-半导体-大规模集成电路工艺流程(精)
半导体集成电路工艺流程
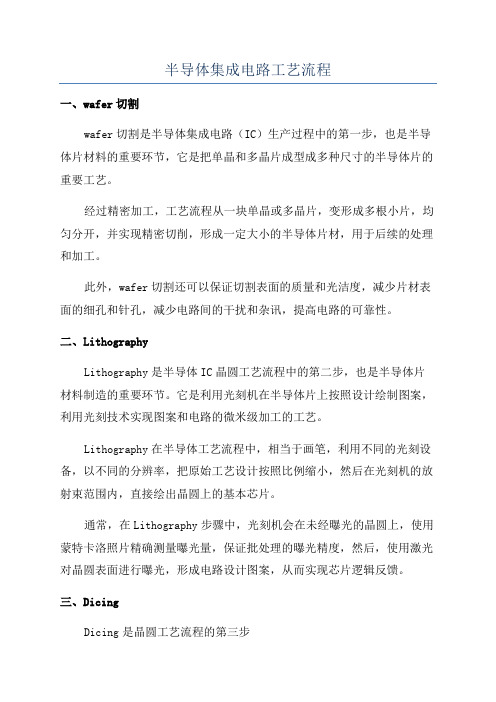
半导体集成电路工艺流程
一、wafer切割
wafer切割是半导体集成电路(IC)生产过程中的第一步,也是半导体片材料的重要环节,它是把单晶和多晶片成型成多种尺寸的半导体片的重要工艺。
经过精密加工,工艺流程从一块单晶或多晶片,变形成多根小片,均匀分开,并实现精密切削,形成一定大小的半导体片材,用于后续的处理和加工。
此外,wafer切割还可以保证切割表面的质量和光洁度,减少片材表面的细孔和针孔,减少电路间的干扰和杂讯,提高电路的可靠性。
二、Lithography
Lithography是半导体IC晶圆工艺流程中的第二步,也是半导体片材料制造的重要环节。
它是利用光刻机在半导体片上按照设计绘制图案,利用光刻技术实现图案和电路的微米级加工的工艺。
Lithography在半导体工艺流程中,相当于画笔,利用不同的光刻设备,以不同的分辨率,把原始工艺设计按照比例缩小,然后在光刻机的放射束范围内,直接绘出晶圆上的基本芯片。
通常,在Lithography步骤中,光刻机会在未经曝光的晶圆上,使用蒙特卡洛照片精确测量曝光量,保证批处理的曝光精度,然后,使用激光对晶圆表面进行曝光,形成电路设计图案,从而实现芯片逻辑反馈。
三、Dicing
Dicing是晶圆工艺流程的第三步。
_半导体_大规模集成电路工艺流程(精)
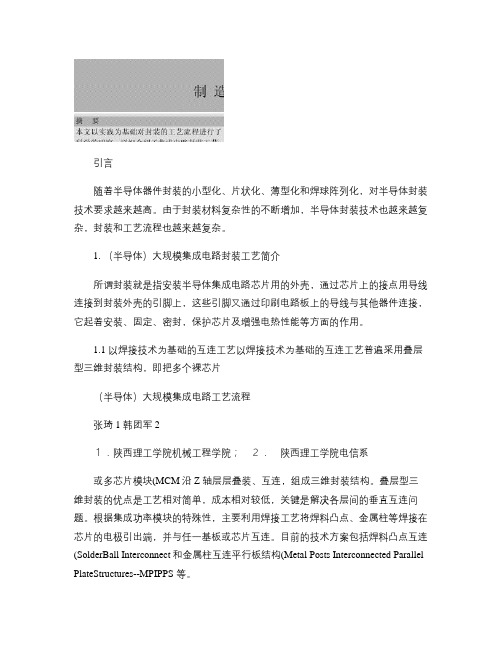
引言随着半导体器件封装的小型化、片状化、薄型化和焊球阵列化,对半导体封装技术要求越来越高。
由于封装材料复杂性的不断增加,半导体封装技术也越来越复杂,封装和工艺流程也越来越复杂。
1. (半导体)大规模集成电路封装工艺简介所谓封装就是指安装半导体集成电路芯片用的外壳,通过芯片上的接点用导线连接到封装外壳的引脚上,这些引脚又通过印刷电路板上的导线与其他器件连接,它起着安装、固定、密封,保护芯片及增强电热性能等方面的作用。
1.1 以焊接技术为基础的互连工艺以焊接技术为基础的互连工艺普遍采用叠层型三维封装结构,即把多个裸芯片(半导体)大规模集成电路工艺流程张琦1 韩团军21.陕西理工学院机械工程学院;2.陕西理工学院电信系或多芯片模块(MCM沿Z 轴层层叠装、互连,组成三维封装结构。
叠层型三维封装的优点是工艺相对简单,成本相对较低,关键是解决各层间的垂直互连问题。
根据集成功率模块的特殊性,主要利用焊接工艺将焊料凸点、金属柱等焊接在芯片的电极引出端,并与任一基板或芯片互连。
目前的技术方案包括焊料凸点互连(SolderBall Interconnect和金属柱互连平行板结构(Metal Posts Interconnected Parallel PlateStructures--MPIPPS 等。
1.2以沉积金属膜为基础的互连工艺多采用埋置型三维封装结构,即在各类基板或介质中埋置裸芯片,顶层再贴装表贴元件及芯片来实现三维封装结构。
其特点是蒸镀或溅射的金属膜不仅与芯片的电极相连,而且可以构成电路图形,并连至其他电路。
