卧式单面多轴钻孔组合机床动力滑台的液压系统的课程设计
液压传动课程设计-卧式单面多轴钻孔组合机床动力滑台的液压系统
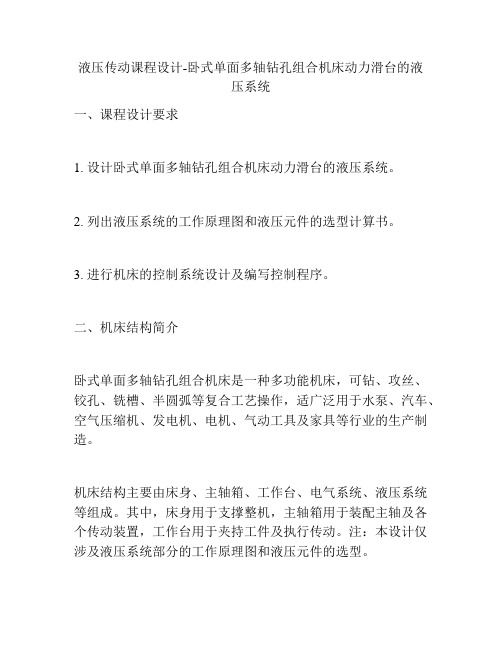
液压传动课程设计-卧式单面多轴钻孔组合机床动力滑台的液压系统一、课程设计要求1. 设计卧式单面多轴钻孔组合机床动力滑台的液压系统。
2. 列出液压系统的工作原理图和液压元件的选型计算书。
3. 进行机床的控制系统设计及编写控制程序。
二、机床结构简介卧式单面多轴钻孔组合机床是一种多功能机床,可钻、攻丝、铰孔、铣槽、半圆弧等复合工艺操作,适广泛用于水泵、汽车、空气压缩机、发电机、电机、气动工具及家具等行业的生产制造。
机床结构主要由床身、主轴箱、工作台、电气系统、液压系统等组成。
其中,床身用于支撑整机,主轴箱用于装配主轴及各个传动装置,工作台用于夹持工件及执行传动。
注:本设计仅涉及液压系统部分的工作原理图和液压元件的选型。
三、液压系统工作原理图液压系统主要用于机床的升降、夹紧、进给等控制操作。
下面的工作原理图展示了该机床的主要液压系统结构。
液压油泵为双联泵,分别提供高压和低压液压油,高压系统主要用于机床的动力传输和工作台的升降,低压系统则用于工作台和主轴箱的夹持、进给和径向递进。
四、液压元件的选型计算本文中设计的液压系统主要包括液压油泵、液压缸、液压阀、液压滤清器、液压压力表等液压元件。
针对所需控制的液压作用,根据相应的公式和数据手册,进行液压元件的选型计算。
液压元件选型计算书如下:五、控制系统设计本设计中,机床的控制系统主要由PLC控制器、触摸屏、传感器、执行器和电磁阀等组成,通过编写相应的控制程序,实现机床的高效稳定运行。
液压系统的控制程序中主要包括如下控制命令:1. 单向液压缸的伸出和缩回控制命令。
2. 双向液压缸的伸出和缩回控制命令。
3. 液压油泵的控制启停命令。
4. 电磁阀的开关控制命令。
5. 液压滤清器的定期清洗命令。
通过不同的控制命令组合,可以实现机床的不同运动状态和操作需求,从而提高机床的生产效率和工作质量。
六、总结本文对卧式单面多轴钻孔组合机床动力滑台的液压系统进行了详细介绍,并给出了液压系统的工作原理图和液压元件的选型计算书,同时简要讲述了机床的控制系统设计流程和控制命令。
设计一台卧式单面多轴钻孔组合机床动力滑台的液压系统

2
第一张 明确液压系统的设计要求
设计一台卧式单面多轴钻孔组合机床动力滑台的液压系统。要实现的动作顺 序为�启动→加速→快进→减速→工进→快退→停止。液压系统的主要参数与性 能要求如下�轴向切削力总和 Fg=30000N�移动部件总重量 G�10000N�快进 行程长度 150mm 工进行程 30mm�快进、快退的速度为 4.2m/min�工进速度 �20~1000�mm/min�其中 20mm/min 为粗加工� 1000mm/min 为精加工�该动 力滑台采用水平放置的平导轨�静摩擦系数 fs�0.2�动摩擦系数 fd�0.1。液压 系统的执行元件使用液压缸。
� � A2 � � D 2 � d 2 4 � 32.43 �10 �4 m 2
工作台在快进过程中�液压缸采用差动连接�此时系统所需要的流量为
q快进 � � A1 � A2 �� v1 � 23 .07 L min
工作台在快退过程中所需要的流量为
q 快退 � A2 � v3 � 22 .7 L min
1
引言
