射线检测技术
射线检测报告标准及检测方法(一)2024

射线检测报告标准及检测方法(一)引言概述:射线检测是一种常用的无损检测方法,广泛应用于工业生产、科研以及安全领域。
本文旨在介绍射线检测的标准及检测方法,帮助读者了解射线检测的基本原理和操作流程,以及如何遵循标准进行有效的检测。
正文:一、射线检测的基本原理1.1 射线检测的概念和作用1.2 射线检测的原理及分类1.3 射线检测设备的种类和特点1.4 射线检测的适用范围和限制1.5 射线检测的安全预防措施二、射线检测标准的选择与遵循2.1 射线检测的国际标准概述2.2 射线检测的国内标准概述2.3 选择适用的射线检测标准的考虑因素2.4 如何遵循射线检测标准进行检测2.5 检测结果的评定标准和说明三、射线检测的检测方法及操作流程3.1 衰减法检测方法3.2 透射法检测方法3.3 散射法检测方法3.4 在线检测和离线检测的区别与应用3.5 射线检测的实际操作流程简介四、射线检测设备的维护和保养4.1 射线检测设备的日常维护4.2 射线检测设备的定期保养4.3 射线检测设备的故障排除和维修4.4 安全问题的处理及应急情况的应对4.5 射线检测设备的更新与升级技术五、射线检测的未来发展趋势和挑战5.1 射线检测技术的发展趋势5.2 射线检测在新兴领域的应用前景5.3 射线检测面临的技术挑战和风险5.4 射线检测行业的规范发展和监管建议5.5 对射线检测技术发展的展望和总结总结:本文对射线检测的标准及检测方法进行了详细介绍。
通过了解射线检测的基本原理、选择适用的标准、掌握各类检测方法和设备的维护保养技巧,读者可以更好地应用射线检测技术,并对其未来发展趋势有所了解。
射线检测在工业领域有着广泛应用的前景,同时也需要关注适用标准的遵循,保证检测的准确性和安全性。
随着技术的发展和需求的变化,射线检测行业将不断迎接新的挑战,并在规范发展和监管建议的引导下取得更好的发展。
射线检测标准及工艺技术要求及说明

射线检测标准及工艺技术要求及说明一、射线检测标准射线检测的标准是确保检测结果准确性和可靠性的重要依据。
常见的射线检测标准包括国际标准(如 ISO 标准)、国家标准(如 GB 标准)以及行业标准。
这些标准通常涵盖了以下方面:1、检测设备的性能要求:包括射线源的能量、焦点尺寸、辐射剂量等参数的规定,以保证检测设备能够提供足够的穿透能力和清晰度。
2、检测技术的分类和适用范围:例如,根据被检测物体的材质、厚度、形状等因素,确定适合的射线检测技术,如 X 射线检测、γ射线检测等。
3、图像质量要求:规定了检测图像的对比度、清晰度、不清晰度等指标,以确保能够清晰地显示缺陷。
4、缺陷评定标准:明确了不同类型和尺寸的缺陷的评定方法和验收标准,以便对检测结果进行准确判断。
二、射线检测工艺技术要求(一)射线源的选择射线源的选择取决于被检测物体的材质、厚度和检测要求。
一般来说,X 射线适用于较薄的物体和对图像质量要求较高的检测,而γ射线则适用于较厚的物体和野外检测等场合。
(二)胶片的选择胶片的性能对检测结果的质量有重要影响。
应根据射线源的能量、被检测物体的材质和厚度等因素选择合适类型和感光度的胶片。
(三)曝光参数的确定曝光参数包括管电压、管电流、曝光时间等。
这些参数的选择需要综合考虑被检测物体的厚度、材质、射线源的强度以及胶片的特性,以获得最佳的检测图像。
