醇裂解部分的甲醇裂解气自塔底进入脱碳吸附塔。
其中绝大部分CO2 及一些杂质气体被吸附下来,脱碳后的氢气等气体进入提氢单元。
吸附塔吸附的CO2等气体通过真空泵抽真空被解吸后高点排放。
4.原料气规格本装置的设计允许原料气组分和压力在较宽的范围内变化,但在不同的原料气条件下吸附参数应作相应的调整以保证产品的质量,同时产品氢收率也将随原料而变化。
当原料气条件变化时,物料平衡也将发生相应的变化。
在原料气条件不变的情况下,所有的调节均可由计算机自动完成。
本单元设计的原料气为:甲醇裂解气其详细规格如下:5.产品规格本单元的主要产品为脱碳气,副产品为脱碳解吸气。
在实际生产中,脱碳气的纯度可通过改变PSA单元的操作条件进行调节,而解吸气的组成也会随原料气和产品气的不同而略有不同。
以下为设计的产品气规格:脱碳气脱碳气纯度:CO2 <3.98 v%脱碳气产量:13650Nm3/h脱碳气温度:40℃脱碳气压力:2.5MpaG脱碳解吸气脱碳解吸气温度:40℃脱碳解吸气压力:0.02MpaG二、工艺过程说明1.基本原理吸附是指:当两种相态不同的物质接触时,其中密度较低物质的分子在密度较高的物质表面被富集的现象和过程。
具有吸附作用的物质(一般为密度相对较大的多孔固体)被称为吸附剂,被吸附的物质(一般为密度相对较小的气体或液体)称为吸附质。
吸附按其性质的不同可分为四大类,即:化学吸着、活性吸附、毛细管凝缩、物理吸附。
其中物理吸附是指依靠吸附剂与吸附质分子间的分子力(即范德华力)进行的吸附。
其特点是:吸附过程中没有化学反应,吸附过程进行得极快,参与吸附的各相物质间的平衡在瞬间即可完成,并且这种吸附是完全可逆的。
甲醇制氢工艺过程及化学反应原理

工艺过程及化学反应原理一、甲醇裂解1.1.工艺过程甲醇催化转化制气工艺过程包括:原料汽化、催化转化反应、转化气冷却冷凝以及洗涤净化等。
1.1.1.原料汽化原料汽化是指,将甲醇和脱盐水按规定比例计量混合后,用泵加压送入系统进行预热、汽化过热至转化温度的过程。
完成此过程需:原料液罐(F102)、甲醇高位槽(F103)、原料液计量泵(J101A、B)、换热器(C102)、汽化过热器(C101)等设备及其配套仪表和阀门。
该工序目的是为催化转化反应提供规定的原料配比、温度、压力等条件。
1.1.2.催化转化反应在规定温度和压力下,原料混合气在转化器(D101)中,同时完成催化裂解和催化转化两个反应。
完成此反应过程仅需一台转化器(D101)及其配套仪表和阀门。
该工序的目的是完成化学反应,得到主要含有氢气和二氧化碳的转化气。
1.1.3.转化气冷却冷凝将转化器下部出来的高温转化气经冷却、冷凝降到常温。
完成该过程的设备有:换热器(C102)、冷凝器(C103)二台设备及其配套仪表和阀门。
该工序目的是降低转化气温度,将未反应的甲醇、水冷凝下来。
1.1.4.转化气洗涤净化经冷却冷凝后的低温转化气,进入净化塔(E101)用脱盐水洗涤回收未反应的甲醇和水的过程。