其最大优点是能大大减少焊点,缩短引线间距,进而减小寄生参数。
另外,这种互连工艺采用的埋置型三维封装结构能够增大芯片的有效散热面积,热量耗散可以沿模块的各个方向流动,有利于进一步提高集成模块的功率密度,以沉积金属膜为基础的互连工艺有薄膜覆盖技术和嵌入式封装等。
2. (半导体)大规模集成电路封装工艺流程2.1 (半导体大规模集成电路封装前道工程TAPE MOUNT →SAWING →DIE ATTACH →WIRE BONDT A P E M O U N T 工程是半导体ASSEMBLY 工程中的第一道工序,其目的在于将要加工的WAFER 固定,便于自动化加工。
大规模集成电路的全制造流程

大规模集成电路的全制造流程一、设计阶段。
集成电路的设计就像是在搭建一座超级复杂的大楼蓝图。
工程师们得先确定这个集成电路要实现啥功能,是用来处理图像呢,还是用来做数据运算之类的。
这就像我们决定盖个写字楼还是住宅楼一样。
他们要使用专门的设计软件,在电脑上画电路原理图。
这个原理图可复杂啦,就像一张密密麻麻的蜘蛛网,里面到处都是线路连接着不同的电子元件。
这些元件就像大楼里的一个个小房间,各自有着不同的用途。
比如说有一些是用来存储数据的,就像大楼里的仓库;还有一些是用来处理数据的,就像大楼里的办公室。
而且在设计的时候,工程师们还得考虑很多实际的问题呢。
比如说功耗,就像大楼的耗电量一样,要是功耗太大,那这个集成电路就像个电老虎,太费电可不行。
还有信号完整性,这就好比大楼里的各种管道要保证水或者气流畅通一样,信号要是不完整,那这个集成电路工作起来就会出问题。
二、制造材料准备。
设计好了之后,就得准备制造的材料啦。
硅片可是集成电路制造的基础材料,它就像大楼的地基一样重要。
硅片的纯度要求特别高,几乎要达到百分之九十九点九九九九这么纯呢。
这就像我们盖楼,地基要是不牢固,那楼肯定盖不好。
除了硅片,还需要一些其他的材料,像光刻胶之类的。
光刻胶这个东西可神奇了,它就像一个超级敏感的小助手。
在后面的制造过程中,光刻胶可以在光照下发生变化,从而帮助我们把设计好的电路图案转移到硅片上。
三、光刻。
光刻这个步骤可太关键啦。
想象一下,我们要把设计好的那些超级复杂的电路图案一点一点地刻到硅片上,就像在一块豆腐上雕刻精美的图案一样。
先把光刻胶均匀地涂在硅片上,这就像给豆腐先涂上一层特殊的颜料。
然后用一种带有电路图案的掩模版,就像一个带有图案的印章一样,通过光照把图案转移到光刻胶上。
光刻胶在光照的地方会发生变化,这样就形成了我们想要的电路图案的轮廓。
这个过程就像我们用印章在涂了颜料的豆腐上印出图案一样,只不过这个过程超级精细,精度要达到纳米级别呢。
半导体制造工艺流程简介
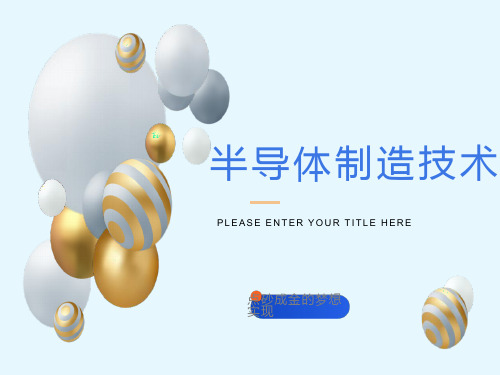
PLEASE ENTER YOUR TITLE HERE
点砂成金的梦想实现
在很久很久以前,大河边上,我们的祖先有一个梦想,他们希望把石头变成值钱的黄金。但是他们一直没有实现他们的梦想
大河滚滚东流,岁月的车轮终于驶入20世纪。三个美国科学家,巴恩,肖特莱,也为这个梦想而苦苦追寻,最终他们找到了让一堆泥砂变成比黄金还贵重的东西的方法。 下面我们将谈谈点石成金的半导体技术。