液压传动是用液体作为来传递能量的�液压传动有以下优点�易于获得较大 的力或力矩�功率重量比大�易于实现往复运动�易于实现较大范围的无级变速� 传递运动平稳�可实现快速而且无冲击�与机械传动相比易于布局和操纵�易于 防止过载事故�自动润滑、元件寿命较长�易于实现标准化、系列化。
液压传动的基本目的就是用液压介质来传递能量�而液压介质的能量是由其 所具有的压力及力流量来表现的。而所有的基本回路的作用就是控制液压介质的 压力和流量�因此液压基本回路的作用就是三个方面�控制压力、控制流量的大 小、控制流动的方向。所以基本回路可以按照这三方面的作用而分成三大类�压 力控制回路、流量控制回路、方向控制回路。
卧式单面多轴钻孔组合机床动力滑台的液压系统的课程设计..

湖南工业大学课程设计资料袋机械工程学院学院(系、部)2013 ~ 20 14 学年第 1 学期课程名称液压与气压传动指导教师罗中平职称教授学生姓名曹炎斌专业班级机工1102班学号11495200131 题目组合机床动力滑台液压系统设计成绩起止日期2013 年12 月19日~1014 年1月02日目录清单湖南工业大学课程设计任务书2013—2014学年第1学期机械工程学院(系、部)机电一体化专业1102 班级课程名称:液压与气动设计题目:组合机床动力滑台液压系统设计1完成期限:自2013 年12 月30 日至2014 年1 月 3 日共 1 周指导教师(签字):年月日系(教研室)主任(签字):年月日(课程设计名称)设计说明书(题目)起止日期:2013 年12月19日至2014 年1 月 2 日学生姓名曹炎斌班级机工1102学号11495200131成绩指导教师(签字)机械工程学学院(部)2013年12 月30 日液压传动课程设计指导书湖南工业大学机械工程学院2013年12月第一章明确液压系统的设计要求要求设计一台卧式单面多轴钻孔组合机床动力滑台的液压系统。
设计要求驱动动力滑台实现“快进→工进→快退→停止”的工作循环。
液压系统的主要参数与性能要求如下:机床上有主轴16个,加工Φ13.9 mm 的孔14个,Φ8.5mm 的孔2个。
刀具材料为高速钢,工件材料为铸铁,硬度为240HBS ,运动部件总质量G=9800N ,快进、快退的速度v 1= v 3=5.5 m/min ,快进行程长度l 1=100mm ,工进行程长度l 2=50 mm ,往复运动的加速,减速时间为0.2s ,动力滑台采用平导轨,其静摩擦系数f s =0.2,动摩擦系数f d =0.1,液压系统中的执行元件使用液压缸。
第二章 负载与运动分析负载分析中,暂不考虑回油腔的背压力,液压缸的密封装置产生的摩擦阻力在机械效率中加以考虑。
因工作部件是卧式放置,重力的水平分力为零,这样需要考虑的力有:夹紧力,导轨摩擦力,惯性力。
卧式单面多轴钻孔组合机床动力滑台液压系统方案

卧式单面多轴钻孔组合机床动力滑台液压系统设计要求设计的动力滑台实现的工作循环是:快进工进快退停止。
主要性能参数与性能要求如下:切削阻力FL=30468N ;运动部件所受重力G=9800N ;快进、快退速度υ1= υ3=0.1m/s ,工进速度υ2=0.88×10-3m/s ;快进展程L1=100mm ,工进展程L2=50mm ;往复运动的加速时间Δt=0.2s;动力滑台采用平导轨,静摩擦系数μs=0.2,动摩擦系数μd=0.1。
液压系统执行元件选为液压缸。
