高炉炼铁新技术
钢铁行业的创新案例介绍行业内的技术创新和产品研发成果

钢铁行业的创新案例介绍行业内的技术创新和产品研发成果钢铁行业一直以来都是现代工业的重要支撑部门,随着科技的进步和全球竞争的日益激烈,钢铁企业必须不断努力寻找技术创新和产品研发的突破口,以确保行业的可持续发展。
本文将介绍钢铁行业内一些成功的创新案例,这些案例涵盖了技术创新、产品研发以及行业转型等方面的成果,并探讨了其对行业发展的积极影响。
一、技术创新1. 新型高效节能高炉技术钢铁行业的高炉是钢铁生产的重要设备,传统高炉存在能源消耗大、污染物排放高等问题。
某钢铁企业引入了新型高效节能高炉技术,通过在高炉炼铁过程中使用新型燃烧器、废气余热回收装置等,有效降低了能源消耗和污染物排放,提高了炼钢效率和资源利用率。
2. 智能制造与大数据应用某钢铁企业通过智能制造和大数据应用,实现了钢铁生产过程的自动化和数字化。
他们引入了现代化的生产线设备和自动控制系统,通过实时监测和数据分析,优化了生产管理和工艺流程,提高了生产效率和产品质量。
3. 清洁炼钢技术传统的炼钢过程中会产生大量的二氧化碳等温室气体,对环境造成严重的污染。
为了解决这一问题,某钢铁企业发展了清洁炼钢技术,采用了先进的碳捕集和储存技术,将二氧化碳等有害气体进行有效处理和利用,降低了环境污染,提高了钢铁生产的可持续性。
二、产品研发1. 高性能特种钢材研发某钢铁企业针对特定需求,积极研发高性能特种钢材。
通过优化合金配方和热处理工艺,他们成功开发了一系列满足航空航天、汽车、能源等行业需求的高强度、高韧性的特种钢材,填补了国内相关领域的空白,提升了国内钢材产品的竞争力。
2. 环保型钢材研发为了适应社会对绿色环保的要求,某钢铁企业投入大量资源进行环保型钢材研发。
他们采用了新型的冶炼工艺和成分调整技术,成功研制出低含铅、低含污染物的环保型钢材,为解决环境问题做出了积极贡献。
3. 新型钢铁产品应用某钢铁企业积极开拓新的市场,发展出适应不同领域需求的新型钢铁产品应用。
国内外高炉炼铁技术的发展现状和趋势

国内外高炉炼铁技术的发展现状和趋势高炉炼铁技术是金属冶炼工业发展的基础,是保证金属铁质量和产量的关键技术,也是社会经济发展的重要依托。
近年来,随着金属冶炼工业的快速发展,国内外高炉炼铁技术的发展也取得了显著的成就,为保证金属铁质量、提高产量、提高经济效益发挥了重要作用。
首先,国内外高炉炼铁技术取得了重大突破,进一步提高了金属铁质量。
随着科学技术的进步,添加剂和冶炼工艺的改进,使高炉炼铁工艺取得重大进展,不仅能够有效提高铁素体组成,同时也能够改善铁水的流动性,有利于铁块的全面成型。
此外,利用新型炉料和改进的热处理技术,可以有效降低铁水的含氧量,提高铁液的液相容量,从而获得更高品质的铁。
其次,国内外高炉炼铁技术的发展,还大大提高了铁的产量。
传统的高炉炼铁工艺存在着大量的炉料损失,限制了铁的产量。
随着国内外高炉炼铁技术的发展,炉料损失大大减少,产量得到提高。
通过对炼铁工艺及其参数进行优化调整,获得合理的炉料计算和分配,进而有效提高铁的产量。
此外,结合智能技术、自动化技术和智能控制技术,还可以实现远程监控和智能化管理,可以使高炉炼铁效率更高,产量更大。
最后,国内外高炉炼铁技术的发展,对提高经济效益具有重要意义。
国内外高炉炼铁技术的发展,不仅缩短了铁的生产周期,提高了产量,而且可以减少能耗消耗和废气排放,降低了生产成本,有利于提高企业的竞争力,实现更高的经济效益。
此外,国内外高炉炼铁技术的发展还可以改善炼铁终端的工作环境,为炼铁行业的发展创造更加良好的条件。
