货车车轮踏面损伤ansys
重载货车车轮磨耗发展规律及其踏面优化研究

重载货车车轮磨耗发展规律及其踏面优化研究
王广宇;赵瑞杰
【期刊名称】《专用汽车》
【年(卷),期】2024()1
【摘要】重载货车车轮踏面优化研究的主要目的是为了解决在实际应用过程中出
现的一些问题,如车轮踏面部分存在着严重的磨损、剥离等现象。
因此需要对其外
形以及结构方面进行一定程度上的改进和完善,使得车辆能够更加安全稳定地行驶。
为了能够更好地保证行车安全和提高运输效率,针对重载货车车轮磨耗发展规律以
及相应的踏面优化展开相关研究与探讨,多目标优化设计和遗传算法为车轮踏面优
化设计提供了可行性分析,研究表明,通过对车轮踏面结构的优化,可以减小车轮与车轮之间的受力,减小车轮磨耗,提高列车运行的安全性。
【总页数】3页(P71-73)
【作者】王广宇;赵瑞杰
【作者单位】郑州工业安全职业学院
【正文语种】中文
【中图分类】U469.2
【相关文献】
1.大秦线重载货车车轮踏面圆周磨耗原因分析及改进措施
2.重载货车车轮踏面垂直磨耗原因分析及改进
3.基于轮轨磨耗对30t轴重货车车轮踏面优化研究
4.30 t轴
重重载货车车轮踏面磨耗规律研究5.重载铁路货车车轮踏面磨耗表征方法及其规律分析
因版权原因,仅展示原文概要,查看原文内容请购买。
《提速货车轮对踏面损伤形式及检修数据分析》111111111要点
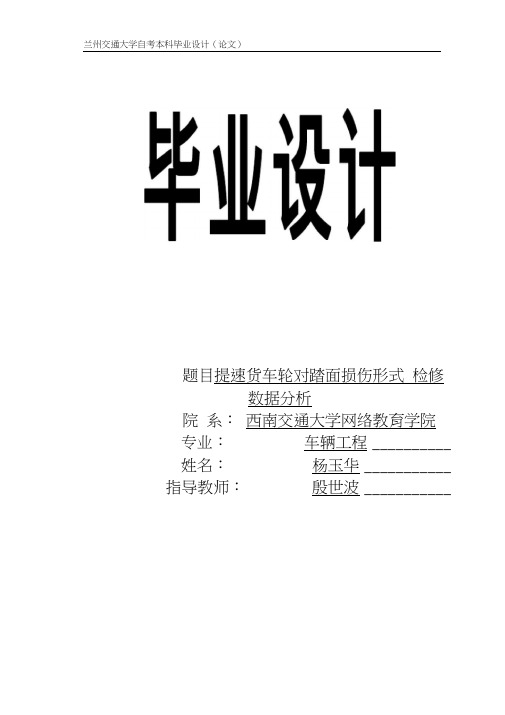
题目提速货车轮对踏面损伤形式检修数据分析院系:西南交通大学网络教育学院专业:车辆工程__________ 姓名:杨玉华___________ 指导教师:殷世波___________西南交通大学网络教育学院2010年6月18日院系西南交通大学网络教育学院专业______________________________ 年级2008—8 (春)学号08822697姓名 __________________________ 学习中心北京学习中心指导教师 _______ 殷世波 ____________ 题目:提速货车轮对踏面损伤形式检修数据分析指导教师评语_____________________________________________________________评阅人___________ (签章)成绩______________答辩组组长_________________________________________ (签章)毕业设计任务书班级2008—8 (春)学生姓名杨玉华学号08822687发题日期:2010年4月9日完成日期:2010年6月18日题目提速货车轮对踏面损伤形式检修数据分析 __________________________________ 题目类型:技术专题研究一、设计任务及要求随着国民经济的快速发展,铁路货运所承担的任务也越来越重。
在此环境下,货车提速就成为有效解决办法之一。
但是,随着货车速度的提高,诸如轮轨动作用力加剧等一系列问题就突显出来。
轮对是铁路机车车辆中不可或缺的重要走行部件,它们在机车车辆中必须完成其特有的功能——安全可靠地承担载荷和在钢轨上快速行使等。
由于车体本身的重量及其所承担的货物的重量最后均是通过轮对与钢轨的滚动接触来完成力的传递,所以一旦轮对丧失其应有的正常功能,即失效时,运输安全得不到有效保障。
从运行安全性和现场经验来看,车轮踏面损伤这种失效形式将会造成脱轨等事故,给行车安全带来极大的隐患。
基于ANSYS的火车车轮热应力有限元分析

基于ANSYS的火车车轮热应力有限元分析童乐1’2钟斌1’2陈刚1’2茆勇1’2邹强1’2高伟1’2(1.高性能轨道交通新材料及安全控制安徽省重点实验室;2.马鞍山钢铁股份有限公司)摘要火车刹车制动过程极易引发车轮热损伤,有必要对新设计车轮进行刹车制动过程的热应力分析。
利用AN SYS软件对新设计车轮进行热应力有限元分析,得出车轮在热载荷和静力载荷下的温度分布及应力分布情况,指导车轮的进一步优化设计。