液压传动课程设计一般包括以下容: (1) 明确设计要求进展工况分析; (2) 确定液压系统主要参数; (3) 拟定液压系统原理图; (4) 计算和选择液压件; (5) 验算液压系统性能; (6) 编制技术文件。
1.负载分析1〕切削阻力 F L =30468N2〕计算摩擦阻力静摩擦阻力:F s =u s G=0.2×9800=1960N 动摩擦阻力:F d =u d G=0.1×9800=980N 3〕计算惯性阻力 F m =ma=g G tv 1=2.08.91.09800⨯⨯=500N 4〕计算各工况负载这里取液压缸效率为0.92.绘制液压缸的F-t 图与v-t 图1〕工进速度 V2=0.88mm/s2〕快进,快退时间 快进:t 1=L1/v1=1s 工进:t 2=L2/v2=56.8s 快退:t 3=(L1+L2)/v3=1.5s3〕绘制液压缸的F-t 图与v-t 图 如图3.确定液压系统参数1〕初选液压工工作压力由工况分析可知,工进阶段的负载力最大,所以,液压缸的工作压力按此负载力计算,根据液压缸与负载关系以及列表,选p 1=40⨯105Pa.本机床为钻孔组合机床,为防止钻通时发生前冲现象,液压缸回油腔应有背压,设背压p 2=6⨯105Pa ,为使快进快退速度相等,选用A 1=2A 2,差动油缸,假定快进,快退的回油压力损失为Δp=7⨯105Pa 。
卧式单面多轴钻孔组合机床液压课程设计

卧式单面多轴钻孔组合机床液压课程设计以卧式单面多轴钻孔组合机床液压课程设计为标题,本文将从机床结构设计、液压系统设计、控制系统设计三个方面进行详细阐述。
一、机床结构设计卧式单面多轴钻孔组合机床是一种具有多轴钻孔功能的机床,其结构设计至关重要。
在设计过程中,需要考虑以下几个方面:1.1 机床整体结构设计卧式单面多轴钻孔组合机床的整体结构应具有良好的刚性和稳定性,以确保加工过程中的精度和稳定性。
同时,还需要考虑机床的操作便捷性和安全性。
1.2 主轴设计主轴是机床的核心部件之一,其设计应考虑主轴的转速范围、功率和扭矩需求,以满足不同工件的加工要求。
1.3 工作台设计工作台是机床上用于夹持工件的部件,其设计应考虑工件的尺寸和重量,以确保工件在加工过程中的稳定性和精度。
二、液压系统设计液压系统是卧式单面多轴钻孔组合机床的重要组成部分,其设计应满足以下要求:2.1 液压元件的选择液压系统中的液压元件包括液压泵、液压马达、液压缸等,其选择应根据机床的工作负荷和工作条件进行合理搭配,以确保液压系统的正常运行。
2.2 液压系统的工作压力和流量设计液压系统的工作压力和流量设计应根据机床的工作要求和液压元件的额定参数进行合理选取,以确保液压系统能够稳定可靠地提供所需的液压能力。
2.3 液压管路设计液压管路的设计应考虑液压系统的布局和液压元件的连接方式,以确保液压油能够顺畅地流动,并且减少液压泄漏的可能性。
三、控制系统设计控制系统是卧式单面多轴钻孔组合机床的关键部分,其设计应满足以下要求:3.1 控制方式的选择控制系统可以采用传统的机械控制方式,也可以采用现代的数控控制方式。
在选择控制方式时,需要考虑机床的加工精度要求和操作人员的技术水平。
3.2 控制系统的功能设计控制系统的功能设计应根据机床的工作要求和操作人员的操作习惯进行合理设计,以提高机床的工作效率和加工质量。
3.3 控制系统的安全设计控制系统的安全设计应考虑到机床在工作过程中可能出现的故障和意外情况,采取相应的安全措施,保障操作人员的人身安全。