以上是国内外高炉炼铁技术的发展现状和趋势的概述,未来的发展趋势可以简单地总结为以下几点:继续提高高炉炼铁质量和产量,推广智能技术,进一步优化炼铁工艺,合理设计炉料配比,提高炼铁效率,减少能耗和污染,改善炼铁环境,提高经济效益,实现绿色经济发展。
未来,相信国内外高炉炼铁技术将取得更好的发展,为我们社会的经济发展提供更多的依托。
高炉炼铁工艺的演变与创新从传统到现代

高炉炼铁工艺的演变与创新从传统到现代随着科学技术的不断发展,高炉炼铁工艺也经历了漫长的历史发展。
从传统到现代,高炉炼铁工艺在不断演变与创新,以适应和满足时代的需求。
本文将从多个方面探讨高炉炼铁工艺的发展历程,并分析其演变和创新对于铁工业的影响。
一、传统高炉炼铁工艺的特点及问题传统高炉炼铁工艺是指早期的高炉炼铁方法,其特点是炉容相对较小,燃料多为木炭或焦炭,矿石和燃料由上部装料口输入,铁水由炉底出口排出。
传统高炉炼铁工艺在一定程度上满足了当时的铁产量需求,但也存在一些问题:1. 低炉容限制了生产能力:由于传统高炉容积较小,无法进行大规模的生产,限制了铁产量的增长。
2. 能源利用效率低:燃料多为木炭或焦炭,其燃烧效率较低,导致能源浪费。
3. 铁矿石利用率较低:传统高炉炼铁工艺无法充分利用矿石中的铁资源,大量铁含量较低的矿石无法被利用。
二、现代高炉炼铁工艺的创新与改进为了提高铁产量、能源利用效率和矿石利用率,现代高炉炼铁工艺进行了一系列的创新与改进。
1. 高炉容积的增大:现代高炉的炉容相对较大,能够进行大规模的生产,提高了铁产量。
2. 燃料的改进:现代高炉炼铁工艺多采用煤炭作为主要燃料,相比木炭或焦炭,煤炭的燃烧效率更高,能源利用效率得到提升。
3. 热交换技术的应用:现代高炉工艺中引入了热交换技术,将高温废气中的热能回收,用于预热进料和蒸汽发电,提高了能源利用效率。
4. 炉渣处理技术的改进:现代高炉炼铁工艺采用了先进的炉渣处理技术,通过加入矿粉、炼钢炉渣等辅助剂,可以调整炉渣的性质,提高铁矿石利用率。
5. 连续铸造技术的应用:现代高炉炼铁工艺中广泛使用了连续铸造技术,将熔融的铁水直接注入连续铸造机,实现了自动连续生产,提高了生产效率。
三、高炉炼铁工艺演变与创新的影响高炉炼铁工艺的演变与创新对铁工业产生了深远的影响。
1. 提高产量和效益:现代高炉的产能大大提高,生产效率显著提升,使得铁工业能够满足不断增长的市场需求。
高炉炼铁工艺技术标准最新

高炉炼铁工艺技术标准最新高炉炼铁工艺技术标准最新700字高炉炼铁工艺技术标准是指在高炉炼铁过程中所涉及到的各种操作和参数的标准。
这些标准的制定对于确保高炉正常运行、提高炼铁效率、降低能耗和保护环境具有重要意义。
下面将介绍高炉炼铁工艺技术标准的最新内容。
1. 原料配比标准:高炉炼铁的原料主要包括铁矿石、焦煤和石灰石。
原料的配比直接影响到炼铁的效果和产品质量。
根据不同的铁矿石和焦煤的性质,制定合理的配比标准,确保高炉内的还原和熔化反应能够顺利进行,同时减少生产成本。
2. 炉渣成分标准:高炉炼铁产生的炉渣是含有高炉灰渣、熔渣和炉渣球等物质的复杂体系,其成分对炼铁过程和产品质量有着重要影响。
制定炉渣成分标准,旨在控制炉渣中各种氧化物和杂质的含量,使炉渣具有良好的流动性、透气性和脱硫脱磷能力。
3. 炉渣脱硫脱磷标准:高炉炼铁过程中,炉渣中的主要成分之一是含有硫和磷的物质。
高炉炼铁工艺技术标准要求对炉渣进行适当的脱硫和脱磷处理,以降低钢铁中的硫和磷含量,提高产品的质量。
4. 炉温和气氛控制标准:高炉炼铁过程中,炉温和气氛对炼铁过程和产品质量起着决定性的作用。
工艺技术标准要求对炉温和气氛进行实时监测和控制,以确保高炉内的化学反应能够充分进行,并减少不良反应和产生有害气体。
