螺距补偿机理
brother系统螺距补偿方法
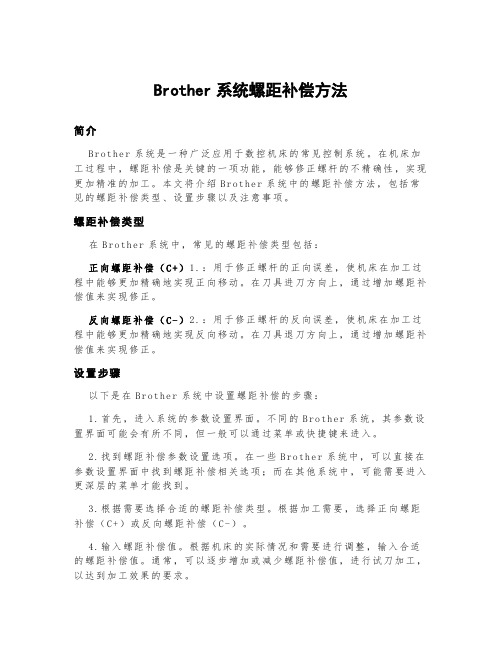
Brother系统螺距补偿方法简介B r ot he r系统是一种广泛应用于数控机床的常见控制系统。
在机床加工过程中,螺距补偿是关键的一项功能,能够修正螺杆的不精确性,实现更加精准的加工。
本文将介绍Br ot he r系统中的螺距补偿方法,包括常见的螺距补偿类型、设置步骤以及注意事项。
螺距补偿类型在B ro th er系统中,常见的螺距补偿类型包括:正向螺距补偿(C+)1.:用于修正螺杆的正向误差,使机床在加工过程中能够更加精确地实现正向移动。
在刀具进刀方向上,通过增加螺距补偿值来实现修正。
反向螺距补偿(C-)2.:用于修正螺杆的反向误差,使机床在加工过程中能够更加精确地实现反向移动。
在刀具退刀方向上,通过增加螺距补偿值来实现修正。
设置步骤以下是在Br ot he r系统中设置螺距补偿的步骤:1.首先,进入系统的参数设置界面。
不同的Br ot he r系统,其参数设置界面可能会有所不同,但一般可以通过菜单或快捷键来进入。
2.找到螺距补偿参数设置选项。
在一些B ro th er系统中,可以直接在参数设置界面中找到螺距补偿相关选项;而在其他系统中,可能需要进入更深层的菜单才能找到。
3.根据需要选择合适的螺距补偿类型。
根据加工需要,选择正向螺距补偿(C+)或反向螺距补偿(C-)。
4.输入螺距补偿值。
根据机床的实际情况和需要进行调整,输入合适的螺距补偿值。
通常,可以逐步增加或减少螺距补偿值,进行试刀加工,以达到加工效果的要求。
5.完成设置后,保存并退出参数设置界面。
注意事项在使用B ro th er系统进行螺距补偿时,需要注意以下事项:1.在设置螺距补偿值时,应根据实际情况进行合理调整。
如果螺距补偿值过大或过小,可能会导致加工精度下降或机床负载过大,从而影响加工质量和机床寿命。
2.在进行螺距补偿时,应定期检查螺距补偿值的准确性。
由于机床使用时间的增加,螺杆的磨损程度可能会发生变化,因此需要及时调整螺距补偿值,保证加工的准确性。
螺距补偿机理

13
二、螺距误差补偿原理
距补偿误差表中计算出实际的补偿值,对指令位置 进行补偿,产生实际输出值控制伺服电机。如图3 所示,数控系统以机床零点为基准,在不同的指令 位置,按补偿表中的误差值进行补偿。数控系统在 每段数据插补过程中均进行误差补偿,以获得最高 精度。
14
二、螺距误差补偿原理
实现过程和步骤如下 :
20
螺距误差补偿是按轴进行的。针对每一个轴可以设 置每个轴的螺距误差补偿。主轴不设置。
21
n=1 螺 距 误 差 补 偿 程 序 图 n++ Xn<X<Xn-1
线性插值计算出△Xn值 X=Xn+△Xn
以数控机床 纵向(X轴)进给 丝杠为例,设:X 表示数控装置发 出的X轴进给坐标 值,Xn表示数控机 床某轴滚珠丝杠 的全行程上选取 的各指令位置点 的坐标值,△Xn表 示用激光干涉仪 测得的各指令位 置点的螺距误差。
22
23
谢谢!
