塑料异型材挤出模具PPT课件
合集下载
异型材挤出成型—异型材成型工艺(塑料挤出成型课件)
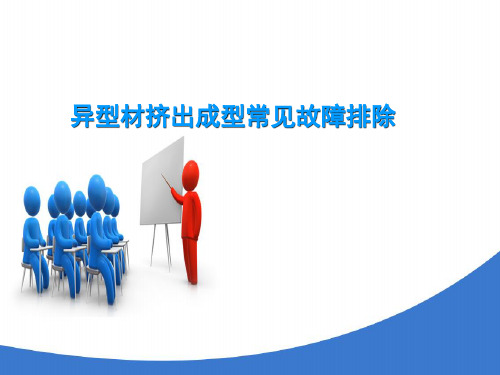
机头 压力 不足
定型段 物料 入机头 配方中 物料 分料筋 挤出 长度 未充分 料流 外润滑性 流动性 处熔体 速度 不足 汇流 偏低 过强 太差 温度偏低 太快
调整 物料 流量
增加 机头 压力
增加 定型段 长度
在模芯 支架后 设置 物料池
增大机头 入口处的 树脂流道
降低 混料的 外润滑性
采用 流动性好 的物料
冷却水对 型材冷却过快
关小冷却水
真空压力过大
定型模与冷却水箱 不在同一直线上
减小真空吸力
调整定型模与水箱 在同一水平直线上
异型材挤出成型工艺规程
异型材挤出工艺规程
1、开机前准备 检查水电供应、辅机是否正常,辅助工具
是否准备齐全,人员是否到位。
2、升温 升温并观察温度变化,打开螺杆油温,开启水阀,
(2)待停机料挤出后,依次关闭定型真空、风机,停止主 机螺杆,关闭螺杆油泵、冷却油泵。牵引机待料条牵引完 毕后关闭;
(3)后退定型台,松动模头紧固螺丝,松开连接法兰螺丝, 整体拆下模头,模具交付模具工清理;
(4)松开定型模底脚紧固丝,关闭主水阀,拔掉水、气管。 (5)关闭总电源,收拾工具,打扫现场卫生。 注:停机清理定型模执行(1)(2),清理模头还需执行
比如850r/min左右,低速排料, 转 速150r/min左右。
(4)混合温度:视冷热混合情况而定。 (5)混合时间:一般为5-15min。
二、异型材成型工艺控制
物料混合包括热混和冷混。
热混的目的是将物料中各个组
分颗粒达到最大程度的分布,使 物料升温,达到预塑化,如PVC 热混温度控制在115~120℃。
挥发物含量过多 产生分解气体
大
增加螺杆压缩比, 使排气完全
塑料异型材挤出模具ppt课件

精品
7
⑤要让型材坯料在离开模头之 前有足够的纯剪切流动过程
➢让料流在纯剪切流动的过程中尽可能充分地实 现弹性松弛,这也就是说,模头流道出口前都 要有一段足够长的平直段(或称成型段)。
➢平直段长度也绝不是越长越好。平直段长, 会增大背压,增加功耗;
➢会延长模塑料在高温段的停留时间,这尤其 对PVC塑料是十分不利的;
应的壁厚中心线之间的距离分别为Ao和Bo 设该 型材口模图形外形的长和宽分别为A’和B’,其
相应的口模缝隙中心线之间的距离分别为A0’ 和 B0’。
由于平缝口模的离模膨胀只发生在型坯壁厚
方向,所以可以认为该型材型坯的离模膨胀,以
口模缝隙中心线为中心对称发生,即型材壁厚中
心线之间的距离不受离模膨胀作用的影响,但仍
精品
精品
22
选择异型材的挤出中心——方法二
➢ 对于横截面形状较分散的异型材,这样的选择 会较有利于实现整个模头流道均衡地分流,对 提高模头的出料稳定性是大有好处的(图c)
精品
23
选择异型材的挤出中心——方法三
➢选择异型材横截面的主要型腔的中心,作为挤 出中心
➢或根据前两种选择方法作适当调整
精品
24
➢选择异型材的挤出中心,也就是在确定模头的 料流开始分流前的流道中心,与挤出生产线上 异型材截面的位置关系,这对实现均衡分流是 有影响的。
精品
27
口模截面图设计 P279
➢口模截面图(简称为口模图形)是挤出模头流 道出口的截面形状,是由挤出模头的型芯(包 括型芯镶件)和口模板(亦称成型板)两种零 件构成的。
➢口模图形确定了型芯(包括内筋)的外形和口 模板的内腔尺寸,是挤出模头上最关键的尺寸。 正确的口模图形是挤出模头设计的基本要求之 一。
挤出成型工艺ppt课件

聚丙烯
160-170 180-190 190-200 200-205 180-200 200-210 200-210 190-200 200-210 200-210
ABS
150-170 160-180 180-195 185-200 180-190 201-215 200-210 190-200 200-210 205-215
• 适用的树脂材料: 绝大部分热塑性塑料及部分热固性塑料,如PVC、PS、ABS、 PC、PE、PP、PA、丙烯酸树脂、环氧树脂、酚醛树脂及密胺树 脂等
• 应用: 塑料薄膜、网材、带包覆层的产品、截面一定、长度连续的管材、 板材、片材、棒材、打包带、单丝和异型材等等,还可用于粉末 造粒、染色、树脂掺和等。
4
塑料工艺
挤出设备
.
