颜料预分散生产工艺
分散染料的染色工艺

3、工艺说明
• 热溶设备
– 热风导辊式:最常用,时间长,幅度不 易控制 – 热风针板式:可控制幅度,但热溶时间 难以保证
– 高温过热蒸汽式:相同时间,则温度可 低些;相同温度,则时间可短些
一、高温高压染色法(卷染)工艺
• 1、工艺流程及主要条件 冷水进缸→温水2道(60~65℃,2道)→60℃
起染色2道→1道升温至100℃→ 1道升温至
110℃→ 1道升温至120℃→1道升温至
130℃→130℃保温染色6道→冷水洗2道→还
原清洗(38% NaOH 3ml/L、85%保险粉 2.5g/L、表面活性剂3g/L,70~80℃,2道)→ 水洗 (40~50℃,1道)→冷水洗→出缸
• 非离子性表面活性剂溶解度随温度的升高而降低,选 择非离子型表面活性剂的浊点一定要高于染色温度, 否则会破坏染液的稳定。
3、工艺说明
(3)浴比 • 1:10~1:30(最低的现已达1:3) (4)染浴的pH值 • 大部分分散染料在高温强碱作用下会被水解破坏, 色光发暗,涤纶pH>7的时候剥皮效应显著 • PH<5影响色光和上染率 ∴因此高温高压染色一般控制在弱酸性范围,pH = 5~ 6。 • 用酸或强酸弱碱盐调节 • 常用:冰醋酸0.5ml/L或磷酸二氢铵1~2g/L
3、工艺说明
• 烘干
– – – – 主要应防止染料的泳移 一般采用红外线预烘,在热风或烘筒烘干 也可红外线、热风和烘筒联合使用 为防止泳移,开始以无接触烘燥较适宜,在织物干至一定 程度后(含水率在25%或30%以下),再用接触烘燥或升 高热风温度,以提高烘燥速率。
• 织物烘干后应立即进行热溶,以保持织物的热量, 缩短升温时间,热溶时,分散染料扩散进入纤维内 部而固着
颜料预分散的生产工艺

颜料预分散的生产工艺颜料分散前的形态,通过生产过程得到的原始颜料称为湿滤饼,还需进一步商品化处理,包括粉碎和干燥等过程。
在干燥过程中,较细的颜料颗粒会产生凝聚,使其粒径较原始颗粒大许多倍,因而不能直接用于着色,必须要进行分散处理。
颜料的质量,除了色光、着色力、遮盖力、各种耐性等性能要求以外,分散性或易研磨性是一项很重要的指标。
颜料的分散性直接关系到所生产的油墨和涂料的色强、细度、光泽度等重要的质量指标,分散效果好的还可以缩短生产涂料时的研磨工时。
(一)颜料的分散一般商品颜料颗粒是指比团聚体还大的粒子,粒径在250μm至750μm(相当于通过60至200目筛)。
根据德国标准协会(German Standard Organization)命名法,认为颜料颗粒状态可分为:原生颗粒、凝聚体和团聚体。
原生颗粒(German Standard Organization)是单晶、块状、球形或微晶组成的大晶体形式存在;凝聚体(Aggregates)是由原生颗粒表面彼此吸附而成;团聚体(Agglomerates)是由原生颗粒或凝聚体疏松的组合,或者是这两者在边、角上相互吸附而成的混合物。
作为使用者来讲,任何商品形式的颜料都要求容易均匀分散,能制成持久稳定、无凝聚、无沉降的悬浮物料。
上世纪七十年代以来,颜料的加工处理技术已有很大发展,包括颜料颗粒的表面处理和颗粒的晶相调整等,但还不能满足使用者对其的要求。
一般情况下,颜料的分散过程可以分为三步:润湿→细化→稳定化混合分散。
