烧结余热发电技术说明
浅析烧结冷却机余热发电技术

浅析烧结冷却机余热发电技术摘要:烧结冷却机余热发电技术是利用烧结冷却机中低温的废气通过余热锅炉产生蒸汽,来推动汽轮机组做功发电。
文章对工业余热资源进行了概述,对钢铁行业烧结冷却机余热发电工艺和方案进行了总结和分析,从而更好的节约能源,有利于环境保护。
关键词:钢铁行业;烧结冷却机;余热发电1 工业余热资源概述余热资源本质上是一种二次能源,是一次能源或者是可燃物料经过转换之后得到的产物,亦或者燃料在实际燃烧过程中所产生的热量在实现某一工艺之后所剩余的热量。
依据余热资源温度品位来进行划分,通常可以将工业余热划分为600℃以上的高温余热,300~600℃之间的中温余热以及300℃以下的低温余热3种类型;依据余熱资源的来源进行划分,可以将工业余热分为烟气余热、冷却介质余热、废汽废水余热、化学反应热、高温产品以及炉渣余热、可燃废气和废料余热等。
纵然余热资源的来源十分广泛,温度范围也相对较广,同时以多种形式存在。
不过单纯从余热资源的利用角度来看,其具备如下共同点:因为工艺生产过程具备一定的周期性、间断性,且生产过程相对较为波动,这就使得余热量相对来说并不稳定;同时,余热介质的性质相对较为恶劣,例如烟气中就包含的而又大量的粉尘以及腐蚀性的物质成分;此外,余热利用装置容易受到场地、原生产等现有条件的限制。
因此,工业余热资源利用系统或设备运行环境相对恶劣,要求有宽且稳定的运行范围,能适应多变的生产工艺要求,设备部件可靠性高,初期投入成本高,从经济性出发,需要结合工艺生产进行系统整体的设计布置,综合利用能量,以提高余热利用系统设备的效率。
2 钢铁行业余热发电工艺以烧结鼓风冷却机为例。
目前钢铁行业烧结矿的冷却方式大多采用鼓风冷卻方式,根据占地方式不同,有带式冷却机和环式冷却机两种。
烧结鼓风冷却机规模按冷却机面积有190m2、280m2、336m2、400m2、435m2、460m2等系列。
烧结鼓风冷却机工作原理为:赤热的烧结矿石从烧结机进入冷却机时的温度高达650~750℃,在烧结机中反应完成的矿石经过破碎,移送至冷却机,并形成一定厚度的填充层。
烧结余热发电资料

1概论在钢铁生产过程中,烧结工序的能耗约占总能耗的10%,仅次于炼铁工序,位居第二。
在烧结工序总能耗中,有近50%的热能以烧结烟气和冷却机废气的显热形式排入大气。
由于烧结冷却机废气的温度不高,仅150~450℃,加上以前余热回收技术的局限,余热回收项目往往被忽略。
随着近几年来余热回收技术突飞猛进,钢铁行业的余热回收项目造价大幅度降低,同时余热回收效率大幅提高,特别是闪蒸发电技术和补汽凝汽式汽轮机在技术上获得突破,为钢铁行业余热回收创造了优越的条件。
时值目前国家能源紧缺、大力提倡生产过程节能降耗的关键时期,国家有关部门对企业节能指标提出了很高的要求。
在这样的形势和技术条件下,一些有远见的钢铁企业,迅速启动各种余热回收项目,不但完成了钢铁企业的节能降耗任务,同时也能为企业本身创造可观的经济效益。
烧结冷却机余热的回收,是通过回收烧结机尾落矿风箱及烧结冷却机密闭段的烟气加热余热锅炉来回收低品味余热能源,结合低温余热发电技术,用余热锅炉的过热蒸气来推动低参数的汽轮发电机组做功发电的最新成套技术;其与火力发电相比:1)不需要消耗一次能源。
2)不产生额外的废气、废渣、粉尘和其它有害气体。
