换热器管子与管板接头胀接工艺守则
换热器管子与管板接头胀接工艺守则

换热器管子与管板接头胀接工艺守则1总则本守则规定了压力容器管子与管板的胀接方法和技术要求;本守则适用于GB150、GB151及《固容规》涉及的强度胀、焊后胀,胀后焊结构的容器产品; 2胀接操作人员2.1 胀接操作人员必须经过有关部门技术培训,考试合格后方能上岗;2.2 胀接操作人员应掌握所用胀接设备的使用性能,熟悉产品图样、工艺文件及标准要求; 2.3 胀接操作人员应认真做好胀接场地的管理工作,对所用工、量、检具能正确使用和妥善保管;3. 胀接设备与胀管器3.1 胀接设备与胀管器应能满足胀接技术条件及有关标准要求;3.2 胀接设备一般有如下几种:a.无自动控制胀管率装置的机械式胀管机;b.液压驱动扭矩自动控制胀管率的胀管机;c.微机控制胀管率的机械式胀管机;d.液压橡胶柔性胀管机;上述胀接设备可视产品情况选择使用;3.3 胀管器可与相应胀接设备一同使用或直接用于手工胀接;3.3.1 胀管器按用途一般分为:a.12°~15°扳边胀管器;b.90°扳边胀管器;c.无扳边胀管器;3.3.2 胀管器按胀柱数量一般分为:a.3个胀柱胀管器;b.5个胀柱胀管器;应优先选用5胀柱胀管器;3.3.3 90°扳边胀管器一般有普通90°扳边胀管器与90°无声扳边胀管器之分;应优先选用无声扳边胀管器;取1个试样;b样坯切取位置及方向应符合GB2975的规定;c硬度测试可在切取的试样上进行,亦可在管板和胀接管端上直接进行;测试前,应将测点处的氧化皮、锈蚀、油污清除掉,使之露出金属光泽;d当在试样上进行时,试验方法、试样尺寸及表面要求应符合GB231的规定;e当在管板和胀接管端上直接进行时,管子测点数量为每台锅炉按胀接管子总数的3%选取,且不少于15点;每根管端上最多不超过3点,测点位置应在距管端50mm范围内;管板测点数量为每个管板取3点,测点均匀分布;4.5胀接管端需做退火处理时,应符合下列要求:a退火可采用电加热,亦可采用火焰直接加热;当采用火焰加热时其燃料可采用焦炭、木炭、锯末,但不得用煤炭做燃料直接加热;b加热时应缓缓升温,平均温升不超过15℃/min,退火温度控制在600~650℃(无论用何种方法加热,都不得将管端加热至650℃以上),保温10~15min,保温后管端应埋于干燥的石棉灰或硅藻土或石灰粉中缓冷,埋入深度不小于350mm,冷却至室温后方可取出;c加热退火时必须配有温控装置或仪器,不得目测估量;d管端退火长度应控制在100~150mm;两端可同时加热;当管子一端加热时,应用木塞将管子的另一端堵住,以防空气在管内流动;加热过程中应旋转管子,使管端加热均匀;4.6胀接前须按下列要求对胀接管端进行清理:a管端外表面应用半自动双头磨管机或机械洗管机等除锈磨光,磨光长度不小于两倍的管板厚度mm;除锈磨光后的表面不应有起皮、凹痕、裂纹和纵向沟槽等缺陷,磨光后的最小管端外径应符合GB8163规定;管端内表面应无严重锈蚀和铁屑等杂物并清除毛刺;b除锈磨光后的胀接管子应及时胀接,如不能及时装配胀接,则应妥善保管以防再次生锈;如生锈应重新打磨,打磨后的管端最小外径仍须符合GB8163规定;5.胀接管孔的技术要求5.1 用汽油或四氟化碳等溶剂清洗管孔壁上的油污,再用细纱布沿孔壁圆周方向打磨残留锈蚀,并除去管孔边缘毛刺;打磨后管孔壁的表面粗糙度不得大于Ra12.5;5.2 清理后的管孔壁不得有纵向刻痕,个别管孔允许有一条螺旋形或环向刻痕,刻痕深度不得超过0.5mm,宽度不得超过1mm,刻痕至管孔边缘的距离不得小于4mm;5.3 胀接管孔尺寸应符合图纸工艺要求;5.4 如管孔直径超差,其超差数值不得超过规定偏差值的50%;当管孔总数不大于500个时,超差孔数不得超过管孔总数的2%,且不得超过5个;当管孔总数大于500个时,超差孔数不得超过管孔总数的1%,且不得超过10个;对于超差管孔在管板上应作出明显标记;6.胀接前对胀接设备的检查6.1 胀管器,胀杆锥度及胀珠胀杆转动灵活;6.2 液压驱动胀管设备和微机控制胀管设备其控制系统应准确灵敏、性能良好;6.3 胀管器先检查外观,然后用涂色法检查接触面(接触面应大于80%),合格后涂以润滑脂待用;7.