5. 炉压和风速控制标准:高炉炼铁过程中,炉压和风速对炼铁效果和能耗有着直接的影响。
制定合理的炉压和风速控制标准,可以保证高炉的正常运行,提高炼铁效率,降低能耗。
6. 冷却水质量标准:高炉炼铁过程中,冷却水用于冷却高炉的各种设备和管道,其质量对设备的寿命和运行稳定性有着重要影响。
制定冷却水质量标准,对冷却水进行定期检测和处理,可以防止设备的腐蚀和水垢的产生,延长设备的使用寿命。
7. 炉外环境保护标准:高炉炼铁过程中,会产生大量的炉渣、烟尘、废水和废气等污染物。
工艺技术标准要求在高炉炼铁过程中采取有效的控制措施,减少污染物的排放,保护环境。
以上是高炉炼铁工艺技术标准的最新内容。
高炉炼铁过程中废渣资源化利用的技术创新

高炉炼铁过程中废渣资源化利用的技术创新由于工业化的快速发展,高炉炼铁已成为现代钢铁工业中不可或缺的环节。
然而,传统的炼铁过程会产生大量的废渣,给环境带来严重污染。
为了实现可持续发展,推动高炉炼铁过程中废渣资源化利用的技术创新势在必行。
本文将探讨当前废渣资源化利用的现状和趋势,并提出一些创新的技术解决方案。
一、废渣资源化利用的现状高炉炼铁过程中主要产生的废渣主要包括烧结矿、烟气净化渣和炉渣等。
这些废渣通常被视为浪费物料,被丢弃或填埋,给环境带来负面影响。
然而,废渣中含有很多有价值的可回收物质,如铁、钢、矿物等。
因此,将废渣转化为可再利用的资源是一种解决环境问题和实现可持续发展的有效途径。
目前,废渣资源化利用主要通过以下几种方式实现:1. 废渣回收再利用:将废渣中的有价值物质进行分离和提取,重新利用于炼铁过程或其他工业生产中。
例如,烧结矿中的铁含量较高,可以再次用于高炉冶炼过程中。
2. 废渣填充利用:将废渣用于填充坑道、道路建设和土地复垦等工程中。
废渣填充可以减少对自然资源的占用,同时改善了被填充地区的土壤质量。
3. 废渣综合利用:将不同种类的废渣进行混合利用,形成新的产品或材料。
例如,烟气净化渣中的硅酸盐可以与矿产废渣混合制备建筑材料。
尽管废渣资源化利用取得了一定的进展,但仍面临一些挑战。
首先,目前的废渣资源化利用技术还不够成熟,存在成本高、技术路线不清晰等问题。
其次,相关政策法规的缺失和监管体系不健全也制约了废渣资源化利用的发展。
二、废渣资源化利用的技术创新为了推动高炉炼铁过程中废渣资源化利用的发展,需要进行技术创新和研发。
以下是一些可行的技术创新方案:1. 废渣熔融处理技术:通过高炉炼铁过程中炉渣的熔融处理,将废渣转化为玻璃状物质。
这种熔融处理技术可以减少废渣体积,提高废渣中有价值物质的回收率,并且可以将熔融后的产品用于建筑材料或其他工业领域。
2. 废渣碳化技术:利用废渣中的碳含量,将其进行碳化处理,生成高价值的碳材料。
绿色低碳炼铁关键技术介绍

绿色低碳炼铁关键技术介绍
绿色低碳炼铁是指利用环保、节能、低碳的技术和方法进行炼铁生产,以减少对环境的影响并降低碳排放。
以下是绿色低碳炼铁的一些关键技术介绍:
1. 高炉燃料替代技术,传统高炉使用焦炭作为还原剂和燃料,而绿色低碳炼铁技术中,可以采用生物质炭、再生资源炭等替代传统焦炭,以减少对森林资源的开采和减少二氧化碳排放。
2. 高炉煤气利用技术,高炉煤气是高炉生产过程中的副产品,通过先进的煤气净化技术和利用技术,可以将高炉煤气中的有用成分提取出来,用于发电、加热或化工原料,从而提高资源利用率和能源利用效率。
3. 高炉炉渣综合利用技术,绿色低碳炼铁技术中,炉渣不再被视为废弃物,而是被视为资源。
通过先进的炉渣处理技术,可以将炉渣中的有用金属成分回收利用,同时生产出对环境影响较小的新型建材产品,如水泥、砖块等。