具体来讲烧结冷却机余热回收的意义体现在如下几个方面:1)利用烧结环冷机烟气余热发电,部分代替来自电网的以化石燃料为能源的供电量,从而起到减少温室气体排放效果;2)降低烧结工序能耗,促进资源节约;降低产品单位价格,使企业更具竞争优势。
3)有利于企业可持续发展目标的实现,减少由常规火电厂带来的SO2、CO2、粉尘之类的大气污染物,有助于改善当地的能源结构,提高能源安全。
2 国家政策一国务院关于做好建设节约型社会近期重点工作的通知国发【2005】 21号文件中提出“在冶金、有色、煤炭、电力、化工、建材、造纸、酿造等重点行业组织开展循环经济试点”。
具体内容:1)钢铁工业。
要加快淘汰落后工艺和设备,提高新建、改扩建工程的能耗准入标准。
实现技术装备大型化、生产流程连续化、紧凑化、高效化,最大限度综合利用各种能源和资源。
浅谈提高烧结余热发电量的技术创新与工艺优化

浅谈提高烧结余热发电量的技术创新与工艺优化烧结余热发电是指将烧结机组废气中的余热利用,通过热电转换技术转化为电能。
烧结余热发电具有低能耗、低排放等优点,是一种环保、节能的新能源。
为了进一步提高烧结余热发电量,需要进行技术创新和工艺优化。
一、技术创新(一)全膜式透平技术总热量利用率和透平效率是决定烧结余热发电量的重要技术参数,对于现有透平技术,其透平效率较低,导致了热量的浪费。
全膜式透平技术是近年来出现的一种新技术,其采用全膜式结构,使得透平的压比得到了提高,透平效率也得到了增加。
同时,采用了新型材料的透平叶片,可以有效降低透平的纵向力矩,进一步提高透平效率。
(二)换热器技术现有的换热器技术存在换热面积小、传热效率低、易结垢等问题,影响了烧结余热发电量。
为此,需要进行换热器技术的创新。
一种创新的换热器结构是采用多组管束,使得管线布局更加合理,管道间传热更加均匀。
同时,采用表面处理技术,可以使得管内壁面更加光滑,减小结垢的风险,增加换热面积,提高传热效率。
(三)低温余热发电技术低温余热发电技术可以有效提高烧结余热发电量。
该技术通过利用烧结机组废气中的低温余热,利用锂离子电池、纳米管技术等进行电热转换,实现废气中低温余热的有效利用。
这种技术具有投资成本低、适用范围广等优点。
二、工艺优化(一)机组布置优化机组布置优化是提高烧结余热发电量的关键。
合理的机组布置可以使得废气的热量更加充分地被利用,使得机组的发电效率得到优化。
对于现有的烧结机组,可以采用两台透平式烧结设备并联的方式,使得机组的总热量利用率提高至90%以上,进一步提高发电量。
(二)调控鼓风量调控鼓风量是提高烧结发电量的重要因素之一。
太大的鼓风量会导致废气中的热量不能充分利用,太小的鼓风量又会导致烧结机组的生产效率下降。
因此,需要对烧结机组的鼓风量进行精细调控,使得废气中的热量被充分利用。
(三)废气的再循环利用废气的再循环利用可以使得机组的总热量利用率进一步提高。
烧结机余热发电技术的详解
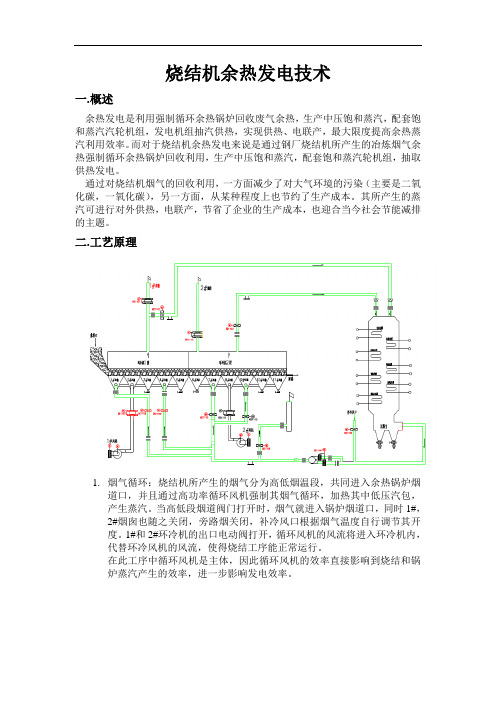
烧结机余热发电技术一.概述余热发电是利用强制循环余热锅炉回收废气余热,生产中压饱和蒸汽,配套饱和蒸汽汽轮机组,发电机组抽汽供热,实现供热、电联产,最大限度提高余热蒸汽利用效率。
而对于烧结机余热发电来说是通过钢厂烧结机所产生的冶炼烟气余热强制循环余热锅炉回收利用,生产中压饱和蒸汽,配套饱和蒸汽轮机组,抽取供热发电。
