氧气底吹熔炼—鼓风炉还原炼铅新技术
底吹炉高铅渣还原的新方法
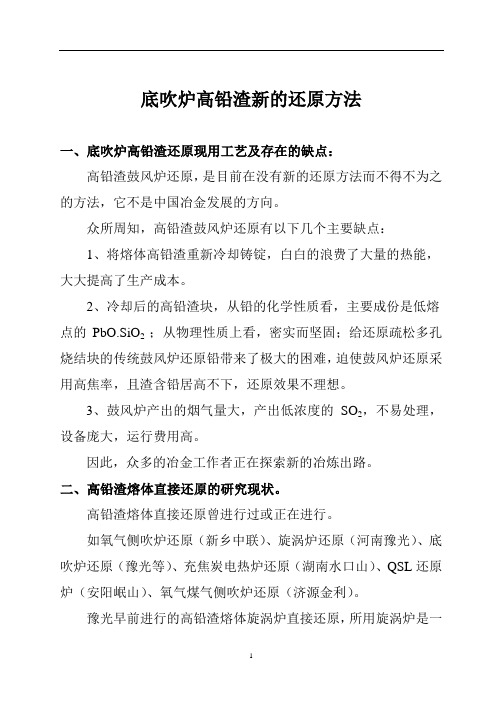
底吹炉高铅渣新的还原方法一、底吹炉高铅渣还原现用工艺及存在的缺点:高铅渣鼓风炉还原,是目前在没有新的还原方法而不得不为之的方法,它不是中国冶金发展的方向。
众所周知,高铅渣鼓风炉还原有以下几个主要缺点:1、将熔体高铅渣重新冷却铸锭,白白的浪费了大量的热能,大大提高了生产成本。
2、冷却后的高铅渣块,从铅的化学性质看,主要成份是低熔点的PbO.SiO2 ;从物理性质上看,密实而坚固;给还原疏松多孔烧结块的传统鼓风炉还原铅带来了极大的困难,迫使鼓风炉还原采用高焦率,且渣含铅居高不下,还原效果不理想。
3、鼓风炉产出的烟气量大,产出低浓度的SO2,不易处理,设备庞大,运行费用高。
因此,众多的冶金工作者正在探索新的冶炼出路。
二、高铅渣熔体直接还原的研究现状。
高铅渣熔体直接还原曾进行过或正在进行。
如氧气侧吹炉还原(新乡中联)、旋涡炉还原(河南豫光)、底吹炉还原(豫光等)、充焦炭电热炉还原(湖南水口山)、QSL还原炉(安阳岷山)、氧气煤气侧吹炉还原(济源金利)。
豫光早前进行的高铅渣熔体旋涡炉直接还原,所用旋涡炉是一园形竖炉,风口略向下并偏离中心轴线,鼓风时熔体成旋涡旋转,用焦粒作还原剂,传热传质良好,还原速度快。
但终因墙体耐火材料抗不住熔体的冲刷而仃止了试验。
底吹炉还原是QSL所采用的方法,它所用的还原剂是粉煤,据传瓜州和池州也在试验用粉煤底吹炉还原。
豫光则采用了天然气加粒煤(焦),已成功用于生产,取代了鼓风炉,有关炉子的详细数据没有报道。
充焦电热还原实质上是借鉴了一种炼锌电炉,高铅渣熔体从上而下通过充满焦炭的竖炉,竖炉上、下方有电极,焦炭柱成为发热体而变灼热,将氧化铅还原,还原后的铅和炉渣流到熔池分层。
此法的试验进展情况不详。
金利进行的氧气煤气侧吹炉还原高铅渣正在试验之中。
可以认为:将底吹炉的风咀用于侧吹炉是可行的,侧吹炉还原效果也是好的。
上述还原工艺相比较,大规模、加高温熔体、间断还原作业在能耗上和技经指标上,都具有明显的优势。
氧气底吹转炉炼铅法
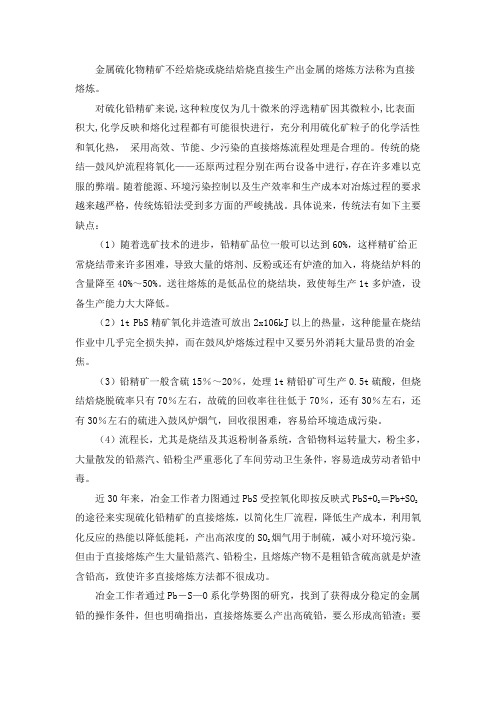
金属硫化物精矿不经焙烧或烧结焙烧直接生产出金属的熔炼方法称为直接熔炼。
对硫化铅精矿来说,这种粒度仅为几十微米的浮选精矿因其微粒小,比表面积大,化学反映和熔化过程都有可能很快进行,充分利用硫化矿粒子的化学活性和氧化热,采用高效、节能、少污染的直接熔炼流程处理是合理的。
传统的烧结—鼓风炉流程将氧化——还原两过程分别在两台设备中进行,存在许多难以克服的弊端。
随着能源、环境污染控制以及生产效率和生产成本对冶炼过程的要求越来越严格,传统炼铅法受到多方面的严峻挑战。
具体说来,传统法有如下主要缺点:(1)随着选矿技术的进步,铅精矿品位一般可以达到60%,这样精矿给正常烧结带来许多困难,导致大量的熔剂、反粉或还有炉渣的加入,将烧结炉料的含量降至40%~50%。
送往熔炼的是低品位的烧结块,致使每生产1t多炉渣,设备生产能力大大降低。
(2)1t PbS精矿氧化并造渣可放出2x106kJ以上的热量,这种能量在烧结作业中几乎完全损失掉,而在鼓风炉熔炼过程中又要另外消耗大量昂贵的冶金焦。
