机械加工零件品质检验流程图
机加工厂质量控制程序文件

机加工厂质量控制管理规定文件管理编号:JJGC-010006-1/9文件版本编号:V1.0文件制定日期:2010-6-25文件修订日期:文件执行部门:机加工厂批准审核编制志博建伟斌/建林〈修订登记〉版数修定日期页码容1 目的为了保证机加工厂加工零件的入库质量,避免批量不合格状况的发生,确保零部件加工的质量处于受控状态。
2 适用围本程序适用于机加工厂各班组日常质量管理;3 责任班组机加工厂各班组4具体要求4.1 工序发生的质量问题的处理4.1.1各工序的操作人员负责对每一种加工零件按照《检验指示表》、零件图纸进行检验,做出合格与否的判断.4.1.2工序检查发现的不合格品应迅速向本部门的负责人报告,并由负责人进行确认。
不合格品应立即填写《不合格报告书》,并将不合格品隔离或标识并通知品质保证部进行判定处理。
4.1.3根据品保部的判断结果,不合格品进行返工、特采或移动到废弃零件放置场所。
具体操作办法,详见《不合格品控制程序》。
4.2 品保发现的送检不良及后工序发生的质量问题的处理流程和方法4.2.1品保、部装、总装发现的不合格品由发现部门填写《不合格品报告书》,责任部门收到《不合格品报告书》,不合格品发生责任人应在5日以填写原因分析和采取的纠正预防对策报品质保证部审批。
4.2.2 A线、部装、总装投诉项目,责任部门在收到装配W5活动外部门问题统计汇总后3日以填写原因分析和采取的纠正预防对策报技术管理科汇总,各部门接到下序投诉后应该在班会期间组织员工进行相关容的培训和学习。
下序投诉原因分类责任部门提出纠正预防对策责任员工自己进行分析对策,提出PPT/EXCEL报告对没有认真落实的给予考核班长审核对策监督实施实施效果验证技术管理科确认实施效果4.4 质量会议的召开4.4.1加工工厂每月的10日左右召开由机加1/2科和技术管理科共同参加的质量总结会议,各班班长不仅对上一个月各班的质量工作进行总结而且要提出下个月质量工作开展的方向,报告的容应包括:一、月份生产质量指标的完成情况1.废品损失;2.送检不良(车床加工中心班重点分析)3.大件返修率;4.100%合格率(QTN滑鞍、MS主轴箱加工精度改善);二、日常质量工作开展情况1.继续推行部质量改善例会机制;2.部门之间的质量改善会;3.现场工艺检查的开展情况;4.工序反馈和交流会议决议的实施状况三、典型质量问题项目改善四、质量工作改善五、材料不良相关报告六、次月质量工作开展的方向和目标4.4.2质量会议形成相关决议,由各班班长按照时限实施,技术管理科负责监督和效果验证。
机械加工品质控制流程图
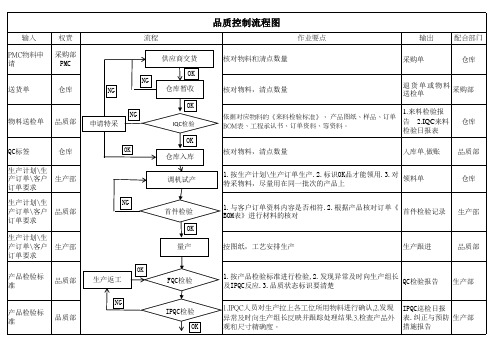
输入 PMC物料申 请 权责 采购部 PMC NG 送货单 仓库 NG
NG
流
输出 采购单
配合部门 仓库
OK 仓库暂收 OK 物料送检单 品质部 申请特采
IQC检验
核对物料,清点数量
退货单或物料 采购部 送检单 1.来料检验报 告 2.IQC来料 检验日报表 入库单.做账
依据对应物料的《来料检验标准》、 产品图纸、样品、订单 BOM表、工程承认书、订单资料、等资料。
仓库
OK
QC标签
仓库
OK
仓库入库 调机试产 NG
首件检验 OK
核对物料,清点数量
品质部
生产计划\生 产订单\客户 生产部 订单要求 生产计划\生 产订单\客户 品质部 订单要求 生产计划\生 产订单\客户 生产部 订单要求 产品检验标 准
OK
1.按生产计划\生产订单生产.2.标识OK品才能领用.3.对 领料单 特采物料,尽量用在同一批次的产品上 1.与客户订单资料内容是否相符.2.根据产品核对订单《 首件检验记录 BOM表》进行材料的核对
仓库
生产部
量产
按图纸,工艺安排生产
生产跟进
品质部
品质部
生产返工 NG
FQC检验
1.按产品检验标准进行检验,2.发现异常及时向生产组长 QC检验报告 及IPQC反应.3.品质状态标识要清楚 1.IPQC人员对生产拉上各工位所用物料进行确认,2.发现 异常及时向生产组长反映并跟踪处理结果.3.检查产品外 观和尺寸精确度。
生产部
产品检验标 准
品质部
IPQC检验 OK
IPQC巡检日报 表.纠正与预防 生产部 措施报告
品质控制流程图
输入 权责 流程 作业要点 输出 配合部门
过程流程图PFD

