塑料异型材挤出模具ppt课件
合集下载
异型材挤出成型—异型材成型工艺(塑料挤出成型课件)
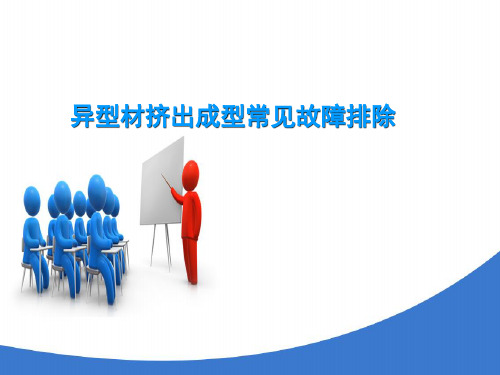
机头 压力 不足
定型段 物料 入机头 配方中 物料 分料筋 挤出 长度 未充分 料流 外润滑性 流动性 处熔体 速度 不足 汇流 偏低 过强 太差 温度偏低 太快
调整 物料 流量
增加 机头 压力
增加 定型段 长度
在模芯 支架后 设置 物料池
增大机头 入口处的 树脂流道
降低 混料的 外润滑性
采用 流动性好 的物料
冷却水对 型材冷却过快
关小冷却水
真空压力过大
定型模与冷却水箱 不在同一直线上
减小真空吸力
调整定型模与水箱 在同一水平直线上
异型材挤出成型工艺规程
异型材挤出工艺规程
1、开机前准备 检查水电供应、辅机是否正常,辅助工具
是否准备齐全,人员是否到位。
2、升温 升温并观察温度变化,打开螺杆油温,开启水阀,
(2)待停机料挤出后,依次关闭定型真空、风机,停止主 机螺杆,关闭螺杆油泵、冷却油泵。牵引机待料条牵引完 毕后关闭;
(3)后退定型台,松动模头紧固螺丝,松开连接法兰螺丝, 整体拆下模头,模具交付模具工清理;
(4)松开定型模底脚紧固丝,关闭主水阀,拔掉水、气管。 (5)关闭总电源,收拾工具,打扫现场卫生。 注:停机清理定型模执行(1)(2),清理模头还需执行
比如850r/min左右,低速排料, 转 速150r/min左右。
(4)混合温度:视冷热混合情况而定。 (5)混合时间:一般为5-15min。
二、异型材成型工艺控制
物料混合包括热混和冷混。
热混的目的是将物料中各个组
分颗粒达到最大程度的分布,使 物料升温,达到预塑化,如PVC 热混温度控制在115~120℃。
挥发物含量过多 产生分解气体
大
增加螺杆压缩比, 使排气完全
挤出成型工艺ppt课件

聚丙烯
160-170 180-190 190-200 200-205 180-200 200-210 200-210 190-200 200-210 200-210
ABS
150-170 160-180 180-195 185-200 180-190 201-215 200-210 190-200 200-210 205-215
• 适用的树脂材料: 绝大部分热塑性塑料及部分热固性塑料,如PVC、PS、ABS、 PC、PE、PP、PA、丙烯酸树脂、环氧树脂、酚醛树脂及密胺树 脂等
• 应用: 塑料薄膜、网材、带包覆层的产品、截面一定、长度连续的管材、 板材、片材、棒材、打包带、单丝和异型材等等,还可用于粉末 造粒、染色、树脂掺和等。
4
塑料工艺
挤出设备
.