(3)铅精矿一般含硫15%~20%,处理1t精铅矿可生产0.5t硫酸,但烧结焙烧脱硫率只有70%左右,故硫的回收率往往低于70%,还有30%左右,还有30%左右的硫进入鼓风炉烟气,回收很困难,容易给环境造成污染。
(4)流程长,尤其是烧结及其返粉制备系统,含铅物料运转量大,粉尘多,大量散发的铅蒸汽、铅粉尘严重恶化了车间劳动卫生条件,容易造成劳动者铅中毒。
近30年来,冶金工作者力图通过PbS受控氧化即按反映式PbS+O2=Pb+SO2的途径来实现硫化铅精矿的直接熔炼,以简化生厂流程,降低生产成本,利用氧化反应的热能以降低能耗,产出高浓度的SO2烟气用于制硫,减小对环境污染。
但由于直接熔炼产生大量铅蒸汽、铅粉尘,且熔炼产物不是粗铅含硫高就是炉渣含铅高,致使许多直接熔炼方法都不很成功。
冶金工作者通过Pb-S—O系化学势图的研究,找到了获得成分稳定的金属铅的操作条件,但也明确指出,直接熔炼要么产出高硫铅,要么形成高铅渣;要获得含硫低的合格粗铅,就必须还原处理含铅高的直接熔炼炉渣。
氧气底吹炼铅新工艺概况
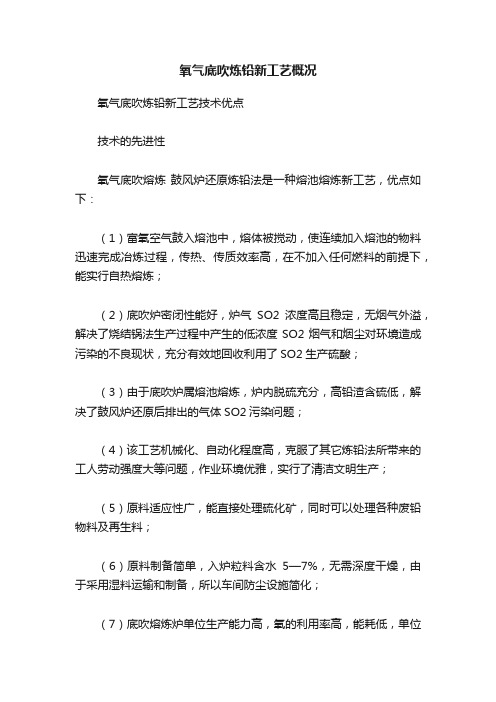
氧气底吹炼铅新工艺概况氧气底吹炼铅新工艺技术优点技术的先进性氧气底吹熔炼鼓风炉还原炼铅法是一种熔池熔炼新工艺,优点如下:(1)富氧空气鼓入熔池中,熔体被搅动,使连续加入熔池的物料迅速完成冶炼过程,传热、传质效率高,在不加入任何燃料的前提下,能实行自热熔炼;(2)底吹炉密闭性能好,炉气SO2浓度高且稳定,无烟气外溢,解决了烧结锅法生产过程中产生的低浓度SO2烟气和烟尘对环境造成污染的不良现状,充分有效地回收利用了SO2生产硫酸;(3)由于底吹炉属熔池熔炼,炉内脱硫充分,高铅渣含硫低,解决了鼓风炉还原后排出的气体SO2污染问题;(4)该工艺机械化、自动化程度高,克服了其它炼铅法所带来的工人劳动强度大等问题,作业环境优雅,实行了清洁文明生产;(5)原料适应性广,能直接处理硫化矿,同时可以处理各种废铅物料及再生料;(6)原料制备简单,入炉粒料含水5—7%,无需深度干燥,由于采用湿料运输和制备,所以车间防尘设施简化;(7)底吹熔炼炉单位生产能力高,氧的利用率高,能耗低,单位成本大大降低。
2、技术的成熟、可靠性本企业新建的氧气底吹炼铅新工艺产业化示范项目一次性投料生产的成果和各项经济技术指标达到并超过了设计指标的事实,证明了该工艺技术是成熟的,产业化生产时可靠的。
(1)作业率经过8个月的试生产,经测算作业率达90%以上。
主要停炉时间是更换氧枪,氧气底吹炉中设有4支氧枪,均由氮气和水保护,喷雾冷却效果好,氧枪平均使用寿命已达50天以上,最长时间57天。
更换氧枪时间较短,一般在2—3小时,炉衬使用至今,仍完好无损。
(2)工艺过程控制通过试生产,操作工已熟练掌握操作技能和工艺条件的控制,主要运用DCS系统对各运转设备及数据监测、观察、分析与处理,同时对氧气底吹炉加料口、放铅口、放渣口及余热锅炉加强管理,熟练掌握了氧枪检查与更换。
目技术内容项“氧气底吹熔炼—鼓风炉还原”炼铅新工艺是由氧气底吹熔炼铅精矿和鼓风炉还原高铅渣,烟气经除尘回收SO2制酸以及制O2、N2系统四大部分组成,其核心技术是氧气底吹熔炼。
科技成果——氧气底吹熔炼技术

科技成果——氧气底吹熔炼技术适用范围有色金属行业铅冶炼企业,规模5-20万t/a均可,亦适用于铜及其它硫化矿物的提取冶金企业行业现状氧气底吹熔炼技术在不断完善与提升,已取得一系列的技术进步。
