铸造工艺及工装设计
铸铁平板(铸铁平板)铸造工艺及工装设计的一般步骤
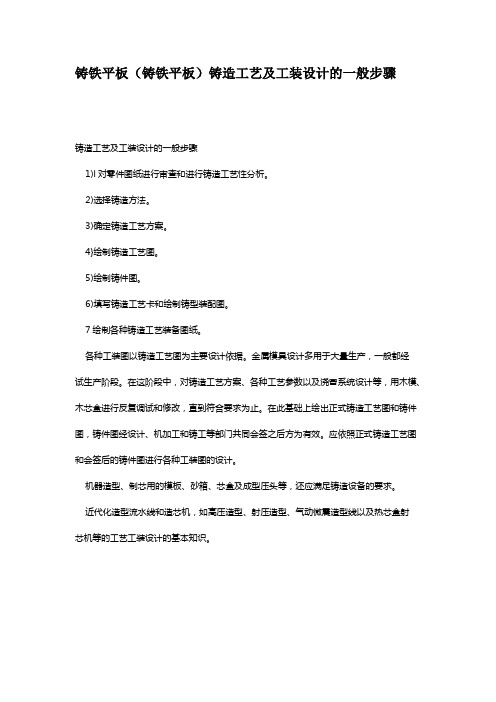
铸铁平板(铸铁平板)铸造工艺及工装设计的一般步骤
铸造工艺及工装设计的一般步骤
1)l对零件图纸进行审查和进行铸造工艺性分析。
2)选择铸造方法。
3)确定铸造工艺方案。
4}绘制铸造工艺图。
5)绘制铸件图。
6)填写铸造工艺卡和绘制铸型装配图。
7绘制各种铸造工艺装备图纸。
各种工装图以铸造工艺图为主要设计依据。
金属模具设计多用于大量生产,一般都经
试生产阶段。
在这阶段中,对铸造工艺方案、各种工艺参数以及浇冒系统设计等,用木模、木芯盒进行反复调试和修改,直到符合要求为止。
在此基础上绘出正式铸造工艺图和铸件图,铸件图经设计、机加工和铸工等部门共同会签之后方为有效。
应依照正式铸造工艺图和会签后的铸件图进行各种工装图的设计。
机器造型、制芯用的模板、砂箱、芯盒及成型压头等,还应满足铸造设备的要求。
近代化造型流水线和造芯机,如高压造型、射压造型、气动微震造型线以及热芯盒射
芯机等的工艺工装设计的基本知识。
第六章铸造工艺装备设计

第六章 铸造工艺装备设计第一节 概 述铸造工艺装备是造型、制芯和合箱过程中所使用的模具和装置的总称,其内容见教材表 61。
第二节 模样设计一、材质的选择1.木模适用于单件、小批量生产的各种铸件。
2.金属模样常用的金属为:适用于大量、成批生产的各种铸件。
3.聚苯乙烯泡沫塑料模(消失模)用于实型造型法、磁丸造型的中、小铸件和单件生产的中、大型铸钢件。
二、金属模样的结构设计1.模样本体结构类型平装式结构简单,容易加工,最常用。
嵌入式在特殊条件下应用,如模样部分表面凹入分型面以 下(图 62a);分型面以上模样过薄,加工、固定困难(图 62b);分型面通过模样圆角(图62c);很 小的模样(图 62d)而方便于加工、定位和固定等。
选定模样结构后,即可依铸造工艺图确定模样的外形。
图 6-2 嵌入式模样1-模样 2-底板2.壁厚及加强筋应尽量减轻模样的质量。
除了薄小模样(小于 50 ㎜×50 ㎜或高度低于 30 ㎜)以外,都应制成空 心结构。
平均轮廓尺寸大于 150 ㎜的模样,内部设加强筋。
3.固定和定位孔模样在模底板上的固定,可用螺钉或螺栓,用定位销定位。
模样上钻通孔,螺钉穿过模样与模底 板固定,称为上固定法,如图 64a 。
优点有:便于选择螺孔位置,钻孔和装配方便;缺点是:破坏模 样的工作表面,紧固后需用塑料或铝等填平模样表面上之螺孔坑。
模底板上钻通孔,模样上攻螺纹孔的 固定方法称下固定法,如图 64b 。
优点是模样工作表面不受损害;缺点是确定螺孔位置要避开模底板 底部之筋条,还要让出扳手空间,安装不甚方便。
下固定法用于模样高大且四周没有低矮的凸边可以利 用的条件下。
定位销孔的位置应选在模样上矮而平的部位,两孔间距尽量远。
每块模样上至少应设 2 个。
图6-4 模样的固定和定位a )上固定法b )下固定法1-模样 2-模底板 3-螺钉 4-定位销4.模样(芯盒)的尺寸标注模样(芯盒)的尺寸有两类:一类是与铸件有关的尺寸;另一类为非关联尺寸,如芯头长度等。
第五 六章 铸造工艺工装设计
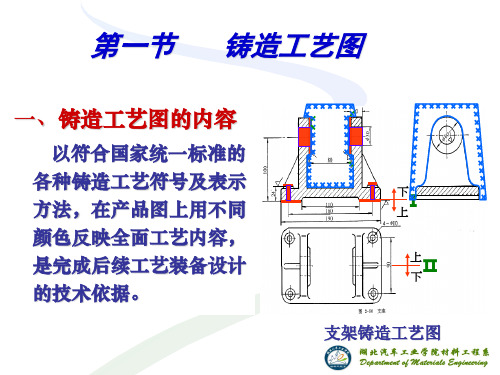
6.工作内腔尺寸