5
塑料工艺
• 由挤出机、机头 和口模、辅机等 组成。
1、挤出设备:
6
塑料工艺
设备组成
7
单螺杆挤出机的组成
塑料工艺
• 1、单螺杆挤出机主 要由传动系统、加 料系统、塑化系统、 加热与冷却系统、 控制系统等组成。
• 2、挤出系统是最主 要的系统,它由料 筒、螺杆、多孔板 和过滤网组成。
8
塑料工艺
单螺杆挤出机的结构
9
塑料工艺
双螺杆挤出机的结构
10
普通单螺杆挤出机的工作过程
塑料工艺
11
单螺杆种类
塑料工艺
12
双螺杆挤出
塑料工艺
• (一)双螺杆挤出机的结构
13
(二)双螺杆挤出的特点
塑料工艺
• 和单螺杆挤出机相比,双螺杆挤出机的特点是: 1、较高的固体输送能力和挤出产量; 2、自洁能力; 3、混合塑化能力高; 4、较低的塑化温度,减小分解可能; 5、结构复杂,成本高。
塑料制品的挤出成型ppt演示课件(86页)
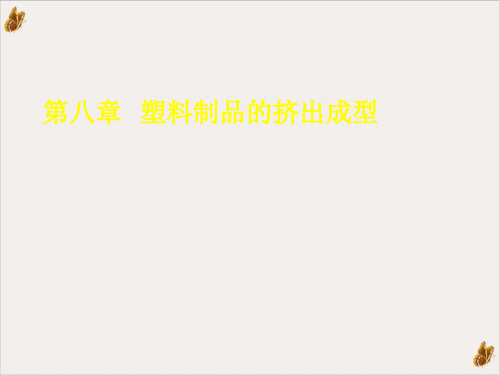
其它:预热干燥和真空减压装置,搅拌器及能够定时定量自动上料或加料的装置。
冷却定型:防止形变,固定尺寸
2 单螺杆挤出机的控制系统
螺槽深度H(h):h1,h2,h3-分别为加料段,压缩段,均化段螺槽深度
2 单螺杆挤出机的控制系统
料筒
8. 1 单螺杆挤出机的基本结构
螺杆
作用:螺杆是挤出机的关键性
部件,通过它 的转动,料筒
螺旋角Φ
8. 1 单螺杆挤出机的基本结构
太小,料流很快变薄,不利于均化。
加料段(固体输送段):
T↑η↓,有利于塑化(尤其对于温敏型塑料),降低熔体压力,挤出物形状稳定性差,易热分解
1 单螺杆挤出机的基本结构
螺槽宽度:B-螺槽轴向宽度
L3-均化段长度
② 启动时,转速从低→高
5 吹塑薄膜挤出成型
1 单螺杆挤出机的基本结构
温度过低,影响塑化效果。
1 单螺杆挤出机的基本结构
密度小、耐腐蚀性好、电性能优良、价格低廉、安装施工力便
1 单螺杆挤出机的基本结构
b-机头口模环形间隙的宽度
1mm以上称为板材。
5 吹塑薄膜挤出成型
① 干燥设备:烘箱
挤出机及机头口模的预热:生产的稳定性,设备的保护
分流器支架:支撑分流器和芯棒
机头压缩比:分流器支架出口处流道环形面积与口模出口处环形面积之比。
5 吹塑薄膜挤出成型
螺杆长度L:L-螺杆有效工作部分长度
1 单螺杆挤出机的基本结构
5 吹塑薄膜挤出成型
每次挤出停机时间长,必须加清洗料,排空后,拆机头,螺杆清理干净。
L2-压缩段长度
各种液体、气体的输送,如上、下水管、建筑线路管、煤气管、采暖管等。
挤出机、机头口模、定型装置、冷却水槽、牵引及切割装置等组成,机头口模和定型装置是关键部件。
冷却定型:防止形变,固定尺寸
2 单螺杆挤出机的控制系统
螺槽深度H(h):h1,h2,h3-分别为加料段,压缩段,均化段螺槽深度
2 单螺杆挤出机的控制系统
料筒
8. 1 单螺杆挤出机的基本结构
螺杆
作用:螺杆是挤出机的关键性
部件,通过它 的转动,料筒
螺旋角Φ
8. 1 单螺杆挤出机的基本结构
太小,料流很快变薄,不利于均化。
加料段(固体输送段):
T↑η↓,有利于塑化(尤其对于温敏型塑料),降低熔体压力,挤出物形状稳定性差,易热分解
1 单螺杆挤出机的基本结构
螺槽宽度:B-螺槽轴向宽度
