动力电池热管理系统组成及设计流程
动力电池的热管理系统及热管理方法 专利
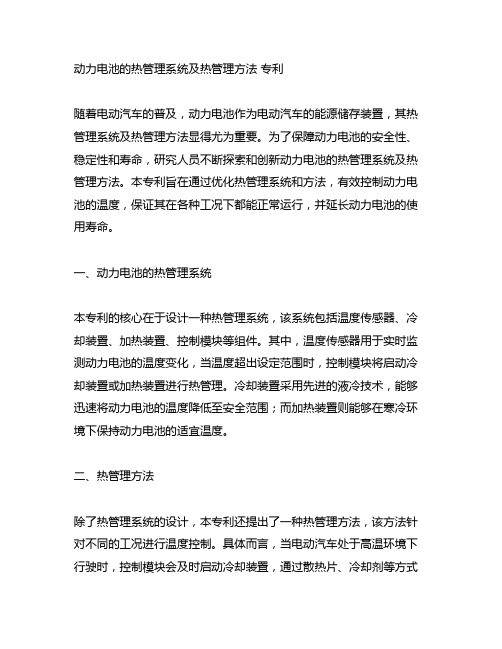
动力电池的热管理系统及热管理方法专利随着电动汽车的普及,动力电池作为电动汽车的能源储存装置,其热管理系统及热管理方法显得尤为重要。
为了保障动力电池的安全性、稳定性和寿命,研究人员不断探索和创新动力电池的热管理系统及热管理方法。
本专利旨在通过优化热管理系统和方法,有效控制动力电池的温度,保证其在各种工况下都能正常运行,并延长动力电池的使用寿命。
一、动力电池的热管理系统本专利的核心在于设计一种热管理系统,该系统包括温度传感器、冷却装置、加热装置、控制模块等组件。
其中,温度传感器用于实时监测动力电池的温度变化,当温度超出设定范围时,控制模块将启动冷却装置或加热装置进行热管理。
冷却装置采用先进的液冷技术,能够迅速将动力电池的温度降低至安全范围;而加热装置则能够在寒冷环境下保持动力电池的适宜温度。
二、热管理方法除了热管理系统的设计,本专利还提出了一种热管理方法,该方法针对不同的工况进行温度控制。
具体而言,当电动汽车处于高温环境下行驶时,控制模块会及时启动冷却装置,通过散热片、冷却剂等方式将动力电池快速降温;而在寒冷环境下行驶时,加热装置则会根据温度传感器的反馈进行自动调节,保持动力电池的适宜温度。
通过这种巧妙的热管理方法,可以有效避免动力电池在特殊环境下受损。
三、本专利的创新之处本专利的热管理系统及热管理方法相较于现有技术具有以下几点创新之处:1. 多元化的热管理方式:本系统结合了冷却装置和加热装置两种方式,能够根据不同的工况灵活调控,并且能够实现快速响应,确保动力电池的安全性。
2. 智能化的控制模块:控制模块采用先进的智能化技术,能够根据温度传感器实时反馈进行智能调节,避免了传统热管理系统操作繁琐、反应迟缓的缺点。
3. 安全性和稳定性:通过本系统和方法的应用,能够有效控制动力电池的温度,避免了因高温或低温而导致的安全隐患,保证了动力电池的稳定运行。
四、结语本专利的热管理系统及热管理方法,为电动汽车行业的发展带来了重大的创新。
动力电池热管理介绍

动力电池热管理介绍动力电池热管理是指针对动力电池在使用过程中产生的热量进行有效管理和控制的技术。
由于动力电池在充放电过程中会产生大量的热能,如果不能有效管理和控制热量,将会对电池的性能、寿命和安全性产生不利影响。
动力电池的热管理主要包括以下几个方面的内容:一、散热系统散热系统是动力电池热管理的重要组成部分,其主要功能是通过散热器、散热风扇等设备将电池组产生的热量散发到外部环境中。
散热系统的有效性直接影响着电池的热管理效果。
目前常见的散热系统有空气散热和液冷散热两种方式,根据不同的应用场景可以选择合适的散热方式。
二、温度传感与控制温度传感与控制是动力电池热管理的关键技术之一。