铅冶炼“氧气底吹熔炼-液态铅渣直接还原”取代“氧气底吹熔炼-鼓风炉还原”,吨粗铅综合能耗由360kgce降至200kgce,吨粗铅减排422.4kgCO2。
液态铅渣直接还原升级改造投资约4000万。
氧气底吹炼铜技术工业化应用以来,吨粗铜综合能耗降至120-140kgce,比2012年全国粗铜平均能耗261.84kgce低很多。
采用氧气底吹炼铜工艺投资比采用其他炼铜工艺投资省至少10%。
目前该技术可实现节能量6万tce/a,减排约16万tCO2/a。
成果简介1、技术原理氧气底吹炼炉为一卧式圆柱体,支撑于设于硐基础的托辊之上,炉体通过齿轮转动,可绕水平轴左右转动。
炉体下部设有氧枪或还原枪,用于氧化硫化矿或还原氧化物。
由于氧气浓度高,烟气量少,炉内衬耐火材料,无冷却水套,热损失少。
铅精矿或铜精矿均可不加任何燃料,实现自然熔炼。
且系统设有烟气余热锅炉生产蒸汽发电,热能利用率高。
故氧气底吹炼铅或炼铜,目前均为世界上所有炼铅炼铜工艺中能耗最低的技术。
2、关键技术氧气底吹熔炼-液态铅渣直接还原炼铅工艺、氧气底吹熔炼-氧气底吹连续吹炼炼铜工艺、熔炼炉、还原炉、底吹连续吹炼炉、氧枪、余热锅炉等与该工艺配套的技术装备。
3、工艺流程铅硫化矿物、二次铅原料(铅膏、含铅玻璃、锌厂铅银渣、钢厂烟灰等)、熔剂及烟尘返料经配料制粒后,直接进入氧气底吹熔炼炉中进行熔炼,产出的高温SO2烟气经余热锅炉回收余热和电收尘器收尘后送两转两吸制酸;产出的一次粗铅送精炼;产出的熔融铅氧化渣直接流入还原炉。
熔融铅氧化渣与配入的熔剂、碎煤在还原炉内进行还原熔炼,也可以配入适量的铅氧化矿,产出的高温烟气经余热锅炉回收余热和收尘器收尘后送尾气脱硫;产出的二次粗铅送精炼;产出的还原炉渣直接流入烟化炉。
《铅冶金》课程标准

《铅冶金》课程标准课程代码:00520109适用专业:冶金技术学时:39学时学分:3学分开课学期:第四学期第一部分前言1.课程性质与地位《铅冶金》是冶金技术专业的主干课程,也是培养学生就业岗位必需的核心技能课程。
本课程以铅冶炼生产过程为行动领域,贯彻国家火法冶炼工职业标准,以岗位技能培养为教学目标,全面提高学生知识、能力、素质。
本课程以铅的冶炼过程为基本主线,围绕环境保护和可持续发展两大问题,着重介绍底吹炉、顶吹炉、鼓风炉、铅电解等新理念、新技术、新工艺、新设备以及技术经济分析和冶炼过程管理等知识。
同时,在操作实习和组织管理过程中可以培养学生的科学态度,激发学生的学习兴趣,培养学生的团结协作精神和组织协调能力,对职业素养的养成起着积极促进作用。
该学习领域以《冶金基础化学》、《冶金制图》、《冶金过程检测与控制》等课程为前导,为学生走上工作岗位奠定坚实的基础。
同时,也是学习《有色冶金设计原理》、《毕业设计》等后续课程的基础。
2.课程的设计思路《铅冶金》课程是现代直接炼铅新技术富氧底(顶)吹一鼓风炉还原熔炼一电解精炼等冶炼新技术为基础,按照企业真实的生产流程,依次介绍了富氧底吹技术、富氧顶吹技术、鼓风炉还原技术、电解精炼技术等冶炼工作任务,并根据完成每个工作任务对知识能力的需求,将冶炼原理、冶炼工艺、冶炼设备、冶炼操作、经济技术指标等知识融于课程教学中,实现“做、教、学”一体化。
本课程是以任务驱动的行动导向的教学模式为主,围绕铅冶炼职业能力,以铅冶金工作过程为依据,以校企合作企业为依托,以实际铅冶炼工作任务为驱动,将知识、技能和态度有机融合,根据不同的教学内容,有针对性地采用任务驱动教学法、案例教学、现场教学等多种教学方法。
