炼铁学
炼铁学复习资料

ೖᄤኧআᇴᓾ೯!
ဉීǖጲሆᒑ۞ࠤஊျਜ਼ݝॊৈཱཽྀᆐᒮገࡼ൙ၤᄌLjఠ၂ดྏᏐࡍ᎖ᑚৈपᆍLjด
ྏᑵཀྵቶݙতۣᑺLjࡊښஞݬఠ!
名词解释:
假象及半假象赤铁矿:由于地表的氧化作用,自然界中纯磁铁矿很少见,在化学成分上Fe3O4被氧化成Fe2O3,但仍保留了原磁铁矿结晶结构特征。
有效容积利用系数:每立方米高炉有效容积每昼夜生产的合格铁量。
焦比:冶炼每吨生铁所消耗的焦炭的千克数。
煤比:冶炼每吨生铁所消耗的煤粉的千克数。
燃料比:冶炼每吨生铁所消耗的固体燃料的总和。
(燃料比=焦比+煤比)
综合焦比:焦比+煤比X煤焦置换比
煤焦置换比:喷吹1kg煤粉所能代替的焦炭数。
焦炭冶炼强度:每立方米高炉有效容积每昼夜燃烧的焦炭吨数。
综合冶炼强度:每立方米高炉有效容积每昼夜燃烧的综合焦炭的吨数。
燃烧强度:每平方米炉缸截面积每昼夜燃烧的焦炭吨数。
工序能耗:Ci=(燃料消耗+动力消耗-回收二次能源)/产品产量
固相反应:在一定温度下,某些离子克服晶格结合力,进行位置交换,并扩散到与其相邻的其他晶格内的过程,叫固相反应。
铁酸钙理论(低温烧结理论):生产高碱度烧结矿,粘结相主要由铁酸钙组成。
该系的特点是无需高温,燃料消耗少;矿物的强度高还原性好。
自蓄热作用:随着烧结层的下移,料层温度的最高值逐渐提高。
自蓄热来源于被上层热烧结矿预热了的空气以及上层带入的热废气的加热作用。
HPS:指小球烧结法,即将烧结混合料用圆盘造球机预先制成一定粒度(上限为6·~8mm),然后使小球外裹部分燃料,最后铺在烧结台车上进行烧结的造块新工艺。
SFCA:即复合铁酸钙理论,实际烧结矿中的铁酸钙,无论是针状还是片状,都不是单纯的CaO和Fe2O3组成的,铁酸钙中含有一定量的Al2O3和SiO2等,称为复合铁酸钙。
铁氧化物的直接还原:还原剂为固体C,还原产物为CO。
铁氧化物的间接还原:还原剂是H2或CO,还原产物为H2O或CO2。
直接还原度:通过直接还原方式还原出来的铁量与还原出来的总铁量之比。
耦合反应:风口以下炉缸区域,渣铁间的氧化还原反应,即耦合反应。
熔化温度:炉渣受热升温过程中,固相完全消失的最低温度,即相图上的液相线温度(相当于软熔带下沿温度)。
熔化性温度:炉渣可以自由流动时的最低温度。
长渣和短渣:温度降到一定值后,粘度急剧上的称为短渣;随温度下降粘度上升缓慢称为长渣。
表面张力:生成单位面积的液相与气相的新交界面所消耗的能量。
界面张力:渣铁之间形成单位面积界面所消耗的能量。
燃烧带:风口前碳被氧化而气化的区域,又叫风口回旋区,它是高炉内唯一的氧化区域,故又称氧化带。
管道行程:煤气总是沿着透气性好的路线上升,高炉炉料的特性及在炉内的分布时不同的,在炉内局部出现气流超过临界速度的转态,局部区域煤气流过分发展的现象。
液泛现象:当渣量多,渣粘度大,煤气流速快时,出现煤气把渣铁拖住而不能降落的现象。
空区(热储备区):高炉中下部,炉料与煤气的温差很小,大约只有5~50℃左右,发生微弱
炼铁学