拉索支架与制动底板点焊
P50
点焊挡泥板
■
后挡泥板与制动底板焊接分总成点焊
P60
点焊制动支架
■
底板挡泥板焊接分总成与左/右制动支架点焊
P70
铆接支座
■
P80
热铆支座
■
P90
旋铆挂簧片
■
P10
加工支架安装面
■
左/右制动支架分总成与半圆头铆钉x2铆接 铆接支座半成品
热铆半成品与挂簧片旋铆 铆接挂簧片半成品支架安装面铣床加工
顾客
过程编号/功能
P10
外协件检验入库
P20
领料
P30
底板凸焊螺母
XXX机械有限公司
过程流程图PFD
零件名称
零件号
批准/日期
过程流程图
○
■◇
△
工序号
作业内容及要求
◇
根据《SX6外协件检验指导书》和《仓库管理规定》执行
○
按生产领料单备料
■
制动底板(小圆盘)与M6凸焊螺母凸焊
编号
等级
P40
点焊拉索支架
■
P110
电泳(黑色)
■
电泳黑漆
P120 P130 P140
检验 包装 入库
◇ ■
△
外观/尺寸 铁框
每筐件数 分区摆放,做标识牌
备注: 1.“○”搬运 “■”制造 “◇”检验 “△”贮存 “┃”基本路径 “┇”可选路径 2.顾客无特殊特性要求,本厂标准规定重要度控制标准符号要求如下:A—特殊特性 B—重要特性 C—一般特性
发行日期
标记
更改原因 审核人
编制人
版次
发行日期
标记
更改原因
进料检验流程图及表格

1、进料检验流程图
1.1进料检验通知单(送检单)
被通知部门:________________ 通知单编号:______________
仓储部主管:______________ 收料仓管专员:______________ 1.2进料检验记录表
1.3进料检验报告表
编号:日期:
限,则判定物料验收结果为“合格”;若检验物料的不合格数量达到或超过企业规定的数量,则判定物料验收结果为“不合格”
进厂零件质量检验表
零件编号:零件名称:号码:
检验主管:检验员:检验日期:年月日进厂零件检验报告表
编号:填写日期:年月日
进厂材料试用检验表
编号:填写日期:
进料检验质量异常处理报告
编号:____________ 填表日期:______________
进料检验日统计表
原材料供应商质量检测表
供应商名称:编号:
外协厂商质量检查表
填写日期:年月日
检验主管:检验人员:
十二、供应商不合格品记录表
年度:月份:编号:
十三、供应商物料拒收月统计表
月份:日期:
主管:制表:
十四、供应商质量评价体系表
十五、供应商综合评价表
编号:填写日期:
岗位职责
1、进料检验主管
2、进料检验专员。
制程检验流程

1、目的:为确保公司内部加工零件质量符合公司品质要求,避免因加工过程中的不合格零件流入下道工序而影响模具的制作周期与品质。
2、适用范围适用公司内部各工序加工的零件与装配中的模具。
3、定义:无4、职责:4.1 各工序操作员对本工序的加工零件自检并填写《工件尺寸检测记录表》以及报检,加工组长复查后并签名。
4.2 钳工组长负责加工后以及装配过程中工件的复检。
4.3 品质部制程检验员负责零件加工完成的检验制程巡检和关键零件终检, 监督纠正预防措施的实施。
4.4品质部文员负责将《异常处理单》及时交相关人员签批并将签批完成后的《异常处理单》复印给相关部门。
4.5品质工程师负责《异常处理单》的审核以及每月制程异常数据的统计与分析。
5.程序内容:5.1 操作员报检、制程检验员巡检5.1.1 各工序操作员在该工序加工完成后,严格按照加工要求以及零件图对外观、重点尺寸进行自检并填写好《工件尺寸检测记录表》,自检确认合格将《工件尺寸检测记录表》交加工组长审核后放置于指定位置报检。
5.1.2 制程检验员不停对机台巡检,收到机台操作员的报检信息或发现待检验区有已加工完成的零件根据加工要求和零件图,结合电脑3D图对其外观、尺寸进行详细的检测。
5.1.3如零件较复杂需要超过一小时的检测时间,需提前与制模组长沟通,以防止模具因非加工、装配停留的时间过长而延误交期;检验完成后,《工件尺寸检测记录表》由品质部制程检验组保存。
5.2 检验标准与测量方法5.2.1车床、钻床、铣床检验标准与测量5.2.2 CNC与数控车加工检验标准与测量方法5.2.3 EDM加工检验标准与测量方法5.2.4 线割加工检验标准与测量方法5.3品质判定5.3.1经过检验若零件外观、尺寸、性能等均符合加工要求则判定该零件此加工工序的品质状态为合格。
5.3.2经过检验若零件外观、尺寸、性能等有一项或多项不符合加工要求则判定该零件此加工工序的品质状态为不合格。
5.4 品质标识检验完成后,根据其零件的品质状态在物料上做好相应的品质状态标识(物料质量合格贴绿色“QC.PASS”标签,不合格贴红色“QC.REJ”标签),必要时在物料上用油性笔标识好模号、零件号等信息。
机械企业生产主流程图与流程说明