关键词 热应力分析 A N S Y S溫度分布应力分布Finite Element Analysis of the Thermal Stress of Train Wheels Based on ANSYS Tong Le1,2Zhong Bin1,2Chen Gang1,2Mao Yong1,2Zou Qiang1,2Gao Wei1,2(1. Anhui Key Laboratory of High-performance Rail Transportation New Materials and Safety Control;2. Maanshan Iron & Steel Co. , Ltd.)Abstract The braking process of the train is very easy to cause the thermal damage of wheels. It is necessary to analyze the thermal stress of the newly designed wheels in the braking process. The thermal stress finite element analysis of the new designed wheels was carried out by ANSYS software, the temperature distribution and stress distribution of the wheels under heat load and static load were obtained* which guides the further optimum design of the wheels.Keywords thermal stress analysis ANSYS temperature distribution stress distribution〇前言目前,随着轨道车辆的运行速度及轴重的不断 增加,轨道车辆在高速行驶过程中所产生的动能也 在不断加大,这导致了在刹车制动过程中因闸瓦和 车轮踏面部位的机械摩擦而产生的热负荷引起的车 轮热损伤加剧[>4]。
用ANSYS分析工程车辆轮胎与路面接触的问题

用ANSYS分析工程车辆轮胎与路面接触的问题
刘文武;胡长胜;陆念力
【期刊名称】《中国工程机械学报》
【年(卷),期】2012(010)003
【摘要】在模拟工程车辆轮胎和路面的接触关系中,如何选择更精确的分析算法,一直是研究工程车辆对路面的作用的关键问题.在ANSYS中建立好工程车辆轮胎和路面的等效有限元模型之后,通过接触对工具建立轮胎和路面之间的接触关系,并且对ANSYS提供的各种分析算法进行分析对比.结果表明,工程车辆轮胎与路面接触问题最好的接触算法是Lagrange算法,接触行为是粘接(bonded).分析思路可以为以后的研究人员提供一定的借鉴和参考.
【总页数】5页(P265-268,275)
【作者】刘文武;胡长胜;陆念力
【作者单位】哈尔滨工业大学机电工程学院,黑龙江哈尔滨150001;哈尔滨工业大学机电工程学院,黑龙江哈尔滨150001;哈尔滨工业大学机电工程学院,黑龙江哈尔滨150001
【正文语种】中文
【中图分类】TH21
【相关文献】
1.轮胎——路面接触压力问题研究 [J], 谢水友
2.工程车辆轮胎滚动状态下与土壤接触有限元分析 [J], 韩卿;孙蓓蓓
3.工程车辆轮胎滚动状态下与土壤接触有限元分析 [J], 韩卿; 孙蓓蓓
4.基于轮胎与路面接触压力特性的路面抗滑性能评价方法 [J], 曹一翔;孙杨勇
5.轮胎/路面接触问题分析 [J], 徐延海;程东升;贾丽萍;张建武
因版权原因,仅展示原文概要,查看原文内容请购买。
关于铁路货车车轮踏面擦伤的分析

关于铁路货车车轮踏面擦伤的分析铁路货车车轮踏面擦伤是车辆运行中的常见问题。
擦伤会严重影响列车和轨道设施的安全和使用寿命,因此对踏面擦伤故障造成的原因进行分析,减少擦伤故障,降低铁路货车检修成本,提高铁路货车使用效率是很有实际意义的。
1 铁路货车车轮踏面擦伤的共性原因车轮踏面擦伤的共性原因大致分几点:制动力过大引起的轮对抱死致使踏面滑行擦伤;制动系统故障或调整不合理引起的踏面擦伤;制动抱闸故障引起的踏面擦伤;缓解不同步引起的踏面擦伤。
1.1 制动力过大引起的车轮踏面擦伤由于制动时机车司机所减压过大,闸瓦压力产生的制动力超过了轮对与钢轨间的粘着力,导致车轮滑行造成踏面擦伤。
粘着系数随速度的增加而减小,列车速度低,冲击振动和轮轨间的横向和纵向的少量滑动减弱,因此粘着系数增加。
1.2 制动装置故障或调整不合理引起的车轮踏面擦伤由于制动装置故障或调整不合理引起车轮踏面擦伤的因素有:基础制动部位调整存在问题、闸调器故障或调整不合理、制动缸行程不合理、空重车调整装置调整不合理、制动管泄漏。
由于基础制动部分调整存在问题,造成一位转向架与二位转向架之间、同一辆车四个制动梁之间,以及同一条制动梁两端的闸瓦之间的制动力均不相同,其中制动力较大的就可能造成车轮踏面擦伤。
基础制动连杆机构连接副的间隙分配不合理导致缓解阻力大,导致不能缓解造成车轮踏面擦伤。
闸调器故障时,螺杆只能缩短而不能伸长,间隙越来越小,制动力越来越大,容易造成轮对踏面擦伤,甚至将车轮抱死。