第二部分课程目标1.知识目标(1)使学生能够完成铅冶炼生产的炉料准备工作,满足底吹(顶吹)等冶炼工艺对原料的要求。
(2)使学生能够掌握底吹炉熔炼的工艺及设备知识,掌握冶炼过程的工艺控制及经济技术指标。
铅冶炼氧气底吹资料
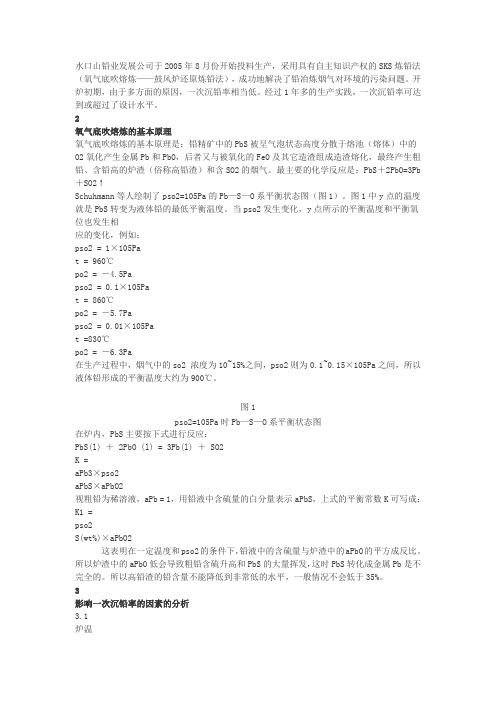
水口山铅业发展公司于2005年8月份开始投料生产,采用具有自主知识产权的SKS炼铅法(氧气底吹熔炼——鼓风炉还原炼铅法),成功地解决了铅冶炼烟气对环境的污染问题。
开炉初期,由于多方面的原因,一次沉铅率相当低。
经过1年多的生产实践,一次沉铅率可达到或超过了设计水平。
2氧气底吹熔炼的基本原理氧气底吹熔炼的基本原理是:铅精矿中的PbS被呈气泡状态高度分散于熔池(熔体)中的O2氧化产生金属Pb和PbO,后者又与被氧化的FeO及其它造渣组成造渣熔化,最终产生粗铅、含铅高的炉渣(俗称高铅渣)和含SO2的烟气。
最主要的化学反应是:PbS+2PbO=3Pb +SO2↑Schuhmann等人绘制了pso2=105Pa的Pb—S—O系平衡状态图(图1)。
图1中y点的温度就是PbS转变为液体铅的最低平衡温度。
当pso2发生变化,y点所示的平衡温度和平衡氧位也发生相应的变化,例如:pso2 = 1×105Pat = 960℃po2 = -4.5Papso2 = 0.1×105Pat = 860℃po2 = -5.7Papso2 = 0.01×105Pat =830℃po2 = -6.3Pa在生产过程中,烟气中的so2 浓度为10~15%之间,pso2则为0.1~0.15×105Pa之间,所以液体铅形成的平衡温度大约为900℃。
图1pso2=105Pa时Pb—S—O系平衡状态图在炉内,PbS主要按下式进行反应:PbS(l) + 2PbO (l) = 3Pb(l) + SO2K =aPb3×pso2aPbS×aPbO2视粗铅为稀溶液,aPb = 1,用铅液中含硫量的白分量表示aPbS,上式的平衡常数K可写成:K1 =pso2S(wt%)×aPbO2这表明在一定温度和pso2的条件下,铅液中的含硫量与炉渣中的aPbO的平方成反比。
所以炉渣中的aPbO低会导致粗铅含硫升高和PbS的大量挥发,这时PbS转化成金属Pb是不完全的。
铅冶炼过程三废污染及治理措施分析

铅冶炼过程"三废"污染及治理措施分析摘要:铅是一种非常重要的金属材料,其本身的性质也直接决定了铅的用途。
较强的耐腐蚀性、延展性等特点,使铅被广泛地应用在电池、电缆等射线防护领域当中。
但是现如今我国对铅的提取还是用较为传统的冶炼方式进行的,这种传统的冶炼方式会造成非常严重的环境污染问题。
针对目前铅冶炼过程中“三废”污染的问题进行分析,并且提出了相应的解决对策,为铅冶炼的发展提供一定参考意见。
关键词:铅冶炼;三废;治理;环境保护前言:铅是人类较早就开始使用的一种金属,我国铅资源的采集和开发也相对较早,随着我国科学技术的不断发展,各种先进的仪器设备也被广泛的应用在行业的生产和人们的生活当中。
这也使得我国对于铅金属的需求量也在不断增加。
但是铅金属熔点低,这一特性导致目前铅金属的冶炼还只能使用传统的方式进行,这种传统的冶炼方法导致冶炼废物的产生,对环境造成了非常严重的污染。