24
5
一、螺距误差产生的原因
3. 机床装配过程中,由于丝杠轴线与机床导轨平行 度的误差引起的机床目标值偏差。 螺距误差补偿是将机床实际移动的距离与指令移 动的距离之差,通过调整数控系统的参数增减指令 值的脉冲数,实现机床实际移动距离与指令值相接 近,以提高机床的定位精度。螺距误差补偿只对机 床补偿段起作用,在数控系统允许的范围内补偿将 起到补偿作用。
1
• 在数控机床上正确安装高精度位移测量装置; • 在整个行程上 , 每隔一定距离取一个位置点 作为补偿点; • 记录运动到补偿点的实际精确位置; • 将各点处的误差标出 , 形成在不同的指令位 置处的误差表; • 多次测量 , 取平均值; • 依 “补偿值 =数控命令值-实际位置值 ”的 公式计算各点的螺距误差,并将各点处的误差 标出,形成在不同指令位置处的误差表,并将该 表输入数控系统 , 系统按此表进行补偿。
数控系统中螺距补偿的原理与设计

数控系统中螺距补偿的原理与设计陈刚;羌铃铃【摘要】Because the manufacturing and instal ation errors and wear oflLong ̄ferm use exist in the lead of NC machine tool,its ac ̄tual moving position is made different from its expected moving posifion. The article puts forward the uni ̄direction and bi ̄direction compensation in numeric control er,introduces the principle of lead ̄screw compensation, including the uni ̄direction and bi ̄direction compensation,then gives out one method which is used to design uni ̄direction and bi ̄direction compensation and edits one program which is used to test whether the bi  ̄direction compensation is valid or not. The result of experiment shows the lead ̄screw error exist ̄ing in numeric control er is solved.%由于数控机床的丝杠在制造、安装上存在误差以及长期使用造成的磨损,导致螺距实际移动值与预期设定值之间存在差异。
提出了螺距误差的单向补偿方法和双向补偿方法。
介绍了螺距补偿的原理,包括单向补偿方法、双向补偿方法的原理;提供了一种实现单向补偿、双向补偿的设计方案;编写了简单的零件位置移动程序来测试双向补偿方法是否生效。
FANUC数控系统螺距误差补偿功能.

FANUC数控系统螺距误差补偿功能数控机床的直线轴精度表现在轴进给上主要由三项精度:反向间隙、定位精度和重复定位精度,其中反向间隙、重复定位精度可以通过机械装置的调整来实现,而定位精度在很大程度上取决于直线轴传动链中滚珠丝杠的螺距制造精度。
在数控机床生产制造及加工应用中,在调整好机床反向间隙、重复定位精度后,要减小定位误差,用数控系统的螺距误差螺距补偿功能是最节约成本且直接有效的方法。
FANUC数控系统已广泛应用在数控机床上,其螺距误差补偿功能有一定的典型性。
螺距补偿原理是将机械参考点返回后的位置作为螺距补偿原点,CNC系统以设定在螺距误差补偿参数中的螺距补偿量和CNC移动指令,综合控制伺服轴的移动量,补偿丝杠的螺距误差。
1 螺距误差补偿前的准备工作回参考点后,编程控制需要螺距误差补偿的轴,从参考点或机床机械位置某一点间歇移动若干个等距检测点,用激光干涉仪等检测计量仪器检测出各点的定位误差。
检测点数量可根据机床的工作长度自设。
2 设定螺距误差补偿参数打开参数开关在MDI方式下设置参数PWE=1,系统出现1000报警,同时按CAN和RESET键清除报警。