液压课程设计--卧式单面多轴钻孔组合机床动力滑台

目录一摘要⋯⋯⋯⋯⋯⋯⋯⋯⋯⋯⋯⋯⋯⋯⋯⋯⋯⋯⋯⋯⋯⋯⋯⋯⋯⋯⋯1二设计的技术要求和设计参数⋯⋯⋯⋯⋯⋯⋯⋯⋯⋯⋯⋯⋯..1三工况分析⋯⋯⋯⋯⋯⋯⋯⋯⋯⋯⋯⋯⋯⋯⋯⋯⋯⋯⋯⋯⋯⋯⋯⋯.21 确定执行元件⋯⋯⋯⋯⋯⋯⋯⋯⋯⋯⋯⋯⋯⋯⋯⋯⋯ (2)2 分析系统工况⋯⋯⋯⋯⋯⋯⋯⋯⋯⋯⋯⋯⋯⋯⋯⋯⋯ (2)3 负载循环图和速度循环图⋯⋯⋯⋯⋯⋯⋯⋯⋯⋯⋯⋯⋯⋯⋯⋯⋯ (3)4 确定系统主要参数⋯⋯⋯⋯⋯⋯⋯⋯⋯⋯⋯⋯⋯⋯⋯⋯⋯⋯⋯⋯⋯4四拟定液压系统原理图⋯⋯⋯⋯⋯⋯⋯⋯⋯⋯⋯⋯⋯⋯⋯⋯⋯..71 速度控制回路的选择⋯⋯⋯⋯⋯⋯⋯⋯⋯⋯⋯⋯⋯⋯⋯⋯⋯⋯⋯⋯72 换向和速度换接回路的选择⋯⋯⋯⋯⋯⋯⋯⋯⋯⋯⋯⋯⋯⋯⋯⋯⋯73 压力控制回路的选择⋯⋯⋯⋯⋯⋯⋯⋯⋯⋯⋯⋯⋯⋯⋯⋯⋯⋯⋯⋯8五液压元件的选择⋯⋯⋯⋯⋯⋯⋯⋯⋯⋯⋯⋯⋯⋯⋯⋯⋯⋯⋯⋯.9 1确定液压泵和电机规格⋯⋯⋯⋯⋯⋯⋯⋯⋯⋯⋯⋯⋯⋯⋯⋯⋯⋯⋯92.电机的选择⋯⋯⋯⋯⋯⋯⋯⋯⋯⋯⋯⋯⋯⋯⋯⋯⋯⋯⋯⋯⋯⋯⋯⋯103.阀类元件和辅助元件的选择⋯⋯⋯⋯⋯⋯⋯⋯⋯ (11)4.油管的选择⋯⋯⋯⋯⋯⋯⋯⋯⋯⋯⋯⋯⋯⋯⋯⋯ (12)5油箱的设计⋯⋯⋯⋯⋯⋯⋯⋯⋯⋯⋯⋯⋯⋯⋯⋯⋯⋯⋯⋯⋯⋯⋯ (13)六液压系统性能的验算⋯⋯⋯⋯⋯⋯⋯⋯⋯⋯⋯⋯⋯⋯⋯⋯⋯.131管路系统压力损失演算⋯⋯⋯⋯⋯⋯⋯⋯⋯⋯⋯⋯⋯⋯⋯⋯⋯ ...⋯13 2油液温升验算⋯⋯⋯⋯⋯⋯⋯⋯⋯⋯⋯⋯⋯⋯⋯⋯⋯⋯⋯⋯⋯⋯ (14)七设计心得⋯⋯⋯⋯⋯⋯⋯⋯⋯⋯⋯⋯⋯⋯⋯⋯⋯⋯⋯⋯⋯⋯⋯⋯16八参考文献⋯⋯⋯⋯⋯⋯⋯⋯⋯⋯⋯⋯⋯⋯⋯⋯⋯⋯⋯⋯⋯⋯⋯⋯17一摘要作为一种高效率的专用机床,组合机床在大批、大量机械加工生产中应用广泛。
本次课程设计将以组合机床动力滑台液压系统设计为例,介绍该组合机床液压系统的设计方法和设计步骤,其中包括组合机床动力滑台液压系统的工况分析、主要参数确定、液压系统原理图的拟定、液压元件的选择以及系统性能验算等。
卧式单面多轴钻孔课程设计说明书

设计内容:设计一台单面多轴钻孔组合机床,动力滑台的工作循环是:快进——工进——快退——停止。
液压系统的主要性能参数要求如下,轴向切削力为24000N;滑台移动部件总质量为510kg;加、减速时间为0.2s;采用平导轨,静摩擦系数为0.2,动摩擦系数为0.1;快进行程为200mm,工进行程为100mm,快进与快退速度相等,均为3.5m/min,工进速度为30~40mm /min。
工作时要求运动平稳,且可随时停止运动。
试设计动力滑台的液压系统。
1 设计方案拟定1.1 方案分析对设计液压系统进行分析,已知设计的是一卧式单面多轴钻孔组合机床的液压系统,要求液压系统完成的工作循环是:快进→工进→快退→停止。
在设计过程中要注意液压设计的注意事项:在滑台的速度变化较大,当滑台由工进转为快退时,以减少液压冲击,须使用背压阀等。
方案一:选用两个柱塞缸组合来实现工作循环所要求的快进、工进运动,在快进和快退时要求速度相等,通过差动连接来实现。
系统在工作过程环境恶劣,时有冲击可通过在回油路上加背压阀来减少其对加工工件精度的影响。
为了减少空间,油箱采用闭式油箱。
由于其工况过程分段情况很大,节约能源,节约成本可采用变量泵来实现不同工况对油量的不同需要。
闭式油箱,不易于散热,要附加散热器,增加了成本。