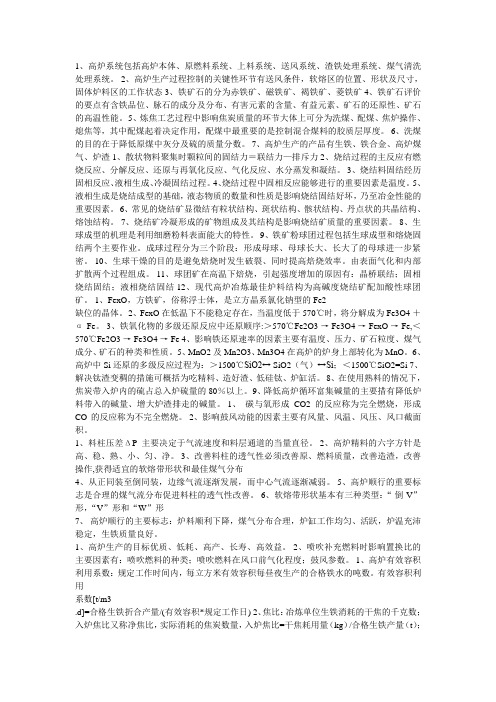
1、高炉系统包括高炉本体、原燃料系统、上料系统、送风系统、渣铁处理系统、煤气清洗处理系统。
2、高炉生产过程控制的关键性环节有送风条件,软熔区的位置、形状及尺寸,固体炉料区的工作状态3、铁矿石的分为赤铁矿、磁铁矿、褐铁矿、菱铁矿4、铁矿石评价的要点有含铁品位、脉石的成分及分布、有害元素的含量、有益元素、矿石的还原性、矿石的高温性能。
5、炼焦工艺过程中影响焦炭质量的环节大体上可分为洗煤、配煤、焦炉操作、熄焦等,其中配煤起着决定作用,配煤中最重要的是控制混合煤料的胶质层厚度。
6、洗煤的目的在于降低原煤中灰分及硫的质量分数。
7、高炉生产的产品有生铁、铁合金、高炉煤气、炉渣 1、散状物料聚集时颗粒间的固结力=联结力—排斥力 2、烧结过程的主反应有燃烧反应、分解反应、还原与再氧化反应、气化反应、水分蒸发和凝结。
3、烧结料固结经历固相反应、液相生成、冷凝固结过程。
4、烧结过程中固相反应能够进行的重要因素是温度。
5、液相生成是烧结成型的基础,液态物质的数量和性质是影响烧结固结好坏,乃至冶金性能的重要因素。
6、常见的烧结矿显微结有粒状结构、斑状结构、骸状结构、丹点状的共晶结构、熔蚀结构。
7、烧结矿冷凝形成的矿物组成及其结构是影响烧结矿质量的重要因素。
8、生球成型的机理是利用细磨粉料表面能大的特性。
9、铁矿粉球团过程包括生球成型和熔烧固结两个主要作业。
成球过程分为三个阶段:形成母球、母球长大、长大了的母球进一步紧密。
10、生球干燥的目的是避免焙烧时发生破裂、同时提高焙烧效率。
由表面气化和内部扩散两个过程组成。
11、球团矿在高温下焙烧,引起强度增加的原因有:晶桥联结;固相烧结固结;液相烧结固结 12、现代高炉冶炼最佳炉料结构为高碱度烧结矿配加酸性球团矿。
1、FexO,方铁矿,俗称浮士体,是立方晶系氯化钠型的Fe2缺位的晶体。
2、FexO在低温下不能稳定存在,当温度低于570℃时,将分解成为Fe3O4 +α-Fe。
炼铁学PPT(辽宁科技大学)

1.2 高炉本体及主要构成
❖ 密闭的高炉本体是冶 炼生铁的主体设备。 它是由耐火材料砌筑 成竖式圆筒形,外有 钢板炉壳加固密封, 内嵌冷却设备保护 (图1-2)。
❖ 高炉内部工作空间的 形状称为高炉内型。 高炉内型从下往上分 为炉缸、炉腹、炉腰、 炉身和炉喉五个部分, 该容积总和为它的有 效容积,反映高炉所 具备的生产能力。
❖ 冶炼过程中,炉料(矿石、熔剂、焦炭)按照确 定的比例通过装料设备分批地从炉顶装入炉内。 从下部风口鼓入的高温热风与焦炭发生反应,产 生的高温还原性煤气上升,并使炉料加热、还原、 熔化、造渣,产生一系列的物理化学变化,最后 生成液态渣、铁聚集于炉缸,周期地从高炉排出。 上升过程中,煤气流温度不断降低,成分逐渐变 化,最后形成高炉煤气从炉顶排出。
传统的高炉—转炉炼钢流程,工艺成熟,可大 规模生产,是现代钢铁生产的主要形式。
现代钢铁生产的一般流程
现代炼铁方法
❖ 现代炼铁方法分为:
非高炉炼铁法 非高炉炼铁法,泛指高炉以外,不用焦炭,用