⑴参考点的螺距误差补偿点号码参数X轴参数No.1000Z轴参数No.2000⑵螺距误差补偿倍率参数参数No.0011的PML1,PML2。
.PML2 PML1 倍率( 0 0 31,0 1 32,1 0 34,1 1 38)设定的螺距补偿值,乘上该倍率,即为输出值.⑶螺距误差补偿点间隔X轴参数No.756Z轴参数No.757螺距误差补偿点为等间隔,设定范围从0到999999999。
一般设定单位是0.001毫米。
⑷螺距补偿点数目各轴从0到127共128个螺距补偿点⑸螺距补偿量及螺距补偿点的号X轴参数No.(1001+螺距补偿点号)Z轴参数No.(2001+螺距补偿点号)每个螺距补偿点螺距补偿量的范围为(-7)~(+7)乘以螺距补偿倍率。
负侧最远补偿点的号=原点补偿点-(负侧的机床长/补偿点间隔)+1正侧最远补偿点的号=原点补偿点+(正侧的机床长/补偿点间隔)3设定好螺距补偿参数后,在MDI方式下,设置参数PWE=0,关闭参数写状态。
双轴螺距误差补偿课件

03
双轴螺距误差补偿的步骤
Chapter
误差测量
误差测量是双轴螺距误差补偿的首要步骤,通过高精度 的测量设备对双轴工作台的实际位置进行测量,获取误 差数据。 测量过程中需要保证测量设备的精度和稳定性,以确保 测量结果的准确性。
测量时需要选取多个位置和角度进行测量,以全面了解 双轴工作台的误差分布情况。
率和安全性。
05
双轴螺距误差补偿的未来发展
Chapter
新技术应用
01
02
03
Hale Waihona Puke 人工智能技术利用人工智能算法对双轴 螺距误差进行实时监测和 补偿,提高加工精度和效 率。
传感器技术
研发高精度、高稳定性的 传感器,用于实时监测双 轴螺距误差,提高补偿精 度。
云计算技术
通过云计算技术实现多轴 联动误差补偿的远程监控 和管理,提高生产效率。
误差建模
在获取到误差数据后,需要对误差进行建模,即分析误差的来源和特性,建立误差 模型。
误差建模过程中需要考虑多种因素对双轴工作台的影响,如温度、湿度、机械磨损 等。
误差模型建立后,可以通过软件仿真或实际测试对模型进行验证和修正,以确保模 型的准确性和可靠性。
补偿实施
补偿实施是根据误差模型对双 轴工作台进行补偿的过程,通 常采用软件补偿的方式进行。
详细描述
软件补偿法主要通过在数控程序中加入补偿指令,对机床的运动轨迹进行修正, 从而补偿螺距误差。这种方法可以在不停机的情况下进行补偿,且对机床性能无 影响,但需要精确的测量和计算,且补偿效果受限于机床的动态特性。
混合补偿法
总结词
结合硬件和软件补偿法的优点进行螺距误差补偿。
详细描述
混合补偿法综合了硬件和软件补偿法的优点,既可以通过调整或更换机械部件来改变机床的几何误差,又可以通 过修改数控程序来修正运动轨迹。这种方法可以在不停机的情况下进行补偿,且补偿效果明显,但实现起来较为 复杂,需要精确的测量和计算,以及对机床性能的深入了解。
9.1 螺距误差补偿[共2页]
![9.1 螺距误差补偿[共2页]](https://img.taocdn.com/s3/m/9edc6295a8956bec0975e3f8.png)
第9章系统补偿功能与SIMODRIVE611D驱动优化
机床在对工件进行加工的过程中,由于测量系统、力的传递过程中产生的误差、机床自身磨损或装配工艺问题的影响,加工工件的轮廓会偏离理想的几何曲线,导致加工工件产品质量的下降。
特别是在加工大型的工件时,由于温度和机械力的影响,加工精度损失更为严重。
因而在机床出厂前,需要进行一定的误差补偿。
螺距误差补偿和反向间隙补偿是两种最常见的补偿方式,还有温度补偿、垂直度补偿、跟随误差补偿以及摩擦补偿也比较常见。
另外,在机械传动结构良好的情况下,要使机械系统与电气系统达到更加良好的匹配,需要通过驱动优化来实现。
9.1 螺距误差补偿
螺距误差的补偿是按坐标轴来进行的,轴的补偿曲线如图9-1所示。
图9-1 轴的补偿曲线
激活误差补偿需设定以下相关机床参数。
① MD 38000 轴最大误差补偿点数。
根据该机床的特点,X轴螺距误差参数补偿点数为50,即MD 38000 [0 AX1] =50;Z轴螺距误差补偿点数为100,即MD 38000 [0 AX2] =100。