5
塑料工艺
• 由挤出机、机头 和口模、辅机等 组成。
1、挤出设备:
6
塑料工艺
设备组成
7
单螺杆挤出机的组成
塑料工艺
• 1、单螺杆挤出机主 要由传动系统、加 料系统、塑化系统、 加热与冷却系统、 控制系统等组成。
• 2、挤出系统是最主 要的系统,它由料 筒、螺杆、多孔板 和过滤网组成。
8
塑料工艺
单螺杆挤出机的结构
9
塑料工艺
双螺杆挤出机的结构
10
普通单螺杆挤出机的工作过程
塑料工艺
11
单螺杆种类
塑料工艺
12
双螺杆挤出
塑料工艺
• (一)双螺杆挤出机的结构
13
(二)双螺杆挤出的特点
塑料工艺
• 和单螺杆挤出机相比,双螺杆挤出机的特点是: 1、较高的固体输送能力和挤出产量; 2、自洁能力; 3、混合塑化能力高; 4、较低的塑化温度,减小分解可能; 5、结构复杂,成本高。
塑料制品的挤出成型ppt演示课件(86页)
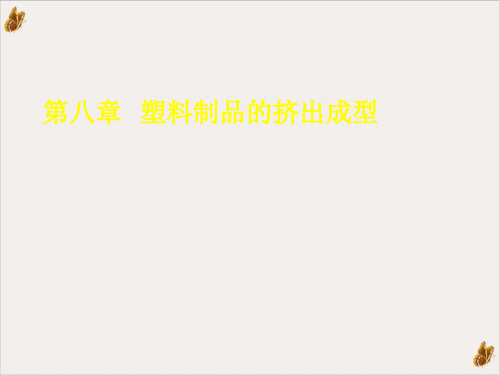
其它:预热干燥和真空减压装置,搅拌器及能够定时定量自动上料或加料的装置。
冷却定型:防止形变,固定尺寸
2 单螺杆挤出机的控制系统
螺槽深度H(h):h1,h2,h3-分别为加料段,压缩段,均化段螺槽深度
2 单螺杆挤出机的控制系统
料筒
8. 1 单螺杆挤出机的基本结构
螺杆
作用:螺杆是挤出机的关键性
部件,通过它 的转动,料筒
螺旋角Φ
8. 1 单螺杆挤出机的基本结构
太小,料流很快变薄,不利于均化。
加料段(固体输送段):
T↑η↓,有利于塑化(尤其对于温敏型塑料),降低熔体压力,挤出物形状稳定性差,易热分解
1 单螺杆挤出机的基本结构
螺槽宽度:B-螺槽轴向宽度
L3-均化段长度
② 启动时,转速从低→高
5 吹塑薄膜挤出成型
1 单螺杆挤出机的基本结构
温度过低,影响塑化效果。
1 单螺杆挤出机的基本结构
密度小、耐腐蚀性好、电性能优良、价格低廉、安装施工力便
1 单螺杆挤出机的基本结构
b-机头口模环形间隙的宽度
1mm以上称为板材。
5 吹塑薄膜挤出成型
① 干燥设备:烘箱
挤出机及机头口模的预热:生产的稳定性,设备的保护
分流器支架:支撑分流器和芯棒
机头压缩比:分流器支架出口处流道环形面积与口模出口处环形面积之比。
5 吹塑薄膜挤出成型
螺杆长度L:L-螺杆有效工作部分长度
1 单螺杆挤出机的基本结构
5 吹塑薄膜挤出成型
每次挤出停机时间长,必须加清洗料,排空后,拆机头,螺杆清理干净。
L2-压缩段长度
各种液体、气体的输送,如上、下水管、建筑线路管、煤气管、采暖管等。
挤出机、机头口模、定型装置、冷却水槽、牵引及切割装置等组成,机头口模和定型装置是关键部件。
冷却定型:防止形变,固定尺寸
2 单螺杆挤出机的控制系统
螺槽深度H(h):h1,h2,h3-分别为加料段,压缩段,均化段螺槽深度
2 单螺杆挤出机的控制系统
料筒
8. 1 单螺杆挤出机的基本结构
螺杆
作用:螺杆是挤出机的关键性
部件,通过它 的转动,料筒
螺旋角Φ
8. 1 单螺杆挤出机的基本结构
太小,料流很快变薄,不利于均化。
加料段(固体输送段):
T↑η↓,有利于塑化(尤其对于温敏型塑料),降低熔体压力,挤出物形状稳定性差,易热分解
1 单螺杆挤出机的基本结构
螺槽宽度:B-螺槽轴向宽度
L3-均化段长度
② 启动时,转速从低→高
5 吹塑薄膜挤出成型
1 单螺杆挤出机的基本结构
温度过低,影响塑化效果。
1 单螺杆挤出机的基本结构
密度小、耐腐蚀性好、电性能优良、价格低廉、安装施工力便