调整不合理是指在调整闸调器时超出了规定的范围,当闸瓦间隙过小时不能再伸长,导致制动时闸瓦压力过大或抱闸。
空重车调整装置调整不合理是指触头与横跨梁间隙过小,空车制动时施加了重车制动力,制动力过大导致踏面擦伤。
制动管系漏泄不能被及时发现和处理,如果漏泄过限容易造成自然制动,容易使轮对踏面擦伤。
1.3 制动抱闸故障引起的踏面擦伤制动抱闸故障是由于空气制动机故障、人力制动机不缓解等原因造成的制动缓解不良、闸瓦未与车轮踏面分离,其主要危害是车轮踏面擦伤。
基于ANSYS的载重车辆轮胎失效仿真研究[1]
![基于ANSYS的载重车辆轮胎失效仿真研究[1]](https://img.taocdn.com/s3/m/526339dd5022aaea998f0fd1.png)
2008年第4期车辆与动力技术Vehicle &Power Technol ogy总第112期文章编号:1009-4687(2008)04-0058-05基于ANS YS 的载重车辆轮胎失效仿真研究齐晓杰1,2, 于建国1(11东北林业大学交通学院,哈尔滨 150050;21黑龙江工程学院汽车工程系,哈尔滨 150050)摘 要:针对轮胎的主要失效形式,利用有限元法进行了失效仿真研究,主要进行了应力、应变及位移状况的分析,并对轮胎的寿命进行了预测.关键词:载重车辆轮胎;有限元分析;失效仿真;寿命预测中图分类号:U4631341+3 文献标识码:ASi m ul ati on Research on the Heavy 2duty Vehi cleTyre Fa ilure Based on ANS YSQ I Xiao 2jie1,2, Y U J ian 2guo1(11The Traffic College,Northeast Forestry University,Haerbin 150050,China;21The Aut omobile Engineering Depart m ent,Hei L ongjiang I nstitute of Technol ogy,Haerbin 150050,China )Abstract:The finite ele ment failure si m ulati on research of tyres is achived t o their main failure f or m.The stress,strain and the dis p lace ment in the tyres are analyzed ,and the seruice life of the Tyres is f orecasted .Key words:heavy 2duty vehicle tyres;finite ele ment analysis;failure si m ulati on;life p redicti on收稿日期:2008-09-01作者简介:齐晓杰(1960-),男,在读博士,教授. 随着汽车技术水平的不断提高,载重车辆行驶的速度越来越快,交通越来越便捷,但同时道路交通事故给人民带来的伤害也越来越大.其中,一部分道路交通事故是由于载重车辆轮胎在高速重载情况下突然失效造成的.因此,研究载重车辆轮胎的力学特性,进行有限元失效仿真研究对提高交通安全具有重要意义.作者主要针对载重车辆轮胎在高速和重载条件下出现的失效形式,研究载重车辆轮胎的力学特性并进行有限元失效仿真研究与分析,获得载重车辆轮胎在不同压力场和温度场下的应力、应变分布状况,最后对轮胎的综合应力、应变分布状况进行了较为深入的分析研究,并对轮胎的寿命进行了预测,为进一步进行子午线轮胎的动态接触分析和结构优化设计奠定了理论基础[1,2].1 载重车辆轮胎主要失效形式载重车辆轮胎大部分用于专业运输系统,承载重,经常在较差路面上行驶.在高速和重载的工况下,常见的失效形式有:①轮胎胎面磨损,包括正常和异常磨损;②轮胎结构性损坏,包括因轮胎使用不当造成的结构性损坏和因车辆底盘技术状况不良造成的结构性损坏.前者表现为轮胎胎体断线穿洞破裂、帘线松散脱胶、线层与面胶脱离等失效形式;后者表现为极度异常磨损、机械擦伤或划伤等失效形式.损坏原因主要有:①当载重车辆速度过高或第4期齐晓杰等:基于ANSYS 的载重车辆轮胎失效仿真研究负荷过大时,轮胎所受载荷也急剧增大,致使轮胎内帘布层之间、帘布层与橡胶之间、内胎和外胎之间的磨损加剧,热量增多,温度升高.而橡胶在高温下的抗拉强度、耐磨性和粘结力均显著降低,最终造成轮胎的结构性损坏;②载重车辆轮胎运营里程过长又没有及时进行换位保养,轮胎经常处以单方向与路面摩擦,极易造成轮胎的不均匀磨损.2 载重车辆轮胎失效仿真研究与分析1)轮胎三维实体模型的建立及模型导入选用典型规格的10100R20载重子午线轮胎作为载体进行建模分析.