参数设定好后,系统自动产生相应轴的补偿文件,补偿文件存放在目录/NC-ACTIVE-DATA/Meas-System-err-comp下。
可以修改每轴的补偿点数。
如果改变MD38000,系统会在下一次上电时重新对内存进行分配。
建议在修改该参数之前,备份已存在的零件加工程序、R 参数和刀具参数的驱动数据。
② MD32700螺距误差补偿使能。
MD32700=0 螺距补偿不生效,允许修改补偿文件。
数控机床螺距误差补偿原理及方法

数 控 机 床 螺 距 误 差 补 偿 原 理 及 方 法
李 晶 刘 国华
( 1 . 包头 职业 技术 学 院 网络信 息 中心 , 内蒙 古 包 头 0 1 4 0 3 0 ; 2 . 帕马( 上海 ) 机床 有 限公 司 , 上海 2 0 1 3 0 6) 摘 要: 数控 机床 的传 动机 构 一般 均为 滚珠 丝杠 副 , 滚珠 丝 杠副在 生产制造 和装 配过 程 中都 存在 一
2 0 1 3年 1 2月 第1 4卷 第 4期
包 头 职 业 技 术 学 院 学 报
J OU RNAL OF B AOT OU V 0C AT 1 0NAL & T E CHNI C AL CO L L E GE
De c e mbe r . 201 3 Vo 1 .1 4. No. 4
机 床 的定位精 度 和重 复 定 位 精 度 , 因 而极 大 地 提 高
为何使用全闭环系统还要进行螺距误差和反向间隙补偿

为何使用全闭环系统还要进行螺距误差和反向间隙补偿?
螺距补偿:意思上丝杠上存在误差通过数控系统功能进行补偿,实际上螺距误差补偿和很多因素都有关系,如机械的调整?机床轴的润滑?机械的热变形等?因此在做螺距误差补偿时候通
常先调整好机械使机械的重复运动时能达到最佳效果,然后机床轴预热(运动一段时间)然后进行螺距定位精度补偿。
这种情况的补偿通常效果比较理想。
闭环的补偿;由于闭环依靠闭环装置来检测,如:光栅尺,通常要做的工作先是拉尺,即校正尺安装后的读数与实际位置的一致,通常的做法采用激光干涉仪做外部检测,通过手动移动轴全程以尺反馈的读数与检测的读数比较,相应调整尺,使之与检测读数一致。
在尺经过调整后由于尺本身的材质原因在调整后其距离存在误差,这时候要通过螺距误差补偿来精确校正,闭环尺是一种闭环检测系统它的主要依靠依然离不开机械良好调整。
机械如果不到位,或存在很大的误差闭环效果也会有很大的影响。
反向间隙这个综合因素包含着丝杠反向间隙丝杠螺母间隙以及其它机械结构存在的反向误差,反向间隙依然和机械的良好调整依然无法分开,即如,某些机床结构中有斜铁也称镶条的调整程度会直接影响方向间隙还有轴运行速度也会直接影响方向间隙的大小,因此很多数控系统中反向间隙补偿大多在机械合理调整后还要分正常速度和快速进给俩种速度俩种速度下的补偿。
摩擦补偿在很多数控系统中很多应用在轴的过象限调整,即加工圆是在上下左右轴换向时候在工件上产生的刀痕,通过摩擦补偿可以一定程度的缓解这种现象,关于此参数在西门子系统的应用,大家有兴趣可以参看以前在论坛中相关的帖子。
有一些应用(个人观点,仅供参考)。
- 1、下载文档前请自行甄别文档内容的完整性,平台不提供额外的编辑、内容补充、找答案等附加服务。
- 2、"仅部分预览"的文档,不可在线预览部分如存在完整性等问题,可反馈申请退款(可完整预览的文档不适用该条件!)。
- 3、如文档侵犯您的权益,请联系客服反馈,我们会尽快为您处理(人工客服工作时间:9:00-18:30)。
3
一、螺距误差产生的原因
利用数控系统提供的螺距误差补偿功能,可以 对螺距误差进行补偿和修正,达到提高加工精度的 目的。另外,数控机床经长时间使用后,由于磨损 等原因造成精度下降,通过对机床进行周期检定和 误差补偿,可在保持精度的前提下延长机床的使用 寿命。
4
一、螺距误差产生的原因
数控机床的螺距误差产生原因如下: 1. 滚珠丝杠副处在进给系统传动链的末级。由于丝 杠和螺母存在各种误差,如螺距累积误差、螺纹滚 道型面误差、直径尺寸误差等(其中最主要的是丝 杠的螺距累积误差造成的机床目标值偏差); 2. 滚珠丝杠的装配过程中,由于采用了双支撑结, 使丝杠轴向拉长,造成丝杠螺距误差增加,产生机 床目标值偏差;
22
23
谢谢!