厂房内:0.25工艺下,在0.1微米的尘埃不能超过100级,就是在1立方米空气中,直径大于0.1微米的尘埃不能超过100个。现在的要求是1级
二是超高纯度技术
03
02
01
要求制造过程中所用的材料、气体和试剂等必须是超纯的。目前已能控制的有害杂质含量可达到ppb〈十亿分之一)以下
芯片内部之间的线很细,芯片很薄,很容易被损坏。
设计是指半导体芯片的设计技术,以开发新的功能或使最终产品获得优良的性能价格比,现在一般采用计算机辅助设计
制造:这是我们要重点介绍的)
半导体工艺--- “三超”技术:
(一)超净技术
即要求严格控制工作环境中的尘埃,做到无污染生产。目前的尘埃颗粒直径已能控制在0.1微米
也就是常说的超净厂房,进入厂房要穿超净服,经过三个吸尘门。
.元素半导体 :如锗、硅、硒、硼、碲、锑等 ,现在说的半导体主要指硅,硅就是我们常见的泥沙。在地壳中,硅的含量仅次于氧,高于铝。
02
化合物半导体 :由两种或两种以上的元素化合而成的半导体材料 ,如砷化镓、磷化锢、锑化锢、碳化硅、硫化镉及镓砷硅 等。
03
无定形半导体材料 :用作半导体的玻璃是一种非晶体无定形半导体材料,分为氧化物玻璃和非氧化物玻璃两种
集成电路的制造工艺流程

集成电路的制造工艺流程集成电路制造工艺流程是指将电子器件的元件和电路按照一定的规则和方法集成在半导体晶片上的过程。
制造工艺流程涉及到多个环节,如晶圆加工、电路图形绘制、光刻、腐蚀、沉积、复合、切割等。
下面将详细介绍集成电路的制造工艺流程。
首先,制造集成电路的第一步是选择合适的基片材料。
常用的基片材料有硅、蓝宝石和石英等。
其中,硅基片是最常用的基片材料,因为硅具有良好的热导性能和机械性能,同时也便于进行光刻和腐蚀等工艺步骤。
接下来,对基片进行晶圆加工。
晶圆加工是指将基片切割成薄片,并对其进行去杂质处理。
这一步骤非常关键,因为只有获得高质量的基片才能保证电路的性能和可靠性。
然后,根据电路设计图纸,使用光刻技术将电路图形绘制在基片上。
光刻技术是一种重要的制造工艺,主要利用分光光源、透镜和光刻胶等材料来实现。
通过光刻,可以将电路的结构图案转移到基片表面,形成精确的电路结构。
接着,进行腐蚀处理。
腐蚀是将未被光刻阻挡住的区域去除,使得电路结果清晰可见。
常用的腐蚀液有氟化氢、硝酸等。
腐蚀过程中需要严格控制时间和温度,以防止过腐蚀或不足腐蚀。
接下来,进行沉积工艺。
沉积是指利用化学反应或物理过程将金属、氧化物等材料沉积在基片表面。
沉积技术包括物理气相沉积(PVD)和化学气相沉积(CVD)等。
沉积工艺可以形成导体、绝缘体和介质等层,以实现电路的功能。
在进行复合工艺之前,还需要对电路进行电性能测试。
通过测试,可以检测电路是否存在故障和缺陷,并对其进行修复或更换。
最后一步是切割。
切割是将晶片切割成小片,以供后续封装和测试使用。
常用的切割工艺有晶圆锯切和激光切割等。
综上所述,集成电路的制造工艺流程包括基片材料选择、晶圆加工、电路图形绘制、光刻、腐蚀、沉积、复合和切割等环节。
每个环节都非常关键,需要严格控制各项参数和步骤,以保证最终产品的质量和性能。