1 单螺杆挤出机的基本结构
b-机头口模环形间隙的宽度
1mm以上称为板材。
5 吹塑薄膜挤出成型
① 干燥设备:烘箱
挤出机及机头口模的预热:生产的稳定性,设备的保护
分流器支架:支撑分流器和芯棒
机头压缩比:分流器支架出口处流道环形面积与口模出口处环形面积之比。
5 吹塑薄膜挤出成型
螺杆长度L:L-螺杆有效工作部分长度
1 单螺杆挤出机的基本结构
5 吹塑薄膜挤出成型
每次挤出停机时间长,必须加清洗料,排空后,拆机头,螺杆清理干净。
L2-压缩段长度
各种液体、气体的输送,如上、下水管、建筑线路管、煤气管、采暖管等。
挤出机、机头口模、定型装置、冷却水槽、牵引及切割装置等组成,机头口模和定型装置是关键部件。
挤出工艺简介ppt课件
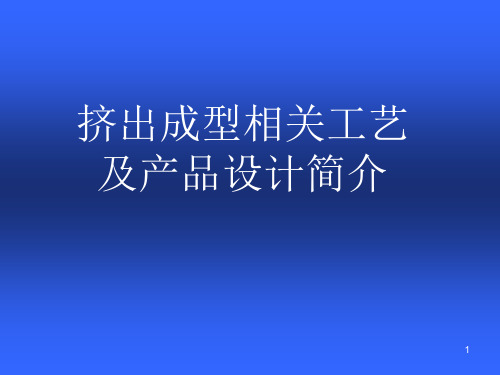
挤出成型相关工艺 及产品设计简介
1
挤出成型简介
挤出成型一般用于热塑性塑料的管材、棒材、 板材、薄膜、线材等连续型材的生产,所得到的 塑件均具有稳定的截面形状。
粉状和粒状
预热和干燥
挤出机加热
开动螺杆
加料 调整
牵引
冷却
定型
卷取(切割)
后处理
挤出成型工艺流程图
挤出成型
成品
2
挤出工艺示意图
3
挤出成型原理和特点
• 挤出挤出过程中的温差和温度波动,都会影 响塑件的质量,使塑件产生残余应力,各点强 度不均匀,表面灰暗无光。
10
2.压力
• 在挤出过程中,由于塑料流动的阻力、螺 杆槽深度的变化、过滤板、过滤网和口模产生 阻碍等原因,在塑料内部形成一定的压力,而 这种压力是塑料经历物理状态变化而达到均匀 密实的重要条件。
6
2.挤出成型阶段
• 均匀塑化的塑料熔体随螺杆的旋转向 料筒前端移动,在螺杆的旋转挤压作用 下,通过一定形状的口模而获得与口模 形状一致的型材。
7
3.定型冷却阶段
• 塑件离开机头口模后,首先通过定型 装置和冷却装置,使其冷却变硬而定型。 在大多数情况下,定型和冷却是同时进 行的,只有在挤出各种管材和棒材时, 才有一个独立的定型过程。
12
4.牵引速度
• 从机头和口模中挤出的成型塑件,在 牵引力作用下将会发生拉伸取向,拉伸 取向程度越高,塑件沿取向方位上的拉 伸强度也越大,但冷却后长度收缩也大。 通常,牵引速度可与挤出速度相当,两 者的比值称为牵引比,一般应略大于1。
13
挤出成型产品设计要点
请做过挤出成型产品的同仁现身说法。传 授宝贵经验。
14
Hale Waihona Puke • 压力随时间的变化也会产生周期性波动,对 塑件质量有不利的影响,如局部疏松、表面不 平、弯曲等。为了减小压力波动,应合理控制 螺杆转速,保证加热和冷却装置的温控精度。
1
挤出成型简介
挤出成型一般用于热塑性塑料的管材、棒材、 板材、薄膜、线材等连续型材的生产,所得到的 塑件均具有稳定的截面形状。
粉状和粒状
预热和干燥
挤出机加热
开动螺杆
加料 调整
牵引
冷却
定型
卷取(切割)
后处理
挤出成型工艺流程图
挤出成型
成品
2
挤出工艺示意图
3
挤出成型原理和特点
• 挤出挤出过程中的温差和温度波动,都会影 响塑件的质量,使塑件产生残余应力,各点强 度不均匀,表面灰暗无光。
10
2.压力
• 在挤出过程中,由于塑料流动的阻力、螺 杆槽深度的变化、过滤板、过滤网和口模产生 阻碍等原因,在塑料内部形成一定的压力,而 这种压力是塑料经历物理状态变化而达到均匀 密实的重要条件。
6
2.挤出成型阶段