(四)散射线的控制散射线会降低检测图像的质量,因此需要采取有效的措施进行控制。
常见的方法包括使用铅屏、滤波板、背散射防护等。
(五)像质计的使用像质计用于评估检测图像的质量和灵敏度。
应根据标准要求选择合适类型和规格的像质计,并正确放置在被检测物体上。
(六)标记与标识在检测过程中,需要对被检测物体进行清晰的标记和标识,包括工件编号、检测部位、透照方向等信息,以便于对检测结果进行追溯和分析。
三、射线检测工艺技术说明(一)检测前的准备工作在进行射线检测之前,需要对被检测物体进行表面处理,去除污垢、氧化皮、油漆等可能影响检测结果的物质。
射线检测的方法

射线检测的方法
射线检测是一种无损检测方法,常用于检测材料或结构内部的缺陷、不连续性或异常情况。
以下是一些常见的射线检测方法:
1. X 射线检测:X 射线检测是一种常用的射线检测方法。
它利用 X 射线的穿透能力,通过将 X 射线照射到被检测物体上,并观察透过物体的 X 射线强度变化,来检测物体内部的缺陷或不连续性。
2. γ 射线检测:γ 射线检测使用放射性同位素(如钴-60)产生的γ 射线进行检测。
与 X 射线检测类似,γ 射线检测通过观察透过物体的γ 射线强度变化来检测缺陷。
3. 中子射线检测:中子射线检测利用中子束的穿透能力来检测物体内部的缺陷。
中子束与物质相互作用时会发生散射和吸收,通过检测中子束的散射和吸收情况,可以判断物体内部是否存在缺陷。
4. 工业 CT 检测:工业 CT(Computed Tomography)检测是一种结合了射线检测和计算机断层扫描技术的方法。
它通过对物体进行多角度的 X 射线或γ 射线投影,并利用计算机重建出物体内部的三维图像,从而实现对缺陷的检测和分析。
5. 射线照相检测:射线照相检测是一种传统的射线检测方法,它通过将 X 射线或γ 射线照射到被检测物体上,然后在胶片上记录下透过物体的射线强度分布,最后通过观察胶片上的影像来检测缺陷。
这些射线检测方法在不同的应用领域中都有广泛的应用,例如航空航天、汽车制造、石油化工、电力等行业。
选择合适的射线检测方法需要考虑被检测物体的材质、尺寸、形状、检测要求等因素。
射线检测原理及发展前景

射线检测原理及发展前景射线检测是利用高能射线对物体进行无损检测的一种方法。
射线可以穿透物体,根据射线被物体吸收的程度来分析物体内部的结构和组成。
常见的射线检测方法包括X射线、γ射线和中子射线检测。
X射线检测是利用X射线穿透物体的特性,通过检测射线通过物体的情况来获取物体内部结构的信息。
X射线具有能量高、穿透力强、辨识度高等优点。
它被广泛应用于医学影像学、工业无损检测、安全检查等领域。
在医学影像学中,X射线可以用于检测骨骼和软组织疾病,如骨折、肿瘤等。
在工业无损检测中,X射线可以用于检测金属构件的缺陷、焊接质量等。
随着技术的不断发展,X射线检测的精度和分辨率也在不断提高,应用范围也日益扩大。
γ射线检测是利用放射性同位素放出的γ射线进行检测。
γ射线具有能量高、穿透力强、易获得等特点。
γ射线检测在工业领域有广泛应用,特别在石油、天然气、化工等行业中,可以用于检测管道的腐蚀、堵塞情况,以及容器内部的结构和组成。
中子射线检测是利用中子射线穿透物体的能力进行检测。
中子射线具有较强的穿透力,对于各种材料都具有适应性强的特点。
中子射线检测在核工业、航空航天、石油化工等领域有广泛应用。