完成该过程的设备有:脱盐水计量泵(J102)、脱盐水储罐(F102)、净化塔(E101)、气液分离缓冲罐(F101)等设备及其配套仪表和阀门。
该工序目的是将转化气中未反应完的甲醇,洗涤净化后送PSA工段。
回收的水溶液去F102循环使用。
1.2.化学反应原理甲醇与水蒸汽混合物在转化器中加压催化裂解和转化一步完成,生成氢气和二氧化碳,其反应式如下:主反应:CH3OH=CO+2H2 -90.7kJ/molCO+H2O=CO2+H2 +41.2kJ/mol总反应:CH3OH+H2O=CO2+3H2 -49.5kJ/mol副反应:2CH3OH=CH3OCH3+H2O +24.90kJ/molCO+3H2=CH4+H2O +206.3kJ/mol二、PSAPSA提纯氢气装置是由七台吸附器(E201A~G,下简称A、B、C、D、E、F、G塔)、一台产品氢气缓冲罐(F201)、一台真空罐(F202)、两台真空泵(J201A/B)和一系列程控阀组成。
甲醇裂解制氢气生产流程的设备

甲醇裂解制氢气生产流程的设备一、反应器甲醇裂解制氢气的核心设备是反应器。
反应器是一个密封的容器,用于进行甲醇的裂解反应。
反应器通常由高温合金材料制成,具有良好的耐高温性能和抗腐蚀性能。
反应器内部设置有加热器和冷却器,用于控制反应温度。
二、加热器加热器是用来提供反应所需的高温热源。
甲醇裂解反应需要高温条件才能进行,通常需要在400-600摄氏度的温度范围内进行反应。
加热器可以使用电加热、燃气加热或者其他方式提供热源,将反应器内的温度升高到所需的反应温度。
三、冷却器冷却器用于控制反应器内的温度,防止反应温度过高引起不良反应。
冷却器通常采用水冷方式,通过水的循环来降低反应器内部的温度。
冷却器能够有效地控制反应器的温度,保证反应的顺利进行。
四、分离器分离器是用来分离反应产物中的氢气和其他组分的设备。
在甲醇裂解制氢气的过程中,反应产物中除了氢气外,还有一些副产物和未反应的甲醇。
分离器通过物理或化学方法将氢气与其他组分进行分离,得到纯净的氢气。
常用的分离方法包括压力摩擦吸附法(PSA)和膜分离法。
五、压缩机压缩机用于将产出的氢气进行压缩,使其达到所需的压力。
压缩机可以采用多级压缩的方式,将氢气逐级压缩至目标压力。
压缩机通常由高强度材料制成,具有良好的密封性和耐压性能。
六、储氢罐储氢罐用于存储压缩后的氢气。
储氢罐通常由高压容器制成,具有良好的密封性和耐压性能。
储氢罐可以根据需要选择不同的材料,如钢制储氢罐、复合材料储氢罐等。
七、安全设备甲醇裂解制氢气的生产过程中需要设置一系列的安全设备,以确保生产过程的安全性。
常见的安全设备包括防爆装置、泄漏报警装置、火焰监测装置等。
这些设备能够及时发现和处理可能出现的安全隐患,保障生产过程的安全运行。
甲醇裂解制氢气的生产流程涉及多个设备,包括反应器、加热器、冷却器、分离器、压缩机、储氢罐和安全设备等。
这些设备的合理选择和正确运行,对于保证甲醇裂解制氢气的生产效率和安全性具有重要意义。