机械企业⽣产主流程图与流程说明⽣产主流程图及要点说明⽣产主流程⼯作要点说明(⽣产组织和产成品输出)⼀、合同转化及传递1.销售系统根据合同进⾏产品设计,包括设计、选材、结构确定与分析、技术规范、⼯作原理、技术经济指标分析(产品设计⽬标成品)等,不仅要考虑设计上的先进性和必要性,同时还要考虑⼯艺上的可能性和经济性;2.由制造事业部会同设计部门根据项⽬产能分析及产品性质选择⽣产单位;3.⽣产单位确定后,编制《⽣产联系单》,传递⾄⽣产运营部。
在编制《⽣产联系单》时需注意:要有合同编号、图件号、材质、数量、价格、交货期、运输⽅式等内容,需产品设计的合同,按设计完的产品图纸、明细表组织⽣产,其它⽼产品的合同必须写清以上内容以便于⽣产组织;4.⽣产运营部进⾏合同签收,⾃此⽣产流程开始。
⼆、编制⽉份⽣产计划1.⽣产运营部根据《⽣产联系单》,按产品合同交货期,技术准备⼯作进度、产品透料计划、设备维修计划、计划和实际供料、前期计划执⾏情况,在本期计划出产的商品数,长线产品需在本期⾛的在制情况,编制出《⽉份⽣产计划》,以此确定产品出⼚顺序;2.⽣产运营部配合制造事业部做好⽤户有要求的《产品出产计划安排》,经领导审核后报制造事业部;3.将《⽉份⽣产计划》传递给技术管理部、采购部、三个⽣产⼯部,并反馈⾄制造事业部供品质管理部门跟进检查。
4.各⽣产⼯部做出周产品零部件加⼯作业班计划,做到周计划、⽇安排、勤调整。
三、产品投料计划1.⽣产运营部根据《⽣产联系单》编制《投料计划单》;2.在下达投料计划时,应在计划中对组焊件分别标注所属参与组焊的专⽤零件、⽆图件等,以便先于组织⽣产;3.投料计划按钢、铁、铜、锻、铆分别进⾏单独分类下达,并汇总出各类⽑坯重量,以达到某⼀种产品各类⽑坯件的所占⽐例;4.根据⽣产资⾦的投⼊情况,有针对性的按⽐例投⼊;5.对于成线产品可按设计⼊库的时间,相似新产品同时投料⽣产,即节省原材料费⽤,⼜可提⾼劳动效率,便于⽣产组织的进⾏;6.对于产品设计中、⼯艺有要求的部件、零件,需⼚外协作加⼯的(⼯艺性外协)在下投料计划时同时下达,采购部预以实施。
过程流程图