煤、燃油、天然气、电为能源基础的一切其它 炼铁方法。例如直接还原法,主要是指在冶炼 过程中,炉料始终保持固体状态而不熔化,产 品为多孔状海绵铁或金属化球团的方法。熔融 还原法是用高品位铁精矿粉(经预还原)在高 温熔融状态下直接还原冶炼钢铁的一种新工艺。 新兴的直接还原—电炉炼钢流程,规模较小, 目前还正在发展,是钢铁生产的重要补充。
❖ 高炉还可生产特殊生铁,如锰铁、硅铁、镜铁(含 10~25%Mn)、硅镜铁(含9~13%Si, 18~24%Mn)等,主要用作炼钢脱氧剂和合金化 剂。
1.3 高炉冶炼产品
❖ 此外,生铁中还可能含有部分微量元素。生铁中微 量元素含量常以ΣT为指标:
❖ ΣT= Pb +Sn +Sb +As +Ti +V +Cr +Zn
钢铁冶金分学科发展——炼铁
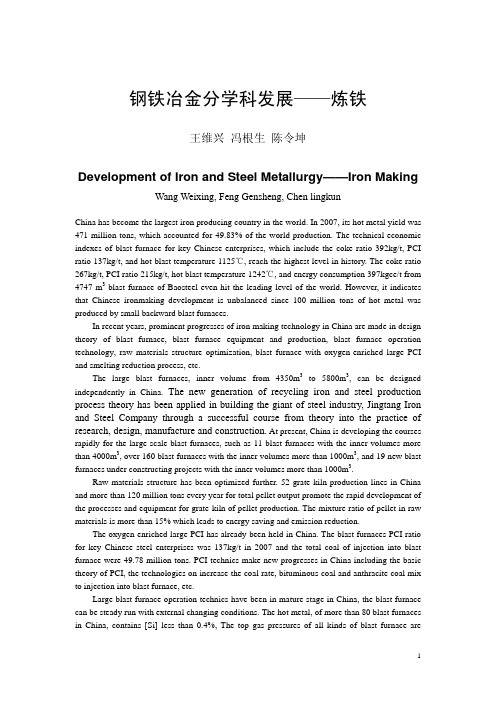
煤气 (CO2%) 24.91 24.47 20.56 19.14 20.30 21.00 17.40
近年来冶金工程技术取得较大发展,钢铁冶金理念的不断提升,使炼铁生产 技术得到不断的提高,炼铁学科也有了新的进展。高炉、烧结机、焦炉等冶金设
2
备加速向大型化、高效化、自动化、长寿化、生产过程环境友好方向发展。以降 低炼铁燃料比和提高喷煤比为中心的科学研究和生产实践不断进步,促进了炼铁 系统的结构优化。中国炼铁生产技术水平的不断提高,缩小了与国际先进水平的 差距。宝钢 COREX-3000 的顺利投产,标志着中国非高炉炼铁技术有了较大的 进步。
1
continuously increased. In November 2007, the biggest and world leading COREX-3000 smelting reduction
equipment was put into operation in Baosteel. Improvements have been made in raw materials prepareing, feeding equipment and operation, etc, which promote the development of non-blast-furnace iron making.
In recent years, prominent progresses of iron making technology in China are made in design theory of blast furnace, blast furnace equipment and production, blast furnace operation technology, raw materials structure optimization, blast furnace with oxygen-enriched large PCI and smelting reduction process, etc.