通过在电池组内部设置温度传感器,可以实时监测电池的温度变化,并根据实际情况进行温度控制。
当电池组温度过高时,可以通过控制散热系统的工作状态来降低电池的温度,从而保证电池的安全性和稳定性。
三、热传导与分布均衡热传导与分布均衡是动力电池热管理的关键技术之一。
电池组内部由于电池单体之间存在微小的差异,可能会导致电池单体之间的温度分布不均衡。
这种不均衡会引起电池单体的老化和损坏,进而影响整个电池组的性能和寿命。
为了解决这个问题,可以通过优化电池组的结构设计,增加热传导通道,提高热传导效率,从而实现电池单体之间的温度均衡。
四、热管理策略热管理策略是指在电池组使用过程中针对不同的工况制定相应的热管理措施。
例如,在高温环境下,可以采取降低电池充放电速率、减小电池组的负载等方式来降低电池的温度。
在低温环境下,可以采取预热电池、增加电池充放电速率等方式来提高电池的温度。
通过合理制定热管理策略,可以最大限度地提高电池的性能和寿命。
动力电池热管理的研究和应用对于推动电动汽车和储能技术的发展具有重要意义。
通过有效管理和控制电池的热量,可以提高电池的安全性、稳定性和寿命,进而提高电动汽车的续航里程和使用寿命,加速电动汽车的普及和推广。
同时,动力电池热管理技术的应用也有助于提高储能系统的效率和可靠性,促进可再生能源的利用和储存。
典型的电池热管理系统结构
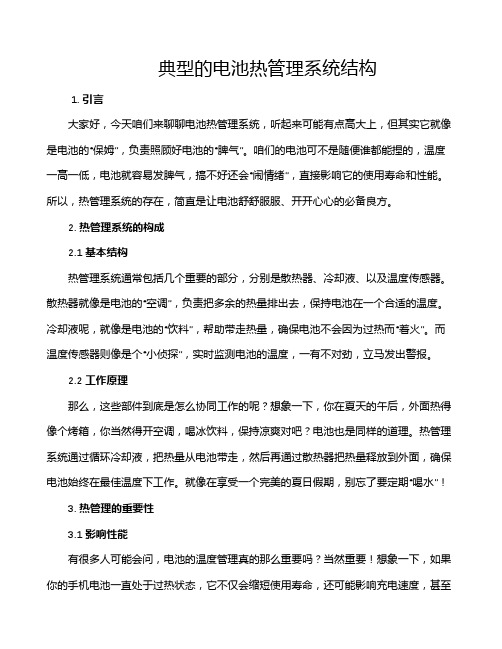
典型的电池热管理系统结构1. 引言大家好,今天咱们来聊聊电池热管理系统,听起来可能有点高大上,但其实它就像是电池的“保姆”,负责照顾好电池的“脾气”。
咱们的电池可不是随便谁都能捏的,温度一高一低,电池就容易发脾气,搞不好还会“闹情绪”,直接影响它的使用寿命和性能。
所以,热管理系统的存在,简直是让电池舒舒服服、开开心心的必备良方。
2. 热管理系统的构成2.1 基本结构热管理系统通常包括几个重要的部分,分别是散热器、冷却液、以及温度传感器。
散热器就像是电池的“空调”,负责把多余的热量排出去,保持电池在一个合适的温度。
冷却液呢,就像是电池的“饮料”,帮助带走热量,确保电池不会因为过热而“着火”。
而温度传感器则像是个“小侦探”,实时监测电池的温度,一有不对劲,立马发出警报。
2.2 工作原理那么,这些部件到底是怎么协同工作的呢?想象一下,你在夏天的午后,外面热得像个烤箱,你当然得开空调,喝冰饮料,保持凉爽对吧?电池也是同样的道理。
热管理系统通过循环冷却液,把热量从电池带走,然后再通过散热器把热量释放到外面,确保电池始终在最佳温度下工作。
就像在享受一个完美的夏日假期,别忘了要定期“喝水”!3. 热管理的重要性3.1 影响性能有很多人可能会问,电池的温度管理真的那么重要吗?当然重要!想象一下,如果你的手机电池一直处于过热状态,它不仅会缩短使用寿命,还可能影响充电速度,甚至在关键时刻掉链子。