甲醇裂解制氢工艺原理
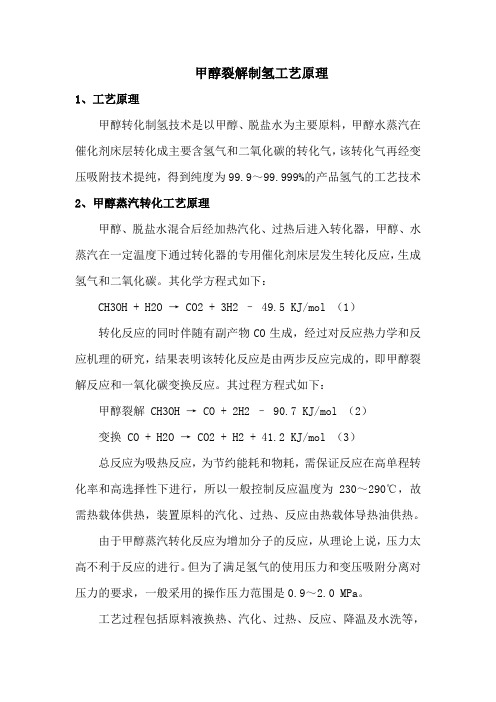
甲醇裂解制氢工艺原理1、工艺原理甲醇转化制氢技术是以甲醇、脱盐水为主要原料,甲醇水蒸汽在催化剂床层转化成主要含氢气和二氧化碳的转化气,该转化气再经变压吸附技术提纯,得到纯度为99.9~99.999%的产品氢气的工艺技术2、甲醇蒸汽转化工艺原理甲醇、脱盐水混合后经加热汽化、过热后进入转化器,甲醇、水蒸汽在一定温度下通过转化器的专用催化剂床层发生转化反应,生成氢气和二氧化碳。
其化学方程式如下:CH3OH + H2O → CO2 + 3H2 – 49.5 KJ/mol (1)转化反应的同时伴随有副产物CO生成,经过对反应热力学和反应机理的研究,结果表明该转化反应是由两步反应完成的,即甲醇裂解反应和一氧化碳变换反应。
其过程方程式如下:甲醇裂解 CH3OH → CO + 2H2 – 90.7 KJ/mol (2)变换 CO + H2O → CO2 + H2 + 41.2 KJ/mol (3)总反应为吸热反应,为节约能耗和物耗,需保证反应在高单程转化率和高选择性下进行,所以一般控制反应温度为230~290℃,故需热载体供热,装置原料的汽化、过热、反应由热载体导热油供热。
由于甲醇蒸汽转化反应为增加分子的反应,从理论上说,压力太高不利于反应的进行。
但为了满足氢气的使用压力和变压吸附分离对压力的要求,一般采用的操作压力范围是0.9~2.0 MPa。
工艺过程包括原料液换热、汽化、过热、反应、降温及水洗等,转化气送出前先进行水洗不但可回收夹带的甲醇、降低甲醇消耗,而且可大大降少从弛放气排出的甲醇量,有利于环境保护。
3、变压吸附气体分离技术工艺原理研究发现一些具有发达微孔结构的固体材料对流体分子具有吸附作用,这类吸附材料被称为吸附剂。
当流体分子与固体吸附剂接触后,吸附作用随即会发生。
吸附过程有以下特性:(1)吸附剂对气体的吸附有选择性,即不同气体在吸附剂上的吸附量是有差别的;(2)气体在吸附剂上的吸附量随其分压的降低而减少。
一种甲醇裂解制氢尾气回收利用方法
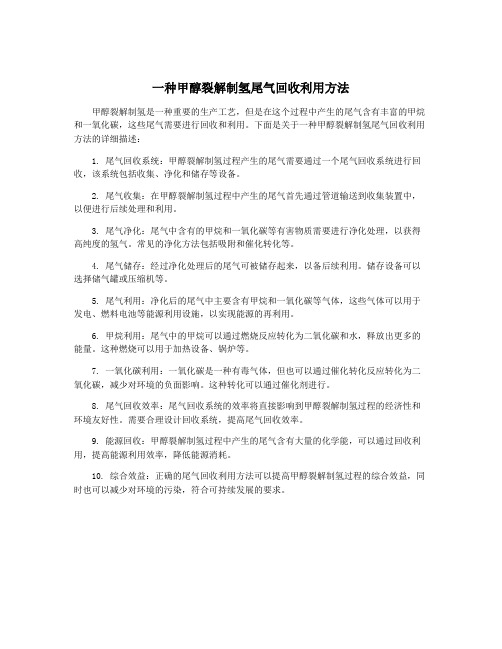
一种甲醇裂解制氢尾气回收利用方法
甲醇裂解制氢是一种重要的生产工艺,但是在这个过程中产生的尾气含有丰富的甲烷和一氧化碳,这些尾气需要进行回收和利用。
下面是关于一种甲醇裂解制氢尾气回收利用方法的详细描述:
1. 尾气回收系统:甲醇裂解制氢过程产生的尾气需要通过一个尾气回收系统进行回收,该系统包括收集、净化和储存等设备。
2. 尾气收集:在甲醇裂解制氢过程中产生的尾气首先通过管道输送到收集装置中,以便进行后续处理和利用。
3. 尾气净化:尾气中含有的甲烷和一氧化碳等有害物质需要进行净化处理,以获得高纯度的氢气。
常见的净化方法包括吸附和催化转化等。
4. 尾气储存:经过净化处理后的尾气可被储存起来,以备后续利用。
储存设备可以选择储气罐或压缩机等。