穿管7.1 穿管前应先按图样核对管板的装配位置;7.2 按照每个胀接面管子、管孔总数的15%,随机测量管孔直径d、管端壁厚t,计算出d、t的算术平均值并做好记录(参见附录A表A1);7.3 根据超差管孔的直径选配管子,选配后的最大间隙不超过管子直径的3%;7.4 管子的两个胀接端穿入管孔时应能自由伸入,管子必须装正,不得歪斜;当发现有卡住,偏斜等现象时,不得强行插入,应取出管子,按大样矫正后,再行插入;7.5 穿管时应超穿一定距离,以再次清理胀接管端或管孔壁上因穿管留下的锈屑污物,清理后,退回正确位置;7.6 管子与管板胀接时,可先穿基准管,基准管找正后,采用预胀或其他方法加以固定;7.7 胀接管端伸出长度应符合图样要求;7.8 对于管端伸出长度超过要求的管子,应用机械(齐头机)方法去除超长部分,并清除毛刺;8.胀接技术要求8.1 试胀8.1.1 正式胀接前应进行试胀,以检查胀管器的质量、管材的胀接性能和确定最佳胀管率;8.1.2 试胀用管子的材质、规格应与产品胀接管子相同,试胀用板的材质、厚度及管孔间距、管孔尺寸、加工质量等均应与产品的管板相同;8.1.3 试胀件尺寸规格及数量按照产品图纸管板的厚度,孔的大小、排列做试胀板一块,开孔12~16个;8.1.4 试胀管子的胀接管端硬度应符合4.5规定;当管端退火时,应按4.6随炉退火,退火后的管端应按要求进行清理;8.1.5 试胀管子与管孔一一对应,编号入座,用油漆在试胀板上做出孔位编号,用游标卡尺逐一测量试胀管壁厚t、管孔直径d值,并作好记录(参见附录A表A2);8.1.6 在胀管率H为1%~2.1%范围内,选用不同的胀管率数值,计算出相应的胀口内径d1值,然后对各个胀口进行试胀,实测胀口内径并作好记录(参见附录A 表A2);8.2 胀接8.2.1 根据试胀所确定的最佳胀管率进行正式胀接;胀接时应在管端内壁涂少许润滑脂,再插入胀管器;胀接过程中,严防油污、水及灰尘渗入胀接面间;8.2.2 胀接时一般采用反阶式胀接顺序,见图4;管子与管板胀接可在管子穿妥后再按图4进行胀接;管子与管板胀接时,为防止油污流进胀接面间,亦可采用错列式胀接顺序,见图5;不足2个时,允许超胀2个;8.3 胀管率的间接控制方法8.3.1 采用液压柔性胀接时控制胀接压力;8.3.2 采用液压驱动机械胀管或微机控制机械胀管时,控制胀接扭矩;采用普通机械胀管时,使用胀管限位器控制胀杆进入胀口的相对位置;8.4 胀口质量要求8.4.1 管端内表面不应有粗糙、剥落、刻痕、裂纹等;8.4.2 12°~15°扳边后管端不应有裂纹;8.4.3 90°扳边后边缘不应有超过2mm长的细小裂纹;8.4.4 胀口处应无偏挤(单边);8.4.5 胀口的内径圆度公差大于0.15mm时,其超差数量在同一胀接面处不得超过胀接总数的10%;9.水压试验、补胀和换管技术要求9.1 胀接管子全部胀妥后,进行胀口及管板的内部清理,并检查管子有无堵塞;9.2 水压试验前应拆除本体组装设施或临时支架;9.3 水压试验按图纸、工艺及《固定式容规》进行;9.4 水压试验检查应在试验压力降至工作压力时进行,检查胀口有无漏水(漏水是指水珠向下流)、水印(指仅有水迹)和泪水(指水压试验期间不向下流的水珠);如发现上述缺陷,应在相应管端处分别作出标记;9.5 对水压试验漏水的胀口或超过允许数量的泪水、水印的胀口应在卸压放水后随即进行补胀,同时还应对其邻近的一些胀口稍加补胀以免受到影响而松弛;补胀前应测量胀口内径;确定合适的补胀量,以免超胀;9.6 同一漏水胀口,补胀次数不宜多于2次,补胀后应重新进行水压试验,对补胀后仍有漏水且胀管率已超过2.8%的管子应予换管重胀(在割除不合格的胀接管子时,必须注意不损伤管孔壁);补胀、重胀后的胀管率应符合8.2.9要求;9.7 应有专人负责记录胀接及水压试验结果(参见附录A表A3),以作为验收依据并备案;10.