《半导体集成电路》课件
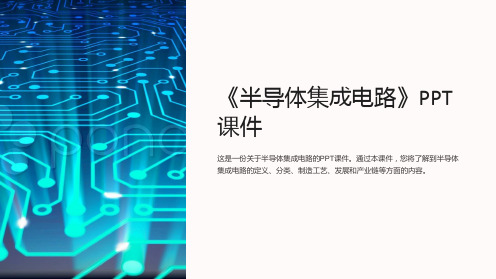
这是一份关于半导体集成电路的PPT课件。通过本课件,您将了解到半导体 集成电路的定义、分类、制造工艺、发展和产业链等方面的内容。
什么是半导体集成电路?
半导体集成电路是一种将多个电子元件组合在一起的电路,利用半导体材料 的特性实现电子信号处理与控制功能的器件。
பைடு நூலகம்
半导体集成电路的分类
半导体集成电路的发展
1
从TTL到MOS
从传统的晶体管技术(TTL)发展到金属氧化物半导体技术(MOS),实现更 高的集成度和更低的功耗。
2
LSI、VLSI及以上集成度的发展
集成度逐步提高,从LSI(大规模集成电路)发展到VLSI(超大规模集成电路) 以及更高的集成度。
3
半导体集成电路的应用和前景
广泛应用于计算机、通信、消费电子、汽车等领域,并具有广阔的发展前景。
半导体集成电路是现代电子技 术进步的核心,深刻改变了人 类社会的各个方面。
发展趋势和未来展望
随着科技的发展,半导体集成 电路将继续向更高的集成度、 更低的功耗和更多的应用领域 发展。
个人对半导体集成电路 的理解和观点
半导体集成电路是现代科技的 基石,让我们能够享受到如此 丰富多样的高科技产品和服务。
半导体集成电路的制造工艺
1
P型和N型半导体的制作
通过控制材料的掺杂和热处理,制作出具有不同电子特性的P型和N型半导体材 料。
2
晶体管和二极管的制作
利用半导体材料的特性,通过掺杂和干涉等工艺制造晶体管和二极管等基本的电 子元器件。
3
集成电路的制作流程
包括光刻、薄膜沉积、刻蚀、离子注入、扩散、金属沉积等一系列工艺步骤。
半导体集成电路的产业链
半导体制造工艺流程简介
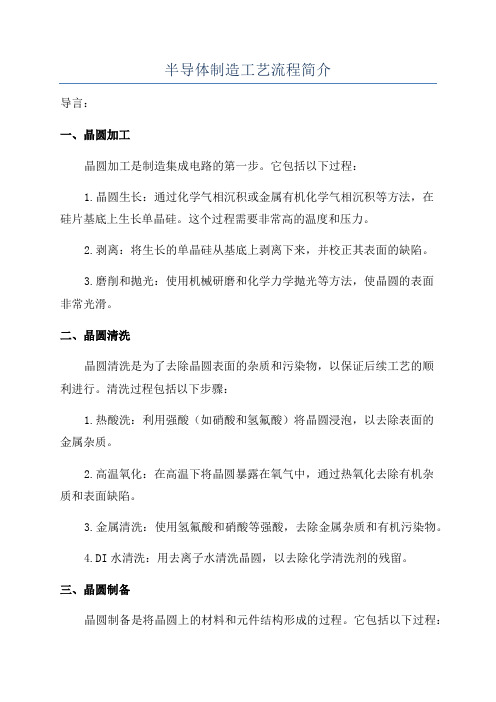
半导体制造工艺流程简介导言:一、晶圆加工晶圆加工是制造集成电路的第一步。
它包括以下过程:1.晶圆生长:通过化学气相沉积或金属有机化学气相沉积等方法,在硅片基底上生长单晶硅。
这个过程需要非常高的温度和压力。
2.剥离:将生长的单晶硅从基底上剥离下来,并校正其表面的缺陷。
3.磨削和抛光:使用机械研磨和化学力学抛光等方法,使晶圆的表面非常光滑。
二、晶圆清洗晶圆清洗是为了去除晶圆表面的杂质和污染物,以保证后续工艺的顺利进行。
清洗过程包括以下步骤:1.热酸洗:利用强酸(如硝酸和氢氟酸)将晶圆浸泡,以去除表面的金属杂质。
2.高温氧化:在高温下将晶圆暴露在氧气中,通过热氧化去除有机杂质和表面缺陷。
3.金属清洗:使用氢氟酸和硝酸等强酸,去除金属杂质和有机污染物。
4.DI水清洗:用去离子水清洗晶圆,以去除化学清洗剂的残留。
三、晶圆制备晶圆制备是将晶圆上的材料和元件结构形成的过程。
它包括以下过程:1.掩膜制作:将光敏材料涂覆在晶圆表面,通过光刻技术进行曝光和显影,形成图案化的光刻胶掩膜。
2.沉积:通过物理气相沉积或化学气相沉积等方法,在晶圆上沉积材料层,如金属、氧化物、硅等。
3.腐蚀:采用湿法或干法腐蚀等技术,去除晶圆上不需要的材料,形成所需的结构。