第一步是使用润湿剂润湿颜料,使颜料之间的凝聚力减小,便于第二步颜料的粉碎和细化。
粉碎细化后的颜料进一步再做包覆处理,由于颜料经分散细分后,粒径减小,表面积增大,颜料表面自由能也增加,造成细化的颜料不稳定性。
所以,当机械研磨能去除以后,颜料粒会再凝集起来。
为此,在颜料研磨后形成新的表面时,在其表面应吸附一层包覆层,使颜料的表面能降低。
当带有包覆层颜料的结合体再度碰撞就不会凝聚起来。
颜料预分散的生产工艺

颜料预分散的生产工艺颜料预分散是一种将颜料粉末事先分散到液体介质中的工艺。
它的目的是在生产过程中,使颜料与介质充分混合,实现均匀悬浮,以便后续加工和应用。
颜料预分散能够提高颜料的利用率,减少生产过程中的环境污染,提高产品质量和生产效率。
颜料预分散工艺的核心是将颜料粉末与液体介质进行混合。
首先,需要选择合适的介质,通常选择的是有机溶剂或水。
然后,将颜料粉末逐渐加入到介质中,并通过搅拌或者高速剪切等方法,将颜料粉末分散到介质中。
在这个过程中,需要控制好颜料的分散度,以保证颜料颗粒的均匀分布。
颜料预分散的生产工艺有多种方法,其中常用的包括机械搅拌、高速剪切、超声波处理等。
机械搅拌是一种通过搅拌设备将颜料粉末与介质进行混合的方法。
这种方法简单易行,适用于大多数颜料的预分散。
高速剪切是一种通过高速旋转刀片将颜料粉末切割并分散到介质中的方法。
这种方法适用于颜料粒径较大的情况。
超声波处理是一种利用超声波的机械作用将颜料粉末分散到介质中的方法。
这种方法适用于颜料粒径较小的情况。
颜料预分散的生产工艺在实际应用中具有广泛的应用。
首先,颜料预分散能够提高颜料的利用率。
由于颜料预分散可以实现颜料的均匀悬浮,减少颜料的聚集和沉淀,因此能够有效地提高颜料的利用率。
其次,颜料预分散能够减少生产过程中的环境污染。
在传统的颜料生产过程中,颜料粉末容易扬尘,对环境造成污染。
而颜料预分散能够将颜料粉末与介质充分混合,减少粉尘的产生,降低环境污染。
此外,颜料预分散还能够提高产品质量和生产效率。
颜料预分散可以使颜料与介质充分混合,提高产品的均匀性和一致性。
同时,颜料预分散还可以减少生产过程中的工艺步骤,提高生产效率和降低生产成本。
总结起来,颜料预分散是一种将颜料粉末事先分散到液体介质中的生产工艺。
它能够提高颜料的利用率,减少生产过程中的环境污染,提高产品质量和生产效率。
颜料预分散的生产工艺包括机械搅拌、高速剪切、超声波处理等方法。
在实际应用中,颜料预分散具有广泛的应用价值。
学习分散/活性染料一浴法生产工艺

学习分散/活性染料一浴法生产工艺聚酯纤维和纤维素纤维混纺织物常采用活性染料和分散染料染色,染色方法一般可以分为:二浴法、一浴两步法、一浴一步法。
一浴法染色主要优势是:缩短染色时间;节约能耗和用水,减少污水;简化染液配制与加料的操作,以及减少由此带来的相关问题。
本文主要对聚酯/纤维素一浴法染色及其所用中性固色活性染料进行综述。
1分散/活性一浴法染色难点1、染色温度分散染料在聚酯纤维中扩散速率很低,所以染色温度高,一般为110~130℃,远高于常用活性染料染色温度,载体染色时,虽然可在100℃左右,这对活性染料来说还是较高的,活性染料染色大部分温度在60~90℃,温度高不仅固色效率低,而且染料直接性降低后难染的深色。
2、染色pH值活性染料大部分是在碱性条件下固色的,而分散染料高温高压染色应在弱酸性介质中进行,载体法染色也是在弱酸性介质中进行。