贴胀(或称“轻胀”、“预胀”)技术要求10.1 贴胀宜在需贴胀的管子焊接后进行,也可在焊接前进行;10.2 当图样要求贴胀或要求用胀接方法消除管子与孔壁间隙时,应采用与前述相同的胀接设备和操作方法,使管子外壁紧贴管孔内壁,并有一定的胀紧力,以消除管子与管孔间的间隙; 10.3 当采用手工贴胀时,应胀至感到扭矩明显增大时止;当采用机械或液压驱动贴胀时,应胀至负载明显时止;10.4 前部管子贴胀完毕后,应仔细检查外观质量,并应用小手锤轻击接近管孔的管段,监听贴胀质量(贴胀紧密时,其声音沉闷;而未贴紧时,声音较清脆);注:贴胀的目的仅是为了消除管子与管孔的间隙及降低焊接应力;因此,在执行本守则时,当对管子按规定进行材质、外观质量检验并合格后,对管子和管板的硬度检查、试胀、胀管率、扳边、记录、检查胀接质量的水压试验等要求均可免去;附录A胀接用数值记录表( 参考件)A1 胀接前各胀接面15%的管子、管孔数值测量记录表,见表A1;注:1.管板管孔:水平—纵向;垂直—环向;2.每个胀接面要分别测量、计算算术平均值;A2 试胀用数值记录表,见表A2注:Hj—最佳胀管率;d1j—最佳胀管率时的胀口内径;A3 胀接后数值记录表,见表A3注:管板管孔:水平—纵向;垂直,。
换热器通用胀接工艺

胀管通用工艺规程一、胀接说明1 胀接胀接是换热管与管板的主要联接形式之一,它是利用胀管器伸入换热管管头内,挤压管子端部,使管端直径扩大产生塑性变形,同时保持管板处在弹性变形范围内。
当取出胀管器后,管板孔弹性变形,管板对管子产生一定的挤紧压力,使管子与管板孔周边紧紧地贴合在一起,达到密封和固定连接的目的。
由于管板与管子的胀接消除了弹性板与塑性管头之间的间隙,可有效地防止壳程介质的进入而造成的缝隙腐蚀。
当使用温度高于300℃时,材料的蠕变会使挤压残余应力逐渐消失,连接的可靠性难以保证。
因此,在这种工况下,或预计拉脱力较大时,可采用管板孔开槽的强度胀接。
胀接又分为贴胀和强度胀。
2 胀管率胀管率是换热管胀接后,管子直径扩大比率。
贴胀与强度胀的主要区别在于对管子胀管率 (管子直径扩大比率) 的控制不同,对冷换设备换热管来说,强度胀要求的胀管率H为1~2.1%,而贴胀要求的胀管率H为0.3~0.7%。
3 贴胀贴胀是轻度胀接的俗称,贴胀是为消除换热管与管板孔之间的缝隙,以防止壳程介质进入缝隙而造成的间隙腐蚀。
由于贴胀时胀管器给管子的胀紧力较小,管子径向变形量也就比较小。
因此换热管与管板孔之间的相对运动的摩擦力就比较小,所以它不能承受较大的拉脱力,且不能保证连接的可靠性,仅起密封作用。
贴胀时,管孔不需要开槽。
4 强度胀强度胀是指管板与换热管连接处的密封性和抗拉脱强度均由胀接接头来保证的连接方式。
强度胀接的管板孔要求开胀管槽,一般开两道胀管槽。
以使管子材料在胀接时嵌入胀管槽内,由此来增加其拉脱力。
特别是当使用温度高于300℃时,材料的蠕变会使挤压残余应力逐渐消失,连接的可靠性下降,甚至发生管子与管板松脱,这时采用强度胀接,其抗拉脱力就比贴胀要大得多。
胀管前应用砂轮磨掉表面污物和锈皮,直至呈现金属光泽,清理锈蚀长度应不小于管板厚度的2倍。
管板硬度应比管子硬度高HB20~30,以免胀接时管板孔产生塑性变形,影响胀接的紧密性。
胀接工艺守则

胀接工艺守则1总则管板和换热管是换热器的主要受压元件,二者之间的连接处是换热器的关键部位。
而胀接是实现换热管与管板连接的方法之一,胀接质量的好坏对换热器的正常运作起着关键作用。
2胀接型式和方法胀接型式按胀接进度可分为贴胀和强度胀2.1贴胀是为消除换热管与管板直径缝隙的轻度胀接,其目的是为了小处缝隙腐蚀和提高焊缝的抗疲劳性能,贴胀后胀接接头的抗拉脱力应达到IMPa 以上;2.2强度胀是包装换热管与管板连接的密封性能及抗拉脱轻度的胀接。
强度胀接后胀接接头的抗拉脱力应达到4MPa以上;2.3胀接方法按胀接工艺的不同可分为机械胀和柔性胀接(橡胶胀、液压胀、液袋式液胀等)。
3胀管器的选用胀管器主要根据换热管的直径、管板厚度、胀接长度及胀接特点来确定,通常有胀接器生产厂家按胀接条件选定。
4换热管与管板硬度测定4.1胀接的远离是胀接时硬度较低的管子产生塑性变形,而硬度较高的管板产生弹性形变,胀接后塑性变形管子收到弹性变形额管板孔壁的挤压而使管子和管板紧密地结合在一起,因此在试胀前应首先测定管子与管板的硬度值是否相匹配;4.2换热管与管板的材料应有适当的硬度差,管板硬度应大于换热管的硬度,其差值最好达到HB30以上,否则胀接后管子的回弹量接近或大于管板的回弹量而造成胀接接头不紧,如果二者硬度差相差很小时,应对管子端部进行退火处理,管子端部退火处理长度一般为管板厚度加IOOmmO5试胀5.1正式胀接之前应进行试胀。