通过对烧结机烟气的回收利用,一方面减少了对大气环境的污染(主要是二氧化碳,一氧化碳),另一方面,从某种程度上也节约了生产成本。
其所产生的蒸汽可进行对外供热,电联产,节省了企业的生产成本,也迎合当今社会节能减排的主题。
二.工艺原理1.烟气循环:烧结机所产生的烟气分为高低烟温段,共同进入余热锅炉烟道口,并且通过高功率循环风机强制其烟气循环,加热其中低压汽包,产生蒸汽。
当高低段烟道阀门打开时,烟气就进入锅炉烟道口,同时1#,2#烟囱也随之关闭,旁路烟关闭,补冷风口根据烟气温度自行调节其开度。
1#和2#环冷机的出口电动阀打开,循环风机的风流将进入环冷机内,代替环冷风机的风流,使得烧结工序能正常运行。
在此工序中循环风机是主体,因此循环风机的效率直接影响到烧结和锅炉蒸汽产生的效率,进一步影响发电效率。
2.中压水循环:中压锅筒给水是来自汽机房凝结水经过低压除氧器处理后,由中压给水泵打入中压锅筒。
中压给水调节中最为重要的是给水三冲量调节,其调节方式是通过汽包水位,给水流量,主蒸汽流量。
给水三冲量调节中,给水流量的准确度直接影响到调节的准确和稳定度。
因此要进行三冲量的调节,给水流量和蒸汽流量以及水位的校验非常重要。
当主蒸汽温度达到一定值(主要由进入汽机的蒸汽温度决定)时,需要打开减温水调节阀来冷却中压减温汽,降低蒸汽温度,符合进入汽机蒸汽温度的要求。
3.低压水循环:低压汽包给水是来自汽机房凝结水经过除氧器处理后进入低压汽包。
对于低压汽包给水调节可以进行两冲量或单冲量调节,其具体调节方式可以根据现场情况而定。
钢铁企业烧结余热利用与发电技术

钢铁企业烧结余热利用与发电技术摘要:钢铁企业烧结工序的能耗仅次于炼铁工序,一般为钢铁企业总能耗的10%〜20%。
我国烧结工序的能耗与先进国家相比有较大差距,每吨烧结矿的平均能耗要高20kgce。
在烧结工序总能耗中,有近50%的热能以烧结机烟气和冷却机废气的显热形式排入大气,即浪费了热能又污染了环境。
据日本某钢铁厂热平衡测试数据表明,烧结机的热收入中烧结矿显热占28.2%、废气显热占31.8%。
可见,烧结厂余热回收的重点为烧结废(烟)气余热和烧结矿(产品)显热回收。
烧结余热也是目前我国低温余热资源应用的重点。
一、烧结余热利用方式与现状烧结余热主要利用方式有(1)在点火前对烧结料层进行预热;(2)送到点火器,进行热风点火;(3)实行热风烧结,回收烧结过程的热量和成品矿显热,降低烧结能耗;(4)利用余热锅炉回收烧结或冷却热废风,所产蒸汽用于预热烧结混合料或生活取暖等,或者进行蒸汽升值发电。
目前,我国大型烧结厂普遍采用了余热回收利用装置,但多数中、小烧结厂的余热仍未得到有效利用。
国内重点大中型企业,钢铁协会会员单位在2006年钢铁协会调研时,只有不到三分之一的烧结机配备了烧结余热利用设备,大部分是蒸汽回收并入全厂动力蒸汽管网,很少利用余热发电的。
近年来,随着低温烟气余热锅炉技术和低参数补汽式汽轮机技术的发展,使低温烟气余热发电成为可能。
二、烧结余热利用与发电技术目前我国烧结余热利用的重点和难点在于:由于存在漏风率高导致废气温度降低,又要保证进入除尘器前废气温度在露点以上等原因,回收利用烧结余热较困难。
因此,如何降低漏风率以提高烧结机烟气温度,以及在保证烧结废气除尘所需温度条件下,实现烧结机尾部高温段废气显热回收?烧结余热蒸汽发电核心技术的消化吸收和本土化,是烧结余热回收的重点。