• 均匀塑化的塑料熔体随螺杆的旋转向 料筒前端移动,在螺杆的旋转挤压作用 下,通过一定形状的口模而获得与口模 形状一致的型材。
7
3.定型冷却阶段
• 塑件离开机头口模后,首先通过定型 装置和冷却装置,使其冷却变硬而定型。 在大多数情况下,定型和冷却是同时进 行的,只有在挤出各种管材和棒材时, 才有一个独立的定型过程。
12
4.牵引速度
• 从机头和口模中挤出的成型塑件,在 牵引力作用下将会发生拉伸取向,拉伸 取向程度越高,塑件沿取向方位上的拉 伸强度也越大,但冷却后长度收缩也大。 通常,牵引速度可与挤出速度相当,两 者的比值称为牵引比,一般应略大于1。
13
挤出成型产品设计要点
请做过挤出成型产品的同仁现身说法。传 授宝贵经验。
14
Hale Waihona Puke • 压力随时间的变化也会产生周期性波动,对 塑件质量有不利的影响,如局部疏松、表面不 平、弯曲等。为了减小压力波动,应合理控制 螺杆转速,保证加热和冷却装置的温控精度。
塑料挤出成型工艺及模具设计PPT学习教案
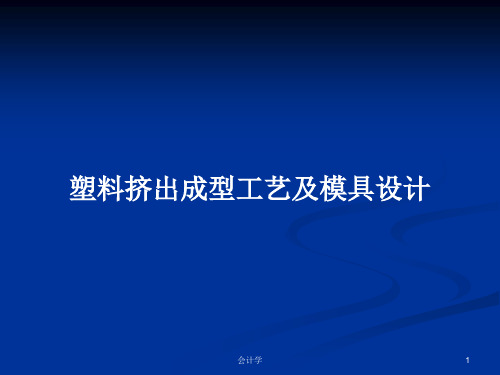
机头以12个内六角螺钉与机头法兰连接固定然后机头法兰又与挤出机法兰以铰链螺栓连接而且在两者间有定位销1定位保证同心度图77机头连接形式之二1定位销2机筒3螺杆5挤出机法兰6铰链7机头法兰8螺钉72挤出成型模具设计要点第14页共27页202161516725挤管机头设计要点7251典型结构常用的挤管机头有直通式直角式与旁侧式三种
图7-9所示。
③芯模收缩角β:对低黏度塑料,
β=45°~60°,对高黏度塑料,β=30°~50°。
2021/5/5
第19页/共27页
20
7.2
3 塑料通过分流器使料层变薄,便于被均匀加热,以
利于塑料进一步塑化。分流肋应尽可能少些,小型机头 3根,中型机头4根,大型机头6~8根。
2021/5/5
图7-8 分流器和分流器支架的结构图
25
7.2
(2)真空法外定径:在定径套内壁2上打很多小孔,做 抽真空用,借助真空吸附力将管材外型紧贴于定径套内 壁2上,与此同时,在定径套外壁1、内壁2夹层内通入 冷却水,管坯伴随真空吸附过程的进行而被冷却硬化。
装置比较简单 ,管口不必堵 塞,常用生产 小型管材
图7-11 真空法外定径
2021/5/5
2021/5/5
第8页/共27页
9
7.2
2 (1)水平直通式机头:
2021/5/5
7-2 直通式管材挤出机头
第9页/共27页
10
7.2
(2)直角式机头:这种机头的进料方向与出料方向垂 直相交,有的机头口模出料口垂直朝上,如图7-3的吹 膜机头;也有朝下的,如图7-4所示的吹塑空心坯料机 头。
2021/5/5
14
7.2
机头与挤出机的连接方式二:
图7-9所示。
③芯模收缩角β:对低黏度塑料,
β=45°~60°,对高黏度塑料,β=30°~50°。
2021/5/5
第19页/共27页
20
7.2
3 塑料通过分流器使料层变薄,便于被均匀加热,以
利于塑料进一步塑化。分流肋应尽可能少些,小型机头 3根,中型机头4根,大型机头6~8根。
2021/5/5
图7-8 分流器和分流器支架的结构图
25
7.2
(2)真空法外定径:在定径套内壁2上打很多小孔,做 抽真空用,借助真空吸附力将管材外型紧贴于定径套内 壁2上,与此同时,在定径套外壁1、内壁2夹层内通入 冷却水,管坯伴随真空吸附过程的进行而被冷却硬化。
装置比较简单 ,管口不必堵 塞,常用生产 小型管材