构建轮胎模型主要使用拉伸、实体化、阵列、环形折弯、镜像、复制特征等工具,轮胎与地面装配模型如图1所示.ANSYS 在默认的情况下是不能直接对Pr o /E 中的pat 及as m 文件进行直接转换的,必须通过以下对ANSYS 设置连接过程进行激活模块:鼠标点击“开始→程序→ANSYS8.0→U tilities →ANS_ADM I N ”,选择configurati on op ti ons →OK,接下来的对话框顺序选取.Configurati on Connecti on f or Pr o /E →OK,AN 2SYSMulti physics &W I N 32→OK,完成后ANSYS 提示已在自己的安装目录中成功生成config anscon 文件,记下config anscon 的路径.在接下来出现的对话框中“Pr o /Engireer I nstallati on path ”选项后输入Pr o /E 的起始安装路径如“C:\Pr o -gra m Files \p r oe W ildfire 3.0”,“Language used with Pr o /Engi 2neer ”选项用默认的usascii,点击OK .出现对话框提示在Pr o /E 目录下建立了一个p r otk .dat 文件,点击确定完成配置.然后将config anscon 拷贝到Pr o /E 的安装路径.最后,将ANSYS 的路径追加到path,如“C:\Pr ogra mFiles \Ansys I nc \Shared Files \bin \intel ”运行Pr o /E,在Pr o /E 软件的工具菜单后面出现了ANSYS8.0,点击Pr o /E 中的ANSYS8.0按钮(如图2所示),子午线轮胎便导入ANSYS 中[3~6].图1 子午线轮胎三维模型图2 将子午线轮胎模型导入ANSYS 软件2)子午线轮胎的有限元失效仿真研究1)网格划分为精确分析接触区域的应力-应变场,对可能接触的胎圈区域进行网格细分,并且接地部分的网格划分得更细,划分密度为10.由平面网格旋转拉伸生成3/4三维模型,如图3所示.图3 网格划分2)模型特殊处理轮辋与胎圈的过盈配合:轮辋与胎圈是过盈配合,考虑到轮辋定位后的实际位置与定位前的胎圈是相交的,本模型先将轮辋沿轮胎轴线移动-40mm ,使轮辋与胎圈有一定间隙,再给轮辋定义一个沿轴向的位移(40mm ),通过定义接触边界条件来真实地模拟轮辋与胎圈的配合.在考虑轮辋的约束时,通过将钢丝圈上所有节点的6个自由度全部约束;当考虑路面对轮胎的约束时,将模型中的目标面(即地面)的所有自由度约束.试验中的下沉量从轮胎充气后的胎面位置开始计算,即充气过程中路面对轮胎没有约束.由于预先不知道充气后胎面的位置,为了真实地模拟试验,本模型将路面从胎面的初始位置沿径向向外移动(大于估计的胎面径向位移量),保证充气过程中路面对轮胎没有约束.3)边界条件的设定通过直接约束法解决接触问题.将轮辋和路面定义为刚体,给定轮辋沿轴向的位移和路面移向轴心的位移,将可能与轮辋、路面发生接触的单元定义为可变形体.・95・车辆与动力技术2008年4)载荷工况的设定对模型先后施加下述5种载荷:①轮辋定位载荷:通过轮辋沿轴向(X方向)的位移来实现;②充气压力:施加在轮胎的内表面;③静负荷:通过路面相对于轮胎轴心的下沉量来实现;④自由滚动:通过轮胎的扭矩控制;⑤稳态滚动:通过轮胎的转速控制.模拟的试验条件:充气压力为0184MPa、静负荷为25000kg(对应路面的下沉量为28mm),充气压力为0125MPa、静负荷为2940kg(对应路面的下沉量为10mm)两种情况.静负荷是充气后加上去的,即路面的下沉量是从轮胎充气后的位置计算的.滚动工况通过施加转矩来实现,在轮胎的中心轴处左右两侧端面约束X方向位移为0,对地面施加固定约束.在轮胎上施加实际工作时承载的重量40kg,在轮心处内表面节点施加恒定转速1313rad/s.考虑到轮胎与地面的摩擦作用,静摩擦系数取为0.7[7,8].首先建立起轮胎与地面的接触模型,定义接触对过程如图4所示.约束的建立及加载过程如图5、6所示.施加对称载荷的过程如图7所示.轮胎与轮辋间的接触换热用热-耦合分析方法来完成,热-耦合分析方法通过施加速度边界条件和施加热边界条件来实现.设置过程如下图8所示.