如开发此技术将烧结矿余热充分利用,则钢铁行业年可节约能源约900万吨标准煤。
烧结余热发电是利用低温余热的一个有效途径,但目前来说应用很少,且存在一些问题,在运行过程中,由于烧结机和环冷机工况发生变化时,余热回收系统的工作参数也将随之变动,输出的蒸汽压力、温度、流量也将发生变化,从而影响发电机组的运行效率。
钢厂烧结机余热技术介绍 共19页PPT资料

江苏中天能源设备有限公司与安徽工业大学、福建三明钢厂、江苏煌明科技公 司多方合作,于2019年成功设计制造了国内第一套烧结机大烟道余热锅炉,系 统运行稳定,取得了良好的经济效益,并拥有国家发明专利。
一种内置于烧结机大小烟道上的 余热锅炉系统 专利技术介绍
江苏能源科技有限公司
公司简介
江苏能源科技有限公司为国家发改委备案的专业化节能服务公司,国家高新 技术企业,国内著名的合同能源管理示范合作单位,行业排名第26位。
我 们 联 合 江苏能源设备有限公司 ( 生产各类余热回收设备国内最知名 的专业厂家之一)。 提供高炉高风温的组合换热系统、烧结机大烟道余热锅炉、环冷机余热 锅炉等。产品广泛应用于钢铁冶炼、石油化工等行业。 “科技创新、优质高效、顾客至上、诚信守约”为公司服务方针,从追求 完善到卓越,实现携手共进,合作共赢!
3、节能增效: 3.1、实际产汽量:11~13吨每小时,增加发电功率约1900KW.h; 3.2、年发电量:1900×24×330=15048000KW.h(年按330天运行计算); 3.3、节能增益:15048000×0.46=692万元(电费单价0.46元/度)。
4、系统投资: 直接680万元Biblioteka 6、综合节能效益:
692-100=592万
投资回收周期:680/592=0.93年,约14个月可收回投资。
合作服务单位
谢谢!
一、项目 背 景
烧结是冶金企业主要耗能工艺,对烧结工艺来说,可进行余热回收的主要有两 部分:其一,冷却机部分;其二:烧结机大小烟道部分。
马钢烧结余热发电技术讲解

项目建设及运行实践
1 .项目建设
马钢烧结带冷废气余热利用工程,是我国第一次在 烧结系统实施的低温废气余热发电项目,不仅没有现成的 经验可借鉴,而且对其工艺设备、技术,工程施工等方面 都缺乏认识。针对这种情况,公司专门成立项目部,来强 化管理、落实责任。从前期调研开始,就不放过任何细节, 充分领会烧结带冷废气余热发电工艺方案和各种运行参数, 从而使整个工程按计划顺利进行。与此同时,还对余热发 电各个岗位的人员进行全面系统的理论培训和到兄弟单位 进行实际操作培训,并制定了操作规程、安全规程以及设 备规程。
废气锅炉采用卧式自然循环汽包炉,额定参数:烟气温度 395℃、流量40万m3/h、含尘量≤2g/ m3;过热蒸汽温度375℃、 压力1.95Mpa、流量37.4t/h。
汽轮发电机组采用多级、冲动、混压、凝汽式,主汽门进汽 参数为温度374℃、压力20.5 MPa (表压),耗汽量86t/h(含闪 蒸器流量),额定功率17.5MW。
(3)摸索闪蒸器产生的混汽与发电量的关系,找出合适 的运行方式。烟气余热发电采用了闪蒸器产生的混汽发 电新技术,将省煤器的部分热水,导入闪蒸器进行闪蒸, 产生饱和蒸汽,和过热蒸汽一同进入发电机发电,随着 闪蒸器产生的混汽量的增加,可以明显提高发电量。
马鞍山钢铁股份有限公司
MAANSHAN IRON & STEEL CO.,LTD.