可不想在重要的时刻突然没电,这可是会闹笑话的。
所以,热管理就像是电池的“保险箱”,保证它的性能始终如一。
3.2 保护安全更重要的是,热管理系统还关系到安全问题。
大家都知道,过热的电池可能会引发火灾,安全隐患不容小觑。
热管理系统就像是电池的“安全阀”,确保一旦温度超过安全范围,就会立刻启动冷却机制,避免事故发生。
毕竟,电池可不是玩笑,一旦出了问题,后果可是相当严重的。
4. 未来的发展随着科技的进步,热管理系统也在不断进化。
现在的技术不仅能实时监测电池的温度,还有些系统甚至能根据不同的使用环境自动调节冷却策略。
一文带你看懂动力电池热管理系统

一文带你看懂动力电池热管理系统如果电池的工作温度超出合理温度区间,不论是过热或过冷,都可能发生热失控,电池性能都会明显甚至急剧下降。
因此,电动汽车都会装备动力电池热管理系统,监测电池的工作温度等状况,出现异常时及时报警和处理。
动力电池热管理系统主要有冷却处理、加热升温、调整充放电策略三方面内容。
一、冷却处理高电压蓄电池的工作温度必须处于特定的范围内,才能确保容量和充电循环数等指标的理想寿命得以优化。
当电池温度较高时,利用冷却液循环、自然风吹散热、热泵空调等冷却方式,对电池进行冷却降温。
1.冷却液循环根据环境温度,可通过低温冷却器或连接在制冷剂循环回路上的热交换器,将高电压蓄电池的余热排出。
低温回路2的控制主要通过驱动高电压蓄电池冷却转换阀来完成。
高电压蓄电池冷却回路的散热器可将余热直接排放到环境中。
热交换器通过热交换器中所喷入或蒸发的制冷剂,对冷却液进行冷却。
随后,冷却后的冷却液提供给低温回路。
低温冷却回路如图所示:在通过充电装置供电插座对高电压蓄电池进行充电时,低温回路转换阀(Y73/2)在中等温度下切换到直流转换器和充电装置方向,并将电子装置的余热通过低温回路的散热器排出为此,风扇可根据冷却液温度分级开启。
当高电压蓄电池温度较低时,冷却液通过被高电压蓄电池冷却系统膨胀阀阻断的热交换器进行输送。
在这种情况下,高电压蓄电池的热容量被用于冷却直流转换器和充电装置的电子系统。
电动制冷剂压缩机将低温气态制冷剂从蒸发器中抽取,对其进行压缩,同时令其升温并输送到冷凝器中。
压缩后的高温制冷剂在冷凝器中通过流经的,或通过风扇马达所吸入的车外空气进行冷却。
当达到根据制冷剂压力所确定的露点后,制冷剂便会发生冷凝,并令其形态由气态变为液态。
随后,制冷剂流入储液罐(干燥器)。
在流过储液罐时,制冷剂吸收潮气,蒸气气泡被析出,同时机械杂质会被滤除,以保护后续部件免受侵害,清洁后的制冷剂继续流向高电压蓄电池冷却膨胀阀。
在那里,处于高压下的液态制冷剂被喷入,或蒸发至高电压蓄电池冷却系统热交换器中。
汽车动力电池热管理系统分析与设计