4. 高炉烟气脱硫脱硝技术,绿色低碳炼铁技术要求高炉烟气中
的二氧化硫和氮氧化物排放达标。
因此,采用先进的脱硫脱硝技术,如湿法脱硫、SCR脱硝等,可以有效降低高炉烟气对环境的污染。
5. 高炉余热回收技术,高炉生产过程中会产生大量余热,通过
余热回收技术,可以将这些余热用于发电或供暖,提高能源利用效率,减少对外部能源的依赖,从而降低碳排放。
总的来说,绿色低碳炼铁技术是一个综合性、系统性的工程,
需要在高炉冶炼的每个环节都进行技术创新和改进,以实现对环境
友好、资源高效利用和碳排放降低的目标。
这些关键技术的应用将
为炼铁行业的可持续发展做出重要贡献。
高炉炼铁新工艺新技术实用手册

《高炉炼铁新工艺新技术实用手册》本书作者: 陈达士图书册数:全四册出版社: 当代中国音像出版社定价:998元现价:450元《高炉炼铁新工艺新技术实用手册》本店是实体店,坚决抵制各类盗版、劣质图书及附件,严格控制图书进货渠道,遵守国家新闻出版、发行的相关规定,直接从经过国家出版发行行政部门审核批准的出版社进货,与国图、中华书局、三联书店、商务印书馆、人民文学、上海古籍、上海世纪出版集团、中国社科、社科文献、电子工业、机械工业、化学工业、科学、法律、上海外教、北大、清华、人大、复旦、武大、南大、广西师大、北京出版集团、浙江少儿、江苏少儿、21世纪、作家、春风文艺、长江文艺、接力、漓江等全国知名的300余家出版社建立了良好的合作关系,所采购的图书均经所在地图书市场审读办公室审读合格后,方上市发行,100%正版、优质,订购速度快,数据提供及时,加工全方位,能全面符合客户的需求。
公司经营的图书科目品种齐全,涉及学科面广,涵盖文学、文化、教育、体育、科技、历史、工具图书、艺术、哲学、语言、政治、经济、学术专著、工具书及其它社科综合类图书等。
经营风格全方位,适合各文化层次读者学习和阅读需要。
内容介绍:商品简介商品编码:pdf87975出版社:当代中国音像出版社册 数:作者: 陈达士出版时间:2012年10月印刷时间2012年10月isbn:版次:第三版装帧:精装纸张:胶版纸印次:第三次页数:正文语种:中文开本:16开目录了全面总结我国炼铁生产的最新科技成果与先进操作技术经验,我们组织具有践经验的炼铁专家,编写了本书。
本书依据炼铁科技的基本原理,在总结我国不同炼铁厂生产实践经验的基础上,对高炉炼铁工艺的操作进行了系统阐述,对主要设备和工艺做了详细介绍,收录了近年来科技进步最新成果,阐述了高炉炼铁优化的“专家系统”及其应用效果。
本书内容翔实,集实用性和可操作性为一体,突出理论性,实践性和技术紧密结合,是提高铁厂产品质量、生产工艺技术、环保水平的必备工具书。
高炉冶炼智能化的发展与探讨
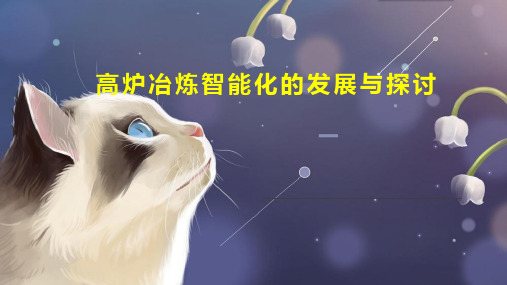
(3)提高产业协同:加强产业链上下游企业的合作与协同,实现资源共享和 优势互补,共同推动高炉冶炼智能化的发展。
(4)注重人才培养:加强高炉冶炼智能化领域人才的培养和引进,提高企业 和技术人员的专业素质和技术水平,为产业的可持续发展提供人才保障。
参考内容
随着全球气候变化和资源紧张问题的日益严峻,高炉炼铁行业面临着巨大的挑 战。为了降低碳排放、提高能源利用效率和推动可持续发展,高炉炼铁的低碳 化和智能化技术发展成为了行业的重要趋势。本次演示将详细介绍高炉炼铁低 碳化和智能化技术发展现状,以期为相关领域的研究和应用提供参考。
2、高炉冶炼智能化中安全问 题
高炉冶炼智能化中的安全问题主要包括设备安全和生产安全两个方面。设备安 全主要是指设备的稳定性和可靠性,以及针对设备故障的预警和处理能力。生 产安全主要是指生产过程中的安全隐患和事故预防,以及应对突发事件的应急 处理能力。保障高炉冶炼智能化的安全运行需要从设备选型、控制系统设计、 预警机制建立、应急预案制定等多个方面进行综合考虑和优化。