这种污染问题对于铅工业的发展也产生了非常大的影响,因此对铅工业中“三废”问题的治理进行研究具有非常重要的意义。
1铅冶炼行业会涉及到的环境问题1.1铅冶炼的基本工艺:世界上大多数国家都采用火法炼铅方式来进行铅的冶炼,通过这种方法能够对原料有较广泛的适应性,既可处理单一的铅精矿,又可处理难以选别的铅锌混合精矿,生产率和燃料利用率高。
采用直接加热,热利用率高,能耗低,冶炼设备能力大大提高,而且有利于实现机械化和自动化,提高劳动生产率。
并且随着我国的不断发展,我国铅工业的冶炼技术也在不断的提升,产量也在逐年上升,铅产业的发展已经成为我国经济发展当中非常重要的一个组成部分。
实际上铅的冶炼工艺有许多种,例如烧结-鼓风炉铅冶炼工艺,卡尔多炉铅冶炼技术,澳斯麦特铅冶炼技术等,在这些冶炼技术当中,烧结鼓风炉铅冶炼工艺是较为落后的一种较为落后的技术,不仅会产生大量的污染,而且铅的提取量也不是很高。
图1铅冶炼的工艺流程1.2铅金属行业应用的分析铅本身具有较好的抗腐蚀性和延展性,通过将铅和其他金属制成合金,能够有效的提高合金本身的性质。
富氧炼铅技术的发展及应用

工艺获得“ 2003中国有色金属工业科学技术一等奖”、 “ 2004国家科
技进步二等奖”和“2007中国矿业国际合作最佳技术创新奖”。 • 氧气底吹炼铅法已被中国九部委联合发文指定为我国首选炼铅工艺。
• 我国《有色金属工业“十二五”发展规划》中推荐的唯一粗铅冶炼工艺。
• 自2002年7月第一家应用底吹炼铅法的工厂建成投产以来,该技术已在 国内广泛应用,采用该技术共有32家,在国外第一家应用氧气底吹技术
氧气底吹炉铅精矿搭配处理其它原料实例3
原料组成 比例(%) 铅精矿 45~75 浸出渣 10~15 废蓄电池铅膏 15~40 入炉物料Pb品位 40~50
氧气底吹炼铅技术的发展及应用
氧气底吹炼铅生产实践证明,底吹炉搭配处理锌浸出渣的比例可达
50%以上,搭配处理废蓄电池铅膏的比例可达40%,入炉物料Pb的品位波 动在30%~75%均能稳定正常作业。现有生产的最低入炉物料含铅品位记
录是某厂的28%,这体现了氧气底吹炼铅技术的灵活性优势,即氧化熔炼
阶段可不产粗铅,为低品位物料的处理提供了完美的解决方案。 氧气底吹炉搭配处理锌厂浸出渣,与锌厂形成铅锌联合企业,综合回
收了各种有价金属,实现了效益的最大化,同时最大程度的减小了对环境
的影响。
氧气底吹炼铅技术的发展及应用
第三代氧气底吹技术 氧气底吹熔炼—底吹电热熔融还原炼铅法
• 还原熔炼过程需要完全依靠燃料(煤气,天然气,煤)提供热量,燃料
消耗量大,热效率较低,烟气量大,烟尘率较高。
氧气底吹炼铅技术的发展及应用
第三代氧气底吹炼铅技术 氧气底吹熔炼—底吹电热熔融还原炼铅法
• 2009年发明并通过专家论证。 • 2010年2月完成工业化装置的工程设计。 • 第一套工业生产装置2011年11月投产。
- 1、下载文档前请自行甄别文档内容的完整性,平台不提供额外的编辑、内容补充、找答案等附加服务。
- 2、"仅部分预览"的文档,不可在线预览部分如存在完整性等问题,可反馈申请退款(可完整预览的文档不适用该条件!)。
- 3、如文档侵犯您的权益,请联系客服反馈,我们会尽快为您处理(人工客服工作时间:9:00-18:30)。
氧气底吹熔炼—鼓风炉还原炼铅新技术氧气底吹熔炼—鼓风炉还原炼铅法一、氧气底吹熔炼—鼓风炉法简介氧气底吹熔炼—鼓风炉还原炼铅法工艺流程为:熔剂、铅精矿或二次铅原料及铅烟尘经配料、制粒或混捏后进行氧气底吹熔炼,产出烟气、一次粗铅和铅氧化渣,烟气经余热锅炉回收余热和电收尘器收尘后采用二转二吸工艺制酸,尾气排放,铅烟尘返回配料。