冶金炼铁学重点
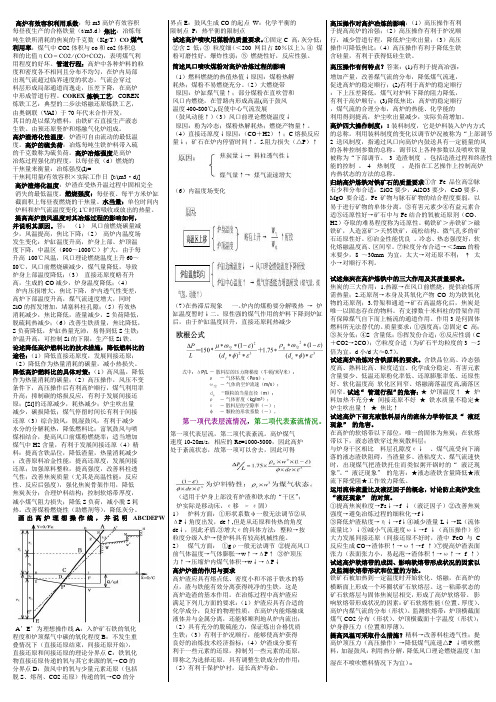
高炉有效容积利用系数:每m3高炉有效容积每昼夜生产的合格铁量(t/m3.d)焦比:冶炼每吨生铁所消耗的焦炭的千克数(Kg/T)CO煤气利用率:煤气中CO2体积与co和co2体积总和的比值ηCO = CO2 ⁄ (CO+CO2),表明煤气利用程度的好坏。
管道行程:高炉中各种炉料的粒度和密度各不相同且分布不均匀,在炉内局部出现气流超过临界速度的状态,气流会穿过料层形成局部通道而逸走,压差下降,在高炉中形成管道行程。
COREX炼铁工艺:CO REX炼铁工艺:典型的二步法熔融还原炼铁工艺,由奥钢联(V AI)于70年代末合作开发,其目的是以煤为燃料,由铁矿石直接生产液态生铁。
由预还原竖炉和熔融气化炉组成。
高炉渣溶化性温度:炉渣可自由流动的最低温度。
高炉的硫负荷:冶炼每吨生铁炉料带入硫的千克数称为硫负荷。
高炉冶炼强度是高炉冶炼过程强化的程度,以每昼夜(d)燃烧的干焦量来衡量:冶炼强度(I)=干焦耗用量/有效容积×实际工作日[t/(m3·d)]高炉渣熔化温度:炉渣在受热升温过程中固相完全消失的最低温度。
燃烧强度:每昼夜、每平方米炉缸截面积上每昼夜燃烧的干焦量。
水当量:单位时间内炉料和炉气流温度变化1℃时所吸收或放出的热量。
提高高炉鼓风温度对其冶炼过程的影响如何,并说明其原因。
答:(1)风口前燃烧碳量减少,风温提高,焦比下降;(2)高炉内温度场发生变化:炉缸温度升高,炉身上部、炉顶温度下降,中温区(900~1000℃)扩大,由于每升高100℃风温,风口理论燃烧温度上升60~80℃,风口前燃烧碳减少,煤气量降低,导致炉身上部温度降低;(3)直接还原度略有升高,生成的CO减少,炉身温度降低;(4)炉内压损增大,焦比下降,炉内透气性变差,高炉下部温度升高,煤气流速度增大,同时SiO的挥发增加,堵塞料柱孔隙;(5)有效热消耗减少,焦比降低,渣量减少,S负荷降低,脱硫耗热减少;(6)改善生铁质量,焦比降低,S负荷降低,炉缸热量充沛,易得到低S生铁;炉温升高,可控制Si的下限,生产低Si铁。
炼铁学 教学大纲

课程名称:炼铁学英文名称:Iron Making学时与学分:32/2(其中实验学时:,课内上机学时:)先修课程要求:无机化学,物理化学,钢铁冶金原理适应专业:矿物加工工程、冶金工程参考教材:钢铁冶金学(炼铁部分),王筱留,北京:冶金工业出版社,2005.3铁冶金学,张家驹,沈阳:东北工学院出版社,1988钢铁冶金教程,包燕平,冯捷,冶金工业出版社,2008.7课程简介:本课程为矿物加工工程(团矿方向)钢铁冶金工程学科的专业课,课程内容包括高炉炼铁的基本物理化学原理、传输理论、能量利用、工艺过程与强化方法、数学模型及非高炉炼铁的原理与工艺,主要讲述炼铁过程的基本理论、工艺过程与强化及炼铁技术的最新发展,使学生掌握炼铁基础理论和系统的专门知识,为从事本领域的科学研究和生产实践奠定基础。
一、课程在培养方案中的地位、目的和任务本课程是面向矿物加工工程专业(团矿方向)本科生的专业必修课程,主要任务是讲述炼铁过程的基本理论、工艺过程与强化及炼铁技术的最新发展,为从事炼铁生产、设计、教学、科学研究与开发、技术经济管理奠定基础。
二、课程的基本要求正确理解炼铁原理,掌握高炉冶炼工艺过程及其强化措施,了解高炉冶炼过程数学模型、自动控制技术、非高炉炼铁的原理与工艺及炼铁技术的最新发展。