5. 尾气利用:净化后的尾气中主要含有甲烷和一氧化碳等气体,这些气体可以用于发电、燃料电池等能源利用设施,以实现能源的再利用。
6. 甲烷利用:尾气中的甲烷可以通过燃烧反应转化为二氧化碳和水,释放出更多的能量。
这种燃烧可以用于加热设备、锅炉等。
7. 一氧化碳利用:一氧化碳是一种有毒气体,但也可以通过催化转化反应转化为二氧化碳,减少对环境的负面影响。
这种转化可以通过催化剂进行。
8. 尾气回收效率:尾气回收系统的效率将直接影响到甲醇裂解制氢过程的经济性和环境友好性。
需要合理设计回收系统,提高尾气回收效率。
9. 能源回收:甲醇裂解制氢过程中产生的尾气含有大量的化学能,可以通过回收利用,提高能源利用效率,降低能源消耗。
10. 综合效益:正确的尾气回收利用方法可以提高甲醇裂解制氢过程的综合效益,同时也可以减少对环境的污染,符合可持续发展的要求。
甲醇裂解制氢含甲醇蒸汽转化和变压吸附制氢两部分
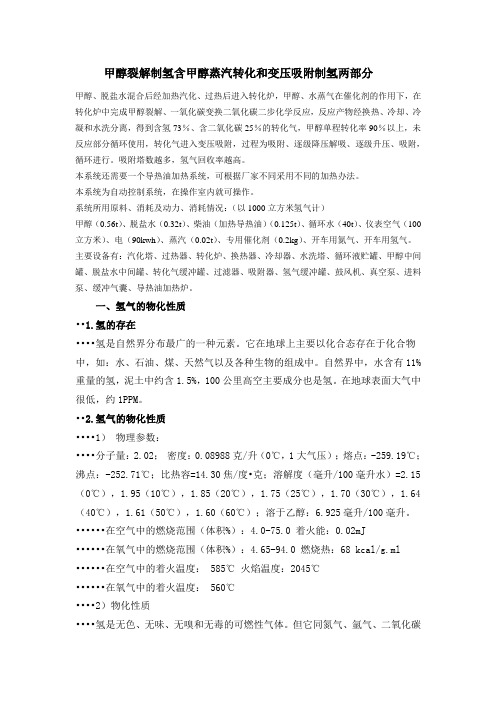
甲醇裂解制氢含甲醇蒸汽转化和变压吸附制氢两部分甲醇、脱盐水混合后经加热汽化、过热后进入转化炉,甲醇、水蒸气在催化剂的作用下,在转化炉中完成甲醇裂解、一氧化碳变换二氧化碳二步化学反应,反应产物经换热、冷却、冷凝和水洗分离,得到含氢73%、含二氧化碳25%的转化气,甲醇单程转化率90%以上,未反应部分循环使用,转化气进入变压吸附,过程为吸附、逐级降压解吸、逐级升压、吸附,循环进行。
吸附塔数越多,氢气回收率越高。
本系统还需要一个导热油加热系统,可根据厂家不同采用不同的加热办法。
本系统为自动控制系统,在操作室内就可操作。
系统所用原料、消耗及动力、消耗情况:(以1000立方米氢气计)甲醇(0.56t)、脱盐水(0.32t)、柴油(加热导热油)(0.125t)、循环水(40t)、仪表空气(100立方米)、电(90kwh)、蒸汽(0.02t)、专用催化剂(0.2kg)、开车用氮气、开车用氢气。
主要设备有:汽化塔、过热器、转化炉、换热器、冷却器、水洗塔、循环液贮罐、甲醇中间罐、脱盐水中间罐、转化气缓冲罐、过滤器、吸附器、氢气缓冲罐、鼓风机、真空泵、进料泵、缓冲气囊、导热油加热炉。
一、氢气的物化性质••1.氢的存在••••氢是自然界分布最广的一种元素。
它在地球上主要以化合态存在于化合物中,如:水、石油、煤、天然气以及各种生物的组成中。
自然界中,水含有11%重量的氢,泥土中约含1.5%,100公里高空主要成分也是氢。
在地球表面大气中很低,约1PPM。
••2.氢气的物化性质••••1)物理参数:••••分子量:2.02;密度:0.08988克/升(0℃,1大气压);熔点:-259.19℃;沸点:-252.71℃;比热容=14.30焦/度•克;溶解度(毫升/100毫升水)=2.15(0℃),1.95(10℃),1.85(20℃),1.75(25℃),1.70(30℃),1.64(40℃),1.61(50℃),1.60(60℃);溶于乙醇:6.925毫升/100毫升。