铅氧化渣经铸块后与焦块、熔剂块混合后入鼓风炉进行还原熔炼,产出炉渣、烟气和粗铅,烟气经收尘后放空,铅烟尘返回配料。
工艺主要设备包括可旋转式氧气底吹熔炼炉,多元套管结构氧枪(多通道水冷高温喷镀耐磨底吹氧枪),特殊耐磨材质的氧枪口保护砖,浅层分格富铅渣速冷铸渣机(铅氧化渣铸渣机),带弧型密封罩和垂直模式壁中压防腐余热锅炉,全封闭铅烟尘输送配料等, 新型结构鼓风炉(双排风口大炉腹角高料柱)等。
工艺的核心设备是氧气底吹熔炼炉。
熔炼炉炉型结构为可回转的卧式圆筒形,在炉顶部设有2~3 个加料口,底侧部设有3~6 个氧气喷入口,炉子两端分别设一个虹吸放铅口和铅氧化渣放出口。
炉端上方设有烟气出口。
铅精矿的氧化熔炼是在一个水平回转式熔炼炉中进行的。
铅精矿、铅烟尘、熔剂及少量粉煤经计量、配料、圆盘制粒后, 由炉子上方的气封加料口加入炉内, 工业纯氧从炉底的氧枪喷入熔池。
氧气进入熔池后, 首先和铅液接触反应, 生成氧化铅(PbO ) , 其中一部分氧化铅在激烈的搅动状态下, 和位于熔池上部的硫化铅(PbS) 进行反应熔炼, 产出一次粗铅并放出SO 2。
反应生成的一次粗铅和铅氧化渣沉淀分离后, 粗铅虹吸或直接放出,铅氧化渣则由铸锭机铸块后, 送往鼓风炉工段还原熔炼, 产出二次粗铅。
出炉SO 2 烟气采用余热锅炉或汽化冷却器回收余热, 经电收尘器收尘, 送硫酸车间处理。
熔炼炉采用微负压操作, 整个烟气排放系统处于密封状态, 从而有效防止了烟气外逸。
同时, 由于混合物料是以润湿、粒状形式输送入炉的, 加上在出铅、出渣口采取有效的集烟通风措施, 从而避免了铅烟尘的飞扬。
经实地检测, 熔炼车间岗位含铅尘低于0. 1m g/Nm 3, 完全达到了国家劳动卫生标准。
由于在熔炼炉内只进行氧化作业, 不进行还原作业, 工艺过程控制大为简单。
氧气底吹熔炼一次成铅率与铅精矿品位有关, 品位越高, 一次粗铅产出率越高。
为适应下一步鼓风炉还原要求, 铅氧化渣含铅应控制在40% 左右, 略低于烧结块含铅率, 相应地,一次粗铅产出率一般为35%~ 40% , 粗铅含S< 0. 2%。
和烧结块相比, 铅氧化渣孔隙率较低, 同时, 由于是熟料, 其熔化速度较烧结块要快些, 从而增加了鼓风炉还原工艺的难度。
但是, 经过半工业试验证明, 采用鼓风炉处理铅氧化渣在工艺上是可行的, 鼓风炉渣含Pb 可控制在4% 以内。
通过炉型改进, 渣型调整、适当控制单位时间物料处理量等措施, 渣含Pb 可望进一步降低。
另外, 尽管现有指标较传统工艺渣含Pb1. 5%~ 2% 的指标稍高, 但由于新工艺中鼓风炉渣量仅为传统工艺的50%~ 60% , 因而,鼓风炉工段铅的损失基本不增加。
在技改过程中, 利用原有的鼓风炉作适当改进即可, 这样, 可以节省大笔投资。
新工艺的一个重要组成部分是氧气站。
目前, 国内工业纯氧的制备技术有两种, 一种为传统的深冷法, 一种为变压吸附法。
前者生产能力大, 氧气纯度高, 但成本高, 氧气单位电耗一般为0. 6~ 0. 7kw h/Nm 3; 后者投资省, 成本低, 氧气单位电耗低于0. 45kw h/Nm 3。
目前, 国内1500m 3/h 的吸附制氧机组已研制成功, 其氧气纯度达93% 以上。