试胀的目的是验证胀管器质量的好坏,验证预定的管子与管板孔的结构是否合理,检验胀接部位的外观质量及接头的密封性能,测试胀接接头的抗拉脱力,孕照合适的胀管率,以便制定合理的产品胀接工艺;5.2试胀应在试胀工艺试板上进行,试板应与产品管板的材料、厚度、管孔大小一致,试板上孔的数量应不少于5个,其管孔的排列形式应与产品管孔排列形式一致,试胀所用管子的材料、规格应与产品用换热器一致,但长度可以不一致,一般为管板厚度加50mm;5.3试胀前应根据胀管率计算公式推送出换热管胀接后的内件尺寸,胀管率计算公式可按我国锅炉规程中给出的公式计算:H=(dι-d2-δ)∕d3×100%δ一一胀前管孔直径与管子外径之差5.4胀管率应在0.9%~2.2%之间选取,胀管率小于0.9%为欠胀,管子胀后为产生足够的塑性变形,不能保证资金质量;胀管率大于2.2%为过胀,管子胀后产生过大的塑性变形,加工硬化现象严重,容易导致管子处理裂纹等缺陷,管板也可能产生塑性变形而使胀后的管板不能有效的回弹,从而影响胀接接头的性能。
胀接通用工艺守则

胀接通用工艺守则1.目的为了确保各种换热器、油冷却器在使用过程中不发生泄露现象。
2.适用范围2.1本守则规定了各种换热器、油冷却器管子与管板的胀接方法和技术要求。
2.2本守则适用于本公司制造的换热器、油冷却器在装备过程中的胀接。
3. 胀接操作人员3.1胀接操作人员应经过有关部门技术培训,考试合格后方能上岗。
3.2胀接人员连续脱岗半年,应重新进行技术培训,经考试合格后,方可回岗工作。
3.3胀接操作人员应掌握所用胀接设备的使用性能,熟悉产品图样、工艺文件及标准要求。
3.4胀接操作人员应认真做好胀接场地的管理工作,对所用的工、量、检具能正确使用和妥善保管。
4. 胀接设备和掌管器4.1胀接设备于胀管器应能满足胀接技术条件及有关标准要求。
4.2掌管设备一般有如下几种:a)无自动控制胀管装置的机械式胀管机;b)液压驱动扭矩自动控制胀管率的胀管机;c)微机控制胀管率的机械式胀管机;d)液压橡胶柔性胀管机。
4.3胀管器可与相应胀接设备一同使用或直接用于手工胀接。
4.3.1胀管器按用途一般分为:a)12°~15°扳边胀管器;b)90°扳边胀管器;c)无扳边胀管器。
4.3.2胀管器按胀柱数量一般分为:a)3个胀柱一个翻边柱胀管器;b)4个胀柱2个翻边胀管器。
应优先选用4胀柱胀管器。
4.3.3 90°扳边胀管器一般有普通90°扳边工具与90°无声扳边胀管器之分。
应优先选用无声扳边胀管器。
5. 胀接管子技术要求5.1胀接管子应符合GB8890、GB14976、GB/T8163的规定,必须经涡流检测合格的管子。
5.2胀接管子的外表不应有重皮、裂纹、压扁等缺陷,胀管端不应有纵向裂纹,如有纵向刻痕、麻点等缺陷式,缺陷深度不应超过管子公称壁厚的10%。
5.3胀接管子的制造偏差应符合相关要求。
5.4胀接管子的断面倾斜度Δf应不大于管子公称外径的1.5%,且最大不大于1mm(见图1)5.5管端硬度应低于管板硬度,若管端硬度大于管板,应进行退火处理。
换热管与管板账接

xx换热管与管板账接xxxxxxxx1 范围本标准规定了换热管与管板胀接的基本要求。
本标准适用于碳钢、合金钢、不锈钢等材料的胀接。
铜及铜合金的胀接可参照使用。
2 引用标准下列标准所包含的条文,通过在本标准中引用而构成为本标准的条文。
在标准出版时,所示版本均为有效。
所有标准都会被修订,使用本标准的各方应探讨,使用下列标准最新版本的可能性。
GB151-1999 钢制管壳式换热器3 定义本标准采用下列定义。
3.1 胀接利用胀管器使换热管与管板之间产生挤压力而紧贴在一起,达到密封与紧固连接的目的。
3.2 胀管率换热管与管板胀接后,换热管壁厚的减薄率。
3.3 强度胀为保证换热管与管板连接的密封性能及抗拉脱强度的胀接。
3.4 密封胀为保证换热管与管板连接的密封性能的胀接。
3.5 贴胀为消除换热管与管孔之间缝隙的轻度胀接。
