低压羰基合成丁辛醇工艺技术
丁辛醇生产技术及其发展趋势
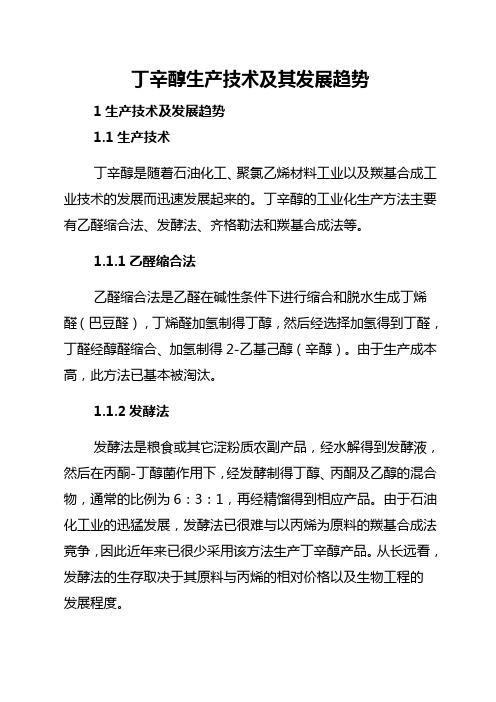
丁辛醇生产技术及其发展趋势1生产技术及发展趋势1.1生产技术丁辛醇是随着石油化工、聚氯乙烯材料工业以及羰基合成工业技术的发展而迅速发展起来的。
丁辛醇的工业化生产方法主要有乙醛缩合法、发酵法、齐格勒法和羰基合成法等。
1.1.1乙醛缩合法乙醛缩合法是乙醛在碱性条件下进行缩合和脱水生成丁烯醛(巴豆醛),丁烯醛加氢制得丁醇,然后经选择加氢得到丁醛,丁醛经醇醛缩合、加氢制得2-乙基己醇(辛醇)。
由于生产成本高,此方法已基本被淘汰。
1.1.2发酵法发酵法是粮食或其它淀粉质农副产品,经水解得到发酵液,然后在丙酮-丁醇菌作用下,经发酵制得丁醇、丙酮及乙醇的混合物,通常的比例为6:3:1,再经精馏得到相应产品。
由于石油化工业的迅猛发展,发酵法已很难与以丙烯为原料的羰基合成法竞争,因此近年来已很少采用该方法生产丁辛醇产品。
从长远看,发酵法的生存取决于其原料与丙烯的相对价格以及生物工程的发展程度。
1.1.3齐格勒法齐格勒丁辛醇生产方法是以乙烯为原料,采用齐格勒法生产高级脂肪醇,同时副产丁醇的方法。
1.1.4羰基合成法羰基合成法是当今最主要的丁辛醇生产技术。
丙烯羰基合成生产丁辛醇工艺过程:丙烯氢甲酰化反应,粗醛精制得到正丁醛和异丁醛,正丁醛和异丁醛加氢得到产品正丁醇和异丁醇;正丁醛经缩合、加氢得到产品辛醇。
丙烯羰基合成法又分为高压法、中压法和低压法。
丙烯羰基合成法的主流技术专利商如下:高压法:鲁尔 (Ruhr)技术、巴斯夫(BASF)技术、三菱(MCC)技术、壳牌(Shell)技术。
中压法:壳牌(Shell)技术、鲁尔-化学(Ruhr-chemic)技术、三菱(MCC)铑法技术。
低压法:雷普法(Reppe)技术、伊士曼(Eastman)技术、戴维(Davy UCC Johnson Matthey)技术、三菱化成(MCC)技术。
高压的羰基合成技术由于选择性较差、副产品(丙烷和高沸物)多,已被以铑为催化剂的低压羰基合成技术所取代。
低压羰基合成丁辛醇工艺技术

低压羰基合成丁辛醇工艺技术摘要:低压羰基合成法是目前生产丁辛醇的主要方法。
世界上羰基合成丁醛装置中,低压羰基合成工艺技术占55%。
丁辛醇装置以丙烯、合成气为原料,采用Davy/DOW低压羰基合成工艺技术生产2-乙基己醇和正丁醇,同时副产异丁醇,设计年运行时间为8000小时,操作弹性为60%~110%。
关键词:低压羰基;丁辛醇;工艺技术;分析引言:丁辛醇装置采用世界较为先进的LP OxoSM SELECTORSM 10液体循环技术,生产2-乙基己醇(俗称辛醇)和正丁醇,它以丙烯和合成气为原料,在铑、三苯基膦催化剂的作用下,发生羰基合成反应生成混合丁醛,丁醛经过丁醛异构物分离得到高纯度正丁醛,在0.2×10-2mol的NaOH溶液作用下,发生缩合反应生成辛烯醛,辛烯醛在铜催化剂作用下与H2发生加氢反应生成粗辛醇,再经过精制后得到产品辛醇;混合丁醛加氢后得到粗混合丁醇,经过预精馏和精馏系统进入丁醇异构物塔。