方案二:选用单杆活塞缸来实现工作循环所要求的快进、工进运动,借鉴经典的实现快进、快退的连接方式,差动连接来实现,而对于有大冲击,工作阻力不定对加工过程的影响,采用使用在回油路上接背压阀和在进油路上用调速阀和行程阀的组合来实现。
对于工况分段情况很大,借鉴同类机床多数采用双泵供油来节约能源。
为减少热变形对加工精度的影响,减少热源,选用远离机床床身的开式油箱。
方案三:选用单杆活塞缸来实现工作环循环所要求的快进、工进运动,对运动方向的改变可以二位二通电磁换向阀来、单向阀和调速阀来实现。
液压泵选用变量泵,这种方案就是在快进的时候油液流经阀的速度快,流量大,局部损失大,油液发热高,使液压液的粘性降低,影响系统的稳定性 。
【精品】液压课程设计卧式单面多轴钻孔组合机床液压系统
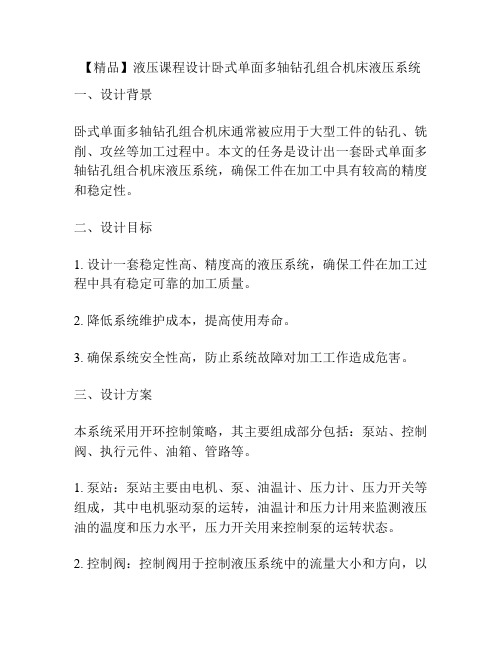
【精品】液压课程设计卧式单面多轴钻孔组合机床液压系统一、设计背景卧式单面多轴钻孔组合机床通常被应用于大型工件的钻孔、铣削、攻丝等加工过程中。
本文的任务是设计出一套卧式单面多轴钻孔组合机床液压系统,确保工件在加工中具有较高的精度和稳定性。
二、设计目标1. 设计一套稳定性高、精度高的液压系统,确保工件在加工过程中具有稳定可靠的加工质量。
2. 降低系统维护成本,提高使用寿命。
3. 确保系统安全性高,防止系统故障对加工工作造成危害。
三、设计方案本系统采用开环控制策略,其主要组成部分包括:泵站、控制阀、执行元件、油箱、管路等。
1. 泵站:泵站主要由电机、泵、油温计、压力计、压力开关等组成,其中电机驱动泵的运转,油温计和压力计用来监测液压油的温度和压力水平,压力开关用来控制泵的运转状态。
2. 控制阀:控制阀用于控制液压系统中的流量大小和方向,以便实现机床的各项功能操作。
3. 执行元件:执行元件包括缸体、柱塞、电磁阀等,其作用是将液压系统中的动力传递给工件进行加工。
4. 油箱:油箱用于储存液压油,其容积需要根据机床的工作强度进行合理估算。
5. 管路:管路是连接各组成部分的管道,其泄漏率应该控制在合理的范围内,以确保机床的加工质量。
四、系统优点1. 稳定性高:本系统采用开环控制策略,其稳定性较高。
2. 驱动力强:泵站的驱动力较强,可以满足机床加工过程中的各种需求。
3. 具有良好的控制效果:控制阀的开关操作可以控制液压油的流量大小和方向,以实现机床的各项功能操作。
4. 安全性高:本系统的压力开关可以保证系统安全性,避免机床在工作过程中出现危险情况。
五、总结本文设计了一套卧式单面多轴钻孔组合机床液压系统,其稳定性高,驱动力强,控制效果良好,安全性高,能够满足机床加工的各项需求,同时降低了系统维护成本,提高了使用寿命。
- 1、下载文档前请自行甄别文档内容的完整性,平台不提供额外的编辑、内容补充、找答案等附加服务。
- 2、"仅部分预览"的文档,不可在线预览部分如存在完整性等问题,可反馈申请退款(可完整预览的文档不适用该条件!)。
- 3、如文档侵犯您的权益,请联系客服反馈,我们会尽快为您处理(人工客服工作时间:9:00-18:30)。