4 总则换热管与管板的胀接除应符合本标准的规定处,还应满足图样和GB151的有关要求。
5 胀接工艺试验5.1 当换热管与管板的连接采用只胀不焊,或采用液压胀接时,产品胀接前应进行换热管与管板的胀接工艺试验,本公司已有成熟胀接工艺的则可免做此项试验。
5.2 胀接工艺试验的内容5.2.1 换热管与管板胀接胀管率的测试,及胀管率的控制试验。
5.2.2 换热管与管板胀接采用强度胀、密封胀时应做水压试验。
5.2.3 换热管与管板胀接采用强度胀时应做拉脱试验。
5.3 胀接工艺试验材料5.3.1 试验用管板应与产品管板具有相同材质和相当的机械性能。
5.3.2 试验用管子应是产品所用的换热管。
6 胀前准备6.1 换热管6.1.1 胀前应抽测出换热管的内径、外径、壁厚并计算出壁厚偏差值。
6.1.2 胀前应提供换热管的屈服强度、延伸率、硬度的数据。
6.2 管板6.2.1 胀前应提供管板的屈服强度、硬度的数据。
6.2.2 抽测出管孔的孔径、胀管槽的轴向位置、宽度、深度。
6.2.3 采用液压胀接的管板,胀管槽应按图1加工制作。
胀接通用工艺

胀接通用工艺1. 总则:本通用工艺适用于管壳式换热器管板与管子的胀接。
2 胀管前准备2.1 管端及管板必须清理干净,不得有油渍污物、毛刺、铁屑、锈蚀等杂物;管孔表面不得有影响紧密性的缺陷,如贯通的纵向或螺旋状刻痕等。
2.2 测量管板厚度,检查所领的胀管器是否符合要求。
2.3 准备润滑油及冷却用油。
3 胀管长度3.1 胀接连接时,其胀接长度不得伸出管板背面(壳程侧),换热管的胀接部分与非胀接部分应圆滑过渡,不得有急剧的棱角。
4 胀管率ρ对于钢管和钢管板,ρ=12~18%为强度胀接;ρ=7~10%为紧密胀接;ρ=3~7%为贴合胀接,不能保证联接强度和严密度。
过大的ρ会使管壁加工硬化严重,甚至发生裂纹,胀接强度也会降低。
如果管子直径较大,管子的金属材料较软,且管板的金属材料较硬时,则选取较大的胀管率。
其值可按下式计算:ρ=(d K-d N-e)/Do×100%式中:d K——管子胀接后的内径d N——管子胀接前的内径e—胀接前管子与管板的间隙(即管子胀前外径)Do—胀接前管板孔径5 胀接过程5.1 为减少管板胀后变形,推荐按梅花状的顺序定位胀。
5.2 对大直径,(D N>1000)特别是薄管板,为避免胀后变形,在定位胀前,将两管板保持与管子垂直,测量四点,其中两管板间距之差不得超过:D N<1000时2mm;D N≥1000时3mm。
两管板按上述要求调好后,靠近中心处临时用拉杆若干根将两管板拉紧,再按上述步骤胀接。
5.3 胀接过程中允许施用润滑油,但一定要防止润滑油带入管板孔内。
5.4 胀管时,一旦过胀,发现管子胀裂,需更换管子,管子抽出后,修磨管板孔。
管孔最大直径应不大于Do+1㎜。
5.5 管子全部胀完后,应逐根检查管口是否有漏胀。
如果管头超差应用钻头锪到允许范围,见下表6 胀管质量要求:6.1 胀口内壁光滑平整,无凹陷擦伤、重皮、起毛。
6.2 胀口扩大部分的过渡区应无明显棱角,不准出现裂纹。
换热器通用胀接工艺 精品
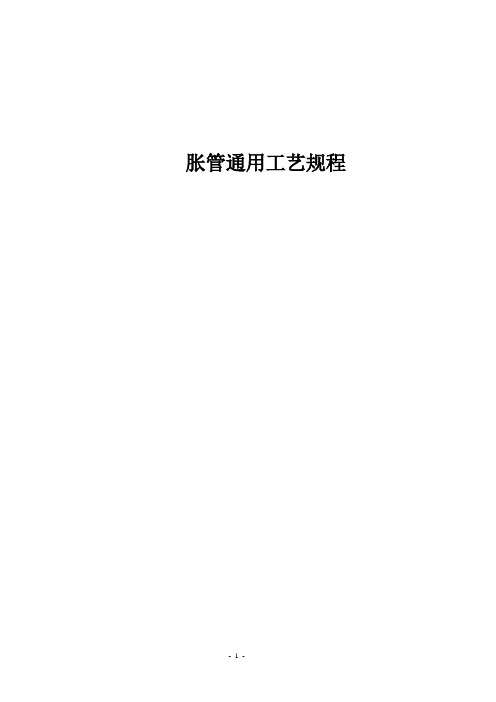
胀管通用工艺规程一、胀接说明1 胀接胀接是换热管与管板的主要联接形式之一,它是利用胀管器伸入换热管管头内,挤压管子端部,使管端直径扩大产生塑性变形,同时保持管板处在弹性变形范围内。
当取出胀管器后,管板孔弹性变形,管板对管子产生一定的挤紧压力,使管子与管板孔周边紧紧地贴合在一起,达到密封和固定连接的目的。
由于管板与管子的胀接消除了弹性板与塑性管头之间的间隙,可有效地防止壳程介质的进入而造成的缝隙腐蚀。
当使用温度高于300℃时,材料的蠕变会使挤压残余应力逐渐消失,连接的可靠性难以保证。
因此,在这种工况下,或预计拉脱力较大时,可采用管板孔开槽的强度胀接。
胀接又分为贴胀和强度胀。
2 胀管率胀管率是换热管胀接后,管子直径扩大比率。
贴胀与强度胀的主要区别在于对管子胀管率 (管子直径扩大比率) 的控制不同,对冷换设备换热管来说,强度胀要求的胀管率H为1~2.1%,而贴胀要求的胀管率H为0.3~0.7%。
3 贴胀贴胀是轻度胀接的俗称,贴胀是为消除换热管与管板孔之间的缝隙,以防止壳程介质进入缝隙而造成的间隙腐蚀。