甲醇裂解制纯氢及CO技术

甲醇裂解制纯氢及CO技术3甲醇转化制取400Nm/h 纯氢及CO合成气装臵时间:项目名称:甲醇转化制取400Nm3/h 纯氢及CO合成气装臵业主:建设地点:一产品规格及规模纯度(V/V) ?99.9% 氢压力 MPa(G) 1.0气温度 ? ?40.0产量 Nm3/h 210纯度(V/V) ?50% 不含氧、HO 2CO压力 MPa(G) ?0.02 合成温度 ? ?40.0 气产量 Nm3/h 190 二装臵能力 1 公称能力 Nm3/h 400 2 年生产时数小时 ?8200 3 装臵运行方式连续运行 4 操作弹性 40--110% 三装臵消耗 1 甲醇 kg/h ~243.43 符合GB338-92,工业一级氯离子?0.1mg/l,电导2 脱盐水 Kg/h ~2.46 率?10μS/cm 3 循环水 m3/h ~50.0 循环量包括机泵、真空泵用电及4 电 KWh/h ~40.0 车间照明 5 仪表空气 Nm3/h ~30.0 四三废排放量1 废水 t/h 无本装臵基本无废水排放本装臵解析气即为产品2 废气 Nm3/h 无 CO合成气催化剂 490.8 年平均更新的催化剂、吸3 废渣 kg/年吸附剂 744.2 附剂(可回收) 4 废液 t/年未反应甲醇及副产物回烧处理2五装臵占地面积 m ~200 根据现场情况具体确定六装臵定员人 8 按四班三运转考虑组分合计名称单位一氧化二氧化甲醇脱盐水氢气甲烷二甲醚碳碳mol% 99.00% 1.00% 100.00% 1 原料Kg/h 243.43 2.46 245.88V% 4.75% 0.43% 61.64% 27.50% 2.37% 0.57% 2.75% 100.00% 裂解2 Nm3/h 20.45 1.84 265.31 118.37 10.20 2.45 11.84 430.45 气Kg/h 29.21 1.48 23.69 147.96 20.04 1.75 21.76 245.88V% 60.45% 2.34% 37.21% 净化3 分离 Kg/h 28.18 1.09 17.35 46.62V% 99.99% 0.01% 100.00% 产品4 Nm3/h 209.98 0.02 210.00 氢气Kg/h 18.75 0.01 18.76V% 0.38% 0.25% 29.13% 62.32% 5.37% 1.29% 1.26% 100.00% 解析5 Nm3/h 0.72 0.48 55.33 118.37 10.20 2.45 2.40 189.95 气Kg/h 1.03 0.39 4.94 147.96 20.04 1.75 4.41 180.521.1.1 工艺指标, 压力 ?1.0MPa(表压G), 温度 ?40?3, 流量210Nm/h, 纯度 ?99.9%(V/V) 1.1.2 生产规模3, 210Nm/h氢气,弹性范围40~110%。