丁醇异构物塔顶分离出的混合丁醛也可直接进行异构物分离得到正丁醛和异丁醛,异丁醛直接外送至界外,正丁醛经加氢、精制后,得到产品正丁醇。
1.低压羰基合成丁辛醇技术七十年代中期,美国UCC公司、英国DAVY公司和J.M公司合作开发了铑膦催化体系─低压羰基合成工艺。
压力1.6-1.8MPa,正异比高达10:1~12:1,基建投资和生产成本均低于高、中压羰基合成技术。
1.1气相法将催化剂加入并联的两台反应器中,丙烯、合成气按一定比例分别从反应器和分馏塔底部进入。
产品由循环气带出,经冷凝、分离后,由分馏塔底部采出,过量气体循环进入反应系统,催化剂留在反应器内直至失效取出再生。
因该羰基合成反应为气相反应,故称气相法。
1.2液相法液相法是以丙烯、合成气为原料,以铑为催化剂生产丁辛醇的低压羰基合成法,是低压羰基合成的进一步改进。
其优点是:一是反应器容积小,产率高;二是原料单耗降低;三是成本及能耗降低;四是催化剂使用形式为活性循环型;五是反应温度低,可用于生产高碳醇。
丁辛醇工艺技术进展及选择
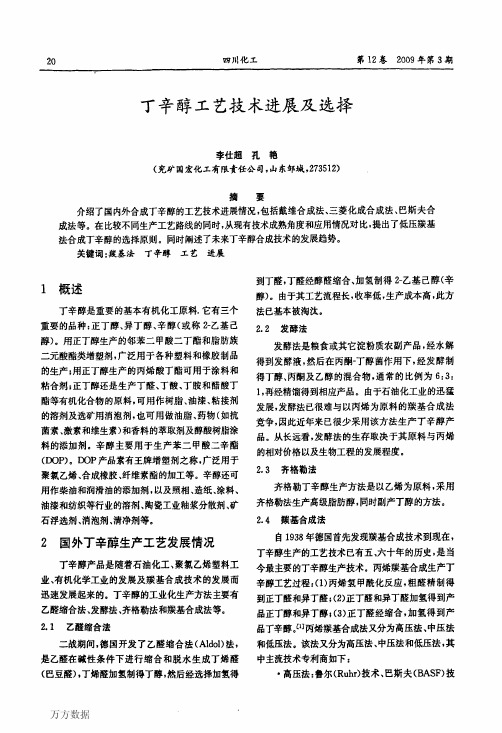
1。[2t引
(2)吉林石化公司研究院于2001年成功开发了 国内首创的辛烯醛高压液相加氢制辛醇催化剂,经 在吉化化肥厂丁辛醇装置上两年的应用证明,可以
丙爆一
问1j】换
谨记翘再 生与琅缩 I
I糯辛尊(:.乙基己尊)
蛩吨囹一异丁啐
对材质的要求最低,大部为碳钢,少量的为304不锈 钢;从流程的长度和装置的复杂性来说,戴维的最 短、最简单;从使用的情况看,戴维合成工艺使用最 多;但是伊斯曼乙烯一丙烯共迸料工艺技术可同时生 产丁醛和丙醛,产品灵活多样,对市场变化有较好的
法合成丁辛醇的选择原则。同时阐述了未来丁辛醇合成技术的发展趋势。
关键词:羰基法丁辛醇工艺进展
1概述
丁辛醇是重要的基本有机化工原料.它有三个
重要的品种:正丁醇、异丁醇、辛醇(或称2一乙基己
到丁醛,丁醛经醇醛缩合、加氢制得2一乙基己醇(辛 醇)。由于其工艺流程长,收率低,生产成本高,此方
法已基本被淘汰。
125 2.5 3~10/l ~9l 332
50
无铁丁醛 三苯基膦羰基铑 催化剂 蒸发分离、 液相循环 ∞~95
1.8~1.9 4~25/I 91~93
278.8
5
催化剂 催化剂 蒸发分离,
6
催化剂分离方式 液相循环 温度℃ 1∞
2 8~9/1
%
7
主要技术参 数
压力-眈
正/异比 转化率 循环水 电
~%
巴斯夫羰基合成工艺采用铑化合物为催化剂,
万方数据
四川化工 近年来,联碳与戴维公司又开发了第四代低压
丁辛醇生产工艺
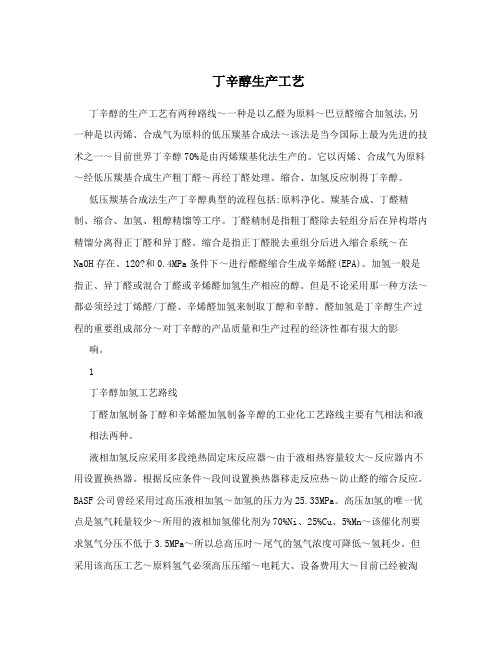