它可以用于检测核燃料棒的损坏情况,航空航天中可以用于检测航天器的结构、连接部件等。
射线检测技术在近几十年来得到了快速发展,尤其是随着图像处理技术、计算机技术的发展,射线检测的精度和效率得到了极大提高。
随着工业领域对质量要求的提高,射线检测在工业无损检测中的应用前景非常广阔。
射线检测技术的不断创新和发展,可以提高产品质量,避免安全事故和环境污染,保障生产过程的安全和正常进行。
同时,射线检测还可以节约人力和物力,并且能够减少对环境的污染。
尽管射线检测技术有许多优点,但也存在一些挑战和问题。
首先,射线检测对设备要求非常高,成本较高。
其次,射线检测涉及到辐射安全问题,需要严格控制辐射剂量。
此外,射线检测在对不同材料的检测上存在一定的限制性。
射线检测的原理
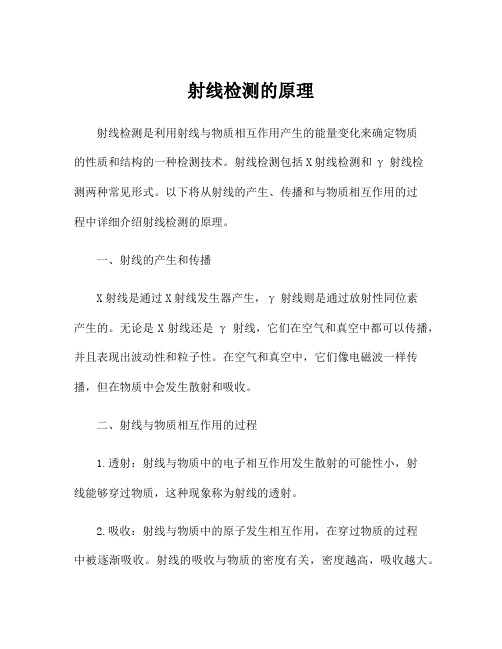
射线检测的原理射线检测是利用射线与物质相互作用产生的能量变化来确定物质的性质和结构的一种检测技术。
射线检测包括X射线检测和γ射线检测两种常见形式。
以下将从射线的产生、传播和与物质相互作用的过程中详细介绍射线检测的原理。
一、射线的产生和传播X射线是通过X射线发生器产生,γ射线则是通过放射性同位素产生的。
无论是X射线还是γ射线,它们在空气和真空中都可以传播,并且表现出波动性和粒子性。
在空气和真空中,它们像电磁波一样传播,但在物质中会发生散射和吸收。
二、射线与物质相互作用的过程1.透射:射线与物质中的电子相互作用发生散射的可能性小,射线能够穿过物质,这种现象称为射线的透射。
2.吸收:射线与物质中的原子发生相互作用,在穿过物质的过程中被逐渐吸收。
射线的吸收与物质的密度有关,密度越高,吸收越大。
3.散射:射线与物质中的原子发生碰撞后改变方向,这种现象称为散射。
散射可分为弹性散射和非弹性散射。
弹性散射是射线碰撞后方向发生改变,但能量不发生改变;非弹性散射是射线碰撞后不仅方向改变,还失去或获得能量。
4.荧光:当射线与物质相互作用后产生能量变化时,物质会发出辐射,这种辐射称为荧光辐射。
荧光辐射在物质中的原子的能级间跃迁过程中发生。
不同的物质有不同的荧光辐射特征,因此可通过荧光辐射分析物质的成分和结构。
5.效应:射线与物质相互作用可产生多种效应,如光电效应、康普顿散射和正负电子对产生等。
这些效应也可以用于分析物质的成分和性质。
三、射线检测的应用1.医学影像学:X射线和γ射线在医学影像学中广泛应用。
通过X射线片或CT扫描可以观察内脏器官的形态和内部细节,用于诊断疾病。
核医学利用放射性同位素发射的γ射线来研究人体的生理功能状态。
2.工业无损检测:射线检测可以用于工业中的无损检测,例如检查金属部件中的缺陷、测量材料的厚度和密度、检测焊接接头质量等。
射线穿透能力较强,可以便利地检测物体的内部结构和材质的均匀性。
3.考古学和文物保护:射线检测可以帮助考古学家探测古墓、古代建筑以及文物中的有用信息,以便更好地理解历史和文化。
射线检测技术说明
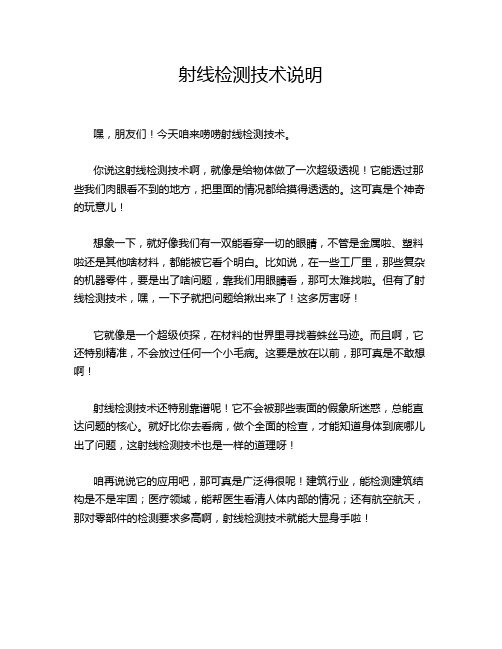
射线检测技术说明
嘿,朋友们!今天咱来唠唠射线检测技术。
你说这射线检测技术啊,就像是给物体做了一次超级透视!它能透过那些我们肉眼看不到的地方,把里面的情况都给摸得透透的。
这可真是个神奇的玩意儿!