热(壳)芯盒内腔尺寸只考虑铸造收缩率。
7.芯盒的定位与夹紧
多用定位销定位。静芯盒上 装销,动芯盒上装套。销直径 为φ15㎜、φ20㎜。 采用可靠的夹紧操作手柄。
8.排气
分盒面上开排气槽,死角处 钻孔,装排气塞。 可利用镶块、顶芯杆的间隙 排气。 总排气道面积应为射口面积 的0.1~0.2倍。
二、铸造工艺符号、表示方法和注意事项
铸造工艺符号及表示 方法是由原国家机械工 业部统一规定的,详见 教材 P148~158。 绘制铸造工艺图的注 意事项将在下一节结合 典型铸件铸造工艺图的 介绍中给予提示。
第二节
车轮轮毂
典型铸件铸造工艺图
Hale Waihona Puke 铸件重13.6 ㎏ ;HT200;主要壁厚为15mm;法兰盘 厚19mm;重要加工表面φ90和φ92 (内装轴承外圈)。
Lm ( L j Ly )(1 K )
式中
Lm —模样尺寸; Lj —零件尺寸; Ly —工艺尺寸,如机械加工余量、
起模斜度等。 K—铸造合金的线收缩率 铸件相关尺寸,可准确到0.1 ㎜ 。
模样标注实例
3)模样(芯盒)的壁厚及加强肋
为减轻质量,模 样(芯盒)都应制成 空心结构。 平均轮廓尺寸大于 150 mm的模样,内部 设加强肋。 金属模(芯盒)的 壁厚及加强肋见右图。
第一节
铸造工艺图
一、铸造工艺图的内容
以符合国家统一标准的 各种铸造工艺符号及表示 方法,在产品图上用不同 颜色反映全面工艺内容, 是完成后续工艺装备设计 的技术依据。
下 上
Ⅰ
上
下
Ⅱ
支架铸造工艺图
图中标出浇注 位置、分型面、加 工余量、不铸孔和 砂芯形状。浇注系 统、冒口、芯座及 芯头间隙等必要内 容。
铸造工艺及工装的设计共52页文档
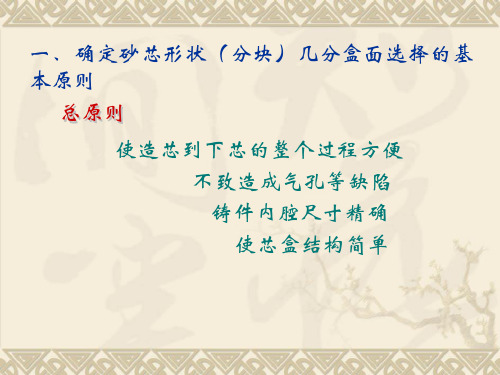
为操作方便将砂芯分块的实例
(三)保证铸件壁厚均匀
使砂芯的起模斜度和模样的起模斜度 大小、方向一致,保证铸件壁厚均匀
保证铸件壁厚均匀
a) 不合理
b) 合理
(四)应尽量减少砂芯数目
用砂胎(自带砂 芯)或吊砂可减少砂 芯 , 右 图 为 12VB 柴 油机曲轴定位套的机 器造型方案。
砂胎
在手工造型时,遇到难
铸造工艺设计参数主要有:
铸件尺寸公差
铸件重量公差
机械加工余量
铸造收缩率 起模斜度 最小铸出孔及槽 工艺补正量 分型负数 反变形量 砂芯负数
非加工壁厚的负余量
分芯负数
一、铸件的尺寸公差 指铸件各部分尺寸允许的极限偏差
我国的铸件尺寸公差标准GB6414-86
ISO8062-1984《铸件尺寸公差制》
3
2
2
1
2
345
6
78
9 10 11 12 13 14 15 16
CT1
精度
CT16
铸件尺寸公差数值 (mm)
铸件基本尺寸
公差等级CT
大于 至 1 2 3 4 5 6 7 8 9 10 11 12 13 14 15 16
-
10
- - 0.18 0.26 0.36 0.52 0.74 1.0 1.5 2.0 2.8 4.2 - - - -
除上述的原则外,还应使没块砂芯有足够的断面, 保证有一定的强度和刚度,并能顺利排出砂芯中的气 体;使芯盒结构简单,便于制造和使用等。
二、芯头设计
芯头伸出铸件以外不与金属接触的砂芯部分。 ➢ 对芯头的要求
✓ 定位和固定砂芯,使砂芯在铸造中有准确 的位 置,并能承受砂芯重力及浇注时液体 金属对砂芯的浮力,使之不破坏