马鞍山钢铁股份有限公司
MAANSHAN IRON & STEEL CO.,LTD.
项目建设及运行实践
2)改进措施
(1)提高烧结系统生产的稳定性,设备运行的可靠性, 降低工艺参数波动及非正常停机对烟气品质的影响,保 证烧结矿热源的稳定性。
烧结厂余热利用技术简介

烧结厂余热利用技术简介1. 引言烧结是一种将粉煤灰、石灰石或其它成分相似的原料通过加热使之部分熔化,然后回结固化成块状的冶金过程。
这个过程产生的高温烟气和废热在烧结厂通常都被排放到大气中。
然而,随着对能源资源的需求和环境保护意识的增强,如何有效利用烧结厂的余热已成为研究和开发的重点。
本文将简要介绍几种常见的烧结厂余热利用技术,并分析其优点和局限性。
2. 烧结厂余热利用技术2.1 热交换器技术热交换器技术是一种常见的烧结厂余热利用技术。
热交换器可以将高温烟气中的热能传递给废水、蒸汽或其他介质,以实现能量的回收和利用。
热交换器通常包括换热管道和换热器设备。
热交换器技术的优点在于可以提供连续的热能供应,并减少对外部能源的需求。
然而,此技术的局限性在于热交换器设备的成本较高,维护困难,并且对脏污、腐蚀性介质敏感。
2.2 ORC技术ORC技术(有机朗肯循环)是一种将烧结厂余热转化为电力的技术。
ORC系统通过将高温烟气中的热能转移到有机工质中,然后通过有机工质的蒸汽驱动涡轮发电机产生电力。
与传统蒸汽发电系统相比,ORC技术可以在较低的温度下工作,提高了热能转化的效率。
此外,ORC技术还可以通过调整有机工质的选用来适应不同温度下的余热利用。
然而,该技术需要较高的初投资成本,并且对有机工质的选择和运行维护要求较高。
2.3 废热蒸汽利用技术废热蒸汽利用技术是一种将烧结厂余热转化为蒸汽以供其他生产过程使用的技术。
在烧结厂中,产生的高温烟气可以通过余热锅炉将废热转化为蒸汽,然后再将蒸汽输送到其他工序中进行能量回收。
废热蒸汽利用技术可以减少对外部能源的需求,并提高能源利用效率。
然而,该技术的缺点在于需要较大的设备投资,且对蒸汽管道的要求较高。
3. 总结烧结厂余热利用技术是一种重要的能源回收利用手段,可以减少环境污染,降低能源消耗,提高能源利用效率。
本文介绍了几种常见的烧结厂余热利用技术,并分析了它们的优点和局限性。
无论是热交换器技术、ORC技术还是废热蒸汽利用技术,都需要根据具体的烧结厂情况和需求来选择和应用。
- 1、下载文档前请自行甄别文档内容的完整性,平台不提供额外的编辑、内容补充、找答案等附加服务。
- 2、"仅部分预览"的文档,不可在线预览部分如存在完整性等问题,可反馈申请退款(可完整预览的文档不适用该条件!)。
- 3、如文档侵犯您的权益,请联系客服反馈,我们会尽快为您处理(人工客服工作时间:9:00-18:30)。
从环冷机来的高温烟气作为余热锅炉的工作介质,通过余热锅炉换热后降至120℃左右(方案二为135℃左右),然后通过循环风机再回到环冷机一段及二段底部冷却风箱。烧结机大烟道设置了热管式余热回收装置,大烟道出口烟气将降低20~30℃左右。
3.
3.1.
按设备布置形式分为机上、机下两种;按照废气流程又分为烟气循环使用和烟气直排两种工艺形式,烧结系统的余热回收技术从其发展历程来看,经过了从机上布置到机下布置的过程。各种余热回收的优缺点总结如下:
机下布置——烟气直排技术
废气直接排放,系统增设一台引风机作为克服余热回收系统阻力的动力源,废气经过除尘和余热回收后直接排放,原有环冷机下的鼓风机继续使用。
余热回收设备布置在烧结环冷机旁,高温烟气从烧结环冷机引出,经除尘、换热后,通过烟囱直接排向大气。
回收效率较高,较机上布置烟气直排方式回收热量多;能耗较低。
2.