想象一下,就好像我们有一双能看穿一切的眼睛,不管是金属啦、塑料啦还是其他啥材料,都能被它看个明白。
比如说,在一些工厂里,那些复杂的机器零件,要是出了啥问题,靠我们用眼睛看,那可太难找啦。
但有了射线检测技术,嘿,一下子就把问题给揪出来了!这多厉害呀!
它就像是一个超级侦探,在材料的世界里寻找着蛛丝马迹。
而且啊,它还特别精准,不会放过任何一个小毛病。
这要是放在以前,那可真是不敢想啊!
射线检测技术还特别靠谱呢!它不会被那些表面的假象所迷惑,总能直达问题的核心。
就好比你去看病,做个全面的检查,才能知道身体到底哪儿出了问题,这射线检测技术也是一样的道理呀!
咱再说说它的应用吧,那可真是广泛得很呢!建筑行业,能检测建筑结构是不是牢固;医疗领域,能帮医生看清人体内部的情况;还有航空航天,那对零部件的检测要求多高啊,射线检测技术就能大显身手啦!
你看,这射线检测技术是不是超级棒?它给我们的生活和工作带来了多大的便利呀!它让那些隐藏的问题无处遁形,让我们能更好地保证产品的质量和安全。
这可真是个了不起的技术呀,咱可得好好珍惜和利用它!
总之,射线检测技术就像是我们的秘密武器,帮助我们在各种领域中披荆斩棘,解决一个又一个难题。
它让我们对这个世界有了更深入的了解,也让我们的生活变得更加美好。
所以啊,大家可别小瞧了它哟!。
射线检测专业知识点

射线检测专业知识点射线检测(Radiographic Testing,RT)是一种常用的无损检测方法,广泛应用于工业领域,用于检测材料内部的缺陷和异物。
射线检测的原理是利用X射线或γ射线穿透被测物体,并通过感光材料记录通过的射线强度变化,从而得到被测物体的内部结构信息。
下面将介绍射线检测的一些专业知识点。
1.射线生成与辐射法则射线检测主要使用X射线和γ射线。
X射线是由高能电子与物质相互作用而产生的,而γ射线则是由放射性核素的放射性衰变产生的。
辐射法则是通过电荷加速或放射性核素衰变来产生射线的方法,其能量与频率之间存在着特定关系。
2.射线源选择与放射性安全在进行射线检测时,需要选择适当的射线源。
X射线源通常是射线管,而γ射线源则是含有放射性核素的封装物。
在选择与使用射线源时,要遵守放射性安全原则,包括选择合适的辐射源、合理设置辐射源与被检测物体的距离、对辐射源进行合理的控制与管理,以确保操作安全。
3.射线几何与成像方法射线检测需要掌握一定的几何知识和成像原理。
射线以一定的角度入射被检测物体,形成射线照片,用以观察物体内部的缺陷和异物。
射线几何知识包括射线入射角度、相对敏感度、扩束、发散角等,而成像方法则包括常见的胶片成像和数码成像。
4.缺陷与判定标准射线检测的目的是通过观察射线照片来确定被检测物体内部的缺陷和异物。
在进行判定时,需要根据不同的材料和不同的使用要求,参考相应的标准和规范,比如ASME标准、ISO标准等。
缺陷的形态、大小、位置以及对材料性能的影响都需要进行评估和判定。
5.仪器与设备射线检测需要使用一些特定的仪器和设备,包括射线发生器(射线管或放射性核素)、影像系统(胶片或数码系统)、探测器(感光材料或数码探测器)等。
这些仪器设备的选择和使用都需要具备一定的专业知识和技能。
6.安全防护与辐射防护射线检测过程中涉及到辐射,必须严格遵守相关的辐射防护规定,确保操作人员和周围环境的安全。
这包括了个人防护设备的选择和使用、辐射区域的合理划定、辐射剂量监测和辐射源的管理等。
射线检测分类

射线检测分类
射线检测分类
射线检测是一种非破坏性检测技术,主要用于检测材料内部的缺陷。
在射线检测中,射线穿过被检材料,然后被探测器接收,根据信号的差异判断材料中是否存在缺陷。
射线检测可以分为以下几类:
1. X射线检测:X射线是一种高能电磁波,具有很强的穿透能力,可以穿过大部分金属和非金属材料。
X射线检测常用于检测铸造件、焊接件、航空航天部件、汽车零部件等材料。
此类检测需要专业的设备和操作技能。
X射线检测具有高灵敏度和可靠性,可以检测到微小的缺陷。
2. γ射线检测:γ射线也是一种高能电磁波,和X射线一样具有很强的穿透力,但γ射线的波长比X射线更短,能量更高。
γ射线检测常用于检测较厚的工件,例如锅炉、反应堆、管道等。
在进行γ射线检测时,需要在被检测物品周围进行防护,以防止辐射危害。
3. β射线检测:β射线是一种带电粒子,比γ射线和X射线穿透力更弱。
β射线检测通常用于表面层薄的材料检测,例如涂层、钢板、底盘等。
4. 中子射线检测:中子射线穿透性比较弱,但是中子射线能够和原子核相互作用,因此具有独特的检测能力。
中子射线检测主要用于检测含水材料、塑料、橡胶等材料。
以上是射线检测的四种常见分类,每种分类都有适用的领域和检测方法。
随着技术的不断发展,射线检测技术将在更多领域得到应用,为安全生产和产品质量保障提供更好的服务。
- 1、下载文档前请自行甄别文档内容的完整性,平台不提供额外的编辑、内容补充、找答案等附加服务。
- 2、"仅部分预览"的文档,不可在线预览部分如存在完整性等问题,可反馈申请退款(可完整预览的文档不适用该条件!)。
- 3、如文档侵犯您的权益,请联系客服反馈,我们会尽快为您处理(人工客服工作时间:9:00-18:30)。
透照厚度是指透照时射线穿过工件的路径长度。显然 ,在透照区内不同的位置其透照厚度是不同的。在一次透 照范围内,如果不同点的透照厚度相差过大,将造成射线 照片上不同点的黑度相差过大, 这必然导致不同点影像 质量明显不同,使得底片的质量难以控制。因此必须控制 一次透照范围,也就是控制透照厚度比K值。JB47302005标准对K值作了以下规定(包括平板对接焊缝和环向 对接焊缝),见书P68 ⑷ θ- 这是射线束最外沿的入射方向与垂直入射方向之 间的夹角,它影响横向裂纹的检出,称为横向裂纹检出角 。θ愈大检出横向裂纹的可能性愈小,标准对其作了明确 的规定。
射线源应垂直入射到焊缝:焊缝的面状缺陷多数与工件 的上下表面垂直或接近垂直,射线源垂直入射可以使射 线入射方向与面状缺陷走向平行最有利于缺陷检出; 正确选择一次透照长度: • 射线源发出的射线束是一个锥体,在平面中是一个等腰 三角形。在图中有七个重要参数,它们是: ⑴ T – 工件厚度 ⑵ T ' – 这是射线束最外沿的入射线在工件内的长度 ⑶ K – 透照厚度比 K = T'/T
⑸ L – 这是等腰三角形与工件上表面的交接线,是射线束 的入射长度(或入射面的直径), 称为一次透照长度 ,它是确定透照次数和透照划线的依据。一次透照长度 内底片上黑度和灵敏度必须满足标准规定。 ⑹ Leff – 这是等腰三角形与工件下表面的交接线,是射 线束的出射长度(或出射面的直径),因为从这里开始 射线离开工件进入到胶片使胶片成像,成像区也是评定 区所以称为有效评定长度。显然 L>Leff。有效评定长 度可以计算,但是由于b值常是不确定因素(受工件下 表面与胶片之间距离的影响),所以计算Leff值有较大 的误差。该值通常由放于一次透照长度两端的搭接标记 (↑)在底片上的投影距离来表示
4、暗室处理:对已曝光的胶片在暗室进行显影、停影、 定影、水洗和干燥等处理,得到射线底片显示被透照物 体的射线照相影像; 5、评片:在观片灯上观察射线底片,按照标准对被检验 的工件的质量进行评定和定级; 6、签发检测报告:依据评片结果签发检测结论报告,签 发人员必须具有2、3级资格证书; 7、整理文件、报告和底片归档。 二、透照方式 1、选择透照方式的原则 1)根据检测对象选择透照方式:如大型容器采用源在内 一次周向曝光;小口径管子采用双璧单影或双璧双影法 ;