三、课程的基本内容以及重点难点1.基本内容1)绪论:钢与铁,钢铁联合企业钢铁工业的发展,炉内主要过程,炼铁原料、燃料及其他辅助原料,炉料结构,高炉产品、技术经济指标。
2)高炉炼铁过程物理化学基础:蒸发、分解与气化,铁氧化物及其它元素的还原,耦合反应,造渣过程,生铁的形成等。
3)高炉炼铁过程中的传输现象:高炉内的动量传输与热量传输。
4)高炉炼铁能量利用:高炉炼铁能量利用指标,高炉炼铁能量利用分析。
5)高炉炼铁工艺:高炉生产的原则,高炉操作制度,高压操作,高风温操作,喷吹补充燃料,富氧和综合鼓风,加湿与脱湿鼓风等。
6)高炉冶炼过程数学模型概述:高炉冶炼过程模拟及控制,人工智能高炉专家系统。
炼 铁 学
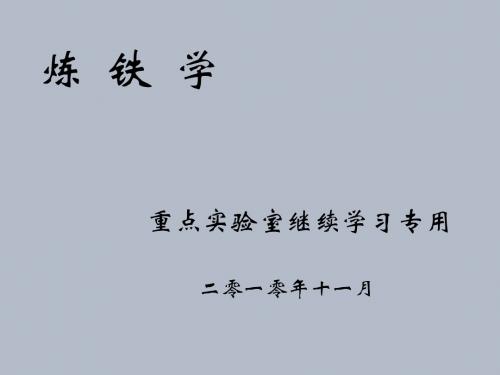
所以 反应平衡气相中 (CO%) = 100/(1+Kp)= f(T) ) ( ) 由于各反应的平衡常数 Kp 值不同,故相应平衡气相中CO%也不同。根据以上各反 应在不同温度下的平衡气相成分作图,可以得到 CO 还原铁氧化物的平衡气相组成与温 度的关系图如下:
2.2 H2 作还原剂
>570 ℃ 时
由上图还可见,在一个大气压下只有﹤ 400 ℃(673k) 时,平衡气相 全部由CO2组成; ﹥ 1000 ℃(1273k) 时则完全由CO组成。事实上除了生铁中含有的碳以外,高炉内的碳 全以焦炭的形式存在。焦炭的溶损反应 C焦 +CO2 =2CO 焦炭的溶损反应 的开始反应温度与激烈反应温 才开始反
3Fe2O3 + H2 = 2Fe3O4 + H2 O Fe3O4 + H2 = 3 FeO + H2 O FeO + H2 = Fe + H2 O
<570 ℃ 时,同样有
+ 21814 KJ
- 63600 KJ - 28011 KJ
1/4 Fe3O4 + H2 = 3/4 Fe + H2 O
- 36908 KJ
应该指出的是 FeO 在小于570℃ 时很不稳定,它会分解为Fe3O4 和 Fe 因此在570℃ 以 下的温度范围内铁氧化物是按着以下顺序还原 3 Fe2O3 2Fe3O4 6Fe
FeO的含氧量是22.8%,但在570℃ 以上氧在FeO 固相内溶解形成固溶体,称为浮氏体 浮氏体
(以 FexO 表示,式中X<1)它在不同温度时的含氧量是不同的(一般为22.65~25.6%)。
•
第一篇
1、铁氧化物的逐级还原特性
高炉炼铁原理
炼铁学 高炉冶炼过程的物理化学

炼铁学——高炉冶炼过程的物理化学
炼铁学——高炉冶炼过程的物理化学
3.1.3 碳酸盐分解
当炉料中单独加入熔剂(石灰石或白云石) 当炉料中单独加入熔剂(石灰石或白云石)或炉料中尚有其他类型 的碳酸盐时,随着温度的升高,当其分压 超过炉内气氛的CO 的碳酸盐时,随着温度的升高,当其分压pCO2超过炉内气氛的 2分压 时,碳酸盐开始分解。 碳酸盐开始分解。 FeCO3、MnCO3、MgCO3分解较容易,在炉内较高的位置即可开始。 分解较容易,在炉内较高的位置即可开始。 以上三种碳酸盐的分解反应发生在低温区,对冶炼过程无大影响。 以上三种碳酸盐的分解反应发生在低温区,对冶炼过程无大影响。 但石灰石(CaCO3)开始分解的温度高达 开始分解的温度高达700℃,且其分解速度受熔剂 但石灰石 开始分解的温度高达 且其分解速度受熔剂 粒度的影响较大。目前石灰石粒度多为 粒度的影响较大。目前石灰石粒度多为25~40mm,有相当一部分 有相当一部分 CaCO3进入 进入900℃以上的高温区后才发生分解 此时反应产物 此时反应产物CO2会与 ℃以上的高温区后才发生分解。此时反应产物 会与 固体碳发生碳素溶解损失反应: 固体碳发生碳素溶解损失反应: CO2+C= 2CO