本项目为辽宁本溪钢铁集团公司300m²、360m²(分别简称为1#、2#烧结环冷机)烧结余热发电工程,烧结环冷机余热锅炉为双压锅炉,烧结机大烟道中也设置了热管式余热回收装置,其中生产出来的中压过热蒸汽与烧结环冷机余热回收装置所产的中压过热蒸汽会合作为主蒸汽送入双压补汽凝汽式汽轮机发电机组发电;低压蒸汽部分供自身除氧用外其余送至低压过热器过热,过热后送至补汽凝汽式汽轮机补汽口。
图一、烧结工序内废气温度分布
由图一所示,余热回收主要在烧结矿成品显热及烧结、冷却机的排气显热三个方面,热烧结矿显热和烟气显热占烧结过程热耗的50%以上,针对烧结机大烟道机尾区域热烟气及冷却机高温废气设置余热回收装置回收利用其余热,可大大地提高能源利用率,节约能源。
烧结机生产时,机尾区域大烟道烟气温度可达300~400℃。为保证烧结矿质量及输送设备运行安全,烧成的热烧结矿从烧结机尾部落下经破碎后,通过振动筛分后经溜槽落到冷却机传送带上,在溜槽部分热料矿温度达800℃以上,以辐射形式向外界散热,落到冷却带上料温很高。烧结冷却机上布置有冷却风罩,风罩内通过鼓风机使冷却风强制穿过料矿层,经料矿加热在风罩内冷却风温提高到350~450℃左右。
烟气流量(万Nm³/h)
烟气温度(℃)
烧结机大烟道
16
350
方案二:
环冷机
1#环冷余热锅炉
烟气流量(万Nm³/h)
烟气温度(℃)
一段
30
380
二段
18
280
烧结机
1#烧结大烟道余热锅炉
烟气流量(万Nm³/h)
烟气温度(℃)
烧结机大烟道
16
350
注:
1、烟气量工况波动按-20%~+10%考虑,烟温按±20℃考虑。
表6.大烟道余热锅炉参数(此为1#锅炉)
序号
项目
单位
设计工况数值
1
中压蒸汽压力
MPa
2.1
2
中压过热蒸汽温度
℃
360
3
中压蒸汽流量
t/h
9
4
供水温度
℃
155.4
5
锅炉排烟温度
℃
260±5
6
余热锅炉烟气阻力(自烟气入口至出口)
Pa
<120
7
锅炉余热利用率
%
95
4.2.3.
表2.锅炉补给水品质
序号
水质项目
热管换热器具有对温度变化大的适应性和在换热过程中对热流密度的可调性,大幅度提高了工程的可靠性。热管式蒸汽发生器充分利用热管在热传导中的超导特性,来进一步降低废气排放温度,从而回收更多的热量,以满足该系统的长周期稳定运行要求,并达到降温、除尘、余热利用的目的。
4.
4.1.
(参照鞍山地区)
4.1.1.
(1)温度
序号
项目
单位
设计工况数值
1
中压蒸汽压力
MPa
1.4
2
中压过热蒸汽温度
℃
360
3
中压蒸汽流量
t/h
10
4
供水温度
℃
147.9
5
锅炉排烟温度
℃
250±5
6
余热锅炉烟气阻力(自烟气入口至出口)
Pa
<120
7
锅炉余热利用率
%
95
方案二
表5.烧结环冷余热锅炉参数(此为1#锅炉)
序号
项目
单位
设计工况数值
1
中压蒸汽压力
4.1.2.
厂区基本地震烈度按7度(第一组)考虑;
设计基本地震加速度值0.1 。
4.2.
充分利用烟气余热本次共做了两套方案。
4.2.1.