图7-11 真空法外定径
2021/5/5
2021/5/5
第8页/共27页
9
7.2
2 (1)水平直通式机头:
2021/5/5
7-2 直通式管材挤出机头
第9页/共27页
10
7.2
(2)直角式机头:这种机头的进料方向与出料方向垂 直相交,有的机头口模出料口垂直朝上,如图7-3的吹 膜机头;也有朝下的,如图7-4所示的吹塑空心坯料机 头。
2021/5/5
14
7.2
机头与挤出机的连接方式二:
【大学课件】塑料挤出成型工艺及模具设计PPT

1 口模 (1) 口模的内径D
巴鲁斯效应和冷却收缩等原因使塑件外径不等 于口模内径 确定口模的内径D方法1: 确定口模的内径D方法2:
D=d/K
I
D2 Ds2
d2 ds2
Page 17
7.3.1 直通式挤出机头工艺参数的确定
1 口模 (2) 定型段长度L1 口模与型棒的平直部分Байду номын сангаас长度成为定型段
第七章 塑料挤出成型工艺及模具设计
7.1挤出成型工艺 主要用于生产具有恒定截面形状的管材、
棒材、板材、片材、线材和薄膜等。
此外,也可用于塑料的着色造粒、 共混、中空塑件型坯的生产。
Page 2
7.1.1 挤出成型原理及特点
挤出成型优点: 连续成型、生产量大、
生产效率高、设备简单
Page 3
成本低、操作方便
7.1.2 挤出成型工艺过程
原材料的准备阶段 塑化阶段 成型阶段 定径阶段 塑件的牵引、卷曲和切割阶段
Page 4
7.1.3 挤出成型工艺参数
温度 压力 挤出速度 牵引速度
Page 5
7.2 挤出成型机头概述
挤出成型的模具成为挤出成型机头
7.2.1 挤出机头的作用及分类 1 挤出机头作用
Page 24
7.3.2 管材的定径和冷却
1 外径定径 外径定径适用于对管材外径尺寸精度要求高、 外表面粗糙度低的情况。 按照压力产生方式不同,外径定径又分为内压法 和真空法。
Page 25
Page 26
Page 27
Page 28
7.3.2 管材的定径和冷却
1 外径定径 (1) 内压法外定径 定型套内径径向尺寸应考虑管材定型后收缩因素、
确定分流器上的角度α,分流锥长度、分流器头部 圆角半径、分流器表面粗糙度、过滤版与分流器顶间隔
巴鲁斯效应和冷却收缩等原因使塑件外径不等 于口模内径 确定口模的内径D方法1: 确定口模的内径D方法2:
D=d/K
I
D2 Ds2
d2 ds2
Page 17
7.3.1 直通式挤出机头工艺参数的确定
1 口模 (2) 定型段长度L1 口模与型棒的平直部分Байду номын сангаас长度成为定型段
第七章 塑料挤出成型工艺及模具设计
7.1挤出成型工艺 主要用于生产具有恒定截面形状的管材、
棒材、板材、片材、线材和薄膜等。
此外,也可用于塑料的着色造粒、 共混、中空塑件型坯的生产。
Page 2
7.1.1 挤出成型原理及特点
挤出成型优点: 连续成型、生产量大、
生产效率高、设备简单
Page 3
成本低、操作方便
7.1.2 挤出成型工艺过程
原材料的准备阶段 塑化阶段 成型阶段 定径阶段 塑件的牵引、卷曲和切割阶段
Page 4
7.1.3 挤出成型工艺参数
温度 压力 挤出速度 牵引速度
Page 5
7.2 挤出成型机头概述
挤出成型的模具成为挤出成型机头
7.2.1 挤出机头的作用及分类 1 挤出机头作用
Page 24
7.3.2 管材的定径和冷却
1 外径定径 外径定径适用于对管材外径尺寸精度要求高、 外表面粗糙度低的情况。 按照压力产生方式不同,外径定径又分为内压法 和真空法。