因大多数分散染料在碱性条件下很容易发生水解或还原破坏,使染料发生色变或退色,而活性染料如在弱酸性条件下固色,不仅固色效率低,而且染料和纤维之间的共价键的断裂速度也快。
3、电解质活性染料浸染时为了提高上染速率和上染百分率,需要加入一定量的中性电解质,特列是在染色温度高和浴比大时,加入量更多。
分散染料是靠分散剂呈悬浮体分散在染液中,分散稳定性随染液中电解质含量的增加而降低,大量的电解质使分散染料颗粒增大,甚至产生沉淀,从而降低其上染率和匀染效果。
4、染料之间或活性染料和分散剂之间的相互作用许多分散染料及分散剂在温度较高的条件下,会与活性染料发生反应,使分散染料和活性染料的固色率均降低,特别容易发生在染色或固色温度较高的情况下,如高温高压法染色。
采用载体法染色时,载体也会与活性染料发生反应。
5、染色牢度由于两种染料不仅上染对应的纤维,还会严重对另一种纤维发生沾色,特别是分散染料对纤维素纤维,例如对棉纤维的沾色,会大大降低其皂洗和摩擦牢度,这也是当前这类混纺织物染色牢度较差的重要原因。
涂料工艺讲座
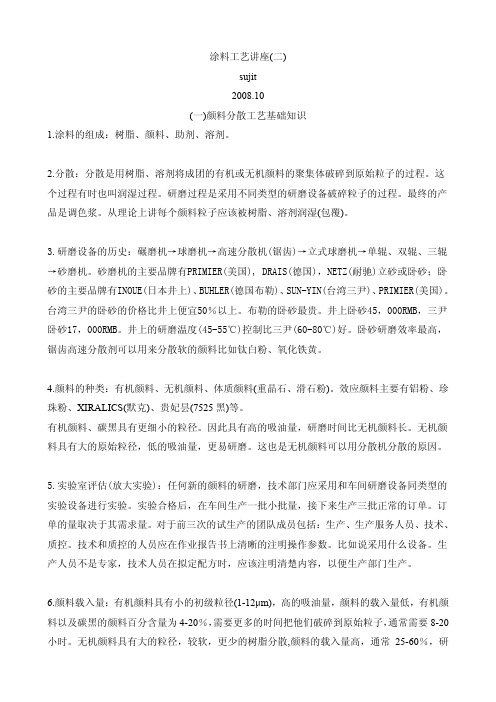
涂料工艺讲座(二)sujit2008.10(一)颜料分散工艺基础知识1.涂料的组成:树脂、颜料、助剂、溶剂。
2.分散:分散是用树脂、溶剂将成团的有机或无机颜料的聚集体破碎到原始粒子的过程。
这个过程有时也叫润湿过程。
研磨过程是采用不同类型的研磨设备破碎粒子的过程。
最终的产品是调色浆。
从理论上讲每个颜料粒子应该被树脂、溶剂润湿(包覆)。
3.研磨设备的历史:碾磨机→球磨机→高速分散机(锯齿)→立式球磨机→单辊、双辊、三辊→砂磨机。
砂磨机的主要品牌有PRIMIER(美国), DRAIS(德国),NETZ(耐驰)立砂或卧砂;卧砂的主要品牌有INOUE(日本井上)、BUHLER(德国布勒)、SUN-YIN(台湾三尹)、PRIMIER(美国)。
台湾三尹的卧砂的价格比井上便宜50%以上。
布勒的卧砂最贵。
井上卧砂45,000RMB,三尹卧砂17,000RMB。
井上的研磨温度(45-55℃)控制比三尹(60-80℃)好。
卧砂研磨效率最高,锯齿高速分散剂可以用来分散软的颜料比如钛白粉、氧化铁黄。
4.颜料的种类:有机颜料、无机颜料、体质颜料(重晶石、滑石粉)。
效应颜料主要有铝粉、珍珠粉、XIRALICS(默克)、贵妃昙(7525黑)等。
有机颜料、碳黑具有更细小的粒径。
因此具有高的吸油量,研磨时间比无机颜料长。
无机颜料具有大的原始粒径,低的吸油量,更易研磨。
这也是无机颜料可以用分散机分散的原因。
5.实验室评估(放大实验):任何新的颜料的研磨,技术部门应采用和车间研磨设备同类型的实验设备进行实验。
实验合格后,在车间生产一批小批量,接下来生产三批正常的订单。
订单的量取决于其需求量。
对于前三次的试生产的团队成员包括:生产、生产服务人员、技术、质控。
技术和质控的人员应在作业报告书上清晰的注明操作参数。
比如说采用什么设备。
生产人员不是专家,技术人员在拟定配方时,应该注明清楚内容,以便生产部门生产。
6.颜料载入量:有机颜料具有小的初级粒径(1-12μm),高的吸油量,颜料的载入量低,有机颜料以及碳黑的颜料百分含量为4-20%,需要更多的时间把他们破碎到原始粒子,通常需要8-20小时。