图4 接触对的建立图5 建立约束(左)和施加均布载荷(右)图6 施加静载荷(左)施加扭矩(右)图7 施加对称载荷图8 施加速度(左)和热(右)边界条件3 仿真结论分析1)不同压力场下应力和应变静止工况下不同压力场的变形如图9所示,自由滚动工况下不同压力场的变形如图10所示,静止工况下不同压力场的应力如图11所示,自由滚动工况下不同压力场的应力如图12所示,轮胎不同层之间的应力关系如图13所示.图9 静止工况下的轮胎变形・6・第4期齐晓杰等:基于ANSYS的载重车辆轮胎失效仿真研究图10 自由滚动工况下的轮胎变形图11 静止工况下的接触应力图12 自由滚动工况下的接触应力图13 轮胎不同层间的应力 2)轮胎的应力关系分析由图可以分析出,在胎冠部中央张力最大,当胎体的约束程度提高时,胎体内的张力逐渐减小,而带束内的帘线所承受的力不断增大.分析结果表明,带束层受力的基本状况主要取决于充气压力,静负荷的作用主要在接地区里影响带束层的受力状况,而钢丝圈的应力几乎不受影响.3)整体分析由分析得到的结果可以发现施加静态载荷后,轮胎接地面内最大值并不出现在接地面中心,而是偏离中心节点.通过胎面位移随充气压力的变化关系可以看出,充气开始阶段胎面位移有波动,随着充气压力增大,胎面位移量增大,且与充气压力基本呈线性关系.4)接地区域分析由图可以看出,垂直位移主要集中在与地面接触的节点上,随着下沉量的增大,接地区域扩大,接触压力增大,并且接地区域近似为1/4椭圆形.随着下沉量增大,接触反力增大,并与下沉量近似呈线性关系.在一定下沉量条件下,随着充气压力提高,路面接触反力增大,并且两者基本呈线性关系.从轮胎断面变形前后的对照图中,可以看到带束层及胎体帘线产生了变形.接地区域轮胎中应变分布图显示了在带束层边缘和胎圈外侧应变较大,由此可以预测轮胎的滚动过程中,由于橡胶存在滞后损失,使这两个部位容易生热,并且散热较困难,致使温度较高.这与轮胎在实际工作过程中,经常出现肩空、肩裂和胎圈爆破是一致的.4 子午线轮胎的疲劳寿命预测通过以上有限元分析得到的变化规律,可以直观的观察与轮胎寿命相关的负荷、压力、速度和温度的变化趋势,从而可以预测出轮胎的使用寿命.当轮胎受随机载荷作用时,其疲劳寿命不能是各循环应力对应寿命的简单迭加,而需要运用一定的累积损伤法则将各应力引起的损伤累加起来,进行寿命计算.本研究采用M iner 线性累积损伤法则计算累积损伤寿命N ,其具体形式如下:N =∑mi =1n i /∑mi =1n iN i,(1)式中 n i 为每次运行中某种循环的循环次数;N i 为根据该循环的应力幅值考虑平均应力的影响,m 为统计出的应力循环种类数.汽车轮胎行驶过程中承受多种载荷的作用,但总的说来可以分为径向载荷和弯曲载荷两种,根据以往的轮胎试验,轮胎因弯曲疲劳造成破坏的比例很高,并且大多数同类型轮胎的疲劳裂纹都产生在轮辐螺母座附近,而径向疲劳造成破坏的比例相对较低,所以选择轮辐螺母座处在弯曲工况下进行寿命计算.在轮胎疲劳试验中,每个循环的最大主应力及最小主应力都分别有它们的最大值和最小值,利用公式(2)可求出当量应力在一个循环周期的幅值σra 和平均值σr m .σra =σ21a +σ22a -σ1a σ2a ,σr m =σ21m +σ22m -σ1m σ2m ,(2)式中 σ1a 为最大主应力在一个循环周期内的幅值;σ2a 为最小主应力在一个循环周期内的幅值;σ1m・16・车辆与动力技术2008年为最大主应力在一个循环周期内的平均值;σ2m为最小主应力在一个循环周期内的平均值.本研究通过对子午线轮胎进行了有限元失效仿真分析,当给轮胎施加25000N垂直载荷和8232 N侧向载荷时,得最大主应力平均值σ1m=35413 MPa,最大主应力幅值σ1a=63183MPa,最小主应力平均值σ2m=186164MPa,最小主应力幅值σ2a =86164MPa.将这些数据代入公式(2),可求当量应力幅值σra=77179MPa,当量应力平均值σ= 306198Mpa.5 结束语利用Pr o/E的强大建模功能建立了载重车辆轮胎三维模型,通过专用的模型数据接口技术将模型导入到ANSYS软件中进行有限元研究与分析,模拟了轮胎模型的受力特点并对轮胎的使用寿命预测进行了探讨,为进一步进行轮胎动态分析和结构优化设计制造奠定了理论基础.由于研究部分相关参数是参考典型规格的轮胎取得的,研究结论在实际应用过程中可能会有所偏差,应根据实际情况详加考虑.参考文献:[1] 崔慧萍,陈 丽.载重汽车轮胎的使用现状及今后的发展[J].橡胶科技市场,2006(22):4-5.[2] 王洪礼,任 炜,乔 宇.汽车轮胎动力学特性研究[J].机械强度,2004(3):345-348.[3] 李 科,傅洪芳.改进花纹设计轻型载重轮胎高速性能[J].轮胎工业,2001(3):131-134.[4] 恒盛杰资讯.Pr o/E NGI N EER中文野火版从入门到精通[M].