4.清洗:再次进行一系列清洗步骤,以去除腐蚀产物和掩膜残留物,保证材料层的质量。
四、材料获取材料获取是指在晶圆上制造晶体管、电阻器、电容器等器件结构的过程。
它包括以下步骤:1.掺杂:通过离子注入或扩散等方法,在晶圆上引入有选择性的杂质,以改变材料的导电性或断电性能。
2.退火:通过高温热处理,消除杂质引入过程中的晶格缺陷,并使掺杂的材料达到稳定状态。
3.金属-绝缘体-金属(MIM)沉积:在晶圆上沉积金属、绝缘体和金属三层结构,用于制造电容器。
4.金属-绝缘体(MIS)沉积:在晶圆上沉积金属和绝缘体两层结构,用于制造晶体管的栅极。
五、封装和测试封装是将晶圆上制造的芯片放在封装底座上,并封装成可插入其他设备的集成电路。
超大规模集成电路及其生产工艺流程

超大规模集成电路及其生产工艺流程超大规模集成电路(VLSI)是一种制造技术,它在一片硅晶圆上集成了大量的电子器件组件,如晶体管、电阻、电容和电感等。
VLSI的发展使得计算机芯片和其他电子设备变得更小、更强大和更可靠。
本文将介绍VLSI及其生产工艺流程的完整内容。
首先,VLSI的发展与摩尔定律息息相关。
根据摩尔定律,集成电路上可容纳的晶体管数量每隔18-24个月就会翻倍。
这种指数级增长使得VLSI成为现代电子设备中最重要的组成部分之一VLSI的生产工艺流程可以分为几个主要步骤。
首先是晶圆准备,这涉及将硅晶圆切割成薄片,并对其进行清洗和涂覆。
接下来是光刻,这是将电路图案投影到硅片上的过程。
通过使用掩膜和光刻胶,可以在硅片上形成图案的副本。
接下来是蚀刻,通过使用化学气相或湿式腐蚀剂去除不需要的材料,从而形成多层电路的结构。
然后是沉积,这是在蚀刻后使用物理或化学方法向硅片上沉积材料,如金属或绝缘体。
这些材料可以作为导线、电容或电阻等电子元件的基础。
再来是清洗和抛光,这是为了去除生产过程中产生的残留物,并使硅片表面平滑。
接下来是刻蚀,通过使用化学气相或湿式腐蚀剂去除不需要的材料,从而形成更加精细的电路结构。
最后是封装,这是将芯片封装到保护材料中,以确保其正常运行,并且可以与其他电子设备连接。
VLSI的生产工艺还包括一系列的测试和质量控制步骤。
这些测试包括测试电路的正确性、性能和可靠性。
质量控制步骤涉及监测和控制生产过程中的各个环节,以确保产品的一致性和性能。
VLSI的发展对现代社会产生了深远的影响。
它使得计算机变得更小、更快、更强大,并为人们带来了各种便利。
VLSI也被广泛应用于通信、医疗、汽车和军事等领域,推动了这些领域的技术进步。
总之,超大规模集成电路及其生产工艺流程是现代电子设备中最重要的组成部分之一、通过不断发展和创新,VLSI不仅使电子设备变得更小、更强大,还推动了科技的进步。
VLSI的生产工艺流程包括晶圆准备、光刻、蚀刻、沉积、清洗和抛光、刻蚀、封装等多个步骤。
- 1、下载文档前请自行甄别文档内容的完整性,平台不提供额外的编辑、内容补充、找答案等附加服务。
- 2、"仅部分预览"的文档,不可在线预览部分如存在完整性等问题,可反馈申请退款(可完整预览的文档不适用该条件!)。
- 3、如文档侵犯您的权益,请联系客服反馈,我们会尽快为您处理(人工客服工作时间:9:00-18:30)。