丁辛醇生产工艺丁辛醇的生产工艺有两种路线~一种是以乙醛为原料~巴豆醛缩合加氢法,另一种是以丙烯、合成气为原料的低压羰基合成法~该法是当今国际上最为先进的技术之一~目前世界丁辛醇70%是由丙烯羰基化法生产的。
它以丙烯、合成气为原料~经低压羰基合成生产粗丁醛~再经丁醛处理、缩合、加氢反应制得丁辛醇。
低压羰基合成法生产丁辛醇典型的流程包括:原料净化、羰基合成、丁醛精制、缩合、加氢、粗醇精馏等工序。
丁醛精制是指粗丁醛除去轻组分后在异构塔内精馏分离得正丁醛和异丁醛。
缩合是指正丁醛脱去重组分后进入缩合系统~在NaOH存在、120?和0.4MPa条件下~进行醛醛缩合生成辛烯醛(EPA)。
加氢一般是指正、异丁醛或混合丁醛或辛烯醛加氢生产相应的醇。
但是不论采用那一种方法~都必须经过丁烯醛/丁醛、辛烯醛加氢来制取丁醇和辛醇。
醛加氢是丁辛醇生产过程的重要组成部分~对丁辛醇的产品质量和生产过程的经济性都有很大的影响。
1丁辛醇加氢工艺路线丁醛加氢制备丁醇和辛烯醛加氢制备辛醇的工业化工艺路线主要有气相法和液相法两种。
液相加氢反应采用多段绝热固定床反应器~由于液相热容量较大~反应器内不用设置换热器。
根据反应条件~段间设置换热器移走反应热~防止醛的缩合反应。
BASF公司曾经采用过高压液相加氢~加氢的压力为25.33MPa。
高压加氢的唯一优点是氢气耗量较少~所用的液相加氢催化剂为70%Ni、25%Cu、5%Mn~该催化剂要求氢气分压不低于3.5MPa~所以总高压时~尾气的氢气浓度可降低~氢耗少。
但采用该高压工艺~原料氢气必须高压压缩~电耗大、设备费用大~目前已经被淘汰。
BASF公司和三菱化成工艺中醛的加氢采用中压液相加氢工艺~加氢压力为4.0-5.0MPa~加氢反应器形式采用填充床~反应温度为60-190?。
气相加氢法由于操作压力相对较低~工艺设备简单而被广泛应用。
目前~工业上丁辛醇装置上大多采用铜系催化剂气相加氢工艺。
如U.D.J联合工艺中采用低压气相加氢~压力为0.59-0.69MPa。
丁辛醇装置工艺技术分析
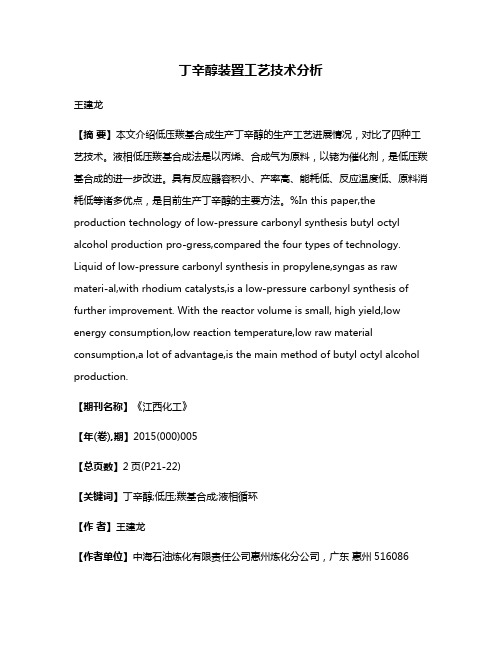
丁辛醇装置工艺技术分析王建龙【摘要】本文介绍低压羰基合成生产丁辛醇的生产工艺进展情况,对比了四种工艺技术。
液相低压羰基合成法是以丙烯、合成气为原料,以铑为催化剂,是低压羰基合成的进一步改进。
具有反应器容积小、产率高、能耗低、反应温度低、原料消耗低等诸多优点,是目前生产丁辛醇的主要方法。