甲醇制氢

3、当汽化塔塔釜液位达10%时,开启汽化塔顶放空 阀,缓慢开启塔釜导热油进口阀旁路阀、前后阀,用 调节阀调节进汽化塔导热油量。当塔顶排放气量稳定 时,开启过热器底部排污阀,无液珠排出时关闭排污 阀,即可转入转化炉开车。
变压吸附
变压吸附气体分离技术有3个主要要素,即 吸附剂、 程序控制阀和操作工艺
吸附剂
用于甲醇裂解气变压吸附分离的吸附剂, 经多次研制改进、筛选,强度、寿命、对 杂质的动态吸附量、分离效率等各方面性 能达到世界先进水平,氢气回收率可达 90%。
程控阀
变压吸附装置中使用的程序控制阀现采用 的是防冲刷、阀杆密封自补偿型的第四代 气动程序控制阀,具有密封性好、外泄漏 量小、使用寿命长等特点
与氨裂解制氢技术相比具有反应条件 温和,原料运输和储存方便。
工艺原理
本工艺以来源方便的甲醇和脱盐水为原料,在220~ 280℃下,专用催化剂上催化转化为组成为主要含氢和 二氧化碳转化气。
其原理如下:
主反应: CH3OH=CO+2H2
+90.7 KJ/mol
CO+H2O=CO2+H2 -41.2 KJ/mol
检查消防和安全设施是否齐备完好。
操作人员、分析人员、管理和维修人员经 技术培训,并考核合格方能上岗。
2 开车操作程序 投料开车程序应在催化剂还原结束后进行,
无时间间隔。开车时序一般为:水冼塔开车、汽 化塔开车、转化炉开车、系统升压。还原结束后, 关闭还原系统阀,开启转化炉后直到放空管线间 所有阀门,关闭有关阀门,准备系统开车。
- 1、下载文档前请自行甄别文档内容的完整性,平台不提供额外的编辑、内容补充、找答案等附加服务。
- 2、"仅部分预览"的文档,不可在线预览部分如存在完整性等问题,可反馈申请退款(可完整预览的文档不适用该条件!)。
- 3、如文档侵犯您的权益,请联系客服反馈,我们会尽快为您处理(人工客服工作时间:9:00-18:30)。
甲醇裂解制氢技术早已成熟,由于水电解制氢设备费用昂贵,耗电量大,氨分解制氢仅对氢氮混合气的制取有明显的经济效果外,而甲醇裂解在某些用氢场合又显得有特殊的经济效果,甲醇是石油化工的一种产物,目前市声上供应比较充足,价格明显低于液氨,而且运输、储存比较方便和安全。
因此甲醇裂解制氢逐步大量推广,有广阔的前景。
甲醇裂解制氢通常将有如下方式:
1.无水甲醇 CH3OH→CO+2H2可得66.7%H2和33.3%CO;
2.甲醇+水 CH3OH+H2O→CO2+H2可得75%H2和25%CO2
上述裂解的混合气,可以用钯管或PSA分离得到含氢99.9%以上的纯氢。
一般小气量情况下应用钯管,大气量情况下应用PSA法提取纯氢,还可以从甲醇裂解中获取二氧化碳。
甲醇裂解制氢装置工艺流程:
甲醇和蒸馏水以一定的比例混合后,经过滤器和计量泵、流量计入汽化器,转为气相后,进入裂炉,内装催化剂,反应温度可控制在300℃左右,裂解气可经过吸收二氧化碳塔来回收二氧化碳,也可直接进入钯管膜或PSA分离装置来提取纯
氢。
氢气纯度达99.999%.。