北京:中国青年出版社,2007.[5] 张许红,赵 红,景世庭.7.50_1614PR混合花纹轻载轮胎的结构设计[J].轮胎工业,2005(4):206-208.[6] 吴小国,秦东晨.Pr o/E与ANSYS接口[J].现代制造技术与装备,2007(1):19-20.[7] 俞 淇,戴元坎,张 凯.静负荷下轮胎接地压力分布测试的研究[J].轮胎工业,1999,20(1):47-49.[8] 闫相桥.轮胎结构有限元分析应用于载重子午胎胎体反包高度的优选[J].复合材料学报,2001,15(4):4-9.(上接第53页)通过表2可知,有限元分析结果与试验分析能很好的对应,该有限元模型的建立具有一定的精度,有限元模型能很好的模拟白车身进行理论分析,模拟分析的结果能较为精确的反映白车身的结构特性.4 结 论白车身的一阶扭转频率值为2919Hz,一阶弯曲模态频率值为4615Hz,一般同类车一阶扭转频率值为25Hz左右,一阶弯曲频率为40Hz左右,因此可以认为该车具有较好的刚度性能,同时具有一定的优化设计空间.所建立的模态试验方法对同类车的开发具有实际价值和指导意义.参考文献:[1] 高云凯.汽车车身结构分析[M].北京:北京理工大学出版社,2006.[2] 蓝晓理.轿车车身的低阶模态分析[D].长春:吉林工业大学,2000.[3] 师汉民,谌 刚,吴 雅.机械振动系统[M].武汉:华中理工大学出版社,1992.[4] 刘生涛,杨凤鹏.精通Ansys[M].北京:清华大学出版社,2002.[5] 李 昊,陈 剑,赵旭东,等.商务车车身地板动态特性的试验研究[J].合肥工业大学学报,2004,27(11):1460-1463.[6] 刘焕广.轿车白车身结构有限元及其试验分析[J].合肥工业大学学报,2007,30(12):1615-1619. [7] 曹树谦,张文德,萧龙翔.振动结构模态分析[M].天津:天津大学出版社,2001.・26・。
货车车轮踏面损伤标准的探讨
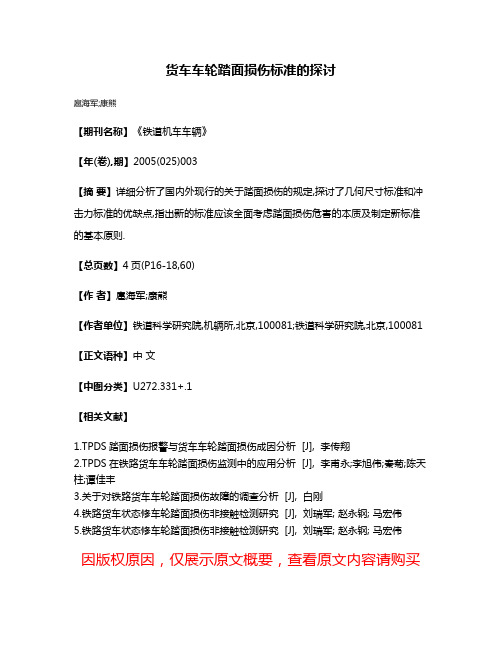
货车车轮踏面损伤标准的探讨
扈海军;康熊
【期刊名称】《铁道机车车辆》
【年(卷),期】2005(025)003
【摘要】详细分析了国内外现行的关于踏面损伤的规定,探讨了几何尺寸标准和冲击力标准的优缺点,指出新的标准应该全面考虑踏面损伤危害的本质及制定新标准的基本原则.
【总页数】4页(P16-18,60)
【作者】扈海军;康熊
【作者单位】铁道科学研究院,机辆所,北京,100081;铁道科学研究院,北京,100081【正文语种】中文
【中图分类】U272.331+.1
【相关文献】
1.TPDS踏面损伤报警与货车车轮踏面损伤成因分析 [J], 李传翔
2.TPDS在铁路货车车轮踏面损伤监测中的应用分析 [J], 李甫永;李旭伟;秦菊;陈天柱;谭佳丰
3.关于对铁路货车车轮踏面损伤故障的调查分析 [J], 白刚
4.铁路货车状态修车轮踏面损伤非接触检测研究 [J], 刘瑞军; 赵永钢; 马宏伟
5.铁路货车状态修车轮踏面损伤非接触检测研究 [J], 刘瑞军; 赵永钢; 马宏伟
因版权原因,仅展示原文概要,查看原文内容请购买。
货车轮对踏面擦伤浅析

货车轮对踏面擦伤浅析作者:于祥行马新锋来源:《魅力中国》2018年第40期摘要:为适应当代铁路运输量的迅速增加,铁路货车大大提高了运载量和运载速度。
同时,货车轮对的踏面擦伤问题更加明显。
本文简要分析了轮对踏面损伤的原因和应对策略。
关键词:铁路货车;提速;踏面损伤货车踏面故障是车辆运行时最为多见的故障,其损伤主要表现为踏面的擦伤及剥离。
车轮踏面擦伤后,车轮的形状受到了破坏,其正常运动轨迹也发生了变化。
故障车辆在行车时会对轨道形成周期性冲击。
随着车轮擦伤深度的增加,轮轨间的动作用力将急剧增大,车轴、轴承等簧下部件的受力条件亦更加恶劣,这将极大地降低车轮、车轴、轴承、钢轨的使用寿命,加速车辆轴承及轨道零部件的疲劳耗损,特别是在高速重载的运行条件下,这种高强度冲击载荷的破坏性更强,同时对车辆的舒适性也有一定影响。
一、轮对擦伤的原因(一)列车运行中制动力过大在车辆实际运行过程中,制动力过大有如下原因。
一是车辆紧急制动。
二是闸瓦厚度不同。
同一辆车上各闸瓦厚度不相同,从而造成这几个闸瓦壓力过大而引起踏面被抱住。
三是列车管系漏泄量过大。
四是遇有特殊情况司机操纵不当采取强行紧急制动,因制动机性能差异,部分车辆未充分缓解带闸强行开车,易造成轮对踏面擦伤。
(二)列车本身设计和质量问题一是在空车制动时,装有手动空重车调整装置车辆的制动力要大于装有自动空重车调整装置的车辆,空重车调整转换塞门导架损坏,手柄在空车位,而转换塞门实际在重车位,导致空车时制动力过大,造成车轮擦伤。