%In this paper,the production technology of low-pressure carbonyl synthesis butyl octyl alcohol production pro-gress,compared the four types of technology. Liquid of low-pressure carbonyl synthesis in propylene,syngas as raw materi-al,with rhodium catalysts,is a low-pressure carbonyl synthesis of further improvement. With the reactor volume is small, high yield,low energy consumption,low reaction temperature,low raw material consumption,a lot of advantage,is the main method of butyl octyl alcohol production.【期刊名称】《江西化工》【年(卷),期】2015(000)005【总页数】2页(P21-22)【关键词】丁辛醇;低压;羰基合成;液相循环【作者】王建龙【作者单位】中海石油炼化有限责任公司惠州炼化分公司,广东惠州516086【正文语种】中文丁辛醇是随着石油化工、聚乙烯塑料工业的发展和羰基合成工业技术的发展迅速发展起来的。
低压羰基合成丁辛醇工艺技术王琪

低压羰基合成丁辛醇工艺技术王琪发布时间:2021-09-23T08:13:01.767Z 来源:《中国科技人才》2021年第16期作者:王琪[导读] 作为化工生产中的基础性化工材料之一,丁辛醇可用于橡胶制品生产环节,可作为增塑剂使用,也属于良好的脱水剂与消泡剂,还具备溶剂的功能。
在丁辛醇生产过程中,主要应用的是低压羰基合成技术。
文章将以低压羰基合成技术的分析入手,分别对其三种合成方法进行阐述,而后概述了当前我国丁辛醇工艺技术的发展状况,并展望了未来丁辛醇生产工艺的发展方向。
大庆石化公司化工二厂丁辛醇造气车间摘要:作为化工生产中的基础性化工材料之一,丁辛醇可用于橡胶制品生产环节,可作为增塑剂使用,也属于良好的脱水剂与消泡剂,还具备溶剂的功能。
在丁辛醇生产过程中,主要应用的是低压羰基合成技术。
文章将以低压羰基合成技术的分析入手,分别对其三种合成方法进行阐述,而后概述了当前我国丁辛醇工艺技术的发展状况,并展望了未来丁辛醇生产工艺的发展方向。
关键词:丁辛醇;低压羰基;工艺技术;发展方向丁辛醇因可利用同一装置采用羰基合成方法同步制备丁醇与辛醇而得名,合成后可得到油状透明液体,其属于无色、可燃性液体,可在化工生产中可作为精细原料而使用,除了化工领域之外,在医药、食品等其他行为具有较高的应用价值。
基于此,了解丁辛醇的生产工艺,探究利用低压羰基合成此材料的具体方法具有重要意义。
1.基于低压羰基合成的丁辛醇技术分析根据合成中所用压力的高低不同,可将低压羰基合成丁辛醇技术分为三种工艺类别,具体如下: 1.1戴维合成技术这是一种源于英美两国,诞生于上世纪七十年代的丁辛醇合成技术,该时期美国研制出了首台铑法低压羰基合成装置,可以丙烯原料以及合成气为基础,在羰基铑的催化作用下进行丁辛醇的合成,所属压力仅为1.76MPa即可。