Page 25
Page 26
Page 27
Page 28
7.3.2 管材的定径和冷却
1 外径定径 (1) 内压法外定径 定型套内径径向尺寸应考虑管材定型后收缩因素、
确定分流器上的角度α,分流锥长度、分流器头部 圆角半径、分流器表面粗糙度、过滤版与分流器顶间隔
塑料成型工艺第六章 挤出成型PPT课件

的物料量或塑件长度。它表示挤出能力的高低。 4.牵引速度
牵引速度与挤出速度相当,可略大于挤出速度。 牵引— 比— 牵引速度与挤出速度的比值,其值 等于或大于1。
§6.3 挤出管材成型工艺
一、挤出管材工艺控制要点
1.温度的控制
挤出成型温度是促使成型物料塑化和塑料熔体流动的 必要条件。对物料的塑化及制品的质量和产量有着十分 重要的影响。
(2)关闭冷却水进水阀、压缩空气机或真空泵、 牵引机等。
(3)拆机头,并清理
一、硬质聚氯乙烯塑料管材
硬质聚氯乙烯塑料简称为PVC-U,也可用UPVC来 1表.原示材。料的选用
硬质聚氯乙烯管材,应选用悬浮聚合的高型 号的树脂,如通常以SG-5型树脂为主要原料, 也可选用SG-6型树脂和SG-4型树脂。
2.压力
a、压力的建立
挤出成型时,沿料筒轴线方向,在物料内部 要建立起不同压力,主要由以下两个方面的因 素造成的:
压缩比的存在:螺槽深度的改变、料筒上的沟 槽深度变化、螺距的改变等。
分流板、滤网和口模产生的阻力。
压力的建立是物料得以经历物理状态变化、得 到均匀密实的熔体、并最后得到成型制品的重 要条件之一。
在各段温度设定应考虑以下几个方面:一是聚 合物本身的性能,如熔点,分子量大小和分布,熔 体指数等。其次考虑设备的性能。有的设备,进料 段的温度对主机电流的影响很大。再次,通过观察 管模头挤出管坯表面是否光滑。有无气泡等现象来 判断。
挤出成型所需控制的温度是机筒温度、机颈温 度、口模温度。
机筒温度分布,从喂料区到模头可能是平坦分布, 递增分布,递减分布及混合分布。主要取决于材 料物点和挤出机的结构。
一、挤出成型基本原理
将熔融的塑料自模具内以挤压的方式往外推出,而 得到与模口相同几何形状的流体,冷却固化后,得到 所要的零件。
牵引速度与挤出速度相当,可略大于挤出速度。 牵引— 比— 牵引速度与挤出速度的比值,其值 等于或大于1。
§6.3 挤出管材成型工艺
一、挤出管材工艺控制要点
1.温度的控制
挤出成型温度是促使成型物料塑化和塑料熔体流动的 必要条件。对物料的塑化及制品的质量和产量有着十分 重要的影响。
(2)关闭冷却水进水阀、压缩空气机或真空泵、 牵引机等。
(3)拆机头,并清理
一、硬质聚氯乙烯塑料管材
硬质聚氯乙烯塑料简称为PVC-U,也可用UPVC来 1表.原示材。料的选用
硬质聚氯乙烯管材,应选用悬浮聚合的高型 号的树脂,如通常以SG-5型树脂为主要原料, 也可选用SG-6型树脂和SG-4型树脂。
2.压力
a、压力的建立
挤出成型时,沿料筒轴线方向,在物料内部 要建立起不同压力,主要由以下两个方面的因 素造成的:
压缩比的存在:螺槽深度的改变、料筒上的沟 槽深度变化、螺距的改变等。
分流板、滤网和口模产生的阻力。
压力的建立是物料得以经历物理状态变化、得 到均匀密实的熔体、并最后得到成型制品的重 要条件之一。
在各段温度设定应考虑以下几个方面:一是聚 合物本身的性能,如熔点,分子量大小和分布,熔 体指数等。其次考虑设备的性能。有的设备,进料 段的温度对主机电流的影响很大。再次,通过观察 管模头挤出管坯表面是否光滑。有无气泡等现象来 判断。