轴承座铸造工艺及工装设计 说明书

毕业设计论文设计(论文)题目:轴承座铸造工艺及工装设计下达日期: 2007 年 4 月 28 日开始日期: 2007 年 4 月 28 日完成日期: 2007 年 6 月 8 日指导教师:韩小峰学生专业: 材料成型与控制技术班级:材料0401学生姓名:李春晖教研室主任:材料工程系摘要铸造是一种将金属熔炼成流动的液态合金,然后浇入一定的几何形状、尺寸大小的型腔之中,凝固冷却后成为成为所需要的零件毛坯的一种制作方法。
本文通过对铸造这一特殊工种的诠释和此铸件的特点相结合给予了比较合理的方法.从铸造工艺的设计到整个铸造工艺的设计我们对此都作了比较详细的论证、对比、数据和计算,并且从中选择较优的方法和方案给以了较合理的应用和实施。
首先我们对所设计的的铸件进行了认真的分析,读懂零件图的几何形状、主要结构和特殊部位以及铸件的工艺要求、工装要求等给以较合理的思考。
其次设计此铸件的整个工艺过程:其中包括铸造方法的选择、分型面的选择及确定、浇注系统的选择及计算设计、铁液的凝固、以及对所要产生缺陷的防止方法和补缩等问题上午考虑设计。
然后对所设计的工艺过程进行工装设计:其中包括模样的设计、模底板的设计、芯盒的设计、砂箱的设计等,而且对这些工装的定位及夹紧等问题进行解决。
最后对所设计的整个过程给以检验、总结。
进一步对此设计的成功率给以进一步的保障。
关键词:铸造,工艺,工装,缺陷BEARINGSEAT TECHNRQUE FROCK DEVISEABSTRACTMaking the smelt metal become the mobile liquid state alloy,pouring—in solidifies in the type cavity having the certain geometry form and dimension,becoming something be needed part blank after cooling down。
7.3铸造工艺设计解析
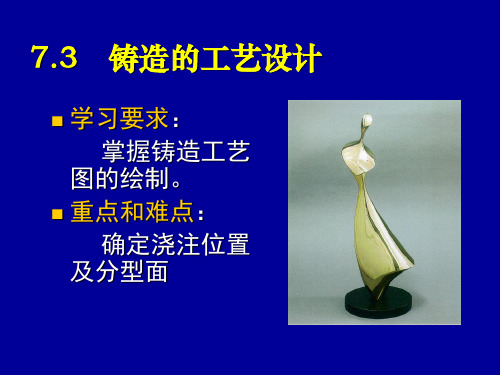
冒口
上
上
中
下
单件小批
中 下
放收缩率1% 余量:上面>侧面>下面
手工三箱造型 大批量
外 型 芯 块
两箱机器造型
7.3.5铸造工艺设计示例
例:支架零件如下图所示,材料为HT200, 单件、小批量生产工作时承受中等静载荷, 试进行铸造工艺设计。 1.零件结构分析:筒壁过厚,转角处未采用 圆角。修改后的结构如图b)所示。 2.选择铸造方法及造型方法 采用砂型铸造 (手工造型)中的两箱造型。 3.选择浇注位置和分型面
1.铸造工艺图: 利用各种的工艺符号,把制造模型和
铸型所需的资料直接绘在零件图上所得到 的图样。
即表示铸型浇注位置、分型面、浇冒口 系统、工艺参数、型芯结构尺寸、控制凝 固措施等的图样。
2. 铸件图:又称毛坯图,是反映铸件实际形 状、尺寸和技术要求的图样,也是铸造生产、 铸件检验与验收的主要依据。
(1)定义: 指铸件从线收缩开始温度冷却至室温时,
线尺寸的相对收缩量。 (2)选取: 大件、重要件不同部位可选取不同的收缩率; 一般件可选取同一收缩率。
4. 起模斜度
(1)定义:为了起模方便,在平行于起模方向的侧壁 加放的一定斜度。