属于一种低压合成方法。
此合成方式无需应用大量设备,对反应条件没有较高要求,并且操过程便捷简单,所应用的催化剂具有较高活性,此技术一经推出便得到了广泛应用。
丁辛醇生产技术及发展

2. 2 国内发展概况 我国的丁辛醇生产技术在 1980 年以前主要采 用粮食发酵法制丁醇 ;采用乙醛缩合制巴豆醛 (丁烯 醛) ,巴豆醛缩合 、加氢制辛醇 。由于工艺技术落后 , 这一类的丁辛醇生产装置均已停产 。 1976 年 , 吉化公司从德国 BASF 公司引进 50 kt/ a 年的高压钴法丁辛醇装置 , 1982 年建成投产 。 随后 ,大庆石化总厂 、齐鲁石化公司从英国 DAV Y 公 司成套引进丁辛醇生产技术 ,并在 1986 年 、1987 年 相继投产 。 1992 年北京化工四厂从日本三菱化学公司引进 丁辛醇生产的专利技术及关键设备 , 于 1996 年投 产。 1996 年齐鲁石化公司在原有装置基础上 ,将原 来低压羰基合成气相循环法改为液相循环法 ,在反 应器不变的情况下 ,将产量扩大为原产量的 1. 9 倍 。 1998 年吉化公司对原有的 BASF 高压羰基合成装置 进行改造 ,引进了 UCC/ DAV Y 第四代低压液相循环 羰基合成技术 ,在保留了原装置的异构物分离 、丁醛 缩合 、辛烯醛液相加氢 、醇的精馏分离等几部分基础 上 ,另外扩建了一套气相加氢 、丁醛缩合 、液相加氢 、 醇精馏分离系统 ,改造后装置于 2000 年 8 月投产 ,目 前吉化公司丁醇 、辛醇合计最大生产能力可达 120 kt/ a 。 3 丁辛醇生产技术概况 丁辛醇的生产工艺有两种路线 ,一种是以乙醛 为原料 ,巴豆醛缩合加氢法 ;另一种是以丙烯为原料 的羰基合成法 ,
丁辛醇装置铑催化剂的失活与活化

丁辛醇装置铑催化剂的失活与活化摘要:国内大部分丁辛醇装置采用DAVY/DOW低压法催化剂羰基合成工艺。
该工艺以丙烯、合成气为原料,在铑催化剂作用下反应生成混合丁醛,其中正丁醛经缩合反应后生成辛烯醛(EPA),EPA再通过加氢生成辛醇;混合丁醛加氢生产丁醇。
羰基合成单元是丁辛醇生产装置的核心,反应过程中采用均相络合物铑膦催化体系,以铑原子为活性中心,以三苯基膦为配位体,在一定条件下添加过量的三苯基膦时可使产物的正异构比提高到20∶1以上。
但贵重金属铑资源稀少、制作工艺复杂,价格十分昂贵。
在正常生产中,少部分催化剂随产品带走,其活性亦随生产周期的延长及毒物的积累逐渐降低,直至完全失活而无法使用,使用寿命设计约为1.5a。
关键词:丁辛醇装置;铑催化剂;失活;活化;分析引言::2017年之前原料丙烯主要为化工一厂裂解聚合级丙烯和化学级丙烯,随着烯烃裂解工艺改进,化学级丙烯产量越来越少,而聚合级丙烯还要供应异丁醛装置和新上聚丙烯装置,烯烃裂解丙烯产量已不能满足丁辛醇装置生产负荷的要求。