颜料预分散的生产工艺

颜料预分散的生产工艺颜料预分散是一种常见的生产工艺,用于将颜料与适当的溶剂或介质混合均匀,以便在后续的应用中更方便地使用。
颜料预分散的生产工艺可以分为以下几个步骤:原料准备、预分散过程和后续处理。
原料准备是颜料预分散的第一步。
在这一步骤中,需要准备颜料和溶剂。
颜料可以是有机颜料或无机颜料,根据不同的应用需求进行选择。
溶剂的选择则需要考虑颜料的特性和使用环境等因素。
选用合适的原料是实现颜料预分散质量的关键。
接下来是预分散过程。
预分散是将颜料和溶剂进行混合的过程,目的是使颜料能够均匀地分散在溶剂中,形成颜料预分散体。
预分散可以通过机械搅拌、高剪切乳化或超声波处理等方法进行。
机械搅拌是一种常用的方法,通过搅拌器的旋转将颜料和溶剂混合均匀。
高剪切乳化则是利用高速旋转的刀片或转子来产生剪切力,将颜料和溶剂分散。
超声波处理则是利用超声波的振动产生剪切力,实现颜料和溶剂的混合。
不同的预分散方法适用于不同的颜料和溶剂。
最后是后续处理。
在预分散完成后,可能需要进行进一步的处理,以满足特定的应用需求。
后续处理可以包括过滤、离心、干燥等步骤。
过滤是将颜料预分散体中的杂质去除,以保证产品的质量。
离心则是利用离心力将颜料和溶剂分离,得到纯净的颜料预分散体。
干燥是将颜料预分散体中的溶剂去除,以便后续的应用。
颜料预分散的生产工艺有着广泛的应用。
在油墨、涂料、塑料等行业中,颜料预分散可以提高生产效率,减少颜料浪费,提高产品质量。
此外,颜料预分散还可以减少颜料对环境的污染,提高生产环境的安全性。
因此,颜料预分散的生产工艺在现代工业中具有重要的意义。
颜料预分散是一种常见的生产工艺,通过将颜料和溶剂混合均匀,可以提高生产效率,减少颜料浪费,提高产品质量。
颜料预分散的生产工艺包括原料准备、预分散过程和后续处理。
合理选择原料、采用适当的预分散方法和进行后续处理可以实现颜料预分散的高质量生产。
颜料预分散的应用广泛,对提高生产效率、保护环境具有重要的意义。
颜料预分散的生产工艺

颜料预分散的生产工艺
颜料预分散是一种将颜料和载体材料预先混合的工艺,以便在后续的
生产过程中更方便地使用。
颜料预分散的生产工艺包括以下几个步骤:
1. 颜料选择:选择适合预分散的颜料,通常选择颗粒较小、易于分散
的颜料。
2. 载体材料选择:选择适合预分散的载体材料,通常选择与颜料相容
性好、易于分散的材料。
3. 预混合:将颜料和载体材料按一定比例混合,通常采用机械混合的
方式,如球磨机、高剪切混合机等。
4. 粉碎:将预混合好的颜料和载体材料进行粉碎,以便更好地分散。
5. 分散:将粉碎后的颜料和载体材料进行分散,通常采用高剪切分散
机等设备。
6. 过滤:将分散好的颜料预分散液进行过滤,以去除杂质和颗粒。
7. 包装:将过滤好的颜料预分散液进行包装,以便后续使用。
颜料预分散的生产工艺需要注意以下几个问题:
1. 颜料和载体材料的选择要合理,以保证预分散后的颜料具有良好的
分散性和稳定性。
2. 预混合和粉碎的过程要控制好时间和速度,以避免颜料和载体材料
的热量过高,影响颜料的质量。
3. 分散的过程要控制好分散机的转速和时间,以保证颜料和载体材料
的充分分散。
4. 过滤的过程要注意过滤器的选择和清洗,以避免杂质和颗粒的残留。