谢谢观看
高炉冶炼智能化的发展与探讨
目录
01 一、高炉冶炼智能化 的发展
03 参考内容
02
二、高炉冶炼智能化 的探讨
随着科技的快速发展,高炉冶炼智能化已成为现代钢铁工业的重要发展方向。 高炉冶炼智能化有助于提高钢铁企业的生产效率和产品质量,同时还能降低能 源消耗和环境污染。本次演示将从高炉冶炼智能化的发展历程和现状、关键技 术、安全与环保问题以及未来发展趋势等方面进行探讨。
3、高炉冶炼智能化的发展方向 与前景
未来,高炉冶炼智能化将朝着以下几个方向发展:
(1)全面智能化:通过不断引进新技术和设备,实现高炉冶炼全流程的智能 化,包括原料准备、高炉操作、煤气回收等环节。
- 1、下载文档前请自行甄别文档内容的完整性,平台不提供额外的编辑、内容补充、找答案等附加服务。
- 2、"仅部分预览"的文档,不可在线预览部分如存在完整性等问题,可反馈申请退款(可完整预览的文档不适用该条件!)。
- 3、如文档侵犯您的权益,请联系客服反馈,我们会尽快为您处理(人工客服工作时间:9:00-18:30)。
许满兴
(北京科技大学)
1、前言
跨入21世纪以来,我国钢铁工业步入了快速发展轨道。从2001 ~2011年11年间,我国高炉炼铁年产量由15554万吨增加到62969.3 万吨,以2001年为起点,年均增长36.8%,增速之高创行业世界之 最。同时,我国高炉炼铁在技术操作方针、技术经济指标评价、高 炉冶炼强化理论、合理喷煤比等方面都跨入了世界先进科学理论的 行列,这为我国钢铁工业由世界钢铁大国向世界钢铁强国迈进不断 创造了条件。
冶炼强度 t/m3.d 1.112 1.140 1.169 1.194 1.220
入炉风量 Nm3/min. 7242.6 7242.0 7241.3 7240.7 7240.1
旧的冶炼强度观是多鼓风、多烧焦炭、多出铁,用新的强化冶炼 观分析,入炉风量基本不变(略有下降),燃料比降低,提高了利用系 数。
该式是由描述高炉阻力的KCarPmBV2aB1nG.7P方T2 程式简化、变换而来的。宝钢采用K值
判断炉况,高炉长期保持顺行稳定,实现了高炉利用煤气热能和化学能达到降低
燃
料比,降
低能
耗的良好
效果
。
式中 K值计 在
算时,热
风压力
PB和炉
顶压力
PT易
于
获得,炉腹煤气量VBG却不能直接得到,但VBG对操作和设计高炉都具有重要意
3) 经过60、70年代的实践至80年代,提出了“高产、低耗、优质 的六字方针”。
4) 1980年又总结提出了“高产、低耗、优质、长寿”的八字方针 ,这方针一直延续到21世纪,在此过程中逐步建立了一套科学且附合 实际的评价方法。
5) 2008年在落实科学发展观,实现钢铁工业可持续发展的大背景 下,总结提出了 “高效、低耗、优质、长寿、环保”十字方针。实践 中为了突出低耗和环保,次序又调为“低耗、环保、优质、长寿、高 效”,把追求高产(高利用系数)转变为降低燃料比,从而达到高效的 目的。其中追求“高效”包括高效利用资源、高效利用能源和降低消 耗,把降低燃料比放到追求“高效”之首。
富氧率 % 0 1 2 3 4 5
利用系数 t/m3.d 2.23 2.33 2.38 2.43 2.48 2.52
冶炼强度 t/m3.d 1.126 1.176 1.203 1.229 1.253 1.274
入炉风量 Nm3/min. 7402.2 7379.7 7222.4 7067.7 6915.7 6766.3