L3-均化段长度
② 启动时,转速从低→高
5 吹塑薄膜挤出成型
1 单螺杆挤出机的基本结构
温度过低,影响塑化效果。
1 单螺杆挤出机的基本结构
密度小、耐腐蚀性好、电性能优良、价格低廉、安装施工力便
1 单螺杆挤出机的基本结构
b-机头口模环形间隙的宽度
1mm以上称为板材。
5 吹塑薄膜挤出成型
① 干燥设备:烘箱
挤出机及机头口模的预热:生产的稳定性,设备的保护
分流器支架:支撑分流器和芯棒
机头压缩比:分流器支架出口处流道环形面积与口模出口处环形面积之比。
5 吹塑薄膜挤出成型
螺杆长度L:L-螺杆有效工作部分长度
1 单螺杆挤出机的基本结构
5 吹塑薄膜挤出成型
每次挤出停机时间长,必须加清洗料,排空后,拆机头,螺杆清理干净。
L2-压缩段长度
各种液体、气体的输送,如上、下水管、建筑线路管、煤气管、采暖管等。
挤出机、机头口模、定型装置、冷却水槽、牵引及切割装置等组成,机头口模和定型装置是关键部件。
挤出工艺简介ppt课件
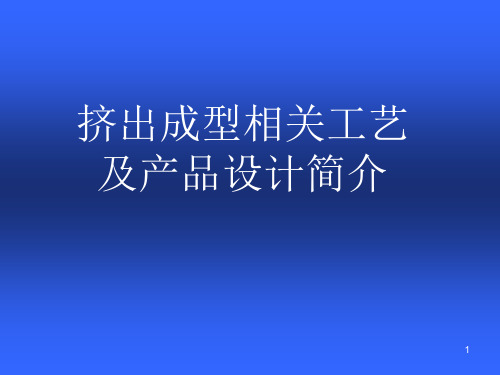
挤出成型相关工艺 及产品设计简介
1
挤出成型简介
挤出成型一般用于热塑性塑料的管材、棒材、 板材、薄膜、线材等连续型材的生产,所得到的 塑件均具有稳定的截面形状。
粉状和粒状
预热和干燥
挤出机加热
开动螺杆
加料 调整
牵引
冷却
定型
卷取(切割)
后处理
挤出成型工艺流程图
挤出成型
成品
2
挤出工艺示意图
3
挤出成型原理和特点
• 挤出挤出过程中的温差和温度波动,都会影 响塑件的质量,使塑件产生残余应力,各点强 度不均匀,表面灰暗无光。
10
2.压力
• 在挤出过程中,由于塑料流动的阻力、螺 杆槽深度的变化、过滤板、过滤网和口模产生 阻碍等原因,在塑料内部形成一定的压力,而 这种压力是塑料经历物理状态变化而达到均匀 密实的重要条件。
6
2.挤出成型阶段
• 均匀塑化的塑料熔体随螺杆的旋转向 料筒前端移动,在螺杆的旋转挤压作用 下,通过一定形状的口模而获得与口模 形状一致的型材。
7
3.定型冷却阶段
• 塑件离开机头口模后,首先通过定型 装置和冷却装置,使其冷却变硬而定型。 在大多数情况下,定型和冷却是同时进 行的,只有在挤出各种管材和棒材时, 才有一个独立的定型过程。
12
4.牵引速度
• 从机头和口模中挤出的成型塑件,在 牵引力作用下将会发生拉伸取向,拉伸 取向程度越高,塑件沿取向方位上的拉 伸强度也越大,但冷却后长度收缩也大。 通常,牵引速度可与挤出速度相当,两 者的比值称为牵引比,一般应略大于1。
13
挤出成型产品设计要点
请做过挤出成型产品的同仁现身说法。传 授宝贵经验。
14
Hale Waihona Puke • 压力随时间的变化也会产生周期性波动,对 塑件质量有不利的影响,如局部疏松、表面不 平、弯曲等。为了减小压力波动,应合理控制 螺杆转速,保证加热和冷却装置的温控精度。
1
挤出成型简介
挤出成型一般用于热塑性塑料的管材、棒材、 板材、薄膜、线材等连续型材的生产,所得到的 塑件均具有稳定的截面形状。
粉状和粒状
预热和干燥
挤出机加热
开动螺杆
加料 调整
牵引
冷却
定型
卷取(切割)
后处理
挤出成型工艺流程图
挤出成型
成品
2
挤出工艺示意图
3
挤出成型原理和特点