引言随着半导体器件封装的小型化、片状化、薄型化和焊球阵列化,对半导体封装技术要求越来越高。
由于封装材料复杂性的不断增加,半导体封装技术也越来越复杂,封装和工艺流程也越来越复杂。
1. (半导体)大规模集成电路封装工艺简介所谓封装就是指安装半导体集成电路芯片用的外壳,通过芯片上的接点用导线连接到封装外壳的引脚上,这些引脚又通过印刷电路板上的导线与其他器件连接,它起着安装、固定、密封,保护芯片及增强电热性能等方面的作用。
1.1 以焊接技术为基础的互连工艺以焊接技术为基础的互连工艺普遍采用叠层型三维封装结构,即把多个裸芯片(半导体)大规模集成电路工艺流程张琦1 韩团军21.陕西理工学院机械工程学院;2.陕西理工学院电信系或多芯片模块(MCM沿Z 轴层层叠装、互连,组成三维封装结构。
叠层型三维封装的优点是工艺相对简单,成本相对较低,关键是解决各层间的垂直互连问题。
根据集成功率模块的特殊性,主要利用焊接工艺将焊料凸点、金属柱等焊接在芯片的电极引出端,并与任一基板或芯片互连。
目前的技术方案包括焊料凸点互连(SolderBall Interconnect和金属柱互连平行板结构(Metal Posts Interconnected Parallel PlateStructures--MPIPPS 等。
1.2以沉积金属膜为基础的互连工艺多采用埋置型三维封装结构,即在各类基板或介质中埋置裸芯片,顶层再贴装表贴元件及芯片来实现三维封装结构。
其特点是蒸镀或溅射的金属膜不仅与芯片的电极相连,而且可以构成电路图形,并连至其他电路。
其最大优点是能大大减少焊点,缩短引线间距,进而减小寄生参数。
另外,这种互连工艺采用的埋置型三维封装结构能够增大芯片的有效散热面积,热量耗散可以沿模块的各个方向流动,有利于进一步提高集成模块的功率密度,以沉积金属膜为基础的互连工艺有薄膜覆盖技术和嵌入式封装等。
2. (半导体)大规模集成电路封装工艺流程2.1 (半导体大规模集成电路封装前道工程TAPE MOUNT →SAWING →DIE ATTACH →WIRE BONDT A P E M O U N T 工程是半导体ASSEMBLY 工程中的第一道工序,其目的在于将要加工的WAFER 固定,便于自动化加工。
过程实质是用T AP E 从背面将WAFER 固定在RING 上。
现在所用的TAPE 成卷筒状,一面有黏性,通常使用的TAPE 为蓝色,具有弹性,呈半透明状。
通常使用的TAPE 缺点是随时间的增加黏性逐渐增大,一般在2~3天内加工完毕对产品没有影响。
TAPE MOUNT 完成后要求在TAPE 与WAFER 间粘贴平整,如果背面存在气泡,在SAWING 时切割好的DIE 会脱离TAPE 翘起,将切割好的BLADE 损坏,同时也损坏了DIE 。
因此T/M后应检查背面的粘合情况,如有少数气泡,可用指甲背面轻轻将气泡压平,若压不平,可用刀片将TAPE 划破一点,放出气泡中的空气,然后压平。
气泡面积不能大于DIE 面积的1/4。
S A W I N G 工程是将W A F E R 上的CHIP 分离的过程,T/M完毕的WAFER 送至SAWING 工程,按照FAB 时形成的SCRIBE LINE 进行切割,将连在一起的CHIP 分开,形成每片IC 的核心。