工业大学课程设计资料袋机械工程学院学院(系、部) 2013 ~ 20 14 学年第 1 学期课程名称液压与气压传动指导教师罗中平职称教授学生炎斌专业班级机工1102班学号题目组合机床动力滑台液压系统设计成绩起止日期 2013 年 12 月 19日~ 1014 年 1月 02日目录清单工业大学课程设计任务书2013—2014学年第1学期机械工程学院(系、部)机电一体化专业 1102 班级课程名称:液压与气动设计题目:组合机床动力滑台液压系统设计1 完成期限:自 2013 年 12 月 30 日至 2014 年 1 月 3 日共 1 周指导教师(签字):年月日系(教研室)主任(签字):年月日(课程设计名称)设计说明书(题目)起止日期: 2013 年 12月 19日至 2014 年 1 月 2 日学生炎斌班级机工1102学号成绩指导教师(签字)机械工程学学院(部)2013年12 月 30 日液压传动课程设计指导书工业大学机械工程学院2013年12月第一章 明确液压系统的设计要求要求设计一台卧式单面多轴钻孔组合机床动力滑台的液压系统。
设计要求驱动动力滑台实现“快进→工进→快退→停止”的工作循环。
液压系统的主要参数与性能要求如下:机床上有主轴16个,加工Φ13.9 mm 的孔14个,Φ8.5mm 的孔2个。
刀具材料为高速钢,工件材料为铸铁,硬度为240HBS ,运动部件总质量G=9800N ,快进、快退的速度v 1= v 3=5.5 m/min ,快进行程长度l 1=100mm ,工进行程长度l 2=50 mm ,往复运动的加速,减速时间为0.2s ,动力滑台采用平导轨,其静摩擦系数f s =0.2,动摩擦系数f d =0.1,液压系统中的执行元件使用液压缸。
第二章 负载与运动分析负载分析中,暂不考虑回油腔的背压力,液压缸的密封装置产生的摩擦阻力在机械效率中加以考虑。
因工作部件是卧式放置,重力的水平分力为零,这样需要考虑的力有:夹紧力,导轨摩擦力,惯性力。
在对液压系统进行工况分析时,本设计实例只考虑组合机床动力滑台所受到的工作负载、惯性负载和机械摩擦阻力负载,其他负载可忽略。
(1)切削负载F W N 30500=工作负载是在工作过程中由于机器特定的工作情况而产生的负载,对于金属切削机床液压系统来说,沿液压缸轴线方向的切削力即为工作负载。
切削负载(确定切削负载应具备机械切削加工方面的知识)用高速钢钻头(单个)钻铸铁孔时的轴向切削力F t (单位为N)为6.08.0t )HB S (5.25Ds F = 2 (8—1)式中:D ——钻头直径,单位为mm ;s ——每转进给量,单位为mm /r ; HBS ——铸件硬度。
根据组合机床加工特点,钻孔时主轴转速n 和每转进给量s 按“组合机床设计手册”取: 对φ13.9mm 的孔:n 1=360r /min ,s l =0.147mm /r ; 对φ8.5mm 的孔:n 2=550r /min ,s 2=0.096mm /r ; 所以,系统总的切削负载F t 为:N F w 30500240096.00.95.252240147.09.135.25146.08.06.08.0=⨯⨯⨯⨯+⨯⨯⨯⨯=令Fw=Fq=30500N 2.惯性负载往复运动的加速,减速时间为0.2s ,所以取t ∆为0.2SN t v g G t v mF m 4582.0605.51000=⨯⨯=∆∆⨯=∆∆=3.阻力负载机床工作部件对动力滑台导轨的法向力为:N G F n 9800==静摩擦阻力:N f f F n s tf 196098002.0=⨯==动摩擦阻力:N F f F n d fd 98098001.0=⨯==加速负载: N t v m f F F d n L 1438/=∆∆+=如果忽略切削力引起的颠覆力矩对导轨摩擦力的影响,并设液压缸的机械效率w η=0.9,根据上述负载力计算结果,可得出液压缸在各个工况下所受到的负载力和液压缸所需推力情况由此得出液压缸在各工作阶段的负载如表110-所列。