• 挤出挤出过程中的温差和温度波动,都会影 响塑件的质量,使塑件产生残余应力,各点强 度不均匀,表面灰暗无光。
10
2.压力
• 在挤出过程中,由于塑料流动的阻力、螺 杆槽深度的变化、过滤板、过滤网和口模产生 阻碍等原因,在塑料内部形成一定的压力,而 这种压力是塑料经历物理状态变化而达到均匀 密实的重要条件。
6
2.挤出成型阶段
• 均匀塑化的塑料熔体随螺杆的旋转向 料筒前端移动,在螺杆的旋转挤压作用 下,通过一定形状的口模而获得与口模 形状一致的型材。
7
3.定型冷却阶段
• 塑件离开机头口模后,首先通过定型 装置和冷却装置,使其冷却变硬而定型。 在大多数情况下,定型和冷却是同时进 行的,只有在挤出各种管材和棒材时, 才有一个独立的定型过程。
12
4.牵引速度
• 从机头和口模中挤出的成型塑件,在 牵引力作用下将会发生拉伸取向,拉伸 取向程度越高,塑件沿取向方位上的拉 伸强度也越大,但冷却后长度收缩也大。 通常,牵引速度可与挤出速度相当,两 者的比值称为牵引比,一般应略大于1。
13
挤出成型产品设计要点
请做过挤出成型产品的同仁现身说法。传 授宝贵经验。
14
Hale Waihona Puke • 压力随时间的变化也会产生周期性波动,对 塑件质量有不利的影响,如局部疏松、表面不 平、弯曲等。为了减小压力波动,应合理控制 螺杆转速,保证加热和冷却装置的温控精度。
塑料挤出成型工艺及模具设计PPT学习教案
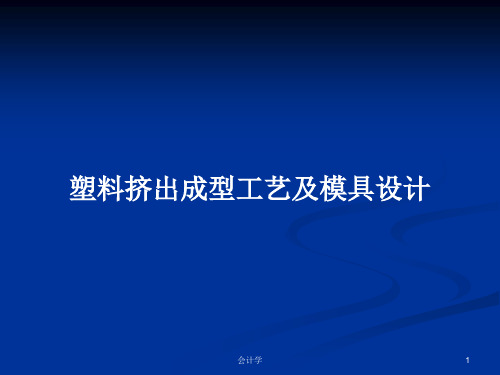
机头以12个内六角螺钉与机头法兰连接固定然后机头法兰又与挤出机法兰以铰链螺栓连接而且在两者间有定位销1定位保证同心度图77机头连接形式之二1定位销2机筒3螺杆5挤出机法兰6铰链7机头法兰8螺钉72挤出成型模具设计要点第14页共27页202161516725挤管机头设计要点7251典型结构常用的挤管机头有直通式直角式与旁侧式三种
图7-9所示。
③芯模收缩角β:对低黏度塑料,
β=45°~60°,对高黏度塑料,β=30°~50°。
2021/5/5
第19页/共27页
20
7.2
3 塑料通过分流器使料层变薄,便于被均匀加热,以
利于塑料进一步塑化。分流肋应尽可能少些,小型机头 3根,中型机头4根,大型机头6~8根。
2021/5/5
图7-8 分流器和分流器支架的结构图
25
7.2
(2)真空法外定径:在定径套内壁2上打很多小孔,做 抽真空用,借助真空吸附力将管材外型紧贴于定径套内 壁2上,与此同时,在定径套外壁1、内壁2夹层内通入 冷却水,管坯伴随真空吸附过程的进行而被冷却硬化。
装置比较简单 ,管口不必堵 塞,常用生产 小型管材
图7-11 真空法外定径
2021/5/5
2021/5/5
第8页/共27页
9
7.2
2 (1)水平直通式机头:
2021/5/5
7-2 直通式管材挤出机头
第9页/共27页
10
7.2
(2)直角式机头:这种机头的进料方向与出料方向垂 直相交,有的机头口模出料口垂直朝上,如图7-3的吹 膜机头;也有朝下的,如图7-4所示的吹塑空心坯料机 头。
2021/5/5
14
7.2
机头与挤出机的连接方式二:
图7-9所示。
③芯模收缩角β:对低黏度塑料,