(2)选取:对同一件,尽可能选用同一起模斜度; 立壁愈高,斜度应越小; 内壁的斜度值应大于外壁; 机器造型比手工造型斜度小; 金属模比木模斜度小。
3.铸型装配图:表示合型后铸型各组元之间
装配关系的工艺图。包括:浇注位置、型芯、 浇冒口系统和冷铁布置及砂箱结构和尺寸等。
7.3.2 铸造方法和造型方法选择
1.选择依据: 1)零件结构特点;2)合金种类; 3)生产批量等
2.选择原则: 单件、小批生产时一般采用砂型铸造
铸造工艺及工装设计

第二节 造型、造芯方法的选择
三、造型方法应适合工厂条件 每个铸工车间只有很少的几种造型、造芯方法,所以选择的 方法应切合现场实际条件。
四、要兼顾铸件的精度要求和成本 各种造型、造芯方法所获得的铸件精度不同,初投资和生产
率也不一致,最终的经济效益也有差异。
第三节 浇注位置的选择
浇注位置的选择
浇注位置:金属浇注时铸件所处的空间位置。同一个铸件, 可以有多种浇注位置。
交错接头适用于中小型铸件; 环形接头适用于大型铸件;
一、从避免缺陷方面审查铸件结构
(六)铸件内壁应壁均衡散热。
阀体的结构改进
一、从避免缺陷方面审查铸件结构
(七)壁厚力求均匀,减少肥厚部分,防止形成热节 热结处易造成缩孔、缩松和 热裂纹。
一、从避免缺陷方面审查铸件结构
零件结构的铸造工艺性分析 浇注位置 分型面的选择
1、机械加工余 量和最小铸出孔 2、拔模斜度 3、收缩率 4、铸造圆角 5、型芯头
铸造工艺参数
型芯的数量及其设计
浇注系统设计
冒口、冷铁、铸筋设计
模型图 合箱图 绘制铸造工艺图
第二章 铸造工艺方案
第一节 零件结构的铸造工艺性
零件的铸造工艺性指的是零件的结构应符合铸造生产 的要求,易于保证铸件品质,简化铸造工艺过程和降低 成本。 对产品零件图进行审查、分析作用: (1)审查零件结构是否符合铸造工艺的要求。 (2)在既定的零件结构条件下,考虑铸造过程中可能 出现的主要缺陷,在工艺设计中采取措施予以防止。
一、从避免缺陷方面审查铸件结构
(一)铸件应有合适的壁厚 最小壁厚:在各种工艺条下,铸造合金能充满型腔的最小 厚度。主要取决于合金的种类、铸件的大小及形状等因素。 临界壁厚:各种铸造合金都存在一个临界壁厚,砂型铸造, 临界壁厚约=3x最小壁厚。 缺陷分析: 铸件壁厚小于 “最小壁厚”。浇不足、冷隔。 铸件壁厚大于 “临界壁厚”。缩孔、 缩松、结晶组织粗 大。
铸造工艺及工装设计任务书

铸造工艺及工装设计课程设计任务书
1,用CAD绘制符合国家制图标准的铸件零件二维三视图(零件图就是第4次作业绘制的铸件图),经过指导老师检查合格打印出图,图纸采用A0图幅;(12月16日至17日,2天);
2、在A0铸件图样上用红蓝铅笔做铸造工艺设计,包括分型面、加工余量、分型(芯)负数、拔模斜度、铸造体(线)收缩率、补正量、冷铁,浇注系统设计、冒口设计、砂芯设计、工艺说明等;必须设计3种分型方案,从中选取一种合适的方案做铸造工艺设计,设计中冒口及浇注系统等设计须有详细的计算过程和计算依据;(12月18日至23日,6天)
3、铸造工艺图设计完成后,根据铸造工艺图设计金属模板装配图、金属芯盒装配图(中等难度砂芯),用A2图幅打印出图;(12月24日至29日,6天)
4、撰写铸造工艺及工装设计说明书,说明书必须是打印文件;(12月30日至元月3日,5天)
5、答辩。
(元月4日至元月5日,2天)
注:1)做课程设计时间包括星期六和星期天。