挤出成型所需控制的温度是机筒温度、机颈温 度、口模温度。
机筒温度分布,从喂料区到模头可能是平坦分布, 递增分布,递减分布及混合分布。主要取决于材 料物点和挤出机的结构。
一、挤出成型基本原理
将熔融的塑料自模具内以挤压的方式往外推出,而 得到与模口相同几何形状的流体,冷却固化后,得到 所要的零件。
- 1、下载文档前请自行甄别文档内容的完整性,平台不提供额外的编辑、内容补充、找答案等附加服务。
- 2、"仅部分预览"的文档,不可在线预览部分如存在完整性等问题,可反馈申请退款(可完整预览的文档不适用该条件!)。
- 3、如文档侵犯您的权益,请联系客服反馈,我们会尽快为您处理(人工客服工作时间:9:00-18:30)。
-
7
⑤要让型材坯料在离开模头之 前有足够的纯剪切流动过程
➢让料流在纯剪切流动的过程中尽可能充分地实 现弹性松弛,这也就是说,模头流道出口前都 要有一段足够长的平直段(或称成型段)。
➢平直段长度也绝不是越长越好。平直段长, 会增大背压,增加功耗;
➢会延长模塑料在高温段的停留时间,这尤其 对PVC塑料是十分不利的;
➢ 挤出模头流道的复杂程度,主要是由于异型材截 面的复杂情况决定的。异型材截面上功能块和空腔 数目越多,截面形状就越复杂,挤出模头的流道也 会更加复杂。异型材截面面积的均匀分布,有利于 模头中料流的均匀分流,容易实现均匀挤出
-
13
(2)挤出模塑料的配方---影响挤出模头结构
➢ 模塑料配方不但决定着塑料熔体的黏度,而且 也影响着塑料熔体的弹性效应,因此是影响挤 出模头结构设计的重要因素。
➢ 剪切速率的提高也将改变熔体的黏弹性状况,很明 显,分流引起的拉伸流动会强烈;熔体入口效应、 离模膨胀等弹性现象也都会增强,超过一定界限 (临界剪忉速率Ý )还将会出现熔体破裂现象。
➢ 在较低挤出速度下料坯均匀挤出,截面形状正确的
挤出模头,提高挤出速度后,将可能失去平衡,出
现出料不均现象和型坯形状的畸变。
-
17
(5) 挤出模头的制造工艺
---影响挤出模头结构
➢制造工艺强烈地影响着挤出模头的结构设计, 满足同一种异型材挤出成型的流道基本要求, 可以设计出很多种可行的挤出模头结构形式。
➢型坯挤出模头后受牵引经过气隙进入定型模 中,至少还将受到3种不能忽略的作用:
➢离模膨胀 ➢拉伸变形 ➢冷却收缩,
改变型坯截面的形状和尺寸→ 挤出模头出口截面形状的设计 必须考虑到这些作用的结果
-
3
离膜膨胀
➢聚合物熔体挤出物的尺寸和截面形状与挤出口 模不同,有明显的胀大,这一现象被称为巴拉 斯(Barus)效应,又称为离模膨胀(Die Swell)或 出口膨胀
挤出模头设计
➢ 在塑料异型材挤出成型过程中,对于由挤 出机挤出的熔融的模塑料,挤出模头起着 稳流、分流和成型3种作用
➢通过挤出模头流道被挤出的模塑料型坯, 还须经过气隙之后,被牵引进入定型模进 行定型和冷却,才能最终成为塑料异型材 产品。
-
ห้องสมุดไป่ตู้
2
挤出模头流道的基本要求
➢①要有正确的出口截面形状
➢从模头挤出的异型材型坯的截面形状,不是 产品的最终截面形状,最多只是近似形状。
-
4
②要让型材坯料均匀地挤出
在模头出口处,要求料流截面上各部分的
平均流速应相等(亦有称之为流速分布均匀)。
否问则题,:在异同型样材的绝牵大引部速分度是下薄,壁离型开材模,头且后一的般型截