科技视界Science&Technology VisionScience&Technology Vision科技视界0引言动力电池热管理(Battery Thermal Management System,BTMS)是汽车动力电池系统的重要组成部分,它不仅对电池性能、寿命、安全等有重要影响,而且它是电动汽车整车热管理的重要组成部分,与整车热管理有着密不可分的关系。
随着电动汽车市场推广程度的逐渐深入,对电池系统热管理的要求也越来越高。
目前已有不少学者对动力电池热管理系统进行研究。
电池生热理论是电池热管理首先需要解决的问题,这个领域研究较早。
有关研究系统分析了电池散热能力的影响因素[1]。
有研究提出了BTMS的设计方法,并详细论述了各种散热系统,包括空冷系统、液冷系统、相变冷却、热管冷却和复合冷却等[2]。
但是,该研究仅仅讨论了各种冷却系统,并没有全面分析与探讨完善的热管理系统。
同样地,有些研究把问题焦点集中在电池散热上,包括散热结构设计、仿真分析等等[3-4],很少有研究从总体上较全面的讨论动力电池热管理系统设计。
鉴于此,本论文对动力电池热管理进行系统分析,并对总体设计做一论述。
1动力电池热管理系统结构与功能的分析从宏观上讲,动力电池热管理是对电池系统内部热环境进行控制、调节和利用。
其目的是为了使动力电池工作在一个最佳的热环境,充分发挥电池的性能。
同时,提供一个能量平衡的环境,实现整车能量的综合利用。
具体而言,热管理就是在电池系统中温度过高时,对系统进行降温;在温度过低时,对系统进行升温;在特殊情况下,譬如停车等待过程中,要对系统进行保温。
根据热管理的不同应用场合和功能,分为冷却系统、加热系统和保温系统。
1.1冷却系统的基本构成与功能冷却系统是动力电池热管理系统中最重要的组成部分。
受制于目前技术瓶颈的限制,动力电池工作的温度环境要满足特定的要求。
譬如磷酸铁锂电池的一般环境温度为-20℃~60℃。
动力电池热管理系统及其设计流程介绍

电池充电过程中的 能量平衡
图2
电池放电过程中的 能量平衡
95%以上。因此,温度对日历寿命的影响极大,温
度越高日历寿命衰退越严重。
从表2、图4可以看出,温度对电池的循环寿
1.2温度升高对电池寿命的影响 温度的升高对电池的日历寿命和循环寿命都 有影响。本文引用了某家动力电池厂关于不同温 度对不同电芯的日历寿命的影响数据,如图3、4 所示。具体数据如表l、2所示。
系统的零部件选型及热管理系统的性能评估等多 个方面来进行电池系统热管理的设计和验证,才 能保证电池的性能和安全性。 参考文献
5
电池热管理系统的性能评估
CFD是电池热管理系统最有效的评估手段之
[3]
方杰,王英,谢先字等.新能源汽车动力电池系统测试
一。根据目前已有的风冷和水冷项目经验,CFD
评价体系[J].上海汽车,2013(9):11-15.