对于1 万t/a 规模的炼铅厂, 氧气需要量一般为700~ 800m 3/h。
采用变压吸附法制氧完全能满足中型炼铅厂技改需要, 该技术为首选方案。
氧气底吹熔炼工艺取代传统烧结工艺后, 不仅解决了SO 2 烟气及铅烟尘的污染问题, 还有如下效益:(1) 由于熔炼炉出炉烟气SO 2 浓度在12% 以上, 对制酸非常有利, 元素硫总回收率可达95%。
( 2) 熔炼炉出炉烟气温度高达1000~1100℃, 可利用余热锅炉或汽化冷却器回收余热。
(3) 采用氧气底吹熔炼, 原料中Pb、S 含量的上限不受限制, 不需要添加返料,简化了流程, 且取消了破碎设备, 从而降低了工艺电耗。
(4) 由于减少了工艺环节, 提高了Pb 及其它有价金属的回收率, 氧气底吹熔炼车间Pb 的机械损失< 0. 5%。
经测算, 采用新的工艺改造传统工艺后,粗铅单位产品综合能耗可降至400kgbm/t·粗铅以下, 达到国家规定的一级能耗标准。
熔炼过程中主要化学反应有:熔池底部铅液和喷入氧气之间的氧化反应,炉料中PbS 和熔渣中PbO 之间的反应熔炼;炉料中熔剂和熔渣中PbO 之间的造渣反应。
氧气底吹熔炼的特点是:Pb 作为O2 的载体,在铅液层中可除去一次铅中的杂质,有利于提高一次粗铅的品位;在熔渣中可加速PbS 的氧化反应,有利于降低熔炼烟尘率。
水口山工业试验遗留两个关键问题未能解决。
其一是氧枪寿命较短,其二是鼓风炉渣含铅较高。
工厂设计对氧枪和鼓风炉的工艺参数及设备结构进行了重大革新。
氧枪由工业试验的二元结构改为多元结构,氧枪冷却介质由空气改为氮气+ 软化水,并对氧枪材质、加工工艺和操作参数进行了改进,经生产验证,新型氧枪寿命由工业试验的5d ±提高至20~50d ,保证了熔炼炉的稳定操作,提高了作业率,降低了生产成本。
针对铅氧化渣还原熔炼的特殊性,工厂设计改进了鼓风炉结构,调整了鼓风炉渣型和供风操作制度,经生产验证,鼓风炉渣含铅由工业试验的7 %~9 %降至3 %~4 % ,提高了铅冶炼回收率。
水口山工业试验熔炼烟气处理设施简陋,不能满足工业生产要求。
工厂设计针对铅精矿熔池熔炼过程烟尘率较高等特点,设计了带垂直上升段、膜式壁结构的余热锅炉,有效回收了烟气余热,并解决了铅烟尘的粘结和密闭输送问题。
新工艺在国内外炼铅行业中首次设计并成功采用铅氧化渣直线铸渣机,氧气底吹熔炼炉产出的铅氧化渣连续铸渣后直接送入鼓风炉还原化渣连续铸渣后直接送入鼓风炉还原。
二、新工艺实际生产指标项目指标氧气底吹熔炼炉有效作业率/ % > 95氧气底吹熔炼炉工业氧气消耗量/ (m3·t - 1粗铅) 300~350氧气底吹熔炼燃料率/ % 0~210氧气底吹熔炼炉一次粗铅产出率/ % 45~55一次粗铅品位/ % > 9815铅氧化渣含Pb/ % 40~50铅氧化渣含S/ % < 015氧气底吹熔炼烟尘率/ % 12~15氧气底吹熔炼炉出炉烟气SO2 浓度/ % 12~14制酸后尾气含SO2/ (mg·m- 3) < 300鼓风炉床能力/ (t·m - 2·d - 1) 45~55鼓风炉焦率/ % 13~15Pb 回收率/ % > 97S 回收率/ % > 95Au 回收率/ % > 98Ag 回收率/ % > 98鼓风炉渣含Pb/ % 3~4氧枪寿命/ d 20~50余热锅炉蒸气产出量(410MPa) / (t·t - 1粗铅) 015~018三、工艺主要特点(1)环境保护好由于熔炼过程在密闭的熔炼炉中进行,避免了烟气外逸,SO2 烟气经二转二吸制酸后,尾气排放达到了环保要求。