5. 包装的过程要注意密封性和防潮性,以保证预分散液的质量和稳定性。
总之,颜料预分散的生产工艺需要严格控制每个环节,以保证预分散
后的颜料具有良好的分散性和稳定性,从而更方便地应用于后续的生
产过程中。
颜料预分散的生产工艺

颜料预分散的生产工艺一、引言颜料预分散是一种在颜料应用领域广泛使用的生产工艺。
通过预分散,颜料粒子可以更好地分散在溶剂或树脂基质中,从而提高颜料的可溶性和稳定性。
本文将深入探讨颜料预分散的生产工艺,包括预分散的原理、工艺流程以及常见的预分散方法。
二、颜料预分散的原理颜料的预分散是通过力的作用,将颜料粒子分散在溶剂或树脂基质中,形成稳定的分散体系。
其原理主要包括表面活性剂作用、机械剪切作用以及热力学作用。
2.1 表面活性剂作用表面活性剂是一种能够降低界面张力的化学物质,它在颜料分散过程中起到了非常重要的作用。
表面活性剂能够吸附在颜料粒子表面,形成一层分散剂分子的保护膜,使颜料粒子间相互排斥,从而防止粒子重新聚集。
同时,表面活性剂还能降低颗粒间的表面能,减小颗粒聚集的能量,增强颜料分散体系的稳定性。
2.2 机械剪切作用机械剪切作用是一种通过剪切力促使颜料粒子分散的方法。
在预分散过程中,通常会使用高速搅拌器、研磨机或超声波设备等设备对颜料进行剪切、碾磨或超声处理。
这些机械作用能够有效地破坏颜料粒子的聚集态,增加颗粒间的碰撞,从而使颜料更好地分散在基质中。
2.3 热力学作用热力学作用是指在预分散过程中,通过加热或冷却颜料分散体系,调节体系的温度以改变其物理性质。
这种方法能够改变颜料粒子和基质之间的相互作用力,提高颜料分散的效果。
例如,加热可以使颜料分散剂的溶解度增加,促进颜料的分散;冷却则可以使颜料粒子聚集,形成较大的颗粒。
三、颜料预分散的工艺流程颜料预分散的工艺流程主要包括颜料的预处理、分散剂的选择与加入、机械剪切或超声处理以及最终产品的收集与储存等步骤。
3.1 颜料的预处理颜料的预处理非常重要,可以提高预分散的效果。
预处理步骤通常包括颜料的筛选、研磨和干燥。
颜料的筛选可以去除颗粒的杂质和过大或过小的颗粒。
研磨可以使颜料颗粒更加均匀,增大颗粒的比表面积,有利于分散剂的吸附和颗粒间的碰撞。
干燥可以去除颜料中的水分,避免水分对分散体系的稳定性产生影响。
- 1、下载文档前请自行甄别文档内容的完整性,平台不提供额外的编辑、内容补充、找答案等附加服务。
- 2、"仅部分预览"的文档,不可在线预览部分如存在完整性等问题,可反馈申请退款(可完整预览的文档不适用该条件!)。
- 3、如文档侵犯您的权益,请联系客服反馈,我们会尽快为您处理(人工客服工作时间:9:00-18:30)。
颜料预分散的生产工艺颜料分散前的形态,通过生产过程得到的原始颜料称为湿滤饼,还需进一步商品化处理,包括粉碎和干燥等过程。
在干燥过程中,较细的颜料颗粒会产生凝聚,使其粒径较原始颗粒大许多倍,因而不能直接用于着色,必须要进行分散处理。
颜料的质量,除了色光、着色力、遮盖力、各种耐性等性能要求以外,分散性或易研磨性是一项很重要的指标。
颜料的分散性直接关系到所生产的油墨和涂料的色强、细度、光泽度等重要的质量指标,分散效果好的还可以缩短生产涂料时的研磨工时。
(一)颜料的分散一般商品颜料颗粒是指比团聚体还大的粒子,粒径在250μm至750μm(相当于通过60至200目筛)。