由于贴胀时胀管器给管子的胀紧力较小,管子径向变形量也就比较小。
因此换热管与管板孔之间的相对运动的摩擦力就比较小,所以它不能承受较大的拉脱力,且不能保证连接的可靠性,仅起密封作用。
贴胀时,管孔不需要开槽。
4 强度胀强度胀是指管板与换热管连接处的密封性和抗拉脱强度均由胀接接头来保证的连接方式。
强度胀接的管板孔要求开胀管槽,一般开两道胀管槽。
以使管子材料在胀接时嵌入胀管槽内,由此来增加其拉脱力。
特别是当使用温度高于300℃时,材料的蠕变会使挤压残余应力逐渐消失,连接的可靠性下降,甚至发生管子与管板松脱,这时采用强度胀接,其抗拉脱力就比贴胀要大得多。
胀管前应用砂轮磨掉表面污物和锈皮,直至呈现金属光泽,清理锈蚀长度应不小于管板厚度的2倍。
管板硬度应比管子硬度高HB20~30,以免胀接时管板孔产生塑性变形,影响胀接的紧密性。
胀管工艺规程
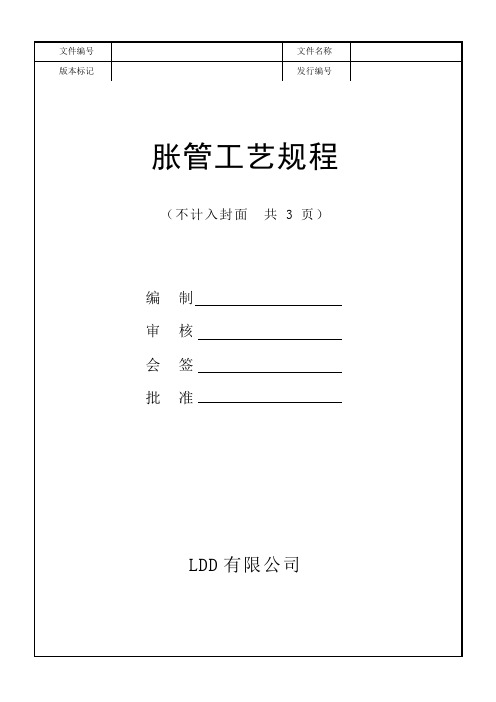
(不计入封面 共3页)
编制
审核
会签
批准
LDD有限公司
一、胀接管子的技术要求
1、胀接管子外表面不得有重皮、压扁、裂纹等表面缺陷,胀接管端不得有纵向刻痕。如有横向刻横、麻点等缺陷时,缺陷深度不超过管子公称壁厚的10%。
2、胀接管子的端面倾斜度应不大于管子公称外径的1.5%,且最大不超过1mm。
10.21~10.3
12.22~12.32
14.23~
14.35
17.25~17.38
23.28~23.46
铜管规格
16X1.5
16X1.8
不锈钢管规格
12~13.35
12.64~12.78
胀管后内径
12.24~
10.32
14.26~14.37
23.89~24.08
3)胀接时每胀完15-20个管口,应对胀管器进行清洗,检查有无损伤,反之更换。
4、胀管率控制
①强度胀:换热管材料为铜、铜合金及不锈钢时,胀管率一般控制在0.5%~1.2%范围内,超胀不得超过2.0%;换热管材料为10钢或20钢时,胀管率一般控制在0 7%~2.1%范围内,超胀不得超过2.8%;换热管材料为黄铜时,胀管率一般控制在1%~1.8%范围内,超胀不得超过2.5%。
4)同一胀口漏水,补胀次数不应多于2次,补胀后重新进行水压试验。对于补胀后仍有漏水且胀管率大于超胀指标的管子应换管重胀。(在割除不合格的管子时,必须注意不损伤管孔壁)
5)应有专人负责记录胀接和水压试验结果,以作为验收依据并备案。
2、胀管率检验
1)每面管板按5%均布随机测量胀后换热管内径,且不少于20根,对少于20根的全部进行测量,比较理论胀管内径值,对于欠胀的管头进行补胀,补胀前应测量胀口内径,确定合适的补胀量,以免超胀。
- 1、下载文档前请自行甄别文档内容的完整性,平台不提供额外的编辑、内容补充、找答案等附加服务。
- 2、"仅部分预览"的文档,不可在线预览部分如存在完整性等问题,可反馈申请退款(可完整预览的文档不适用该条件!)。
- 3、如文档侵犯您的权益,请联系客服反馈,我们会尽快为您处理(人工客服工作时间:9:00-18:30)。
换热器管子与管板接头胀接工艺守则
1总则
本守则规定了压力容器管子与管板的胀接方法和技术要求;
本守则适用于GB150、GB151及《固容规》涉及的强度胀、焊后胀,胀后焊结构的容器产品; 2胀接操作人员
2.1 胀接操作人员必须经过有关部门技术培训,考试合格后方能上岗;
2.2 胀接操作人员应掌握所用胀接设备的使用性能,熟悉产品图样、工艺文件及标准要求; 2.3 胀接操作人员应认真做好胀接场地的管理工作,对所用工、量、检具能正确使用和妥善保管;
3. 胀接设备与胀管器
3.1 胀接设备与胀管器应能满足胀接技术条件及有关标准要求;
3.2 胀接设备一般有如下几种:
a.无自动控制胀管率装置的机械式胀管机;
b.液压驱动扭矩自动控制胀管率的胀管机;
c.微机控制胀管率的机械式胀管机;
d.液压橡胶柔性胀管机;
上述胀接设备可视产品情况选择使用;
3.3 胀管器可与相应胀接设备一同使用或直接用于手工胀接;
3.3.1 胀管器按用途一般分为:
a.12°~15°扳边胀管器;
b.90°扳边胀管器;
c.无扳边胀管器;