2)根据环境条件选择透照方式:如在用设备检测环境条 件恶劣,多数情况只能采用双璧透照法,甚至采用上下 焊缝垂直透照法; 3)根据质量要求选择透照方式:如对质量要求高的工件 采用单璧透照以取得较好的清晰度和灵敏度; 4)根据设备条件选择透照方式:如只有低能射线机的情 况下必须采用单璧透照; 5)根据可能产生的缺陷形状和方向选择透照方式:如容 器根部未焊透、内壁表面裂纹用外透法比用内透法更容 易检出。 2、常用透照方法有:
⑺△L – 由图可知,这是底片上二次透照的重叠部分,称 为搭接长度,△L=Leff-L
T' K T
-1
T cosθ T'
T -1 1 θ cos( ) cos ( ) T' K
L/2 又 tgθ f
L ftgθ 2
L 2 ftgθ
S n L
• 选择合理的透照次数:
1)平板对接焊缝和环形工件的纵缝单壁单影透照法
• 平板对接焊缝和环形 工件的纵缝呈直线状, 是制造工程中应用最为 广泛的一种连接形式, 焊工考试的试板通常都 是平板对接焊缝。射线 只穿过一个壁厚在胶片 上成像,这种透照方法 即称为单壁单影透照。平板对接焊缝和环形工件的单壁单 影透照是最基本的透照方式,具有较高的清晰度和灵敏度 ,操作时应注意:
T
Leff
环缝源在外单壁透照法
• 根据透照级别确定K值(表7-3); • 根据K值选用图解确定最少透照次数(见图7-19); • 根据透照次数计算L值: S
L n
式中: n – 环形焊缝透照次数 S – 焊缝长度(环形工件的周长) L – 一次透照长度 图7-19是JB4730-2005标准的“源在外单壁透 照环向对接焊缝,透照厚度比K=1.1时的透照次数图”。 图中De是工件的外径、f是射线源到工件上表面的距离、 T是工件的母材厚度。 图中横坐标表示T/De、纵坐标表示 De/f,对某一工件而言算出T/De和De/f值,在图中便可确 定最少透照次数。
式中: n – 平板焊缝透照次数
S – 焊缝长度 L – 一次透照长度 例: 射线源尺寸为2mm,工件表面到胶片距离为30mm ,焊缝总长2000mm,焦距为600mm,作A级、AB级和 B级检测该焊缝须透照多少次? 解:根据表7-3,A级、AB级检测K=1.03
A、AB级: θ cos -1 ( 1 1 ) cos -1 ( ) 13.8 K 1.03
n
S 2000 11.7 L 170
答:B级透照需拍12次。
2)环缝源在外单壁单影透照法(下图) 环形工件的环缝透照如果 可以在内壁贴片,应采用 源在外单壁单影透照方法, 源在外易于操作。环形焊 缝由于焊缝呈弧形,所以 几何关系比较复杂。在工 程应用中,常采用以下步 骤:
d
f
θ T’ L
L 2 ftgθ 2 600 tg13.8 294(mm)
n S 2000 6.8 L 294
答:A、AB级透照需拍7次。
B级:
1 1 -1 θ cos ( ) cos ( ) 8.1 K 1.01
-1
L 2 ftgθ 2 600 tg8.1 170(mm)
第八专题
焊缝射线照相法
一 、焊缝射线照相的基本程序 1、技术和工艺准备:首先要编制射线照相作业指导书或 工艺卡,确定使用设备后要准备曝光曲线,对射线照相 的具体技术作出规定,操作人员必须理解、读懂作业指 导书或工艺卡; 2、透照前的操作准备:胶片、增感屏、暗盒、透度计和 各种标记铅字的选用和摆放; 3、照相:确定透照部位、一次透照长度L(图7-3)、透 照次数、工件上定位划线、射线源-工件-胶片摆放、环 境安全警戒,按照作业指导书或工艺卡的规定完成射线 照相;