β=45°~60°,对高黏度塑料,β=30°~50°。
2021/5/5
第19页/共27页
20
7.2
3 塑料通过分流器使料层变薄,便于被均匀加热,以
利于塑料进一步塑化。分流肋应尽可能少些,小型机头 3根,中型机头4根,大型机头6~8根。
2021/5/5
图7-8 分流器和分流器支架的结构图
25
7.2
(2)真空法外定径:在定径套内壁2上打很多小孔,做 抽真空用,借助真空吸附力将管材外型紧贴于定径套内 壁2上,与此同时,在定径套外壁1、内壁2夹层内通入 冷却水,管坯伴随真空吸附过程的进行而被冷却硬化。
装置比较简单 ,管口不必堵 塞,常用生产 小型管材
图7-11 真空法外定径
2021/5/5
2021/5/5
第8页/共27页
9
7.2
2 (1)水平直通式机头:
2021/5/5
7-2 直通式管材挤出机头
第9页/共27页
10
7.2
(2)直角式机头:这种机头的进料方向与出料方向垂 直相交,有的机头口模出料口垂直朝上,如图7-3的吹 膜机头;也有朝下的,如图7-4所示的吹塑空心坯料机 头。
2021/5/5
14
7.2
机头与挤出机的连接方式二:
【大学课件】塑料挤出成型工艺及模具设计PPT

1 口模 (1) 口模的内径D
巴鲁斯效应和冷却收缩等原因使塑件外径不等 于口模内径 确定口模的内径D方法1: 确定口模的内径D方法2:
D=d/K
I
D2 Ds2
d2 ds2
Page 17
7.3.1 直通式挤出机头工艺参数的确定
1 口模 (2) 定型段长度L1 口模与型棒的平直部分Байду номын сангаас长度成为定型段
第七章 塑料挤出成型工艺及模具设计
7.1挤出成型工艺 主要用于生产具有恒定截面形状的管材、
棒材、板材、片材、线材和薄膜等。
此外,也可用于塑料的着色造粒、 共混、中空塑件型坯的生产。
Page 2
7.1.1 挤出成型原理及特点
挤出成型优点: 连续成型、生产量大、
生产效率高、设备简单
Page 3
成本低、操作方便
7.1.2 挤出成型工艺过程
原材料的准备阶段 塑化阶段 成型阶段 定径阶段 塑件的牵引、卷曲和切割阶段
Page 4
7.1.3 挤出成型工艺参数
温度 压力 挤出速度 牵引速度
Page 5
7.2 挤出成型机头概述
挤出成型的模具成为挤出成型机头
7.2.1 挤出机头的作用及分类 1 挤出机头作用
Page 24
7.3.2 管材的定径和冷却
1 外径定径 外径定径适用于对管材外径尺寸精度要求高、 外表面粗糙度低的情况。 按照压力产生方式不同,外径定径又分为内压法 和真空法。
Page 25
Page 26
Page 27
Page 28
7.3.2 管材的定径和冷却
1 外径定径 (1) 内压法外定径 定型套内径径向尺寸应考虑管材定型后收缩因素、
确定分流器上的角度α,分流锥长度、分流器头部 圆角半径、分流器表面粗糙度、过滤版与分流器顶间隔
巴鲁斯效应和冷却收缩等原因使塑件外径不等 于口模内径 确定口模的内径D方法1: 确定口模的内径D方法2:
D=d/K
I
D2 Ds2
d2 ds2
Page 17
7.3.1 直通式挤出机头工艺参数的确定
1 口模 (2) 定型段长度L1 口模与型棒的平直部分Байду номын сангаас长度成为定型段