炼铁学——高炉冶炼过程的物理化学
该反应吸收大量热量,并消耗碳素,对高炉能量消耗不利。 该反应吸收大量热量,并消耗碳素,对高炉能量消耗不利。计算中一 般取石灰石在高温区分解的部分占50~70%。 般取石灰石在高温区分解的部分占 炉料中碳酸盐来源:生熔剂 石灰石 白云石)、 石灰石、 炉料中碳酸盐来源:生熔剂(石灰石、白云石 、天然块矿 碳酸盐分解反应: 碳酸盐分解反应: FeCO3= FeO+ CO2 MnCO3= MnO+ CO2 MgCO3= MgO+ CO2 CaCO3= CaO+ CO2 碳酸盐分解条件 开始分解: 分解压) 炉内CO 分压)⇐⇒T开 开始分解:Pco2(分解压 ≥Pco2(炉内 2分压 分解压 炉内 化学沸腾: 分解压) 总 炉内总压 炉内总压)⇐⇒T沸 化学沸腾:Pco2(分解压 ≥P总(炉内总压 分解压
- 1、下载文档前请自行甄别文档内容的完整性,平台不提供额外的编辑、内容补充、找答案等附加服务。
- 2、"仅部分预览"的文档,不可在线预览部分如存在完整性等问题,可反馈申请退款(可完整预览的文档不适用该条件!)。
- 3、如文档侵犯您的权益,请联系客服反馈,我们会尽快为您处理(人工客服工作时间:9:00-18:30)。
第一章
有效容积利用系数:指高炉单位有效容积的日产铁量。
焦比:指生产每吨生铁所消耗的焦炭量。
综合焦比:是生产1t生铁实际耗用的焦炭以及各种辅助燃料折算为相应的干焦的综合。
冶炼强度:指单位体积高炉有效容积焦炭日消耗量,是标志高炉强化程度的指标之一。
焦炭负荷:指每批炉料中铁、锰矿石的总重量与焦炭重量之比,用以评估燃料利用水平操作水平,调节配料的重要参数。
生铁合格率:指合格生铁量占高炉总产量的百分数。
休风率:指高炉休风时间占规定作业时间的百分数,降低休风率是增产节约的重要途径。
生铁成本:指生产1t生铁所需的费用。
是衡量高炉生产经济效益的重要指标。
炉龄:指从高炉点火开炉到停炉大修,或高炉相邻两次大修之间的冶炼时间。
生铁分类:炼钢生铁、铸造生铁(翻砂铁、灰口铁)
高炉渣:由钙、镁、硅、铝的氧化物构成的复杂硅酸盐。
高炉煤气:是钢铁联合企业的重要二次能源,主要用作热风炉燃料,还可供动力、炼焦、烧结、炼钢、轧钢等部门使用。
第八章
高炉冶炼的五个主要区:块料带、软熔带、滴落带、风口带、渣铁带
铁的氧化物存在形式:三氧化二铁(赤铁矿)、四氧化三铁(磁铁矿)、氧化亚铁FeO(浮士体)铁的低级氧化物比高级氧化物稳定,因此还原与分解的顺序是一致的。
还原顺序:3个三氧化二铁→2个四氧化三铁→6个氧化亚铁FeO→6个Fe
温度大于570摄氏度时:三氧化二铁→四氧化三铁→氧化亚铁FeO→Fe
温度小于570摄氏度时:三氧化二铁→四氧化三铁→Fe
间接还原:在低、中温区进行的还原反应。
高炉内铁氧化物用CO还原,生成CO(2),并主要为放热反应的还原反应。
直接还原:在高温区所进行的还原反应。
高炉内铁氧化物用C还原,生成CO,并吸收大量热量的还原反应。
高炉常用还原剂:C、CO、H(2)
CO与H(2)作为还原剂有何差异,他们的利用率如何表示?