空冷/水冷混合冷却系统 空冷/水冷}昆合冷却系统原理如图8所示。
3
热管理系统的设计流程介绍
空冷/水冷混合冷却系统中有两个关键零部件:一 个是水冷的电池冷却器,另一个是空冷的电池散 热器。
3.1产品开发流程 电池热管理系统的开发流程应与电池包开发 流程保持一致。热管理系统的设计贯穿于整个电 池包的设计过程中,在整车开发经过A样件、B样 件、C样件、D样件以及最后的产品5个阶段,电池 热管理参与每个阶段的设计、更改、试制以及验 证,具体流程见图10。 3.2热管理开发流程 电池的热管理系统开发首先必须明确客户的 需求以及对电芯性能的了解,根据电芯特点和整 车实际情况,确认电池的冷却方式是空气冷却还 是水冷却。不管哪种冷却方式,首先根据电池的
的性能和寿命有至关重要的作用。
动力电池热管理系统介绍
动力电池热管理系统及其设计流程介绍

上海汽车 2014. 06
·9·
新能源汽车
图 10 产品开发流程示意图
图 11 电池热管理开发流程示意图
4 电池热管理系统的零部件选型
4. 1 冷却板选型 冷却板作为电池包水冷系统中最关键的零部
件之一,冷 却 板 的 选 型 至 关 重 要。 冷 却 板 的 选 型 必须满足如下要求: 冷却板的压降必须满足客户 要求; 冷却水流动的一致性要求; 爆破压力要求; 冷却板的机械要求; 冷却板必须通过振动和冲击 载荷测试; 冷却板必须满足公差要求以及空间尺 寸要求。 4. 2 风机选型
新能源汽车
动力电池热管理系统及其设计流程介绍
周 奕 王 英 黄晨东 ( 上海汽车集团股份有限公司新能源和技术管理部,上海 201804)
【摘要】 从电池热管理系统、热管理系统零部件类型、电池热管理系统设计流程、热管理系统的零部件
选型以及热管理系统性能验证等几个方面全面介绍了动力电池热管理系统。对动力电池热管理系统的设计工 作有一定的指导意义。
参考文献
[1] 谭晓军. 电动汽车动力电池管理系统设计[M]. 广州: 中山大学出版社,2011.
[2] 陈世全. 先进电动汽车技术[M]. 北京: 化学工业出版 社,2013.
[3] 方杰,王英,谢先宇 等. 新能源汽车动力电池系统测试 评价体系[J]. 上海汽车,2013( 9) : 11-15.
【关键词】 动力电池 热管理系统 零部件 汽车
doi: 10. 3969 / j. issn. 1007-4554. 2014. 06. 02
动力电池组作为混合动力汽车的主要储能元 件,直接影响到 HEV 的性能。由于充放电过程中 电池本身会产生一定热量,从而导致温度上升,而 温度升高会影响电池的很多特性参数,如内阻、电 压、SOC、可用容量、充放电效率和电池寿命。电池 热效应问题也会影响到 HEV 整车的性能和循环 寿命。因此,研究电池的散热问题,对保持电池组
008 动力电池热管理系统

从宏观上讲,动力电池热管理是对电池系统内部热环 境进行制约、调节和利用。其目的是为了使动力电池工作 在一个最佳的热环境,充分发挥电池的性能。同时,提供 一个能量平衡的环境,实现整车能量的综合利用。
具体而言,热管理就是在电池系统中温度过高时,对 系统进行降温;在温度过低时,对系统进行升温;在特殊 情况下,譬如停车等待过程中,要对系统进行保温。根据 热管理的不同应用场合和功能,分为冷却系统、加热系统 和保温系统。
由于高温可以加速电解液、电极和隔板的老化速率, 当电池组中温差较大时,高温部分的老化速率会明显快 于低温部分,随着时间的积累不同电池之间的物性差异将 越加明显,从而破坏了电池组的一致性,最终使整组电 池提前失效。为了避免上述情况发生就必须对动力电池 进行热管理。对动力电池的热管理主要是通过电池热管 理系统(Battery Thermal Management System, BTMS)来实 现的。