2)提前完成的同学经指导老师检查认可后,可以申请提前答辩,
提前答辩时间安排在12月29日至31日其中的一天。
3)本次课程设计时间及进程安排不受学校提前放假日期的影响,
完全按学校制定的原教学计划执行。
- 1、下载文档前请自行甄别文档内容的完整性,平台不提供额外的编辑、内容补充、找答案等附加服务。
- 2、"仅部分预览"的文档,不可在线预览部分如存在完整性等问题,可反馈申请退款(可完整预览的文档不适用该条件!)。
- 3、如文档侵犯您的权益,请联系客服反馈,我们会尽快为您处理(人工客服工作时间:9:00-18:30)。
第一节 铸造工艺设计的概念、设计依据、内容 及程序
铸造 工艺 设计
要求根据零件的结构特点,技术要求, 生产批量和生产条件,确定铸造方案 和工艺参数,绘制铸造工艺图,编制 工艺卡等技术文件的过程。
第一节 铸造工艺设计的概念、设计依据、内容及程序
一、铸造生产的特点 1.适应范围广 2.可制造各种合金。如铸铁、铸钢、铸铜等 3. 铸件尺寸精度高 4.成本低
2 重要加工面应朝下或呈直立状态
第三节 浇注位置的确定 3 使铸件的大平面朝下,避免夹砂结疤类缺陷
第一节 零件结构的铸造工艺性 3 改进铸件内腔结构以减少砂芯 4 减少和简化分型面
5 有利于芯子的排气和固定
第一节 零件结构的铸造工艺性
6 减少清理铸件的工作量
7 简化模具的制造
第一节 零件结构的铸造工艺性 8 大型复杂件分体铸造和简单小件联合铸造
第二节 造型、造芯方法的选择
一 造型方 法的选择
第二节 铸造工艺设计经济指标和环境保护 的关系
铸件的工艺出品率=
铸件重量 铸件+浇冒系统
100%
铸件成品率=
铸件重量 投入的金属原料总重
100%
第二章 铸造工艺方案的确定
第一节 零件结构的铸造工艺性
零件结构的 铸造工艺性
零件结构应符合铸造生产的要求,
易于保证铸件品质,简化铸造工 艺过程和降低成本
第三节 浇注位置的确定
二 浇注位置的确定原则
1 铸件的中重要部分应尽量置于下部 2 重要加工面应朝下或呈直立状态 3使铸件的大平面朝下,避免夹砂结疤类缺 陷 4 应保证铸件能充满 5 有利于铸件的补缩 6 要注意保证砂芯在铸型中的稳定,排气顺 畅,下芯检验方便
第三节 浇注位置的确定
1 铸件的中重要部分应尽量置于下部。 下部分在静压力作用下凝固并得到补缩,组织致密
1 优先选用湿型 2 造型及造芯方法的选择应 与实际生产相适应 3 造型方法应适合工艺条件 4 要兼顾成本
第二节 造型、造芯方法的选择
(1)铸件过高,金属静
应 用 湿 型 注
压力超过湿型的抗压强 度时,考虑干型等
(2)铸件上部有较大的 水平壁
(3)造型过程长或需长
1)手工造型,一 般选用普通粘土
2)机器造型,一 般膨润土,造型
3)干、湿铸型的 比较
意
时间等待浇注的砂型
的
(4)型内防止冷铁较多
问
时,应避免使湿型,表
题
干型的烘干深度一般在
15~80mm
第二节 造型、造芯方法的选择
干、 湿铸 型的 比较
A 干铸型比湿铸型强度高 高度较高,轮廓较大的铸型用干型 大平面铸件用干型 B 干比湿抗压能力强 C 干比湿耐高温能力强 D干型内腔空气润湿度高 E 金属凝固时间长用于干型 干型 (表面干型,铸型表面 20~30mm,全干型)
第三节 浇注位置的确定
一、浇注位置 铸件在浇注时在型内所处的位置与状态