因此,2017年初针对将炼油厂气体分离装置所产丙烯用做丁辛醇装置原料进行了可研分析,并在2017年上半年完成了相应的设计与改造。
炼油厂丙烯应用于丁辛醇生产在之前尚无先例,无经验可借鉴。
目前国内大部分丁辛醇生产装置都是采用英国戴维工艺技术有限公司的低压羰基合成工艺,其中的羰基合成反应是整个工艺的核心。
羰基合成反应的铑催化剂是以铑(Rh)原子为中心,三苯基膦和一氧化碳作为配位体的络合物,为淡黄色结晶体,它的主要特点为:异构化能力弱、加氢活性低、选择性高、反应速度快,几乎为钴催化剂的102-103倍。
其铑催化剂的活性对整个反应至关重要,影响着整个装置的经济效益。
1.试验部分1.1铑膦催化剂失活原理铑膦催化剂是以铑(Rh)原子为中心、三苯基膦(TPP)和一氧化碳作为配位体的络合物,淡黄色结晶体。
其主要特点:异构化能力弱、加氢活性低、选择性高、反应速度快,几乎为钴催化剂的100-1000倍。
- 1、下载文档前请自行甄别文档内容的完整性,平台不提供额外的编辑、内容补充、找答案等附加服务。
- 2、"仅部分预览"的文档,不可在线预览部分如存在完整性等问题,可反馈申请退款(可完整预览的文档不适用该条件!)。
- 3、如文档侵犯您的权益,请联系客服反馈,我们会尽快为您处理(人工客服工作时间:9:00-18:30)。
低压羰基合成丁辛醇工艺技术
摘要:低压羰基合成法是目前生产丁辛醇的主要方法。
世界上羰基合成丁醛装
置中,低压羰基合成工艺技术占55%。
丁辛醇装置以丙烯、合成气为原料,采用Davy/DOW低压羰基合成工艺技术生产2-乙基己醇和正丁醇,同时副产异丁醇,设计年运行时间为8000小时,操作弹性为60%~110%。
关键词:低压羰基;丁辛醇;工艺技术;分析
引言:丁辛醇装置采用世界较为先进的LP OxoSM SELECTORSM 10液体循环技术,生产2-乙基己醇(俗称辛醇)和正丁醇,它以丙烯和合成气为原料,在铑、三苯基膦催化剂的作用下,发生羰基合成反应生成混合丁醛,丁醛经过丁醛异构物分离得到高纯度正丁醛,在0.2×10-2mol的NaOH溶液作用下,发生缩合反应生成辛烯醛,辛烯醛在铜催化剂作用下与H2发生加氢反应生成粗辛醇,再经过精制后得到产品辛醇;混合丁醛加氢后得到粗混合丁醇,经过预精馏和精馏系统进入丁醇异构物塔。
丁醇异构物塔顶分离出的混合丁醛也可直接进行异构物分离得到正丁醛和异丁醛,异丁醛直接外送至界外,正丁醛经加氢、精制后,得到产品正丁醇。
1.低压羰基合成丁辛醇技术
七十年代中期,美国UCC公司、英国DAVY公司和J.M公司合作开发了铑膦催化体系─低压羰基合成工艺。
压力1.6-1.8MPa,正异比高达10:1~12:1,基建投资和生产成本均低于高、中压羰基合成技术。
1.1气相法