第七章 塑料挤出成型工艺及模具设计
7.1挤出成型工艺 主要用于生产具有恒定截面形状的管材、
棒材、板材、片材、线材和薄膜等。
此外,也可用于塑料的着色造粒、 共混、中空塑件型坯的生产。
Page 2
7.1.1 挤出成型原理及特点
挤出成型优点: 连续成型、生产量大、
生产效率高、设备简单
Page 3
成本低、操作方便
7.1.2 挤出成型工艺过程
原材料的准备阶段 塑化阶段 成型阶段 定径阶段 塑件的牵引、卷曲和切割阶段
Page 4
7.1.3 挤出成型工艺参数
温度 压力 挤出速度 牵引速度
Page 5
7.2 挤出成型机头概述
挤出成型的模具成为挤出成型机头
7.2.1 挤出机头的作用及分类 1 挤出机头作用
Page 24
7.3.2 管材的定径和冷却
1 外径定径 外径定径适用于对管材外径尺寸精度要求高、 外表面粗糙度低的情况。 按照压力产生方式不同,外径定径又分为内压法 和真空法。
Page 25
Page 26
Page 27
Page 28
7.3.2 管材的定径和冷却
1 外径定径 (1) 内压法外定径 定型套内径径向尺寸应考虑管材定型后收缩因素、
确定分流器上的角度α,分流锥长度、分流器头部 圆角半径、分流器表面粗糙度、过滤版与分流器顶间隔
塑料成型工艺第六章 挤出成型PPT课件

的物料量或塑件长度。它表示挤出能力的高低。 4.牵引速度
牵引速度与挤出速度相当,可略大于挤出速度。 牵引— 比— 牵引速度与挤出速度的比值,其值 等于或大于1。
§6.3 挤出管材成型工艺
一、挤出管材工艺控制要点
1.温度的控制
挤出成型温度是促使成型物料塑化和塑料熔体流动的 必要条件。对物料的塑化及制品的质量和产量有着十分 重要的影响。
(2)关闭冷却水进水阀、压缩空气机或真空泵、 牵引机等。
(3)拆机头,并清理
一、硬质聚氯乙烯塑料管材
硬质聚氯乙烯塑料简称为PVC-U,也可用UPVC来 1表.原示材。料的选用
硬质聚氯乙烯管材,应选用悬浮聚合的高型 号的树脂,如通常以SG-5型树脂为主要原料, 也可选用SG-6型树脂和SG-4型树脂。
2.压力
a、压力的建立
挤出成型时,沿料筒轴线方向,在物料内部 要建立起不同压力,主要由以下两个方面的因 素造成的:
压缩比的存在:螺槽深度的改变、料筒上的沟 槽深度变化、螺距的改变等。
分流板、滤网和口模产生的阻力。
压力的建立是物料得以经历物理状态变化、得 到均匀密实的熔体、并最后得到成型制品的重 要条件之一。
在各段温度设定应考虑以下几个方面:一是聚 合物本身的性能,如熔点,分子量大小和分布,熔 体指数等。其次考虑设备的性能。有的设备,进料 段的温度对主机电流的影响很大。再次,通过观察 管模头挤出管坯表面是否光滑。有无气泡等现象来 判断。
挤出成型所需控制的温度是机筒温度、机颈温 度、口模温度。
机筒温度分布,从喂料区到模头可能是平坦分布, 递增分布,递减分布及混合分布。主要取决于材 料物点和挤出机的结构。
一、挤出成型基本原理
将熔融的塑料自模具内以挤压的方式往外推出,而 得到与模口相同几何形状的流体,冷却固化后,得到 所要的零件。
牵引速度与挤出速度相当,可略大于挤出速度。 牵引— 比— 牵引速度与挤出速度的比值,其值 等于或大于1。
§6.3 挤出管材成型工艺