现在最常用的是Blade Sawing ,将金刚石Blade 装在高速旋转的SPINDLE 上,靠机械力量将Wafer 划开。
由于通过高速旋转的Blade 对Wafer 进行切割,会产生大量的热,因而再加工时需进行冷却。
为防止污染Wafer ,采用DI WATER 进行冷却,但DI WATER电阻率高达17-18M Ω,无法消除加工时产生的静电,增加D I WATER 的导电性,消除静电,在其中充入CO 2,降低电阻率。
根据Blade 在Wafer 上的切割深度,通常分为Half Cutting和Full Cutting ,Half Cutting 指切削深度占Wafer 厚度70%~80%的加工,而Full Cutting 的切削深度为Wafer 厚度的95%~105%,如图1所示。
过100%的原因是将Wafer 完全切开,另外5%是切在Tape 上的,但不可将Tape 切破。
现在通常采用Full Cutting 方式进行加工。
根据切削时Blade 的运动轨迹,可分为R O U N D P A T T E R N 和S Q U A R E PATTERN 两种,如图2所示。
显然,Round Pattern 方式更节约时间,通常我们采用这种方式进行加工。
新Blade 在使用前,由于表面有毛刺,为-保证被加工的Wafer 质量,预先要用一片没有用的Wafer 进行试切削,将表面的毛刺磨光,这个过程称为Dressing ,考虑到加工中不断磨损,Dressing 用的Wafer 应比正常的Wafer 厚一点。
Die Attach是将Die (也叫Chip )黏合到LEAD FRAME的PAD 上的过程,目的是固定Die ,以便于以后的加工,同时将Chip 工作时发出的热量散发出去,保护其不会损坏。
Lead Frame 是一种固定Chip ,为Chip 提供引脚,并提供Chip 与外界进行信息交换的材料,Lead Frame一般由铜和不锈钢制成。
通常用来将C h i p 、P a d 粘合起来。
AG-EPOXY 是一种糨糊状的胶体,具有一定的黏性,主要成分是银,它的导电导热性较好,用它将Chip 粘在Lead Frame 上,有助于将Chip 工作时产生的热量散发出去。
图3 芯片接合方式粘贴时,AG-EPOXY 是糊状,但为了固定Chip ,必须使其固化,才能将Chip 彻底固定。
AG-EPOXY 的固化不能像胶水一样自然固化。
根据试验,如果A G -E P O X Y 未经处理而自然固化,一周后Chip 还可以用手移动,一个月后才能完全固定住。
所以,为提高生产效率,采用加热的方式,提高Epoxy 固化速度。
E p o x y 固化方法有两种,一种是Oven Cure, 另一种是Snap Cure 。
Oven即烘箱。
Oven Cure 即将D/A完成的产品送入烘箱中烘烤,以使Ag-epoxy 完全固化。
加热的温度为左右,加热时间为分钟。
Snap Cure 则采用高频加热方式,可使Ag-Epoxy 快速固化,一般加热时间为60-90秒。