24
13
二、螺距误差补偿原理
距补偿误差表中计算出实际的补偿值,对指令位置 进行补偿,产生实际输出值控制伺服电机。如图3 所示,数控系统以机床零点为基准,在不同的指令 位置,按补偿表中的误差值进行补偿。数控系统在 每段数据插补过程中均进行误差补偿,以获得最高 精度。
14
二、螺距误差补偿原理
实现过程和步骤如下 :
7
二、螺距误差补偿原理
8
二、螺距误差补偿原理
9
二、螺距误差补偿原理
数控系统中设置螺距误差补偿需要NCK(numericcontrol kernel) 的支持,目前可针对某个点把 它的补偿值写入NCK补偿文件。机械零件程序运行 时自动地读取相应补偿文件中各点的补偿数据,并 进行相应的调整,随之产生对应的机械
2.3软件方法螺距误差补偿原理 采用定点的脉冲补偿方法可修正螺距误差,提 高定位精度。其原理是在各坐标轴上设定一些坐标 点,当机床经这些点时,数控系统根据事先测定的 补偿值进行补偿。补偿所需参数如:①各补偿轴起 、终点机床坐标(以机床零点为基准);②补偿间 隔或等分段数;③每段补偿间隔对应补偿值。 将测出的误差值输入到螺距补偿误差表中。当 工作台移动时,系统根据当前位置和指令位置在螺
17
二、螺距误差补偿原理
2.5双向螺距误差补偿(CEC) CEC的原理支持两个方向,即从起点到终点方 向和从终点返回到起点方向,如图5所示。规定从 起点到终点方向为正方向,从终点到起点方向为负 方向。刀具在丝杠上的运动轨迹是先从起点运动, 依次经过各个等份点,到达终点;
18
二、螺距误差补偿原理
然后再从终点按原路返回到起点,逆向依次经过各 个等份点,直至起点。CEC补偿在两个方向上生效 ,分别计算每个方向上当运动到某一个等份点时, 根据运动实际移动的距离与预期的距离的偏差计算 出该点的补偿值。注意正向与负向的方向性。同一 个点在两个方向上补偿不同。以图5中10点为例。当 刀具从起点向终点运动即正方向,途中经过10点;假 如从0点向10点实际移动了9mm,与预期移动距离10 的偏差是10-9=1mm,那么10这个点在正方向上的 补偿是1mm。
2
3
15
二、螺距误差补偿原理
2.4单向螺距误差补偿( EEC) EEC的原理是从起点到终点这个方向,在起点 与终点之间等份若干点,如图4所示,刀具在丝杠 上的运动轨迹是先从起点运动,依次经过各个等份 点,到达终点。EEC补偿只对从起点到终点这个方 向生效。
16
二、螺距误差补偿原理
当运动到某一个等份点时,根据刀具实际移动 的距离与预期的距离的偏差,计算出该点的补偿值 。例如,以图4中10这个点为例,预期希望刀具从0 点能够运动到10点,其间移动距离为10mm。但是 由于丝杠的误差,实际运动的距离是9mm,偏差为 10-9=1mm,那么10这个点的补偿值就是1mm; 如 果其间实际移动距离为11mm,偏差为10-11=- 1mm,那么10这个点的补偿值就-1mm。其他各点 的螺距误差补偿同理实现。
1
• 在数控机床上正确安装高精度位移测量装置; • 在整个行程上 , 每隔一定距离取一个位置点 作为补偿点; • 记录运动到补偿点的实际精确位置; • 将各点处的误差标出 , 形成在不同的指令位 置处的误差表; • 多次测量 , 取平均值; • 依 “补偿值 =数控命令值-实际位置值 ”的 公式计算各点的螺距误差,并将各点处的误差 标出,形成在不同指令位置处的误差表,并将该 表输入数控系统 , 系统按此表进行补偿。