1、找出铸 件三大重要 部位
2、考虑如 何避免缺陷
3、控制凝 固
1)重要的机械加工面 2)重要的受力面 3)重要的承压面
1)厚大部分容易出现收缩缺陷 2)薄壁部分易出现浇不足,冷隔, 3)大平面易出现鼠尾夹砂 4)壁厚差距大部分易出现应力集中 ,裂纹
第一节 零件结构的铸造工艺性
1 铸件应有适宜的壁厚
主要原因: 1 )避免冷隔和浇不足 2 )合金成分 3 )浇注温度 4 )铸件尺寸大小 5)铸型本身的冷却能力
第一节 零件结构的铸造工艺性
2 铸件壁的连接应逐渐过渡(避免热节) 两壁成直角连接就形成热节,收缩时一旦受阻, 就易形成裂纹,为此壁与壁之间应以圆角过渡。
6 防止铸件翘曲变形(上表面散热快,上 表面边缘先结壳) 7避免浇注位置上有水平的大平面结构
第一节 零件结构的铸造工艺性
二 从简化铸造工艺改进零件结构
1 改进妨碍起模的凸台,凸缘和肋 板的结构 2取消铸件的外表侧凹 3 改进铸件内腔结构以减少砂芯 4 减少和简化分型面
第一节 零件结构的铸造工艺性 1 改进妨碍起模的凸台,凸缘和肋板的结构 2取消铸件的外表侧凹
零件 设计 步骤
1 功用设计 2 依据铸造经验修改和简化设计 3 熔化设计 4 经济效益
第一节 零件结构的铸造工艺性
审查、分 析零件图 的作用
1 审查零件结构是否符合铸造工艺的 要求
2 分析铸造过程中可能出现的主要缺 陷,在工艺设计中采取措施加以防止
审查 的主 要方 面Fra bibliotek一 从避免缺陷方面审核铸件结构 二 从简化铸造工艺改进零件结构 三 加工基准和某些技术条件的合理 性
1 内容
1)根据零件图绘制铸造工艺图 2)根据工艺图绘制铸件图 3)铸型装配图 4)铸造工艺卡 5)铸件操作工艺规程 6)铸件模具及工装的设计图 7)数值模拟
第一节 铸造工艺设计的概念、设计依据、内容及程序
三 设计内容和程序
2 程序
1)零件的技术条件及结构工艺性分析 2)选择铸造及造型方法 3)确定浇注位置及分型面 4)选择工艺参数 5)设计浇冒系统以及冷铁,铸肋 6)砂芯设计 7)在完成工艺图基础上,绘制铸件图 8)在完成砂箱图基础上 绘制铸型装配图 9)编制工艺卡 10)在工艺图基础上设计模具图与模具装配图
第一节 零件结构的铸造工艺性
从避 免缺 陷方 面审 核铸 件结 构
1 铸件应有适宜的壁厚, 2 铸件壁的连接应逐渐过渡(避免热节) 3 铸件的内壁薄于铸件外壁(内外散热 有别) 4 壁厚力求均匀,减少肥厚部分,防止 出现热节 5 有利于补缩,和实现顺序凝固 6 防止铸件翘曲变形 7避免浇注位置上有水平的大平面结构
第一节 零件结构的铸造工艺性
3 铸件的内壁薄于铸件外壁(内外散热有别) 由于散热条件的差异,避免产生较大的应力。
4 壁厚力求均匀,减少肥厚部分,防止出现热节
第一节 零件结构的铸造工艺性
5 有利于补缩,和实现顺序凝固
凝固——收缩——体积亏损(孔 松) ——补给(重力 压力)——液体在顶 端
第一节 零件结构的铸造工艺性
第一节 铸造工艺设计的概念、设计依据、内容及程序
二 设计依据
1 生产任务 2 生产条件 3 考虑经济性
1)铸件零件图 2)零件的技术要求 3)产品数量级生产期限
1)设备能力 2)车间原料 3) 工人技术水平和生产经验 4)模具及装备的加工能力
第一节 铸造工艺设计的概念、设计依据、内容及程序
三 设计内容和程序