轮对承受的闸瓦压力大,在制动时易抱死车轮产生滑行从而导致轮对踏面擦伤。
二是一部分车辆的安全阀损坏,空气压力达到190kPa时不能排风,安全阀失去作用,造成车轮擦伤。
这种情况与车辆定检质量有关。
二、解决办法(一)逐步改造或淘汰现有手动空重车调整装置,全部采用自动空重车调整装置因为自动空重车调不仅杜绝手动人为忘调、错调现象发生,更主要的是,列车运行制动时有较均匀的制动缸压力范围,能达到理想的制动效果。
- 1、下载文档前请自行甄别文档内容的完整性,平台不提供额外的编辑、内容补充、找答案等附加服务。
- 2、"仅部分预览"的文档,不可在线预览部分如存在完整性等问题,可反馈申请退款(可完整预览的文档不适用该条件!)。
- 3、如文档侵犯您的权益,请联系客服反馈,我们会尽快为您处理(人工客服工作时间:9:00-18:30)。
货车车轮踏面损伤温度场与应力场的有限元分析
XXXX 专业XX 班XXXX 学号 姓名
摘 要:在铁路运输不断提速及重载的情况下,采用踏面制动方式制动的货车车轮承受着强摩擦、高热载荷及大轮轨作用力的恶劣条件,在反复制动时,车轮将产生热疲劳损伤而造成车轮的失效破坏。
本文根据货车的实际工作条件,对21t 轴重、速度为120 km/h 的货车车轮在一次紧急制动过程中的温度场和应力场分布进行了有限元模拟,分析了温度场和应力场的分布与货车车轮踏面损伤之间的关系。
研究结果表明,在整个制动过程中,温度与热应力的最高点都集中在闸瓦与车轮的接触摩擦面部位,且随着制动过程的温度不断上升,达到峰值后又缓缓降低;车轮的温度是由踏面向轮轴位置逐渐降低的,越靠近轮轴,温度与热应力值越低;制动结束后,车轮内部的温度高于踏面的温度,最大应力产生在车轮踏面之下。
关键词:货车车轮;温度场;应力场;有限元模拟;热疲劳损伤
FEA of Temperature and Stress Field Distribution on the Touching Area
of Freight Train Wheel
1
引言
提速和重载是提高铁路运输能力的有效措施,已成为铁路货车发展的趋势。
我国货车目前制动方式仍然是踏面制动,列车车轮在强摩擦、高热负荷以及大轮轨作用力等恶劣条件下工作。
列车在制动过程中,动能逐渐转变为制动装置产生的热能,对于采用踏面制动的高速重载铁路货车,这样的制动过程非常严苛,由此产生的热疲劳损伤已成为车轮失效的主要形式之一。
车轮经过多次制动后,会在车轮与铁轨的接触踏面上产生均匀分布的横向裂纹,周围会伴随剥离、掉块等现象。
因此,在国家倡导货运列车提速的前提下,现有的踏面制动正面临的严峻的挑战,也对车轮的抗热损伤能力和疲劳寿命提出了更高的要求。
由于热损伤和疲劳损伤都与车轮在紧急制动过程中的温度场和应力场分布有密切的关系,本文以21t 轴重、120km/h 的货运列车车轮为研究对象,拟结合具体货车车轮的结构,利用建模软件对其建模,通过有限元模拟其紧急制动过程中的温度场和应力场分布,并针对实际踏面损伤情况对其模拟准确性给予评估,为进一步研究车轮的热疲劳损伤提供技术参考。
2
车轮紧急制动温度场模拟
货车车轮的轮径为840mm ,轮辋内侧内径为710mm ,轮毂孔直径为170mm ,轮辋外径为273mm ,理论重量351 kg 。
车轮材料为CL60,材料各项物热参数如下:弹性模量E =2.05×105 MPa ,泊松比μ=0.3,密度ρ=7800 kg/m 3,热膨胀系数α=10.3×10-6℃-1,比热容c=470 J/(kg ·K),热传导率k =51W/(m ·K),对流换热系数h=40W/(m 2·K)。
由于车轮是周向对称的结构,在考虑热流输入车轮踏面和车轮的热耗散时,可以认为在车轮的周向是无变化的,即温度场是轴对称的,因此,选取车轮的1/18进行分析,即取周向20°的模型。
2.1 热流密度的确定:
为简化问题,可以认为在高速行进过程中,踏面的温度在周向是均匀分布的,且热流输入也是均匀的。
初速度为120km/h 时,各项制动参数如表1所示。
表1 制动参数
制动初速度(km/h )
轴重(t ) 减速度(m/s2) 制动距离(m ) 闸瓦压力(kN ) 摩擦系数 热量分配系数 120
21
0.556
1000
21
0.278
0.91
根据热流密度计算公式
f
d S t p t q )
()(η
=
其中:f S ——闸瓦在踏面上扫过的面积;η——输入到车轮的热量分配系数;)(t p d ——热生成功率。
计算得热流密度 )/(838.145.889)
()(2m kW t S t p t q f
d -≈=η