3.3.2 胀管器按胀柱数量一般分为:
a.3个胀柱胀管器;
b.5个胀柱胀管器;
应优先选用5胀柱胀管器;
3.3.3 90°扳边胀管器一般有普通90°扳边胀管器与90°无声扳边胀管器之分;应优先选用无声扳边胀管器;
取1个试样;
b样坯切取位置及方向应符合GB2975的规定;
c硬度测试可在切取的试样上进行,亦可在管板和胀接管端上直接进行;测试前,应将测点处的
氧化皮、锈蚀、油污清除掉,使之露出金属光泽;
d当在试样上进行时,试验方法、试样尺寸及表面要求应符合GB231的规定;
e当在管板和胀接管端上直接进行时,管子测点数量为每台锅炉按胀接管子总数的3%选取,且
不少于15点;每根管端上最多不超过3点,测点位置应在距管端50mm范围内;管板测点数量为每个管板取3点,测点均匀分布;
4.5胀接管端需做退火处理时,应符合下列要求:
a退火可采用电加热,亦可采用火焰直接加热;当采用火焰加热时其燃料可采用焦炭、木炭、锯末,但不得用煤炭做燃料直接加热;
b加热时应缓缓升温,平均温升不超过15℃/min,退火温度控制在600~650℃(无论用何种方法
加热,都不得将管端加热至650℃以上),保温10~15min,保温后管端应埋于干燥的石棉灰或硅藻土或石灰粉中缓冷,埋入深度不小于350mm,冷却至室温后方可取出;
c加热退火时必须配有温控装置或仪器,不得目测估量;
d管端退火长度应控制在100~150mm;两端可同时加热;当管子一端加热时,应用木塞将管子的另一端堵住,以防空气在管内流动;加热过程中应旋转管子,使管端加热均匀;
4.6胀接前须按下列要求对胀接管端进行清理:
a管端外表面应用半自动双头磨管机或机械洗管机等除锈磨光,磨光长度不小于两倍的管板厚度mm;除锈磨光后的表面不应有起皮、凹痕、裂纹和纵向沟槽等缺陷,磨光后的最小管端外径应符合GB8163规定;管端内表面应无严重锈蚀和铁屑等杂物并清除毛刺;
b除锈磨光后的胀接管子应及时胀接,如不能及时装配胀接,则应妥善保管以防再次生锈;如生
锈应重新打磨,打磨后的管端最小外径仍须符合GB8163规定;
5.胀接管孔的技术要求
5.1 用汽油或四氟化碳等溶剂清洗管孔壁上的油污,再用细纱布沿孔壁圆周方向打磨残留锈蚀,并除去管孔边缘毛刺;打磨后管孔壁的表面粗糙度不得大于Ra12.5;
5.2 清理后的管孔壁不得有纵向刻痕,个别管孔允许有一条螺旋形或环向刻痕,刻痕深度不得
超过0.5mm,宽度不得超过1mm,刻痕至管孔边缘的距离不得小于4mm;
5.3 胀接管孔尺寸应符合图纸工艺要求;
5.4 如管孔直径超差,其超差数值不得超过规定偏差值的50%;当管孔总数不大于500个时,超差孔数不得超过管孔总数的2%,且不得超过5个;当管孔总数大于500个时,超差孔数不得超过管孔总数的1%,且不得超过10个;对于超差管孔在管板上应作出明显标记;
6.胀接前对胀接设备的检查
6.1 胀管器,胀杆锥度及胀珠胀杆转动灵活;
6.2 液压驱动胀管设备和微机控制胀管设备其控制系统应准确灵敏、性能良好;
6.3 胀管器先检查外观,然后用涂色法检查接触面(接触面应大于80%),合格后涂以润滑脂待用;
7.穿管
7.1 穿管前应先按图样核对管板的装配位置;
7.2 按照每个胀接面管子、管孔总数的15%,随机测量管孔直径d、管端壁厚t,计算出d、t的算术平均值并做好记录(参见附录A表A1);
7.3 根据超差管孔的直径选配管子,选配后的最大间隙不超过管子直径的3%;
7.4 管子的两个胀接端穿入管孔时应能自由伸入,管子必须装正,不得歪斜;当发现有卡住,偏斜等现象时,不得强行插入,应取出管子,按大样矫正后,再行插入;
7.5 穿管时应超穿一定距离,以再次清理胀接管端或管孔壁上因穿管留下的锈屑污物,清理后,退回正确位置;
7.6 管子与管板胀接时,可先穿基准管,基准管找正后,采用预胀或其他方法加以固定;
7.7 胀接管端伸出长度应符合图样要求;
7.8 对于管端伸出长度超过要求的管子,应用机械(齐头机)方法去除超长部分,并清除毛刺;
8.胀接技术要求
8.1 试胀
8.1.1 正式胀接前应进行试胀,以检查胀管器的质量、管材的胀接性能和确定最佳胀管率;