工况负载组成负载值F 工况 负载组成负载值F 启动 s n L f F F = 1960 快退 d n L f F F = 980 快进 d n L f F F = 980 停止 m fd F F F -= 522 工进 q d n L F f F F +=31480注:在负载分析中,没有考虑动力滑台上倾翻力矩的作用第三章 负载图和速度图的绘制根据工作循环(总行程L1+L2=150mm 工进速度V2绘制动力滑台速度图(如图8-1(b)所示。
快进、工进和快退的时间可由下式分析求出。
快进 s v l t 09.1605.51.0111=⨯==工进 s v l t 6.5660053.005.0222=⨯== 快退 s v l l t 63.1605.515.03123=⨯=+= 根据上述已知数据绘制组合机床动力滑台液压系统绘制负载图(F-t )如图1(b),速度循环图如图1(c)所示。
初选液压缸工作压力所设计的动力滑台在工进时负载最大,在其它工况负载都不太高,参考表1和表2,初选液压缸的工作压力p 1=4MPa 。
组合机床液压缸的负载图和速度图图1 速度负载循环图a)工作循环图 b)负载速度图 c)负载速度图第四章确定液压系统主要参数4.1确定液压缸工作压力由表2和表3可知,组合机床液压系统在最大负载约为40000N时宜取5MP。
负载/KN <5 5~10 10~20 20~30 30~50 >50 工作压力/MPa < 0.8~1 1.5~2 2.5~3 3~4 4~5 ≥5机械类型机床农业机械小型工程机械建筑机械液压凿岩机液压机大中型挖掘机重型机械起重运输机械磨床组合机床龙门刨床拉床工作压力/Mpa 0.8~2 3~5 2~8 8~10 10~18 20~32 4.2计算液压缸主要结构参数由于工作进给速度与快速运动速度差别较大,且快进、快退速度要求相等,从降低总流量需求考虑,应确定采用单杆双作用液压缸的差动连接方式。
通常利用差动液压缸活塞杆较粗、可以在活塞杆中设置通油孔的有利条件,最好采用活塞杆固定,而液压缸缸体随滑台运动的常用典型安装形式。
这种情况下,应把液压缸设计成无杆腔工作面积1A是有杆腔工作面积2A两倍的形式,即活塞杆直径d与缸筒直径D呈d = 0.707D的关系。
工进过程中,当孔被钻通时,由于负载突然消失,液压缸有可能会发生前冲的现象,因此液压缸的回油腔应设置一定的背压(通过设置背压阀的方式),选取此背压值为p 2=0.8MPa 。
快进时液压缸虽然作差动连接(即有杆腔与无杆腔均与液压泵的来油连接),但连接管路中不可避免地存在着压降p ∆,且有杆腔的压力必须大于无杆腔,估算时取p ∆≈0.5MPa 。
快退时回油腔中也是有背压的,这时选取被压值2p =0.6MPa 。