[1] 考虑到车轮周围的空气流动状态较为简单,本模拟中,取对流换热系数α=40W/(m 2·K),并忽略车轮的热辐射影响。
本次计算对车轮进行一次紧急制动,并在制动结束后空冷10分钟。
2.2 模型的网格划分、约束、对流换热面的确定
将在SolidWorks 中建好的模型导入ANSYS 软件,进行网格划分。
在热分析中选取Solid90单元,应力分析选择Solid186单元,网格大小8mm ,踏面附近的网格为6mm 。
对于热分析,选取车轮的踏面为热流输入面,选取与空气接触的面,设置为对流换热面。
在制动盘的剖切面上施加周向对称耦合。
对模型施加载荷,输入载荷命令流,设置输出每个子步选项,并开始计算。
2.3 计算结果及分析
图5、图6分别显示了制动结束时刻和制动结束空冷10分钟后的温度场分布。
制动结束时刻的最高温度为224℃,冷却10分钟后,最高温度为97.5℃。
分别取踏面上如图7所示的位置的节点,读取其制动过程中的最高温度,并绘制其制动过程中的节点温度变化曲线,如图8所示。
分别取车轮径向上如图9所示的位置的节点,读取其制动过程中的最高温度,并绘制其制动过程中的节点温度变化曲线,如图10所示。
综合以上的模拟结果,经过分析后可以得到如下结论:
1)在整个制动过程中,温度的最高点都集中在闸瓦与车轮的接触摩擦面部位;
2)随着制动过程的进行,货车的运行速度也在下降,闸瓦与车轮踏面的摩擦剧烈程度也发生着变化,导致制动过程的温度不是一直上升,而是达到峰值后缓缓降低;
3)踏面上,只有摩擦面与闸瓦接触的部位温度较高,其余部分的温度较低;
4)车轮的温度是由踏面向轮轴位置逐渐降低的,越靠近轮轴位置,轮的温度越低,出现最高温度的时间也越晚。
3 车轮紧急制动应力场模拟
1)输入载荷的确定
对于货车车轮在紧急制动过程中应力场的模拟,可以利用间接偶合法,将紧急制动全程车轮的温度场的模拟结果作为应力场的载荷,施加在模型的所有节点上,利用命令流,调用温度场计算结果文件(*.rth 文件)中的节点温度值到结构分析中,并在结构分析时设置与热分析相对应的每一个载荷步,以确保耦合的正确性。
2)结构约束的施加
由于车轮与车轴是压装的,属于过盈装配,因此需要在轮毂的内圈施加沿轴向和径向的零位移约束,即全约束。
由于模型选取的是周角对称的1/18模型,需要在剖切面上施加对称耦合,以满足边界连续的条件。
结构约束示意图如图11。
3)计算结果及分析
图12、图13分别显示了制动结束时刻和制动结束空冷10分钟后的应力场分布。
制动结束时刻的最大应力为370MPa ,冷却10分钟后,最大应力为126MPa 。
图14显示了制动过程中车轮中有最大应力值时刻(制动开始后的第25秒)的应力分布云图,最大应力值为460MPa 。
分别取如图15所示的位置的节点,读取其制动过程中的最大热应力,并绘制其制动过程中的热应力变化曲线,如图16所示。
综合以上的模拟结果,经过分析后可以得到如下结论:
1)整个制动过程中,随着踏面温度的迅速升高,成为车轮的最高温部位,有强烈的热膨胀,因此此过程应力值最大的点都在闸瓦与车轮的接触摩擦面部位;
5
1 2
4 3
1 2 4 5
3 5
4
3 2 1
1 2
3
4 5
S t r e s s
2)制动过程的进行,车轮踏面的热量逐渐传入车轮内部,使得踏面温度与轮辋和轮毂温度的差值缓缓减小,从而制动结束时,踏面的温度迅速下降,而使内部温度高于踏面,最大应力部位产生在车轮踏面之下;
3)踏面的最大热应力随着与内部的温度差的减小,也并不是一直递增的,而是达到峰值后缓缓下降;
4)踏面附近较大的应力为周向的拉应力。
4 结论
通过对上述车轮紧急制动过程中的温度场和应力场的分析,可以看出车轮在制动过程中会由于温度变化产生较大的热应力,使得踏面附近极易发生屈服,而车轮原本存在的加工缺陷和热处理留下的参与应力与之相互作用,会促进热裂纹的萌生。
在短时间的连续制动情况下,踏面会来不及降温而反复接受摩擦,使得温度不断上升,踏面附近由原本的无应力或残余的周向拉应力变为受到周向的压应力,而制动结束,温度降低后,踏面附近则会恢复到残余的周向拉应力状态,再次制动又会使周向受拉,如此往复循环,会产生低周疲劳,是车轮在服役时最严苛的服役状态,极易产生疲劳裂纹。
因此可以推断,在货车的制动过程中,由于其温度场和应力场的分布特点,应该极力避免短时多次的快速制动[2]。
参考文献
[1] 郑红霞, 李智令, 刘玉军. 紧急制动下货车车轮温度场和应力场的数值仿真研究[J], 鲁
东大学学报, 2008, 24 (4) : 367—371.
[2] 彭莉, 谢基龙, 郑红霞. 大秦线全程制动条件下货车车轮温度及热应力场的数值模拟[J], 北京交通大学学报, 2007, 31(1) : 37—40.。