答:当t小于810摄氏度时,CO还原能力比氢气强。
当t大于810摄氏度时,氢气还原能力比CO强。
说明氢气的还原能力随温度升高而升高。
炉顶煤气中CO2与煤气中CO2+CO 之比叫CO利用率,它是反映风口前碳燃烧和炉内直接还原产生的CO在上升过程中参加间接还原程度的指标。
CO(2)+C=2CO一般叫什么反应,对高炉冶炼过程有何影响?
答:碳的气化反应。
是高炉可直接根据温度划分稳定区,没有这个方程则需根据图划分稳定区。
A消耗焦炭B吸收高温区热量C破坏焦炭强度D影响料柱透气性。
复杂Fe氧化物:先分解为游离的铁氧化物,再被还原剂还原(先分解再还原)
为什么100%直接还原与100%间接还原都不是高炉冶炼最理想过程?
答:事实上焦炭燃烧既发热,又提供还原剂,而要完成冶炼过程,热能和化学能的消耗,或者说直接还原和间接还原的发展,在一定的冶炼条件下,有一个合适的比值,在此比值下,高炉冶炼需要的热能和化学能都能得到满足,从而获得最小的燃料消耗,这也就是最合适的高炉行程。
锰的还原发生在高炉的滴落带区域
提高锰还原的条件:(1)足够高的炉缸温度(2)提高炉渣碱度,锰回收率增加(3)正确选择原料(4)调整软熔带位置
硅的还原:P144(低碱度、软熔带位置)
改善及控制硅还原的条件:(1)较高的炉缸温度和充足的热储备(2)适宜的造渣制度(3)注意原料选择
铸造铁炼酸性渣。
高炉条件下:完全不还原的有CaO、MgO、Al2O3部分还原的有MnO、SiO2(Cr、Mn、V、Si、Ti)容易还原的有Cu、Pb、Ni、Co、Fe最难还原的非Fe成分为C、Si、Mn、P、S消耗热量最多的为Si
C在Fe中存在形态:Fe3C(化合态、银白色、白口铁)、C(石墨、灰色、灰口铁)
第九章
炉渣的熔化温度(软熔带下面):是指炉渣完全熔化成液相的温度也是炉渣冷却时开始析出固相的温度。
炉渣的熔化性温度:是指炉渣熔化后能够自由流动的温度。
炉渣的稳定性:指当化学成分或温度改变时,对炉渣物理性质影响的程度。
炉渣在成分波动条件下保持稳定的能力,成为化学稳定性;在温度波动条件下炉渣保持稳定的能力,成为热稳定性。
什么叫硫负荷,一般是多少?
答:每吨生铁的炉料带入的总硫量,成为硫负荷,一般在4~8kg/t范围。
渣的作用:(起到渣铁分离、脱硫、调整生铁成分,影响炉温,促进顺行和保护炉衬等作用)1)通过调整炉渣的成分、性质和数量,来控制钢液中各元素的氧化还原反应过程,如脱碳、脱磷、脱氧、脱硫等;2)吸收金属液中的非金属夹杂物;3)覆盖在钢液上面,可减少热损失,防止钢液吸收气体;4)能吸收铁的蒸发物,能吸收转炉氧流下的反射铁粒,可稳定电弧炉的电弧;5)冲刷和侵蚀炉衬,好的炉渣能减轻这种不良影响,延长炉衬寿命。
渣的成分:化学分析表明,炼钢炉渣的主要成分是:Ca0、Si02、Fe203、Fe0、Mg0、P205、Mn0、CaS等,这些物质在炉渣中能以多种形式存在,除了上面所说的简单分子化合物以外,还能形成复杂的复合化合物,如2Fe0·Si02、2Ca0·Si02、4Ca0·P205等。
渣的来源(形成):1) 由造渣材料或炉料带入的物质。
2) 元素的氧化产物。
3) 炉衬的侵蚀和剥落材料。
4)合金元素脱氧产物及炉渣脱硫产物。
何谓液态炉渣的“表面性能”,表面性能不良会给冶炼过程造成哪些危害?