根据德国标准协会(German Standard Organization)命名法,认为颜料颗粒状态可分为:原生颗粒、凝聚体和团聚体。
原生颗粒(German Standard Organization)是单晶、块状、球形或微晶组成的大晶体形式存在;凝聚体(Aggregates)是由原生颗粒表面彼此吸附而成;团聚体(Agglomerates)是由原生颗粒或凝聚体疏松的组合,或者是这两者在边、角上相互吸附而成的混合物。
作为使用者来讲,任何商品形式的颜料都要求容易均匀分散,能制成持久稳定、无凝聚、无沉降的悬浮物料。
上世纪七十年代以来,颜料的加工处理技术已有很大发展,包括颜料颗粒的表面处理和颗粒的晶相调整等,但还不能满足使用者对其的要求。
一般情况下,颜料的分散过程可以分为三步:润湿→细化→稳定化混合分散。
第一步是使用润湿剂润湿颜料,使颜料之间的凝聚力减小,便于第二步颜料的粉碎和细化。
粉碎细化后的颜料进一步再做包覆处理,由于颜料经分散细分后,粒径减小,表面积增大,颜料表面自由能也增加,造成细化的颜料不稳定性。
所以,当机械研磨能去除以后,颜料粒会再凝集起来。
为此,在颜料研磨后形成新的表面时,在其表面应吸附一层包覆层,使颜料的表面能降低。
当带有包覆层颜料的结合体再度碰撞就不会凝聚起来。
降低新形成的接口表面能,以便在进一步加工时,不至于使颜料产生再凝聚现象。
第三步是将细化后的颜料在熔体中能均匀分散。
由于细化了的颜料表面积增加,进而表面能提高,导致颜料的稳定性降低,颜料之间就容易相互凝聚起来,从而使表面能降低至稳定的状态。
由于吸附了一层包覆层,也使能量下降,比之前的状态要稳定,所以达到了颜料细化的目的。
(二)颜料分散的办法大体上讲,颜料的分散方法大致有下列三种:干混合法、融体剪切法和液体研磨法。
干混合法是指颜料与树脂由低到高速强度下混合,颜料分散主要通过冲击研磨而实现的,其主要设备有高低速混合机;融体剪切法是指在捏合作用下,通过熔化树脂传递大剪切应力;液体研磨法则是指通过液态载体的冲击式剪切力来分散颜料。
目前,市场上能比较好地解决颜料分散性的产品主要有以下几种商品形式:预分散颜料色片、浆状颜料和色母粒等三种。
除此之外,还有一些如色饼、色膏等针对性很强的产品。
一是由专业生产厂家将颜料加工成颜料色片(Pigmented chips,Color chips)。
所谓颜料色片,也称固体色浆、色粒、干片、切片、预分散颜料,指的是颜料和指定载体树脂的固态均匀混合物,也就是预分散在树脂中的高浓度颜料。
预分散颜料色片中的颜料含量比较高,根据体系的不同,一般可以在50-70%之间,载体树脂的含量比例在30-50%左右,某些如硝化棉(N/C)体系的颜料色片品种还含有环保的增塑剂。
预分散颜料色片,等同于给油墨制造商按比例配制好的颜料和树脂,它可以被直接装入油墨配方,也可以先按色浆的要求先分散成半成品——色浆,再以色浆加入调墨油的形式混合制成油墨。
由于预分散颜料可以很容易地在高速分散机上进行分散,其分散细度完全可以满足一般油墨的要求。
由此可见,易分散性是它的最大优势。
如果对油墨产品的细度要求很高,或者说要求有纳米级效果,可以对半成品色浆进行一次快速砂磨处理,得到的色浆性能可以用“极好的巅峰状态”来形容,不管是色泽、光泽和亮度都是无与伦比的。
预分散颜料的市场推广应用,有一个价格因素在制约。