将催化剂加入并联的两台反应器中,丙烯、合成气按一定比例分别从反应器和分馏塔底部进入。
产品由循环气带出,经冷凝、分离后,由分馏塔底部采出,过量气体循环进入反应系统,催化剂留在反应器内直至失效取出再生。
因该羰基合成反应为气相反应,故称气相法。
1.2液相法
液相法是以丙烯、合成气为原料,以铑为催化剂生产丁辛醇的低压羰基合成法,是低压羰基合成的进一步改进。
其优点是:一是反应器容积小,产率高;二是原料单耗降低;三是成本及能耗降低;四是催化剂使用形式为活性循环型;五是反应温度低,可用于生产高碳醇。
同气相法相比,液相法进一步降低了原料消耗、能耗
及成本。
使用等规模的反应器,将气相法改为液相法生产丁辛醇,可使丙烯利用率
提高4%,生产能力提高80%左右。
1.3气相法与液相法工艺技术评析
气相法的特点是,催化剂活性高,但消耗定额较高;操作温度、压力低;正异比较高;不需特殊材质,流程短,设备少;操作维修量少;工艺先进。
液相法工艺不但催化剂活性高,选择性强,且装置内可回收再生催化剂,原材料和动力消耗定额低,操作温度、压力低;正异比较高;生产过程中不产生腐蚀介质,不需特殊材质;流程短,设备少;操作平稳,维修方便。
目前,液相法处于世界领先地位。
1.4新催化剂技术
由于铑的储量少,价格昂贵。
因此国外除了开发对铑催化剂的活化回收外,还积极开展铂系催化剂等非铑催化剂的研究。
如壳牌(Shell)公司开发的铂离子络合催
化剂,性能优于铑催化剂。
同时,国外还在开发非贵金属化合物作羰基合成催化剂,
如美国联碳公司采用的非均相催化剂,用来生产丁醇;此外还开发研究了固定床载
体催化剂;以及羰基铁、羰基钌等催化剂。
2.低压羰基法合成丁辛醇工艺的技术分析
2.1生产工艺流程
低压羰基法合成丁辛醇的工艺流程主要可以划分为两个单元。
其一为羰基合
成单元,重要的装置构成为:净化合成气、反应装置系统、分离异物等。
其二为
辛烯醛单元,主要通过缩合的形式进行反应等装置构成。
在羰基进行合成的过程中,合成气会与C3H6产生反应,形成C4H8O,具体的正异构的比大概为(7∶1)-(10∶1)。
但是在辛烯醛的单元中,C4H8O是利用缩合反应形成的,中间所形
成的产物为辛烯醛,利用催化并且加氢气实施处理之后,才能产生辛醇。
2.2羰基合成单元
净化分离装置是C3H6与混合合成气的原料首先通过的工序,其作用在于将
催化剂当中含有的毒性物质去除,例如:O2、氯化物等。
一般情况下,羰基合成
反应会在催化剂当中进行,将催化剂加入之后能够让反应的整个过程在比较低的
温度和比较低的压力下实施。
C3H6在与相关的合成气发生具体的反应之后,可以产生正丁醇以及异丁醇混合物,借助不同的两个压力段,进行相关的蒸发处置,
之后实施液相循环。
在这个过程当中,在反应的产物以及副产物混合物液相当中
会将催化剂溶解,以便得以保留。
在具体进行反应的过程中,所产生的丁醇相关
产物,会在气提塔当中溶解气进行气提,在分离塔中,可将正构物以及异构物进