在Snap Cure 设备中,每段温度不同,每段间距很短。
Snap Cure 生产效率明显提高,而且Snap Cure设备直接与D/A设备相连,每条Lead Frame 加工完毕立即送S n a p C u r e 设备, 与D i e Attach 生产同时进行,几乎不占用工作时间,缺点是设备成本较高。
WIRE BOND 工程用金线或铝线把CHIP 上的 PAD 与 LEAD FRAME 的内部LEAD 连接起来,以实现 CHIP 与其外部电路的电气特性。
在整个ASSEMLY 工程中WIRE BOND是一个极为重要的工程,它属于FRONT 工程,由于设备种类多,数量多,而且操作较为复杂,形成不良的因素较多,所以它是个质量较难控制的工程也是一个极为复杂的过程。
除了需要较高识别精度的PRS 系统外,还需要极其精密的机械设备和计算机控制技术。
3 结论(半导体大规模集成电路封装和工艺流程在工程实践中的技术和条件要比上述的复杂得多,而且要有较高的工作经验,随着计算机的发展和各种精密机械设备技术的发展,对于传统的封装技术有了很大的简化,但是随着现在电子线路要求小型化,低能化,以及参数要求精确度的提高,封装技术会变得越来越复杂。
图1 Cutting加工方式图2 Blade切削轨迹下面以我台1143KHz 干扰机天线调配网络调试为例,介绍一下方程求根原理的具体应用。
天调网络如图5,a=36-j35,L0=40uh,L1=51.45uh,L2=47.5uh,C1=1000pf,C 2=850pf。
L 0是防雷线圈,C 0隔直电容, L1C1是702khz 阻塞网络,L 2C 2是阻抗匹配。
首先调整并联阻塞网络L1C1。
从网络中将L1C1两端断开,并接至导纳电桥,测量其阻抗。
如果没有电抗,则处于谐振,电抗呈感性说明电感值偏小(依据图1),反之则电感值偏大。
此时为粗调,电感调节量可以大一些,以2圈为宜,主要判断L 1谐振点的范围。
加大2圈,再测电感,呈容型说明谐振点在这其中。
如果还呈感性,继续加大电感直至电抗呈容性。
假如电感调至最大任呈感性则说明网络元件计算有误,需重新设计。
找到L 1谐振点的范围以后,要细调L 1,调节量要小一些,以1/4圈为宜,调节电抗值至最小,这样并联阻塞网络就调节完毕。
采用这个方法可以迅速判断网络设计的正确性并找出谐振点。
由L 2C2可以判断Z 0j 函数图形的开口向下,并且过顶点取其右半边,如图6。
图6将导纳电桥接在C2两端,测量网络输出阻抗,阻抗呈容性,电感偏大,减小2圈(此时主要判断谐振点,电感调节量可以大一些)直至电抗呈感性。
如果一直是容性则说明网络设计或安装有误,需要重新设计安装。
找到L 2的范围之后,仔细调节L 2,电感变化量要小一些,将Z0的值调到近似馈线的特性阻抗,调试完毕。
利用方程求根法进行天调网络的调试一般分三个步骤,一)是按照网络设计图纸将可以利用方程求根法调试的网络逐个换算出关于可调元件的函数并画出图形,二)依据图形进行粗调,确定元件的谐振点范围,三)确定了范围就要对元件细调,找到最佳点。
总之利用好方程求根法可在调试中达到事半功倍的效果。