工进时液压缸的推力计算公式为11221112/(/2)m F A p A p A p A p η=-=-,式中:F ——负载力m——液压缸机械效率A 1——液压缸无杆腔的有效作用面积 A 2——液压缸有杆腔的有效作用面积 p 1——液压缸无杆腔压力 p 2——液压有无杆腔压力因此,根据已知参数,液压缸无杆腔的有效作用面积可计算为-643603.333101===0.09478990.85-221-2x FA mm m p p η液压缸缸筒直径为=41/D A mm π由于有前述差动液压缸缸筒和活塞杆直径之间的关系,d = 0.707D ,因此活塞杆直径为d=0.707×109.89=77.69mm ,根据GB/T2348—1993对液压缸缸筒径尺寸和液压缸活塞杆外径尺寸的规定,圆整后取液压缸缸筒直径为D =110mm ,活塞杆直径为d =80mm 。
此时液压缸两腔的实际有效面积分别为:2-421=/4=94.79510A D x m π 22-422=(-d )/4=44.55510A D x m π工作台在快进过程中,液压缸采用差动连接,此时系统所需要的流量为63.27)(121=⨯-=V A A q 快进工作台在快退过程中所需要的流量为m in /50.2432L v A q ==快退工作台在工进过程中所需要的流量为m in /502.021L v A q ==工进根据上述液压缸直径及流量计算结果,进一步计算液压缸在各个工作阶段中的压力、流量和功率值,如表4所示。
工况 负载 F L /N 回油腔 压力 P 2/MPa 进油腔 压力 P 1/MPa 输入理论流量 q/(L/s) 输入功率 P /kW计算式快迸(差 动) 启动 1960 01.17--()[]()212m L 1//A A p A F p -∆+=η()121v A A q -= q p P 1=加速 980 p p ∆+11.005 - - 恒速 980 0.804 0.5485 0.441 工进314800.6 4.88 0.0084 0.041 ()[]qp P v A q A A p F p 121122m L 1//==+=η 快退启动 1960 0 0.38 - - ()[]qp P v A q A A p F p 132122m L 1//==+=η 加速 980 0.60.573--恒速 980 0.424 0.486 0.205并据表4可绘制出液压缸的工况图,如图2所示。
图2 组合机床液压缸工况图第五章 液压系统方案设计根据组合机床液压系统的设计任务和工况分析,所设计机床对调速围、低速稳定性有一定要求,因此速度控制是该机床要解决的主要问题。
速度的换接、稳定性和调节是该机床液压系统设计的核心。
此外,与所有液压系统的设计要求一样,该组合机床液压系统应尽可能结构简单,成本低,节约能源,工作可靠。
5.1选用执行元件因系统运动循环要求正向快进和工进,反向快退,且快进,快退速度相等,因此选用单活塞杆液压缸,快进时差动连接,无杆腔面积A 1等于有杆腔面积A 2的两倍。
工况图表明,所设计组合机床液压系统在整个工作循环过程中所需要的功率较小,系统的效率和发热问题并不突出,因此考虑采用节流调速回路即可。
虽然节流调速回路效率低,但适合于小功率场合,而且结构简单、成本低。
该机床的进给运动要求有较好的低速稳定性和速度-负载特性,因此有三种速度控制方案可以选择,即进口节流调速、出口节流调速、限压式变量泵加调速阀的容积节流调速。
钻镗加工属于连续切削加工,加工过程中切削力变化不大,因此钻削过程中负载变化不大,采用节流阀的节流调速回路即可。
但由于在钻头钻入铸件表面及孔被钻通时的瞬间,存在负载突变的可能,因此考虑在工作进给过程中采用具有压差补偿的进口调速阀的调速方式,且在回油路上设置背压阀。