图8-7(a)和图8-7(b)为Ni/MH电池在不同温度下的 常规循环性能和工况循环性能。可以看出无论是常规寿命 实验还是工况寿命实验都以高温55℃温度条件下的容量衰 减最快。200次循环其放电容量就低于初始容量的60%。低 温0℃条件下的常规循环寿命实验中,放电容量的变化曲 线与常温条件下的相接近。
电池的热相关问题是决定其使用性能、安全性、寿命 及使用成本的关键因素。电池热管理系统是应对电池的热 相关问题,保证动力电池使用性能、安全性和寿命的关键 技术之一。
我们以锂离子电池热相关问题为例从三个方面进行讲 述。
首先,锂离子电池的温度水平直接影响其使用中的能 量与功率性能。温度较低时,电池的可用容量将迅速发生 衰减,在过低温度下(如低于0℃)对电池进行充电,则 可能引发瞬间的电压过充现象,造成内部析锂并进而引发 短路。
- 1、下载文档前请自行甄别文档内容的完整性,平台不提供额外的编辑、内容补充、找答案等附加服务。
- 2、"仅部分预览"的文档,不可在线预览部分如存在完整性等问题,可反馈申请退款(可完整预览的文档不适用该条件!)。
- 3、如文档侵犯您的权益,请联系客服反馈,我们会尽快为您处理(人工客服工作时间:9:00-18:30)。
动力电池热管理系统组成及设计流程动力电池是电动汽车的能量来源,在充放电过程中电池本身会伴随产生一定热量,从而导致温度上升,而温度升高会影响电池的很多工作特性参数,如内阻、电压、SOC、可用容量、充放电效率和电池寿命。
电池热效应问题也会影响到整车的性能和循环寿命,因此,做好热管理对电池的性能、寿命至整车行驶里程都十分重要。
接下来,就从电池热管理系统及设计流程、零部件类型及选型、热管理系统性能及验证等几个方面来和大家聊一聊:动力电池热管理必要性1、电池热量的产生由于电池阻抗的存在,在电池充放电过程中,电流通过电池导致电池内部产生热量。
另外,由于电池内部的电化学反应也会造成一定的生热量。
2、温度升高对电池寿命的影响温度的升高对电池的日历寿命和循环寿命都有影响。
从上面两个图可以看出,温度对电池的日历寿命有很大的影响。
同样的电芯,在环境温度23℃,6238天后电池的剩余容量为80%,但是电池在55℃的环境下,272天后电池的剩余容量已经达到80%。
温度升高32℃,电芯的日历寿命下降了95%以上。
因此,温度对日历寿命的影响极大,温度越高日历寿命衰退越严重。
从上面两个图可以看出,温度对电池的循环寿命也有很大的影响。
同一款电芯,当剩余容量为90%,25℃温度下输出容量为300kWh,而35℃温度下的输出容量仅为163kWh。
温度上升10℃,电芯的循环寿命下降了近50%。
由此可见,温度对电池的循环寿命有很大的影响。
因此,为了电池包性能的最优化,需要设计热管理系统确保各电芯工作在一个合理的温度范围内。
02热管理系统的分类及介绍不同的热管理系统,零部件类型的结构不同、重量不同以及系统的成本不同和控制方式不同,使得系统所达到的性能也不相同。
主要有如下五大类:1、直冷系统直冷系统具有系统紧凑、重量轻以及性能好的优点。
但是此系统是一个双蒸发器系统、系统没有电池制热、没有冷凝水保护、制冷剂温度不易控制且制冷剂系统寿命短。
2、低温散热器冷却系统低温散热器冷却系统是电池的一个单独系统,由散热器、水泵和加热器组成。
该冷却系统具有系统简单、成本低、低温环境下经济节能等优点。
但是此系统有着冷却性能低、夏天水温高、应用受天气限制等缺点。
3、直接冷却水冷却系统直接冷却水冷却系统具有系统紧凑、冷却性能好以及工业应用范围广等优点。
但是此系统零部件比直冷多、系统复杂、燃料经济性差且压缩机负荷高。
此类型的冷却系统是目前最常用的电池热管理系统之一。
4、空冷/水冷混合冷却系统空冷/水冷混合冷却系统中有两个关键零部件:1)水冷电池冷却器;2)空冷电池散热器。