笔者一直希望其能进行大规模的商品化生产,从源头上降低成本。
如能和颜料生产厂家一起研究开发,不仅能从原材料成本上控制,更能从技术、服务上得到长足进展。
二是由颜料生产厂直接制成浆状颜料(色浆,Color paste),由油墨、涂料生产厂在生产时直接加入配方使用,从而可以省却费时费力的研磨作业工序,得到效果比较满意的产品。
典型意义上的浆状颜料(色浆)是指颜料生产厂将颜料湿滤饼,采取脱水步骤后,把颜料分散到各种基料中去,制成一种色浆。
一般有机颜料比重小,色浆的颜料含量也较低;而无机颜料的比重大,则可达到较高的颜料含量。
浆状颜料可保持颜料沉淀时的颗粒尺寸,特点是细度好、色泽也较鲜明、着色力也较高。
三是色母粒。
色母粒(Color Master Batch)是指颜料按20%-80%的比例经研磨或双螺杆挤出均匀地分散到树脂中而制得的颜色颗粒,美国称之为颜料浓缩物(Pigment Concentration)或颜料制备物(Pigment Preparation)。
它具有着色效果优越、便于自动计量和运输、节约能源、无粉尘、无污染等优点,在[wiki]塑料[/wiki]等材料的着色中应用普遍。
这其中,载体是色母粒的重要组成部分,其作用是增强颜料与要着色的树脂之间的亲和力和提高着色组分与树脂的分散与混合。
用茂金属催化法合成的树脂作载体能大大提高颜料在色母粒中的协同效应和分散性。
由于颜料在色母粒中分散性提高,更可获得一个更均一的相,因此,可以做到颜料用量更少,却能同时保持高着色质量效果。
这是因为茂金属催化法合成的树脂与Z-N催化法合成的树脂不同,茂金属催化法合成的树脂作载体能制备高浓度的色粒,颜料含量更可达80%。
除此之外,色母粒中用茂金属催化法合成的树脂作载体,不仅会使着色容易,还能使色母粒产生美观感,而且对着色产品的力学性能也有改善,这是因为颜料分散好以后,结晶性可以提高,得到的制品的耐应力、开裂性能相应提高。
(三)颜料色片的生产与前景1、生产颜料色片的主要方法目前主要的通用方法有混炼法和挤水法。
前者主要是将颜料和纤维素、增塑剂、稳定剂和树脂等混合后,在加热的混炼机上进行熔融混炼,直至均匀,然后拉成片状,冷却后,以粉碎机粉碎成预分散颜料色片。
挤水法生产,则是通过对颜料滤饼和纤维素、增塑剂、稳定剂及树脂等混合后挤压,直至均匀,再将其进行脱水后处理,拉成片状,粉碎成颜料色片。
2、颜料色片的生产设备主要的设备是开放式炼塑机,也称二辊机。
它通过两个具有一定速度差的转动辊筒对物料进行混合、塑化。
两辊相向旋转使物料在辊筒隙间受到强烈的挤压和剪切,从而达到颜料分散和混合均匀,混炼均匀出片后,冷却切粒即可。
一般影响开炼机塑化质量的因素主要有:辊筒的温度、辊筒间距、前后辊筒速度、物料堆放量及混炼次数。
该设备用于小型生产的较多,也有厂商用于生产色母粒和碳酸钙填充母粒。
3、颜料色片的发展方向颜料色片的发展,和高性能的颜料发展一直是同步的。
性能的卓越性、应用时的持久性和对供应链中所有部分高附加值的经济性是当今高档有机颜料的发展方向。
比如,颜料紫23(PV23),也被称为咔唑紫,它也许是仅次于酞菁蓝或酞菁绿颜料的可以用于世界上几乎所有用途的最重要的高性能颜料之一。
颜料紫23呈现紫红的颜色,其特点是具有非常高的着色力,无与伦比的鲜亮色泽,以及在几乎所有塑料中很好的耐光性和耐热性。