一、挤出管材工艺控制要点
1.温度的控制
挤出成型温度是促使成型物料塑化和塑料熔体流动的 必要条件。对物料的塑化及制品的质量和产量有着十分 重要的影响。
(2)关闭冷却水进水阀、压缩空气机或真空泵、 牵引机等。
(3)拆机头,并清理
一、硬质聚氯乙烯塑料管材
硬质聚氯乙烯塑料简称为PVC-U,也可用UPVC来 1表.原示材。料的选用
硬质聚氯乙烯管材,应选用悬浮聚合的高型 号的树脂,如通常以SG-5型树脂为主要原料, 也可选用SG-6型树脂和SG-4型树脂。
2.压力
a、压力的建立
挤出成型时,沿料筒轴线方向,在物料内部 要建立起不同压力,主要由以下两个方面的因 素造成的:
压缩比的存在:螺槽深度的改变、料筒上的沟 槽深度变化、螺距的改变等。
分流板、滤网和口模产生的阻力。
压力的建立是物料得以经历物理状态变化、得 到均匀密实的熔体、并最后得到成型制品的重 要条件之一。
在各段温度设定应考虑以下几个方面:一是聚 合物本身的性能,如熔点,分子量大小和分布,熔 体指数等。其次考虑设备的性能。有的设备,进料 段的温度对主机电流的影响很大。再次,通过观察 管模头挤出管坯表面是否光滑。有无气泡等现象来 判断。
挤出成型所需控制的温度是机筒温度、机颈温 度、口模温度。
机筒温度分布,从喂料区到模头可能是平坦分布, 递增分布,递减分布及混合分布。主要取决于材 料物点和挤出机的结构。
一、挤出成型基本原理
将熔融的塑料自模具内以挤压的方式往外推出,而 得到与模口相同几何形状的流体,冷却固化后,得到 所要的零件。
塑料异型材挤出模具ppt课件

精品
7
⑤要让型材坯料在离开模头之 前有足够的纯剪切流动过程
➢让料流在纯剪切流动的过程中尽可能充分地实 现弹性松弛,这也就是说,模头流道出口前都 要有一段足够长的平直段(或称成型段)。
➢平直段长度也绝不是越长越好。平直段长, 会增大背压,增加功耗;
➢会延长模塑料在高温段的停留时间,这尤其 对PVC塑料是十分不利的;
应的壁厚中心线之间的距离分别为Ao和Bo 设该 型材口模图形外形的长和宽分别为A’和B’,其
相应的口模缝隙中心线之间的距离分别为A0’ 和 B0’。
由于平缝口模的离模膨胀只发生在型坯壁厚
方向,所以可以认为该型材型坯的离模膨胀,以
口模缝隙中心线为中心对称发生,即型材壁厚中
心线之间的距离不受离模膨胀作用的影响,但仍
精品
精品
22
选择异型材的挤出中心——方法二
➢ 对于横截面形状较分散的异型材,这样的选择 会较有利于实现整个模头流道均衡地分流,对 提高模头的出料稳定性是大有好处的(图c)
精品
23
选择异型材的挤出中心——方法三
➢选择异型材横截面的主要型腔的中心,作为挤 出中心
➢或根据前两种选择方法作适当调整
精品
24
➢选择异型材的挤出中心,也就是在确定模头的 料流开始分流前的流道中心,与挤出生产线上 异型材截面的位置关系,这对实现均衡分流是 有影响的。
精品
27
口模截面图设计 P279
➢口模截面图(简称为口模图形)是挤出模头流 道出口的截面形状,是由挤出模头的型芯(包 括型芯镶件)和口模板(亦称成型板)两种零 件构成的。
➢口模图形确定了型芯(包括内筋)的外形和口 模板的内腔尺寸,是挤出模头上最关键的尺寸。 正确的口模图形是挤出模头设计的基本要求之 一。