更改级别:/日期(最初): 更改日期:/日期(修订):XXX 精密机械有限公司过程流程图文件编号:/ 零件号:零件名称:图纸日期:图 纸 号:更改级别:/日期(最初): 更改日期:/日期(修订):/ 零件号:零件名称:图纸日期:图 纸 号:更改级别:/日期(最初): 更改日期:/日期(修订):/ 零件号:零件名称:图纸日期:图 纸 号:更改级别:/日期(最初): 更改日期:/日期(修订):/ 零件号:零件名称:图纸日期:图 纸 号:5-Φ5深13.6±0.55-M6X1.0-6H 深10.6Min55.0±0.25° TYP 45°KCC 4±0.23.5±0.214.7±0.2KCC4-Φ7.9深54.8±1.04-3/8-16UNC 深50.0Min2-Φ3.3深11.1±2.02-M4X0.7-6H 深9.0Min1.三轴加工中心2.刀具3.夹具4.切削液浓度1.气动攻丝机2.刀具3.夹具4.切削液浓度检验KPCKPC 机加工槽边缘毛刺清理干净;机加工无发霉、发黑现象;机加工槽粗糙度为Ra1.6;KPCKCC KPCKPCKCCKCCKCC检验110-1机加一序MTL0142/147KPC除非另有说明,螺纹孔倒角至大径,螺纹孔内无铝屑;110-2机加二序MTL0142/1472-Φ3.3深13.1±2.02-M4X0.7-6H 深11.0Min5-Φ3.3深10.1±2.05-M4X0.7-6H 深8.0Min2-Φ3.3深11.1±2.02-M4X0.7-6H 深9.0Min14-Φ3.3深9.114-M4X0.7-6H 深7.0Min4-Φ3.3深12.1±1.04-M4X0.7-6H 深10.0Min4-Φ2.5深9.5±1.04-M3X0.5-6H 深8.0MinΦ3.3深11.1±2.0M4X0.7-6H 深9.0MinKPCKCCKPCKPCKCC KPCKCCKCCKPCKCCKPC1.加工中心2.刀具3.夹具4.切削液浓度KCCKPCKCC110-3机加三序MTL0142/147更改级别:/日期(最初):更改日期:/日期(修订):过程流程图文件编号:/ 零件号:零件名称:图纸日期:图 纸 号:Φ3.3深11.1±2.0M4X0.7-6H 深9.0MinΦ3.3深10.1±2.0M4X0.7-6H 深8.0Min(4.0X2.0)±0.21.9±0.22±0.21.7Min 2±0.2Φ36.9±0.2 (通)Φ2.7深10.4±1.0检验KPC 机加工槽无振刀纹,边缘无毛刺;机加工槽无发霉、发黑现象;除非另有说明,螺纹孔倒角至大径,螺纹孔内无铝屑,机加工槽边缘毛刺清理干净;机加工槽粗糙度为Ra1.6KPC1.加工中心KPCKPCKCCKCC加工中心2.刀具3.夹具KCCKPC KCCMTL0142/147KCC更改级别:/日期(最初): 更改日期:/日期(修订):/ 零件号:零件名称:图纸日期:图 纸 号:。
机械加工检验控制程序

1.0 目的: 本程序规定了机械加工过程中质量检验程序,明确和统一产品质量检验控制方式。 2.0 适用范围: 公司机加工过程的质量检验。 3.0 流程图: 本程序适用于
机械加工检验流程图
生产调试
责任人
作业内容
投入生产时,操作者先对产品进行调试,并做自 检,检验合格后首件检验;不合格继续调试
检验员
检验员定时进行巡检并填写相关检验记录
Байду номын сангаас
检验员
检验员结果判定合格,继续生产;判定不合格, 立即停机改善,通知操作者调试;将这一时间段 生产的产品进行标识、隔离,并按照《不合格品 处理程序》执行
操作者
自检 合格 首样送检 合格 批量生产 合格 定时自检 不合格 质检员/
车间主任
记录 不合格
检验员
检验员对产品进行首件检验,检验合格,通过操 作者开始生产;检验不合格交操作者继续调试, 直到合格 操作者开始批量生产
操作者
操作员
操作者定时进行自检,并填写相关检验结果
车间主任
合格 定时巡检 不合格 车间主任 合格 终检 合格 入库 不合格 车间主任 不合格评审
- 1、下载文档前请自行甄别文档内容的完整性,平台不提供额外的编辑、内容补充、找答案等附加服务。
- 2、"仅部分预览"的文档,不可在线预览部分如存在完整性等问题,可反馈申请退款(可完整预览的文档不适用该条件!)。
- 3、如文档侵犯您的权益,请联系客服反馈,我们会尽快为您处理(人工客服工作时间:9:00-18:30)。
品检验流程图
品质主管
保证合格设备出厂 统计质量信息报告
单个零件检验
待检零件 按图纸要求检 堆 放 区 验各待检零件
安装过程检验
按组装图要求检 验安装过程设备
设备出厂检验
按总装图要求 检验出厂设备
检验部门 检验区
合格品 入库
安装部门 组装区
合格品 入库
安装部门 总装区
检验后零件
检验后部件
检验后设备
不良零件
合格零件
不良部件
合格部件
不良设备
合格设备
返回给供应商 办理利用品零件
返回给设备组装 办理整改措施 返回给设备总装 办理整改措施
品质主管设计确认签字
品质主管设计确认签字
品质主管设计确认签字