1#环冷机、2#环冷机参数相同,以1#为例
方案一:
环冷机
单套环冷余热锅炉
烟气流量(万Nm³/h)
烟气温度(℃)
一段
18
400
二段
30
320
烧结机
1#烧结大烟道余热锅炉
占地面积大;一次投资较大;烟气直排,不能最大限度的回收热量;对环境有一定污染。
机下布置——烟气循环利用
实践证明,当冷却风温为50℃时废气温度提高15℃,冷却风温达120℃时,废气温度可提高45℃,通过烟气循环利用,提高了废气温度,有利于余热利用,且减少了粉尘的排放。
烟气循环利用系统需增设一台循环风机,循环风机提供克服料矿、余热回收系统的阻力,原环冷机下的鼓风机留做备用,实现废气的循环利用。余热回收设备布置在烧结环冷机旁,高温烟气从烧结环冷机引出,经除尘、换热后,烟气温度还有~140℃左右,增设烟气循环系统,可将该部分热量有效的利用起来,实现废气的循环利用。
300/360m²
二〇一一年五月
1.
钢铁工业是能源消耗最大的产业部门之一,烧结矿是高炉炼铁的主要原料,烧结过程中的能源消耗占钢铁企业总能耗的10%左右,仅次于炼铁;在可供利用的余热中仅环冷机废气及烧结烟气的显热约占烧结全部热支出的30%以上,充分回收利用这些烧结余热,是烧结节能的重要途径及发展趋势,冶金烧结工序内废气温度分布示意图如图一所示。
单位
除盐水
1
硬度
μmol/l
≤2.0
2
电导率
μs/cm(25℃)
≤5
3
二氧化硅
μg/l
≤20
给水品质符合GB/T12145-2008火力发电机组及蒸汽动力设备水汽质量
4.2.4.
高压10.5kV AC 50Hz
低压380V/220V
直流电源:24V DC
4.3.
余热锅炉的设计、制造、检验必须执行,但不限于下列标准(下列标准如果有国家或行业新颁布标准,乙方须注明,并按最新标准执行):
劳部发[1996]276号
《蒸汽锅炉安全技术监察规程》
GBJ17-1988
《钢结构设计规范》
GB9222-2008
《水管锅炉受压元件强度计算》
GB/T12145-2005
《火力发电机组及蒸汽动力设备水汽质量标准》
DL/T5072-2007
《火力发电厂保温油漆设计规程》
JB/T1615-1991
《锅炉油漆和包装技术条件》
JB3191-1999
《锅炉内部装置技术条件》
JB/T1609-1993
《锅炉汽包制造技术条件》
JB/T1610-1993
《锅炉集箱制造技术条件》
JB/T1611-1993
《锅炉管子制造技术条件》
JB/T1620-1993
《锅炉钢结构制造技术条件》
JB/T 6512-1992(
《高频电阻焊螺旋翅片管制造和验收技术条件》
工艺
特点
优点
缺点
机上布置——烟气直排技术
换热设备直接安装在烧结环冷机上部,高温烟气经除尘、换热后,直接排入大气。
设备直接安装在环冷机上部,可直接利用料矿的辐射热,且占地面积小、投资省、能耗抵、操作简单。
受设备布置位置的限制,设备不能设置过大;烟气只能直排,不能最大限度的回收热量;回收效率低,热量回收有限;对环境有一定污染。
该余热回收装置共采用我公司9项专利
序号
专利类型
专利名称
专利号
1
实用新型
ZL200520069009.4
冶金烧结机余热产汽节能装置
2
实用新型
ZL200520069010.7
分离套管式热管蒸汽发生器
3
实用新型
ZL200520069203.2
直管板热管换热器
4
实用新型
ZL 200520069204.7
等流速热管换热器
目前对烧结工序的余热利用大多限于烧结冷却机部分,并未对大烟道烟气余热进行回收。烧结冷却机的余热利用有两种方式:一类是热利用,即利用余热来产生热水或蒸汽以供暖、制冷、拌料用,或直接用于热风烧结等;另一类是动力利用,即将余热转换为电能或机械能。用于余热发电或带动透平机工作等。考虑到提高烧结工序节能量,减少产品单耗,本次余热发电方案对烧结、环冷排气两部分均进行余热回收。
(1)·工艺技术成熟,充分利用了烧结工序中各段可利用的能量,最大限度的回收烟气余热,并将余热用于产汽或发电;
(2)·设备布置合理,占地少,便于操作;
(3)·减少了废渣、废气等气体的排放,切实有效地改善了环境;
(4)·不消耗一次能源,经济效益不受燃料价格波动的影响;
(5)·采用高效、先进、结构合理的设备和可靠的材质;
适应高温变低温差组合式余热回收蒸汽发生装置