行分离,在原料当中没有产生的反应化学物质便会因为蒸发而被去除,在第二个
反应器的上部将其排放至燃烧装置当中。
因为在羰基合成时,为发生放热的一种
过程。
所以,反应器要利用外面的水进行冷却,将液相采出物实施冷却。
经过以
上的反应过程可以获取的产物为:高纯度的正丁醇和异丁醛
2.3辛烯醛单元
该单元的重要作用为把羰基合成单元所产生的正丁醇进行转化,形成辛醇相
关产品。
在这一单元当中流入的正丁醇在恰当的温度和合适的压力下,与NaOH
的水溶液进行混合,在利用反应之后,便会产生辛烯醛。
将水相分离进行完成之后,可以利用连个环节将氢化完成。
一是辛烯醛在利用催化剂实施相关的反应。
二是有些辛烯醛气体没有产生任何的反应,在借助合理的温度以及相应的压力下,将汽液进行分离,之后实施加氢的相关处理。
最后,在具体的产物当中,利用相
关的处理,将其置入贮存槽当中进行存储。
2.4技术要点
这项生产工艺利用H2、C3H6等相关的原材料进行生产,产生的丁辛醇和H2、CO和C3H6会在对空气进行净化完成之后,进入到反应单元中,反应完成之后会
产生正丁醛和异丁醛,并会进入到该分离单元当中,把正丁醇分离。
对原料进行
净化,丙烯原料在实施预热处理的过程中,会进入到净化器以及相关过滤器当中,将净化完成,之后将其直接送入至进行合成的反应器当中。
合成气在实施预热的
相关处理完成之后,会置入到净化器当中,对其进行加热完成之后,利用过滤器
流入之分离当中,与循环合成气体实施有效的混合。
利用净化单元实施有效的处
理之后,C3H6与相关的合成气混合物质在合成装置当中会与催化剂混合。
利用分离器将已经分离出来的气体冷凝,在稳定塔当中进行分馏,之后再把丁醇引入之
异构塔当中实施有效的分离,在分离之后,正丁醇会在缩合单元中实施有效的缩
合反应,在催化剂的作用下以及进行精馏处理,最后合成出丁辛醇。
3.研究进展
在超临界的环境中,将临界的CO2、H2O当作溶剂,应用母体铑催化剂与水溶性的配体实施相关的反应,能够有效将污染性消除,为当前的一种绿色没有污染的合成工艺。
总结:我国在对丁辛醇进行合成的工艺有非常大的进步,也对相关的催化试剂进行了改进,使其更加绿色没有污染。
尽管,在该项工艺上的探究取得了非常大的进步,但是与一些发达国家比较,还存在非常大的差距。
现在,我国正在使用的装置,大多从国外进口,在具体的生产工艺上,装置的改造相关工作始终依附国外的一些技术。
为了更好地提升我国的生产工艺,要对该项工艺不断进行探究,将内部的产业结构进行优化,推进合成工艺技术的进步。
参考文献:
[1]贺星淳,曹彬.甲醇低压羰基合成醋酸工艺、流程及控制新进展[J].中小企业管理与科技(中旬刊),2017(01):187-188.
[2]戴小卉,胡青华.低压羰基合成工艺醋酸成品丙酸影响因素及其控制方法[J].科技创新与应用,2015(20):35.。