8.1.2 试胀用管子的材质、规格应与产品胀接管子相同,试胀用板的材质、厚度及管孔间距、管孔尺寸、加工质量等均应与产品的管板相同;
8.1.3 试胀件尺寸规格及数量
按照产品图纸管板的厚度,孔的大小、排列做试胀板一块,开孔12~16个;
8.1.4 试胀管子的胀接管端硬度应符合4.5规定;当管端退火时,应按4.6随炉退火,退火后的管端应按要求进行清理;
8.1.5 试胀管子与管孔一一对应,编号入座,用油漆在试胀板上做出孔位编号,用游标卡尺逐一测量试胀管壁厚t、管孔直径d值,并作好记录(参见附录A表A2);
8.1.6 在胀管率H为1%~2.1%范围内,选用不同的胀管率数值,计算出相应的胀口内径d1值,然后对各个胀口进行试胀,实测胀口内径并作好记录(参见附录A 表A2);
8.2 胀接
8.2.1 根据试胀所确定的最佳胀管率进行正式胀接;胀接时应在管端内壁涂少许润滑脂,再插入胀管器;胀接过程中,严防油污、水及灰尘渗入胀接面间;
8.2.2 胀接时一般采用反阶式胀接顺序,见图4;管子与管板胀接可在管子穿妥后再按图4进行胀接;管子与管板胀接时,为防止油污流进胀接面间,亦可采用错列式胀接顺序,见图5;
不足2个时,允许超胀2个;
8.3 胀管率的间接控制方法
8.3.1 采用液压柔性胀接时控制胀接压力;
8.3.2 采用液压驱动机械胀管或微机控制机械胀管时,控制胀接扭矩;采用普通机械胀管时,使用胀管限位器控制胀杆进入胀口的相对位置;
8.4 胀口质量要求
8.4.1 管端内表面不应有粗糙、剥落、刻痕、裂纹等;
8.4.2 12°~15°扳边后管端不应有裂纹;
8.4.3 90°扳边后边缘不应有超过2mm长的细小裂纹;
8.4.4 胀口处应无偏挤(单边);
8.4.5 胀口的内径圆度公差大于0.15mm时,其超差数量在同一胀接面处不得超过胀接总数的10%;
9.水压试验、补胀和换管技术要求
9.1 胀接管子全部胀妥后,进行胀口及管板的内部清理,并检查管子有无堵塞;
9.2 水压试验前应拆除本体组装设施或临时支架;
9.3 水压试验按图纸、工艺及《固定式容规》进行;
9.4 水压试验检查应在试验压力降至工作压力时进行,检查胀口有无漏水(漏水是指水珠向下流)、水印(指仅有水迹)和泪水(指水压试验期间不向下流的水珠);如发现上述缺陷,应在相应管端处分别作出标记;
9.5 对水压试验漏水的胀口或超过允许数量的泪水、水印的胀口应在卸压放水后随即进行补胀,同时还应对其邻近的一些胀口稍加补胀以免受到影响而松弛;补胀前应测量胀口内径;确定合适的补胀量,以免超胀;
9.6 同一漏水胀口,补胀次数不宜多于2次,补胀后应重新进行水压试验,对补胀后仍有漏水且胀管率已超过2.8%的管子应予换管重胀(在割除不合格的胀接管子时,必须注意不损伤管孔壁);补胀、重胀后的胀管率应符合8.2.9要求;
9.7 应有专人负责记录胀接及水压试验结果(参见附录A表A3),以作为验收依据并备案;
10.贴胀(或称“轻胀”、“预胀”)技术要求
10.1 贴胀宜在需贴胀的管子焊接后进行,也可在焊接前进行;
10.2 当图样要求贴胀或要求用胀接方法消除管子与孔壁间隙时,应采用与前述相同的胀接设备和操作方法,使管子外壁紧贴管孔内壁,并有一定的胀紧力,以消除管子与管孔间的间隙; 10.3 当采用手工贴胀时,应胀至感到扭矩明显增大时止;当采用机械或液压驱动贴胀时,应胀至负载明显时止;
10.4 前部管子贴胀完毕后,应仔细检查外观质量,并应用小手锤轻击接近管孔的管段,监听贴胀质量(贴胀紧密时,其声音沉闷;而未贴紧时,声音较清脆);
注:贴胀的目的仅是为了消除管子与管孔的间隙及降低焊接应力;因此,在执行本守则时,当对管子按规定进行材质、外观质量检验并合格后,对管子和管板的硬度检查、试胀、胀管率、扳边、记录、检查胀接质量的水压试验等要求均可免去;
附录A
胀接用数值记录表
( 参考件)
A1 胀接前各胀接面15%的管子、管孔数值测量记录表,见表A1;
注:1.管板管孔:水平—纵向;垂直—环向;
2.每个胀接面要分别测量、计算算术平均值;
A2 试胀用数值记录表,见表A2
注:Hj—最佳胀管率;
d1j—最佳胀管率时的胀口内径;
A3 胀接后数值记录表,见表A3
注:管板管孔:水平—纵向;垂直,。