19
二、螺距误差补偿原理
当刀具从终点向起点反向运动,途中反向地经过10 点;假如从20点向10点实际移动了9mm,与预期移动 距离10的偏差是10-9 =1mm,但是由于从终点到起 点是反方向,所以10点在反方向上的补偿是-1mm; 假如实际移动距离为11mm,与预期移动距离10的偏 差是10-11=-1mm,但是由于从终点到起点是反 方向,所以10这个点在反方向上的补偿是1mm其他 各点正方向和反方向上的补偿依此类推。
10
二、螺距误差补偿原理
2.2硬件方法补偿滚珠丝杠螺距误差的原理 过去,在开环数控机床中,经常采用硬件方法 对丝杠螺距误差进行补偿,即采用机械方法测出 数控机床某一轴滚珠丝杠在全行程上的误差分布 曲线,在丝杠的螺距累积误差值达到一个脉冲当 量处的位置点安装一个挡块,当机床工作台移动 时,安装在机床上的微动开关每与挡块接触一次, 就发出一个误差补偿信号,通过控制电路指示步 进电机多走或少走一步。
5
一、螺距误差产生的原因
3. 机床装配过程中,由于丝杠轴线与机床导轨平行 度的误差引起的机床目标值偏差。 螺距误差补偿是将机床实际移动的距离与指令移 动的距离之差,通过调整数控系统的参数增减指令 值的脉冲数,实现机床实际移动距离与指令值相接 近,以提高机床的定位精度。螺距误差补偿只对机 床补偿段起作用,在数控系统允许的范围内补偿将 起到补偿作用。
螺距补偿机理
汇报人:
时 间:2015年4月24日
内容提纲
一、螺距误差产 生的原因 二、螺距误差补 偿原理
硬件方法补偿螺 距误差的原理
软件方法补偿螺 距误差原理
单向螺距误差补 偿原理
双向螺距误差补 偿原理
2
一、螺距误差产生的原因
数控机床大都采用滚珠丝杠作为机械传动部件, 电机带动滚珠丝杠,将电机的旋转运动转换为直线运 动。如果滚珠丝杠没有螺距误差,则滚珠丝杠转过的 角度与对应的直线位移存在线性关系。实际上,制造 误差和装配误差始终存在,难以达到理想的螺距精度, 存在螺距误差,其反映在直线位移上也存在一定的误 差,降低了机床的加工精度。
6
二、螺距误差补偿原理
2.1螺距误差补偿的方法描述 对螺距误差进行补偿时,在机床的运行轨道上 取若干点,通过激光干涉仪测得机床的实际定位位 置,与预期设定的位置进行比较,得出偏移距离, 并将其写入补偿文件中。选取的点越多,补偿精度 越高。机床在下次运行时,将会把补偿文件的数据 也计算在内,从而达到精度要求。
11
二、螺距误差补偿原理
这种断续的脉冲补偿方法给数控机床的工作台增加 了一些机械构件(如补偿杆、挡块等)和电路(如将 微动开关发出的补偿信号传送给数控装置的电路) 。另外,这种补偿方法比较适用于采用脉冲增量插 补方法、步进电机驱动的开环数控机床,而对于采 用数据采样插补方法、直流或交流伺服电机驱动的 半闭环数控机床,则不适宜。因此,目前,大多数数 控机床补偿滚珠丝杠的螺距误差时均采用软件的方 法。
20
螺距误差补偿是按轴进行的。针对每一个轴可以设 置每个轴的螺距误差补偿。主轴不设置。
21
n=1 螺 距 误 差 补 偿 程 序 图 n++ Xn<X<Xn-1
线性插值计算出△Xn值 X=Xn+△Xn
以数控机床 纵向(X轴)进给 丝杠为例,设:X 表示数控装置发 出的X轴进给坐标 值,Xn表示数控机 床某轴滚珠丝杠 的全行程上选取 的各指令位置点 的坐标值,△Xn表 示用激光干涉仪 测得的各指令位 置点的螺距误差。