坯 面各形部状分都的十形分状复就 杂会,产壁生厚不也一并样不的完变全化相。等流。速尤 较 其快是的异部型分材就的会各比种流功速能较块慢结的构部大分多体数积不增是加规范, 这 的样几,何很形难状保。证对型材产品截面形状的要求
方法:必须对各部分流道中的流动阻力进行调
整。另外,异型材各部分流道的前后级之间是
相互关联的,分流部分的流道设计也会影响成
型部分流道中流速的分布→合理的流道设计
-
5
③需要产生适当的背压
➢模塑料只有在一定的压力下才能实现塑化的要 求,该压力称为背压。
➢背压的大小主要是由模塑料料流通过模头流 道时产生的压力降(Δp)所决定的。背压过低 会导致模塑料塑化不良,不能保证制品的物 理性能;而背压高将消耗更多的动力,过高 还可能对设备造成过度的磨损,甚至损坏。
➢很重的模头对于制造和使用也都是很不利的。
-
8
⑥流道壁表面需要十分光滑
➢由于流道壁表面的状况,对于聚合物熔体 在流道中的挤出流动状态会产生很大的影 响。所以要求流道壁表面不但要平整光滑, 而且要求粗糙度一致。不能有缺陷,更不 能有死角和毛刺,以至出现挂料现象,这 一点对于PVC塑料更加重要
-
9
挤出模头的基本结构
-
14
➢实际上,PVC-U模塑料是有十多种组分的干 混粉料,其采购和混料作业的过程,难免存 在一些不确定因素。因此出料不均现象所引 起的异型材型坯形状的畸变,在一定范围内, 是塑料异型材的尺寸公差所允许的;进而可 以通过各种工艺手段(如微调温度和速度 等),减轻或改善;
-
15
(3)挤出机的性能---影响挤出模头结构
➢在一台挤出机上已经实现型坯均匀挤出的挤出 模头,调换挤出机后原先的流道平衡状态被打 破,不再有均匀的出料,型坯发生了畸变。甚 至在同一规格型号的两台挤出机之间,也会出 现型坯畸变。
-
16
(4)型材挤出的速度---影响挤出模头结构
➢ 塑料异型材挤出的速度是挤出模具(包括模头和 定型模)设计的一个十分重要的参数。对于模头来 说,随着挤出速度的提高,熔体剪切速率将提高, 体积流量Q将增加,模头压力降Δp将增大
-
10
-
11
-
12
影响挤出模头结构设计的主要因素
➢ (1)异型材的截面形状---影响挤出模头结构
➢ 挤出模头的总体结构根据异型材的类型区分,中 空型材的挤出模头必须设计分流锥、分流支架和型 芯结构来形成中空型材的主空腔;
➢ 开式型材(包括半开式型材)没有主空腔,所以开 式型材的挤出模头一般没有分流锥、分流支架和型 芯构件。
➢ 对于PVC塑料:抑制或缓解PVC塑料的热降解过程, 是PVC-U加工中首先要考虑的重要问题。添加热稳 定剂,或利用润滑剂和加工助剂等改变熔体流变状况, 以获得较低的加工温度,是模塑料配方方面可采取的 措施;而缩短模头流道长度,改善流道结构,减少料 流在模头内的时间,杜绝积料和挂料现象,则是模头 结构设计方面可考虑采取的措施。对于一定的要求来 说,这两方面的措施是可以互补的。
➢影响背压的因素:型坯截面的复杂程度、模头
流道的结构、型坯的挤出速度和模塑料的流变
性能等都有直接的影响。
-
6
④流道的变化应尽量平缓
➢流道壁面曲线应呈流线型,不能有突变。引起 料流方向改变的扩张或收缩角的半角的角度, 一般要求不大于1 2 °。
➢流道变化的过程,应尽可能做到均匀,或只是 让熔体料流平缓地加速;这样做的目的都是为 了减轻熔体料流中的高分子链段可能产生的弹 性变形的程度,使得弹性效应所引起的离模膨 胀等不利影响减至最低,而让熔体破裂等现象 产生的可能性趋于零。