空冷/水冷混合冷却系统具有系统紧凑、性能好且低温环境下经济节能等优点。
但是此系统复杂、成本高、控制复杂且可靠性要求高。
5、直接空气冷却系统此系统利用驾驶舱的低温空气对电池进行冷却。
直接空气冷却系统具有系统简单、空气温度可控以及成本低等优点。
但是此系统并不是对所有类型的电芯都适合,浸湿后回复慢且电池内部会有污染的风险。
03热管理系统设计流程1、产品开发流程电池热管理系统的开发流程应与电池包开发流程保持一致。
热管理系统的设计贯穿于整个电池包的设计过程中,在整车开发经过A样件、B样件、C样件、D样件以及最后的产品5个阶段,电池热管理参与每个阶段的设计、更改、试制以及验证。
2、热管理开发流程设计性能良好的电池组热管理系统,要采用系统化的设计方法。
电池组热管理系统设计的过程包括如下7个步骤:04设计过程中的关键技术1、确定电池工作最优工作温度范围由于气候和车辆运行条件对电池影响很大,所以设计BTMS时需要确定电池组最优的工作温度范围。
目前电动汽车用电池主要有铅酸电池、氢镍电池和锂离子电池。
1)铅酸电池经研究发现,铅酸电池的寿命随温度增加线性减少,充电效率却线性增加,随着电池温度的降低充电接受能力下降,特别是0℃以下;模块间的温度梯度减少了整个电池组的容量,推荐保持电池组内温度的均匀分布和控制现有铅酸电池温度在35~40℃之间。
效率和最大运行功率在-26~65℃范围内增加。
2)氢镍电池当温度超过50℃时,电池充电效率和电池寿命都会大大衰减,在低温状态下,电池的放电能力也比正常温度小得多。
下图是某80Ah氢镍电池不同温度下电池放电效率图,由图中可以看出,在温度高于40℃或者温度低于0℃时,电池的放电效率显著降低。
如果仅根据这一限制,此电池的工作运行范围应该在0~40℃之间。
3)锂离子电池与氢镍电池、铅酸电池相比,能量密度更高,导致生热更多,所以对散热要求更高。
锂离子电池最佳工作温度在-20~75℃之间。
铅酸电池、氢镍电池、锂离子电池热管理的必要性取决于各自的生热率、能量效率和性能对温度的敏感性。
氢镍电池在高温> 40℃)时生热最多、效率最低并且易于发生热失控事故。
因此,氢镍电池很需要热管理,很多对氢镍电池进行液体冷却的努力也突出了这一点。
2、电池热场计算及温度预测电池不是热的良导体,电池表面温度分布不能充分说明电池内部的热状态,通过数学模型计算电池内部的温度场,预测电池的热行为,对于设计电池组热管理系统是不可或缺的环节。
通常使用如下公式进行计算:式中:a、T 是温度;b、ρ 是平均密度;c、Cp 是电池比热;d、kx 、ky 、kz 分别是电池在x 、y 、z 方向上的热导率;e、q 是单位体积生热速率。
3、电池生热率电池充电过程中的反应生热可以分为两个阶段。
第1阶段:没有发生过充电副反应之前,生热量主要来自: 电池化学反应生热、电池极化生热、内阻焦耳热。
第2阶段:在发生过充电副反应之后,生热量主要来自: 电池化学反应生热、电池极化生热、过充电副反应生热、内阻焦耳热。
其中大部分的生热量来自于过充电副反应生热。
充电末期和过充电时,过充电副反应就开始发生。
电池放电过程中的生热量主要来自: 电池化学反应生热、电池极化生热、内阻焦耳热。
需要指出的是氢镍电池放电时化学反应是吸热反应,能吸收一部分热量,所以生热问题不是很严重。
电池的内阻是影响电池生热速率的关键指标,它随着电池SOC变化,在得到电池内阻值后可以通过计算获得电池生热量,下图是某12V~80Ah氢镍电池模块在不同SOC下的内阻值。
采用专门设计的量热计可以直接测量出电池的生热量,还可以测出电池的热容量。
4、电池生热量主要因素5、散热结构设计电池箱内不同电池模块之间的温度差异,会加剧电池内阻和容量的不一致性,如果长时间积累,会造成部分电池过充电或者过放电,进而影响电池的寿命与性能,造成安全隐患。