在橙色与红色色泽区域中,最著名最流行的高性能颜料有喹吖啶、二萘嵌苯、索兰士林亮橙、二酮基吡咯并吡咯颜料,它们具有优异的耐光性和耐候性、高度热稳定性和令人满意的抗色移性。
高性能颜料中杰出的一类是酞菁蓝和酞菁绿一类,它们具有优异的整体耐受性能以及热稳定性和色迁移稳定性。
在涂料、油墨的生产中,分散是一个复杂且耗费成本的过程。
谁都希望在简化步骤的同时,能得到可重复生产的高色强度和高质量。
在使用无机颜料的领域中,颜料色片很好地解决了性能不稳定、色浓度差、研磨费时等难题。
颜料的易分散化是需求者最希望获得的特性,如奶粉和速溶咖啡的出现,只要搅拌就会很容易地分散于媒体中的颜料,是使用者最为理想的状态。
可以不夸张地说,由于颜料色片的出现和表面处理的工业化发展,加上新型分散剂的开发和分散机的进步,颜料的分散变得比往年更加地容易了。
本身,粉体颜料飞散所致粉尘污染,从作业环境来看绝不是一件好事,所以,通过颜料的珠粒化、颗粒化、片状化及添加飞散防止剂等手段,使得非飞散性且容易计量的颜料得以普及,这也是颜料色片生存和发展的土壤。
今后随着使用者需求的多样化,逐渐需要以多品种、少批量生产来迎合市场。
由于多品种、少批量生产一定会提高制品的成本,所以,由特定颜料色片制造商集中生产颜料色片制品,各油墨制造商以自己的品牌和销售途径提供给需求者的方法会日趋增加,这是大势所趋。
4、颜料色片在开发、销售过程中的几个问题(1)印刷油墨工业在需要其性能时会采用高档有机颜料。
就好比用红122来替代光稳定性不够的颜料红57;在需要降低铜含量时,用颜料蓝16和蓝79来替代颜料蓝15。
这也就要求颜料色片生产厂家时时刻刻踏准节奏,及时推出适合市场的新产品。
业内有学者指出,未来有机颜料的发展趋势无怪乎以下几个方面:新型化学结构的有机颜料、金属络盐颜料、偶合(Co-coupling)偶氮颜料、固溶体颜料、粒度分布调整颜料、结晶形调整颜料、颜料改质剂,这同时也是给颜料色片指明了一条道路。
(2)当然,我们也不希望看到一窝蜂地上颜料色片生产线,毕竟这是只有在制造中高档油墨时油墨生产商才会考虑的。
省工省时、性能超群是一点不假,但国内真正能理解的还是不多,推广应用起来还是有一定的困难。
许多新开业的颜料色片生产厂家开工率不足,就是很好的一个说明。
有句俗话:中国人想要的一定贵,中国人能做的一定便宜。
我们不希望这句话在颜料色片生产领域也一样的应验。
在低层次地领域竞争,只会对这个行业产生最负面的影响。
图一时之利的后果大家一定都明白。
从有外资背景的珠海芳迪亚(Frontier printing inks Zhuhai)1996年建厂开始,虽然国内对颜料色片的研究开发已有近10年的历史,由于一直以国外市场为主要的终端客户,在国内还没有形成潮流之势。
星星之火,可以燎原。
从笔者浅显地经验来讲,我国颜料色片工业可用一句话概括:发展快、差距小、前景广。
颜料色片在国外发展也只不过几十年的历史,中国改革开放使我国颜料色片工业一起步就紧跟世界发展的潮流。
芳迪亚全套引进了世界先进生产设备和生产技术,进口质量优异的颜料和分散剂,可以生产世界一流水平的颜料色片。
因此可以说中国颜料色片工业水平与世界水平差距不大。
然而中国与外国颜料色片工业不同,国外颜料色片工业由极少数的几个跨国公司垄断生产,反观国内,我国颜料色片生产还没有形成凝聚的核心力量。