铅精矿或其他铅原料配合制粒后直接入炉,没有烧结返粉作业,生产过程中产出的铅烟尘均密封输送并返回配料,防止了铅烟尘的弥散;同时在虹吸放铅口设通风装置,防止铅蒸气的扩散。
彻底解决了铅冶炼烟气、烟尘污染问题。
河南豫光经环保部门实测,生产岗位含尘量为7mg/ m3 ,其中铅尘含量0103 mg/ m3 , 硫酸尾气SO2 含量< 100mg/ m3。
均远低于国家排放标准。
实际生产比较证明,氧气底吹熔炼炉前噪音较低,岗位操作环境优于氧气顶吹熔炼( ISA 法和Ausmelt 法) 。
(2) 能耗低与传统流程相比,氧气底吹实现了自热熔炼并回收了高温烟气中的余热;熔炼炉已产出一次粗铅,鼓风炉物料处理量大幅减少,焦炭消耗相应节省了30 %~40 %。
与氧气顶吹熔炼( ISA 法和Ausmelt法) 相比,由于采用工业纯氧熔炼,动力消耗较少。
(3)投资省前述两厂的吨铅基建投资为3 000~3 500 元,与国外较先进的炼铅工艺相比,相同生产规模节省投资40 %~60 % ;由于工艺流程短,相同生产规模较传统烧结机—鼓风炉流程投资亦可节省20 % ;新工艺尤其适合烧结—鼓风炉流程的技改:除烧结设施外,其余设施均可通过适当改造加以利用,从而可进一步节省技改费用。
(4) 生产成本低与国外较先进的炼铅工艺相比,投资省,折旧费用低,生产成本低;和传统流程相比,生产过程简单,动力和焦炭消耗量少,生产效率高,人工费用低,同时有价金属和硫回收率高,生产成本相对亦较低,据实际生产测算,和烧结机—鼓风炉流程相比,每吨粗铅生产成本降低约10 %。
(5) 对原料适应性强氧气底吹熔炼炉既可直接处理各种品位的铅精矿,又可同时处理各种二次铅原料。
实际生产中,上述两厂处理的铅原料含铅品位在45 %~65 % ,均能正常作业。
(6) 自动化水平高氧气底吹熔炼过程采用DCS 控制系统,实现了配料、制粒、供氧、熔炼、余热锅炉、锅炉循环水、电收尘、高温风机等全流程、全部设备的集中控制。
(7) 产品质量好氧气底吹熔炼炉产出的一次粗铅品位高,烟气制酸可产出无色透明的一级酸。
4 新工艺应用中的问题讨论(1) 关于氧枪寿命影响氧枪寿命的因素有氧枪结构、材质、制造工艺、操作参数和冷却介质,控制合理的氧气流速对提高氧枪寿命有显著效果。
(2) 关于熔炼烟尘率由于PbS 在高温下有较大挥发性,铅熔池熔炼过程烟尘率较高。
生产中降低烟尘率的关键因素是控制较低的熔炼温度和较高的PbO 活度。
(3) 关于鼓风炉还原氧气底吹熔炼炉产出的铅氧化渣含硫较低,有效防止了由ZnS 造成的炉结的产生。
生产中基本不需要清理炉结。
针对铅氧化渣熔点较低等特点,为降低渣含铅,除需调整渣型和适当提高焦率外,应严格控制较高的料柱和适当的床能力。
氧气底吹熔炼—鼓风炉还原炼铅新工艺除根治了铅冶炼的环境污染外,还具有投资省、节能、生产成本低和对原料适用性强等优点,工艺技术水平达到国际先进。
该工艺及装置的投产成功,为国内外炼铅行业新建和技改起到良好示范作用,具有广阔的推广前景。
主要工艺过程1.电解铅生产所进矿源主要为浮选后的硫化铅精矿,用抓斗吊车进行预配料,再与辅料混合,混合料由梭式布料机给烧结机布料,烧结采用鼓风返烟烧结,烧结机大烟罩较高浓度的二氧化硫烟气收尘后送非定态制酸系统生产硫酸。