电池箱内电池模块的温度差异与电池组布置有很大关系,一般情况下,中间位置的电池容易积累热量,边缘的电池散热条件要好些。
所以在进行电池组结构布置和散热设计时,要尽量保证电池组散热的均匀性。
以空冷散热为例来,通风方式一般有串行和并行两种,如下图所示。
串行通风方式下,冷空气从左侧吹入从右侧吹出。
空气在流动过程中不断地被加热,所以右侧的冷却效果比左侧要差,电池箱内电池组温度从左到右依次升高。
并行通风方式使得空气流量在电池模块间更均匀地分布。
并行通风方式需要对进排气通道,电池布置位置进行很好地设计,其楔形的进排气通道使得不同模块间缝隙上下的压力差基本保持一致,确保了吹过不同电池模块的空气流量的一致性,从而保证了电池组温度场分布的一致性。
6、风机与测温点选择在设计电池热管理系统时,希望选择的风机种类与功率、温度传感器的数量与测温点位置都恰到好处。
以空冷散热方式为例,设计散热系统时,在保证一定散热效果的情况下,应该尽量减小流动阻力,降低风机噪音和功率消耗,提高整个系统的效率。
可以用实验、理论计算和流体力学CFD仿真(本案例采用FloEFD软件)的方法通过估计压降、流量来估计风机的功率消耗。
当流动阻力小时,可以考虑选用轴向流动风扇;当流动阻力大时,离心式风扇比较适合。
当然也要考虑到风机占用空间的大小和成本的高低。
寻找最优的风机控制策略也是热管理系统的功能之一。
同侧风道流线图异侧风道流线图电池箱内电池组的温度分布一般是不均匀的,因此需要知道不同条件下电池组热场分布以确定危险的温度点。
测温传感器数量多,有测温全面的优点,但会增加系统成本。
考虑到温度传感器有可能失效,整个系统中温度传感器的数量又不能太少,至少为两个。
根据不同的实际工程背景,理论上利用有限元分析、试验中利用红外热成像或者实时的多点温度监控的方法可以分析和测量电池组、电池模块和电池单体的热场分布,决定测温点的个数,找到不同区域合适的测温点。
一般的设计应该保证温度传感器不被冷却风吹到,以提高温度测量的准确性和稳定性。
在设计电池时,要考虑到预留测温传感器空间,比如可以在适当位置设计合适的孔穴。
05热管理系统性能评估仿真是电池热管理系统最有效的评估手段之一。
根据目前已有的风冷和水冷项目经验,仿真可以完成如下工作:1)水冷系统冷却板的压降计算以及冷却水流动一致性计算;2)电池包热性能评估计算;3)空气冷却系统优化计算。
1、散热型电池包热管理案例以下为某混合动力汽车建立的整车热管理,其中包含电池包热管理模型、乘员舱模型、发动机冷却、HVAC、油冷系统和电机冷却系统FloMASTER软件(软件原名称Flowmaster)仿真模型,其中针对电池冷却系统,开展了一系列的设计仿真工作。
针对电池包,建立了电芯模型和冷却模型,考虑了电芯的热容、热阻和热桥,对冷却和加热过程进行了研究,得到了满足冷却温度要求(电芯不超过40℃)的水流量和在规定的30分钟内升温30℃的加热功率,以及加热过程中各电芯的温度均匀性及滞后性能。
2、直接空气冷却型电池包该案例为三菱欧兰德车型的热管理仿真,得到了不同气象条件及整个测试循环工况下蒸发器出口的冷风状态及电芯温度。
3、空/水混合冷却型电池包以下模型为空/水混合冷却型电池热管理及整车热管理模型,并对该系统进行了不同季节、不同车况的热管理仿真,并结合控制策略,研究了不同档位的采暖和电池加热工况以及纯加热工况,对系统设计及控制策略优化提供了重要依据。
最后小编想说电池的温度直接影响了电池的安全性,因此电池的热管理系统设计研究是电池系统设计中最关键的工作之一。
必须严格按照电池的热管理设计流程、电池的热管理系统及零部件类型、热管理系统的零部件选型及热管理系统的性能评估等多个方面来进行电池系统热管理的设计和验证,才能保证电池的性能和安全性。
文章来源:海基科技。