答:
有几种表示炉渣碱度的方法?
答:三种:(1)二元碱度CaO/SiO2;(2)三元碱度(总碱度):CaO+MgO/SiO2(3)四元碱度(全碱度):CaO+MgO/SiO2+ Al2O3
第十章
C与O的燃烧包括:风口回旋区加上中间层(区域:燃烧带)
燃烧带:就是风口前O2和CO2存在,并进行着碳燃烧反应的区域,即回旋区空腔加周围疏松焦炭的中间层。
由于是氧化性气氛,所以又称为氧化带。
影响燃烧带的因素:鼓风动能、燃烧反应速度、炉料分布状况
鼓风动能:指单位时间内鼓风所具有的能量,其大小表示鼓风克服风口前料层阻力,向炉缸中心穿透的能力。
影响鼓风动能的因素:风量、风温、风压和风口截面积等。
煤气体积变化:上升过程中,CO是先增加后减少,造成这一现象的原因是煤气在上升过程中,因直接还原、溶剂分解出的CO2被C还原生成的CO,以及焦炭挥发物的CO不断进入煤气中,使煤气上升到间接还原区时CO增至最大含量。
煤气成分变化:炉缸煤气中CO含量在35%~45%范围,而无CO2存在。
炉顶煤气中,CO 含量一般为20%~26%,而CO2含量为14%~22%。
煤气温度变化:在下部煤气温度迅速降低,中部变化很小,上部温度又迅速降低。
煤气温度不仅沿高炉高度有所变化,而且在同一断面上温度也是有差异的。
沿高炉截面上,中心和边缘气流发展,温度较高。
如何根据CO2曲线来分析炉内煤气能量利用与煤气流分:
答案:①中心与边缘CO2的高低,可说明中心与边缘气流的发展程度;
②CO2曲线平均水平的高低,说明高炉内煤气能量利用的好坏;
③4个方向CO2曲线的对称性,说明炉内煤气流是否偏行;
④CO2曲线平均水平无提高的情况下,CO2最高点移向2、3点,也说明煤气能量利用有所改善,因为此处正对应炉内截面积大、矿石多的地方;
⑤某一方向长期出现第2点甚至扩展到第3点CO2含量低于第1点,说明此方向炉墙破损,有结厚现象。
判断煤气的热能利用性质:炉顶煤气温度(t顶)。
t顶低,说明炉内热交换充分,炉料预热好,煤气热能利用好;反之,t顶高,炉料预热差,煤气热能利用差。
水当量(高炉内炉料):指单位时间内,通过高炉的某一截面的炉料,温度升高1摄氏度所吸收的热量
水当量(煤气):指单位时间内,通过高炉某一截面的煤气,温度降低1摄氏度所放出的热量。
水当量:单位时间内通过高炉某一截面的炉料(或煤气),其温度升高(或降低)1摄氏度所吸收(或放出)的热量。
水当量在高炉高度上的变化规律:(答案一)高炉上部:炉料所需热量主要消耗在加热炉料、水分蒸发、部分碳酸盐分解,因此需要热量较少,机上间接还原放出少量热量,故Ws<Wg,是t(s)上升较快。
高炉下部:炉料要进行大量直接还原、加热渣铁熔化等需要大量热量,愈到下部需要热量越大,因此,Ws上升很快,而t(s)上升很慢。
高炉中部:Ws约=Wg,煤气炉料温差很小,煤气放出热量与炉料吸收热量基本平衡,炉料的升温速率大致等于煤气降温速率。
(答案二)煤气当量在上升过程中又所增加,但因下部高温区煤气比热较大,而上部比热较小,故Ws基本保持不变。
(答案三)煤气水当量上、下部基本相同,这是因为G气上部大,下部小,而c气相反,上部小,下部大,两者乘积基本相同;炉料水当量上部小,下部大,这是由于上部不仅吸热反应少,而且C0间接还原还放热
第十三章
强化冶炼的方向:精料、高压操作、高风温、喷吹、富氧、综合鼓风和自动控制等技术。
精料八字:高、稳、熟、小、匀、净、少、好
第十四章
高炉操作制度:装料制度、送风制度、热制度、造渣制度。