义。
炉腹煤气量VBG与鼓风量、富氧量、喷吹物的数量和成分、湿分等因 素有关。在高炉生产喷吹煤粉的条件下,一般VBG的简便计算式为:
VBG
1.21VB
2VO2
44.8WB (VB 18000
VO2 )
22.4PC • H 120
式中: VB 为不包括富氧的风量 Nm3; WB 为湿分,g/Nm3; PC 为喷煤粉量,Kg/h;
4、树立高炉冶炼强化的新观念
陈旧的高炉冶炼强化观为:单位容积高炉多烧焦炭多出铁。
从这种观
念出发形成的高冶炼强化观认为:在焦比一定的条件下,提高冶炼强度就等于提
高利用系数。反之提高利用系数的办法就是提高冶炼强度。可见,用冶炼强度来
衡量高炉的强化程度是不正确的。因此,必须建立新的高炉冶炼强化观。
高炉透气性指数:
旧的冶炼强度观是多鼓风、多烧焦炭、多出铁,用新的强化冶炼 观分析则刚好相反,富氧率高了,鼓风小了,冶炼强度高了,提高了 利用系数。
表2 燃料比对利用系数和冶炼强度的影响(富氧率为1%)
燃料比 Kg/t 520 510 500 490 480
利用系数 t/m3.d 2.20 2.26 2.31 2.36 2.41
H 为煤粉的含,H量%。
其中,大小不同级别高炉的VBG和炉缸面积是不一样的,为了把VBG 用于大小不同级别的高炉,将炉腹煤气量(VBG)除以炉缸面积定义为高 炉炉腹煤气量指数(XBG)用作高炉强化的指标,比冶炼强度具有更强的 科学合理性和代表性。
这里有一个最基本的道理:空气中的N2基本不参加化学反应,N2在 空气中占79%,但是N2被加热消耗大量的能量并带走大量的热量。降低 炉腹煤气量指数,就是改善透气性,降低能耗,因此这是降低能耗,节
· v
高炉平均日产量(p t / d ) (t/m3
高炉容积(V m 3 )
d)
高炉容积为铁口中心线平面以上至料线平面以下的容积(m3)
高炉炉缸断面积利用系数(t/m2·d)
· A
高炉平均日产量 (p 炉缸断面积 ( A
t m2
/ )
d
)
(t/m2
d)
以上两种方法都有一定道理,炉缸断面积表达法更为合理。
本文将张寿荣院士以及著名设计大师项钟庸等炼铁专家近年来 发表的关于高炉技术操作方针和高炉冶炼强化等新观念、新理论进 行了汇集,编写出了本篇文章。
2、高炉炼铁技术操作方针的进步与发展
1) 解放初至1958年大办钢铁期间高炉操作方针:大风(全风量操 作)高温4字方针。
2) 经过大办钢铁后,1959年总结出:“以原料为基础,以风为纲 ,提高冶炼强度与降低焦比并举”的操作方针。
能减排强化高炉冶炼的新观念。
X
BG
4VBG
D 2
式中D为高炉炉缸直径。
影响XBG的因素和XBG的实用价值: 设计大师项钟庸根据宝钢4000m3级高炉作了具体计算(三个表),反 映出富氧率、燃料比和炉顶压力三大因素对XBG的影响,并从中得出高炉 冶炼强化的新观念。
表1 富氧对利用系数和冶炼强度的影响
3、科学评价高炉利用系数
利用系数:v
冶炼强度( x) 燃料比( y)
实际上冶炼强度与燃料比的关系存在着一个燃料比最低的冶 炼强度区域,这个区域一般在1.05~1.15的范围内 。
图1 高炉冶炼强度与燃料比的关系
由利用系数的公式可知
1) 当燃料比升高超过冶炼强度升高时,提高冶炼强度、利用系数反而会 降低;
2) 实践经验证明:低的燃料比才能有高的利用系数; 3) 降低燃料比对提高利用系数的作用和影响远大于提高冶炼强度; 各级高炉利用系数的确定(设计规范)
1000m3级:2.0~2.4t/m3·d 2000m3级:2.0~2.35t/m3·d
3000m3级高炉:2.0~2.30t/m3·d
高炉容积利用系数:(t/m3·d)